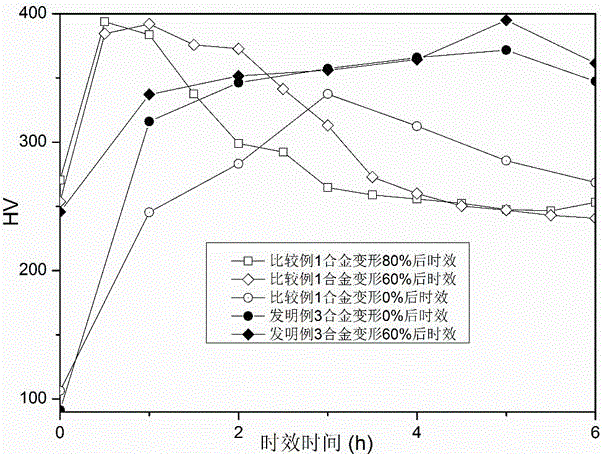
本发明涉及一种高弹性、耐腐蚀、耐磨Cu-Ni-Sn合金的制备方法,属于铜合金材料加工
技术领域:
。
背景技术:
:高强度铜合金当以铍青铜应用最为广泛,但铍铜合金在生产过程中所散发的含铍化合物粉尘、烟雾会引起人体多种器官急慢性中毒,因此铍被列入各种工业毒害中最为严重的污染物,世界各国都限制定含铍材料在本国的生产。上世纪70年代美国率先开展了铍青铜代用材料的研究,采用spinodal热处理工艺开发了3种Cu-Ni-Sn合金材料,并于80年代纳入了AMS标准体系。国内在该领域的研究工作已持续20余年,但到目前为止,很多研究成果尚处于实验室阶段,大规格棒材产品的研发仍属空白;尤其是当Cu-Ni-Sn合金成分中Sn含量较高时,铸态组织是存在明显成分偏析的树枝晶,主要表现为液态合金首先结晶出Cu、Ni原子富集的树枝状ɑ固溶体,枝晶间为富集着溶质原子Sn的固溶体,以及数量、尺寸不等的(Cu,Ni)3Sn化合物,因而增加了材料塑性成形的难度,易诱发组织内的显微裂纹、降低产品的疲劳寿命。技术实现要素:本发明的目的是提供一种高弹性、耐腐蚀、耐磨Cu-Ni-Sn合金制备方法,该制备方法能够消除该系合金微观和宏观偏析,改善该系合金的塑性加工性能,提高合金使用寿命,且具有节约能源、提高生产效率、降低生产成本的优势。本发明的目的是通过下述技术方案实现的。一种高弹性、耐腐蚀、耐磨Cu-Ni-Sn合金制备方法,所述制备方法的步骤为:步骤一:准备制备Cu-Ni-Sn合金的各个组分的重量百分比为:Ni3~41%,Sn1~26%,微量元素Cr、Mn、Nb、Si、Zr和Ti中的至少一种,且Cr、Mn、Nb、Si、Zr、Ti总量为0.03%~0.3%;余量为Cu;步骤二:上述合金采用真空感应熔炼方式或者利用覆盖保护的非真空熔炼方式进行熔炼,投料是,Cu和Ni同时加,等Cu和Ni熔融并精炼后再加Sn和其他微量元素;熔清后进行浇铸;步骤三:凝固过程中施加电磁搅拌至合金液完全凝固,电磁搅拌的搅拌时间为20s~100s;步骤四:将上述铸态合金经均匀化退火水冷固溶冷变形时效处理。本发明一种高弹性、耐腐蚀、耐磨Cu-Ni-Sn合金制备方法,所述步骤一中:Ni和Sn的重量百分比含量为:Ni14~16%;Sn8.5~10.5%。本发明一种高弹性、耐腐蚀、耐磨Cu-Ni-Sn合金制备方法,所述步骤二中:控制出炉温度为1100~1300℃。本发明一种高弹性、耐腐蚀、耐磨Cu-Ni-Sn合金制备方法,所述步骤四中:,其中均匀化退火工艺:840℃×8h,固溶处理工艺:750~840℃×1h,冷变形量:60%~80%,时效处理工艺:350~400℃×(0.5~6h)。与现有技术相比,本发明的有益效果是:本发明能够解决Cu-Ni-Sn合金铸态组织的偏析问题,改善该系合金的塑性加工性能,提高合金使用寿命,显著提高产品质量和生产效率,节约能源,降低生产成本。具体的讲,本发明可细化晶粒,减小枝晶间距,消除该系合金微观和宏观偏析且时效强化效果优异,改善该系合金的塑性加工性能,提高合金使用寿命,且凝固过中施加电磁搅拌,所得铸态组织中的偏析程度小、易消除,因此具有节约能源、提高生产效率、降低生产成本的优势。附图说明:图1为凝固过程中不同功率电磁搅拌后的Cu-Ni-Sn的合金显微组织;其中:(a)0KW;(b)1KW;(c)2.5KW;(d)4KW图2不同冷变形条件下的时效硬度曲线。具体实施方式本发明涉及的一种高弹性、耐腐蚀、耐磨Cu-Ni-Sn合金制备方法,所述制备方法的步骤为:步骤一:准备制备Cu-Ni-Sn合金的各个组分的重量百分比为:Ni3~41%,Sn1~26%,微量元素Cr、Mn、Nb、Si、Zr和Ti中的至少一种,且Cr、Mn、Nb、Si、Zr、Ti总量为0.03%~0.3%;余量为Cu;上述Ni、Sn选择需保证Cu-Ni-Sn合金能发生调幅分解;优选的,该步骤一中:Ni和Sn的重量百分比含量为:Ni14~16%;Sn8.5~10.5%步骤二:上述合金采用真空感应熔炼方式或者利用覆盖保护的非真空熔炼方式进行熔炼,投料是,Cu和Ni同时加,等Cu和Ni熔融并精炼后再加Sn和其他微量元素;熔清后进行浇铸;控制出炉温度为1100~1300℃,步骤三:凝固过程中施加电磁搅拌至合金液完全凝固,电磁搅拌的搅拌时间为20s~100s;凝固过程中施加电磁搅拌一方面能够细化晶粒,减小枝晶间距,减小溶质扩散距离,另一方面使枝晶凝固前沿的液态金属温度梯度分布更为平缓,既降低一次枝晶沿轴距生长的速度,也相应的减少了二次枝晶及更高次枝晶相互之间对液态金属的封锁区域,进一步缓和枝晶间的溶质浓度,减缓合金枝晶偏析的严重程度,抑制甚至消除偏析的产生,并为后续处理提供有利条件。步骤四:将上述铸态合金经均匀化退火水冷固溶冷变形时效处理,其中均匀化退火工艺:840℃×8h,固溶处理工艺:750~840℃×1h,冷变形量:60%~80%,时效处理工艺:350~400℃×(0.5~6h)。具体的讲,步骤一种合金中添加微量元素Cr、Mn、Nb、Si、Zr和Ti时的重量百分比为:Cr0.03%~0.3%,Mn0.03%~0.3%,Nb0.03%~0.3%,Si0.03%~0.3%,Zr0.03%~0.3%,Ti0.03%~0.3%。且所添加微量元素的作用为:Cr:延缓调幅分解过程,提高合金强度,改善淬火时效样品的塑性。Mn:延缓或加速合金时效和形变时效过程,提高最佳时效温度,增强硬化效果和在酸中的耐蚀性。Nb:促进白铜合金的Spinodal分解,加速其Spinodal分解的强化,但同时也促进晶界析出相的长大。亦能细化白铜合金的晶粒,改善其强度和塑性。Si:固溶之余的Si主要与Ni结合形成Ni2Si和Ni3Si相。由于Ni3Si相难溶于基体,在晶界上析出,占据不连续沉淀物的形核位置,从而起到抑制不连续沉淀物的行核、长大和不连续沉淀物前沿界面移动的作用。而Ni2Si相则相反,经固溶处理后,有大部分Ni2Si相固溶于基体形成过饱和的固溶体。时效过程中,析出的Ni2Si相起到与Ni3Si相相同的作用。Zr:有效地推迟合金晶界上的连续沉淀过程,因此能有效地促进白铜合金的调幅分解过程,并有效地改善该合金的强度和延性。Ti:可细化合金的晶粒并提高合金的强度和塑性性能。Ti含量超过0.3%时,Ti能与基体中的Ni结合生成新的第二相Ni3Ti,从而有效地抑制合金中的γ第二相的析出,推迟硬度到达峰值的时效时间,同时,也使胞状组织的生长得到抑制。下面,结合具体实施例进行分析;真空冶炼试验用Cu-Ni-Sn合金,其化学成分如表1所示。合金熔清后浇铸,在凝固过程中施加不同强度的电磁搅拌至完全凝固,随后对铸态合金进行相同处理,即均匀化退火水冷固溶冷变形时效处理,其中均匀化退火工艺:840℃×8h,固溶处理工艺:800℃×1h,冷变形量:70%,时效处理工艺:400℃×(2.5h)。电磁搅拌参数:比较例1、发明例1、发明例2以及发明例3的搅拌功率分别为0KW,1KW,2.5KW和4KW。不同电磁搅拌功率条件下的显微组织、均匀化退火固溶处理后的硬度以及不同冷变形条件下的时效硬度如图1、表2和图2所示。表1为各试验用钢的化学成分(wt%)CuNiSn其他发明例174.715.68.71发明例274.615.68.81发明例374.815.78.51比较例174.815.68.61表2为均匀化退火固溶处理后的硬度电搅功率0KW1KW2.5KW4KW维氏硬度106.498.6296.5491.41由发明例1~3结果可知:凝固过程中施加电磁搅拌能够细化晶粒,减小枝晶间距,抑制偏析的产生;相同均匀化退火及固溶处理条件下,随电磁搅拌功率升高,硬度逐渐降低,凝固过程中施加电磁搅拌作用,会使枝晶凝固前沿的液态金属温度、溶质浓度分布均匀,减轻枝晶偏析,在经历相同均匀化退火热处理条件下,所得组织更加均匀,硬度相对较低,而且时效处理后,发明例硬度强化峰出现较迟,且峰值相对较高,时效效果优异。当前第1页1 2 3