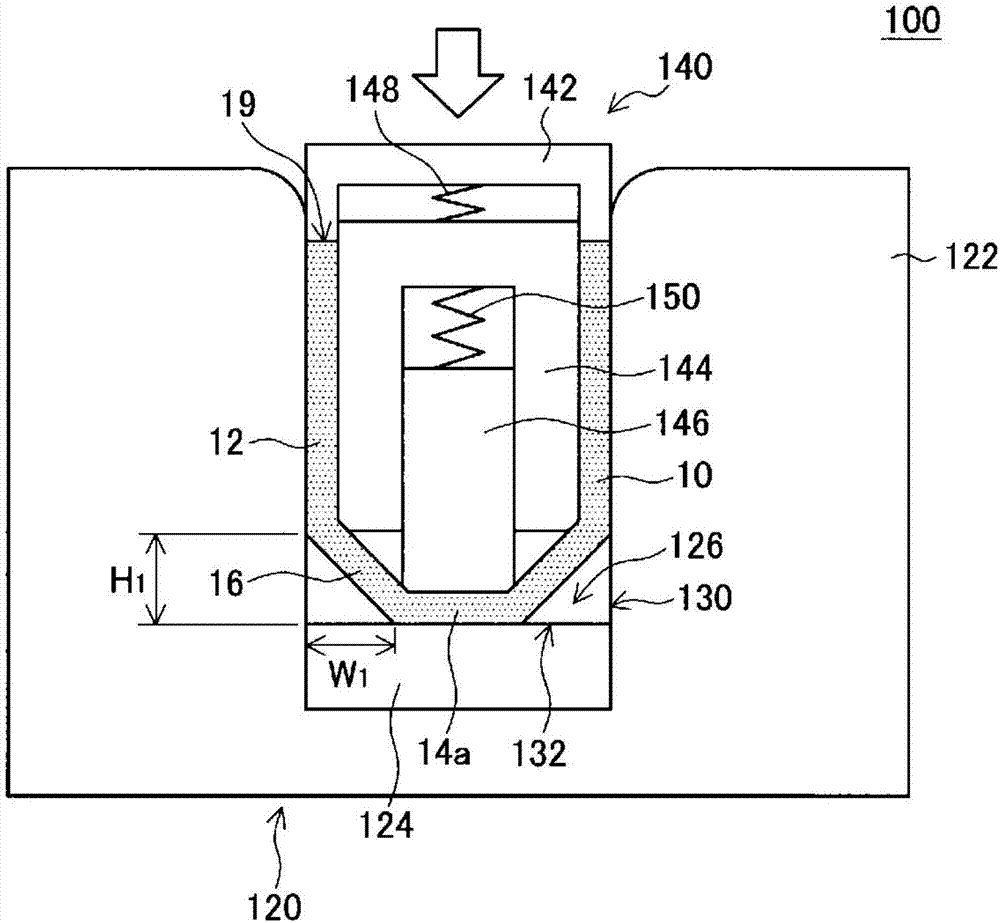
本发明涉及压制加工装置、压制加工方法以及压制成形品,特别是,涉及用于获得在截面含有u字形部分的成形品的压制加工装置、压制加工方法以及利用该种装置或方法获得的压制成形品。
背景技术:
:通过压制加工而成形的长条状的槽形件、帽形件一般用作例如车辆等的骨架构件。在车辆的骨架构件中,为了确保碰撞安全性、车身刚度等而要求较高的强度。另外,同样通过压制加工而成形的轴对称的杯形件一般用作例如车辆的变速器中的鼓、毂等旋转构件。在旋转构件中,为了经受得住所传递的转矩,也要求较高的强度。所述这样的槽形件、帽形件以及杯形件的共通点在于,截面都含有u字形部分。u字形部分包括纵壁部、顶板部以及纵壁部与顶板部之间的角部。在所述那样要求构件的强度的情况下,需要在该u字形部分充分地确保构件的板厚。于是,公知有例如如专利文献1所述那样的技术:在压制加工中使阴模与冲头的间隔比被加工件的板厚大,在形成了u字形部分的大致形状后,推入纵壁部的端部,从而使包括角部在内的u字形部分的整体的板厚增加(增厚)。现有技术文献专利文献专利文献1:日本特开2009-208149号公报技术实现要素:发明要解决的问题在所述这种现有技术中,在推入了纵壁部的端部时,使材料在纵壁部与顶板部之间流动,从而使u字形部分的整体增厚。因此,需要将角部的外侧形成为具有曲率的形状,并且使曲率半径在一定程度上增大,这一点成为设计上的制约。另外,为了使u字形部分整体增厚而进行只使例如角部增厚至期望的板厚那样的加工较为困难。于是,本发明是鉴于所述问题而做成的,本发明的目的在于提供一种在用于获得在截面含有u字形部分的成形品的压制加工中能够实现角部的自如的成形的、新型且改良了的压制加工装置、压制加工方法以及压制成形品。用于解决问题的方案为了解决所述问题,根据本发明的一观点,提供一种压制加工装置,该压制加工装置用于通过被加工件的压制加工来获得成形品,其中,成形品在截面含有由顶板部、纵壁部以及顶板部与纵壁部之间的角部形成的u字形部分,所述压制加工装置包括:阴模,其形成有用于容纳u字形部分的凹部;第1冲头,在其与凹部的底面之间夹持顶板部的中央区域;以及第2冲头,其比第1冲头晚地被推入到凹部中,在该第2冲头与凹部的侧面之间约束纵壁部,并且在该第2冲头与底面之间夹入被加工件而成形顶板部的边缘区域以及角部,基于角部的目标板厚来设定对顶板部的中央区域进行夹持的第1冲头的夹持宽度以及第2冲头在推入方向上自第1冲头后退的后退量。在所述的压制加工装置中,也可以是,在压制加工开始时,被加工件为平板状,第1冲头以及第2冲头通过第1压制在维持着第2冲头比第1冲头后退的状态的状态下向凹部推入平板状的被加工件,成形纵壁部以及顶板部的中央区域。也可以是,第2冲头通过第2压制加工被推入到凹部中,在该第2冲头与底面之间夹入被加工件而成形顶板部的边缘区域以及角部。另外,也可以是,将第1冲头的夹持宽度以及第2冲头的后退量设定为,使通过第1压制加工而成形得到的顶板部的中央区域与纵壁部之间的锥形部的截面积,与通过第2压制加工而成形得到的角部达到了目标板厚的成形品的棱线部的截面积一致。例如,可以将第1冲头的夹持宽度以及第2冲头的后退量设定为满足下述式子(a),[算式1]这里,h1为第2冲头的后退量,w1为锥形部在宽度方向上的长度,rp为角部的内侧的曲率半径,t为被加工件的板厚。在所述的压制加工装置中,成形品既可以为u字形部分形成槽形形状的长条状构件,也可以为u字形部分形成杯状的轴对称构件。另外,角部也可以成形为板厚比纵壁部以及顶板部的板厚厚。角部的外侧也可以成形为大致直角。所述的压制加工装置也可以还包括第3冲头,该第3冲头抵接于纵壁部的与角部所在侧相反的那一侧的端面,在成形了角部后朝向底面进行压制。另外,为了解决所述问题,根据本发明的另一观点,提供一种压制加工方法,其用于通过被加工件的压制加工来获得成形品,其中,成形品在截面含有由顶板部、纵壁部以及顶板部与纵壁部之间的角部形成的u字形部分,所述压制加工方法包括如下工序:第1压制加工工序,在该第1压制加工工序中,第1冲头在其与凹部的底面之间夹持顶板部的中央区域;以及第2压制加工工序,在该第2压制加工工序中,第2冲头比第1冲头晚地被推入到阴模的凹部中,在第2冲头与凹部的侧面之间约束纵壁部,并且在第2冲头与底面之间夹入被加工件而成形顶板部的边缘区域以及角部,基于角部的目标板厚来设定对顶板部的中央区域进行夹持的第1冲头的夹持宽度以及第2冲头在推入方向上自第1冲头后退的后退量。也可以是,在压制加工开始时,被加工件为平板状,在第1压制加工工序中,第1冲头以及第2冲头在维持着第2冲头比第1冲头后退的状态的状态下向凹部推入平板状的被加工件,成形纵壁部以及顶板部的中央区域。在第2压制加工工序中,也可以是,第2冲头被推入到凹部中,在第2冲头与底面之间夹入被加工件而成形顶板部的边缘区域以及角部。也可以是,将第1冲头的夹持宽度以及第2冲头的后退量设定为,使通过第1压制加工而成形得到的顶板部的中央区域与纵壁部之间的锥形部的截面积,与通过第2压制加工而成形得到的角部达到了目标板厚的成形品的棱线部的截面积一致。例如,也可以将第1冲头的夹持宽度以及第2冲头的后退量设定为满足下述式子(b),[算式2]这里,h1为第2冲头的后退量,w1为锥形部在宽度方向上的长度,rp为角部的内侧的曲率半径,t为被加工件的板厚。另外,压制加工方法也可以在第1压制加工工序之前,具有将被加工件加热到预定的温度的加热工序。此外,压制加工方法也可以在第1压制加工工序之前,还具有将成形品的u字形部分容纳到形成于阴模的凹部的容纳工序。所述压制加工方法也可以还包括附加成形工序,将在截面含有由顶板部、纵壁部和角部形成的u字形部分的成形品作为第2被加工件,使用第2压制加工装置在利用第2阴模以及第4冲头夹持着第2被加工件的顶板部的状态下,利用第5冲头推入第2被加工件的纵壁部的端面,成形第2成形品,所述第2压制加工装置包括:第2阴模,其具有凹部,该凹部是与第2成形品的形状相对应的形状,该凹部用于收纳第2被加工件,所述第2阴模至少支承第2被加工件的顶板部;第4冲头,其与第2阴模一起夹持第2被加工件的顶板部;以及第5冲头,其推入第2被加工件的纵壁部的端面,成形第2成形品。这里,也可以是,第2压制加工装置的第2阴模的凹部的与第2被加工件的纵壁部相对应的面之间的长度形成为比第2被加工件的纵壁部的外表面之间的长度长,在附加成形工序中,在利用第2阴模以及第4冲头夹持着第2被加工件的顶板部的状态下,利用第5冲头推入第2被加工件的纵壁部的端面,使第2被加工件的纵壁部增厚。或者,也可以利用用于支承中央区域的固定阴模和用于支承端部并能沿纵壁部的延伸设置方向移动的可动阴模构成第2压制加工装置的第2阴模中的、用于支承第2被加工件的顶板部的部分,在附加成形工序中,在利用第2阴模以及第4冲头夹持着第2被加工件的顶板部的状态下,利用第5冲头推入第2被加工件的纵壁部的端面,使可动阴模移动而形成在纵壁部延伸设置的纵壁延伸设置部。另外,也可以在第2压制加工装置的第2阴模中的、用于支承第2被加工件的纵壁部的部分,在与第2被加工件的顶板部相对应的位置形成有向与纵壁部分开的方向凹陷的台阶部,在附加成形工序中,在利用第2阴模以及第4冲头夹持着第2被加工件的顶板部的状态下,利用第5冲头推入第2被加工件的纵壁部的端面,形成在顶板部延伸设置的顶板延伸设置部。另外,为了解决所述问题,根据本发明的另一观点,提供一种压制成形品,通过被加工件的压制加工而成形得到该压制成形品,并且该压制成形品在截面含有由顶板部、纵壁部以及顶板部与纵壁部之间的角部形成的u字形部分,其中,角部比纵壁部以及顶板部的板厚厚。另外,根据本发明的另一观点,提供一种压制成形品,通过被加工件的压制加工而成形得到该压制成形品,并且该压制成形品在截面含有由顶板部、纵壁部以及顶板部与纵壁部之间的角部形成的u字形部分,其中,角部的外侧为大致直角。这里,角部的内侧的曲率半径r1、角部的外侧的曲率半径r2、被加工件的顶板部以及纵壁部的板厚t满足下述式子(c)的关系,r2≤r1+t……(c)。另外,压制成形品的角部的硬度比被加工件的硬度高。例如,压制成形品的角部的硬度为被加工件的硬度的1.5倍以上。另外,压制成形品的顶板部由中央区域和边缘区域形成,该边缘区域位于中央区域与角部之间,是距角部预定的距离内的区域,中央区域与边缘区域的交界部分的硬度比被加工件的硬度高,且比角部的硬度低。这里,也可以基于被加工件的板厚和角部的内侧的曲率半径来确定距角部的预定的距离。也可以是,压制成形品的顶板部的中央区域是通过第1压制加工而成形得到的区域,压制成形品的顶板部的边缘区域是通过第1压制加工后的第2压制加工而成形得到的区域。另外,也可以是,压制成形品的纵壁部的板厚比顶板部的板厚厚。压制成形品也可以还包括将纵壁部延伸设置后形成的纵壁延伸设置部。或者,压制成形品也可以还包括将顶板部延伸设置后形成的顶板部延伸设置。发明的效果如上所述,采用本发明,能在用于获得在截面含有u字形部分的成形品的压制加工中实现角部的自如的成形。附图说明图1是将本发明的第1实施方式的压制加工装置的结构与压制加工时的动作一起表示的概略性的剖视图。图2是将本发明的第1实施方式的压制加工装置的结构与压制加工时的动作一起表示的概略性的剖视图。图3是将本发明的第1实施方式的压制加工装置的结构与压制加工时的动作一起表示的概略性的剖视图。图4是将本发明的第1实施方式的压制加工装置的结构与压制加工时的动作一起表示的概略性的剖视图。图5是用于说明第2压制加工后的被加工件的形状所涉及的尺寸的图。图6a是用于说明利用本发明的第1实施方式的压制加工装置成形得到的成形品的截面上的角部的形状的例子的图。图6b是用于说明利用本发明的第1实施方式的压制加工装置成形得到的成形品的截面上的角部的形状的例子的图。图7是表示利用压制加工而成形得到的被加工件的角部以及顶板部的一部分的塑性应变分布的图。图8是表示图7所示的被加工件的硬度分布的图表。图9a是表示本发明的第1实施方式中的成形品的例子的图。图9b是表示本发明的第1实施方式中的成形品的例子的图。图10是表示本发明的第1实施方式的变形例的压制加工装置的动作的概略性的剖视图。图11是表示本发明的第1实施方式的变形例的压制加工装置的动作的概略性的剖视图。图12是用于说明利用本发明的第1实施方式的另一变形例的压制加工装置成形得到的成形品的截面形状的例子的图。图13是将本发明的第1实施方式的另一变形例的压制加工装置的结构与压制加工时的动作一起表示的概略性的剖视图。图14是将本发明的第1实施方式的另一变形例的压制加工装置的结构与压制加工时的动作一起表示的概略性的剖视图。图15是将本发明的第1实施方式的另一变形例的压制加工装置的结构与压制加工时的动作一起表示的概略性的剖视图。图16是将现有技术的压制加工装置的结构与深拉深成形时的动作一起表示的概略性的剖视图。图17是将现有技术的压制加工装置的结构与深拉深成形时的动作一起表示的概略性的剖视图。图18是将本发明的第2实施方式的压制加工装置的结构与压制加工(深拉深成形)时的动作一起表示的概略性的剖视图。图19是将本发明的第2实施方式的压制加工装置的结构与压制加工(深拉深成形)时的动作一起表示的概略性的剖视图。图20是将本发明的第2实施方式的压制加工装置的结构与压制加工(深拉深成形)时的动作一起表示的概略性的剖视图。图21是表示利用本发明的第3实施方式的压制加工而成形得到的成形品的一个例子的说明图。图22是表示使纵壁部增厚的压制加工的初始状态的概略性的剖视图。图23是表示使纵壁部增厚的压制加工的、纵壁部增厚后的状态的概略性的剖视图。图24是表示利用本发明的第4实施方式的压制加工而成形得到的成形品的一个例子的说明图。图25是表示使纵壁部延伸设置的压制加工的初始状态的概略性的剖视图。图26是表示纵壁部的延伸设置后的状态的概略性的剖视图。图27是表示利用本发明的第5实施方式的压制加工而成形得到的成形品的一个例子的说明图。图28是表示使顶板部延伸设置的压制加工的初始状态的概略性的剖视图。图29是表示顶板部的延伸设置后的状态的概略性的剖视图。图30是表示在实施例中作为试验对象的具有凸缘的槽形形状的压制成形的成形方法的说明图。图31是在实施例中作为试验对象的压制成形品的立体图。图32是在实施例中作为试验对象的压制成形品的主视图。图33是表示在实施例中作为试验对象的压制成形品的形状的说明图。图34是说明三点弯曲试验的说明图。图35是表示用在试验1~试验5中的压制成形品的增厚率和最大载荷比的图表。具体实施方式以下,参照附图详细说明本发明的优选的实施方式。另外,在本说明书以及附图中,对于实际上具有相同的功能结构的构成要素,在附图中标注相同的附图标记,有时省略重复的说明。(1.第1实施方式:角部的增厚)(1-1.压制加工装置的动作)图1~图4是将本发明的第1实施方式的压制加工装置的结构与压制加工时的动作一起表示的概略性的剖视图。参照图1~图4,压制加工装置100包括阴模120和冲头140。阴模120包括固定阴模122和可动阴模(垫板)124。冲头140包括固定冲头142、外侧可动冲头(垫板)144和内侧可动冲头(垫板)146。即,冲头140具有内侧可动冲头146作为第1冲头,具有外侧可动冲头144作为第2冲头,具有固定冲头142作为第3冲头。如图1所示,当本实施方式中的压制加工开始时,被加工件10为平板状。利用与形成于固定阴模122的凹部126的底部相连结的缓冲件128,以可动阴模124的上表面与被加工件10抵接的方式支承可动阴模124。另一方面,在冲头140中,内侧可动冲头146与被加工件10的中央部抵接,内侧可动冲头146在与可动阴模124的上表面之间夹持被加工件10。利用与固定冲头142相连结的缓冲件148和与内侧可动冲头146相连结的缓冲件150,将外侧可动冲头144支承在比内侧可动冲头146后退了预定的后退量(即,远离被加工件10以及阴模120)的位置。在压制加工开始后,当冲头140朝向凹部126的底面进行压制时(第1压制加工),首先,缓冲件128收缩,可动阴模124保持着在其与内侧可动冲头146之间夹持着被加工件10的中央部的状态被推入到凹部126中。在此时刻,缓冲件148、150不收缩,因此冲头140在维持着外侧可动冲头144比内侧可动冲头146后退的位置关系的状态下被推入凹部126。也就是说,外侧可动冲头144比内侧可动冲头146晚地被推入凹部126。如图2所示,在可动阴模124触碰到凹部126的底部的时刻,形成了u字形部分的大致形状,该u字形部分将以被夹持在可动阴模124与内侧可动冲头146之间的状态推入到凹部126的被加工件10的中央部设为顶板部14a(最终形成的顶板部14的中央区域),将随之折入到外侧可动冲头144与凹部126的侧面130之间的被加工件10的边缘部设为纵壁部12。这里,在本实施方式中,纵壁部12被约束在外侧可动冲头144与凹部126的侧面130之间。也就是说,在压制加工装置100中,外侧可动冲头144被设计成其与侧面130的间隔与被加工件10的板厚大致一致。另外,在被内侧可动冲头146推入的可动阴模124触碰到凹部126的底部的时刻,由于外侧可动冲头144比内侧可动冲头146晚地被推入凹部126,因此在顶板部14a与纵壁部12之间形成有锥形部16。如图3所示,当冲头140进一步继续压制时(第2压制加工),这次,缓冲件150收缩,外侧可动冲头144被进一步推入到凹部126中而追上内侧可动冲头146。此时,外侧可动冲头144在其与底面132之间夹入被加工件10(锥形部16),成形顶板部14b(顶板部的边缘区域)以及顶板部14与纵壁部12之间的角部18。这里,参照图2以及图3可清楚得知,在被加工件10的截面上,锥形部16的长度比顶板部的边缘区域14b与角部18相加后得到的长度长。因而,在压制加工装置100中,能以使角部18增厚,即,使角部18的板厚比纵壁部12、顶板部14的板厚厚的方式成形。如图4所示,作为附加性的工序,此后也可以使冲头140进一步朝向凹部126的底面132进行压制。在该情况下,缓冲件148收缩,固定冲头142被推入到凹部126中。固定冲头142与纵壁部12的端面19抵接,通过向外侧可动冲头144与侧面130之间推入纵壁部12,使角部18进一步增厚。另外,端面19是纵壁部12的端部中的、位于与角部18所在侧相反的那一侧的端部的面。在图中表示的例子中,固定冲头142推入纵壁部12,从而将外侧可动冲头144与侧面130、底面132之间填满,使角部18的外侧成形为大致直角。在这样对被加工件10进行加工的压制加工装置100中,将利用第1压制加工成形得到的锥形部16的长度加工为比顶板部的边缘区域14b与角部18相加后的长度长,从而将角部18成形为板厚比纵壁部12、顶板部14的板厚厚。因此,需要适当地设定用于规定锥形部16的长度的、对被加工件10的顶板部14的中央区域14a进行夹持的内侧可动冲头146的上表面的夹持宽度以及外侧可动冲头144在推入方向上自内侧可动冲头146后退的后退量。详细而言,为了将角部18成形为板厚比纵壁部12、顶板部14的板厚厚,使构成锥形部16的被加工件的量与为了将角部18形成为目标板厚所需要的被加工件的量相同或在为了将角部18形成为目标板厚所需要的被加工件的量以上即可。即,在使锥形部16的截面积与由锥形部16形成的包括角部18在内的部分(相当于后述的棱线部)的截面积相同或为该部分的截面积以上时,能使角部18为目标板厚以上。首先,以如下方式算出由锥形部16形成的包括角部18在内的部分的截面积。为了进行该说明,在图5中表示图3所示的第2压制加工后的被加工件10的一个例子。图5是用于说明第2压制加工后的被加工件10的形状所涉及的尺寸的图。如图5所示,第2压制加工后的被加工件10包括纵壁部12、顶板部14和角部18。将该被加工件10设定为在所有的位置均为板厚t。另外,将角部18的内侧的曲率半径设定为rp,将角部18的外侧的曲率半径设定为rp+t。并且,设定包括角部18在内、共有被加工件10的纵壁部12的外侧和顶板部14的外侧的正方形的区域s。区域s的一边的长度设为板厚t与曲率半径rp的和。即,1/4个半径为rp+t的圆以及1/4个半径为rp的圆包含于区域s内。以下,也将被加工件10中的区域s内的部分称为棱线部。图5所示的棱线部的截面积sa用下述式子(1)表示。式子(1)的棱线部的截面积sa表示1个棱线部的截面积,例如若是图5,则表示左右任一棱线部的截面积。[算式3]另外,在将角部18的外侧设为直角的情况下,被加工件10的棱线部的截面积sb用下述式子(2)表示。[算式4]另一方面,如图2所示,在将锥形部16在推入方向上的长度设定为h1,将锥形部16在宽度方向上的长度设定为w1时,锥形部16的截面积st用下述式子(3)表示。用下述式子(3)表示的锥形部16的截面积st也表示1个锥形部16的截面积,例如若是图2,则表示左右任一锥形部16的截面积。[算式5]根据以上说明,锥形部16的截面积st只要至少为由所述式子(1)表示的截面积sa以上,就不会使角部18的板厚相对于被加工件10的板厚减薄。另外,为了使角部18的外侧为大致直角,使锥形部16的截面积st与由所述式子(2)表示的截面积sb相等即可。这样,依据角部18的目标板厚设定锥形部16的截面积st即可。在压制加工装置100中,规定锥形部16的截面积st的、锥形部16在推入方向上的长度h1对应于压制加工装置100的外侧可动冲头144在推入方向上自内侧可动冲头146后退的后退量。另外,规定锥形部16的截面积st的、锥形部16在宽度方向上的长度w1对应于固定阴模122的凹部126的宽度与内侧可动冲头146的上表面的宽度之差的1/2。内侧可动冲头146的上表面的宽度为夹持顶板部14的中央区域14a的夹持宽度。固定阴模122的凹部126的宽度被确定为成形品的尺寸,因此根据内侧可动冲头146的上表面的宽度调整锥形部16的宽度方向的长度w1。因而,通过调整压制加工装置100的外侧可动冲头144在推入方向上自内侧可动冲头146后退的后退量和内侧可动冲头146的上表面的宽度(即,夹持宽度),能使锥形部16的截面积st达到预定的大小。于是,根据角部18的目标板厚确定锥形部16的截面积st,将压制加工装置100以能获得具有确定好的截面积st的锥形部16的方式构成,从而能够获得角部18被增厚了的成形品。(1-2.成形品的特征)图6a以及图6b是用于说明利用本发明的第1实施方式的压制加工装置成形得到的成形品的截面上的角部的形状的例子的图。图6a是将角部18成形为板厚比纵壁部12以及顶板部14的板厚厚的例子。图6b是将角部18的外侧成形为大致直角的例子。如上所述,在现有技术中,通过增大角部的外侧的曲率半径,使材料在纵壁部与顶板部之间流动,使截面的u字形部分的整体增厚。在该情况下,当角部的外侧的曲率半径较小时,材料的流动受到阻碍,从而产生折入等缺陷。相对于此,在本实施方式中,在成形了纵壁部12以及顶板部14的中央区域后,使外侧可动冲头144将锥形部16压扁,从而成形角部18,因此不发生纵壁部12与顶板部14之间的材料的流动,因而,能够减小角部18的外侧的曲率半径,或者能使角部18的外侧形成为大致直角。如上所述,在图6a所示的例子中,将被加工件10的角部18成形为板厚比纵壁部12以及顶板部14的板厚厚。也就是说,在本例中,角部18被增厚。在该情况下,在被加工件10的截面上,角部18的外侧的曲率半径r2比纵壁部12以及顶板部14的板厚t与内侧的曲率半径r1相加后得到的值小(r2<r1+t)。也能够如图示的例子那样使外侧曲率半径r2比内侧的曲率半径r1小(r2<r1)。另外,在角部18为与纵壁部12以及顶板部14相同的板厚的情况下,r2=r1+t。另外,在角部18的板厚比纵壁部12以及顶板部14的板厚小的情况下,r2>r1+t。因而,使角部18增厚等价于使角部18的外侧的曲率半径r2比板厚t与内侧的曲率半径r1相加后得到的值小。作为具体的例子,在被加工件10的纵壁部12以及顶板部14的板厚t为5mm的情况下,将角部18的外侧的曲率半径r2设为0.5mm(板厚t的10%),将内侧的曲率半径r1设为7.5mm(板厚t的1.5倍),能够不产生缺陷地实施压制加工。另外,也能够如图6b所示的例子那样使角部18的外侧为直角,因此曲率半径r2也可以比0.5mm小。另外,虽然在与所述那样的现有技术之间的关系上,本实施方式的有利性在减小了曲率半径r2的情况下较明显,但角部18的外侧的曲率半径r2较大并不阻碍本实施方式的应用,因此曲率半径r2也可以比0.5mm大。关于角部18的内侧的曲率半径r1,若相对于曲率半径r2而言过大,则可能产生由材料的折入等导致的缺陷,但至少在曲率半径r1相对于板厚t而言处于所述的例子那样的范围内的情况下,能够不产生缺陷地实施压制加工。另一方面,在图6b所示的例子中,在被加工件10的截面上,角部18的外侧成形为大致直角。另外,在本说明书中,“角部18的外侧为大致直角”的情况不仅包括角部18的外侧严格地为直角的情况,也包括角部18的外侧的曲率半径无限小而接近于0的情况。在该情况下,也能够将角部18的内侧成形为大致直角,但从避免应力向角部18集中的观点出发,期望的是,使角部18的内侧具有一定程度的(并不那么接近于0的)曲率半径r1。在该情况下,可理解为:角部18的外侧的曲率半径比板厚t与内侧的曲率半径r1相加后得到的值小。因而,在图6b所示的例子中,也可以说角部18实现了增厚。另外,利用本实施方式的压制加工装置成形得到的被加工件的角部比其他部分硬。作为一个例子,在图7以及图8中表示使用本实施方式的压制加工装置对270mpa级钢板进行了压制加工时的、对纵壁部、角部以及顶板部的硬度分布进行测量而得到的结果。图7是表示利用压制加工而成形得到的被加工件的角部以及顶板部的一部分的塑性应变分布的图。图8是表示图7所示的被加工件的硬度分布的图表。在图8中,对在厚度方向上距被加工件的外表面200μm的位置的硬度分别从角部朝向纵壁部以及顶板部侧每隔1mm地进行了测量。用维氏硬度表示硬度,硬度的值越大,则越硬。另外,测量距离w以角部的位置为原点,用正的值表示顶板部方向,用负的值表示纵壁部方向。本例的被加工件的压制加工前的厚度为1.6mm,硬度(以下也称为“原料硬度”。)hv0为85。利用第1压制加工形成的锥形部的宽度方向的长度为10mm,推入方向的长度为10mm。并且,在利用第2压制加工成形了角部以及顶板部的边缘区域之后,对在厚度方向上距被加工件的外表面200μm的位置的硬度分别从角部朝向纵壁部以及顶板部侧每隔1mm地进行了测量。根据图7所示的塑性应变分布可知,在角部以及顶板部的一部分,应力增大。另外,当观察被加工件的硬度分布时,如图8所示,表示角部的原点位置的硬度比其他部分高。另外,自原点位置朝向顶板部侧去,硬度降低,但在测量距离为约10mm的位置,硬度再次升高。这样,利用本实施方式的压制加工装置成形得到的被加工件在角部和顶板部的与角部分开了预定的距离的位置处比原料硬度硬。考虑是在这些位置,塑性应变增大,因此加工硬化加大。如图8所示,在本例中,原料硬度hv0为85,相对于此,角部(测量距离w=0)处的硬度为212,是原料硬度hv0的约2.5倍。另外,顶板部的与角部分开了10mm的位置(测量距离w=10mm)处的硬度为127,是原料硬度hv0的约1.5倍。这样,在角部和顶板部的与角部分开了预定的距离的位置处,硬度变高。另外,角部的硬度比顶板部的与角部分开了预定的距离的位置处的硬度高。这里,顶板部的与角部分开了预定的距离的位置对应于顶板部的边缘区域与中央区域之间的交界部分。更详细而言,对应于与通过第1压制加工在阴模的凹部中由内侧可动冲头夹持的部分相邻的、锥形部的顶板部侧端部区域。顶板部的中央区域通过第1压制加工而被夹持,因此大致维持原料硬度hv0的硬度,但锥形部的顶板部侧端部区域并未通过第1压制加工而被夹持。因此,考虑是利用在第1压制加工后进行的第2压制加工使锥形部的顶板部侧端部区域发生了加工硬化。因而,利用本实施方式的压制加工装置成形得到的被加工件具有图8所示那样的硬度分布。作为比较,例如当利用1次的压制加工成形角部时,应力集中施加于角部,只在角部产生塑性应变。另一方面,当如本实施方式的压制加工装置那样利用多级的压制加工成形角部时,通过第1压制加工,顶板部的中央区域能够大致维持原料硬度hv0的硬度,此外使第1压制加工后的第2压制加工中的载荷易于分散到在第1压制加工中成形得到的锥形部整体。因此,能够抑制应力集中于由锥形部成形得到的角部,也能减小由锥形部成形角部以及顶板部的边缘区域时的载荷。另外,本例的被加工件为270mpa级钢板,是加工硬化能力大的软钢,但即使是例如高张力钢板等加工硬化能力小的钢板,在角部和顶板部的与角部分开了预定的距离的位置处,也同样体现出硬度变高这一倾向。在该情况下,与本例那样的软钢相比,锥形部以及顶板部的与角部分开了预定的距离的位置处的硬度的上升率降低。详细而言,角部处的硬度为原料硬度hv0的1.5倍左右,顶板部的与角部分开了预定的距离的位置处的硬度为原料硬度hv0的1.1倍左右。图9a以及图9b是表示本实施方式中的成形品的例子的图。图9a的例子所示的长条状的成形品50具有槽形形状52。槽形形状52包括纵壁部54和顶板部56。在本例中,图3、图4所示那样的被加工件10的截面(含有u字形部分)对应于图9a所示的成形品50的a-a截面。另外,在本例的情况下,在压制加工装置100中,形成于阴模120的凹部126形成槽,使用阴模120和冲头140对被加工件10实施弯曲成形。另一方面,图9b的例子所示的轴对称形状的成形品60具有杯状62。杯状62包括纵壁部64和顶板部66。在本例中,图3、图4所示那样的被加工件10的截面(含有u字形部分)对应于图9b所示的成形品60的b-b截面。另外,在本例的情况下,在压制加工装置100中,形成于阴模120的凹部126形成孔,使用阴模120和冲头140对被加工件10实施拉深成形。上述说明了的成形品50、60均是通过压制加工而成形得到的、在截面含有u字形部分的成形品。在这些成形品中,例如如上述说明了的那样,能看到u字形部分的角部实现了增厚或者角部的外侧为大致直角的特征。另外,详见后述,特别是在成形品具有杯状的情况下,有时在截面的u字形部分的成形工序中,角部发生壁厚减小。在这种情况下,在应用本实施方式抑制了壁厚减小的情况下,成形品的角部的外侧的曲率半径也可能与将板厚与内侧的曲率半径相加后得到的值相等,或者比该值小。(1-3.变形例)图10以及图11是表示本发明的第1实施方式的变形例的压制加工装置的动作的概略性的剖视图。在本变形例中,利用与上述参照图1和图2说明了的工序同样的工序,成形构成被加工件10的截面的u字形部分的纵壁部12以及顶板部14a(该工序已做说明,因此省略图示)。接着,使冲头140朝向底面132进一步压制,使缓冲件150收缩,从而外侧可动冲头144被进一步推入到凹部126中。此时,外侧可动冲头144追赶已经在其与底面132之间夹持着顶板部14a的内侧可动冲头146,但在本变形例中,如图10所示,在外侧可动冲头144追上内侧可动冲头146之前,使被加工件10的锥形部16扩张而形成的角部18的外侧与凹部126的侧面130以及底面132紧密接触,成为大致直角。此后,当冲头140朝向底面132进一步进行压制时,角部18的内侧被外侧可动冲头144扩张,从而纵壁部12被向上方推出。此时,固定冲头142被纵壁部12的端面19上推而相对于外侧可动冲头144后退。也就是说,在本变形例中,固定冲头142相对于端面19进行与所述的图4所示的例子相反的动作。结果,如图11所示,沿外侧可动冲头144成形了角部18的内侧,被加工件10的成形完成。在本变形例中,例如通过压制加工开始时的外侧可动冲头144与内侧可动冲头146的位置之差(缓冲件150的初始长度)的设定来调节锥形部16的长度,不像所述图4所示的例子那样实施由固定冲头142进行的附加的压制,而将角部18的外侧成形为大致直角。在该情况下,在由外侧可动冲头144进行的压制的过程中,纵壁部12可能被在角部18多余的材料上推。在那种情况下,如所述说明的那样,一边用固定冲头142按压端面19一边允许纵壁部12的上升,从而能够精度良好地成形端面19。图12是用于说明利用本实施方式的另一变形例的压制加工装置成形得到的成形品的截面形状的例子的图。在图12所示的例子中,使外侧可动冲头144的下表面具有朝向冲头140的外侧的锥形,从而使利用外侧可动冲头144成形得到的被加工件10的顶板部14的除中央区域ra以外的区域rb自中央区域ra朝向角部18逐渐增厚。在该情况下,顶板部14与角部18之间的板厚的变化平缓,从而能够缓和应力向角部18的集中。(1-4.总结)在以上说明了的本发明的第1实施方式中,在使用了压制加工装置100的被加工件10的压制加工中,外侧可动冲头144比内侧可动冲头146晚地被推入到凹部126中,从而在纵壁部12与顶板部14a之间形成有锥形部16。锥形部16的长度比最终形成的顶板部的边缘区域14b以及角部18相加后得到的长度长,因此通过使锥形部16扩张而成形角部18,从而即使不使材料在纵壁部12与顶板部14之间流动,也能使角部18增厚。因此,在本实施方式中,与现有技术相比,能够减小角部18的外侧的曲率半径,或者能使角部18的外侧为大致直角。另外,也能不使纵壁部12以及顶板部14增厚而只使角部18增厚。在本实施方式的压制加工装置100中,在推入冲头140的一系列的压制工序中,利用缓冲件150的作用将外侧可动冲头144比内侧可动冲头146晚地推入到凹部126中,由此能够进行角部18的自如的成形。因而,压制加工装置100为单轴即可,不需要使冲头的多个部分彼此独立地进行压制的多轴的压制加工装置。另外,在上述的例子中,如图1所示,从被加工件10为平板状的状态开始进行压制加工,但本实施方式不限定于这种例子。例如也可以利用其他装置实施成形用于形成被加工件10的u字形部分的纵壁部12以及顶板部14a(中央区域)的工序来作为一次成形,利用压制加工装置100例如如上述图2所示地从被加工件10的截面的u字形部分被容纳到凹部126中的状态开始进行压制加工,来作为接着上述一次成形的二次成形。在这种情况下,也可以不必设置可动阴模124。另外,本实施方式也能应用在用于获得如下成形品的压制加工中,即,截面具有还含有与纵壁部12的端部(与角部18所在侧相反的那一侧的端部)连续的凸缘部在内的帽状部分的成形品。(1-5.补充:使角部的外侧具有曲率的情况)作为本发明的第1实施方式的另一变形例,例如也可以在形成于阴模的凹部中,在侧面与底面之间形成角面。通过沿该角面成形被加工件,能将纵壁部与顶板部之间的角部的外侧精度良好地加工成具有曲率的形状。以下,说明使角部的外侧具有曲率的情况下的压制成形加工。另外,除此以外的方面与第1实施方式相同,因此省略重复的说明。图13~图15是将本发明的第1实施方式的另一变形例的压制加工装置的结构与压制加工时的动作一起表示的概略性的剖视图。参照图13~图15,压制加工装置200包括阴模220和冲头140。阴模220包括固定阴模222和可动阴模(垫板)224。另外,冲头140的结构与所述的第1实施方式相同。如图13所示,在本实施方式中的压制加工开始时,被加工件20为平板状。利用与形成于固定阴模222的凹部226的底部相连结的缓冲件228,将可动阴模224支承为该可动阴模224的上表面与被加工件20抵接。另一方面,在冲头140中,与所述的第1实施方式相同,内侧可动冲头146与被加工件20的中央部抵接,并在内侧可动冲头146与可动阴模224的上表面之间夹持被加工件20。另外,将外侧可动冲头144支承在比内侧可动冲头146后退了的位置。在压制加工开始后,当冲头140朝向凹部126的底面进行压制时,首先,缓冲件228收缩,可动阴模224在保持着在其与内侧可动冲头146之间夹持着被加工件20的中央部的状态下被推入到凹部226中。与第1实施方式相同,冲头140在维持着外侧可动冲头144比内侧可动冲头146后退的位置关系的状态下被推入凹部126。因而,外侧可动冲头144比内侧可动冲头146晚地被推入凹部226。如图14所示,在可动阴模224触碰到凹部226的底部的时刻,形成了u字形部分的大致形状,该u字形部分将以被夹持在可动阴模224与内侧可动冲头146之间的状态推入到凹部226的被加工件20的中央部设为顶板部24a(最终形成的顶板部24的中央区域),将随之折入到外侧可动冲头144与凹部226的侧面230之间的被加工件20的边缘部设为纵壁部22。这里,作为与第1实施方式的不同之处,在本实施方式中,在凹部226的底面232与侧面230之间夹设有具有曲率的角面234。底面232由触碰到底部的可动阴模224形成,侧面230以及角面234由固定阴模222形成。因而,在本实施方式中,可动阴模224的外尺寸比凹部226的内尺寸小了与角面234相应的量。在本实施方式中也是外侧可动冲头144比内侧可动冲头146晚地被推入凹部126,从而形成锥形部26,但锥形部26未与角面234接触。如图15所示,当冲头140进一步继续进行压制时,这次,缓冲件150收缩,外侧可动冲头144被进一步推入到凹部226中而追上内侧可动冲头146。此时,在外侧可动冲头144与底面232以及角面234之间夹入被加工件20(锥形部26),成形顶板部24b(顶板部的边缘区域)以及角部28。沿外侧可动冲头144成形角部28的内侧,沿凹部226的角面234成形角部28的外侧。角面234是具有曲率的面,因此角部28的外侧也成形为具有曲率的形状。在本实施方式中,参照图14以及图15可清楚得知,在被加工件20的截面,锥形部26的长度也比顶板部24b与角部28相加后得到的长度长。因而,在压制加工装置200中,与第1实施方式相同,能使角部28增厚。在该情况下,如已述的那样,在被加工件20的截面,角部28的外侧的曲率半径r2比纵壁部22以及顶板部24的板厚t与内侧的曲率半径r1相加后得到的值小(r2<r1+t)。也能够使外侧曲率半径r2比内侧的曲率半径r1小(r2<r1)。另外,在本实施方式中,与第1实施方式相同,在抑制了角部28的壁厚减小的情况下,角部28的曲率半径也可能为r2≥r1+t。另外,除了如上所述那样成形为在截面上、角部的外侧具有曲率的形状以外,利用本实施方式的压制加工装置200成形得到的成形品具有与所述的第1实施方式中的成形品同样的特征。也就是说,在本实施方式的成形品中,与例如在第1实施方式中图6a所示的例子同样,也能看到角部增厚了的特征。此时,纵壁部以及顶板部也可以不必一定增厚。或者,在本实施方式的成形品中,能看到在现有技术中发生的角部的壁厚减小得到抑制的特征。另外,本实施方式中的成形品的形状既可以为例如在所述的第1实施方式中图9a所示那样的长条状(u字形部分形成槽形形状),也可以为轴对称形状(u字形部分形成杯状)。另外,与第1实施方式相同,本实施方式也能应用在用于获得如下成形品的压制加工中,即,截面具有还含有与纵壁部22的端部连续的凸缘部在内的帽状部分的成形品。在以上说明了的本发明的第1实施方式的另一变形例中,与第1实施方式相同,在使用了压制加工装置200的被加工件20的压制加工中,外侧可动冲头144比内侧可动冲头146晚地被推入到凹部226中,从而形成锥形部26。锥形部26的长度比最终形成的顶板部24b以及角部28相加后得到的长度长,因此通过使锥形部26扩张而成形角部18,从而即使不使材料在纵壁部22与顶板部24之间流动,也能使角部28增厚。在本实施方式中,在凹部226形成有角面234,从而能将角部28的外侧稳定地成形为具有曲率的形状,但由于不需要如所述那样地使材料在纵壁部22与顶板部24之间流动,因此能使由角面234规定的角部28的外侧的曲率半径比例如现有技术中的角部小。另外,在本实施方式中,与第1实施方式相同,压制加工装置200为单轴即可。另外,与第1实施方式相同,在本实施方式中,也可以不必一定如图13所示地从被加工件20为平板状的状态开始进行利用压制加工装置200的压制加工,例如也可以利用其他的装置实施被加工件20的一次成形。在该情况下,在压制加工装置200中,作为二次成形,如图14所示,从被加工件20的截面的u字形部分被容纳在凹部226中的状态开始进行压制加工。在这种情况下,压制加工装置200也可以不设置可动阴模224。(2.第2实施方式:深拉深成形)接下来,说明本发明的第2实施方式。在本实施方式中,实施了用于获得包含由截面的u字形部分形成的杯状在内的轴对称形状的成形品的所谓深拉深成形。在以下的说明中,一边与基于现有技术的深拉深成形进行比较,一边说明根据本实施方式的深拉深成形及其优点。另外,如上所述,所述的第1实施方式也能应用在用于获得包含杯状在内的轴对称形状的成形品的深拉深成形中。也就是说,即使没有另外的说明,在本实施方式的深拉深成形中也能采用与第1实施方式同样的结构。同样,在将第1实施方式应用于深拉深成形的情况下,也能采用与本实施方式同样的结构。图16以及图17是将现有技术的压制加工装置的结构与深拉深成形时的动作一起表示的概略性的剖视图。参照图16以及图17,用于实施被加工件90的深拉深成形的压制加工装置900包括阴模920、冲头940和压料圈960。阴模920包括固定阴模922和借助缓冲件928连结于固定阴模922的可动阴模(垫板)924。冲头940与本实施方式不同,是单一的块体。当冲头940自图16所示的状态开始压制时,平板状的被加工件90被推入到形成于固定阴模922的凹部926。由此,如图17所示,成形出截面的u字形部分。此时,压料圈960在其与固定阴模922的上表面之间约束被加工件90的边缘部分,抑制褶皱的产生。在现有技术的情况下,纵壁部92与顶板部94之间的角部98被冲头940的肩部952单纯地折弯,因此,由于外侧与内侧的周长差而使角部98的板厚比纵壁部92、顶板部94小(角部98发生了壁厚减小)。例如当在截面上减小了角部98的内侧的曲率半径的情况下,这种壁厚减小明显。在角部98有时反倒需要高于纵壁部92、顶板部94的强度,因此通常不希望在角部98发生壁厚减小。在本实施方式的深拉深成形中,改善了所述那样的现有技术中的角部的壁厚减小的问题。图18~图20是将本发明的第2实施方式的压制加工装置的结构与压制加工(深拉深成形)时的动作一起表示的概略性的剖视图。参照图18~图20,压制加工装置300包括阴模120、冲头340和压料圈360。冲头340包括固定冲头344和可动冲头(垫板)346。另外,阴模120的结构与所述的第1实施方式相同。如图18所示,在本实施方式中的压制加工开始时,被加工件30为平板状。与第1实施方式相同,将可动阴模124支承为上表面与被加工件30抵接。另一方面,冲头340的可动冲头346与被加工件30的中央部抵接,在可动冲头346与可动阴模124的上表面之间夹持被加工件30。在固定冲头344与可动冲头346之间夹设有缓冲件350,维持固定冲头344比可动冲头346后退了的位置关系。在压制加工开始后,当冲头340朝向凹部126的底面进行压制时,首先,缓冲件128收缩,可动阴模124被推入到凹部126中。在该时刻,缓冲件350不收缩,因此冲头340在维持着固定冲头344比可动冲头346后退了的位置关系的状态下被推入凹部126。也就是说,固定冲头344比可动冲头346晚地被推入凹部126。此时,压料圈360在其与固定阴模122的上表面之间约束被加工件30的边缘部分,抑制褶皱的产生。另外,也可以是,例如在利用所述的第1实施方式的结构实施深拉深成形时,同样也设置这种压料圈。如图19所示,在可动阴模124触碰到凹部126的底部的时刻,形成了u字形部分的大致形状,该u字形部分将以被夹持在可动阴模124与可动冲头346之间的状态推入凹部126的被加工件30的中央部设为顶板部34a(最终形成的顶板部34的中央区域),将随之折入到固定冲头344与凹部126的侧面130之间的被加工件30的边缘部设为纵壁部32。在该时刻,由于固定冲头344比可动冲头346晚地被推入到凹部126中,因此在顶板部34a与纵壁部32之间形成有锥形部36。如图20所示,当冲头340进一步继续压制时,这次,缓冲件350收缩,固定冲头344被进一步推入到凹部126中而追上可动冲头346。此时,固定冲头344以在其与凹部126的底面132之间夹入被加工件30(锥形部36)、成形顶板部34b(顶板部的边缘区域)以及角部38的方式进行压制。参照图19以及图20可清楚得知,在被加工件30的截面上,锥形部36的长度比顶板部34b与角部38相加后得到的长度长。因而,在压制加工装置300中,能够抑制角部38的壁厚减小,以适当的板厚成形角部38。作为具体的例子,在本实施方式中,在被加工件30的纵壁部32以及顶板部34的板厚为2mm的情况下,能够使用压制加工装置300以将角部38的板厚维持为2mm的方式实施深拉深成形。另外,在相同的情况下,在利用现有技术进行的深拉深成形中,角部的板厚减薄至1.57mm。在以上说明的本发明的第2实施方式中,在使用了压制加工装置300的被加工件30的深拉深成形中,固定冲头344比可动冲头346晚地被推入到凹部126中,从而在纵壁部32与顶板部34a之间形成有锥形部36。与第1实施方式相同,通过使锥形部36扩张而成形角部38,能够抑制角部38的壁厚减小。另外,在本实施方式中,也与第1实施方式相同,压制加工装置300为单轴即可。另外,与第1实施方式相同,在本实施方式中,也可以不必一定如图18所示地从被加工件30为平板状的状态开始进行基于压制加工装置300的压制加工,例如也可以利用其他的装置实施被加工件30的一次成形。在该情况下,在压制加工装置300中,作为二次成形,如图19所示,从被加工件30的截面的u字形部分被容纳于凹部126的状态开始进行压制加工。在这种情况下,压制加工装置300也可以不设置可动阴模124、压料圈360。另外,在第1实施方式中,夹持顶板部的中央区域的第1冲头和一边约束纵壁部一边成形顶板部的边缘区域以及角部的第2冲头均设置为可动冲头,但在本实施方式中,第2冲头成为固定冲头。另外,在本实施方式中,未设置如第1实施方式那样与纵壁部的端面抵接的第3冲头。在第1实施方式中,同样也能够是不设置第3冲头并且将第2冲头设为固定冲头的结构。另外,将本实施方式作为抑制深拉深成形中的角部的壁厚减小的结构而进行了说明,但同样的角部的壁厚减小也会发生在用于获得长条状的成形品的弯曲成形中。因而,为了在弯曲成形中也抑制角部的壁厚减小(即,角部不必一定增厚),也可以采用本实施方式的结构。(3.第3实施方式:纵壁部的增厚)接下来,说明本发明的第3实施方式。在本实施方式中,追加了附加成形工序,在该附加成形工序中,对利用上述的第1实施方式或第2实施方式(以下也简称为“上述的实施方式”。)中的任一种方法成形得到的成形品进行进一步压制加工,成形纵壁部的壁厚比顶板部的壁厚厚的成形品。使用由上述的实施方式成形得到的成形品压制成形纵壁部实现了增厚的成形品,从而内部的角面不会重合而能使纵壁部增厚。以下,以使用由上述的实施方式成形得到的成形品为前提,说明使纵壁部增厚的附加成形工序。图21是表示利用本实施方式的压制加工成形得到的成形品70a的一个例子的说明图。图21所示的成形品70a包括纵壁部74和顶板部76,是具有由纵壁部74和顶板部76形成的凹部72的杯状的成形品。例如利用以下说明的第2压制加工装置,对图9b所示的在截面含有角部的外侧的曲率半径较小或大致直角的u字形部分在内的杯状的成形品60进一步进行压制加工,从而成形得到该成形品70a。在图22以及图23中表示作为本实施方式的第2压制加工装置的用于使纵壁部74增厚的压制加工装置400的结构。图22是表示使纵壁部增厚的压制加工的初始状态的概略性的剖视图。图23是表示纵壁部的增厚后的状态的概略性的剖视图。参照图22以及图23,压制加工装置400包括阴模420和冲头440。阴模420为固定阴模。冲头440包括固定冲头442和可动冲头(垫板)444。如图22所示,在本实施方式中的压制加工开始时,被加工件40为利用上述的任一实施方式成形得到的成形品,角部的外侧的曲率半径较小,或者为大致直角。例如,被加工件40是图9b所示的杯状的成形品60,在该情况下,利用压制加工装置400成形图21所示的纵壁部74实现了增厚的杯状的成形品70a。另外,本发明不限定于此例,也能利用压制加工装置400同样实施如下加工,即,例如从图9a所示的具有槽形形状的长条状的成形品50获得纵壁部实现了增厚的具有槽形形状的长条状的成形品。阴模420具有收纳被加工件40的凹部430。凹部430的形状与利用被加工件40制造的成形品的形状对应地形成。因而,将凹部430在与被加工件40的纵壁部42相对的方向上的长度形成为比与凹部430相对的纵壁部42的外表面之间的长度长。被加工件40以在收纳在凹部430中的状态下在被加工件40的纵壁部42的外部侧存在通过该压制加工实现增厚的量的空间的方式使杯状的开口侧朝向冲头440侧地配置于凹部430。另一方面,冲头440的可动冲头444具有与被加工件40的杯状相对应的形状。可动冲头444自被加工件40的开口插入,并配置为其下表面以及侧面与被加工件40的杯状的内表面(即,底面432以及侧面434)相接触。此时,可动冲头444利用与固定冲头442相连结的缓冲件446按压被加工件40,在可动冲头444与阴模420的凹部430的底面432之间夹持被加工件40的顶板部44。另外,固定冲头442与被加工件40的纵壁部42的端面49抵接。当开始由压制加工装置400进行的压制加工时,如图23所示,设在固定冲头442与可动冲头444之间的缓冲件446收缩,固定冲头442朝向凹部430的底面432移动。由此,构成被加工件40的纵壁部42的材料向存在于该材料与阴模420的凹部430之间的空间流动,填满该空间。这样,如图23所示,使被加工件40的纵壁部42的壁厚比压制加工前增厚,并且能使压制加工后的角部48的外侧的曲率半径与压制加工前同样地较小、或者成为大致直角。这里,利用压制加工装置400对利用上述的实施方式成形得到的角部的外侧的曲率半径较小或大致直角的成形品进行压制加工,从而获得利用本实施方式成形得到的成形品。若被加工件的角部的外侧的曲率半径较大、角部的板厚较薄,则在利用压制加工装置400按压了纵壁部的端部时,纵壁部以及顶板部的材料流动,在角部的内部产生折入等缺陷。折入部分是纵壁部与顶板部的内表面彼此接触而重叠的部分,纵壁部与顶板部之间的重叠容易解开,因此比其他部分的强度低。另外,折入部分也成为疲劳破坏的主要原因。相对于此,在如本实施方式那样将在截面含有角部的外侧的曲率半径较小或大致直角的u字形部分在内的成形品用作被加工件的情况下,在利用凹部430的底面432和可动冲头444的下表面夹持着被加工件40的顶板部44的状态下,角部48的材料流动而将凹部430的底面432以及侧面434之间填满。因而,不会在角部48的内部产生折入,并且能使角部48的外侧的曲率半径与压制加工前同样地较小、或者成为大致直角。在以上说明的本发明的第3实施方式中,在使用了压制加工装置400的被加工件40的压制加工中,作为被加工件40,使用在上述的实施方式中成形得到的在截面含有角部的外侧的曲率半径较小或者大致直角的u字形部分在内的成形品。并且,利用压制加工装置400在夹持着被加工件40的顶板部44的状态下对纵壁部42的端面49施加载荷,从而即使不使材料在纵壁部42与顶板部44之间流动也能使纵壁部42增厚,并且能使角部48的外侧的曲率半径比现有技术小,或者使角部48的外侧成为大致直角,因此也能使成形后的角部48增厚。(4.第4实施方式:纵壁部的推出)接下来,说明本发明的第4实施方式。在本实施方式中,追加了附加成形工序,在该附加成形工序中,进一步对利用上述的第1实施方式或第2实施方式中的任一种方法成形得到的成形品进行压制加工,成形相对于顶板部将纵壁部延伸设置后形成的成形品。使用由上述的实施方式成形得到的成形品对相对于顶板部将纵壁部延伸设置后形成的成形品进行压制成形,从而能够使内部的角面不会重合而将纵壁部推出,延伸设置纵壁部。以下,以使用由上述的实施方式成形得到的成形品为前提,说明将纵壁部延伸设置的附加成形工序。图24是表示利用本实施方式的压制加工成形得到的成形品70b的一个例子的说明图。图24所示的成形品70b包括纵壁部74、顶板部76和纵壁延伸设置部78,是具有由纵壁部74和顶板部76形成的凹部72的杯状的成形品。也是利用以下说明的第2压制加工装置,进一步压制加工例如图9b所示的在截面含有角部的外侧的曲率半径较小或大致直角的u字形部分在内的杯状的成形品60,从而成形该成形品70b。在图25以及图26中表示作为本实施方式的第2压制加工装置的、用于延伸设置纵壁部74的压制加工装置500的结构。图25是表示使纵壁部延伸设置的压制加工的初始状态的概略性的剖视图。图26是表示纵壁部的延伸设置后的状态的概略性的剖视图。参照图25以及图26,压制加工装置500包括阴模520和冲头540。阴模520包括纵壁固定阴模522、顶板固定阴模523和可动阴模(垫板)524。冲头540包括固定冲头542和可动冲头(垫板)544。如图25所示,在本实施方式中的压制加工开始时,与第3实施方式相同,被加工件40是利用第1实施方式或第2实施方式中的任一种方法成形得到的成形品,角部的外侧的曲率半径较小,或者成为大致直角。例如,被加工件40是图9b所示的杯状的成形品60,在该情况下,利用压制加工装置500成形图24所示的将纵壁部74延伸设置后形成的杯状的成形品70b。另外,本发明不限定于此例,也能利用压制加工装置500同样地实施如下加工,即,自例如图9a所示的具有槽形形状的长条状的成形品50获得具有将纵壁部延伸设置后形成的槽形形状的长条状的成形品。阴模520利用纵壁固定阴模522、顶板固定阴模523以及可动阴模524形成用于收纳被加工件40的凹部。纵壁固定阴模522支承被加工件40的纵壁部42,顶板固定阴模523以及可动阴模524支承被加工件40的顶板部44。顶板固定阴模523的内表面如图24所示,包括能与被加工件40的顶板部44接触的中央区域(除两侧的纵壁部42延伸设置的部分以外的区域)523a和比该中央区域523a向冲头540的相反侧凹陷的端部区域523b。当在顶板固定阴模523的两侧配置纵壁固定阴模522时,在端部区域523b形成空间。可动阴模524在被与顶板固定阴模523的端部区域523b相连结的缓冲件526支承的状态下配置在该空间内。在将被加工件40配置到阴模520的凹部中时,利用被加工件40的顶板部44将可动阴模524推入至顶板部44与顶板固定阴模523的内表面的中央区域523a抵接的位置。另一方面,冲头540的可动冲头544具有与被加工件40的杯状相对应的形状。可动冲头544自被加工件40的开口插入,配置为其下表面以及侧面与被加工件40的杯状的内表面(即,底面以及侧面)接触。此时,利用缓冲件546而与固定冲头542相连结的可动冲头544按压被加工件40,在可动冲头544与顶板固定阴模523之间夹持被加工件40的顶板部44。另外,固定冲头542与被加工件40的纵壁部42的端面49抵接。在初始状态下,即使固定冲头542与被加工件40的纵壁部42的端面49抵接,被加工件40也不会变形。当开始由压制加工装置500进行的压制加工时,如图26所示,设在固定冲头542与可动冲头544之间的缓冲件546收缩,固定冲头542朝向凹部的底面进行移动。由此,构成被加工件40的纵壁部42的材料推入可动阴模524,以一边使缓冲件546收缩一边代替可动阴模524地将纵壁固定阴模522与顶板固定阴模523的中央区域之间的空间填满的方式进行移动。这样,如图26所示,与压制加工前相比,能够使被加工件40的纵壁部42延伸设置。此时,压制加工后的被加工件40具有:凹部内的第1内角部48a;和第2内角部48b,该第2内角部48b由顶板部44和将纵壁部42延伸设置后形成的纵壁延伸设置部46形成。与第3实施方式相同,也能利用压制加工装置500,压制加工利用上述的第1实施方式或第2实施方式中的任一者成形得到的角部的外侧的曲率半径较小或大致直角的成形品,从而获得利用本实施方式成形得到的成形品。若假设被加工件的角部的外侧的曲率半径较大、角部的板厚较薄,则在利用压制加工装置500按压了纵壁部的端部时,纵壁部以及顶板部的材料流动,在第1内角部48a产生折入等缺陷。折入部分比其他部分的强度低,也成为疲劳破坏的主要原因。相对于此,在如本实施方式那样将在截面含有角部的外侧的曲率半径较小或大致直角的u字形部分在内的成形品用作被加工件的情况下,在利用凹部的底面和可动冲头544的下表面夹持着被加工件40的顶板部44的状态下,角部48的材料一边下推可动阴模524一边流动。因而,不会在角部48的内部产生折入。另外,第2内角部48b与第1内角部48a同样,从避免应力向角部48集中的观点出发,期望的是,使角部48的内侧具有一定程度的(不是那么接近于0的)曲率半径。例如,可以使第2内角部48b具有与第1内角部48a相同程度的曲率半径。在以上说明的本发明的第4实施方式中,在使用了压制加工装置500的被加工件40的压制加工中,作为被加工件40,使用在上述的实施方式中成形得到的在截面含有角部的外侧的曲率半径较小或大致直角的u字形部分在内的成形品。并且,利用压制加工装置500在利用中央区域523a夹持着被加工件40的顶板部44的状态下对纵壁部42的端面49施加载荷。由此,即使不使材料在纵壁部42与顶板部44之间流动,也能延伸设置纵壁部42,不会使第1内角部48a产生折入。(5.第5实施方式:顶板部的推出)接下来,说明本发明的第5实施方式。在本实施方式中,追加了附加成形工序,在该附加成形工序中,对利用上述的第1实施方式或第2实施方式中的任一种方法成形得到的成形品进一步进行压制加工,成形将顶板部延伸设置后形成的成形品。使用由上述的实施方式成形得到的成形品,压制成形将顶板部延伸设置后形成的成形品,从而内部的角面不会重合而能将顶板部推出,延伸设置顶板部。以下,以使用由上述的实施方式成形得到的成形品为前提,说明将顶板部延伸设置的附加成形工序。图27是表示利用本实施方式的压制加工成形得到的成形品70c的一个例子的说明图。图27所示的成形品70c包括纵壁部74、顶板部76和顶板延伸设置部79,是具有由纵壁部74和顶板部76形成的凹部72的杯状的成形品。也是利用以下说明的第2压制加工装置,进一步压制加工例如图9b所示的在截面含有角部的外侧的曲率半径较小或大致直角的u字形部分在内的杯状的成形品60,从而成形该成形品70c。在图28以及图29中表示作为本实施方式的第2压制加工装置的、用于延伸设置顶板部76的压制加工装置600的结构。图28是表示使顶板部延伸设置的压制加工的初始状态的概略性的剖视图。图29是表示顶板部的延伸设置后的状态的概略性的剖视图。参照图28以及图29,压制加工装置600包括阴模620和冲头640。阴模620包括纵壁固定阴模622和顶板固定阴模623。冲头640包括固定冲头642和可动冲头(垫板)644。如图28所示,在开始本实施方式中的压制加工时,被加工件40与第3实施方式以及第4实施方式相同,是利用第1实施方式或第2实施方式中的任一种方法成形得到的成形品,角部的外侧的曲率半径较小,或者成为大致直角。例如,被加工件40是图9b所示的杯状的成形品60,在该情况下,利用压制加工装置600成形图27所示的将顶板部76延伸设置后形成的杯状的成形品70c。另外,本发明不限定于此例,也能利用压制加工装置600同样地实施如下加工,即,自例如图9a所示的具有槽形形状的长条状的成形品50获得将纵壁部延伸设置后形成的具有槽形形状的长条状的成形品。阴模620利用纵壁固定阴模622以及顶板固定阴模623形成用于收纳被加工件40的凹部。纵壁固定阴模522支承被加工件40的纵壁部42中的、除延伸设置顶板部44的部分以外的区域。另外,在纵壁固定阴模522的与延伸设置顶板部44的部分的区域相对应的部分,以对应于要形成的顶板延伸设置部47的形状的方式形成有向与被加工件40的纵壁部42分开的方向凹陷的台阶部622a。通过将纵壁固定阴模622设置在顶板固定阴模623上,利用纵壁固定阴模622的台阶部622a和顶板固定阴模624形成与顶板延伸设置部47的形状相对应的空间632。配置在阴模620的凹部中的被加工件40如图28所示,处于纵壁部42的一部分区域和顶板部44被支承着的状态。另一方面,冲头640的可动冲头644具有与被加工件40的杯状相对应的形状。可动冲头644自被加工件40的开口插入,配置为其下表面以及侧面与被加工件40的杯状的内表面(即,底面以及侧面)接触。此时,可动冲头644利用与固定冲头642相连结的缓冲件646按压被加工件40,从而在可动冲头644与顶板固定阴模623之间夹持被加工件40的顶板部44。另外,固定冲头642与被加工件40的纵壁部42的端面49抵接。在初始状态下,即使固定冲头642与被加工件40的纵壁部42的端面49抵接,被加工件40也不会变形。当开始由压制加工装置600进行的压制加工时,如图29所示,设在固定冲头642与可动冲头644之间的缓冲件646收缩,固定冲头642朝向凹部的底面进行移动。由此,角部48的材料以将纵壁固定阴模622的台阶部622a与顶板固定阴模624之间的空间632填满的方式进行移动。这样,如图29所示,与压制加工前相比,能够延伸设置被加工件40的顶板部44。与第3实施方式以及第4实施方式相同,也能利用压制加工装置600压制加工利用上述的第1实施方式或第2实施方式中的任一者成形得到的角部的外侧的曲率半径较小或大致直角的成形品,从而获得利用本实施方式成形得到的成形品。若假设被加工件的角部的外侧的曲率半径较大、角部的板厚较薄,则在利用压制加工装置600按压了纵壁部的端部时,纵壁部以及顶板部的材料流动,在角部48的内侧产生折入等缺陷。折入部分比其他部分的强度低,也成为疲劳破坏的主要原因。相对于此,在如本实施方式那样将在截面含有角部的外侧的曲率半径较小或大致直角的u字形部分在内的成形品用作被加工件的情况下,在利用凹部的底面和可动冲头644的下表面夹持着被加工件40的顶板部44的状态下,角部48的材料流动,将空间632填满。因而,不会在利用纵壁部42的内表面和顶板部44形成的第1内角部48a产生折入。另外,通过形成将顶板部44延伸设置后形成的顶板延伸设置部47,利用纵壁部42的外表面和顶板延伸设置部47形成第3内角部48c。第3内角部48c与第1内角部48a相同,从避免应力向角部48集中的观点出发,期望的是,使角部48的内侧具有一定程度的(不是那么接近于0的)曲率半径。例如,也可以使第3内角部48c具有与第1内角部48a相同程度的曲率半径。在以上说明的本发明的第5实施方式中,在使用了压制加工装置600的被加工件40的压制加工中,作为被加工件40,使用在上述的实施方式中成形得到的在截面含有角部的外侧的曲率半径较小或大致直角的u字形部分在内的成形品。并且,利用压制加工装置600在夹持着被加工件40的顶板部44的状态下对纵壁部42的端面49施加载荷。由此,即使不使材料在纵壁部42与顶板部44之间流动,也能将顶板部44延伸设置,不会使第1内角部48a产生折入。(6.总结)采用以上说明的本发明的第1实施方式以及第2实施方式,在使用了压制加工装置的被加工件的压制加工中,当在纵壁部与顶板部之间形成了锥形部后,使锥形部扩张而成形角部。由此,即使不使材料在纵壁部与顶板部之间流动,也能使角部增厚。因此,与现有技术相比,能够减小角部的外侧的曲率半径,或者能使角部的外侧成为大致直角。另外,采用本发明的第1实施方式以及第2实施方式,并不是利用1个工序由平板成形为角部的外侧的曲率半径较小或者成形为大致直角,而是阶段性地推入而成形角部的外侧的形状,从而与现有技术相比,能以较小的载荷进行压制成形。因而,对于强度高的钢铁材料的压制成形也能不在成形时产生裂纹等地进行加工。另外,能用本发明的第1实施方式以及第2实施方式的压制成形方法进行成形的材料除了钢铁以外,还包含铝等。另外,采用本发明的第3实施方式~第5实施方式,将利用第1实施方式或第2实施方式的压制成形装置成形得到的角部的外侧的曲率半径较小或大致直角的成形品用作第2被加工件,进一步进行压制加工,形成其他形状的成形品。通过将角部的外侧的曲率半径较小或大致直角的成形品用作第2被加工件,能在通过压制加工进行了纵壁部的增厚、纵壁部或顶板部的延伸设置时,不会使角部的内侧产生折入等缺陷。此外,利用本发明的第3实施方式~第5实施方式的压制成形装置成形得到的成形品是复杂的形状的成形品,以往通常通过焊接等将多个零件连接而形成这样的成形品。但是,通过将使用了第1实施方式或第2实施方式的压制成形装置的压制成形与使用了第3实施方式~第5实施方式的压制成形装置的压制成形组合,能将复杂的形状的成形品作为1个零件进行制造。由此,能够减少零件件数,零件重量也小,而且制造成本也能降低。实施例为了对利用本发明的压制加工装置成形得到的压制成形品的冲击吸收性能进行评价,实施了碰撞试验。在本实施例中,对形成有自纵壁部延伸的凸缘部的含有u字形部分的槽形形状的压制成形品实施三点弯曲试验,根据每单位体积的吸收能评价了冲击吸收性能。对角部的形状不同的5个压制成形品实施了试验。被加工件使用了980mpa级钢板。使用将第1实施方式所示的压制加工装置100构成为也能一并成形凸缘部的压制加工装置,成形了作为试验对象的压制成形品。这里,在图30中表示用于成形作为试验对象的具有凸缘部的压制成形品的、压制成形品的成形方法。另外,在图30中,只表示压制加工装置700的右半部分,压制加工装置700实际上具有相对于中心线左右对称的构件。压制加工装置700如图30所示,包括阴模720和冲头740。阴模720包括固定部722、内侧可动阴模(垫板)724和外侧可动阴模(垫板)726。利用缓冲件723将内侧可动阴模724支承于固定部722,利用缓冲件725将外侧可动阴模726固定于固定部722。另一方面,冲头740包括固定冲头742和可动冲头(垫板)744。利用缓冲件750将可动冲头744支承于固定冲头742。首先,在开始进行压制加工时,利用可动冲头744和内侧可动阴模724夹持平板状的被加工件10(步骤1)。并且,向冲头740侧推入阴模720,直到外侧可动阴模726与固定冲头742抵接,在固定冲头742的突起部742a与外侧可动阴模726之间约束纵壁部,利用可动冲头744和内侧可动阴模724成形顶板部的中央区域(步骤2)。此时,在顶板部的中央区域与纵壁部之间形成有锥形部。另外,被加工件10中的被外侧可动阴模726与固定冲头742夹持的部分成为凸缘部。然后,当进一步向冲头740侧推入阴模720时,缓冲件750收缩而使可动冲头744与固定冲头742抵接。此时,可动冲头744的端面与固定冲头742的突起部742a的端面处于同一平面上。通过形成为此状态,成形顶板部的边缘区域和角部。这样,可动冲头744较晚地被推入固定冲头742,从而使角部增厚。在图31以及图32中表示在图30所示的压制加工装置700中成形得到的压制成形品80的外形。图31是压制成形品80的立体图,图32是压制成形品80的主视图。另外,在图31以及图32中,为了方便说明,表示压制成形品80的凸缘部88与平板89分开的状态,但实际上两者接触并被焊接在一起。压制成形品80是含有槽形形状82的长条状的成形品。压制成形品80具有纵壁部84、顶板部86以及凸缘部88。在进行冲击吸收试验时,以封闭压制成形品80的槽形形状82的开口的方式配置平板89,在凸缘部88处进行了平板89的点焊。在本实施例中,将高度h设为50mm,将槽形形状82的开口宽度wa设为80mm,将包括凸缘部88在内的压制成形品的宽度wb设为120mm,成形了图31以及图32所示的形状的压制成形品80。被加工件的板厚为1.6mm。并且,如图33以及下述表1所示,将角部87的内侧c1的曲率半径r1设定为1.0mm并在各试验对象共用此值,改变角部87的外侧c2的曲率半径r2,成形了各试验对象的压制成形品。将角部87的板厚与被加工件的板厚相同的试验1的压制成形品作为基准时的增厚率如表1所示。另外,压制成形品80的长度方向(x方向)的长度l为300mm。[表1]no.r1[mm]r2[mm]角部板厚[mm]增厚率试验11.02.61.60-试验21.02.01.8516%试验31.01.52.0629%试验41.01.02.2641%试验51.002.6465%如图34所示,以将图31所示的焊接有平板89的压制成形品80的长度方向的端部支承于试验机的支承部5的方式设置该压制成形品80,实施了三点弯曲试验。支承部5间的距离lb为200mm。支承部5的角部的曲率半径rb为15mm。并且,在支承部5间的中央部,利用压头3按压了压制成形品80的顶板部86。压头3是前端部形成为曲面的圆柱构件,重量为30kg,直径da为100mm,前端部ra的曲率半径为50mm。压头3自在压制成形品80的顶板部86向上方与顶板部86分开1m的位置以4.4m/s的负荷速度对压制成形品80施加了冲击。作为三点弯曲试验的结果,在图35中表示用在试验1~试验5中的压制成形品的增厚率和最大载荷比。这里,将试验1的压制成形品的角部的板厚以及最大载荷作为基准。如图35所示,随着角部的增厚率的增高,最大载荷比也变大,试验4的压制成形品的最大载荷比为约1.5倍。这样,通过增加角部的增厚率,能够有效地吸收初始载荷负荷,例如在用作汽车等的冲击吸收构件的情况下,能够期待碰撞安全性的提高。另外,用在本实施例中的试验2~试验5的压制成形品在使角部的板厚比被加工件的板厚厚的基础上,加之利用上述的压制加工装置700进行成形,从而如图7以及图8所示在顶板部以及角部具有加工硬化了的部位。由此,在三点弯曲试验中也理解为,试验2~试验5的压制成形品显示较高的抗压载荷。另外,利用以往的压制成形装置压制成形的含有u字形部分的压制成形品只在角部具有加工硬化了的部位。另外,由加工硬化获得的强度的上升也小。因而,认为采用以往的手法成形得到的压制成形品无法具有像采用本发明的手法成形得到的压制成形品那样的较高的冲击吸收性能。另外,如在上述的实施方式、本实施例中说明的那样,成形本发明的压制成形品的压制加工方法简易,还能容易且以低成本提供对于三点弯曲载荷具有较高的抗压载荷的冲击吸收构件。以上,参照附图详细说明了本发明的优选的实施方式,但本发明不限定于此例。明确的是,只要是具有本发明所属的
技术领域:
内的通常的知识的人,就能在权利要求所记载的技术思想的范畴内想到各种变更例或修改例,应了解这些变更例或修改例当然也属于本发明的权利范围。另外,在所述实施方式中,作为被加工件,作为一个例子,举出了钢板,但本发明不限定于此例。例如,作为利用压制加工装置加工的被加工件,也可以在铁、铝、钛、不锈钢等的金属板、复合材料(金属-树脂,异种金属)、碳纤维等中应用本发明。此外,也能在以将被加工件加热到预定的温度而使该被加工件变为软质的状态进行压制加工的热冲压中应用本发明。在该情况下,在被加工件的加热后的压制加工时,应用、实施本发明的压制加工装置以及压制加工方法。通过热冲压成形得到的压制成形品的u字形部分的角部也实现了增厚。另外,利用该压制加工装置成形得到的压制成形品不仅能利用在例如汽车或汽车用零件中,还能利用在各种车辆、通用机械、家电和船舶等中。附图标记说明10、20、30、40、被加工件;12、22、32、42、纵壁部;14、24、34、44、顶板部;18、28、38、48、角部;19、49、端面;50、60、70a、70b、70c、成形品;100、200、300、压制加工装置;400、500、600、压制加工装置(第2压制加工装置);120、220、420、520、620、阴模;122、222、固定阴模;124、224、524、可动阴模;126、226、430、凹部;140、340、440、540、640、冲头;142、344、442、542、642、固定冲头;144、外侧可动冲头;146、内侧可动冲头;346、444、544、644、可动冲头;360、压料圈。当前第1页12