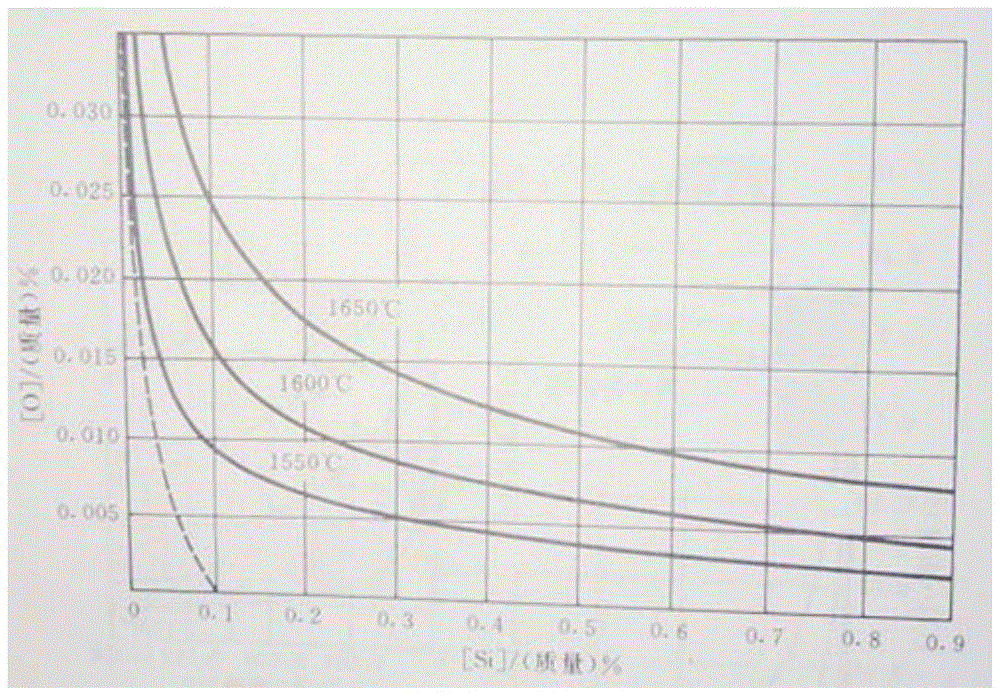
本发明属于钢铁冶金
技术领域:
,具体地讲,涉及一种深度去除钢材中夹杂物的方法。
背景技术:
:钢材中的夹杂物损坏钢基体的连续性,夹杂物含量多的钢材在使用过程中易发生断裂,钢铁企业一直致力于减少钢材中夹杂物的数量,主要采用以下几种措施来减少夹杂物数量,包括1、采用具有深脱氧能力的脱氧元素进行脱氧;2、采用钢包底吹氩气来促进夹杂物上浮;3、利用吸附夹杂物能力强的精炼渣来去除吸附夹杂物;但是夹杂物必须先在钢液中生成,然后才能利用以上工艺去除夹杂物,而现有公开的技术并没有“如何促进夹杂物在钢液中生成的工艺”。众所周知,脱氧元素与氧反应生成氧化物夹杂的反应是放热反应,根据热力学定律,温度越低越能促进放热反应的进行,即温度越低越能促进氧化物夹杂的生成,如附图1的硅脱氧状态图和附图2的铝脱氧状态图所示,在相同硅或铝浓度下,温度越低,与硅或铝平衡的溶解[o]浓度越低。但在实际的炼钢生产中,由于连铸浇钢过程中大包工位和中间包工位的高温钢水持续向外部环境散热,钢水会产生50℃左右的温降,因此为避免钢水流经结晶器浸入式水口位置处发生冻眼现象(冻眼现象是指:钢水从中间包通过结晶器浸入式水口流入结晶过程中,由于温度降低至液相线以下,钢液在结晶器浸入式水口内壁上凝固,堵塞水口,导致浇钢无法继续进行),因此钢厂一般是在精炼工位将钢包内的钢水加热至高于钢水液相线温度以上50度左右的温度,以抵消连铸浇钢过程中钢水的温降,但在精炼工位将钢水加热至过高温度不利于氧化物夹杂物的生成和氧化物夹杂的去除,会降低精炼工位夹杂物的去除效率。技术实现要素:为解决以上问题,针对以上存在的问题,本发明提供一种深度去除钢材中夹杂物的方法。该方法是在lf精炼工位使用比钢水液相线温度高20~30℃的温度进行精炼,该温度比现有技术使用的精炼温度低30℃以上,利用低温来促进氧化夹杂物生成和氧化物夹杂的去除,为弥补连铸浇钢过程中的大包工位和中间包工位中钢液的温度散失,在钢包炉衬内部增设电磁感应线圈,连铸浇钢过程中,电磁感应线圈利用感应加热持续的对大包内的钢水进行加热,使大包内钢水的温度稳定控制在钢水液相线温度以上20~30℃范围内。本发明提供一种深度去除钢材中夹杂物的方法,包括以下方法:1)钢水由初炼炉工位运至lf精炼工位后,检测钢水温度,并加入造渣料,然后降下电极进行通电升温和化渣;其中,lf精炼工位的精炼温度比钢水液相线温度高20~30℃,利用低温来促进氧化夹杂物生成和氧化物夹杂的去除;2)钢包由lf精炼工位运至连铸工位后,打开钢包水口的滑板,同时开启电磁感应线圈加热装置和氩气装置,其中,所述电磁感应线圈的埋入位置处为:钢包包衬中的永久层内部。作为优选,方法2)中电磁感应线圈的电源额定功率设定为1500~2000kw,频率300~500hz,电磁感应线圈的入口和出口处的铜制线圈为水平状,并穿过钢包外壳向外探出,电磁感应线圈的入口和出口通过导线与外部电源连接。作为优选,所述电磁感应线圈的线圈为中空矩形铜质线圈,线圈壁厚为6~8mm,矩形线圈截面规格为50~70mm*20~40mm,匝数为18~22匝,匝间距为8~12mm。作为优选,方法2)中在该炉钢水浇铸的前20-30min时间内使用电磁感应线圈对钢水进行加热。进一步优选,其具体包括以下方法:1)钢水由初炼炉工位运至lf精炼工位后,利用钢水温度检测探头检测钢水温度,并加入造渣料,然后降下电极进行通电升温和化渣,通过电极通电升温的速率计算出升高目标温度所需的通电时间,控制精炼末期钢水的温度在液相线温度以上20~30℃范围内。以下以铝脱氧的反应为例,简述低温精炼对夹杂物生成的有利作用:反应:2al+3[o]→al2o3的平衡常数k的计算公式和平衡常数k与温度t的关系式分别为如下①、②式:k={(aal)2×(a[o])3}/aal2o3①lgk=(-62780/t)+20.54②其中k为铝氧反应的平衡常数,t为温度(℃),aal为钢水中al的活度,根据亨利定律,在钢水中al含量很低的情况下,铝的活度可以用铝的浓度来代替,a[o]为钢水中[o]的活度,根据亨利定律,在钢水中[o]含量很低的情况下,[o]的活度可以用[o]的浓度来代替,aal2o3为钢水中al2o3夹杂的活度,由于al2o3夹杂不溶于钢水中,因此aal2o3=1。目前钢厂针对低碳钢的lf精炼大部分在1580℃温度附近进行精炼,钢水中al浓度一般控制在0.03%左右,本发明的技术方案是比现有技术低30℃左右进行精炼,也就是在1550℃温度附近进行精炼,因此通过式①、②分别计算在1550℃和1580℃下,与0.03%的铝平衡的[o]浓度,对比不同温度下与0.03%的铝平衡的[o]浓度差,以此显示低温精炼对于氧化物夹杂生成的促进作用。通过式①、②的计算结果如下表1。表1:不同温度下与0.03%的铝平衡的[o]浓度温度(℃)铝浓度(%)与铝平衡的[o]浓度(%)1580℃0.03%0.00037%1550℃0.03%0.00024%由表1可看出温度降低30℃,与铝平衡的[o]浓度约降低0.00013%,降低幅度为35%,氧含量由0.00037降至0.00024%所产生的氧化物夹杂在1580~1550℃温度范围内析出,若采用低温精炼的工艺(在1550℃温度附近进行精炼),则该部分氧化物夹杂在lf精炼工位就能生成,生成的该部分夹杂物可以在精炼过程和随后的大包浇钢过程中上浮去除,夹杂物析出时间早,留给夹杂物上浮的时间长,夹杂物的去除率高,而如果采用现有技术(在1580℃温度附近进行精炼),氧含量由0.00037降至0.00024%所产生的氧化物夹杂就无法在精炼过程中析出,该部分夹杂物是钢包由精炼工位运至连铸工位后,随着钢水温度降低而逐渐析出的,夹杂物析出时间晚,留给夹杂物上浮的时间短,夹杂物的去除率低,因此低温精炼工艺有利于夹杂物的生成和去除。2)钢包由lf精炼工位运至连铸工位后,打开钢包水口的滑板,大包开浇(大包是指连铸工位的钢包),同时开启电磁感应线圈加热装置和氩气装置,对大包内的钢水进行加热,并通过氩气冷却电磁感应线圈和促进大包内夹杂物上浮,电磁感应线圈对钢水进行加热的时间为:在该炉钢水浇铸的前20-30min时间内使用电磁感应线圈对钢水进行加热。在钢包内壁的中下部位置处布置电磁感应线圈,电磁感应线圈埋入钢包包衬的耐火材料内部,电磁感应线圈加热对钢水输入的热量约等于钢水向外界环境的散失的热量。电磁感应线圈的埋入位置处为:钢包包衬中的永久层内部,电磁感应加热线圈的电源额定功率设定为1500~2000kw,频率300~500hz,电磁感应线圈的入口和出口处的铜制线圈为水平状,并穿过钢包外壳向外探出,电磁感应线圈的入口和出口通过导线与外部电源连接。为匹配电磁感应线圈的电源功率,设计高电感的电磁感应线圈,其规格参数为,线圈为中空矩形铜质线圈,线圈壁厚为6~8mm,矩形线圈截面规格为(50~70)mm*(20~40)mm,匝数为18~22匝,匝间距为8~12mm。采用绝缘支撑架固定电磁感应线圈,并且绝缘支撑架与钢包外壳相连并固定。中空矩形状铜质电磁感应线圈采用氩气来进行冷却,电磁感应线圈的入口处与外部氩气源相连接,电磁感应线圈的出口处通过气管与钢包底部透气砖相连接。氩气顺线圈内部的中空矩形状通道流动,气体流速为0.6~1m/s,氩气冷却完电磁感应线圈后从钢包底部透气砖喷入钢水中,喷入钢水中的氩气在上浮过程中能捕捉夹杂物,并带动夹杂物上浮去除,起到去除夹杂物的作用。氩气能起到冷却电磁感应线圈和去除夹杂物的双重效果。采用气冷来代替水冷能避免冷却水渗漏到钢液中引起的危险,并且氩气会把冷却带走的热量传递到钢液中,节约了热量,减少了钢水温降。电磁感应线圈外部电源功率的调节方法为:首先根据钢水重量、钢水升温目标值、钢水比热容、感应线圈加热效率、感应线圈加热时间计算出电磁感应线圈的目标加热功率,计算公式如下式③,然后调节电磁感应线圈外部电源的功率与电磁感应线圈的目标加热功率相同。w×t×η×3600000=m×c×δt③③式中的w为电磁感应线圈外部电源功率(kw·h),t为加热时间(h),m为钢水重量(kg),c为钢水的比热容(j/(kg·℃),η为电磁感应线圈加热效率(%),δt为钢水温度的升高值(℃)。与现有技术相比,本发明的优势在于:在lf精炼工位在较低的温度对钢水进行精炼,由于温度降低有利于夹杂物的生成,夹杂物的析出时间早,留给夹杂物上浮的时间长,夹杂物的去除率高。在钢包包衬的永久层内部埋入电磁感应线圈,在连铸的大包工位采用电磁感应线圈对钢水进行加热,电磁感应线圈输入给钢水的热量等于钢水向外部环境散失的热量,能弥补低温精炼工艺热量输入不足的缺点。附图说明图1为硅脱氧时,不同温度下硅含量和氧含量的平衡状态图;图2为铝脱氧时,不同温度下铝含量和氧含量的平衡状态图。具体实施方式实施例1以下配合具体实施例对一种通过低温精炼工艺来深度去除夹杂物的方法做进一步说明。某炼钢厂冶炼一炉q460c钢水,根据炉钢水的目标成分计算出其液相线温度为1518℃,在lf精炼工位使用1540~1550℃的温度对钢水进行精炼,该温度比现有技术采用的温度低30℃以上,利用低温来促进氧化夹杂物生成和氧化物夹杂的去除。钢水由初炼炉工位运至lf精炼工位后,检测钢水进lf精炼温度为1545℃,并加入造渣料,由于精炼过程控制的温度低,因此精炼目标渣系也是低熔点渣系,目标渣系成分的百分含量为:cao:40~50%,al2o3:30~40%,sio2:5~15%,mgo:5~10%,t·fe:0~1.5%,根据精炼渣系的目标成分确定造渣料的加入量,共加入石灰700kg和铝酸钙类合成渣500kg,然后降下电极进行通电升温和化渣,根据以往的操作经验得出每吨造渣料化渣所的热量为:600kw·h/吨,电极通电升温的效率为75%,钢水向外部环境的散热速度为1℃/min,需精炼40min,钢水重量120吨,钢水比热为0.46×103j/(kg·℃),以下式④计算出控制精炼末期钢水的温度在液相线温度以上30℃所需的通电用电量为1839kw·h,因此利用电极通电约1840kw·h并配合钢水温度检测探头控制精炼末期钢水温度在液相线温度以上30℃。q=(m钢水×c钢水×δt)/(3600000×η)+m造渣料×600/η④④式中的q为所需通电量(kw·h),c钢水为钢水比热容(j/(kg·℃),δt为考虑到钢水向外部散热以及lf进站温度和精炼末期目标温度之间的差值得出的钢水升温温度,本实施例计算出的结果为43℃,m造渣料为造渣料加入总量(吨),η为电磁极加热效率(%)。精炼末期钢水温度为1548℃,经检测钢水中酸溶铝含量为0.035%,溶解氧[o]含量为2.1ppm,溶解氧含量极低,低温精炼有利于氧化物夹杂的生成,能达到夹杂物早生成、早上浮去除的目的。在钢包内壁的中下部位置处布置电磁感应线圈,电磁感应线圈埋入钢包包衬的耐火材料内部,电磁感应线圈加热对钢水输入的热量约等于钢水向外界环境的散失的热量。电磁感应线圈的埋入位置处为:钢包包衬中的永久层内部,电磁感应加热线圈的电源额定功率设定为1500kw,频率500hz,电磁感应线圈的入口和出口处的铜质线圈为水平状,并穿过钢包外壳向外探出,电磁感应线圈的入口和出口通过导线与外部电源连接。为匹配电磁感应线圈的电源功率,设计高电感的电磁感应线圈,其规格参数为,线圈为中空矩形铜质线圈,线圈壁厚为6mm,矩形线圈截面规格为50mm*20mm,匝数为18匝,匝间距为8mm。采用绝缘支撑架固定电磁感应线圈,并且绝缘支撑架与钢包外壳相连并固定。中空矩形状铜质电磁感应线圈采用氩气来进行冷却,电磁感应线圈的入口处与外部氩气源相连接,电磁感应线圈的出口处通过气管与钢包底部透气砖相连接。氩气顺线圈内部的中空矩形状通道流动,气体流速为0.6m/s,氩气冷却完电磁感应线圈后从钢包底部透气砖喷入钢水中,喷入钢水中的氩气在上浮过程中能捕捉夹杂物,并带动夹杂物上浮去除,起到去除夹杂物的作用。氩气能起到冷却电磁感应线圈和去除夹杂物的双重效果。采用气冷来代替水冷能避免冷却水渗漏到钢液中引起的危险,并且氩气会把冷却带走的热量传递到钢液中,节约了热量,减少了钢水温降。钢包由lf精炼工位运至连铸工位后,打开钢包水口的滑板,大包开浇(大包是指连铸工位的钢包),同时开启电磁感应线圈加热装置和氩气装置,对大包内的钢水进行加热,并通过氩气冷却电磁感应线圈和促进大包内夹杂物上浮,电磁感应线圈对钢水进行加热的时间为:在该炉钢水浇铸的前2/3时间内使用电磁感应线圈对钢水进行加热,该炉钢水共浇铸30分钟,也即该炉钢水浇铸的前20分钟使用电磁感应线圈对钢水进行加热。电磁感应线圈外部电源功率的调节方法为:首先根据钢水重量、钢水升温目标值、钢水比热容、感应线圈加热效率、感应线圈加热时间计算出电磁感应线圈的目标加热功率,计算公式如下式(5),然后调节电磁感应线圈外部电源的功率与电磁感应线圈的目标加热功率相同。w×t×η×3600000=m×c×δt(5)(5)式中的w为电磁感应线圈外部电源功率(kw·h);t为加热时间(h)本实施例为0.33h;m为钢水重量(kg),本实施例为120000kg;c为钢水的比热容(j/(kg·℃),本实施例为0.46×103j/(kg·℃);η为电磁感应线圈加热效率(%),本实施例为80%.δt为目标加热温度值,由于钢水散热速度为1℃/min,共浇铸30min,因此需将钢水升温20℃才能补偿钢水的散热损失,δt为20℃。经计算电磁感应线圈外部电源的目标加热功率为1161kw·h,调节电磁感应线圈外部电源的功率至1160kw·h,在该炉钢水浇铸的前20分钟使用电磁感应线圈对钢水进行加热,经检测,中间包内钢水温度为1530~1540℃范围内,中间包内钢水过热度为12~22℃范围内,钢水温度适宜,未发生结晶器浸入式水口冻眼现象,连铸浇钢顺利进行,连铸铸坯的全氧含量为17ppm,轧材夹杂物评级为a类夹杂0.5级、b类夹杂0.5级、c类夹杂0级、d类夹杂0级,钢材纯净度高,低温精炼工艺起到了深度去夹杂的效果。实施例2某炼钢厂冶炼一炉65mn钢水,根据炉钢水的目标成分计算出其液相线温度为1476℃,在lf精炼工位使用1500~1510℃的温度对钢水进行精炼,该温度比现有技术采用的温度低30℃以上,利用低温来促进氧化夹杂物生成和氧化物夹杂的去除。钢水由初炼炉工位运至lf精炼工位后,检测钢水进lf精炼温度为1510℃,并加入造渣料,由于精炼过程控制的温度低,因此精炼目标渣系也是低熔点渣系,目标渣系成分的百分含量为:cao:35~45%,al2o3:30~40%,sio2:10~20%,mgo:5~10%,t·fe:0~1.5%,根据精炼渣系的目标成分确定造渣料的加入量,共加入石灰500kg和铝酸钙类合成渣500kg,然后降下电极进行通电升温和化渣,根据以往的操作经验得出每吨造渣料化渣所的热量为:600kw·h/吨,电极通电升温的效率为75%,钢水向外部环境的散热速度为1℃/min,需精炼40min,钢水重量120吨,钢水比热为0.46×103j/(kg·℃),以下式④计算出控制精炼末期钢水的温度在液相线温度以上20℃范围内(也即控制精炼末期钢水温度为1496℃)所需的通电用电量为1332kw·h,因此利用电极通电约1332kw·h并配合钢水温度检测探头控制精炼末期钢水温度在液相线温度以上20℃。q=(m钢水×c钢水×δt)/(3600000×η)+m造渣料×600/η④④式中的q为所需通电量(kw·h),c钢水为钢水比热容(j/(kg·℃),δt为考虑到钢水向外部散热以及lf进站温度和精炼末期目标温度之间的差值得出的钢水升温温度,本实施例计算出的结果为26℃,m造渣料为造渣料加入总量(吨),η为电磁极加热效率(%)。精炼末期钢水温度为1496℃,经检测钢水中酸溶铝含量为0.030%,溶解氧[o]含量为1.1ppm,溶解氧含量极低,低温精炼有利于氧化物夹杂的生成,能达到夹杂物早生成、早上浮去除的目的。在钢包内壁的中下部位置处布置电磁感应线圈,电磁感应线圈埋入钢包包衬的耐火材料内部,电磁感应线圈加热对钢水输入的热量约等于钢水向外界环境的散失的热量。电磁感应线圈的埋入位置处为:钢包包衬中的永久层内部,电磁感应加热线圈的电源额定功率设定为2000kw,频率300hz,电磁感应线圈的入口和出口处的铜质线圈为水平状,并穿过钢包外壳向外探出,电磁感应线圈的入口和出口通过导线与外部电源连接。为匹配电磁感应线圈的电源额定功率,设计高电感的电磁感应线圈,其规格参数为,线圈为中空矩形铜质线圈,线圈壁厚为8mm,矩形线圈截面规格为70mm*40mm,匝数为22匝,匝间距为12mm。采用绝缘支撑架固定电磁感应线圈,并且绝缘支撑架与钢包外壳相连并固定。中空矩形状铜质电磁感应线圈采用氩气来进行冷却,电磁感应线圈的入口处与外部氩气源相连接,电磁感应线圈的出口处通过气管与钢包底部透气砖相连接。氩气顺线圈内部的中空矩形状通道流动,气体流速为1.0m/s,氩气冷却完电磁感应线圈后从钢包底部透气砖喷入钢水中,喷入钢水中的氩气在上浮过程中能捕捉夹杂物,并带动夹杂物上浮去除,起到去除夹杂物的作用。氩气能起到冷却电磁感应线圈和去除夹杂物的双重效果。采用气冷来代替水冷能避免冷却水渗漏到钢液中引起的危险,并且氩气会把冷却带走的热量传递到钢液中,节约了热量,减少了钢水温降。钢包由lf精炼工位运至连铸工位后,打开钢包水口的滑板,大包开浇(大包是指连铸工位的钢包),同时开启电磁感应线圈加热装置和氩气装置,对大包内的钢水进行加热,并通过氩气冷却电磁感应线圈和促进大包内夹杂物上浮,电磁感应线圈对钢水进行加热的时间为:在该炉钢水浇铸的前2/3时间内使用电磁感应线圈对钢水进行加热,该炉钢水共浇铸45分钟,也即该炉钢水浇铸的前30分钟使用电磁感应线圈对钢水进行加热。电磁感应线圈外部电源功率的调节方法为:首先根据钢水重量、钢水升温目标值、钢水比热容、感应线圈加热效率、感应线圈加热时间计算出电磁感应线圈的目标加热功率,计算公式如下式(5),然后调节电磁感应线圈外部电源的功率与电磁感应线圈的目标加热功率相同。w×t×η×3600000=m×c×δt(5)(5)式中的w为电磁感应线圈外部电源功率(kw·h);t为加热时间(h),本实施例为0.5h;m为钢水重量(kg),本实施例为120000kg;c为钢水的比热容(j/(kg·℃),本实施例为0.46×103j/(kg·℃);η为电磁感应线圈加热效率(%),本实施例为80%.δt为目标加热温度值,由于钢水散热速度为1℃/min,共浇铸45min,因此需将钢水升温45℃才能补偿钢水的散热损失,δt为45℃。经计算电磁感应线圈外部电源的目标加热功率为1725kw·h,调节电磁感应线圈外部电源的功率至1725kw·h,在该炉钢水浇铸的前30分钟使用电磁感应线圈对钢水进行加热,经检测,中间包内钢水温度为1490~1500℃范围内,中间包内钢水过热度为14~24℃范围内,钢水温度适宜,未发生结晶器浸入式水口冻眼现象,连铸浇钢顺利进行,连铸铸坯的全氧含量为12ppm,轧材夹杂物评级为a类夹杂0.5级、b类夹杂0.5级、c类夹杂0级、d类夹杂0级,钢材纯净度高,低温精炼工艺起到了深度去夹杂的效果。最后所应说明的是,以上实施例仅用以说明本发明的技术方案而非限制。尽管参照实施例对本发明进行了详细说明,本领域的普通技术人员应当理解,对本发明的技术方案进行修改或者等同替换,都不脱离本发明技术方案的精神和范围,其均应涵盖在本发明的权利要求范围当中。当前第1页12