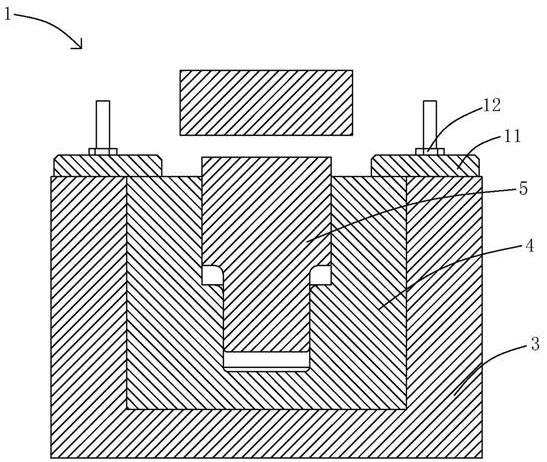
1.本发明涉及机械加工技术领域,更具体地说,它涉及一种行星齿轮轴、行星齿轮轴专用材料及其热锻成型工艺。
背景技术:2.行星齿轮轴是机动车变速器中的关键零部件,其精度是齿轮传动精度的有力保证。行星齿轮轴在使用过程中常常发生磨损,使用量大,当行星齿轮轴磨损严重时,会对机械结构的性能和寿命产生不良影响,因此,行星齿轮轴的加工工艺需同时考虑产品的机械性能和加工成本。
3.目前,行星齿轮轴在加工时,多采用国产棒料直接车削成型,国产棒料的材料多为20mcr5,这种加工工艺使用的棒料毛坯的尺寸为φ65x96mm,重量2.5kg,加工后成品的重量是1.12kg,材料的利用率只有45%,造成了极大的浪费,并且,20mcr5加工后的产品淬透性差,当齿轮轴两端需要滚齿时,中间连接部分的结构薄弱,现有的材料和成型工艺无法满足产品的强度要求;因此需要提出一种行星齿轮轴、行星齿轮轴专用材料及其热锻成型工艺,提高材料的利用率,增强行星齿轮轴的机械强度。
技术实现要素:4.针对现有技术存在的不足,本发明的目的在于提供一种行星齿轮轴、行星齿轮轴专用材料及其热锻成型工艺,其优点是替代传统的直接车削加工工艺,提高材料利用率和行星齿轮轴的结构强度。
5.为实现上述目的,本发明提供了如下技术方案:一种行星齿轮轴专用材料,按质量百分比含有以下组分:c:0.15%~0.21%、si:0.15%-0.40%、mn:0.60%-0.90%、p:≤0.035%、s:≤0.035%、cr:0.70%-1.00%、mo:0.15%-0.25%、ni:1.20%-1.50%、al:0.02%-0.05%、n:0.005%-0.015%、v:≤0.10%、nb:≤0.04%,余量由fe和不可避免的杂质构成。
6.本发明进一步设置为:按质量百分比各组分的含量为:c:0.18%、si:0.24%、mn:0.84%、p:0.015%、s:0.009%、cr:0.95%、mo:0.17%、ni:1.45%、al:0.025%、n:0.008%、v:0.08%、nb:0.03%。
7.通过上述技术方案,在铁基材料中添加一定比例的钼、铬、钒、铌,使其具有较高的淬透性的同时保持高强度和韧性。
8.本发明还提供了一种行星齿轮轴,利用上述所述的行星齿轮轴专用材料制造,包括支撑轴、设置于所述支撑轴一端的滚齿和设置于所述支撑轴远离滚齿一端的转轴,所述支撑轴、转轴、滚齿同轴且一体成型,所述转轴的直径小于支撑轴的直径,所述滚齿的中部设置有沿中心轴线贯穿该滚齿的轴孔。
9.本发明进一步设置为:滚齿的齿数为10,模数为3,压力角20
°
,螺旋角0
°
,中径30mm,齿根圆直径25.44mm,两齿齿厚(mm)14.91(+0.03/0)。
10.通过上述技术方案,行星齿轮轴的强度和韧性大,综合力学性能好,使用寿命长,并且,行星齿轮轴一体成型,结构稳定、传动平稳、运行噪音小。
11.本发明还提供了一种行星齿轮轴热锻成型工艺,用于制造上述所述的行星齿轮轴,包括以下步骤:步骤一:制备锻造棒料:通过铁基改性、锻打和等温正火三道工序制造锻造棒料,其中:铁基改性工序:在钢包炉外精炼期通过对铁基材料按材料配比添加钼丝、铬条、钒丝、铌丝,并搅拌均匀,对基材进行改性;锻打工序:将材料通过电炉或天然气炉加热至ac3以下200摄氏度左右即820~850摄氏度,经模具热锻压,形成锻材;等温正火工序:将锻打工序形成的锻材进行等温正火处理,获得锻造棒料;步骤二:下料:切割锻造棒料获得锻造毛坯,锻造毛坯直径为φ40mm,锻前长度为200mm,综合锻造比为4:1;步骤三:锻前预热:利用加热炉将锻造毛坯加热至1050℃
±
50℃,且最高温度控制在1090℃以下,锻造毛坯在最高温停留10秒形成预锻件后,立即取出;步骤四:一锻:将步骤三中形成的预锻件放入预锻模具内进行预锻,形成外形与行星齿轮轴外形一致的终锻件;步骤五:二锻:将步骤四中形成的终端件放入终锻模具内,使用冲头对终锻件进行终锻,形成锻造品;终锻时,对冲头进行水冷降温,并在冲头与终锻件的接触处添加石墨颗粒;步骤六:堆冷:将锻造品堆放,使其自然缓慢冷却至0℃~40℃,冷却的温度根据自然室温确定;步骤七:滚齿加工:利用滚齿机对锻造品的端部进行滚齿加工,形成机加工品;步骤八:渗碳:利用热处理炉对步骤七形成的机加工品进行渗碳处理,形成最终的成品。
12.通过上述技术方案,优选综合锻造比为4:1的锻造毛坯进行热锻处理,锻造出来的成品饱满无塌边;此外,热锻工艺使元素的晶粒重新组合,得到更加均匀的组织,锻造毛坯热轧时化学元素偏析对材料性能的负影响,消除了棒料内部较大的气孔和夹渣;热锻工艺改变了材料内部的金属流线,使材料内部的流线连贯,不是单向流线,产品的抗疲劳、抗冲击能力得到很大的提升,产品拥有更大的结构强度和综合力学性能,可以在不超出设计安全上限的较大工作载荷的状态下长期工作;通过冲头加工轴孔,加工精度高,可提高行星齿轮轴的传动稳定性;表面渗碳工艺有利于增强行星齿轮轴的耐磨性;二锻时使用水对冲头进行降温冷却,同时添加石墨颗粒,增加冲头的润滑性,使冲出的型腔表面光滑,无凸起或凹陷;热锻后再进行机加工,与传统的直接车削加工相比,提高了材料的使用率,降低了机加工的成本,同时行星齿轮轴的结构强度得到提升。
13.本发明进一步设置为:等温正火工序包括以下步骤:步骤一:装框:锻材平铺于料架上,保证锻材的中心轴线与料架呈正交;步骤二:加热:将锻材加热至920℃,加热时间按照材料的有效厚度/2*(2~3)分钟,利用热电偶检测温度;
步骤三:奥氏体保温+等温处理:保温时间按照材料的有效厚度/2*(2~3)分钟控制,材料完全奥氏体化,冷却均匀,使奥氏体过冷到a1温度以下的580~650℃温度,等温850摄氏度至少4小时,形成f+p组织,去除残余奥氏体组织;步骤四:风冷:风冷2-2.5小时至室温。
14.通过上述技术方案,采用等温处理的锻材,能够获得良好的切削加工性能和稳定的淬火变形规律。
15.本发明进一步设置为:所述预锻模具包括模套和可拆卸设置于所述模套内的模舱,所述模舱的中部形成外形与行星齿轮轴外形一致的锻造腔,预锻件的侧面贴合锻造腔的侧壁,所述终锻模具与预锻模具的结构相同。
16.通过上述技术方案,模套的作用是稳定模舱,同时防止在锻打时,模舱发生变形和开裂;模舱与模套可拆卸连接,模舱磨损后,直接更换新的模舱,无需更换整套模具,提高了整套模具的使用寿命。
17.本发明进一步设置为:所述预锻模具、终锻模具的材质均为4cr5mosiv模具钢,所述冲头的材质为3cr2w8v工具钢。
18.通过上述技术方案,4cr5mosiv模具钢能承受较大冲击,载荷大;3cr2w8v工具钢有较高的强度和硬度、耐冷热疲劳性良好,且有较好的淬透性。
19.本发明进一步设置为:渗碳时,渗碳温度920℃~940℃,碳势0.4%~0.6%。
20.通过上述技术方案,使得行星齿轮轴的渗碳深度达到0.7
±
0.15、渗碳硬度达到58~62hrc,提高行星齿轮轴的表面硬度、耐磨性和疲劳强度,并保持心部有低碳钢淬火后的强韧性,使行星齿轮轴能承受较大的冲击载荷。
21.综上所述,本发明具有以下有益效果:1.本发明优化了行星齿轮轴的材料组成,在铁基材料中加入钼、铬、钒、铌等改性成分,利用该材料制造的行星齿轮轴具有较高的淬透性,并且强度高、韧性好;2.本发明通过热锻工艺的改进和优化,替代传统的车削加工制造行星齿轮轴,提高材料利用率的同时增强了行星齿轮轴的综合力学性能,延长产品的使用寿命;3.本发明的行星齿轮轴强度高、韧性好;行星齿轮轴一体成型,通过锻打和热处理后进行机加工,加工精度高,行星齿轮轴的轴孔通过冲压一次成型,轴孔的内壁光滑,机械配合稳定,应用在减速起动机上,传动稳定、噪音小。
附图说明
22.图1是本实施例的行星齿轮轴的结构示意图;图2是本实施例的预端模具的结构示意图;图3是本实施例的终锻模具的结构示意图;图4是本实施例的专用材料的金相结构200倍放大图;图5是本实施例的专用材料的金相结构600倍放大图;图6是本实施例的行星齿轮轴的热锻工艺的金属流线测试图;图7是本实施例的行星齿轮轴直接机加工的金属流线示意图。
23.附图标记:1、预锻模具;2、终锻模具;3、模套;4、模舱;5、预锻件;6、终锻件;7、支撑轴;8、滚齿;9、转轴;10、轴孔;11、压板;12、螺栓;13、冲头。
具体实施方式
24.以下结合附图对本发明作进一步详细说明。
25.实施例1:参考图1,一种行星齿轮轴,包括支撑轴7、设置在支撑轴7一端的滚齿8和设置在支撑轴7远离滚齿8一端的转轴9,支撑轴7、转轴9、滚齿8同轴设置且一体成型,转轴9的直径小于支撑轴7的直径,滚齿8的中部设置有沿中心轴线贯穿该滚齿8的轴孔10;本方案中的行星齿轮轴的滚齿8的齿数为10,模数为3,压力角20
°
,螺旋角0
°
,中径30mm,齿根圆直径25.44mm,两齿齿厚(mm)14.91(+0.03/0)。
26.上述行星齿轮轴采用热锻成型工艺制造而成,该热锻成型工艺包括以下步骤:步骤一:制备锻造棒料:通过铁基改性、锻打和等温正火三道工序制造锻造棒料,其中:铁基改性工序:在钢包炉外精炼期通过对铁基材料按材料配比添加钼丝、铬条、钒丝、铌丝,并搅拌均匀,对基材进行改性,使其在具备较高淬透性的同时,又能保持高强度和韧性;材料配比为:按质量百分比含有以下组分,c:0.15%~0.21%、si:0.15%-0.40%、mn:0.60%-0.90%、p:≤0.035%、s:≤0.035%、cr:0.70%-1.00%、mo:0.15%-0.25%、ni:1.20%-1.50%、al:0.02%-0.05%、n:0.005%-0.015%、v:≤0.10%、nb:≤0.04%,余量由fe和不可避免的杂质构成;优选的,材料配比可按以下比例添加,按质量百分比计各组分的含量为:c:0.18%、si:0.24%、mn:0.84%、p:0.015%、s:0.009%、cr:0.95%、mo:0.17%、ni:1.45%、al:0.025%、n:0.008%、v:0.08%、nb:0.03%;锻打工序:将材料通过电炉或天然气炉加热至ac3以下200摄氏度左右即820~850摄氏度,经热锻压形成锻材;等温正火工序:将锻打工序形成的锻材进行等温正火处理,获得锻造棒料,等温正火工序包括以下流程:流程一:装框,将锻材平铺于料架上,保证锻材的中心轴线与料架呈正交;流程二:加热,将锻材加热至920℃,加热时间按照材料的有效厚度/2*(2~3)分钟,利用热电偶检测温度;流程三:奥氏体保温+等温处理:保温时间按照材料的有效厚度/2*(2~3)分钟控制,材料完全奥氏体化,冷却均匀,使奥氏体过冷到a1温度以下的580~650℃温度,等温850摄氏度至少4小时,形成f+p组织,即珠光体和铁素体组织,去除残余奥氏体组织;流程四:风冷:风冷2-2.5小时至室温;上述流程二至流程四中的温度与时间可采用下列数值:
步骤二:下料:切割锻造棒料获得锻造毛坯,锻造毛坯直径为φ40mm,锻前长度为200mm,综合锻造比为4:1,获得的锻造毛坯的重量为1.9kg,由于成品重量为1.12kg,与现有的车削加工相比,材料的使用率提高到59%。
27.步骤三:锻前预热:利用加热炉将锻造毛坯加热至1050℃
±
50℃,且加热的最高温度控制在1090℃以下,防止过烧,导致坯料的晶粒粗大,锻造时产生裂纹;锻造毛坯在最高温停留10秒形成预锻件5后,需立即取出。
28.步骤四:一锻:使用预锻模具1对已加热的坯料进行预锻,将步骤三中形成的预锻件5放入预锻模具1内进行预锻,获得外形与行星齿轮轴外形一致的终锻件6;参考图2,预锻模具1包括模套3和可拆卸设置在模套3内的模舱4,模舱4的中部向下凹陷形成外形与行星齿轮轴外形一致的锻造腔,预锻件5的侧面贴合锻造腔的侧壁,预锻模具1选用能承受较大冲击、载荷大的4cr5mosiv模具钢制作,设计寿命为2万件;模舱4的上端通过压板11和螺栓12固定在模套3上,模舱4磨损后松开螺栓12,直接更换新的模舱4,而不更换整套模具,有利于提高整付模具的使用寿命。
29.参考图3,步骤五:二锻:预锻完成后,将步骤四中形成的终端件立即转移到终锻模具2上,使用冲头13对已预锻的产品进行二次锻造,形成锻造品;锻造时,使用水对冲头13进行降温冷却,同时,在冲头13与终锻件6的接触处添加石墨颗粒,增加冲头13的润滑性,使冲出的型腔表面光滑,无凸起或凹陷;终锻模具2与预锻模具1的结构相同,预锻模具1、终锻模具2的材质均为4cr5mosiv模具钢,冲头13的材质为3cr2w8v工具钢。
30.步骤六:堆冷:将锻造品堆放,使其自然缓慢冷却至0℃~40℃,冷却的温度根据自然室温确定;该工艺利用锻造品自身的余温做正火处理,细化和均匀组织晶粒,保证渗碳处理时尺寸的稳定性。
31.步骤七:滚齿:利用滚齿机对锻造品的端部进行滚齿8加工,形成机加工品。
32.步骤八:渗碳:利用热处理炉对步骤七形成的机加工品进行渗碳处理,形成最终的成品;渗碳时,渗碳温度920℃~940℃,碳势0.4%~0.6%。
33.试验例1:将行星齿轮轴专用材料(以下称专用材料)制造的锻材与传统的20mncr5材料制造的锻材进行对比测试:表1:化学成分
通过拉力试验机检测锻材的机械性能,获得以下数据:表2:机械性能材料的淬透性是获得热处理效果的一种能力,通常用淬硬层深度来表示,采用洛氏硬度计测试,测试方法见标准iso642,获得以下数据:表3:淬透性:参考图4和图5,经等温正火处理后,通过金相显微镜观测(方法详见金属显微组织检测方法gb/t13298-1991),由图中检测的数据显示,能获得晶粒度5~8级均匀分布的珠光体和铁素体组织,该结构硬度散差小(160~190hb),具有机加工性能优良,渗碳淬火变形小等优势。
34.试验例2:对专用材料制造形成的行星齿轮轴的金属流线和机械性能进行测试,结果如下:(1)使用拉力试验机测试渗碳后的行星齿轮轴的机械性能,测试结果如下:表四:行星齿轮轴的机械性能(2)参考图6和图7,用金相镶嵌机镶嵌,然后金相抛光机抛光,再用金相显微镜测试金属流线,由测试结果可知,本方案的工艺改变了材料内部的金属流线,使材料内部的流
线连贯,不是单向流线,产品的抗疲劳、抗冲击能力得到很大的提升。
35.本具体实施例仅仅是对本发明的解释,其并不是对本发明的限制,本领域技术人员在阅读完本说明书后可以根据需要对本实施例做出没有创造性贡献的修改,但只要在本发明的权利要求范围内都受到专利法的保护。