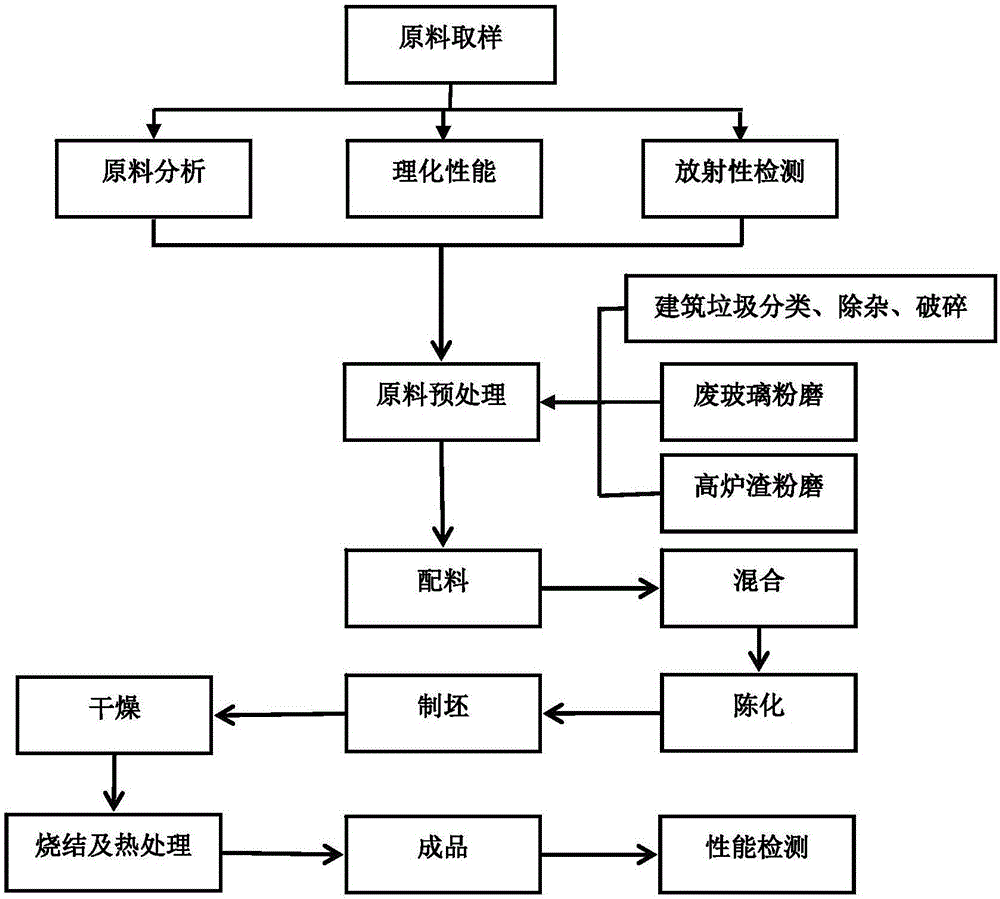
本发明涉及一种利用建筑垃圾和高炉渣制备的烧结砖及其制备方法,属于建筑材料领域。
背景技术:
:传统烧结砖,即凡以粘土、页岩、煤矸石或粉煤灰为原料,经成型和高温焙烧而制得的用于砌筑承重和非承重墙体的砖统称为烧结砖。根据原料不同分为烧结粘土砖、烧结粉煤灰砖、烧结页岩砖等。我国大部分使用的烧结砖为粘土砖,因此,粘土砖也被称为烧结砖。粘土砖的生产和使用,在我国已有3000多年历史。现今,在广大农村地区,房屋建造、围护工程中使用的墙体材料中,烧结砖仍占主导地位。但随着经济的高速发展、人口的日益增长,粘土资源也变得日益紧缺起来;同时,粘土资源与耕地保护政策的矛盾加深,在二十一世纪初期,国家开始禁止生产粘土烧结实心砖。而随着农村人口向城市的转移,2005年后城市农村人口差额逐渐降低,2010年基本持平,之后城市人口逐渐高于农村,城市住房问题成为一大难题。因此,寻求新型墙体材料已成为建筑行业的重中之重。固体废弃物的污染防治及回收利用是近年来政府工作的一大重心,对于环境的保护和固体废弃物的资源化利用,我们势在必行。建筑垃圾是指建设、施工单位或个人对各类建筑物、构筑物、管网等进行建设、铺设或拆除、修缮过程中所产生的渣土、弃土、弃料、淤泥及其他废弃物。随着工业化、城市化进程的加速,建筑业也同时快速发展,相伴而产生的建筑垃圾日益增多,中国建筑垃圾的数量已占到城市垃圾总量的1/3以上。因此,建筑垃圾的处理处置问题已成为各界共同关注的问题。结合墙体材料寻求革新与建筑垃圾的回收再利用两项难题,人们改革创新,寻求利用建筑垃圾制备墙体材料的新技术与新工艺。目前我国的建筑垃圾多数采用露天堆放或者填埋的方式进行处理,这样既造成资源的浪费又造成严重的环境污染。经过多年研究发现,固体建筑垃圾如废弃砖块、混凝土块等经过破碎筛分处理后可作为再生骨料来使用,但存在吸水率大、材料性能变异大等缺点,多数难以达到取代天然砂、石等原料的目的;利用废弃混凝土块、粘土砖细骨料、粉煤灰与水泥浆混合制备再生多孔砖,成品抗压强度低、吸水率高、干燥收缩率大,不适合作为承重墙材,较适宜为墙体填充材料来使用;以建筑渣土、拆迁装修垃圾、煤渣为原料制备烧结砖,烧成过程难以控制,不能有效利用其他工业固体废弃物;以固体垃圾渣土、黏土、煤矸石为原料制备烧结砖,虽有效利用了部分渣土,但同时消耗了大量的黏土资源;利用建筑垃圾、工程渣土以及煤渣制备自保温烧结砖,虽成本低廉、解决部分环境问题,但产品在性能方面没有较大的优势。因此,一种有效且大量利用建筑垃圾及工业废渣、成本低、高性能、废弃物附加值高、能大量生产、值得大范围推广的建筑垃圾烧结砖亟待研发。申请公布号为cn103183494a的中国发明专利公开了一种用建筑垃圾制得的环保生态砖,由下列重量份数的原料制成:外加剂13~15份,粉煤灰或电石渣15~17份,建筑垃圾骨料40~42份,页岩石28~30份,其余均为水;所述外加剂由重量份为硅酸盐水泥熟料65~72份、高炉渣20~22份、煤矸石10~24份、水琉璃1~1.5份的原料配制而成,建筑垃圾骨料由重量份为砖瓦35~58份、混凝土50~55份、废浆砂10~12份的原料配制而成的颗粒料,该专利公开的环保态砖的原料仍添加有硅酸盐水泥熟料等外加剂,且其抗压强度等性能仍有待进一步提高。技术实现要素:本发明的目的在于提供一种利用建筑垃圾和高炉渣制备的烧结砖,该烧结砖成本低且性能优异。本发明的第二个目的在于提供一种上述烧结砖的制备方法。为实现上述目的,本发明的技术方案是:一种利用建筑垃圾和高炉渣制备的烧结砖,主要由以下重量份数的原料制成:建筑垃圾60~90份,废玻璃5~15份,高炉渣5~25份。上述建筑垃圾、废玻璃、高炉渣的重量份数之和为100份。上述烧结砖的原料还包括水,所述水的用量为5~20份。上述水为城市自来水。上述烧结砖,密度为1500kg/m3~1800kg/m3。所述建筑垃圾为拆迁或在建过程中产生的弃土、渣土、废旧砖石、废旧混凝土等固体废弃物。所述建筑垃圾中弃土的质量分数为60%~90%。所述弃土为工程挖、填土方平衡后剩余的无法利用的土。其中不同土层所含矿物略有区别,部分弃土中含有大量的石英相,表明此部分废土为沙质土,作为原料能起到降低产品的干燥收缩和烧结收缩率的作用。所述建筑垃圾由以下质量百分比的组分组成:60%~90%弃土,其它建筑垃圾10~40%。所述其它建筑垃圾为渣土、废旧砖石、废旧混凝土等废弃物。所述建筑垃圾主要由cao-sio2-al2o3系列矿物构成。所述高炉渣为冶炼生铁时产生的高炉水渣。本发明中的高炉渣优选为河北某钢厂冶炼生铁时从高炉中排出的高炉水渣。高炉渣中含有晶核剂,可在特定的烧结制度下析出微晶,提高产品强度。所述废玻璃包含但不限于建筑、日用、装饰废玻璃。所述废玻璃优选为在玻璃生产过程中、生活过程中、装修中产生的废玻璃。由于玻璃的软化温度较低,选用废玻璃作为助熔剂可以在较低的温度下形成液相烧结,降低产品的烧结温度。本发明的烧结砖,以建筑垃圾、废玻璃、高炉渣为原料,得到一种抗压强度为20mpa~90mpa(满足国标gb5101、gb13544-2011规定等级mu25的要求)、密度1500kg/m3~1800kg/m3、吸水率15%~20%、饱和系数≤0.89(满足国标对于非严重风化区要求),收缩率≤1%,基本无泛霜,冻融损失率、放射性核素限量符合国家标准的优质烧结砖。本发明的烧结砖具有良好的抗冻、抗风化性能。上述烧结砖的制备方法,包括以下步骤:1)将建筑垃圾、废玻璃、高炉渣与水混匀,得泥料;2)将步骤1)所得泥料陈化3~5h后制成坯体;3)将步骤2)所得坯体于95~105℃干燥1~4h,然后升温至700~750℃保温10~30min,之后继续升温至800~850℃保温1~3h,最后升温至900~1050℃保温1~5h,随炉冷却即得。步骤1)中的水为城市自来水。步骤1)建筑垃圾、废玻璃和高炉渣的含水率均小于1%。所述建筑垃圾的粒度≤20目,废玻璃的粒度≤40目,高炉渣的粒度≤100目。上述≤20目指能够通过20目筛。上述≤40目为能够通过40目筛。上述≤100目是指能够通过100目筛。上述筛为试验筛。上述建筑垃圾和废玻璃在使用前经除杂、粉碎处理。上述建筑垃圾的除杂为剔除垃圾中较大的石块、金属结构件、有机物等,再用磁铁将残存的金属物质剔除。上述建筑垃圾的粉碎为将除杂后的建筑垃圾按照不同类别(即弃土、渣土、废旧砖石、废旧混凝土等)分类进行破碎处理,然后根据不同类别球磨5~30min。球磨后的原料分别过筛。之后装封放置。上述废玻璃的除杂为将废玻璃进行清洗,以去除玻璃上的粉尘等杂质。上述废玻璃的粉碎为将清洗后的废玻璃破碎至粒径≤10mm,然后球磨3~10min。由于收集到的高炉渣一般为大颗粒,在使用前进行粉磨减小粒径,使其粒径≤100目,提高高炉渣粉体的表面活性。所述建筑垃圾的粒径优选为74μm~900μm。所述废玻璃的粒径为≤450μm。所述高炉渣的粒径为≤150μm。步骤1)中建筑垃圾、废玻璃、高炉渣与水混匀,具体为:先将建筑垃圾、废玻璃、高炉渣混合5~30min,然后再加水继续搅拌20~120min,使其混合均匀,得泥料。所述泥料的含水率为5%~20%。步骤2)中的陈化在密封的空间内进行。步骤2)中制成坯体的方法为半干压成型,所述半干压成型的压力为3~20mpa,保压时间5~30s。步骤3)中干燥在干燥箱中进行。步骤3)中于95~105℃干燥1~4h后测量坯体收缩率。将收缩率高、出现裂缝的样品记录并剔除。步骤3)中升温至700~750℃为:先以1~3℃/min的升温速率升温至300℃;再以2~4℃/min的升温速率升温至600℃;然后以4~8℃/min的升温速率升温至700~750℃。上述升温至300℃的升温速率较慢,可以使坯体中游离水和结合水充分排出;从300℃升至600℃,升温速率为2~4℃/min,此阶段玻璃软化,形成液相;从600℃以4~8℃/min的升温速率升至700~750℃,并在此温度下保温10~30min,此阶段为高炉渣形核阶段。步骤3)中升温至800~850℃的升温速率为5~10℃/min。在800~850℃温度下保温1~3h,此阶段为高炉渣析晶阶段,高炉渣形核-晶化,最终析出微晶相。步骤3)中升温至900~1050℃的升温速率为5~10℃/min。此过程中,随着温度升高,晶粒逐渐长大,玻璃熔体粘度系数增大,熔融液相填充孔隙,控制成品最终的强度及密度。本发明通过控制原料的粒径得到最佳的原料粒度范围,并调整废弃物原料间的质量比、废弃物原料总量与水的配比得到原料的最佳配比范围,最后通过控制烧成条件使烧结砖析出微晶相。本发明的烧结砖的制备方法,相比现有烧结砖的制备方法,有以下优势:1)本发明所用原料除水外均属于固体废弃物,一方面保护了耕地、降低了生产成本,另一方面又保护了环境,减轻固体废弃物对环境的污染,变废为宝,综合利用了建筑废弃物与工业废弃物,具有良好的经济和环境效益。2)本发明利用建筑垃圾和高炉渣为原料,通过配料、制坯、干燥、烧结等工序制得轻质高强的烧结砖,整个工艺流程简洁且易于操作,可重复性强,原料来源广,生产耗能少,可实现大规模推广和生产。3)本发明制备方法得到的烧结砖具有强度高、质量轻、收缩率小、烧结温度低的优点,利用废渣生产墙材,不仅降低了建筑材料的成本,保护环境,同时综合利用几种废渣的优势,降低烧结温度的同时,提高墙材的性能,符合国家建筑垃圾回收再利用的发展政策,具有广泛的经济、社会和环境效益。附图说明图1为实施例1中烧结砖的制备方法流程图;图2为实施例2中高炉渣的dsc曲线图;图3为实施例3中950℃条件下烧结所得烧结砖的sem图。具体实施方式下面结合附图对本发明的实施方式作进一步说明。下述实施例中所用建筑垃圾取自郑州市某楼盘建设、某安置区建设等地在建过程中产生的弃土、未及时施工造成凝固的砂浆等固体垃圾以及某小区拆迁过程中产生的废旧砖石、废旧混凝土块等固体废弃物。下述实施例中所用高炉渣为河北某钢厂冶炼生铁时从高炉中排除的高炉水渣。下述实施例中所用废玻璃为玻璃生产过程中、生活过程中、装修中产生的废玻璃。实施例1本实施例利用建筑垃圾和高炉渣制备的烧结砖,由以下重量份数的原料制成:建筑垃圾70份,废玻璃10份,高炉渣20份,水7份;其中建筑垃圾中含有60%的弃土,渣土、废旧砖石等其它建筑垃圾占40%;建筑垃圾的粒径为0.15~0.9mm;废玻璃的粒径为74~150μm;高炉渣的粒径为74~150μm;建筑垃圾、废玻璃、高炉渣的含水率均小于1%。本实施例的烧结砖的制备方法,如图1所示,包括以下步骤:1)原料分析通过xrd、xrf等手段确定原料建筑垃圾、废玻璃、高炉渣的化学组成,初步拟定烧结砖的配比;经检测分析得到废弃物中主要含有ca、al、si、fe的氧化物并含有碱金属化合物;根据国家标准利用低本底多道γ能谱仪测定各固体废弃物的放射性元素含量,确保用于制备烧结砖的原料的放射性元素含量符合标准;2)原料预处理a)对建筑垃圾的预处理:首先除杂,即剔除垃圾中较大的石块、金属结构件、有机物等,再用磁铁将残存的金属物质剔除;将除杂后的建筑垃圾按照不同类别(即弃土、渣土、废旧砖石、废旧混凝土等)分类进行破碎处理,然后按照不同类别球磨5min;球磨后的原料分别过筛,之后分别装封放置;最后干燥至含水率小于1%,以备后用;本实施例选取的建筑垃圾粒径为0.15~0.9mm;b)对废玻璃的预处理:首先将废玻璃简单清洗,去除玻璃上的粉尘等杂质;将清洗后的玻璃破碎至粒径≤10mm,将破碎后的碎玻璃在高能球磨机中球磨3min,然后将玻璃粉体干燥至含水率小于1%后过筛备用;本实施例选取的废玻璃粒径为74~150μm;c)对高炉渣的预处理:将高炉渣球磨过筛,然后干燥至含水率低于1%后备用;本实施例选取的高炉渣粒径为74~150μm;3)混料将处理好的原料按照建筑垃圾70份(其中弃土60%,其它建筑垃圾40%),废玻璃10份,高炉渣20份搅拌5min后加入自来水7份,继续搅拌20min使其混合均匀,得泥料;泥料的含水率为7%;4)陈化:将泥料在密封的空间陈化3h;5)制坯:将陈化后的泥料通过半干压成型制成坯体,成型压力3mpa,保压时间20s;6)烧成:将制好的坯体放入干燥箱中以1℃/min的升温速率升温至100℃并干燥1h,同时测量干燥收缩率,将收缩率高、出现裂缝的样品记录并剔除;将干燥后的坯体放入箱式炉中进行产品的烧结,先以1℃/min的升温速率从室温升至300℃,再以2℃/min的升温速率从300℃升至600℃,然后以4℃/min的升温速率从600℃升至700℃并在700℃保温30min,再以5℃/min的升温速率从700℃升至800℃并于800℃保温1h,最后以5℃/min的升温速率从800℃升温至900℃并在此温度保温1h,随炉冷却即得。实施例2本实施例利用建筑垃圾和高炉渣制备的烧结砖,由以下重量份数的原料制成:建筑垃圾80份,废玻璃8份,高炉渣12份,水10份;其中建筑垃圾中含有质量分数为90%的弃土,渣土、废旧砖石等占10%;建筑垃圾的粒径为0.15~0.45mm,废玻璃的粒径为100~150μm;高炉渣的粒径≤74μm;建筑垃圾、废玻璃、高炉渣的含水率均小于1%。本实施例的原料高炉渣的dsc曲线如图2所示,从中可以看出高炉渣的形核温度为730℃,析晶温度为850℃。本实施例的烧结砖的制备方法,包括以下步骤:1)原料分析通过xrd、xrf等手段确定原料建筑垃圾、废玻璃、高炉渣的化学组成,初步拟定烧结砖的配比;经检测分析得到废弃物中主要含有ca、al、si、fe的氧化物并含有碱金属化合物;根据国家标准利用低本底多道γ能谱仪测定各固体废弃物的放射性元素含量,确保用于制备烧结砖的原料的放射性元素含量符合标准;2)原料预处理a)对建筑垃圾的预处理:首先除杂,即剔除垃圾中较大的石块、金属结构件、有机物等,再用磁铁将残存的金属物质剔除;将除杂后的建筑垃圾按照不同类别(即弃土、渣土、废旧砖石、废旧混凝土等)分类进行破碎处理,然后按照不同类别球磨30min;球磨后的原料依次过筛,后分别装封放置;最后干燥至含水率小于1%,以备后用;本实施例选取的建筑垃圾粒径为0.15~0.45mm;b)对废玻璃的预处理:首先将废玻璃简单清洗,去除玻璃上的粉尘等杂质;将清洗后的玻璃破碎至粒径≤10mm;将破碎后的碎玻璃在高能球磨机中球磨10min;然后将玻璃粉体干燥至含水率小于1%后过筛备用;本实施例选取的废玻璃粒径为100~150μm;c)对高炉渣的预处理:将高炉渣球磨过筛,然后干燥至含水率低于1%后备用;本实施例选取的高炉渣粒径为≤74μm;3)混料将处理好的原料按照建筑垃圾80份(其中弃土90%,其它建筑垃圾10%),废玻璃8份,高炉渣12份搅拌30min后加入10份自来水继续搅拌120min使其混合均匀,得泥料;泥料的含水率为10%;4)陈化:将泥料在密封的空间陈化5h;5)制坯:将陈化后的泥料通过半干压成型制成坯体,成型压力8mpa,保压时间30s;6)烧成:将制好的坯体放入干燥箱中以1℃/min的升温速率升温至95℃并干燥4h,同时测量干燥收缩率,将收缩率高、出现裂缝的样品记录并剔除;将干燥后的坯体放入箱式炉中进行产品的烧结,先以3℃/min的升温速率从室温升至300℃,再以4℃/min的升温速率从300℃升至600℃,然后以5℃/min的升温速率从600℃升至730℃并在730℃保温20min,再以6℃/min的升温速率从730℃升至850℃并在850℃保温2h,最后以8℃/min的升温速率从850℃升至1050℃并于1050℃保温2h,随炉冷却即得。实施例3本实施例利用建筑垃圾和高炉渣制备的烧结砖,由以下重量份数的原料制成:建筑垃圾75份,废玻璃10份,高炉渣15份,水18份;其中建筑垃圾中含有质量分数为80%的弃土,渣土、废旧砖石等其它建筑垃圾占20%;建筑垃圾的粒径为0.074~0.3mm;废玻璃的粒径为0.1~0.45mm;高炉渣的粒径≤74μm;建筑垃圾、废玻璃、高炉渣的含水率均小于1%。本实施例的烧结砖的sem图如图3所示,从中可以看出微晶均匀分布,非晶玻璃体包裹微晶。本实施例的烧结砖的制备方法,包括以下步骤:1)原料分析通过xrd、xrf等手段确定原料建筑垃圾、废玻璃、高炉渣的化学组成,初步拟定烧结砖的配比;经检测分析得到废弃物中主要含有ca、al、si、fe的氧化物并含有碱金属化合物;根据国家标准利用低本底多道γ能谱仪测定各固体废弃物的放射性元素含量,确保用于制备烧结砖的原料的放射性元素含量符合标准;2)原料预处理a)对建筑垃圾的预处理:首先除杂,即剔除垃圾中较大的石块、金属结构件、有机物等,再用磁铁将残存的金属物质剔除;将除杂后的建筑垃圾按照不同类别(即弃土、渣土、废旧砖石、废旧混凝土等)分类进行破碎处理,然后根据不同分类分别球磨15min;球磨后的原料依次过筛,之后分别装封放置;最后干燥至含水率小于1%,以备后用;本实施例选取的建筑垃圾粒径为0.074~0.3mm;b)对废玻璃的预处理:首先将废玻璃简单清洗,去除玻璃上的粉尘等杂质;将清洗后的玻璃破碎至粒径≤10mm;将破碎后的碎玻璃进行粉磨,高能球磨机中球磨7min;然后将玻璃粉体干燥至含水率小于1%后备用;本实施例选取的废玻璃粒径为0.1~0.45mm;c)对高炉渣的预处理:将高炉渣球磨过筛,然后干燥至含水率低于1%后备用;本实施例选取的高炉渣粒径为≤74μm;3)混料将处理好的原料按照建筑垃圾75份(其中弃土80%,其它建筑垃圾20%),废玻璃10份,高炉渣15份搅拌15min后加入18份自来水继续搅拌50min使其混合均匀,得泥料;泥料的含水率为19%;4)陈化:将泥料在密封的空间陈化4h;5)制坯:将陈化后的泥料通过半干压成型制成坯体,成型压力15mpa,保压时间10s;6)烧成:将制好的坯体放入干燥箱中以1℃/min的升温速率升温至105℃并干燥3h,同时测量干燥收缩率,将收缩率高、出现裂缝的样品记录并剔除;将干燥后的坯体放入箱式炉中进行产品的烧结,先以2℃/min的升温速率从室温升至300℃,再以3℃/min的升温速率从300℃升至600℃,然后以8℃/min的升温速率从600℃升至750℃并在750℃保温30min,再以10℃/min的升温速率从750℃升温至830℃并在830℃保温3h,最后以5℃/min的升温速率从830℃升至950℃并于950℃保温5h,随炉冷却即得。实施例4本实施例利用建筑垃圾和高炉渣制备的烧结砖,由以下重量份数的原料制成:建筑垃圾90份,废玻璃5份,高炉渣5份,水20份;其中建筑垃圾中含有80%的弃土,渣土、废旧砖石等其它建筑垃圾20%;建筑垃圾的粒径0.1~0.45mm;废玻璃的粒径74~300μm;高炉渣的粒径74~100μm;建筑垃圾、废玻璃、高炉渣的含水率均小于1%。本实施例的烧结砖的制备方法,包括以下步骤:1)原料分析通过xrd、xrf等手段确定原料建筑垃圾、废玻璃、高炉渣的化学组成,初步拟定烧结砖的配比;经检测分析得到废弃物中主要含有ca、al、si、fe的氧化物并含有碱金属化合物;根据国家标准利用低本底多道γ能谱仪测定各固体废弃物的放射性元素含量,确保用于制备烧结砖的原料的放射性元素含量符合标准;2)原料预处理a)对建筑垃圾的预处理:首先除杂,即剔除垃圾中较大的石块、金属结构件、有机物等,再用磁铁将残存的金属物质剔除;将除杂后的建筑垃圾按照不同类别(即弃土、渣土、废旧砖石、废旧混凝土等)分类进行破碎处理,然后按照建筑垃圾不同分类分别球磨15min;球磨后的原料依次过筛,之后分别装封放置;最后干燥至含水率小于1%,以备后用;本实施例选取的建筑垃圾粒径为0.1~0.45mm;b)对废玻璃的预处理:首先将废玻璃简单清洗,去除玻璃上的粉尘等杂质;将清洗后的玻璃破碎至粒径≤10mm;将破碎后的碎玻璃在高能球磨机中球磨7min;然后将玻璃粉体干燥至含水率小于1%后备用;本实施例选取的废玻璃粒径为74~300μm;c)对高炉渣的预处理:将高炉渣球磨过筛,然后干燥至含水率低于1%后备用;本实施例选取高炉渣粒径为74~100μm;3)混料将处理好的原料按照建筑垃圾90份(其中弃土80%,其它建筑垃圾20%),废玻璃5份,高炉渣5份搅拌15min后加入20份自来水继续搅拌50min使其混合均匀,得泥料;泥料的含水率为20%;4)陈化:将泥料在密封的空间陈化3h;5)制坯:将陈化后的泥料通过半干压成型制成坯体,成型压力20mpa,保压时间5s;6)烧成:将制好的坯体放入干燥箱中以1℃/min的升温速率升温至100℃并干燥1h,同时测量干燥收缩率,将收缩率高、出现裂缝的样品记录并剔除;将干燥后的坯体放入箱式炉中进行产品的烧结,先以2℃/min的升温速率从室温升至300℃,再以3℃/min的升温速率从300℃升至600℃,然后以8℃/min的升温速率从600℃升至720℃并在720℃保温30min,再以10℃/min的升温速率从720℃升温至820℃并在820℃保温3h,最后以5℃/min的升温速率从850℃升至1000℃并于1000℃保温5h,随炉冷却即得。实施例5本实施例利用建筑垃圾和高炉渣制备的烧结砖,由以下重量份数的原料制成:建筑垃圾60份,废玻璃15份,高炉渣25份,水5份;其中建筑垃圾中含有80%的弃土,其它建筑垃圾20%;建筑垃圾的粒径0.074~0.9mm;废玻璃的粒径≤74μm;高炉渣的粒径100~150μm;建筑垃圾、废玻璃、高炉渣的含水率均小于1%。本实施例的烧结砖的制备方法,包括以下步骤:1)原料分析通过xrd、xrf等手段确定原料建筑垃圾、废玻璃、高炉渣的化学组成,初步拟定烧结砖的配比;经检测分析得到废弃物中主要含有ca、al、si、fe的氧化物并含有碱金属化合物;根据国家标准利用低本底多道γ能谱仪测定各固体废弃物的放射性元素含量,确保用于制备烧结砖的原料的放射性元素含量符合标准;2)原料预处理a)对建筑垃圾的预处理:首先除杂,即剔除垃圾中较大的石块、金属结构件、有机物等,再用磁铁将残存的金属物质剔除;将除杂后的建筑垃圾按照不同类别(即弃土、渣土、废旧砖石、废旧混凝土等)分类进行破碎处理,然后根据建筑垃圾不同分类分别球磨15min;球磨后的样品依次过筛,之后分别装封放置;最后干燥至含水率小于1%,以备后用;本实施例选取的建筑垃圾粒径为0.074~0.9mm;b)对废玻璃的预处理:首先将废玻璃简单清洗,去除玻璃上的粉尘等杂质;将清洗后的玻璃破碎至粒径≤10mm;将破碎后的碎玻璃进行粉磨,高能球磨机中球磨7min;然后将玻璃粉体干燥至含水率小于1%后备用;本实施例选取的废玻璃粒径为≤74μm;c)对高炉渣的预处理:将高炉渣球磨过筛,然后干燥至含水率低于1%后备用;本实施例选取高炉渣粒径为100~150μm;3)混料将处理好的原料按照建筑垃圾60份(其中弃土80%,其它建筑垃圾20%),废玻璃15份,高炉渣25份搅拌15min后加入5份自来水继续搅拌50min使其混合均匀,得泥料;泥料的含水率为5%;4)陈化:将泥料在密封的空间陈化1h;5)制坯:将陈化后的泥料通过半干压成型制成坯体,成型压力10mpa,保压时间15s;6)烧成:将制好的坯体放入干燥箱中以1℃/min的升温速率升温至100℃并干燥2h,同时测量干燥收缩率,将收缩率高、出现裂缝的样品记录并剔除;将干燥后的坯体放入箱式炉中进行产品的烧结,先以2℃/min的升温速率从室温升至300℃,再以3℃/min的升温速率从300℃升至600℃,然后以8℃/min的升温速率从600℃升至720℃并在720℃保温10min,再以10℃/min的升温速率从720℃升温至840℃并在840℃保温1h,最后以10℃/min的升温速率从850℃升至1020℃并于1020℃保温2h,随炉冷却即得。实验例对实施例1-5所得的烧结砖进行抗压强度、密度、吸水率、饱和系数、冻融损失率等进行测试,本实验例所有性能测试均根据gbt2542-2012《砌墙砖试验方法》所述试验方法,测试结果如表1所示。表1实施例1-5中的烧结砖的性能测试数据项目抗压强度/mpa密度/kg/m3吸水率/%饱和系数冻融损失率/%收缩率/%实施例149.44154016.920.890.110.12实施例278.08172015.030.850.050.06实施例337.98161016.200.880.140.08实施例466.73169015.790.870.070.10实施例527.78158017.220.890.120.20由表1内容可知,本发明的烧结砖具有烧结温强度高、质量轻、收缩率小的优势。当前第1页12