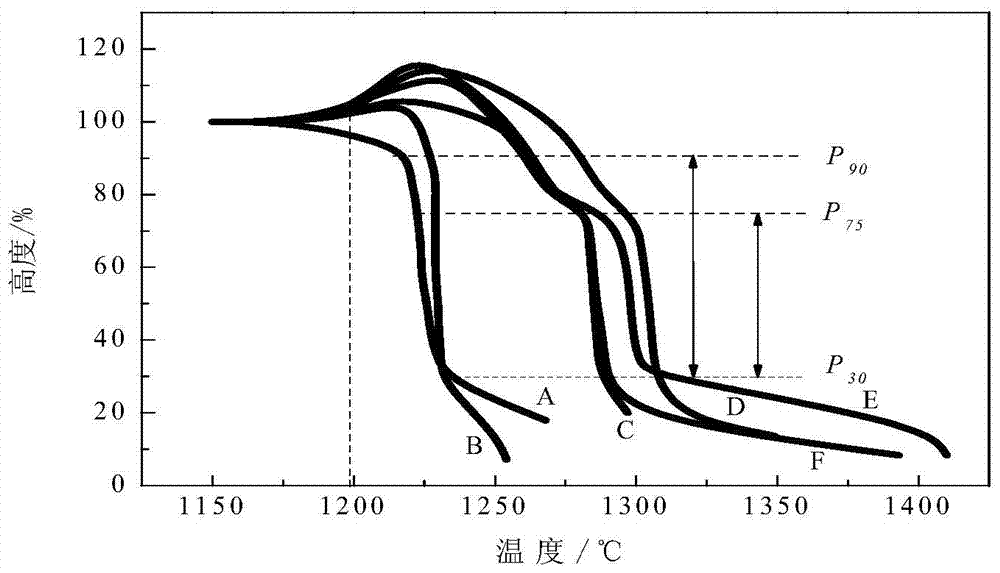
本发明涉及高炉炼铁烧结技术领域,特别涉及一种测定铁矿粉烧结液相流动性能的方法。
背景技术:随着我国钢铁企业产能过剩,钢铁企业普遍处于亏损状态,国内高炉炼铁企业为谋求生存,合理高效利用铁矿粉来提高烧结矿的性价比对企业摆脱困境很有必要。低质铁矿资源的特点是成分和性能波动较大,且某些烧结性能不足,但烧结中的使用量不大;通过不同种类铁矿粉的合理搭配,不但可在一定程度上改善铁矿石综合冶金性能,保证高炉生产的经济技术指标稳定,也能够达到降低炼铁成本的目的。不同铁矿粉的合理搭配,需通过烧结杯试验来获取一些基本参数,为了更准确地模拟烧结生产过程,烧结杯容积趋于大型化,使得其工作量增大,试验周期变长。通过铁矿粉烧结基础特性的研究,获得铁矿粉基础性能的信息和数据,既可优化烧结杯试验,提高工作效率,又可以应对在低质矿种的频繁变化时知道烧结配料。其中,烧结过程中铁矿粉与CaO反应生成液相的流动能力,即铁矿粉的流动性能至关重要;烧结液相自身特性及其流动能力是影响烧结固结好坏,乃至烧结矿冶金性能优劣的重要因素。测量铁矿粉流动的方法很多,其一是文献《铁矿粉烧结液相流动特性》(吴胜利,杜建新等.北京科技大学学报,2005,27(3):291)中提出了流动性指数(面积增长率);其二是研究者认为温度和时间是影响铁矿粉流动性至关重要的因素,提出的特征熔化温度、熔化时间等评价指标;其三是用高温共焦显微镜对液相进行原位观察,提出的流动速度,可以对液相某一方向上流动做出动态表征。上述方法中存在以下缺点和不便:考虑了温度因素,却没有定量给出温度对流动性的影响;选择了温度区间,却不能合理的结合流动与收缩的规律;提出了流动速度,却不能表征整体流动状态;评价指标繁多,需重复多次取值,指标间内在关系考虑不足,不能全面表征液相流动全程信息,由此造成评价指标使用不便,且不能真实表征铁矿粉的流动性能。
技术实现要素:本发明的目的就是克服现有技术的不足,提供了一种测定铁矿粉烧结液相流动性能的方法,具体包括以下步骤:步骤一、将铁矿粉和分析用纯CaO试剂研磨成粒度<149μm的细粉状,干燥;步骤二、制作铁矿粉和CaO的混合矿粉试样以及铁矿粉垫片试样,在压片机上分别压制成混合矿粉圆柱试样和铁矿粉垫片试样;步骤三、将所述混合矿粉圆柱试样置于所述铁矿粉垫片试样之上,放入高温炉内进行焙烧;对试样在升温过程中进行摄像的同时记录时间和温度;步骤四、由计算机系统在升温过程中采集图像和数据信息;确定所述混合矿粉试样烧结液相有效流动的起点和终点;利用Photoshop像素法测量试样的流动面积,由起点和终点所对应的时间点、温度及流动面积,计算得出流动时间、流动温度、面积增长率;进一步计算出流动性特征数LD:式中:LD为流动性特征数;为流动参数;为温度对速度修正系数;υz为烧结液相自身流动速度,即液相流动面积增长率与流动时间之比ΔS/t,1/s;ΔS为面积增长率,即流动起点到终点液相流动面积增长率,%;t为流动时间,s;T为流动温度,即流动起点与终点温度平均值,K;T标为实际烧结温度,K;H为升温速率,K/s。进一步的,步骤二中所述混合矿粉的碱度为3.0-5.0。进一步的,所述混合矿粉的碱度为4.0。进一步的,步骤二中所述混合矿粉圆柱试样的尺寸为直径8mm、高为5-6mm,混合矿粉圆柱试样的质量为0.6-1.0g;所述铁矿粉垫片试样尺寸为直径24mm、高4mm,铁矿粉垫片试样的质量为3g。进一步的,步骤三中焙烧的升温过程为:室温到600℃以15℃/min升温,600~1150℃以10℃/min升温,1150℃以上以5℃/min升温;同时,在室温到1150℃过程中通氮气,通气量为3L/min;在温度达到1150℃直到试验结束过程中通空气,通气量为3L/min。进一步的,步骤四中面积增长率S=(SP30-SP75)/SP75;其中SP30、SP75为烧结过程中混合矿粉试样高度分别下降70%、25%时铁矿粉试样液相流动面积;T标为实际烧结温度1563K。本发明和现有技术相比具有的有益效果在于:(1)本发明考虑了铁矿粉与Cao反应生成液相过程中各种重要信息,如流动温度、流动时间、面积增长率和升温速率等因素对铁矿粉流动过程的影响,改进了以往方法不能全面表征液相流动全程信息的缺陷,避免评价指标使用不便,且不能真实表征铁矿粉的流动性能的问题。(2)本发明的工艺流程简单,工艺参数稳定,使用的可视卧式高温炉可以同步采集铁矿粉与CaO反应生成的液相流动过程的图像信息和时间信息,可随时取出试样用以检测液相流动过程的流动状态。(3)本发明提出的同化反应特征数,全面包含了铁矿粉与CaO反应生成的液相流动过程中的各种信息,易于在实验室进行试验,作为铁矿粉液相流动性能评价和开展烧结杯试验的依据,更易于为生产技术人员接受和采纳。附图说明图1所示为铁矿粉试样熔融流动过程图。图2所示为铁矿粉试样高度变化与温度的关系图。图3所示为温度对流动速度的修正函数曲线图。具体实施方式下文将结合具体附图详细描述本发明具体实施例。应当注意的是,下述实施例中描述的技术特征或者技术特征的组合不应当被认为是孤立的,它们可以被相互组合从而达到更好的技术效果。在下述实施例的附图中,各附图所出现的相同标号代表相同的特征或者部件,可应用于不同实施例中。本发明实施例一种测定铁矿粉烧结液相流动性能的方法,具体包括以下步骤:步骤一、将铁矿粉和分析用纯CaO试剂研磨成粒度<149μm的细粉状,干燥;步骤二、制作铁矿粉和CaO的混合矿粉试样以及铁矿粉垫片试样,在压片机上分别压制成混合矿粉圆柱试样和铁矿粉垫片试样;步骤三、将所述混合矿粉圆柱试样置于所述铁矿粉垫片试样之上,放入高温炉内进行焙烧;对试样在升温过程中进行摄像的同时记录时间和温度;步骤四、由计算机系统在升温过程中采集图像和数据信息;确定所述混合矿粉试样烧结液相有效流动的起点和终点;利用Photoshop像素法测量试样的流动面积,由起点和终点所对应的时间点、温度及流动面积,计算得出流动时间、流动温度、面积增长率;进一步计算出流动性特征数LD:式中:LD为流动性特征数;为流动参数;为温度对速度修正系数;υz为烧结液相自身流动速度,即液相流动面积增长率与流动时间之比ΔS/t,1/s;ΔS为面积增长率,即流动起点到终点液相流动面积增长率,%;t为流动时间,s;T为流动温度,即流动起点与终点温度平均值,K;T标为实际烧结温度,K;H为升温速率,K/s。步骤二中所述混合矿粉的碱度为3.0-5.0,优选为4.0;步骤二中所述混合矿粉圆柱试样的尺寸为直径8mm、高为5-6mm,混合矿粉圆柱试样的质量为0.6-1.0g,优选为0.8g;所述铁矿粉垫片试样尺寸为直径24mm、高4mm,铁矿粉垫片试样的质量为3g。步骤三中焙烧的升温过程为:室温到600℃以15℃/min升温,600~1150℃以10℃/min升温,1150℃以上以5℃/min升温;同时,在室温到1150℃过程中通氮气,通气量为3L/min;在温度达到1150℃直到试验结束过程中通空气,通气量为3L/min。步骤四中面积增长率S=(SP30-SP75)/SP75;其中SP30、SP75为烧结过程中混合矿粉试样高度分别下降70%、25%时铁矿粉试样液相流动面积;T标为实际烧结温度1563K。本实施例中,针对6种铁矿粉(A、B、C、D、E和F)按照上述步骤进行铁矿粉液相流动性测试试验,6种铁矿粉化学成分如表1所示:表1铁矿粉的化学成分(质量分数,%)1.实验结果分析在试验过程中,试样在1150℃之前形态基本没有变化,故定义试样在形态没有变化时的初始高度为1,则熔化流动试验过程中铁矿粉试样在不同温度下的对应高度如图1所示;随着温度升高,试样的高度会发生变化,如果高度增加,即为试样膨胀,反之则为收缩;120%代表试样高度变为初始高度的1.2倍,即试样膨胀了20%;80%则代表试样高度变为初始高度的80%,即试样收缩了20%。试样随着温度的升高对应的高度变化曲线如图2所示,从图2中可以看出,矿粉在升温过程中高度收缩经历:慢速阶段、快速阶段、慢速阶段。C、D、E和F四种矿粉试样从开始收缩至P75为第一个慢速阶段;从P75至P30为快速阶段,经历了较短的温度段,但却完成了主要的收缩部分;从P30到试样形态不再变化为第二个慢速阶段,较第一个慢速阶段更慢。A、B两种矿粉的不同之处在于其第一个慢速阶段(开始收缩至P90)较早结束,由表1可知这两种矿粉的SiO2含量较其他矿粉高出很多,充分液相的生成是快速阶段(P90至P30)提前出现的可能原因。再结合图1可以看出,在试样高度下降了25%左右时,有效液相已经逐渐形成,之后其生成量逐渐增加,而在25%之前试样在不断收缩,但产生的液相量有限,不足以流动;在试样高度下降了70%左右时,液相充分形成,且之后其生成量将会逐渐减小,并最终停止,这解释了图2中试样高度下降在不同阶段有着不同下降速度的原因。因此定义矿粉在该区间内的流动是烧结液相的有效流动区间,即试样高度下降了25%和70%处分别为烧结液相有效流动的起点P75和终点P30。2.烧结液相流动过程的表征结果分析6种矿粉在试验过程中液相流动起点P75和终点P30对应的基础数据如表2所示;表3所示为烧结液相流动过程数据。表2试验过程基础数据表3烧结液相流动过程数据表4是以T标为1290℃做标准,将实验数据代入下列公式得到的结果。流动性特征数:流动参数:可得:表4铁矿粉流动参数与流动性特征数由表4可知,6种矿粉用流动性特征数进行表征时的结果为LDB>LDA>LDC>LDD>LDF>LDE,与用流动参数表征的结果FB>FA>FC>FD>FF>FE的顺序保持一致,但两种评价指标的数值有较大变化,其原因正是考虑了温度对流动速度的修正作用。修正函数如下:图3所示为温度对流动速度的函数曲线,对应表3中不同矿粉的流动温度,可在图3中得到其修正值。矿粉A和B由于其流动温度较低,使用流动性特征数进行表征较使用流动参数表征时,在数值上增大为原来的2~3倍;D和E矿粉由于其流动温度较高,使用流动性特征数进行表征较使用流动参数表征时,在数值上减小为原来的0.8~0.9倍;而矿粉C和F使用两种表征方法时,数值变化不大,这是其流动温度接近烧结生产标准温度的缘故。因此,充分考虑了温度的重要影响,经过温度修正后的流动性特征数更客观、真实的反映了铁矿粉的流动性能差异。由表2可知,6种矿粉的面积增长率由大到小的排序为SA>SB>SC>SD>SF>SE,与使用流动性特征数表征结果的差别在于矿粉A和B,流动摊开面积增长率较大的A矿粉需要相对来说较长的流动时间才能流动开,所以在用流动性特征数进行表征时远不如矿粉B。由于流动性特征数综合考虑了流动过程中的流动温度、时间等因素,故其可以细分出不同铁矿粉流动过程的性能差异。本发明和现有技术相比具有的有益效果在于:(1)本发明考虑了铁矿粉与Cao反应生成液相过程中各种重要信息,如流动温度、流动时间、面积增长率和升温速率等因素对铁矿粉流动过程的影响,改进了以往方法不能全面表征液相流动全程信息的缺陷,避免评价指标使用不便,且不能真实表征铁矿粉的流动性能的问题。(2)本发明的工艺流程简单,工艺参数稳定,使用的可视卧式高温炉可以同步采集铁矿粉与CaO反应生成的液相流动过程的图像信息和时间信息,可随时取出试样用以检测液相流动过程的流动状态。(3)本发明提出的同化反应特征数,全面包含了铁矿粉与CaO反应生成的液相流动过程中的各种信息,易于在实验室进行试验,作为铁矿粉液相流动性能评价和开展烧结杯试验的依据,更易于为生产技术人员接受和采纳。本文虽然已经给出了本发明的一个实施例,但是本领域的技术人员应当理解,在不脱离本发明精神的情况下,可以对本文的实施例进行改变。上述实施例只是示例性的,不应以本文的实施例作为本发明权利范围的限定。