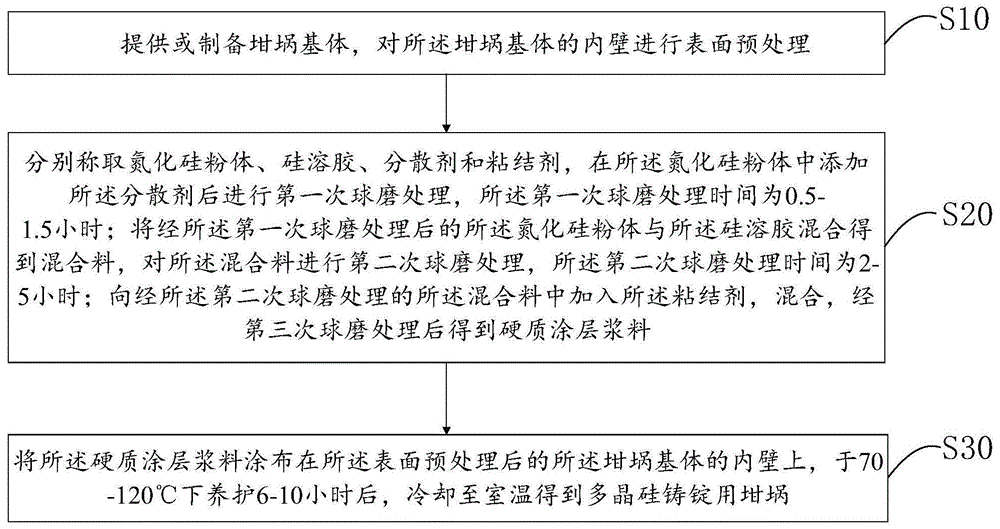
本发明涉及坩埚涂层
技术领域:
,具体涉及一种多晶硅铸锭用坩埚及其制备方法。
背景技术:
:多晶硅电池就是光伏发电的主要发电方式。在多晶硅电池片的制作过程中,铸造多晶硅锭是一道重要的工艺,多晶硅锭的质量将直接影响太阳能电池的转换效率和质量。其中,坩埚是生产多晶硅锭的必要器件之一,主要用于盛装硅料,硅料在坩埚内经高温融化,并最终定向凝固得到多晶硅锭,在整个铸锭工艺中起着重要作用;与此同时,硅锭与坩埚之间的脱模剂—氮化硅涂层,其性能表现也直接影响到硅锭的产品性能表现。目前,在多晶铸锭过程中,氮化硅涂层主要存在以下几点问题:(1)涂层绝大多数靠喷涂造粒方式获得,喷涂过程存在较多扬尘,同时造成了氮化硅粉体的浪费;(2)喷涂获得的氮化硅涂层,颗粒堆积松散不紧密,氮化硅粉体间结合力差,使得涂层会逐渐被硅液冲刷减薄、甚至剥落而造成粘埚;(3)涂层表面粗糙度大,且容易掉落粉尘,使得过多的粉尘掉入进硅液中,带来了更高的硅锭杂质不良率,降低了硅锭利用率;(4)氮化硅涂层仅仅作为脱模剂,对于硅锭红边红区改善等其他功能的开发未能有所挖掘。因此,有必要开发一种抗硅液冲刷能力强,杂质阻隔能力强的多晶硅铸锭用坩埚。技术实现要素:有鉴于此,本发明提供了一种多晶硅铸锭用坩埚及其制备方法,该多晶硅铸锭用坩埚抗硅液冲刷能力强,杂质阻隔能力强,硅锭粘埚率低;制备的硅锭脱模性好,硅锭外观平整干净。第一方面,本发明提供了一种多晶硅铸锭用坩埚,包括坩埚基体,和设置在所述坩埚基体内壁的硬质涂层,所述硬质涂层的成分包括氮化硅粉体、硅溶胶和粘结剂,所述粘结剂包括聚乙烯醇(pva)、聚乙烯吡咯烷酮(pvp)和聚乙烯醇缩丁醛(pvb)中的一种或多种;所述硬质涂层的粗糙度为1.0-1.5μm。可选地,所述硬质涂层的成分还包括改性剂,所述改性剂包括正硅酸乙酯、聚硅氮烷、白炭黑和纳米石英粉中的一种或多种。可选地,所述硬质涂层的厚度为150μm-450μm。进一步地,可选地,所述硬质涂层的厚度为150μm-250μm。例如,所述硬质涂层的厚度为150μm,或为200μm,或为250μm,或为300μm,或为350μm,或为400μm,或为450μm。可选地,所述硬质涂层的邵氏硬度为80-90hd。其中,所述hd表示d型邵氏硬度计检定点的标准硬度值。第二方面,本发明提供了一种多晶硅铸锭用坩埚的制备方法,包括:提供或制备坩埚基体,对所述坩埚基体的内壁进行表面预处理;分别称取氮化硅粉体、硅溶胶、分散剂和粘结剂,在所述氮化硅粉体中添加所述分散剂后进行第一次球磨处理,所述第一次球磨处理时间为0.5-1.5小时;将经所述第一次球磨处理后的所述氮化硅粉体与所述硅溶胶混合得到混合料,对所述混合料进行第二次球磨处理,所述第二次球磨处理时间为2-5小时;向经所述第二次球磨处理的所述混合料中加入所述粘结剂,混合,经第三次球磨处理后得到硬质涂层浆料;将所述硬质涂层浆料涂布在所述表面预处理后的所述坩埚基体的内壁上,于70-120℃下养护6-10小时后,冷却至室温得到多晶硅铸锭用坩埚。可选地,所述分散剂包括去离子水、乙醇或丙醇中的一种或多种;所述粘结剂包括聚乙烯醇、聚乙烯吡咯烷酮和聚乙烯醇缩丁醛中的一种或多种。可选地,所述氮化硅粉体和所述硅溶胶的质量比为1:(0.3-1),所述分散剂的质量占所述硬质涂层浆料总质量的40%-60%,所述粘结剂的质量占所述硬质涂层浆料总质量的1%-10%。可选地,所述加入所述粘结剂的同时还包括添加改性剂,所述改性剂包括正硅酸乙酯、聚硅氮烷、白炭黑和纳米石英粉中的一种或多种,所述改性剂的质量占所述硬质涂层浆料总质量的0.1%-2%。本发明所述第一次球磨处理、第二次球磨处理或第三次球磨处理均可以通过球磨装置完成。所述球磨装置中的球石种类可以但不限于包括氧化锆球或氮化硅球。进一步地,可选地,本发明中,不引入fe、cu等影响硅锭少子寿命,且具备磨削细化粉体的球石,均视为球石种类的保护范围。可选地,所述球磨装置中,所述球石的质量为所述氮化硅粉体质量的2-4倍。可选地,所述球磨装置中,所述球石的球径可以为3-15mm;所述球磨装置中,可以同时配有多种规格球径的球石。例如,所述球磨装置配置10mm球石:5mm球石的质量比为1:(2-4)。进一步地,可选地,所述球磨装置配置10mm球石:5mm球石的质量比为1:2,或为1:3,或为1:4。所述10mm球石是指球径为10mm的球石,所述5mm球石是指球径为5mm的球石。本发明所述第一次球磨处理、第二次球磨处理或第三次球磨处理可以有效磨削细化粉体,并且均不会引入fe、cu等杂质,不会影响制备得到的多晶硅锭少子寿命。可选地,所述表面预处理的过程包括:对所述坩埚基体的内壁的表面依次进行粗糙化打磨处理和表面湿润处理。其中,所述表面湿润处理可以通过润湿试剂对所述坩埚基体内壁的表面进行润湿。可选地,所述润湿试剂可有效降低表面张力,且所述润湿试剂不与坩埚基体或硬质涂层内成分之间发生化学反应;例如润湿试剂可以但不局限于包括去离子水或醇类。通过降低坩埚基体表面张力,可促使硬质涂层浆料更好的附着,极大地提高硬质涂层与坩埚基体的结合强度。所述粗糙化打磨处理可以提高基体粗糙度,进一步增加坩埚基体与硬质涂层之间的结合面积,提高硬质涂层与坩埚基体的结合强度。可选地,所述第三次球磨处理之后,所述涂布过程之前,还包括:将所述经第三次球磨处理后得到硬质涂层浆料经100-200目的过滤器进行过滤后。可选地,所述过滤器可以但不局限于尼龙网等。可选地,所述硬质涂层浆料的粒度d50为0.5-2μm,粒度d90为2-5μm。经过多次球磨处理之后,本发明所述硬质涂层浆料中各成分混合更加均匀,所述硬质涂层浆料的粒度分布更小,其中粒度d50为0.5-2μm,粒度d90为2-5μm,可以一定程度的提升硬质涂层致密性,降低粗糙度。具体地,第一次球磨处理后,氮化硅粉体均匀分散在分散剂中,加入硅溶胶后,可使得硅溶胶微粒充分与氮化硅粉体均匀混合,同时,经过更长时间的第二次球磨处理后,在进一步磨削细化氮化硅粉体的颗粒粒径的同时,磨削细化后的氮化硅粉体的新鲜断面由于存在较大的表面能,会吸附硅溶胶微粒形成胶团,并获得最后所需的胶团颗粒;然后在粘结剂的加入后,所述粘结剂一方面可以改善浆体制备后涂层的常温性能(如不开裂、保水),另一方面,所述粘结剂在最后一步加入,可以使得粘结剂更好的包裹住胶团颗粒,保护胶团颗粒,这样获得的硬质涂层由于氮化硅粉体颗粒表面存在硅溶胶的胶团粒子,在高温下会烧结在一起,可获得结构更加致密、抗硅液侵蚀能力强和杂质阻隔性优异的效果。可选地,所述硬质涂层浆料的粘度范围为10-20cp。本发明所述硬质涂层浆料的粘度值可以通过调节氮化硅粉体、硅溶胶、分散剂或粘结剂的质量比例来调整。可选地,由于粘结剂的含量较少,一般可以通过调节氮化硅粉体、硅溶胶或分散剂含量进行粘度值的调整。可选地,所述涂布过程的涂布方式包括刷涂、流延或浸涂等方式。现有工艺大部分采用喷涂方式,但是喷涂过程中更多的是以将浆料雾化成颗粒,以颗粒堆垛的方式在坩埚基体上制备出一定厚度的涂层;而相比于现有工艺的喷涂,本发明所述的刷涂、流延或浸涂等涂布方式,均为将硬质涂层浆料溶液直接接触坩埚基体,以涂覆方式附着在坩埚上,致密性均更优于喷涂方式,得到的硬质涂层的粗糙度也进一步减小。第三方面,本发明还提供了一种包含本发明第二方面所述的所述制备方法制得的多晶硅铸锭用坩埚在多晶硅铸锭方面的应用。本发明所述多晶硅铸锭用坩埚可以用于制备高质量的晶体硅锭,包括用于制备多晶硅和/或类单晶硅;具有广泛而重要的应用前景。本发明的有益效果包括:(1)本发明所述多晶硅铸锭用坩埚的坩埚基体内壁上设置有硬质涂层,该硬质涂层稳定、耐高温,具有良好的致密性和硬度,所述多晶硅铸锭用坩埚抗硅液冲刷能力强,杂质阻隔能力强,并且硅锭粘埚率低,大大降低生产成本。(2)本发明所述多晶硅铸锭用坩埚的制备方法采用涂布方式,采用多次球磨的方式配置更细、更均匀的硬质涂层浆料,使硬质涂层内的颗粒堆垛最大化,颗粒间接触面积加大,颗粒间结合力增强,实现硬度更突出,结构更致密的硬质涂层,可有效的提高抗硅液冲刷能力;经球磨后的氮化硅粉体进一步进行分散和破碎磨削,粒度进一步降低,硬质涂层具备更为光滑的表观结构,可以有效改善涂层脱落,硅锭粘埚率高的情况。(3)本发明所述多晶硅铸锭用坩埚,具有致密的硬质涂层结构,整个硬质涂层内的扩散通道极少,杂质微粒的震动阻碍增多,扩散速度大幅降低,从而使得多晶硅铸锭用坩埚向硅锭中的杂质扩散量大幅度减少,并体现出更优的硅锭红区,降低硅锭损耗率,提高硅锭出材率;制备的硅锭脱模性好,硅锭外观平整干净。本发明的优点将会在下面的说明书中部分阐明,一部分根据说明书是显而易见的,或者可以通过本发明实施例的实施而获知。附图说明为更清楚地阐述本发明的内容,下面结合附图与具体实施例来对其进行详细说明。图1为本发明一实施例提供的多晶硅铸锭用坩埚的制备方法的工艺流程图。图2为本发明一实施例提供的多晶硅铸锭用坩埚的结构示意图。图3为本发明一实施例提供的多晶硅铸锭用坩埚的硬质涂层结构对比图;图3中(a)为常规喷涂法制备的多晶硅铸锭用坩埚,图3中(b)为本发明所述多晶硅铸锭用坩埚。图4为本发明另一实施例提供的多晶硅铸锭用坩埚的硬质涂层的扫描电镜图;图4中(a)为常规喷涂法制备的多晶硅铸锭用坩埚,图4中(b)为本发明所述多晶硅铸锭用坩埚。具体实施方式以下所述是本发明实施例的优选实施方式,应当指出,对于本
技术领域:
的普通技术人员来说,在不脱离本发明实施例原理的前提下,还可以做出若干改进和润饰,这些改进和润饰也视为本发明实施例的保护范围。下面分多个实施例对本发明实施例进行进一步的说明。其中,本发明实施例不限定于以下的具体实施例。在不变主权利的范围内,可以适当的进行变更实施。若无特别说明,本发明实施例所采用的原料及其它化学试剂皆为市售商品。如图1所示,本发明一实施例提供了一种多晶硅铸锭用坩埚的制备方法,包括:s10、提供或制备坩埚基体,对所述坩埚基体的内壁进行表面预处理;s20、分别称取氮化硅粉体、硅溶胶、分散剂和粘结剂,在所述氮化硅粉体中添加所述分散剂后进行第一次球磨处理,所述第一次球磨处理时间为0.5-1.5小时;将经所述第一次球磨处理后的所述氮化硅粉体与所述硅溶胶混合得到混合料,对所述混合料进行第二次球磨处理,所述第二次球磨处理时间为2-5小时;向经所述第二次球磨处理的所述混合料中加入所述粘结剂,混合,经第三次球磨处理后得到硬质涂层浆料;s30、将所述硬质涂层浆料涂布在所述表面预处理后的所述坩埚基体的内壁上,于70-120℃下养护6-10小时后,冷却至室温得到多晶硅铸锭用坩埚。可选地,所述s10中,所述坩埚基体可以但不限于包括石英坩埚或石墨坩埚。所述表面预处理的过程包括:对所述坩埚基体的内壁的表面依次进行粗糙化打磨处理和表面湿润处理。其中,所述表面湿润处理可以通过润湿试剂对所述坩埚基体内壁的表面进行润湿。可选地,所述润湿试剂可有效降低表面张力,且所述润湿试剂不与坩埚基体或硬质涂层内成分之间发生化学反应;例如润湿试剂可以但不局限于包括去离子水或醇类。通过降低坩埚基体表面张力,可促使硬质涂层浆料更好的附着,极大地提高硬质涂层与坩埚基体的结合强度。所述粗糙化打磨处理可以提高基体粗糙度,增加坩埚基体与硬质涂层之间的结合面积,提高硬质涂层与坩埚基体的结合强度。可选地,所述s20中,所述氮化硅粉体和所述硅溶胶的质量比为1:(0.3-1)。进一步地,硬质涂层浆料中,所述氮化硅粉体和所述硅溶胶的质量比为1:(0.5-0.8),所述粘结剂的质量占所述硬质涂层浆料总质量的1%-10%,所述分散剂的质量占所述硬质涂层浆料总质量的40%-60%。进一步地,可选地,所述粘结剂的质量占所述硬质涂层浆料总质量的1%-10%。可选地,经第一次球磨处理、第二次球磨处理和第三次球磨处理后得到的所述硬质涂层浆料的粒度d50为0.5-2μm,粒度d90为2-5μm。第一次球磨处理、第二次球磨处理和第三次球磨处理的总用时至少在4h以上。可选地,第一次球磨处理、第二次球磨处理和第三次球磨处理的总用时为4h-24h。整个球磨处理以粒度分布大小作为最终的管控标准,粒度达到要求的范围,即可停止球磨。可选地,可选地,所述硬质涂层浆料的粘度范围为10-20cp。本发明所述硬质涂层浆料的粘度值可以通过调节氮化硅粉体、硅溶胶、分散剂或粘结剂的质量比例来调整。可选地,由于粘结剂的含量较少,一般可以通过调节氮化硅粉体、硅溶胶或分散剂含量进行粘度值的调整。可选地,所述s30中,所述养护过程中的温度制恒定在于70-120℃。该温度下的养护过程中可以有效的排除硬质涂层中的水分等分散剂成分,同时又可以保留住涂层中粘结剂固相,保证硬质涂层在盛载硅料时都能保持加好的硬质和不掉粉状态。养护过程结束,自然冷却后可直接进行使用。由于,坩埚基体经历1000℃以上的高温,会增加坩埚的热历史时间,加大坩埚风险,且给后续铸锭过程中带来不可预测的风险,因此,本发明所述制备方法采用的较低温度的养护温度可以有效避免该风险,同时减少生产能耗,降低生产成本。整个养护过程对气氛无特殊要求,整个过程保持温度的恒定以及养护窑炉内排水气的管道顺畅即可。如图2所示,本发明还提供了一种由于本发明所述实施例提供的制备方法制备的多晶硅铸锭用坩埚100,包括坩埚基体10,和设置在所述坩埚基体10内壁的硬质涂层20,所述硬质涂层20的成分包括氮化硅粉体、硅溶胶和粘结剂,所述粘结剂包括聚乙烯醇(pva)、聚乙烯吡咯烷酮(pvp)和聚乙烯醇缩丁醛(pvb)中的一种或多种;所述硬质涂层的粗糙度为1.0-1.5μm。可选地,所述硬质涂层的厚度为150μm-450μm。实施例1一种多晶硅铸锭用坩埚的制备方法,包括:提供一石英坩埚基体,用去离子水对所述石英坩埚基体的内壁进行表面润湿处理;称取氮化硅粉体1000g,在氮化硅粉体中添加分散剂去离子水550g后进行第一次球磨处理,第一次球磨处理时间为1小时;将经第一次球磨处理后的氮化硅粉体与硅溶胶750g混合得到混合料,对混合料进行第二次球磨处理,第二次球磨处理时间为3小时;向经过第二次球磨处理的混合料中加入聚乙烯醇粘结剂115g,混合,经第三次球磨处理后得到硬质涂层浆料,然后使用100目尼龙网对硬质涂层浆料过滤处理;将过滤后的硬质涂层浆料通过羊毛刷均匀刷涂在石英坩埚基体的内壁上,于100℃下养护10小时后,冷却至室温得到多晶硅铸锭用坩埚,其中,多晶硅铸锭用坩埚的硬质涂层厚度为250μm。实施例2一种多晶硅铸锭用坩埚的制备方法,包括:提供一石英坩埚基体,用去离子水对所述石英坩埚基体的内壁进行表面润湿处理;称取氮化硅粉体1000g,在氮化硅粉体中添加分散剂乙醇550g后进行第一次球磨处理,第一次球磨处理时间为1.5小时;将经第一次球磨处理后的氮化硅粉体与硅溶胶750g混合得到混合料,对混合料进行第二次球磨处理,第二次球磨处理时间为5小时;向经过第二次球磨处理的混合料中加入聚乙烯吡咯烷酮粘结剂118g,混合,经第三次球磨处理后得到硬质涂层浆料,然后使用100目尼龙网对硬质涂层浆料过滤处理;将过滤后的硬质涂层浆料通过羊毛刷均匀刷涂在石英坩埚基体的内壁上,于100℃下养护8小时后,冷却至室温得到多晶硅铸锭用坩埚,其中,多晶硅铸锭用坩埚的硬质涂层厚度为250μm。实施例3一种多晶硅铸锭用坩埚的制备方法,包括:提供一石英坩埚基体,用去离子水对所述石英坩埚基体的内壁进行表面润湿处理;称取氮化硅粉体1000g,在氮化硅粉体中添加分散剂去离子水550g后进行第一次球磨处理,第一次球磨处理时间为0.8小时;将经第一次球磨处理后的氮化硅粉体与硅溶胶750g混合得到混合料,对混合料进行第二次球磨处理,第二次球磨处理时间为5小时;向经过第二次球磨处理的混合料中加入聚乙烯醇粘结剂115g和白炭黑25g,混合,经第三次球磨处理后得到硬质涂层浆料,然后使用100目尼龙网对硬质涂层浆料过滤处理;将过滤后的硬质涂层浆料通过羊毛刷均匀刷涂在石英坩埚基体的内壁上,于100℃下养护10小时后,冷却至室温得到多晶硅铸锭用坩埚,其中,多晶硅铸锭用坩埚的硬质涂层厚度为300μm。效果实施例(1)粗糙度(ra值)对比测试将由本发明所述实施例提供的制备方法制得的多晶硅铸锭用坩埚与常规喷涂法制备多晶硅铸锭用坩埚的粗糙度进行对比测试,分别从各自两组实验组中随机选取5个检测点进行测试,结果如表1所示:表1:粗糙度对比测试数据表对象取点1取点2取点3取点4取点5平均值(单位:μm)喷涂法对比组124.34020.12325.17126.58922.61023.767喷涂法对比组220.16222.65021.22721.56023.12321.744本发明实验组11.5010.9981.2131.2200.9811.183本发明实验组21.3321.0521.4851.6631.4761.402从表1所述的数据对比可知,常规喷涂工艺制备的多晶硅铸锭用坩埚的粗糙度(ra值)的平均值超过20μm,而本发明所述多晶硅铸锭用坩埚的粗糙度的平均值仅为1.183μm或1.402μm,粗糙度明显减少。进一步参见图3所示硬质涂层结构对比图,图3中(b)的本发明多晶硅铸锭用坩埚的硬质涂层表面光滑平整,颗粒之间结合紧密,表面无肉眼可见的颗粒;而图3中(a)的常规喷涂法制备的多晶硅铸锭用坩埚颗粒多,颗粒之间堆积间隙大,涂层粗糙度大。(2)涂层致密性和硬度对比测试将由本发明所述实施例提供的制备方法制得的多晶硅铸锭用坩埚与常规喷涂法制备多晶硅铸锭用坩埚的分别通过了电镜图进行对比,对比相同倍数下的涂层形貌,确定涂层致密性,以及通过硬度测试仪器,进行硬度测试。如图4所示,图4中(a)的常规喷涂法制备的多晶硅铸锭用坩埚的涂层整体颗粒更为粗大且间隙较大;图4中(b)为本发明所述多晶硅铸锭用坩埚的硬质涂层的颗粒更为细小,且颗粒间的间隙更小,颗粒堆积更为致密。相比于常规喷涂法制备的多晶硅铸锭用坩埚,本发明所述多晶硅铸锭用坩埚表面更加光滑、致密。表2为两种多晶硅铸锭用坩埚的涂层的硬度测试数据表,根据涂层材料的性质及硬度估计情况,硬度值采用采用邵氏硬度仪器测量获得(单位hd):表2:粗糙度对比测试数据表对象取点1取点2取点3取点4取点5平均值(单位:hd)喷涂法对比组145.841.543.147.442.544.1喷涂法对比组240.342.346.245.243.943.6本发明实验组183.684.586.284.283.484.4本发明实验组287.586.785.487.986.186.7从表2所述的数据对比可知,本发明所述多晶硅铸锭用坩埚的硬质涂层的硬度为常规喷涂法制备的多晶硅铸锭用坩埚的涂层硬度的两倍,硬度改善明显。(3)浆料颗粒粒度对比测试参见表3,表3为常规喷涂法和本发明所述制备方法中的浆料颗粒的粒度对比数据表,制备开始,两种方法采用相同尺寸的氮化硅粉体,分别经两种制备方法后,本发明所述制备方法中经球磨处理后的硬质涂层浆料中,检测出的硬质涂层浆料颗粒的粒度的粒径整体上相比于常规喷涂工艺都大大减少,并且本发明所述制备方法中经球磨处理后的硬质涂层浆料颗粒的比表面积(s.s.a,specificsurfacearea)是增加的。因此,相比常规的喷涂法涂层,在铸锭过程中,本发明制备的多晶硅铸锭用坩埚采用的硬质涂层浆料颗粒之间的间隙更小,颗粒之间的结合更加紧密,所述坩埚的硬质涂层更容易烧结致密化,。表3:浆料颗粒的粒度对比数据表类型d10/μmd50/μmd90/μms.s.a/m2/g喷涂法对比组10.7611.7414.7674.078本发明实验组10.7011.3502.7984.943喷涂法对比组20.8362.0914.7273.642本发明实验组20.7931.6613.6544.157以上所述实施例仅表达了本发明的几种实施方式,其描述较为具体和详细,但并不能因此而理解为对本发明专利范围的限制。应当指出的是,对于本领域的普通技术人员来说,在不脱离本发明构思的前提下,还可以做出若干变形和改进,这些都属于本发明的保护范围。因此,本发明专利的保护范围应以所附权利要求为准。当前第1页12