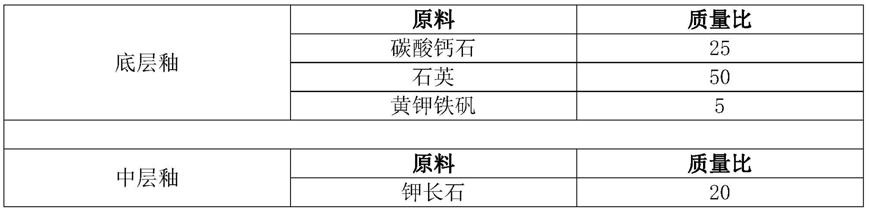
[0001]
本发明涉及陶器釉料技术领域,尤其涉及一种生态青釉料及其烧制方法。
背景技术:[0002]
在陶器的生产过程中,通常会在陶器的表面涂覆釉料,以起到美观、防水、提升触感等作用。而在各式釉料中,青釉是我国使用最早,延用时间最久,分布最广的一个釉种。青色也符合我国人民的传统审美情趣,青色与碧玉相若,被人认为是稳重而高雅的象征。但是现有的青釉料产品,普遍存在烧制情况不稳定,存在釉色暗沉、偏差明显的问题。
技术实现要素:[0003]
针对现有技术中所存在的不足,本发明提供了一种生态青釉料及其烧制方法,其解决了现有技术中存在的现有的青釉料产品,存在烧制情况不稳定,存在釉色暗沉、偏差明显的问题。
[0004]
本发明的上述技术目的是通过以下技术方案得以实现的:
[0005]
一种生态青釉料,包括底层釉、中层釉和面层釉;所述底层釉包括以下物质:碳酸钙石、石英和黄钾铁矾;所述中层釉包括以下物质:钾长石、石英、高岭土、青金石、蓝铜矿、硼砂、硫酸锰和硫酸铬;所述面层釉包括以下物质:碳酸钙石、朱泥、石英和黄泥。
[0006]
进一步的,所述底层釉中物质的质量比为:碳酸钙石20-30、石英45-55、黄钾铁矾3-8;所述中层釉中物质的质量比为:钾长石15-25、石英25-35、高岭土5-15、青金石1-3、蓝铜矿2-6、硼砂3-7、硫酸锰0.2-0.7、硫酸铬0.2-0.8;所述面层釉中物质的质量比为:碳酸钙石45-55、朱泥5-10、石英15-25、黄泥5-15。
[0007]
进一步的,所述底层釉包括以下质量比的物质:碳酸钙石25、石英50、黄钾铁矾5;所述中层釉包括以下质量比的物质:钾长石20、石英30、高岭土10、青金石2、蓝铜矿6、硼砂5、硫酸锰0.5、硫酸铬0.8;所述面层釉包括以下质量比的物质:碳酸钙石50、朱泥10、石英20、黄泥10。
[0008]
进一步的,所述黄泥包括熟性黄泥和生性黄泥,其中熟性黄泥与生性黄泥的质量比为4:6。
[0009]
本发明还提供了一种生态青釉料的烧制方法,所述烧制方法包括如下步骤:
[0010]
s1,制备底层釉:按照质量比称取碳酸钙石、石英和黄钾铁矾,将上述原料加入球磨机进行干式球磨,球磨完成后加水勾兑成50-65%质量浓度,待用;
[0011]
s2,制备中层釉:按照质量比称取钾长石、石英、高岭土、青金石、蓝铜矿、硼砂、硫酸锰和硫酸铬,将上述原料加入球磨机进行干式球磨,球磨完成后加水勾兑成50%质量浓度,待用;
[0012]
s3,制备面层釉:按照质量比称取碳酸钙石、朱泥、石英、熟性黄泥和生性黄泥,将上述原料加入球磨机进行干式球磨,球磨完成后加水勾兑成25-35%质量浓度,待用;
[0013]
s4,取胚体,进行干燥除水处理,取出后使用浸釉工艺将底层釉浸涂在胚体上,上
釉量200-250g/
㎡
,常温下等待底层釉的釉面表干;
[0014]
s5,底层釉的釉面表干后,将中层釉均匀刷涂在底层釉的表面,上釉量150-200g/
㎡
,常温下等待中层釉的釉面表干;
[0015]
s6,中层釉的釉面表干后,将面层釉均匀淋涂在中层釉的表面,上釉量50-100g/
㎡
,常温下等待面层釉的釉面表干;
[0016]
s7,将胚体置于1200-1350℃下釉烧,制得生态青釉。
[0017]
本发明的有益效果如下:
[0018]
1、本发明将釉料分为底层釉、中层釉和面层釉。底层釉烧制完成后由于黄钾铁矾的存在使得底层釉呈现偏褐色。而中层釉中的蓝铜矿在高温下会分解出cu,cu将底层釉中的fe
3+
还原成fe
2+
,使得底层釉与中层釉的交界处呈现出青色。而由于青金石的存在使得中层釉烧制完成后呈现偏蓝色,通过褐色底层釉与蓝色中层釉对光线折射和反射的结合,使得底层釉与中层釉呈现出青色的光泽,且光泽通透富有美感。面层釉中的红泥与熟性黄泥中含有fe
3+
,中层釉中的cu将底层釉中的fe
3+
还原成fe
2+
,使得面层釉与中层釉的交界处呈现出青色光泽。以上效果使得本发明的釉色向青色的指向性更为明显,且光泽更加通透。
[0019]
2、由于面层釉的上釉量少,因此高温下面层釉会与中层釉的表层融合。在中层釉中添加了硫酸铬,在高温烧结的过程中,能够促进釉体发育,使得釉面紧密连接从而提高釉面硬度与热稳定性。添加了硼砂,使得釉面更为通透纯净,有利于光线的折射与反射。
具体实施方式
[0020]
下面结合实施例和对比例对本发明中的技术方案进一步说明。
[0021]
实施例1:
[0022][0023][0024]
实施例2:
[0025][0026]
实施例3:
[0027][0028]
实施例4:
[0029][0030][0031]
实施例5:
[0032][0033]
实施例6:
[0034][0035][0036]
实施例7:
[0037][0038]
实施例1-7的生态青釉料按照如下步骤进行烧制:
[0039]
s1,制备底层釉:按照质量比称取碳酸钙石、石英和黄钾铁矾,将上述原料加入球磨机进行干式球磨,球磨时间为8小时,球磨完成后加水勾兑成50-65%质量浓度,待用;
[0040]
s2,制备中层釉:按照质量比称取钾长石、石英、高岭土、青金石、蓝铜矿、硼砂、硫
酸锰和硫酸铬,将上述原料加入球磨机进行干式球磨,球磨时间为20小时,球磨完成后加水勾兑成50%质量浓度,待用;
[0041]
s3,制备面层釉:按照质量比称取碳酸钙石、朱泥、石英、熟性黄泥和生性黄泥,将上述原料加入球磨机进行干式球磨,球磨时间为20小时,球磨完成后加水勾兑成25-35%质量浓度,待用;
[0042]
s4,取胚体,在80℃下干燥除水30min,取出后使用浸釉工艺将底层釉浸涂在胚体上,上釉量200-250g/
㎡
,常温下等待底层釉的釉面表干;
[0043]
s5,底层釉的釉面表干后,将中层釉均匀刷涂在底层釉的表面,上釉量150-200g/
㎡
,常温下等待中层釉的釉面表干;
[0044]
s6,中层釉的釉面表干后,将面层釉均匀淋涂在中层釉的表面,上釉量50-100g/
㎡
,常温下等待面层釉的釉面表干;
[0045]
s7,将胚体置于1200-1350℃下釉烧7h,制得生态青釉。
[0046]
对比例1:
[0047][0048]
对比例1的生态青釉料按照如下步骤进行烧制:
[0049]
s1,制备底层釉:按照质量比称取碳酸钙石、石英和黄钾铁矾,将上述原料加入球磨机进行干式球磨,球磨时间为8小时,球磨完成后加水勾兑成50-65%质量浓度,待用;
[0050]
s2,制备中层釉:按照质量比称取钾长石、石英、高岭土、青金石、硼砂、硫酸锰和硫酸铬,将上述原料加入球磨机进行干式球磨,球磨时间为20小时,球磨完成后加水勾兑成50%质量浓度,待用;
[0051]
s3,制备面层釉:按照质量比称取碳酸钙石、朱泥、石英、熟性黄泥和生性黄泥,将上述原料加入球磨机进行干式球磨,球磨时间为20小时,球磨完成后加水勾兑成25-35%质量浓度,待用;
[0052]
s4,取胚体,在80℃下干燥除水30min,取出后使用浸釉工艺将底层釉浸涂在胚体
上,上釉量200-250g/
㎡
,常温下等待底层釉的釉面表干;
[0053]
s5,底层釉的釉面表干后,将中层釉均匀刷涂在底层釉的表面,上釉量150-200g/
㎡
,常温下等待中层釉的釉面表干;
[0054]
s6,中层釉的釉面表干后,将面层釉均匀淋涂在中层釉的表面,上釉量50-100g/
㎡
,常温下等待面层釉的釉面表干;
[0055]
s7,将胚体置于1200-1350℃下釉烧7h,制得生态青釉。
[0056]
对比例2:
[0057][0058][0059]
对比例2的生态青釉料按照如下步骤进行烧制:
[0060]
s1,制备底层釉:按照质量比称取碳酸钙石、石英和黄钾铁矾,将上述原料加入球磨机进行干式球磨,球磨时间为8小时,球磨完成后加水勾兑成50-65%质量浓度,待用;
[0061]
s2,制备中层釉:按照质量比称取钾长石、石英、高岭土、青金石、蓝铜矿、硼砂和硫酸锰,将上述原料加入球磨机进行干式球磨,球磨时间为20小时,球磨完成后加水勾兑成50%质量浓度,待用;
[0062]
s3,制备面层釉:按照质量比称取碳酸钙石、朱泥、石英、熟性黄泥和生性黄泥,将上述原料加入球磨机进行干式球磨,球磨时间为20小时,球磨完成后加水勾兑成25-35%质量浓度,待用;
[0063]
s4,取胚体,在80℃下干燥除水30min,取出后使用浸釉工艺将底层釉浸涂在胚体上,上釉量200-250g/
㎡
,常温下等待底层釉的釉面表干;
[0064]
s5,底层釉的釉面表干后,将中层釉均匀刷涂在底层釉的表面,上釉量150-200g/
㎡
,常温下等待中层釉的釉面表干;
[0065]
s6,中层釉的釉面表干后,将面层釉均匀淋涂在中层釉的表面,上釉量50-100g/
㎡
,常温下等待面层釉的釉面表干;
[0066]
s7,将胚体置于1200-1350℃下釉烧7h,制得生态青釉。
[0067]
对比例3:
[0068][0069][0070]
对比例3的生态青釉料按照如下步骤进行烧制:
[0071]
s1,制备底层釉:按照质量比称取碳酸钙石、石英和黄钾铁矾,将上述原料加入球磨机进行干式球磨,球磨时间为8小时,球磨完成后加水勾兑成50-65%质量浓度,待用;
[0072]
s2,制备中层釉:按照质量比称取钾长石、石英、高岭土、青金石、蓝铜矿、硫酸铬和硫酸锰,将上述原料加入球磨机进行干式球磨,球磨时间为20小时,球磨完成后加水勾兑成50%质量浓度,待用;
[0073]
s3,制备面层釉:按照质量比称取碳酸钙石、朱泥、石英、熟性黄泥和生性黄泥,将上述原料加入球磨机进行干式球磨,球磨时间为20小时,球磨完成后加水勾兑成25-35%质量浓度,待用;
[0074]
s4,取胚体,在80℃下干燥除水30min,取出后使用浸釉工艺将底层釉浸涂在胚体上,上釉量200-250g/
㎡
,常温下等待底层釉的釉面表干;
[0075]
s5,底层釉的釉面表干后,将中层釉均匀刷涂在底层釉的表面,上釉量150-200g/
㎡
,常温下等待中层釉的釉面表干;
[0076]
s6,中层釉的釉面表干后,将面层釉均匀淋涂在中层釉的表面,上釉量50-100g/
㎡
,常温下等待面层釉的釉面表干;
[0077]
s7,将胚体置于1200-1350℃下釉烧7h,制得生态青釉。
[0078]
对比例4:
[0079][0080]
对比例4的生态青釉料按照如下步骤进行烧制:
[0081]
s1,制备面层釉:按照质量比称取碳酸钙石、朱泥、石英、熟性黄泥和生性黄泥,将上述原料加入球磨机进行干式球磨,球磨时间为20小时,球磨完成后加水勾兑成25-35%质量浓度,待用;
[0082]
s2,取胚体,在80℃下干燥除水30min,取出后使用浸釉工艺将第一道面层釉浸涂在胚体上,上釉量200-250g/
㎡
,常温下等待第一道面层釉的釉面表干;
[0083]
s3,第一道面层釉的釉面表干后,将第二道面层釉均匀刷涂在第一道面层釉的表面,上釉量150-200g/
㎡
,常温下等待第二道面层釉的釉面表干;
[0084]
s4,第二道面层釉的釉面表干后,将第三道面层釉均匀淋涂在第二道面层釉的表面,上釉量50-100g/
㎡
,常温下等待第三道面层釉的釉面表干;
[0085]
s7,将胚体置于1200-1350℃下釉烧7h,制得生态青釉。
[0086]
实验测试
[0087]
测试一:表面状态对比实验
[0088]
对实施例1-7及对比例1-4进行烧制,烧制完成后通过肉眼观察釉面状态包括光泽度、通透性和釉色情况,结果如下表1:
[0089]
表1.釉面状态观察表
[0090][0091]
表1中,实施例2、实施例6、实施例7、实施例1和对比例1中的蓝铜矿添加量越来越低,使得烧制出的釉面的光泽度也越来越差,通透性也越来越差,由此可得,蓝铜矿的添加能够使得釉面通透、有光泽且富有青色的美感。由实施例2和对比例3之间对比可得,硼砂的添加也对釉面的通透性与光泽度起到促进作用。综上,蓝铜矿与硼砂能同时对釉面的通透性与光泽度起到促进作用。且由对比例4可得,通过使用底层釉、中层釉与面层釉的结合式烧制方法,能够提高釉面光泽度和通透性。
[0092]
测试二:热稳定性对比实验
[0093]
1.实验仪器:
[0094]
(1)电加热烘箱;(2)循环恒温水浴锅。
[0095]
2.样品:
[0096]
按照实施例2、实施例3、实施例4、实施例5和对比例2方法制得生态青釉样品。
[0097]
3.试验方法:
[0098]
(1)将生态青釉样品清洗干净,检查样品是否完好。
[0099]
(2)将循环恒温水浴锅的温度调整为20℃,待用。
[0100]
(3)调节电加热烘箱至温度180℃,将生态青釉样品放入电加热烘箱中,加热维持40min。
[0101]
(4)从电加热烘箱中取出生态青釉样品,迅速放入循环恒温水浴锅中冷却20min。
[0102]
(5)将样品从水中取出,擦干,观察裂纹情况。
[0103]
(6)重复多次试验,并观察裂纹情况。
[0104]
试验结果如下表2:
[0105]
表2.热稳定性裂纹情况观察表
[0106][0107]
通过表2的裂纹情况可得,在中层釉中添加硫酸铬,在高温烧结的过程中,能够促进釉体发育,使得釉面紧密连接从而提高釉面强度与热稳定性。
[0108]
最后说明的是,以上实施例仅用以说明本发明的技术方案而非限制,尽管参照较佳实施例对本发明进行了详细说明,本领域的普通技术人员应当理解,可以对本发明的技术方案进行修改或者等同替换,而不脱离本发明技术方案的宗旨和范围,其均应涵盖在本发明的权利要求范围当中。