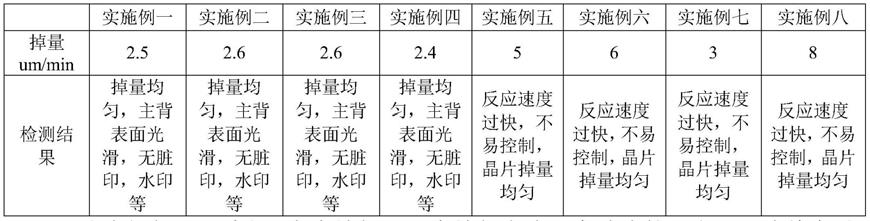
[0001]
本发明涉及半导体材料技术领域,尤其涉及一种晶片腐蚀液及腐蚀方法。
背景技术:[0002]
磷化铟作为重要的化合物半导体材料,在光子领域(波长为1000nm以上的发射和探测能力)和射频领域(高频rf应用中的高速和低噪声性能)中占有重要的地位。对于磷化铟而言,具有电子迁移率高、耐辐射性能好、禁带宽度大、热导率高、击穿电场高等优点。对于军事通信、雷达和辐射测量等性能驱动型利基市场以及自动测试设备的首选,在微波、毫米波电路及高速数字集成电路的制备中是首选的衬底材料。并且在5g通信时代,对比其他半导体材料而言,磷化铟材料的性能更好,尽管现如今磷化铟材料的技术受到其他半导体材料技术的挑战,但是凭借其优越的性能,依旧是未来半导体材料的主流材料,并且对于产品性能的提高和更高的追求,未来对于磷化铟技术的开发与提升,拥有更广阔的发展前景。
[0003]
磷化铟晶片是由磷化铟晶棒进行加工而成,在加工的过程中,会在晶片的表面产生锯纹,晶片内部产生内应力,并且晶片切割后,其厚度较产品具有很大的差距。在切片后,抛光之前需要进行研磨处理,修复晶片表面的锯纹、划痕等缺陷,并且研磨晶片的厚度,达到抛光前的厚度标准。然后进行晶片的腐蚀,去除晶片表面的应力层及损伤层。
[0004]
因此在磷化铟晶片进行腐蚀时,需要对磷化铟晶片的腐蚀液以及腐蚀方法进行研究与探讨,经过大量的数据实验,得到更加优异的腐蚀液配比,以及操作方法。
[0005]
现有的磷化铟晶片,在研磨过后,大多仅使用去离子水进行清洗后,即使用腐蚀液进行一次腐蚀,首先,使用使用传统的腐蚀液对晶片进行腐蚀清洗,表面清洗速度较慢,且发现表面进行完腐蚀后,用去离子水清洗后,然后烘干发现,少许晶片的表面有些许的腐蚀药印、水印等污渍,导致晶片腐蚀不合格。
技术实现要素:[0006]
针对上述问题,本发明的目的在于公开一种晶片腐蚀液及腐蚀方法,能够改善晶片腐蚀速度慢以及晶片腐蚀后不易清洗的问题,能够在一定程度上有效增加腐蚀液腐蚀后的成功率。
[0007]
具体的,本发明的一种晶片腐蚀液,所述腐蚀液包括以下体积百分比的组分:双氧水70%~77%、浓硫酸3.8%~5%、冰醋酸7.7%~10%、浓盐酸9.5%~11.5%。
[0008]
进一步,所述腐蚀液包括以下体积百分比的组分:双氧水77%,浓硫酸3.8%,冰醋酸7.7%,浓盐酸11.5%。
[0009]
此外,本发明还公开了一种晶片腐蚀液的制备方法,所述腐蚀方法是将研磨后的晶片经浸泡清洗后,再经过四次腐蚀,最后脱水、干燥进入下一工序。
[0010]
进一步,所述腐蚀方法具体包括以下步骤:
[0011]
浸泡清洗:将研磨完成后的晶片连同卡塞浸泡于水中;
[0012]
一次腐蚀:配制好质量分数为10%的稀硝酸溶液,将晶片从水中捞出,至于稀硝酸
溶液中,进行一次腐蚀,腐蚀完成后用去离子水清洗、浸泡;
[0013]
二次腐蚀:分别量取双氧水和稀硫酸搅拌混合均匀得到混合溶液一,将一次腐蚀完成的晶片加入混合溶液一中进行二次腐蚀,腐蚀完成后用去离子水清洗、浸泡;
[0014]
三次腐蚀:按照权利要求1或2的比例配制腐蚀液,将经过二次腐蚀的晶片加入腐蚀液中,腐蚀完成后用去离子水清洗、浸泡;
[0015]
四次腐蚀:分别量取柠檬酸、双氧水加入去离子水中,搅拌混合均匀得到混合溶液二,将经过三次腐蚀的晶片至于混合溶液二中,腐蚀完成后用去离子水清洗、浸泡;
[0016]
脱水、烘干:将四次腐蚀完成的晶片浸泡于酒精中脱水,脱水完成后捞出、烘干,进入下一工序。
[0017]
和传统的腐蚀工艺相比,进行了四次腐蚀,按照本发明进行改进,可以大幅度提高晶片的生产效率,降低药印,脏印的出现。晶片的清洗效果更加明显
[0018]
进一步,所述一次腐蚀的腐蚀时间为10-20s,腐蚀温度为25-35℃。
[0019]
进一步,所述混合溶液一中,双氧水和稀硫酸的质量比为20~25:1。
[0020]
进一步,所述二次腐蚀的腐蚀时间为20-30s,腐蚀温度为25-30℃。
[0021]
进一步,所述三次腐蚀的腐蚀时间为3-5min,腐蚀温度为25-30℃。
[0022]
进一步,所述混合溶液二中柠檬酸、双氧水和去离子水的体积比为1~1.5:1~2:3~5。
[0023]
进一步,所述四次腐蚀的腐蚀时间为2-3min,腐蚀温度为25-30℃。
[0024]
本发明的有益效果:
[0025]
1.本发明公开了一种晶片腐蚀液,对配方的优化,可以加快晶片的掉量,避免掉量缓慢且掉量不均匀的情况出现,由此可以大幅度提高晶片的生产效率,降低药印,脏印的出现,使得晶片的清洗效果更加明显。
[0026]
2.本发明的一种晶片腐蚀方法,通过一次腐蚀和二次腐蚀步骤,可以在进行掉量腐蚀三次腐蚀之前清洗掉表面的残余杂质,将表面的研磨液腐蚀掉,并且通过硝酸的强氧化,强腐蚀效果可以有效的清理掉腐蚀液中无法清洗的物质,三次腐蚀相结合,使得晶片表面的腐蚀效果更好,再通过四次腐蚀步骤,主要进行晶片表面的清洗作用,在三次腐蚀步骤中进行掉量后腐蚀后,晶片上还残留有部分研磨液的杂质与磷化铟自身的杂质,而混合溶液二中含有的柠檬酸,可以沉淀金属物质,使得杂质分散和悬浮,再用去离子水即能快速清洗干净晶片表面的杂质,最后结合酒精脱水烘干,从而有效的降低了晶片表面杂质的出现的可能性。
具体实施方式
[0027]
以下将结合具体实施例对本发明进行详细说明:
[0028]
本发明的一种晶片腐蚀液,包括以下体积百分比的组分:双氧水70%~77%、浓硫酸3.8%~5%、冰醋酸7.7%~10%、浓盐酸9.5%~11.5%,利用本发明的腐蚀液进行晶片腐蚀,其中实施例一至实施例五的腐蚀液的配方组成如表1所示:
[0029]
表1
[0030] 双氧水(%)浓硫酸(%)冰醋酸(%)浓盐酸(%)实施例一773.87.711.5
实施例二73.551011.5实施例三7541011实施例四765910实施例五80-812实施例六83.44-12.6实施例七874.28.8-实施例八703.87.718.5
[0031]
使用表1中的配方的腐蚀液,均采用以下方法对晶片进行腐蚀:
[0032]
浸泡清洗:将研磨完成后的晶片连同卡塞浸泡于水中;
[0033]
一次腐蚀:配制好质量分数为10%的稀硝酸溶液,将晶片从水中捞出,置于稀硝酸溶液中,于25-35℃温度下,进行第一次腐蚀10-20s,优选的在30℃温度下,进行一次腐蚀15s,腐蚀过程中上下抖动,以均匀腐蚀晶片表面,腐蚀完成后用去离子水清洗、浸泡;
[0034]
二次腐蚀:按照20:1的质量比分别量取双氧水和稀硫酸,搅拌混合均匀得到混合溶液一,将一次腐蚀完成的晶片加入混合溶液一中,于25-30℃温度下,进行第二次腐蚀20-30s,优选的在25℃温度下,进行一次腐蚀25s,腐蚀过程中转动晶片,使得晶片腐蚀均匀,腐蚀完成后用去离子水清洗、浸泡;
[0035]
三次腐蚀:按照表1中的比例分别量取双氧水、浓硫酸、冰醋酸和浓盐酸,搅拌混合均匀配制得到腐蚀液,将经过二次腐蚀的晶片加入腐蚀液中,于25-30℃温度下,优选为30℃温度下,进行第三次腐蚀,采用间歇腐蚀的方式,先将晶片置于腐蚀液中转动晶片腐蚀1min,然后取出晶片用去离子进行清洗,清洗干净后,再将晶片置于腐蚀液中转动晶片腐蚀1min,重复腐蚀和取出清洗的过程,依次循环3-5次,腐蚀晶片的总时间为3-5min,优选为5min,腐蚀完成后将晶片用去离子水清洗、浸泡;
[0036]
四次腐蚀:按照1:1:3的体积比分别量取柠檬酸、双氧水和去离子水中,搅拌混合均匀得到混合溶液二,将经过三次腐蚀的晶片置于混合溶液二中,于25-30℃温度下,优选的为25℃温度下,进行第四次腐蚀,先抖动晶片,使得晶片表面均被腐蚀过后,将晶片放在腐蚀液中浸泡2-3min,优选的为3min,腐蚀完成后用去离子水清洗、浸泡;
[0037]
脱水、烘干:将四次腐蚀完成的晶片浸泡于酒精中脱水30s,脱水完成后捞出、烘干,进入下一工序。
[0038]
对腐蚀完成后的晶片的掉量和表面进行观察检测,检测结果如表2所示:
[0039]
表2
[0040][0041]
通过上表可以看出,在实施例一至实施例六中,腐蚀液的配方,影响整个晶片的腐蚀过程,在腐蚀过程中,当缺少浓硫酸、冰醋酸、浓盐酸中的任何一种酸,都会降低晶片的腐蚀速率,并且影响晶片表面的腐蚀清洗情况,并且在腐蚀药液的配制过程中,其中盐酸与硫
酸的成分增加,都会影响腐蚀液的反应温度,不易控制药液的温度,导致晶片的腐蚀速率大幅度提高,晶片表面的掉量不均匀,晶片清洗不干净。
[0042]
对比例一
[0043]
本对比例在对晶片进行腐蚀过程中,和本申请的方法相比,其不同之处在于,不进行一次腐蚀步骤,具体为:
[0044]
浸泡清洗:将研磨完成后的晶片连同卡塞浸泡于水中;
[0045]
一次腐蚀:按照20:1的质量比分别量取双氧水和稀硫酸,搅拌混合均匀得到混合溶液一,将一次腐蚀完成的晶片加入混合溶液一中,于25-30℃温度下,进行第一次腐蚀20s,腐蚀过程中转动晶片,使得晶片腐蚀均匀,腐蚀完成后用去离子水清洗、浸泡;
[0046]
二次腐蚀:按照表1中的实施例一的比例分别量取双氧水、浓硫酸、冰醋酸和浓盐酸,搅拌混合均匀配制得到腐蚀液,将经过一次腐蚀的晶片加入腐蚀液中,于25-30℃温度下,进行第二次腐蚀,采用间歇腐蚀的方式,先将晶片置于腐蚀液中转动晶片腐蚀1min,然后取出晶片用去离子进行清洗,清洗干净后,再将晶片置于腐蚀液中转动晶片腐蚀1min,重复腐蚀和取出清洗的过程,依次循环5次,腐蚀晶片的总时间为5min,腐蚀完成后将晶片用去离子水清洗、浸泡;
[0047]
三次腐蚀:按照1:1:3的体积比分别量取柠檬酸、双氧水和去离子水中,搅拌混合均匀得到混合溶液二,将经过二次腐蚀的晶片置于混合溶液二中,于25-30℃温度下,进行第三次腐蚀,先抖动晶片,使得晶片表面均被腐蚀过后,将晶片放在腐蚀液中浸泡3min,腐蚀完成后用去离子水清洗、浸泡;
[0048]
脱水、烘干:将三次腐蚀完成的晶片浸泡于酒精中脱水30s,脱水完成后捞出、烘干,进入下一工序。
[0049]
对比例二
[0050]
本对比例在对晶片进行腐蚀过程中,和本申请的方法相比,其不同之处在于,不进行二次腐蚀步骤,具体为:
[0051]
浸泡清洗:将研磨完成后的晶片连同卡塞浸泡于水中;
[0052]
一次腐蚀:配制好质量分数为10%的稀硝酸溶液,将晶片从水中捞出,置于稀硝酸溶液中,于25-35℃温度下,进行第一次腐蚀20s,腐蚀过程中上下抖动,以均匀腐蚀晶片表面,腐蚀完成后用去离子水清洗、浸泡;
[0053]
二次腐蚀:按照表1中的实施例一的比例分别量取双氧水、浓硫酸、冰醋酸和浓盐酸,搅拌混合均匀配制得到腐蚀液,将经过一次腐蚀的晶片加入腐蚀液中,于25-30℃温度下,进行第二次腐蚀,采用间歇腐蚀的方式,先将晶片置于腐蚀液中转动晶片腐蚀1min,然后取出晶片用去离子进行清洗,清洗干净后,再将晶片置于腐蚀液中转动晶片腐蚀1min,重复腐蚀和取出清洗的过程,依次循环5次,腐蚀晶片的总时间为5min,腐蚀完成后将晶片用去离子水清洗、浸泡;
[0054]
三次腐蚀:按照1:1:3的体积比分别量取柠檬酸、双氧水和去离子水中,搅拌混合均匀得到混合溶液二,将经过二次腐蚀的晶片置于混合溶液二中,于25-30℃温度下,进行第三次腐蚀,先抖动晶片,使得晶片表面均被腐蚀过后,将晶片放在腐蚀液中浸泡3min,腐蚀完成后用去离子水清洗、浸泡;
[0055]
脱水、烘干:将三次腐蚀完成的晶片浸泡于酒精中脱水30s,脱水完成后捞出、烘
干,进入下一工序。
[0056]
对比例三
[0057]
本对比例在对晶片进行腐蚀过程中,和本申请的方法相比,其不同之处在于,不进行二次腐蚀步骤,具体为:
[0058]
浸泡清洗:将研磨完成后的晶片连同卡塞浸泡于水中;
[0059]
一次腐蚀:配制好质量分数为10%的稀硝酸溶液,将晶片从水中捞出,置于稀硝酸溶液中,于25-35℃温度下,进行第一次腐蚀20s,腐蚀过程中上下抖动,以均匀腐蚀晶片表面,腐蚀完成后用去离子水清洗、浸泡;
[0060]
二次腐蚀:按照20:1的质量比分别量取双氧水和稀硫酸,搅拌混合均匀得到混合溶液一,将一次腐蚀完成的晶片加入混合溶液一中,于25-30℃温度下,进行第二次腐蚀20s,腐蚀过程中转动晶片,使得晶片腐蚀均匀,腐蚀完成后用去离子水清洗、浸泡;
[0061]
三次腐蚀:按照表1中的实施例一的比例分别量取双氧水、浓硫酸、冰醋酸和浓盐酸,搅拌混合均匀配制得到腐蚀液,将经过二次腐蚀的晶片加入腐蚀液中,于25-30℃温度下,进行第三次腐蚀,采用间歇腐蚀的方式,先将晶片置于腐蚀液中转动晶片腐蚀1min,然后取出晶片用去离子进行清洗,清洗干净后,再将晶片置于腐蚀液中转动晶片腐蚀1min,重复腐蚀和取出清洗的过程,依次循环5次,腐蚀晶片的总时间为5min,腐蚀完成后将晶片用去离子水清洗、浸泡;
[0062]
脱水、烘干:将三次腐蚀完成的晶片浸泡于酒精中脱水30s,脱水完成后捞出、烘干,进入下一工序。
[0063]
对腐蚀完成后的晶片的掉量和表面进行观察检测,检测结果如表3所示:
[0064]
表3
[0065][0066]
由表3可知,本发明的腐蚀方法作为一个整体的方法,当缺少其中任何一个腐蚀步骤,都可能增加晶片腐蚀的不合格率,在四次腐蚀的步骤的共同作用下,使得晶片表面腐蚀更均匀,洁净光滑,符合客户的要求需求。
[0067]
以上实施例仅用以说明本发明的技术方案而非限制,尽管参照较佳实施例对本发明进行了详细说明,本领域的普通技术人员应当理解,可以对本发明的技术方案进行修改或者等同替换,而不脱离本发明技术方案的宗旨和范围,其均应涵盖在本发明的权利要求范围当中。本发明未详细描述的技术、形状、构造部分均为公知技术。