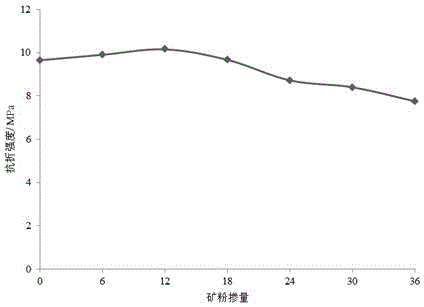
本发明涉及水工结构领域,特别是一种用于在役桥梁工程、水利水电工程、港口航道与海岸工程等水工环境下的混凝土面强化修补材料。
背景技术:
:随着我国基础设施建设的迅猛发展,钢筋混凝土结构已经普遍使用于桥梁工程、水利水电工程、港口航道与海岸工程等。但在水工环境(如桥梁工程、水利水电工程、港口航道与海岸工程等经常或周期性有水作用的环境)下,钢筋混凝土结构耐久性问题日益突出。一方面受高速含沙水流冲刷,混凝土表面会遭受较严重的磨损,造成钢筋保护层减小;另一方面由于水中氯盐侵蚀,混凝土中的钢筋易发生锈蚀,造成混凝土结构出现锈胀裂缝,表层剥落。若不及时维修,如此恶性循环则会大大降低钢筋混凝土结构的承载力和使用寿命。为保证水工环境下既有混凝土建筑物安全运行,我国学者提出了“以表面防护代替整体防护”的技术思想,进行了许多修补材料和修补工艺的研究及应用。现有的修补防护材料主要有聚脲材料、环氧系列材料以及丙乳砂浆等。与其他材料相比,聚脲材料无论是在抗冲磨性能、耐久性能,还是与老混凝土的粘结性方面均表现出较大优势,且工程实践的效果也非常显著,但它一方面价格较贵,另一方面只能作为防护材料,不能作为修补材料进行工程修复。传统的环氧砂浆或环氧树脂材料虽然本身具有优异的强度和抗冲磨性,但是在与老混凝土粘结问题上易产生内应力,导致开裂鼓包等问题。丙乳砂浆作为修补材料与混凝土的粘结性和抗碳化性能优异,在钢筋混凝土结构的防渗防腐以及维修工程中应用较多,但由于其在抗冲磨性及抗氯离子渗透性能方面不足,不能满足实际工程中的要求。因此,提供一种可以提高混凝土抗冲磨性能、延缓钢筋锈蚀等作用的修补材料,已成为本领域亟待解决的技术难题。技术实现要素:针对上述问题,本发明提供一种水工混凝土表面强化修补材料,通过矿粉等量取代水泥的方式对丙乳砂浆的性能进行提升,本发明是这样实现的:一种水工混凝土表面强化修补材料,该材料组分及配比如下:以重量份计,丙乳30份,胶凝材料100份;细砂200份;水30份;其中,所述凝胶材料由水泥和矿粉组成。优选的,本发明所述水工混凝土表面强化修补材料,所述凝胶材料中,矿粉所占凝胶材料的质量比为6-36%,余量为水泥。优选的,本发明所述水工混凝土表面强化修补材料中,所述矿粉比表面积为411m2/kg。一种如本发明所述水工混凝土表面强化修补材料在修补混凝土工程中的应用。如本发明所述水工混凝土表面强化修补材料在修补混凝土工程中的应用,其具体步骤如下:A)施工前,清理混凝土表面杂物,打磨混凝土表面去除松软的砂浆,并用水清洗干净;B)在混凝土表面刷1-2mm厚的丙乳净浆作为修补材料和老混凝土之间的粘结剂;C)涂覆所述水工混凝土表面强化修补材料,厚度为7-10mm;即完成对混凝土表面的修复。优选的,如本发明所述应用中,所述丙乳净浆是由等质量的水泥和丙乳混合获得的。修补材料可通过调整矿粉掺量来满足不同的工程需求,若工程对修补材料的力学性能、抗冲磨性及抗碳化性有较高的要求,矿粉掺量建议为6-12重量份;若对修补材料抗氯离子渗透性能有较高的要求,矿粉掺量建议为36重量份。本发明中,水胶比(水与胶凝材料的质量比)及丙乳比(丙乳与胶凝材料的质量比)优选为0.3。矿粉是活性矿物掺合料的一种,具有较好的填充效应、火山灰效应和缓凝减水作用,可用来改善混凝土微结构,提高混凝土的性能。其中,密实填充作用是指一般情况下,矿物掺合料的颗级比水泥颗粒小的多,能填充在水泥颗粒之间,提高水泥基材料的密实程度,从而改变体系内部的孔结构。火山灰作用是指活性矿物掺合料中富含大量的Al2O3和SiO2等活性氧化物能在水泥进行水化反应后,继续发生二次水化反应产生CSH胶凝颗粒,进而改善水泥砂浆或混凝土的内部结构。缓凝减水作用是指矿物掺合料颗粒的细度较高,比表面积较大,取代水泥后级配体系具有较强的流动体系,相同稠度标准下,可以降低水量;在用水量不变的条件下,也可以增加水泥基材料的流动度,具有矿物减水的作用。考虑力学性能和抗冲磨性能:随着矿粉掺量的增加,一方面由于微集料的填充效应提高了砂浆密实性,另一方面火山灰反应改善了砂浆表面状况,进而提高了砂浆的力学性能及抗冲磨性能;但矿粉掺量超过20份后,由于本试验试件的配比设计均为以矿物掺合料等量取代水泥,水泥含量明显减少,矿粉的填充效应和火山灰效应的综合作用不再占优势,水泥水化反应产生的硅酸钙总量减少,进而导致力学性能及抗冲磨强度降低;因此,需获得较高的力学性能及抗冲磨性能,矿粉掺量建议为6-12重量份。考虑抗碳化性能:随着矿粉掺量的增加,水泥含量减少,水化反应后的Ca(OH)2的含量随之降低;另一方面矿粉与水化反应产生的Ca(OH)2发生火山灰反应,Ca(OH)2进一步被消耗掉,与CO2结合能力降低,抗碳化性能降低。因此为保证既有混凝土结构原有的抗碳化性能,修补材料中矿粉掺量不宜超过36重量份。考虑抗氯离子渗透性能:随着矿粉掺量的增加,一方面矿粉的火山灰反应使C-S-H胶凝含量增多堵塞了砂浆内部的通道,改善了砂浆孔结构,同时矿粉微粉的掺入在水泥颗粒间起到了填充密实的作用进一步阻碍了氯离子的扩散;另一方面二次水化反应后的产物如C3A等物质提高了固化氯离子的能力,因此掺入矿粉后的丙乳砂浆抗氯离子渗透能力明显增强。因此,在仅考虑抗氯离子渗透性条件下,矿粉掺量建议为36重量份。与现有技术相比,本发明具有如下有益效果:1、本发明产本既能用于混凝土结构防护,又能作为修补材料在修复工程中大量使用。2、本发明产本具有良好的抗压、抗折、粘结强度、耐久性好以及施工方便等特征,并且针对不同工程需求提出修补材料中矿粉建议掺量。附图说明图1为28d抗折强度随水工混凝土表面强化修补材料中矿粉掺量增加的变化曲线。图2为28d抗压强度随水工混凝土表面强化修补材料中矿粉掺量增加的变化曲线。图3为28d粘结强度随水工混凝土表面强化修补材料的矿粉掺量增加的变化曲线。图4为抗冲磨强度随水工混凝土表面强化修补材料中矿粉掺量增加的变化曲线。图5为28d碳化深度随水工混凝土表面强化修补材料中矿粉掺量增加的变化曲线。图6为氯离子扩散系数随水工混凝土表面强化修补材料中矿粉掺量增加的变化曲线。图7为实施例通港二桥修补前概况示意图;其中,图7(a)-(d)依次为港二桥全貌图、桥墩钢筋外露示意图、桥台迎水面混凝土空蚀示意图、桥台过流面混凝土冲蚀示意图。图8为施工部位示意图;其中图8(a)为迎水面;(b)为过流面。图9为修补后修补材料与基底混凝土粘结示意图。具体实施方式实施例中涉及的原料来源:矿粉,标号为S95级矿粉,其比表面积为411m2/kg,购自句容市金润粉体材料有限公司;丙乳,细度为200-1000,购自南京瑞迪高新技术公司;细沙,其细度模数为1.92,平均粒径为0—2.5mm,购自南京栖霞区渡江砂场;水泥,普通硅酸盐水泥,标号为42.5R,购自南京江南水泥厂提供。实施例1矿粉掺量对修补材料性能影响实验依据矿粉掺量(以矿粉等量取代水泥,具体指100份由矿粉水泥组成的胶凝材料中,矿粉所占的重量份)的不同,本实验共分7组,依次编号1-7,其矿粉掺量依次为0、6、12、18、24、30、36重量份。水工混凝土表面强化修补材料的各组原料及配比如表1所示:表1组1-7原料及配比编号丙乳(kg)矿粉(kg)水泥(kg)细沙(kg)水(kg)13001002003023069420030330128820030430188220030530247620030630307020030730366420030试验方法:按照《聚合物改性水泥砂浆试验规程》DL/T5126-2001测试本发明的抗折强度、抗压强度,按照日本材料科学协会推荐的粘结抗折试验方法测试本发明与普通水泥砂浆的粘结强度,采用国家标准《水工混凝土试验规程》SL352-2006中的水下钢球法、RCM试验法、快速碳化法测试本发明的抗冲磨强度、抗氯离子渗透性能及抗碳化性能,检测结果如图1-图6所示。图1为28d抗折强度随水工混凝土表面强化修补材料中矿粉掺量增加的变化曲线;图2为28d抗压强度随水工混凝土表面强化修补材料中矿粉掺量增加的变化曲线;图3为28d粘结强度随水工混凝土表面强化修补材料的矿粉掺量增加的变化曲线;图4为28d抗冲磨强度随水工混凝土表面强化修补材料中矿粉掺量增加的变化曲线;图中,曲线方程为y=0.000218x3-0.014012x2+0.192422x+3.940404R2=0.960333。由图1-4可见,在仅改变矿粉掺量的情况下,本发明的获得修补材料的力学性能以及抗冲磨强度基本上都随着-矿粉掺量的增加呈先增加后降低的趋势,即矿粉掺量在12重量份以内时,其力学性能及抗冲磨性能逐渐提高,超过12重量份时力学性能及抗冲磨强度开始下降。其原因是:随着矿粉掺量的增加,一方面由于微集料的填充效应提高了砂浆密实性,另一方面火山灰反应改善了砂浆表面状况,进而提高了砂浆的力学性能及抗冲磨性能;但矿粉掺量超过20份后,由于本试验试件的配比设计均为以矿物掺合料等量取代水泥,水泥含量明显减少,矿粉的填充效应和火山灰效应的综合作用不再占优势,水泥水化反应产生的硅酸钙总量减少,进而导致力学性能及抗冲磨强度降低;因此,需获得较高的力学性能及抗冲磨性能,矿粉掺量建议为6-12重量份。图5为28d碳化深度随水工混凝土表面强化修补材料中矿粉掺量增加的变化曲线;由图5可见,矿粉掺量在36重量份以内且仅改变-矿粉掺量的条件下,实施例中7组材料28d碳化深度随着矿粉掺量的增加而逐渐增大,即抗碳化性能逐渐降低。掺量为0时,丙乳砂浆28d碳化深度为9mm,掺量为30-36重量份时,碳化深度加深了6~7mm,增加幅度约66%-77%。其原因是:随着矿粉掺量的增加,水泥含量减少,水化反应后的Ca(OH)2的含量随之降低;另一方面矿粉与水化反应产生的Ca(OH)2发生火山灰反应,Ca(OH)2进一步被消耗掉,与CO2结合能力降低,抗碳化性能降低。因此为保证既有混凝土结构原有的抗碳化性能,修补材料中矿粉掺量不宜超过36重量份。图6为28d氯离子扩散系数随水工混凝土表面强化修补材料中矿粉掺量增加的变化曲线;由图6可见,随着矿粉掺量由0增加到36重量份,本发明的氯离子扩散系数呈线性降低的趋势,即其抗氯离子渗透性能随着矿粉掺量的增加而明显提高。矿粉掺量为36重量份时,其氯离子扩散系数仅是未掺矿粉的41%,即抗氯离子渗透性能比原来未改性时提高了59%,改善效果较为明显。其原因是:随着矿粉掺量的增加,一方面矿粉的火山灰反应使C-S-H胶凝含量增多堵塞了砂浆内部的通道,改善了砂浆孔结构,同时矿粉微粉的掺入在水泥颗粒间起到了填充密实的作用进一步阻碍了氯离子的扩散;另一方面二次水化反应后的产物如C3A等物质提高了固化氯离子的能力,因此掺入矿粉后的丙乳砂浆抗氯离子渗透能力明显增强。因此,在仅考虑抗氯离子渗透性条件下,矿粉掺量建议为36重量份。实施例2通港二桥工程修补1、工程概况:柘汪镇马站村通港二桥1995年建成通车,为10跨混凝土简支板桥,每跨6m共60m,由于临黄海而建,桥梁处于典型的海工环境,修补前该桥全貌如图7(a)所示。桥墩桥台长期受海水潮汐冲刷,满潮时水面距桥面约1.7m,退潮时水面位于承台处,距桥面约为3.2m。在潮差区,混凝土常年处于干湿交替的环境,受含盐海水腐蚀,以致桥墩出现锈胀裂缝,混凝土剥落,钢筋外露,锈蚀严重如图7(b)所示;同样高度位置桥台混凝土保护层较厚,没有出现锈胀裂缝。桥台迎水面混凝土出现由海浪空蚀引起的坑洞,如图7(c)所示;桥台过流面混凝土不仅有空蚀坑洞,且有含沙水流冲蚀引起骨料外露的现象,如图7(d)所示。桥墩钢筋混凝土锈蚀严重需进行结构加固,而桥台仅是混凝土表面亟待强化,因此将施工部位选于桥台潮差区。2、修补材料配比本次施工时间为2015年7月,修补材料应用于桥台过流面,因此将矿粉掺量分别为6份、36份的两组配比的修补材料均分别覆在桥台的迎水面和过流面上,如图8(a)、(b)所示,为保证两种配比砂浆处于相同的海水环境,将两种砂浆涂覆在同一高度上,修补块上边缘距桥面约为2.3m,处于潮差区位置,以下是两组配比的修补材料每立方米的主要组分及其重量如下:组(1),用于修补桥台的迎水面,采用矿粉掺量6份的修补材料,其组成及配比:丙乳(细度为200-1000):300kg;矿粉(标号为S95级矿粉,其比表面积为411m2/kg):60kg;普通硅酸盐水泥(标号42.5R):940kg;细砂:2000kg;水:300kg;组(2),用于修补桥台的过流面,采用矿粉掺量为36份的修补材料,其组成及配比:丙乳(细度为200-1000):300kg;矿粉(标号为S95级矿粉,其比表面积为411m2/kg):360kg;普通硅酸盐水泥(标号42.5R):640kg;细砂:2000kg;水:300kg。3、施工方法配置丙乳净浆:由等质量的水泥和丙乳混合获得。施工步骤:A)施工前,先清理混凝土表面杂物,用钢刷打磨混凝土表面以去除松软的砂浆,并用水清洗干净,保证粘结面没有杂质;B)涂覆修补材料前,需在基底凿毛表面刷一层1-2mm厚的丙乳净浆进行打底,作为修补材料与基底混凝土之间的粘结剂;C)四块砂浆层高均为600mm,宽为400mm,分别涂覆上述两组修补材料,修补材料涂覆的厚度控制在7-10mm之间。4、修补结果在表面涂覆施工完成约2个月后,观测修补效果并取样用于耐久性性能测试。(1)粘结效果组(1)迎水面的粘接效果如图9所示,由图9可见,本发明产品与基底混凝土粘结较好,修补砂浆层未出现局部脱空现象。(2)耐久性性能测试采用国家标准《水工混凝土试验规程》SL352-2006中的RCM试验法、快速碳化法分别测试2组修补材料的抗氯离子渗透性能及抗碳化性能,同时以未修复的桥台表面混凝土作为对照组,检测结果如表2所示:表2修补后检测结果氯离子扩散系数(10-12m/s)28天碳化深度(mm)对照组3.3819.1组(1)3.1112.6组(2)1.5916.5由表2可以看出本发明获得的水工混凝土表面强化修补材料可以用来改善桥梁混凝土的耐久性。以上实施例仅用以说明本发明的技术方案而非限制,尽管参照较佳实施例对本发明进行了详细说明,本领域的普通技术人员应当理解,可以对本发明的技术方案进行修改,其均应涵盖在本发明的权利要求范围当中。当前第1页1 2 3