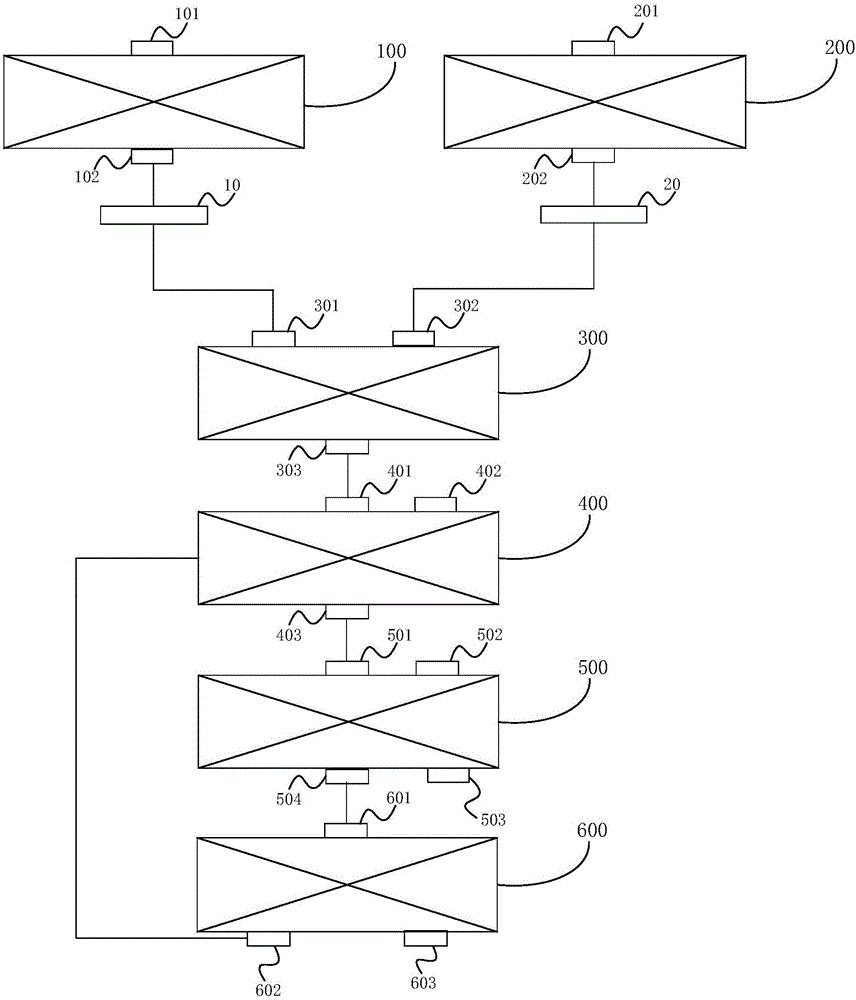
本发明涉及能源化工领域,具体而言,本发明涉及制备电石的系统和方法。
背景技术:
:电石的生产方法有氧热法和电热法两种,目前工业上一般采用电热法生产电石,即焦炭(C)和氧化钙(CaO)在电石反应炉内,采用固定床依靠电弧高温(>2000℃)熔化反应而生成电石,电热法制备电石的特点是采用块状原料进料和利用电能生产电石,它存在反应速率慢、反应时间长、反应温度高,耗电量大,电石产量低、粉尘和尾气治理困难的问题。正是由于传统电石生产技术存在“高投入、高污染、高电耗”的缺点,不符合节能减排和可持续发展的要求,因此发展受限。氧热法是在氧的存在下使部分碳发生燃烧,产生的高温热量使剩余碳和钙发生反应生成电石,该法由于具有反应时间短、反应温度低、污染小的优点逐渐被重视。但是氧热法由于采用碳素材料燃烧供热,难免产生大量的灰,如何降低氧热法生产的电石中的灰分是制约氧热法发展的重要因素。因而,目前制备电石的手段仍有待改进。技术实现要素:本发明旨在至少在一定程度上解决相关技术中的技术问题之一。为此,本发明的一个目的在于提出制备电石的系统和方法。采用该系统可以较低能耗下显著提高制备电石的效率,有效地降低制备电石的成本,同时将制备电石过程中产生的灰分转化为熔融态灰渣的形式进行分离,避免了对环境的污染。在本发明的第一方面,本发明提出了一种制备电石的系统。根据本发明的实施例,该系统包括:碳基粉碎装置,所述碳基粉碎装置具有碳基原料入口和超细碳基粉末出口;钙基粉碎装置,所述钙基粉碎装置具有钙基原料入口和超细钙基粉末出口;混合装置,所述混合装置具有超细碳基粉末入口、超细钙基粉末入口和混合物料出口,所述超细碳基粉末入口与所述超细碳基粉末出口相连,所述超细钙基粉末入口与所述超细钙基粉末出口相连;预热炉,所述预热炉具有混合物料入口、热解气出口和高温固体物料出口,所述混合物料入口与所述混合物料出口相连;电石反应炉,所述电石反应炉具有高温固体物料入口、氧气入口、熔融态灰渣出口和混合烟气出口,所述高温固体物料入口与所述高温固体物料出口相连;以及分离器,所述分离器具有混合烟气入口、合成气出口和电石出口,所述混合烟气入口与所述混合烟气出口相连。由此,根据本发明的实施例,该系统通过采用碳基粉碎装置和钙基粉碎装置分别将碳基原料和钙基原料粉碎为超细碳基粉末和超细钙基粉末,由此可以提高物料的比表面积和接触面积,从而显著降低制备电石所需的能耗;通过混合装置将超细碳基粉末和超细钙基粉末混合后,将混合物料送入预热炉进行预热处理,由此不仅可以得到高附加值的热解气,还可以显著提高混合物料的反应活性;进而将预热得到的高温固体物料热送至电石反应炉,同时通入氧气,与高温固体物料中的碳反应提供热量,并使碳与钙反应生成电石,制备得到的电石与副产的大量合成气以混合烟气的形式进入分离器,经分离处理得到电石产品和合成气,而制备电石产生的灰分在电石反应炉中形成熔融态灰渣,从电石反应炉底部排出。由此,根据本发明实施例的制备电石的系统可以在较低能耗下显著提高制备电石的效率,有效地降低制备电石的成本,同时将制备电石过程中产生的灰分转化为熔融态灰渣的形式进行分离,避免了对环境的污染。另外,根据本发明上述实施例的制备电石的系统还可以具有如下附加的技术特征:在本发明的一些实施例中,所述合成气出口与所述预热炉相连。由此,可以利用合成气对所述预热炉中的混合物料进行预热处理,从而显著降低所述预热炉所需的能耗。在本发明的一些实施例中,所述制备电石的系统进一步包括:超细碳基粉末过滤筛,所述超细碳基粉末过滤筛设置在所述碳基粉碎装置和所述混合装置之间,所述超细碳基粉末过滤筛的孔径为不大于0.01mm。由此,可以保证进入混合装置的超细碳基粉末粒径不高于0.01mm,从而有效地提高混合装置制备得到的混合物料的比表面积。在本发明的一些实施例中,所述制备电石的系统进一步包括:超细钙基粉末过滤筛,所述超细钙基粉末过滤筛设置在所述钙基粉碎装置和所述混合装置之间,所述超细钙基粉末过滤筛的孔径为不大于0.01mm。由此,可以保证进入混合装置的超细钙基粉末粒径不高于0.01mm,从而有效地提高混合装置制备得到的混合物料的比表面积。在本发明的第二方面,本发明提出了一种采用上述实施例的制备电石的系统实施制备电石的方法,根据本发明的实施例,该方法包括:将碳基原料在碳基粉碎装置中进行粉碎处理,以便得到超细碳基粉末;将钙基原料在钙基粉碎装置中进行粉碎处理,以便得到超细钙基粉末;将所述超细碳基粉末和所述超细钙基粉末在混合装置中进行混合,以便得到混合物料;将所述混合物料供给至预热炉并进行预热处理,以便得到热解气和高温固体物料;将所述高温固体物料和氧气供给至电石反应炉并进行电石反应,以便得到混合烟气和熔融态灰渣。以及将所述混合烟气供给至分离器进行分离处理,以便得到合成气和电石。由此,根据本发明的实施例,该方法通过采用碳基粉碎装置和钙基粉碎装置分别将碳基原料和钙基原料粉碎为超细碳基粉末和超细钙基粉末,由此可以提高物料的比表面积和接触面积,从而显著降低制备电石所需的能耗;通过混合装置将超细碳基粉末和超细钙基粉末混合后,将混合物料送入预热炉进行预热处理,由此不仅可以得到高附加值的热解气,还可以显著提高混合物料的反应活性;进而将预热得到的高温固体物料热送至电石反应炉,同时通入氧气与高温固体物料中的碳反应提供热量,使碳与钙反应生成电石,制备得到的电石与副产的大量合成气以混合烟气的形式进入分离器,经分离处理得到电石产品和合成气,而制备电石产生的灰分在电石反应炉中形成熔融态灰渣,从电石反应炉底部排出。由此,根据本发明实施例的制备电石的方法可以在较低能耗下显著提高制备电石的效率,有效地降低制备电石的成本,同时将制备电石过程中产生的灰分转化为熔融态灰渣的形式进行分离,避免了对环境的污染。另外,根据本发明上述实施例的制备电石的方法还可以具有如下附加的技术特征:在本发明的一些实施例中,所述超细碳基粉末和所述超细钙基粉末的粒径分别独立地不高于0.01mm。由此可以提高物料的比表面积和接触面积,从而显著降低制备电石所需的能耗。在本发明的一些实施例中,将所述超细碳基粉末和所述超细钙基粉末按照质量比(3~4):1进行混合。由此,可以显著提高制备电石的产率。在本发明的一些实施例中,控制所述预热炉的温度为550~800摄氏度。由此,可以有效地提高混合物料的反应活性,同时得到高附加值的热解气。在本发明的一些实施例中,所述电石反应炉中氧气、所述超细碳基粉末和所述超细钙基粉末质量比为(2~3):(3~4):1。由此,可以进一步提供制备电石的产率。在本发明的一些实施例中,控制所述电石反应炉的温度为1450~1600摄氏度。由此,可以显著提高制备电石的效率。在本发明的一些实施例中,将所述合成气返回用于对所述混合物料进行所述预热处理。由此,可以利用合成气对所述预热炉中的混合物料进行预热处理,从而显著降低所述预热炉所需的能耗。本发明的附加方面和优点将在下面的描述中部分给出,部分将从下面的描述中变得明显,或通过本发明的实践了解到。附图说明本发明的上述和/或附加的方面和优点从结合下面附图对实施例的描述中将变得明显和容易理解,其中:图1是根据本发明一个实施例的制备电石的系统结构示意图;图2是根据本发明再一个实施例的制备电石的系统结构示意图;图3是根据本发明一个实施例的制备电石的方法流程示意图;图4是根据本发明再一个实施例的制备电石的方法流程示意图;图5是根据本发明再一个实施例的制备电石的系统结构示意图。具体实施方式下面详细描述本发明的实施例,所述实施例的示例在附图中示出,其中自始至终相同或类似的标号表示相同或类似的元件或具有相同或类似功能的元件。下面通过参考附图描述的实施例是示例性的,旨在用于解释本发明,而不能理解为对本发明的限制。在本发明的描述中,需要理解的是,术语“相连”应做广义理解,例如,可以是固定连接,也可以是可拆卸连接,或成一体;可以是机械连接,也可以是电连接;可以是直接相连,也可以通过中间媒介间接相连,可以是两个元件内部的连通或两个元件的相互作用关系,除非另有明确的限定。对于本领域的普通技术人员而言,可以根据具体情况理解上述术语在本发明中的具体含义。在本发明的第一方面,本发明提出了一种制备电石的系统。根据本发明的实施例,参考图1,该系统包括:碳基粉碎装置100、钙基粉碎装置200、混合装置300、预热炉400、电石反应炉500以及分离器600。其中,碳基粉碎装置100具有碳基原料入口101和超细碳基粉末出口102;钙基粉碎装置200具有钙基原料入口201和超细钙基粉末出口202;混合装置300具有超细碳基粉末入口301、超细钙基粉末入口302和混合物料出口303,超细碳基粉末入口301与超细碳基粉末出口102相连,超细钙基粉末入口302与超细钙基粉末出口202相连;预热炉400具有混合物料入口401、热解气出口402和高温固体物料出口403,混合物料入口401与混合物料出口303相连;电石反应炉500具有高温固体物料入口501、氧气入口502、熔融态灰渣出口503和混合烟气出口504,高温固体物料入口501与高温固体物料出口403相连;分离器600具有混合烟气入口601、合成气出口602和电石出口603,混合烟气入口601与混合烟气出口504相连。下面参考图1~2对根据本发明实施例的制备电石的系统进行详细描述:根据本发明的实施例,碳基粉碎装置100具有碳基原料入口101和超细碳基粉末出口102,碳基粉碎装置100适于将碳基原料进行破碎处理,以便得到超细碳基粉末。具体地,碳基原料可以为长焰煤。根据本发明的实施例,超细碳基粉末的粒径并不受特别限制,本领域技术人员可以根据实际需要进行选择,根据本发明的具体实施例,超细碳基粉末的粒径可以不高于0.01mm。发明人发现,通过将碳基原料破碎至该粒径,可以显著提高得到的超细碳基粉末的比表面积和接触面积,使超细碳基粉末与超细钙基粉末充分混合均匀,由此可以显著降低后续电石反应所需的温度,使混合物料中的碳与钙可以在较低温度下发生反应生成电石。根据本发明的实施例,钙基粉碎装置200具有钙基原料入口201和超细钙基粉末出口202,钙基粉碎装置200适于将碳基原料进行破碎处理,以便得到超细钙基粉末。具体地,钙基原料可以为生石灰。根据本发明的实施例,超细钙基粉末的粒径并不受特别限制,本领域技术人员可以根据实际需要进行选择,根据本发明的具体实施例,超细钙基粉末的粒径可以不高于0.01mm。发明人发现,通过将钙基原料破碎至该粒径,可以显著提高得到的超细钙基粉末的比表面积和接触面积,使超细钙基粉末与超细碳基粉末充分混合均匀,由此可以显著降低后续电石反应所需的温度,使混合物料中的碳与钙可以在较低温度下发生反应生成电石。根据本发明的实施例,混合装置300具有超细碳基粉末入口301、超细钙基粉末入口302和混合物料出口303,超细碳基粉末入口301与超细碳基粉末出口102相连,超细钙基粉末入口302与超细钙基粉末出口202相连,混合装置300适于将超细碳基粉末和超细钙基粉末进行混合,以便得到混合物料。根据本发明的实施例,混合物料中超细碳基粉末和超细钙基粉末的质量比并不受特别限制,本领域技术人员可以根据实际需要进行选择,根据本发明的具体实施例,可以将超细碳基粉末和超细钙基粉末按照质量比(3~4):1进行混合。根据本发明的实施例,在后续电石反应中,需通入氧气与混合物料中的碳燃烧为反应提供热量,所以超细碳基粉末的配入量须高于超细钙基粉末的配入量,发明人通过大量实验意外地发现,将超细碳基粉末和超细钙基粉末按照质量比(3~4):1进行混合的效果较好,如果超细碳基粉末的配入量过低,则无法满足制备电石和燃烧提供热量的需要,而超细碳基粉末的配入量过高则会造成资源的浪费。根据本发明的实施例,预热炉400具有混合物料入口401、热解气出口402和高温固体物料出口403,混合物料入口401与混合物料出口303相连,预热炉400适于将混合物料进行预热处理,以便得到热解气和高温固体物料。根据本发明的实施例,通过采用预热炉400对混合物物料进行预热处理,可以显著提高混合物料的反应活性,从而降低后续电石反应中所需的能耗和所需的氧气的量,进而降低整个系统的综合能耗,另外,通过采用预热炉400对混合物物料进行预热处理,还可以使混合物料生成高附加值的热解气,从而进一步提高了系统的经济效益。根据本发明的实施例,预热炉400的温度并不受特别限制,本领域技术人员可以根据实际需要进行选择,根据本发明的具体实施例,可以控制预热炉400的温度为550~800摄氏度。发明人通过大量实验意外地发现,由于采用粒径不高于0.01mm的超细碳基粉末和超细钙基粉末制备混合物料,混合物料具有较高的比表面和接触面积,从而可以在较低温度(550~800摄氏度)下达到对混合物料的预热效果。根据本发明的实施例,电石反应炉500具有高温固体物料入口501、氧气入口502、熔融态灰渣出口503和混合烟气出口504,高温固体物料入口501与高温固体物料出口403相连,电石反应炉500适于将高温固体物料进行电石反应,以便得到混合烟气和熔融态灰渣。具体地,根据本发明的实施例,可以将经预热炉400预热得到的高温固体物料热送至电石反应炉500,并向电石反应炉500中通入氧气,进行上述电石反应;在电石反应炉500中,氧气和高温固体物料中的碳燃烧提供热量,从而可以显著降低电石反应炉的能耗,进一步地,高温固体物料中碳和钙反应生成电石和大量高温合成气,生成的电石呈固体粉状,与合成气以混合烟气的形式从电石反应炉500上部的混合烟气出口504排出,而电石反应产生的灰分形成熔融态灰渣,从电石反应炉500底部的融态灰渣出口503排出,由此可以避免灰分对环境的污染。根据本发明的具体实施例,电石反应炉中氧气、超细碳基粉末和超细钙基粉末的质量比可以为(2~3):(3~4):1。发明人发现,在电石反应中,需通入氧气与混合物料中的碳燃烧为反应提供热量,所以超细碳基粉末的配入量须高于超细钙基粉末的配入量;根据本发明的另一些实施例,氧气与超细碳基粉末的质量比可以为(0.5~0.6):1,发明人发现,在此配比下氧气可以与超细碳基粉末有效地进行燃烧并为电石反应提供热量,从而降低电石反应炉的能耗。根据本发明的实施例,电石反应炉的温度并不受特别限制,本领域技术人员可以根据实际需要进行选择,根据本发明的具体实施例,可以控制所述电石反应炉的温度为1450~1600摄氏度,发明人发现,由于可以通过氧气与超细碳基粉末燃烧为电石反应提供热量,所以并不需要将电石反应炉设置过高的温度,只要控制电石反应炉的温度为1450~1600摄氏度即可,由此可以显著降低电石反应炉的能耗。根据本发明的实施例,分离器600具有混合烟气入口601、合成气出口602和电石出口603,混合烟气入口601与混合烟气出口504相连,分离器600适于将包含电石产品和合成气的混合烟气进行分离处理,以便得到合成气和电石。根据本发明的具体实施例,合成气出口602可以与预热炉400相连,由此,可以利用合成气对预热炉400中的混合物料进行预热处理,从而显著降低预热炉400所需的能耗。参考图2,根据本发明实施例的制备电石的系统进一步包括:超细碳基粉末过滤筛10和超细钙基粉末过滤筛20。根据本发明的实施例,超细碳基粉末过滤筛10设置在碳基粉碎装置100和混合装置300之间,超细碳基粉末过滤筛10适于对碳基粉碎装置100制备得到的超细碳基粉末进行过筛处理。根据本发明的具体实施例,超细碳基粉末过滤筛10的孔径可以不大于0.01mm,由此,可以保证进入混合装置300的超细碳基粉末粒径不高于0.01mm,从而有效地提高混合装置300制备得到的混合物料的比表面积。根据本发明的实施例,超细钙基粉末过滤筛20设置在钙基粉碎装置200和混合装置300之间,超细钙基粉末过滤筛20适于对钙基粉碎装置200制备得到的超细钙基粉末进行过筛处理。根据本发明的具体实施例,超细钙基粉末过滤筛20的孔径可以不大于0.01mm,由此,可以保证进入混合装置300的超细钙基粉末粒径不高于0.01mm,从而有效地提高混合装置300制备得到的混合物料的比表面积。由此,根据本发明的实施例,该系统通过采用碳基粉碎装置和钙基粉碎装置分别将碳基原料和钙基原料粉碎为超细碳基粉末和超细钙基粉末,进而通过利用超细碳基粉末过滤筛和超细钙基粉末过滤筛对超细碳基粉末和超细钙基粉末进行过筛处理,保证进入后续进入混合装置的超细碳基粉末和超细钙基粉末的粒度均不大于0.01mm,由此可以提高物料的比表面积和接触面积,从而显著降低制备电石所需的能耗;通过混合装置将超细碳基粉末和超细钙基粉末混合后,将混合物料送入预热炉进行预热处理,由此不仅可以得到高附加值的热解气,还可以显著提高混合物料的反应活性;进而将预热得到的高温固体物料热送至电石反应炉,同时通入氧气,与高温固体物料中的碳反应提供热量,并使碳与钙反应生成电石,制备得到的电石与副产的大量合成气以混合烟气的形式进入分离器,经分离处理得到电石产品和合成气,而制备电石产生的灰分在电石反应炉中形成熔融态灰渣,从电石反应炉底部排出。由此,根据本发明实施例的制备电石的系统可以在较低能耗下显著提高制备电石的效率,有效地降低制备电石的成本,同时将制备电石过程中产生的灰分转化为熔融态灰渣的形式进行分离,提高了电石的品质。在本发明的第二方面,本发明提出了一种采用上述实施例的制备电石的系统实施制备电石的方法,根据本发明的实施例,该方法包括:将碳基原料在碳基粉碎装置中进行粉碎处理,以便得到超细碳基粉末;将钙基原料在钙基粉碎装置中进行粉碎处理,以便得到超细钙基粉末;将超细碳基粉末和超细钙基粉末在混合装置中进行混合,以便得到混合物料;将混合物料供给至预热炉并进行预热处理,以便得到热解气和高温固体物料;将高温固体物料和氧气供给至电石反应炉并进行电石反应,以便得到混合烟气和熔融态灰渣。以及将混合烟气供给至分离器进行分离处理,以便得到合成气和电石。下面对根据本发明实施例的制备电石的方法进行详细描述,参考图4~5,该方法包括:S100:碳基原料粉碎处理该步骤中,将碳基原料在碳基粉碎装置中进行粉碎处理,以便得到超细碳基粉末。具体地,碳基原料可以为长焰煤。根据本发明的实施例,超细碳基粉末的粒径并不受特别限制,本领域技术人员可以根据实际需要进行选择,根据本发明的具体实施例,超细碳基粉末的粒径可以不高于0.01mm。发明人发现,通过将碳基原料破碎至该粒径,可以显著提高得到的超细碳基粉末的比表面积和接触面积,使超细碳基粉末与超细钙基粉末充分混合均匀,由此可以显著降低后续电石反应所需的温度,使混合物料中的碳与钙可以在较低温度下发生反应生成电石。S200:钙基原料粉碎处理该步骤中,将钙基原料在钙基粉碎装置中进行粉碎处理,以便得到超细钙基粉末。具体地,钙基原料可以为生石灰。根据本发明的实施例,超细钙基粉末的粒径并不受特别限制,本领域技术人员可以根据实际需要进行选择,根据本发明的具体实施例,超细钙基粉末的粒径可以不高于0.01mm。发明人发现,通过将钙基原料破碎至该粒径,可以显著提高得到的超细钙基粉末的比表面积和接触面积,使超细钙基粉末与超细碳基粉末充分混合均匀,由此可以显著降低后续电石反应所需的温度,使混合物料中的碳与钙可以在较低温度下发生反应生成电石。S300:混合处理该步骤中,将超细碳基粉末和超细钙基粉末在混合装置中进行混合,以便得到混合物料。具体地,在将超细碳基粉末和超细钙基粉末混合前,可以先采用超细碳基粉末过滤筛和超细钙基粉末过滤筛分别对超细碳基粉末和超细钙基粉末进行过筛处理,由此,可以保证进入混合装置的超细碳基粉末和超细钙基粉末粒径均不高于0.01mm,从而有效地提高混合装置制备得到的混合物料的比表面积。根据本发明的实施例,混合物料中超细碳基粉末和超细钙基粉末的质量比并不受特别限制,本领域技术人员可以根据实际需要进行选择,根据本发明的具体实施例,可以将超细碳基粉末和超细钙基粉末按照质量比(3~4):1进行混合。根据本发明的实施例,在后续电石反应中,需通入氧气与混合物料中的碳燃烧为反应提供热量,所以超细碳基粉末的配入量须高于超细钙基粉末的配入量,发明人通过大量实验意外地发现,将超细碳基粉末和超细钙基粉末按照质量比(3~4):1进行混合的效果较好,如果超细碳基粉末的配入量过低,则无法满足制备电石和燃烧提供热量的需要,而超细碳基粉末的配入量过高则会造成资源的浪费。S400:预热处理该步骤中,将混合物料供给至预热炉并进行预热处理,以便得到热解气和高温固体物料。根据本发明的实施例,通过采用预热炉对混合物物料进行预热处理,可以显著提高混合物料的反应活性,从而降低后续电石反应中所需的能耗和所需的氧气的量,进而降低整个系统的综合能耗,另外,通过采用预热炉对混合物物料进行预热处理,还可以使混合物料生成高附加值的热解气,从而进一步提高经济效益。根据本发明的实施例,预热炉的温度并不受特别限制,本领域技术人员可以根据实际需要进行选择,根据本发明的具体实施例,可以控制预热炉的温度为550~800摄氏度。发明人通过大量实验意外地发现,由于采用粒径不高于0.01mm的超细碳基粉末和超细钙基粉末制备混合物料,混合物料具有较高的比表面和接触面积,从而可以在较低温度(550~800摄氏度)下达到对混合物料的预热效果。S500:电石反应该步骤中,将高温固体物料和氧气供给至电石反应炉并进行电石反应,以便得到混合烟气和熔融态灰渣。具体地,根据本发明的实施例,可以将经预热炉预热得到的高温固体物料热送至电石反应炉,并向电石反应炉中通入氧气,进行上述电石反应;在电石反应炉中,氧气和高温固体物料中的碳燃烧提供热量,从而可以显著降低电石反应炉的能耗,进一步地,高温固体物料中碳和钙反应生成电石和大量高温合成气,生成的电石呈固体粉状,与合成气以混合烟气的形式从电石反应炉上部排出,而电石反应产生的灰分形成熔融态灰渣,从电石反应炉底部排出,由此可以避免灰分对环境的污染。根据本发明的具体实施例,电石反应炉中氧气、超细碳基粉末和超细钙基粉末的质量比可以为(2~3):(3~4):1。发明人发现,在电石反应中,需通入氧气与混合物料中的碳燃烧为反应提供热量,所以超细碳基粉末的配入量须高于超细钙基粉末的配入量;根据本发明的另一些实施例,氧气与超细碳基粉末的质量比可以为(0.5~0.6):1,发明人发现,在此配比下氧气可以与超细碳基粉末有效地进行燃烧并为电石反应提供热量,从而降低电石反应炉的能耗。根据本发明的实施例,电石反应炉的温度并不受特别限制,本领域技术人员可以根据实际需要进行选择,根据本发明的具体实施例,可以控制所述电石反应炉的温度为1450~1600摄氏度,发明人发现,由于可以通过氧气与超细碳基粉末燃烧为电石反应提供热量,所以并不需要将电石反应炉设置过高的温度,只要控制电石反应炉的温度为1450~1600摄氏度即可,由此可以显著降低电石反应炉的能耗。S600:分离处理该步骤中,将混合烟气供给至分离器进行分离处理,以便得到合成气和电石。根据本发明的具体实施例,可以将分离得到的合成气返回至预热炉,用于对混合物料进行预热处理,由此可以显著降低预热炉所需的能耗。由此,根据本发明的实施例,该方法通过采用碳基粉碎装置和钙基粉碎装置分别将碳基原料和钙基原料粉碎为超细碳基粉末和超细钙基粉末,进而通过利用超细碳基粉末过滤筛和超细钙基粉末过滤筛对超细碳基粉末和超细钙基粉末进行过筛处理,保证进入后续进入混合装置的超细碳基粉末和超细钙基粉末的粒度均不大于0.01mm,由此可以提高物料的比表面积和接触面积,从而显著降低制备电石所需的能耗;通过混合装置将超细碳基粉末和超细钙基粉末混合后,将混合物料送入预热炉进行预热处理,由此不仅可以得到高附加值的热解气,还可以显著提高混合物料的反应活性;进而将预热得到的高温固体物料热送至电石反应炉,同时通入氧气,与高温固体物料中的碳反应提供热量,并使碳与钙反应生成电石,制备得到的电石与副产的大量合成气以混合烟气的形式进入分离器,经分离处理得到电石产品和合成气,而制备电石产生的灰分在电石反应炉中形成熔融态灰渣,从电石反应炉底部排出。由此,根据本发明实施例的制备电石的方法可以在较低能耗下显著提高制备电石的效率,有效地降低制备电石的成本,同时将制备电石过程中产生的灰分转化为熔融态灰渣的形式进行分离,避免了对环境的污染。下面参考具体实施例,对本发明进行描述,需要说明的是,这些实施例仅仅是描述性的,而不以任何方式限制本发明。实施例参考图5制备电石:采用气流磨将粒度在5mm以下的长焰煤以及生石灰分别进行细磨干燥处理,以便分别得到粒径低于0.01mm的超细碳基粉末和超细钙基粉末;将超细碳基粉末和超细钙基粉末按照重量3.5:1的比例混合送入预热炉,在650℃温度下,产生热解气和高温固体物料,高温固体物料直接热送入反应炉,同时向反应炉中通入氧气,控制反应炉温1500℃左右,得到固态电石颗粒和高温合成气,同时碳基材料燃烧产生的熔融态灰渣从反应炉底部排出,电石随着高温合成气以混合烟气的形式从反应炉上部排出,实现了灰渣和电石的分离,提高了电石品质,电石反应炉排出的混合烟气通过分离器实现电石和合成气的分离,电石在分离器底部排出,高温合成气则进入预热炉为混合物料进行预热,回收了合成气所带的高温显热。对电石产品取5批样品(每批样品50g)在LJD碳化钙发气量测定装置上按照国标测量发气量,发气量均在320L/kg之上,达到超优质电石标准,此外,上述采用的长焰煤工业分析如表1所示。表1长焰煤工业分析(wt%)水分(Mad)灰分(Aad)挥发分(Vad)固定碳(Cad)8.074.8030.3056.83在本说明书的描述中,参考术语“一个实施例”、“一些实施例”、“示例”、“具体示例”、或“一些示例”等的描述意指结合该实施例或示例描述的具体特征、结构、材料或者特点包含于本发明的至少一个实施例或示例中。在本说明书中,对上述术语的示意性表述不必须针对的是相同的实施例或示例。而且,描述的具体特征、结构、材料或者特点可以在任一个或多个实施例或示例中以合适的方式结合。此外,在不相互矛盾的情况下,本领域的技术人员可以将本说明书中描述的不同实施例或示例以及不同实施例或示例的特征进行结合和组合。尽管上面已经示出和描述了本发明的实施例,可以理解的是,上述实施例是示例性的,不能理解为对本发明的限制,本领域的普通技术人员在本发明的范围内可以对上述实施例进行变化、修改、替换和变型。当前第1页1 2 3