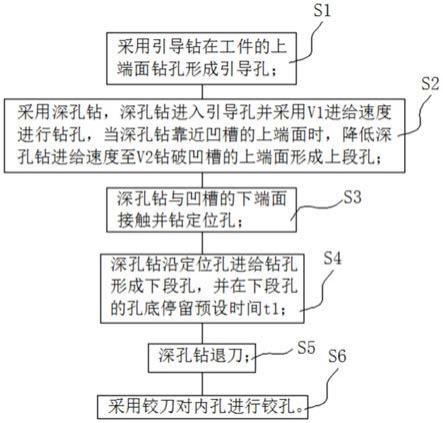
1.本发明涉及工件钻孔技术领域,尤其涉及一种工件内孔加工工艺。
背景技术:2.现有技术中,在加工膝关节置换用的切骨板中的内孔是一个难点,该内孔存在特殊:
3.1、内孔被凹槽分隔形成两段,导致加工该内控的刀具的长径比,提高了加工难度,同时导致内孔在加工过程中形成破边结构,因此,现有技术的加工方法加工精度较差,无法满足该产品内孔相对基准的位置度0.03mm、内孔相对凹槽的高度差0.02mm以及内孔直径公差0.02mm的加工要求;
4.2、现有加工方式的刀具寿命较差,且无法满足内孔与凹槽位置度的要求。
技术实现要素:5.本发明的目的是提供一种满足两段内孔加工的精度要求,并有助于提高加工刀具寿命的工件内孔加工工艺。
6.为了实现上述目的,本发明提供一种工件内孔加工工艺,工件开设有内孔和凹槽,所述凹槽贯穿所述内孔并将所述内孔分隔形成同轴布置的上段孔和下段孔,所述上段孔贯穿所述工件的上端面和所述凹槽的上端面,所述工件内孔的加工工艺包括以下步骤:
7.s1、采用引导钻在工件的上端面钻孔形成引导孔;
8.s2、采用深孔钻,所述深孔钻进入引导孔内并采用v1进给速度进行钻孔,当所述深孔钻靠近所述凹槽的上端面时,降低所述深孔钻进给速度至v2钻破所述凹槽的上端面形成所述上段孔;
9.s3、所述深孔钻与凹槽的下端面接触并钻定位孔;
10.s4、所述深孔钻沿所述定位孔进给钻孔形成下段孔,并在所述下段孔的孔底停留预设时间t1;
11.s5、所述深孔钻退刀;
12.s6、采用铰刀对所述内孔进行铰孔。
13.本技术方案进一步的改进为,所述v1=2v2。
14.本技术方案进一步的改进为步骤s1中,所述引导钻钻孔的进给速度v3/7=v1。
15.本技术方案进一步的改进为步骤s4中,所述预设时间t1=2s-4s。
16.本技术方案进一步的改进为所述深孔钻和所述铰刀均为15倍径刀具。
17.本技术方案进一步的改进为所述步骤s6中,铰刀对所述上段孔进行铰孔形成直径大于所述上段孔的沉孔。
18.本技术方案进一步的改进为所述步骤s2中,所述深孔钻进入引导孔后,先以低转速钻孔预设深度后,再提高转速钻孔至下段孔的孔底。
19.实施本发明的实施例,具有以下技术效果:
20.本发明的工艺简单,在钻孔过程中,为了保证内孔与凹槽的位置度0.03mm的要求,首先通过引导钻以高转速低进给速度形成引导孔,从而保证深孔钻钻孔的位置,当深孔钻即将钻破凹槽的上端面时,通过降低深孔钻的进给速度,避免深孔钻钻出凹槽上端面导致翻边,再进一步的,深孔钻在钻下段孔时,与凹槽的下端面接触并钻定位孔,实现下段孔的定位,保证形成的下段孔与上段孔的同轴度在0.02mm以内,并满足内孔与凹槽的高度差0.02mm的要求;
21.另外,在保证内孔加工精度的同时,提高了刀具的使用寿命。
附图说明
22.图1是本发明优选实施例的步骤流程图;
23.图2是本发明优选实施例中工件的剖视图。
24.附图标记说明:
25.1、内孔,11、上段孔,12、下段孔,13、沉头孔,2、凹槽。
具体实施方式
26.下面结合附图和实施例,对本发明的具体实施方式作进一步详细描述。以下实施例用于说明本发明,但不用来限制本发明的范围。
27.在本发明的描述中,需要说明的是,术语“中心”、“纵向”、“横向”、“上”、“下”、“前”、“后”、“左”、“右”、“竖直”、“水平”、“顶”、“底”、“内”、“外”等指示的方位或位置关系为基于附图所示的方位或位置关系,仅是为了便于描述本发明和简化描述,而不是指示或暗示所指的装置或元件必须具有特定的方位、以特定的方位构造和操作,因此不能理解为对本发明的限制。
28.此外,本发明中采用术语“第一”、“第二”等来描述各种信息,但这些信息不应限于这些术语,这些术语仅用来将同一类型的信息彼此区分开。例如,在不脱离本发明范围的情况下,“第一”信息也可以被称为“第二”信息,类似的,“第二”信息也可以被称为“第一”信息。
29.参考图1和图2,本发明的一个实施例提供了一种工件内孔加工工艺,该工件为17-4ph不锈钢(马氏体沉淀硬化不锈钢)材料,工件开设有内孔1和凹槽2,凹槽2贯穿内孔1并将内孔1分隔形成同轴布置的上段孔11和下段孔12,上段孔11贯穿工件的上端面和凹槽2的上端面,工件内孔1的加工工艺包括以下步骤:
30.s1、引导钻以(s4000,f50)在工件的上端面钻孔形成深度为2.9mm的引导孔,即引导钻的转速为4000r/min,进给速度v3为50mm/min,然后以(s4000,f500)退刀到引导孔口;
31.s2、采用深孔钻,深孔钻进入引导孔内并采用(s4500,f350)进行钻孔,其中,深孔钻的进给速度v1=350mm/min,当深孔钻靠近凹槽2的上端面时,降低深孔钻进给速度至v2钻破凹槽2的上端面形成深度为25.77mm的上段孔11,此时,v2=175mm/min;
32.s3、深孔钻以(s4500,f50)与凹槽2的下端面接触并钻定位孔0.5mm;
33.s4、深孔钻(s4500,f350)沿定位孔进给钻孔形成深度为4.26mm的下段孔12,并在下段孔12的孔底停留预设时间t1,该预设时间可为2s-4s,具体优选的,在本实施例中,t1=3s;
34.s5、深孔钻退刀到孔口;
35.s6、采用铰刀以(s1000,f90)对内孔1进行铰孔并在上段孔11中形成沉头孔13,该沉头孔13的深度为21.66mm、直径为5mm。
36.其中,本实施例中深孔钻和铰刀均为15倍径刀具,具体的,引导钻和深孔钻的直径均为2.9mm,铰刀的直径为2.96mm。
37.步骤s6中,铰刀对上段孔11进行铰孔形成直径大于上段孔11的沉孔。
38.本发明的工艺简单,在钻孔过程中,为了保证内孔1与凹槽2的位置度0.03mm的要求,首先通过引导钻以高转速低进给速度形成引导孔,从而保证深孔钻钻孔的位置,当深孔钻即将钻破凹槽2的上端面时,通过降低深孔钻的进给速度,避免深孔钻钻出凹槽2上端面导致翻边,再进一步的,深孔钻在钻下段孔12时,与凹槽2的下端面接触并钻定位孔,实现下段孔12的定位,保证形成的下段孔12与上段孔11的同轴度,在0.02mm以内,并满足内孔1与凹槽2的高度差0.02mm的要求。
39.以上所述仅是本发明的优选实施方式,应当指出,对于本技术领域的普通技术人员来说,在不脱离本发明技术原理的前提下,还可以做出若干改进和替换,这些改进和替换也应视为本发明的保护范围。