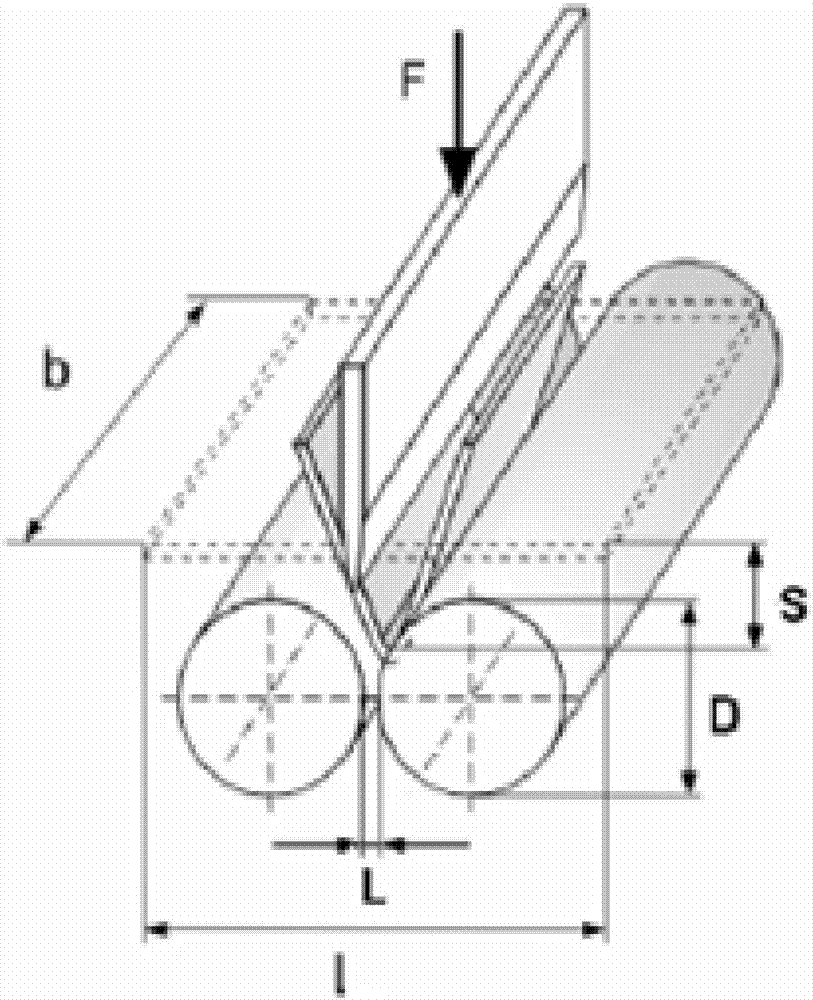
本发明属于轧钢
技术领域:
,涉及一种高韧性热成形钢及其制造方法。
背景技术:
:随着汽车工业的发展,节能减排已成为当今世界共同关注的焦点。汽车轻量化是实现这一目标的主要措施。而汽车轻量化必须兼顾安全性,高强度汽车用钢的应用则是节能减排、同时又保持汽车安全性的重要途径。但是,高强度钢板强度很高,在冷冲过程中易出现回弹严重、冲压开裂、复杂零件冲压成形困难等问题。目前,热冲压成形工艺可以克服上述的问题,并成为人们关注的焦点。热冲压成形过程为将钢板加热至奥氏体温度区间保温,然后利用钢板在高温下塑性良好、变形抗力小等特点,在装有冷却系统的模具中快速成形并淬火冷却,以获得超高强度零件,同时保证了零件的形状及尺寸精度。在复杂的载荷条件下不仅要求热成形零件具有高强度,同时也需要良好的塑韧性。然而,由于热成形淬火后得到的全部为马氏体组织,强度非常高,但是韧性不足,其强度可达1500mpa以上,而延伸率只有5%左右,三点弯曲角度一般在65度以下。中国专利200810112020.2一种热成形马氏体钢,该钢的主要化学成分(wt%)为:c:0.10~0.33%,si:0.50~2.30%,mn:0.50~2.00%,p:≤0.020%,s:≤0.015%,al:0.015~0.060%,o:≤0.002%,n:0.002~0.008%,其余为fe及不可避免的不纯物。其抗拉强度为1300mpa~1700mpa,延伸率高于15%,主要通过添加0.50~2.30%的si,在热成形工序中马氏体转变前采用缓冷工艺获得一定量残余奥氏体的方法,提高延伸率。然而此方法热成形时工艺控制难度大,缓冷工艺使生产效率降低,同时,残余奥氏体的存在也限制了应用。中国专利201110269388.1一种汽车用高韧性热成形钢板的热处理方法,其成分质量百分比为:c:0.20~0.40%,si:0.10~0.50%,mn:1.0~2.0%,p:≤0.02%,s:≤0.01%,nb:0.02~0.06%,ti:0.01%~0.05%,cr:0.1~0.5%,b:0.001~0.005%,al:0.01~0.1%,n:≤0.01%,其余为fe及不可避免杂质。热成形钢板在冲压成形后放入退火炉内;在100~500℃范围内,进行1~10min的回火处理,将回火后的钢板取出后再空气中自然冷却至室温。该发明在传统热成形钢的基础上,通过回火的方法消除钢板快速冷却产生的内应力和软化马氏体组织,进而改善高强韧性钢的韧性,但其强度也有较为明显的降低,且生产效率及成本较高。中国专利201110259342.1一种双相热成形钢的制备方法,该钢的主要化学成分质量百分比为::c:0.10~0.50%,si:0.30~2.50%,mn:1.0~3.0%,p:≤0.02%,s:≤0.01%,al:1.0~3.0%,n:≤0.01%,余量为fe及不可避免杂质;制造方法为:首先根据化学成分进行冶炼铸造,原料坯入加热炉加热,加热温度为1200~1250℃,保温0.5~1.5小时,终轧温度为800~900℃,卷取温度为600~700℃;热成形工艺为:加热温度为750~850℃,保温3~8min,以大于40℃/s的速度冷却至室温,主要通过设置热成形工艺的加热温度为780~850℃,进而使得热成形钢处于奥氏体和铁素体对应的两个相区,快冷即可获得铁素体和马氏体构成的双相组织。通过此方法虽然使得成形后的钢板塑性增加,但强度大幅降低。中国专利201410209907.9汽车用高抗弯性能热成形钢及其制造方法,该钢的主要化学成分质量百分比为:c:0.18~0.30%,si:≤0.30%,mn:1.00~1.60%,p:≤0.015%,s:≤0.0020%,nb:0.02%~0.10%,mo:0.15%~0.40%,v:≤0.10%,w:≤0.40%,ti:0.02%~0.06%,cr:0.10~0.30%,b:0.0005~0.0040%,al:0.020~0.060%,n:≤0.004%,o:≤0.003%,余量为fe及不可避免杂质;制造方法为:首先根据化学成分进行冶炼铸造,原料坯入加热炉加热至1100~1250℃,保温2.8~4小时,精轧温度控制在820~890℃,卷取温度为540~650℃,然后再进行冷轧退火处理。热成形工艺为:加热至奥氏体化温度,保温,以大于40℃/s的速度模淬至小于等于200℃。该方法通过加入大量的合金元素,细化晶粒,从而提高热成形钢的塑韧性。但是,大量的合金元素加入大大增加了材料的制造成本;同时,这种热成形钢是在传统热成形钢的基础进行的改进,主要还是通过添加b元素来提高淬透性,b元素的添加给钢区生产带来了一定的难度。技术实现要素:因此,基于上述背景,本文开发了一种汽车用高韧性热成形钢及其制造方法。(1)与中国专利200810112020.2(主要通过添加0.50~2.30%的si,在热成形工序中马氏体转变前采用缓冷工艺获得一定量残余奥氏体的方法,提高延伸率。然而此方法热成形时工艺控制难度大,缓冷工艺使生产效率降低)相比,本专利仅通过合金元素的控制,获得高韧性的热成形钢,提高了生产效率;(2)与中国专利201110269388.1以及中国专利201110259342.1(利用软相组织来提高钢的韧性,但钢的强度降低)相比,本专利在保证热成形钢强度的同时,提高了韧性;(3)与中国专利201410209907.9相比,本专利成分设计不含ti、mo、b等元素,合金成本更低、炼钢工艺更易控制;同时也提高了热成形钢的延伸率与抗弯性能(弯曲角度大于80°)。(4)根据某高端主机厂要求,热成形钢在成形后的三点弯曲角度必须≥60°,本发明获得的热成形钢三点弯曲角度达到了80°以上。为实现本发明钢的制造,成分选择、工艺过程和工艺内容如下:1)主要化学成分重量百分比为:c:0.1~0.25;si:0.1~0.5;mn:1.0~2.0;p:≤0.020;s:≤0.010;al:0.01~0.06;cr:0.1~0.5;nb:0.01~0.06。余量为fe和不可避免的杂质。2)生产工艺采用炼钢→热轧→酸轧→连退;3)采用专用保护渣;4)加热出炉温度控制在1150℃~1250℃;5)终轧温度控制在850℃~950℃;6)卷取温度:550℃~700℃;7)酸轧压下率:50%~70%;8)退火温度:700℃~850℃;9)热成形加热温度:900℃~950℃;10)保温时间:3min~10min;11)保压时间:3s~12s。本发明在成功开发出的热成形钢屈服强度≥1000mpa、抗拉强度≥1500mpa、延伸率≥10%,三点弯曲角度≥80°。说明钢板在具有高强度的同时也有良好的抗弯曲性能。附图说明图1(a)热成形前钢的组织:铁素体+珠光体;图1(b)热成形后的组织:马氏体;图2vda238-100冷弯性能检测标准具体实施方式下面根据附图对本发明进行详细描述,其为本发明多种实施方式中的一种优选实施例。铸坯化学成分(wt%)为:c:0.1~0.25;si:0.1~0.5;mn:1.0~2.0;p:≤0.020;s:≤0.010;al:0.01~0.06;cr:0.1~0.5;nb:0.01~0.06。余量为fe和不可避免的杂质。1)铁水预处理:要求前后扒渣;2)转炉冶炼:出钢进行脱氧合金化;同时加强出钢挡渣操作;3)氩站:进行强搅操作对钢包顶渣初步还原;4)lf炉精炼:出站前保证喂钙线ca含量控制在0.0030~0.0050%;5)rh炉精炼:真空度在300pa以下保持时间12min以上;6)连铸:中包目标温度控制在液相线温度以上20~40℃,采用专用保护渣;二次冷却采用弱冷制度;7)加热出炉温度控制在1150℃~1250℃;8)终轧温度控制在850℃~950℃;9)卷取温度:550℃~700℃;10)酸轧压下率:50%~70%;11)退火温度:700℃~850℃;12)热成形加热温度:900℃~950℃;13)保温时间:3min~10min;14)保压时间:3s~12s。钢水的化学成分见表1,其余为fe和不可避免的杂质元素。表1实施例化学成分,wt%实施实例csimnpsalcrnb10.220.261.270.01/0.0320.350.03120.220.271.280.01/0.0320.370.032钢水连铸后,进行热轧轧制,然后再进行酸轧和连续退火,最后经过热成形冲压,典型显微组织如图1所示。图1为本发明所涉及的高抗弯性能热成形钢的显微组织照片为4%硝酸腐蚀后显微组织照片,组织为铁素体+珠光体;热成形后的组织为98%以上的马氏体组织。其主要工艺参数和最终力学性能见表2。表2生产工艺与产品力学性能上面结合附图对本发明进行了示例性描述,显然本发明具体实现并不受上述方式的限制,只要采用了本发明的方法构思和技术方案进行的各种改进,或未经改进直接应用于其它场合的,均在本发明的保护范围之内。当前第1页12