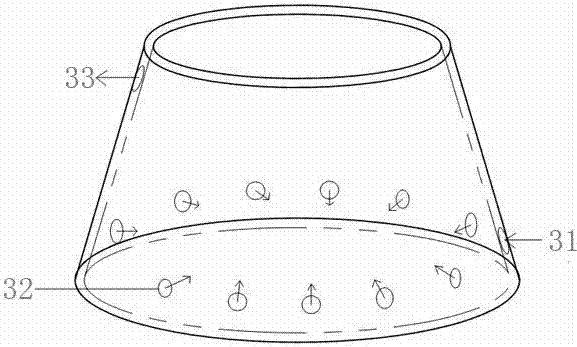
本发明涉及材料制备
技术领域:
,具体的说是一种耐高温浓硫酸用高硅不锈钢制造方法及其设备。
背景技术:
:硫酸是一种腐蚀性强、腐蚀过程复杂的基本化工原料,高温浓硫酸产生氢去极化腐蚀和氧去极化腐蚀。在高温浓硫酸中,高硅不锈钢具有极其优异的耐腐蚀性能,是硫酸工业中的首选材料。由于高硅不锈钢的特殊应用环境,不仅要求材料在高温浓硫酸中具有优良的耐点腐蚀缝隙腐蚀和应力腐蚀开裂性能,而且要求其具有优良的塑性变形性能,可用于锻造开坯、热轧、冷轧等加工变形工艺,满足低成本生产和工业应用。通过对高硅钢相关专利进行检索,分析如下:专利“cn101228287a”公开了一种高硅不锈钢及其材料与高硅不锈钢的制造方法,该专利所描述的高硅钢的特征在于,各元素的重量百分比为:c:0.02;si:4;cr:12;ni:7;余量为fe。该专利的优点是:通过细化晶粒的方法,使材料具有较高断裂延伸率,以此材料可以制作长寿命、高耐磨的弹簧,应用于高荷重的负荷环境中。专利“cn1544680a”公开了一种高硅钢及其制造方法,该专利所描述的高硅钢的特征在于,各元素的重量百分比为:c:0.007-1;si:5-10;cr≤0.01;ni≤0.01;mn≤0.01;p≤0.01;s≤0.01;余量为fe。该专利的优点是:改善了硅钢的拉伸塑性和加工性能,有利于不同厚度高硅片大规模生产,利用热机械处理技术,控制其显微组织、碳含量和软磁性能。专利“cn101985679a”公开了一种高硅钢板的短流程生产工艺,该专利所描述的高硅钢的特征在于,各元素的重量百分比为:si:3.5-7;余量为fe。该专利的优点是:采用离心浇注方法生产的三层复合金属管坯,三层金属为硅含量不同的高硅钢,利用热塑性变形与冷轧相结合的方法,生产出厚度为0.1-1mm的钢板。专利“cn102139279a”公开了一种利用定向凝固板坯制备取向高硅钢冷轧薄板的方法,该专利所描述的高硅钢的特征在于,各元素的重量百分比为:si:4.5-1.0;b:50-2000ppm;余量为fe。该专利的优点是:采用重熔定向凝固技术制备<110>方向生长的定向板坯,然后,再进行轧制,获得取向高硅钢薄板,使高硅钢的软磁性能进一步提高。专利“cn102321785a”公开了一种高硅低氧洁净钢的冶炼方法,该专利所描述的高硅钢牌号为60si2mna,该专利的优点是:采用al粒+电石渣渣面扩散脱氧,禁止使用硅铁粉或者碳化硅,将钢中的氧含量控制在6-10ppm,提高炉高硅钢的疲劳性能。专利“cn103266215a”公开了一种基于合金化的高硅钢薄带及其制造方法,该专利所描述的高硅钢的特征在于,各元素的重量百分比为:si:5.5-7.0;cu:0.05-2.5;余量为fe及不可避免的杂质。该专利的优点是:采用合金化的方法不仅改善炉高硅钢薄带的低温延展性,还保证炉其具有较好的软磁性能,使高硅钢薄带可以通过传统轧制方式进行制备。专利“cn104372238a”公开了一种取向高硅钢的制备方法,该专利所描述的高硅钢的特征在于,各元素的重量百分比为:c:0.001-0.003;si:5.0-6.6;mn:0.2-0.3;al:0.05-0.12;v:0.01-0.03;nb:0.03-0.06;s:0.02-0.03;n:0.009-0.02;o:≤0.002;余量为fe及不可避免的杂质。该专利的优点是:设计抑制剂,通过铸带晶粒凝固-长大行为控制盒抑制剂元素固溶析出行为设计,实现组织-织构-析出柔性控制,得到高磁感取向高硅钢。专利“cn104630619a”公开了一种用于薄板坯连铸连轧生产的高硅钢及制备方法,该专利所描述的高硅钢的特征在于,各元素的重量百分比为:c≤0.003;si:4.5-7.0;mn:0.25-1.0;al≤0.008;s≤0.005;n≤0.003;o:≤0.002;余量为fe及不可避免的杂质。该专利的优点是:采用连铸连轧短流程,获得柱状晶体积比例不低于90%,细纤维组织、磁性能良好的高硅钢。这些专利所涉及的为合金含量低的高硅钢,主要用来制作各种变压器、电动机和发电机的铁芯,应用于电力、电子和军事工业的重软磁性材料。但是,均不能应用于高温硫酸环境中。通过文献检索,20世纪80年代国外开始研究应用于高温硫酸环境中的高硅不锈钢,相继开发出多个牌号的高硅不锈钢,但是,其生产制造工艺均未见报道公开,国内在高硅不锈钢的研究还处于起步阶段。目前,生产高硅不锈钢主要采用两种制造工艺,第一种工艺为:电弧炉+aod(氩氧脱碳)或者vod(真空吹氧脱碳)炉外精炼工艺冶炼钢锭,将钢锭锻造开坯后进行热轧、冷轧。该工艺的优点是:生产效率高,成本低。该工艺的缺点是:钢锭的锻造开坯成材率低,最高75%,材料的纯净度低,夹杂物含量高,影响材料的耐腐蚀性能。第二种工艺为:电弧炉或者中频感应炉+aod(氩氧脱碳)+保护气氛电渣炉工艺冶炼钢锭,将钢锭锻造开坯后进行热轧、冷轧。该工艺的优点是:采用电渣重熔工艺提高钢锭的利用率,可以将钢锭锻造开坯成材率提高至95%。材料的成分均匀性、纯净度高,夹杂物含量低,材料具有更优异的耐腐蚀性能。该工艺的缺点是:为了避免电渣重熔过程中si元素的烧损,采用全保护气氛电渣重熔炉冶炼,避免大气中的氧气进入钢中烧损si元素,而全保护气氛电渣重熔炉设备投资高,是常规电渣重熔炉的5-6倍,造成生产成本高,吨钢生产成本是常规电渣重熔炉的2倍,难以推广应用。技术实现要素:本发明目的是为解决上述技术问题的不足,提供一种耐高温浓硫酸用高硅不锈钢制造方法及其设备,该方法和设备所制备的高硅不锈钢,在高温环境下,耐浓硫酸腐蚀性强。本发明为解决上述技术问题所采用的技术方案是:一种耐高温浓硫酸用高硅不锈钢制造方法,包括以下步骤:(1)通过模拟相图,匹配各元素的含量,设计出钢锭的化学成分组成,保证高硅不锈钢处于稳定的奥氏体区,减少钢锭中的δ铁素体含量,获得均匀的奥氏体组织;各元素组成及质量百分比含量为:c≤0.03;si:5.2-5.8;mn≤1.0;p≤0.025;s≤0.01;cr:17.5-18.5;ni:21-22;mo:0.5-1.3;cu:2.0-2.5;al:≤0.05;ce:≤0.05;nb:0.02-0.05;o:≤0.006;n:≤0.01;其余为不可避免的杂质和fe;(2)、通过中频感应炉初炼+氩氧脱碳(aod)炉精炼工艺冶炼圆形电极;所述电极的元素组成及重量百分比为:c≤0.03;si:5.8-6.0;mn≤1.0;p≤0.025;s≤0.01;cr:17.5-18.5;ni:21-22;mo:0.5-1.3;cu:2.0-2.5;al:0.04-0.06;ce≤0.05;nb:0.02-0.05;o:≤0.006;n:≤0.01;其余为不可避免的杂质和fe;电极的直径d与钢锭的直径d的比值为0.7-0.8;(3)、通过电渣重熔(esr)工艺冶炼钢锭。所述电渣重熔(esr)工艺,包括以下步骤:(1)、将电极表面的氧化皮清理干净,并将其焊接在假电极上,送入井式电阻加热炉内,电极预热至500-600℃,保温5-6小时,去除电极表面的水分;(2)、选用的渣料组元和重量百分比为:caf260%~70%,al2o315%~20%,cao10%~20%,sio22%~5%,渣料为50-200kg,渣料烘烤温度为800℃,烘烤时间为8-10小时;(3)、采用石墨电极引弧造渣,将烘烤好的渣系按照caf2、sio2、cao、al2o3的顺序加入到结晶器中,将渣料熔化成液态,液态渣温度控制在1650-1700℃;(4)、将自耗电极移至液态渣池内,在大气环境下,开始电渣重熔,电渣锭的直径用d表示,根据钢锭直径d的大小选择相应的电极熔化速度v,其中,v=(0.7-0.8)×d,电渣锭直径d的单位为mm,电极熔化速度v的单位为kg/h;(5)、冶炼过程中向渣池中均匀的加入硅钙粉进行脱氧,硅钙粉在渣面与大气中的氧气反应生成cao和sio2,减少大气中的氧气进入液态渣池中,氧化钢液中的si元素;电极的重量表示为w,w的单位为kg,硅钙粉的加入量表示为w1,w1的单位为g,硅钙粉的加入量为:w1=(3-4)×w;将电渣重熔冶炼过程平均分成两个阶段,电渣重熔开始,硅钙粉的加入频率表示为m1,m1的单位为g/min,硅钙粉的加入频率为:m1=(3-4)×v/60;当电极重量冶炼至一半时,硅钙粉的加入频率表示为m2,m2的单位为g/min,硅钙粉的加入频率为:m2=(1-3)×v/60;电渣重熔补缩期,硅钙粉的加入频率表示为m3,m3的单位为g/min,硅钙粉的加入频率为:m3=(0.5-2)×v/60;所述硅钙粉si:ca=1:1;(6)、冶炼过程中,炉口放置保护罩,保护装置内通入氩气,氩气的流量控制在20-40m3/h;保护罩内的氩气通过其内壁上的小孔流出,在炉口汇集形成保护层,减少了大气中的氧气进入液态渣池内;(7)、电极熔化完毕后,钢锭在结晶器内缓慢冷却40-90分钟,保证液态金属和熔渣凝固充分,钢锭脱模后空冷至室温。用于所述耐高温浓硫酸用高硅不锈钢制造方法的设备,包括电极和液态渣池;在液态渣池上方设有保护罩,所述保护罩设有内腔,内腔中设有电极;保护罩底部设有惰性气体的内壁出气孔,侧面下方设有惰性气体的主进气孔,侧面上方设有惰性气体的主进气孔。有益效果是:(1)在大气环境下,采用常规的电渣重熔炉冶炼钢锭,降低了设备投资和钢锭的制造成本,具有明显的经济效益;(现有技术:采用全密闭保护气氛电渣重熔炉冶炼工艺。为什么不采用常规的电渣重熔炉冶炼钢锭的原因:此材料含有大量的易氧化元素si,此工艺高温钢液与大气中的氧始终接触,容易在冶炼过程中发生氧化反应,生产sio2,造成材料中的si元素减少,甚至不合格,工艺稳定性差,难以控制);(2)通过设计保护罩,冶炼过程中在电渣重熔炉口形成惰性气体保护层,并在冶炼的不同阶段,均匀的向渣中加入不同剂量的硅钙粉脱氧剂,有效控制了硅元素的烧损,冶炼出低氮、低氧、成分均匀的高硅奥氏体不锈钢钢锭,通过优于成分设计,加入微量ce、nb、al等合金元素,提高了钢的热加工性能和耐腐蚀性能。(3)本发明制造工艺简单,生产成本低廉,钢锭具有良好的成分均匀性,优异的耐高温硫酸腐蚀性能,能够应用在硫酸工业的恶略腐蚀环境中,大大延长了产品的使用寿命,提高设备的安全性,具有良好的社会效益;耐高温硫酸腐蚀性根据标准进行实验,以材料表面没有腐蚀现象为标准,现有技术的腐蚀数据:在150℃的98%浓度的h2so4溶液中,平均腐蚀速率为0.09-0.125mm/年,本发明的腐蚀速率为小于0.08mm/年。附图说明图1是本发明耐高温浓硫酸用高硅不锈钢制造方法的设备结构示意图;图2是本发明耐高温浓硫酸用高硅不锈钢制造方法设备的保护罩结构示意图;图中标记是:1、电极升降机构,2、电极,3、保护罩,4、液态渣池,5、金属熔池,6、结晶器,7、钢锭,8、底水箱,9、控制系统;31、主进气孔,32、内壁出气孔,33、主出气孔。具体实施方式一种耐高温浓硫酸用高硅不锈钢制造方法,包括以下步骤:(一)通过模拟相图,匹配各元素的含量,设计出钢锭的化学成分组成,保证高硅不锈钢处于稳定的奥氏体区,减少钢锭中的δ铁素体含量,获得均匀的奥氏体组织;各元素组成及质量百分比含量为:c≤0.03;si:5.2-5.8;mn≤1.0;p≤0.025;s≤0.01;cr:17.5-18.5;ni:21-22;mo:0.5-1.3;cu:2.0-2.5;al:≤0.05;ce:≤0.05;nb:0.02-0.05;o:≤0.006;n:≤0.01;其余为不可避免的杂质和fe;(二)、通过中频感应炉初炼+氩氧脱碳(aod)炉精炼工艺冶炼圆形电极;所述电极的元素组成及重量百分比为:c≤0.03;si:5.8-6.0;mn≤1.0;p≤0.025;s≤0.01;cr:17.5-18.5;ni:21-22;mo:0.5-1.3;cu:2.0-2.5;al:0.04-0.06;ce≤0.05;nb:0.02-0.05;o:≤0.006;n:≤0.01;其余为不可避免的杂质和fe;电极的直径d与钢锭的直径d的比值为0.7-0.8;本发明增加了al、ce元素的含量,达到的效果:降低钢锭中杂质o元素的含量,提高钢锭的热加工性能。增加了nb元素的含量,达到的效果:提高材料的耐腐蚀性能。钢锭化学成分设计原理如下:(1)c≤0.03%碳是强烈形成并稳定奥氏体元素,并能提高材料的机械性能,但是,碳含量过高能明显促进碳化物cr23c6沿晶间析出,导致晶界贫铬,使材料的耐晶间腐蚀性能下降。高硅不锈钢在冶炼过程中尽量降低碳含量,但是,碳含量过低,会显著地增加冶炼成本。因此,本发明的碳元素含量重量百分比为:c≤0.03%,碳元素含量重量百分比的优选范围为:c≤0.02%。(2)si:5.2-5.8si是重要的耐蚀合金元素之一,具有优良的抗氧化性能,能够在不锈钢的表面生成sio2氧化膜。si≤5.2时,不能与不锈钢中的铬、镍元素形成一些阴极性的含硅复合化合物,促进不锈钢的钝化,造成不锈钢的耐蚀性降低。si≥5.8时,过高的含硅量使铬、镍的钝化作用减弱,反而减弱不锈钢的耐蚀性。而且,过量的铁素体形成元素硅会使钢锭中产生大量的一次δ铁素体,降低钢锭的热加工塑性。因此,本发明的硅元素含量重量百分比为:si:5.2-5.8,硅元素含量重量百分比的优选范围为:5.5-5.8。(3)mn≤1%mn对不锈钢在浓硫酸中的耐蚀性影响不大,主要是作为脱氧剂带入钢中的,考虑到钢在冶炼过程中的脱氧效果和冶炼经济性,本发明的mn元素含量重量百分比为:mn≤1%(4)s≤0.01%s是钢中的杂质元素,能够降低材料的热加工性能和耐腐蚀性能,因此,s在钢中的含量越低越好,根据本发明所采取的冶炼工艺,在不增加生产成本的基础上,s元素含量重量百分比为:s≤0.01%,s元素含量重量百分比的优选范围为:s≤0.006%。(5)p≤0.025%p是钢中的杂质元素,容易聚集在晶界恶化材料的性能,因此,p在钢中的含量越低越好,根据本发明所采取的冶炼工艺,在不增加生产成本的基础上,磷元素含量重量百分比为:p≤0.025%,硫元素含量重量百分比的优选范围为:p≤0.02%。(6)17.5%≤cr≤18.5%cr元素显著提高材料的耐腐蚀性能,对提高不锈钢在高温浓硫酸中的耐腐蚀性能作用仅次于si。因此,cr元素是本发明高硅不锈钢必不可缺的元素。当cr≤17.5%时,不能与硅、镍元素形成足够厚的含硅复合化合物薄膜,造成不锈钢的耐蚀性降低。同时,cr元素是强烈形成并稳定铁素体的元素,缩小单相奥氏体区,随着cr含量的增加,能够促进金属间相的析出,从而降低材料的塑韧性。当cr元素含量重量百分比大于18.5%时,材料的奥氏体组织稳定性变差,钢中会保留一定数量的高温铁素体组织,降低材料的热加工塑性。因此,本发明的cr元素含量重量百分比为:17.5%≤cr≤18.5%。(7)21%≤ni≤22%镍对提高不锈钢在高温浓硫酸中的耐腐蚀性能有一定作用,但不十分明显。在本发明中,镍是强烈形成并稳定奥氏体且扩大单相奥氏体区的元素,其主要作用是维持镍、铬当量的平衡,得到稳定的奥氏体组织,保证变形性能。因此,本发明的ni元素含量重量百分比为:21%≤ni≤22%。(8)0.5%≤mo≤1.3%mo元素可以促进不锈钢钝化。当mo≤0.5%时,通过铬、钼的复合作用提高不锈钢在浓硫酸中的耐蚀性的作用不明显;当mo≥1.3%时,钼在氧化性介质浓硫酸中极易产生过钝化,对不锈钢的耐蚀性不利。因此,本发明的mo元素含量重量百分比为:mo:0.5%≤mo≤1.3%,mo元素含量重量百分比的优选范围为:0.6%≤mo≤1.0%。(9)2.0%≤cu≤2.5%cu元素可以提高不锈钢在浓硫酸中的耐腐蚀性。主要原因为:铜的电极电位比氢高,可抑制析氢腐蚀。但是,cu元素含量过高会降低钢的热加工塑性。因此,本发明的cu元素含量重量百分比为:mo:2%≤mo≤2.5%。(10)0.02%≤nb≤0.05%铌是稳定化元素,铌与碳的结合力强于铬元素,钢中加入铌后,优先与碳结合形成化合物在晶内或者晶界析出,不仅可以抑制cr23c6析出,提高材料的抗腐蚀性能,而且铌的析出物可以提高材料的强度,当铌的添加量重量百分比超过0.05%时,强化作用达到饱和。当铌的添加量重量百分比低于0.02%时,不能有效抑制cr23c6析出,影响耐腐蚀性能。因此,本发明的nb元素含量重量百分比为:0.02%≤nb≤0.05%。(11)ce:≤0.05稀土ce可以改变钢中易于形成点蚀的硫化物夹杂的成分和形态,降低钢中的硫含量,提高钢的耐点蚀能力。另外,稀土ce可以在晶界和碳化物-基体界面上富集,提高钢锭的热加工性能,当ce的添加量重量百分比超过0.05%时,生产成本提高。因此,本发明的ce元素含量重量百分比为:ce≤0.05%。(12)al≤0.05%al元素主要是作为脱氧剂带入钢中的,另外,钢中适量的铝可以抑制电渣重熔过程中硅元素的烧损。当al≥0.05%时,会形成粗大的晶粒,使钢锭的热加工性能降低。考虑到钢在冶炼过程中的脱氧效果、电渣重熔冶炼过程中硅元素的烧损规律,本发明的al元素含量重量百分比为:al≤0.05%。(13)n≤0.01%n元素是钢中的杂质元素,会在钢中形成氮化物,影响钢的耐腐蚀性能,需要进行严格控制。n元素含量控制的越低,钢的使用性能越好,但是,会大大增加冶炼工艺的难度和生产成本,不适合批量生产应用。因此,结合制造工艺的适应性的生产成本,本发明的n元素含量重量百分比为:n≤0.01%。(14)o≤0.006%氧含量过高会恶化钢的纯净度,降低钢锭的热加工性能,材料的耐腐蚀性能以及韧性,氧含量过低会增加冶炼成本。因此,综合考虑冶炼成本和材料的使用性能,本发明的o元素含量重量百分比为:o≤0.006%。(三)、通过电渣重熔(esr)工艺冶炼钢锭。所述电渣重熔(esr)工艺,包括以下步骤:(1)、将电极表面的氧化皮清理干净,并将其焊接在假电极上,送入井式电阻加热炉内,电极预热至500-600℃,保温5-6小时,去除电极表面的水分;(2)、选用的渣料组元和重量百分比为:caf260%~70%,al2o315%~20%,cao10%~20%,sio22%~5%,渣料为50-200kg,渣料烘烤温度为800℃,烘烤时间为8-10小时;(3)、采用石墨电极引弧造渣,将烘烤好的渣系按照caf2、sio2、cao、al2o3的顺序加入到结晶器中,将渣料熔化成液态,液态渣温度控制在1650-1700℃;(4)、将自耗电极移至液态渣池内,在大气环境下,开始电渣重熔,电渣锭的直径用d表示,根据钢锭直径d的大小选择相应的电极熔化速度v,其中,v=(0.7-0.8)×d,电渣锭直径d的单位为mm,电极熔化速度v的单位为kg/h;(5)、冶炼过程中向渣池中均匀的加入硅钙粉进行脱氧,硅钙粉在渣面与大气中的氧气反应生成cao和sio2,减少大气中的氧气进入液态渣池中,氧化钢液中的si元素;电极的重量表示为w,w的单位为kg,硅钙粉的加入量表示为w1,w1的单位为g,硅钙粉的加入量为:w1=(3-4)×w;将电渣重熔冶炼过程平均分成两个阶段,电渣重熔开始,硅钙粉的加入频率表示为m1,m1的单位为g/min,硅钙粉的加入频率为:m1=(3-4)×v/60;当电极重量冶炼至一半时,硅钙粉的加入频率表示为m2,m2的单位为g/min,硅钙粉的加入频率为:m2=(1-3)×v/60;电渣重熔补缩期,硅钙粉的加入频率表示为m3,m3的单位为g/min,硅钙粉的加入频率为:m3=(0.5-2)×v/60;所述硅钙粉si:ca=1:1;(6)、冶炼过程中,炉口放置保护罩,保护装置内通入氩气,氩气的流量控制在20-40m3/h;保护罩内的氩气通过其内壁上的小孔流出,在炉口汇集形成保护层,减少了大气中的氧气进入液态渣池内;(7)、电极熔化完毕后,钢锭7在结晶器内缓慢冷却40-90分钟,保证液态金属和熔渣凝固充分,钢锭脱模后空冷至室温。用于所述耐高温浓硫酸用高硅不锈钢制造方法的设备,设备包括电极升降机构1、电极2、结晶器6、底水箱8、保护罩3、液态渣池4、金属熔池5和控制系统9等部分,如图1所示;所述升降机构的作用为:将电极夹持牢固后插入结晶器中,自上至下传动。所述电极的作用为:电极熔化后在结晶器内重新凝固成电渣锭。所述结晶器的作用为:电极被高温液态渣池逐渐熔化后,金属液滴滴到结晶器内形成金属熔池,金属熔池在结晶器冷却水的冷却条件下,凝固成电渣锭。所述保护罩设在液态渣池上方,所述保护罩3设有内腔,内腔中设有电极2;保护罩3底部设有惰性气体的内壁出气孔32,侧面下方设有惰性气体的主进气孔31,侧面上方设有惰性气体的主进气孔33。一定压力的惰性气体从31孔进去,从32、33孔出去,其中从32出去的气体在设备炉口形成一层惰性气体,起与大气中的氧隔离作用)所述保护罩3的作用为:在电渣重熔过程中,通入保护罩内的氩气从其内壁四周的小孔内流出,在结晶器上口形成氩气保护层,阻止大气中的氧进入液态渣池中,氧化金属液滴中的硅元素,如图2所示。所述底水箱的作用为:在电渣重熔刚开始阶段,与结晶器形成封闭的空间,金属熔滴滴落在该空间内形成金属熔池。所述控制系统的作用为:控制升降机构下降速度。以下结合实施例对本发明加以详细说明:实施例1:φ360mm的高硅不锈钢电渣重熔锭。第一步、采用“中频感应+aod精炼”工艺冶炼自耗电极,电极规格为φ260mm×2500mm,电极的化学成分如表1所示。表1电极化学成分(重量%)第二步、将自耗电极表面打磨干净。第三步,根据热力学原理,计算si烧损反应达到平衡时出渣系中所需的sio2理论含量,然后由sio2理论含量选择匹配的渣系,具体方法为:(1)电渣重熔阶段,电极插入液态熔渣中逐渐熔化,金属液滴穿过渣池的过程中,发生反应:[si]+2[o]=sio2公式1根据热力学原理,当反应达到化学平衡时:公式2-480626+213.389t公式3=公式4=公式5lg=公式6lg=公式7为1873k时,钢液中各个元素与si的相互作用系数,为1873k时,钢液中各个元素与o的相互作用系数。t为化学反应式的平衡温度,1873k;r为气体常数,8.314。利用公式1~公式7,计算出的活度值为:=0.031,则设计渣系中的sio2的理论摩尔浓度为0.031,质量百分比为2%。第三步、制备渣料。渣系采用caf2、al2o3、cao、sio2四元渣系,各组元的重量百分比分别为70%、15%、13%、2%,渣量50kg。将渣料分开置入电炉内,温度控制在850℃,烘烤8小时。第四步,将保护罩放置在结晶器上,接好氩气的进口和出口;第五步,将烘烤好的渣系按照caf2、sio2、cao、al2o3的顺序加入结晶器内,采用石墨电极将渣料熔化成液态,液态渣温控制在1650-1700℃,保证渣系化开、化清;第六步,将预热好的自耗电极移至液态渣池内,开始电渣重熔,电压为38-52v,电流为0.4-0.8ka,电极熔化速度为290kg/h,氩气的流量为20m3/h,保护罩内的氩气通过其内壁上的小孔流出,在炉口汇集形成保护层,减少了大气中的氧气进入液态渣池内。电渣重熔开始,硅钙粉的加入频率为m1=15g/min。当电极重量冶炼至一半时,硅钙粉的加入频率表为m2=10g/min。电渣重熔补缩期,硅钙粉的加入频率m3=5g/min;第七步,电极熔化完毕后,钢锭在结晶器内缓慢冷却40分钟,保证液态金属和熔渣凝固充分,钢锭脱模后空冷至室温。直径为φ360mm的高硅不锈钢钢锭表面质量良好,没有重皮、夹渣、波纹等缺陷。根据gb/t1979-2001《结构钢低倍组织缺陷评级图》标准,对实施例钢锭内部质量进行检测,未发现疏松、偏析、白亮带、皮下气泡、残余缩孔、翻皮、白点、轴心晶间裂纹、内部气泡、非金属夹杂物及夹渣、异金属夹杂物等缺陷,钢锭内部质量良好。钢锭经锻造后,具有良好的热加工性能。根据gb/t4334.6-2015《不锈钢5%硫酸腐蚀试验方法》、jb/t7901-1999《金属材料实验室均匀腐蚀全浸试验方法》要求,将试样放置在150℃的98%浓度的h2so4溶液中浸泡7天,试样表面没有明显变化,没有发生局部腐蚀现象,平均腐蚀速率为0.075mm/年,可见,本发明高硅不锈钢具有良好的耐腐蚀性能。实施例2:φ440mm的高硅不锈钢电渣重熔锭。第一步、采用“中频感应+aod精炼”工艺冶炼自耗电极,电极规格为φ310mm×3500mm,电极的化学成分如表1所示。表2电极化学成分(重量%)第二步、将自耗电极表面打磨干净。第三步,按照实施1的方法计算出的活度值为:=0.04,则设计渣系中的sio2的理论摩尔浓度为0.04,质量百分比为3%。第三步、制备渣料。渣系采用caf2、al2o3、cao、sio2四元渣系,各组元的重量百分比分别为69%、15%、13%、3%,渣量80kg。将渣料分开置入电炉内,温度控制在850℃,烘烤8小时。第四步,将保护罩放置在结晶器上,接好氩气的进口和出口;第五步,将烘烤好的渣系按照caf2、sio2、cao、al2o3的顺序加入结晶器内,采用石墨电极将渣料熔化成液态,液态渣温控制在1650-1700℃,保证渣系化开、化清;第六步,将预热好的自耗电极移至液态渣池内,开始电渣重熔,电压为60-40v,电流为0.5-11.5ka,电极熔化速度为360kg/h,氩气的流量为25m3/h,保护罩内的氩气通过其内壁上的小孔流出,在炉口汇集形成保护层,减少了大气中的氧气进入液态渣池内。电渣重熔开始,硅钙粉的加入频率为m1=20g/min。当电极重量冶炼至一半时,硅钙粉的加入频率表为m2=12g/min。电渣重熔补缩期,硅钙粉的加入频率m3=6g/min;第七步,电极熔化完毕后,钢锭在结晶器内缓慢冷却50分钟,保证液态金属和熔渣凝固充分,钢锭脱模后空冷至室温。直径为φ440mm的高硅不锈钢钢锭表面质量良好,没有重皮、夹渣、波纹等缺陷。根据gb/t1979-2001《结构钢低倍组织缺陷评级图》标准,对实施例钢锭内部质量进行检测,未发现疏松、偏析、白亮带、皮下气泡、残余缩孔、翻皮、白点、轴心晶间裂纹、内部气泡、非金属夹杂物及夹渣、异金属夹杂物等缺陷,钢锭内部质量良好。钢锭经锻造后,具有良好的热加工性能。根据gb/t4334.6-2015《不锈钢5%硫酸腐蚀试验方法》、jb/t7901-1999《金属材料实验室均匀腐蚀全浸试验方法》要求,将试样放置在150℃的98%浓度的h2so4溶液中浸泡7天,试样表面没有明显变化,没有发生局部腐蚀现象,平均腐蚀速率为0.064mm/年,可见,本发明高硅不锈钢具有良好的耐腐蚀性能。实施例3:φ560mm的高硅不锈钢电渣重熔锭。第一步、采用“中频感应+aod精炼”工艺冶炼自耗电极,电极规格为φ420mm×3000mm,电极的化学成分如表3所示。表3电极化学成分(重量%)合金csimnspcrnimocualcenbon电极0.0155.50.60.010.01718.0521.50.662.20.040.040.040.0060.007第二步、将自耗电极表面打磨干净。第三步,按照实施1的方法计算出的活度值为:=0.05,则设计渣系中的sio2的理论摩尔浓度为0.05,质量百分比为4%。第三步、制备渣料。渣系采用caf2、al2o3、cao、sio2四元渣系,各组元的重量百分比分别为61%、20%、15%、4%,渣量120kg。将渣料分开置入电炉内,温度控制在850℃,烘烤8小时。第四步,将保护罩放置在结晶器上,接好氩气的进口和出口;第五步,将烘烤好的渣系按照caf2、sio2、cao、al2o3的顺序加入结晶器内,采用石墨电极将渣料熔化成液态,液态渣温控制在1650-1700℃,保证渣系化开、化清;第六步,将预热好的自耗电极移至液态渣池内,开始电渣重熔,电压为54-62v,电流为7-16ka,电极熔化速度为450kg/h,氩气的流量为35m3/h,保护罩内的氩气通过其内壁上的小孔流出,在炉口汇集形成保护层,减少了大气中的氧气进入液态渣池内。电渣重熔开始,硅钙粉的加入频率为m1=30g/min。当电极重量冶炼至一半时,硅钙粉的加入频率表为m2=15g/min。电渣重熔补缩期,硅钙粉的加入频率m3=10g/min;第七步,电极熔化完毕后,钢锭在结晶器内缓慢冷却70分钟,保证液态金属和熔渣凝固充分,钢锭脱模后空冷至室温。直径为φ560mm的高硅不锈钢钢锭表面质量良好,没有重皮、夹渣、波纹等缺陷。根据gb/t1979-2001《结构钢低倍组织缺陷评级图》标准,对实施例钢锭内部质量进行检测,未发现疏松、偏析、白亮带、皮下气泡、残余缩孔、翻皮、白点、轴心晶间裂纹、内部气泡、非金属夹杂物及夹渣、异金属夹杂物等缺陷,钢锭内部质量良好。钢锭经锻造后,具有良好的热加工性能。根据gb/t4334.6-2015《不锈钢5%硫酸腐蚀试验方法》、jb/t7901-1999《金属材料实验室均匀腐蚀全浸试验方法》要求,将试样放置在150℃的98%浓度的h2so4溶液中浸泡7天,试样表面没有明显变化,没有发生局部腐蚀现象,平均腐蚀速率为0.06mm/年,可见,本发明高硅不锈钢具有良好的耐腐蚀性能。实施例4:φ700mm的高硅不锈钢电渣重熔锭。第一步、采用“中频感应+aod精炼”工艺冶炼自耗电极,电极规格为φ500mm×3200mm,电极的化学成分如表3所示。表3电极化学成分(重量%)合金csimnspcrnimocualcenbon电极0.0255.40.30.010.0217.821.60.92.30.050.030.030.0060.007第二步、将自耗电极表面打磨干净。第三步,按照实施1的方法计算出的活度值为:=0.06,则设计渣系中的sio2的理论摩尔浓度为0.06,质量百分比为5%。第三步、制备渣料。渣系采用caf2、al2o3、cao、sio2四元渣系,各组元的重量百分比分别为60%、20%、15%、5%,渣量200kg。将渣料分开置入电炉内,温度控制在850℃,烘烤8小时。第四步,将保护罩放置在结晶器上,接好氩气的进口和出口;第五步,将烘烤好的渣系按照caf2、sio2、cao、al2o3的顺序加入结晶器内,采用石墨电极将渣料熔化成液态,液态渣温控制在1650-1700℃,保证渣系化开、化清;第六步,将预热好的自耗电极移至液态渣池内,开始电渣重熔,电压为33-78v,电流为8-17ka,电极熔化速度为560kg/h,氩气的流量为38m3/h,保护罩内的氩气通过其内壁上的小孔流出,在炉口汇集形成保护层,减少了大气中的氧气进入液态渣池内。电渣重熔开始,硅钙粉的加入频率为m1=35g/min。当电极重量冶炼至一半时,硅钙粉的加入频率表为m2=20g/min。电渣重熔补缩期,硅钙粉的加入频率m3=10g/min;第七步,电极熔化完毕后,钢锭在结晶器内缓慢冷却70分钟,保证液态金属和熔渣凝固充分,钢锭脱模后空冷至室温。直径为φ700mm的高硅不锈钢钢锭表面质量良好,没有重皮、夹渣、波纹等缺陷。根据gb/t1979-2001《结构钢低倍组织缺陷评级图》标准,对实施例钢锭内部质量进行检测,未发现疏松、偏析、白亮带、皮下气泡、残余缩孔、翻皮、白点、轴心晶间裂纹、内部气泡、非金属夹杂物及夹渣、异金属夹杂物等缺陷,钢锭内部质量良好。钢锭经锻造后,具有良好的热加工性能。根据gb/t4334.6-2015《不锈钢5%硫酸腐蚀试验方法》、jb/t7901-1999《金属材料实验室均匀腐蚀全浸试验方法》要求,将试样放置在150℃的98%浓度的h2so4溶液中浸泡7天,试样表面没有明显变化,没有发生局部腐蚀现象,平均腐蚀速率为0.068mm/年,可见,本发明高硅不锈钢具有良好的耐腐蚀性能。当前第1页12