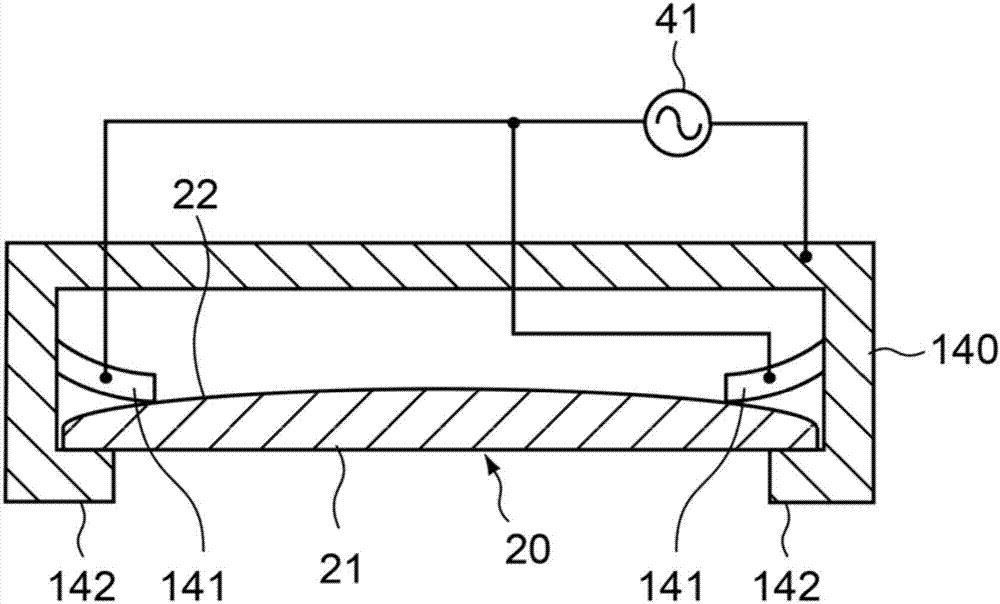
本发明涉及一种成膜工艺中使用的膜厚传感器。
背景技术:
:以往,在真空蒸镀装置等成膜装置中,为了测量被成膜于基板的膜厚度和成膜速度,使用所谓的石英振荡法(qcm:quartzcrystalmicrobalance,石英晶体微天平)的技术。该方法是利用被配置于腔室内的石英振子的谐振频率随着蒸镀物的堆积引起的质量增加而减小的方法。因此,能够通过测量石英振子的谐振频率的变化来测量膜厚和成膜速度。对于该种膜厚传感器,随着膜量的增加,石英振子的谐振频率逐步降低,当达到规定的频率时,频率的变动大到已经无法进行稳定的膜厚测量的程度。因此,谐振频率降低规定值以上时,判断石英振子达到使用寿命并实施更换。为了易于进行此更换,例如在专利文献1中公开有一种传感器头,其保持多个具有5mhz的谐振频率的石英板,并且能够各自更换所使用的石英板。另一方面,该种膜厚传感器具有所谓的抗热冲击特性引起的成膜率的测量值变动大的问题。例如,在像专利文件1中记载的使用传感器头的石英振子的更换时,或者在遮挡蒸发源的遮挡板的打开操作时,存在瞬间接受来自蒸发源的辐射热而导致石英振子频率特性大幅变动的情况。为了改善这样的问题,例如专利文件2中,公开了使石英振子的成膜面的表面粗糙度(ra)为规定值以下的技术方案,由此改善石英振子的抗热冲击特性。【现有技术文献】【专利文献】【专利文献1】日本特开2003-139505号公报【专利文献2】wo2015/182090号公报技术实现要素:【发明所要解决的问题】最近几年,在真空蒸镀装置等成膜装置中,要求膜厚传感器的高精度化,特别是关于抗热冲击特性,因为对成膜率、膜厚的控制带来的影响很大,因此开发抗热冲击特性优异的膜厚传感器成为当务之急。然而,仅仅减小石英振子的表面粗糙度仍不足以改善抗热冲击特性,需要进一步改善。此外,sc切型、it切型石英振子具有抗热冲击特性比较优异的优点,但因为与如at切型那样广泛应用的石英振子相比价格高,因此存在导致膜厚传感器的高成本化的问题。鉴于上述情况,本发明的目的在于提供一种抗热冲击特性优异、能够抑制高成本化的膜厚传感器。【用于解决问题的技术方案】为了实现上述目的,本发明人发现,使石英振子的成膜面的表面粗糙度(ra)为规定值以下,并且切割水平50%的载荷长度比率(tp)为规定值以上的情况下,石英振子的抗热冲击特性大幅改善。也就是说,本发明的一个实施方式的膜厚传感器具备石英振子。上述石英振子由具有表面粗糙度(ra)为0.4μm以下、并且切割水平50%的载荷长度比率(tp)为95%以上的成膜面的at切型石英振子构成。上述成膜面的切割水平50%的载荷长度比率(tp)优选为97%以上。此外,上述成膜面的表面粗糙度(ra)优选为0.25μm以下。上述石英振子也可以由相对于晶体的r面具有3°05'±03'的切割方位的石英振子构成。上述石英振子的基本振荡频率没有特别限制,典型地为4mhz、5mhz或6mhz。上述成膜面可以由金属膜构成。典型地,金属膜为ag膜或au膜。上述石英振子可以具有上述成膜面为平坦面的平凸形状。由此,能够得到等效电阻低、易于振动的振子。【发明效果】如上所述基于本发明的膜厚传感器,能够优化抗热冲击特性,抑制高成本化。附图说明图1是表示具有本发明一个实施方式的膜厚传感器的成膜装置的剖面简图。图2是表示上述膜厚传感器的结构的剖面简图。图3是表示在上述成膜装置中的测定单元的结构的框图。图4的a是示意性地表示在上述膜厚传感器中的石英振子的成膜面的主视图,图4的b是示意性地表示在上述膜厚传感器中的石英振子的成膜面的后视图。图5是表示上述石英振动板的抗热冲击特性的一例的图。图6是表示上述石英振动板的抗热冲击特性的一例的图。图7是表示上述石英振动板的成膜面的一例的主要部分放大图。图8是说明一般的at切基板的切割角的石英的示意图。图9是表示上述石英振动板的抗热冲击特性的一例的图。图10是表示上述石英振动板的抗热冲击特性的一例的图。图11是表示上述石英振动板的抗热冲击特性的一例的图。图12是表示上述石英振动板的抗热冲击特性的一例的图。具体实施方式以下,参照附图,对本发明的实施方式进行说明。图1是表示具有本发明的一个实施方式的膜厚传感器的成膜装置的剖面简图。本实施方式的成膜装置构成为真空蒸镀装置。本实施方式的成膜装置10具有真空腔室11、设置在真空腔室11的内部的蒸镀源12、与蒸镀源12相对设置的基板架13、设置在真空腔室11的内部的膜厚传感器14。真空腔室11构成为与真空排气系统15连接,内部能够排气为规定的减压气氛并能够保持。蒸镀源12构成为能够产生蒸镀材料的蒸汽(粒子)。在本实施方式中,蒸镀源12构成为用于加热蒸发金属材料、金属化合物材料或有机材料而放出蒸镀粒子的蒸发源。蒸发源的种类没有特别的限制,能够应用电阻加热式、感应加热式、电子束加热式等各种方式。基板架13构成为能够将半导体晶片、玻璃基板等作为成膜对象的基板w朝向蒸镀源12地进行保持。膜厚传感器14内置有具有规定基本频率(固有频率)的石英振子,如后所述,构成用于测量基板w上的蒸镀膜的膜厚及成膜率的传感器头。膜厚传感器14配置在真空腔室11的内部、且与蒸镀源12相对设置的位置。典型的是,膜厚传感器14配置在基板架13的附近。膜厚传感器14的输出向测量单元17供给。测量单元17根据石英振子的谐振频率的变化,测量上述膜厚及成膜率,并且控制蒸镀源12以使该成膜率成为规定值。qcm的吸附引起的频率变化与质量载荷的关系使用以下数学式(1)所示的sauerbrey的数学式。【数学式1】在数学式(1)中,δfs表示频率变化量、δm表示质量变化量、f0表示基本频率、ρq表示石英的密度、μq表示石英的剪切应力、a表示电极面积、n表示常数。成膜装置10还具有遮挡板16。遮挡板16被设置在蒸镀源12与基板架13之间,且构成为能够打开或遮挡从蒸镀源12至基板架13和膜厚传感器14的蒸镀粒子的入射路径。遮挡板16的开关由未图示的控制单元控制。典型的是,蒸镀开始时,遮挡板16关闭,直至在蒸镀源12稳定放出蒸镀粒子。然后,稳定放出蒸镀粒子时,遮挡板16被打开。由此,来自蒸镀源12的蒸镀粒子到达基板架13上的基板w,开始基板w的成膜处理。同时,来自蒸镀源12的蒸镀粒子到达膜厚传感器14,监测基板w上的蒸镀膜的膜厚及其成膜率。[膜厚传感器]接下来,对膜厚传感器14进行详细说明。图2是膜厚传感器14的剖面简图。如图2所示,膜厚传感器14具有石英振子20和可振动地支撑石英振子20的壳体140。石英振子20具有平凸(planoconvex)形状,所述平凸形状是作为成膜面的表面21为平坦面、与之相反的背面22为凸面。石英振子20以其成膜面与蒸镀源12相对设置的方式被容纳于壳体140。膜厚传感器14在壳体140内部还具有:与石英振子20的背面22的周围的电极膜32(图4的b)弹性接触的多个施力部件141、以及与石英振子20的表面21的周围的电极膜31(图4的a)抵接的保持爪142。施力部件141由与壳体140电绝缘的金属等导电性材料构成,与后述振荡电路41电连接。保持爪142构成使石英振子20的表面21朝向蒸镀源12露出的壳体140的开口的周围部。壳体140及保持爪142由金属等导电性材料构成,与震荡电路41电连接。膜厚传感器14不限于保持有单个石英振子20的结构,也可以构成为能够保持有多个石英振子20。这种情况下,即使没有图示,多个石英振子也可保持为能够在壳体内同一圆周上旋转。该壳体设有使位于任意旋转角度的石英振子向蒸镀源露出的单一的开口,并且设有能够选择切换面对该开口的石英振子的切换机构。[测量单元]接着,对测量单元17进行说明。图3是表示测量单元17的一个结构例子的概略框图。测量单元17具有振荡电路41、测量电路42和控制器43。振荡电路41使膜厚传感器14的石英振子20振荡。测量电路42用于测量从振荡电路41输出的石英振子20的谐振频率。控制器43按照每单位时间借助测量电路42获取石英振子20的谐振频率,算出成膜到基板w上的蒸镀材料粒子的成膜率以及堆积在基板w上的蒸镀膜的膜厚。控制器43进一步控制蒸镀源12以使成膜率达到规定值。测量电路42具有混频电路51、低通滤波器52、低频计数器53、高频计数器54和基准信号生成电路55。从振荡电路41输出的信号被输入高频计数器54,首先测量振荡电路41的振荡频率的概略值。用高频计数器54测量到的振荡电路41的振荡频率的概略值被输出到控制器43。控制器43以与测量到的概略值接近的频率的基准频率(例如5mhz)来使基准信号生成电路55振荡。以这个基准频率振荡的频率信号和从振荡电路41输出的信号被输入混频电路51。混频电路51将输入的两种信号混合,并且经由低通滤波器52输出到低频计数器53。在此,在将从振荡电路41输入的信号设为cos((ω+α)t),将从基准信号生成电路输入的信号设为cos(ωt)时,在混频电路51内生成由数学式cos(ωt)·cos((ω+α)t)表示的交流信号。该数学式为cos(ωt)和cos((ω+α)t)乘积的形式,该数学式表示的交流信号等于由cos((2·ω+α)t)表示的高频分量信号与由cos(αt)表示的低频分量信号的和。由混频电路51生成的信号被输入低通滤波器52,高频分量信号cos((2·ω+α)t)被除去,仅低频分量信号cos(αt)被输入低频计数器53。即,在低频计数器53输入作为振荡电路41的信号cos((ω+α)t)与基准信号生成电路55的信号cos(ωt)之差的频率绝对值|α|的低频分量信号。低频计数器53测量该低频分量信号的频率,并将测量值向控制器43输出。控制器43根据由低频计数器53测量到的频率与基准信号生成电路55的输出信号的频率,算出振荡电路41输出的信号的频率。具体而言,在基准信号生成电路55的输出信号的频率比振荡电路41的输出信号的频率小的情况下,在振荡电路41的输出信号上加上低频分量信号的频率,在相反的情况下,从振荡电路41的输出信号减去低频分量信号的频率。例如,在通过高频计数器54对振荡电路41的振荡频率的测量值超出5mhz、以5mhz的频率使基准信号生成电路55振荡的情况下,基准信号生成电路55的振荡频率变得低于振荡电路41的实际振荡频率。因此,为了求得振荡电路41的实际振荡频率,将由低频计数器53求得的低频分量信号的频率|α|与基准信号生成电路55的设定频率5mhz相加即可。若低频分量的频率|α|为10khz,则振荡电路41的准确的振荡频率为5.01mhz。低频计数器53的分辨率具有上限,但为了测量上述差的频率|α|能够分配其分辨率,因此,与以相同分辨率来测量振荡电路41的振荡频率的情况相比,能够进行准确的频率测量。另外,基准信号生成电路55的振荡频率通过控制器43控制,能够以使差值的频率|α|变得比规定值小的方式设定该振荡频率,所以能够有效利用低频计数器53的分辨率。所求得的频率的值被存储于控制器43。控制器43从所求得的频率的值,通过运用上述数学式(1)所示的运算式算出堆积在基板w上的蒸镀材料的膜厚及成膜率。[石英振子]接下来,对石英振子20进行详细说明。图4的a、图4的b分别是石英振子20的主视图和后视图。在石英振子20的表面21和背面22,分别形成有规定形状的电极膜31、32。电极膜31与保持爪142相接触,电极膜32与施力部件141相接触。如图4的a、图4的b的网点部分所示,电极膜31、32形成为互不相同的形状,但电极膜31、32的形状不限于图示的例子。电极膜31、32分别用金(au)、银(ag)等金属膜形成。经由振荡电路41向电极膜31、32施加高频电压,使得石英振子20在厚度滑动振动(thicknessslipvibration)模式下振动。本实施方式中的石英振子20使用在25℃下基本频率为5mhz或6mhz的石英振子。而且,石英振子20的基本频率不限于5mhz,能够使用以不足5mhz的任意频率(例如4mhz、3.25mhz、2.5mhz等)作为基本频率的石英振子。或者,也可使用以超过5mhz的任意频率(例如6mhz等)作为基本频率的石英振子。石英振子20的背面22由具有规定曲率半径的曲面构成。通过使背面22由曲面构成,石英振子20的串联电阻变小,能够使石英振子20在期望的基本振动频率下稳定地振动。背面22的曲率半径没有特别限制,能够根据石英振子20的直径等适当设定。本实施形式的石英振子20中,直径为12.4mm,背面22的曲率半径为100mm~200mm。[石英振子的抗热冲击特性]在这种膜厚传感器中,存在抗热冲击特性引起的成膜率的测量值变动很大的问题。这里所说的抗热冲击特性是指,例如在石英振子的更换时,或者,在遮挡蒸镀源的遮挡板的打开操作时,瞬间接受来自蒸发源的辐射热时的石英振子的局部温度变化引起的测量频率的暂时变动,这个频率的变动量越大,成膜率、膜厚的测量精度越低。图5以及图6表示模拟这个的实验。在热量输入的开始和结束时观测频率的变动量(δf)。仅以该热量输入引起的、而非以整个振子的温度变化引起的频率变动来定义耐抗热冲击特性。这里,已知通过将石英振子的成膜面的表面粗糙度(ra)设定在规定值以下,可改善石英振子的抗热冲击特性。例如图5比较并示出了成膜面的表面粗糙度(ra)为0.37μm的石英振子样本6m-1(基本频率6mhz,切割角θ=35°15′±20′)的抗热冲击特性以及成膜面的表面粗糙度(ra)为0.43μm的石英振子样本6m-2(基本频率6mhz,切割角θ=35°15′±20′)的抗热冲击特性。图5还示出了用30w的卤素灯在石英振子的成膜面侧施加热辐射时的频率的变化,设置为自测量开始10秒后开灯,40秒后关灯。如图5所示,表面粗糙度(ra)小的样本6m-1的频率变化更小,抗热冲击特性优异。虽然,如上所述在成膜面上设有金属膜(电极膜31),但因为电极膜31的厚度薄至约为150nm,因此以成膜面的表面粗糙度(ra)作为电极膜31的表面粗糙度(ra)来评价。近年来,膜厚传感器被要求高精度化,特别是关于抗热冲击特性,由于其对成膜率、膜厚的控制带来的影响很大,因此开发抗热冲击特性优异的膜厚传感器成为当务之急。然而,单是减小石英振子的表面粗糙度仍不足以改善抗热冲击特性,需要进一步改善。另一方面,本发明人发现,通过使石英振子的成膜面的表面粗糙度(ra)为规定值以下、而且切割水平50%的载荷长度比率(tp)为规定值以上,石英振子的抗热冲击特性大幅改善。也就是说,石英振子的抗热冲击特性不仅与成膜面的表面粗糙度(ra)有关,还与上述载荷长度比率(tp)有很大关系,即使表面粗糙度(ra)控制为较小,在上述载荷长度比率(tp)的值不足规定值的情况下,相反地有抗热冲击特性有劣化的倾向。例如图6中示出了成膜面的表面粗糙度(ra)为0.34μm的石英振子样本6m-3(基本频率6mhz,切割角θ=35°15′±20′)的抗热冲击特性。实验条件与图5的例子相同。样本6m-3的切割水平50%的载荷长度比率(tp)是80.2%,与样本6m-1的95.2%、样本6m-2的95.5%相比更低。虽然样本6m-3的表面粗糙度(ra)与样本6m-1和6m-2的相比更小,但由图5及图6所示,样本6m-3的频率变化比样本6m-1和6m-2差。如此,可以确认,成膜面的切割水平50%的载荷长度比率与石英振子的抗热冲击特性有很大相关性。此外,将上述样本6m-1、6m-2和6m-3的各自的表面粗糙度(ra、ry、rz)和切割水平50%的载荷长度比率(tp)归纳在表1中。【表1】样本no.ra[μm]ry[μm]rz[μm]tp[%]δf[hz]6m-10.375.275.2695.23906m-20.435.85.6995.54806m-30.344.244.280.2580在这里,ra为算术平均粗糙度,ry为最大高度,rz为十点平均粗糙度(ten-pointaverageroughness)(jisb0601-1994)。对于表面粗糙度,通过最小二乘法求得高度数据的基准面,计算该基准面与各点的高度数据的差作为粗糙度。表面粗糙度(ra)通过对从基准面到测量曲面的偏差的绝对值进行加和平均计算求得。表面粗糙度(ry)通过从基准面到最高顶点的高度yp和从基准面到最低谷底的深度yv的和求得。表面粗糙度(rz)通过“从最高顶点到第五高顶点的标高的绝对值的平均值”与“从最低谷底到第五低谷底的标高的绝对值的平均值”之和求得。切割水平50%的载荷长度比率(tp)通过将粗糙曲面以平行于顶点面的切割水平(ry的50%)切割时得到的切割面积的和相对于基准面的百分比求得。在本说明书中,使用表面粗糙度计(keyence公司制控制器vk-9500/测量器9510)测得上述各值。后述的说明中也是一样的。本实施方式中的石英振子20具有表面粗糙度(算术平均粗糙度:ra)为0.4μm以下且切割水平50%的载荷长度比率(tp)为为95%以上的成膜面(表面21)。与表面粗糙度(ra)为0.4μm以下的情况相比,即使上述载荷长度比率(tp)为95%以上,当成膜面的表面粗糙度(ra)超过0.4μm时,热冲击时的频率变化增大(参照样本6m-1、6m-2)。此外,与上述载荷长度比率(tp)为95%以上的情况相比,即使表面粗糙度(ra)为0.4μm以下,当成膜面的上述载荷长度比率(tp)不足95%时,热冲击时频率变化增大(参照样本6m-1、6m-3)。此外,比较具有大致一样的表面粗糙度(ra)的样本6m-1和样本6m-3,从两者的δf的比(390/580:67%)可以看到样本6m-1相对于样本6m-3的大约33%的δf的改善。这是因为样本6m-1的载荷长度比率(tp)高于样本6m-3的载荷长度比率,由此可知载荷长度比率(tp)对于δf减小的显著效果。该载荷长度比率(tp)的效果在表面粗糙度(ra)比样本6m-3高的样本6m-2上也能同样地看到,从二者的δf的比(480/580:83%)可知,相对于样本6m-3,样本6m-2的δf大约改善了17%。此外,虽然不特别限定表面粗糙度(ra)的下限,但是,表面粗糙度(ra)的值越小,一方面能够将热冲击时的频率变化抑制得更小,而另一方面成膜面的加工变得更加困难、有加工成本增加的趋势。为此,作为表面粗糙度(ra)的下限,例如能够设为0.19μm。由此,能够抑制加工成本的增加并得到抗热冲击特性优异的石英振子。获取上述成膜面的方法没有特别限制,典型的是通过使用游离磨粒的双面研磨机,以经由粗研磨至可得期望的基本频率的厚度后、再进行中度研磨、最终研磨的顺序加工石英板。上述成膜面优选镜面,但是镜面加工如上所述通常需要巨大的加工成本。因此,并不将成膜面的整个区域均质地加工为镜面,而是将成膜面的部分区域研磨成镜面或者接近镜面的状态。具体而言,作为最终研磨,使用例如#1000~#2000左右粒度的研磨磨粒,以仅刮除表面的突出部(山顶部)的方式研磨。也可根据需要并用化学研磨。此外,也可以分阶段地调节加工方向、加工压力。通过这样的加工方法,能够得到具有上述表面粗糙度(ra)及载荷长度比率(tp)的成膜面。图7表示将本实施方式中的石英振子20的成膜面以150倍放大时的表面状态的一个例子。在图7中,符号s对应镜面或者接近镜面状态的区域(以下称为镜面部)。如图7所示,可知镜面部s分散存在于成膜面的部分区域。作为石英振子20,典型的是,使用温度特性比较优异的at切型石英振子(切割角θ=35°15′±20′)。除此以外,石英振子20也可以使用与at切型相比温度特性更优异的sc切型石英振子(切割角θ=33°30′±11′、φ=20°25′±6°),但通常sc切型基板与at切型基板相比价格更高,因此导致膜厚传感器的高成本化。所以,石英振子20优选为使用at切型基板。通常的at切型基板如图8的b所示,围绕晶体的x轴(电轴)以相对于z轴(成长轴)35°15′的角度切出而形成。另一方面,相对于晶体的z轴构成规定角度的r面(晶面指数(01-11))及r面(晶面指数(10-11))如图8的a所示,交替地定位为以z轴为中心绘制正六边形。这些r面及r面相对于z轴的角度,如图8的b所示,均为38°13′。实际获取石英振子时,需要从晶体切下石英片,得到坯料。在这种情况下,因为石英坯料变薄,z轴变不清晰。但是,因为晶体的r面能够确认,能够以该r面作为基准切出石英坯料。at切型基板相对于该r面的切割角度为(38°13′)-(35°15′)=2°58′。at切型基板中,具有35°08′±03′(相对于r面的切割方位为3°05′±03′)的切割角θ的石英振子,其谐振频率的温度漂移能够控制为在室温(25℃)到80℃附近的范围内在20ppm以下,因此抗热冲击性优异。由此,可以谋求频率测定的稳定化,能够实现高精度的膜厚监测和成膜率的控制。[实验例]接下来,对使用基本频率为5mhz的石英振子的实验例进行说明。本发明人准备了具有表2所示的各种表面粗糙度的成膜面的基本频率为5mhz的石英振子,评价了它们的抗热冲击特性。在本实验例中,将热冲击引起的频率变动量的允许值设为300hz,将δf的值为300hz以上的样本评价为“×”,δf的值为200hz以上且不足300hz的样本评价为“δ”,δf的值不足200hz的样本评价为“○”。为了实现高精度的膜厚监测及成膜率的控制,δf的值优选为不足300hz,进一步优选为不足200hz。【表2】样本no.ra[μm]ry[μm]rz[μm]tp[%]δf[hz]评价5m-10.233.653.6498.4140○5m-20.192.642.6197.0140○5m-30.192.642.6272.2300×5m-40.284.123.9776.9330×5m-50.254.194.0599.0280δ(实验例1)准备在表面粗糙度(ra)为0.23μm且切割水平50%的载荷长度比率(tp)为98.4%的成膜面上蒸镀有厚度约150nm的au膜作为电极膜的、直径为12.4mm且曲率为200mm的平凸型石英振子样本(切割角θ=35°08′±03′(相对于r面的切割方位为3°05′±03′))5m-1。然后,用30w的卤素灯在样本5m-1的成膜面一侧施加热辐射并测定频率变化时,频率变化量(δf)约为140hz。样本5m-1的抗热冲击特性示于图9。(实验例2)除成膜面的表面粗糙度(ra)为0.19μm、切割水平50%的载荷长度比率(tp)为97.0%以外,制备其他特征与实验例1相同的石英振子样本5m-2,在与实验例1同样条件下测定热冲击时的频率变化。测定结果是频率变化量(δf)约为140hz。(实验例3)除成膜面的表面粗糙度(ra)为0.19μm、切割水平50%的载荷长度比率(tp)为72.2%、曲率为100mm以外,制备其他特征与实验例1相同的石英振子样本5m-3,在与实验例1同样条件下测定热冲击时的频率变化。测定结果是频率变化量(δf)约为300hz。样本5m-3的抗热冲击特性示于图10。(实验例4)除成膜面的表面粗糙度(ra)为0.28μm、切割水平50%的载荷长度比率(tp)为76.9%、切割角θ=35°15′±20′(相对于r面的切割方位为2°58′±20′)以外,制备其他特征与实验例1相同的石英振子样本5m-4,在与实验例1同样条件下测定热冲击时的频率变化。测定结果是频率变化量(δf)约为330hz。样本5m-4的抗热冲击特性示于图11。(实验例5)除成膜面的表面粗糙度(ra)为0.25μm、切割水平50%的载荷长度比率(tp)为99.0%、切割角θ=35°15′±20′(相对于r面的切割方位为2°58′±20′)以外,制备其他特征与实验例1相同的石英振子样本5m-5,在与实验例1同样条件下测定热冲击时的频率变化。测定结果是频率变化量(δf)约为280hz。样本5m-5的抗热冲击特性示于图12。样本5m-1~5m-5的石英振子与上述的基本频率为6mhz的石英振子相比较,可以确认在热冲击时的频率变化更小。(参考表1、表2)。此外,根据成膜面的表面粗糙度(ra)为0.4μm以下且切割水平50%的载荷长度比率(tp)为95%以上的样本5m-1、5m-2、5m-5,与样本5m-3、5m-4相比较,频率变化量(δf)较小。其中,根据上述表面粗糙度(ra)为0.23μm以下的样本5m-1、5m-2,可以确认频率变化量(δf)能够进一步减小,能够控制在样本5m-5的一半大小。其中,优选的是,成膜面的切割水平50%的载荷长度比率(tp)为97%以上,进一步优选的是,成膜面的表面粗糙度(ra)为0.25μm以下。这里,具有大致相同的表面粗糙度(ra)的样本5m-4和样本5m-5相比较,从两者的δf的比(280/330:85%)可知,相对于样本5m-4,样本5m-5的δf改善约15%。这是因为以下原因:样本5m-5的载荷长度比率(tp)比样本5m-4高,由此认定载荷长度比率(tp)有利于δf的减小。此外,相同切割方位的样本5m-1和样本5m-3相比较,从两者的δf的比(140/300:47%)可知,相对于样本5m-3,样本5m-1的δf改善约53%。从这个例子,可认定载荷长度比率(tp)对于δf的减小有显著效果。另一方面,样本5m-1与样本5m-5相比,尽管载荷长度比率(tp)变差,但δf提高了50%。这是由两个样本的切割方位不同引起的,由此发现,切割角θ为35°08′±03′(相对于r面的切割方位为3°05′±03′)的石英振子的优势。如上所述,根据本实施方式,能够得到抗热冲击特性优异的膜厚传感器。由此,使得难以受到例如石英振子的更换时、蒸镀源的遮挡板打开时的热辐射的影响的、高精度的成膜率测量或膜厚测量成为可能。此外,根据本实施方式,通过调整石英振子的成膜面的载荷长度比率(tp),能够稳定地制造具有期望的振动特性的石英振子。特别是,无需对成膜面进行镜面加工、或使用sc切型基板等价高的石英板,也能够比较低价地制造抗热冲击特性优异的石英振子。以上是有关本发明的实施方式的说明,当然,本发明不仅限于上述实施方式,还可以进行各种改变。例如,在上述实施方式中,作为石英振子20,列举说明了平凸形状的石英振子,但并不限于此,本发明也能够适用于两面由平坦面构成的石英振子。此外,上述实施方式中,作为成膜装置虽然列举说明了真空蒸镀装置,但不限于此,本发明也能够适用于溅射装置等其他的成膜装置。溅射装置的情况下,有机材料源由溅射阴极构成,所述溅射阴极含有由有机材料构成的靶材。【附图标记说明】10···成膜装置11···真空腔室12···蒸镀源13···基板架14···膜厚传感器16···遮挡板17···测量单元20···石英振子w····基板当前第1页12