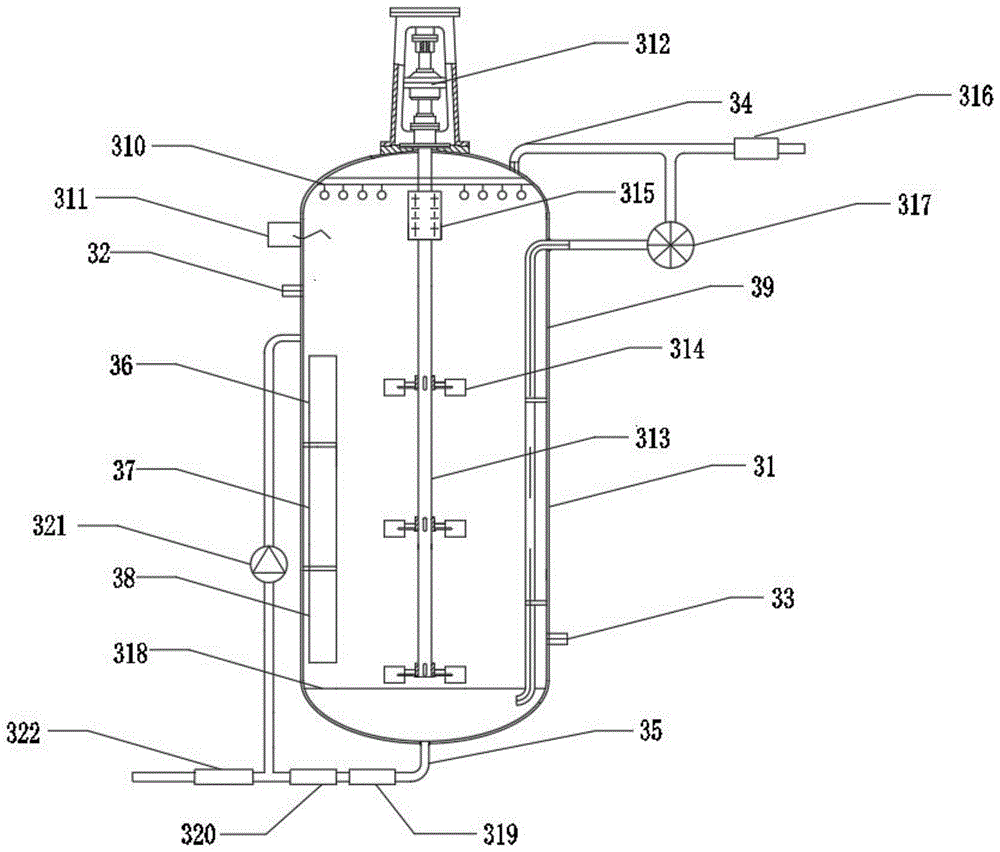
本发明涉及垃圾处理
技术领域:
,更具体的说是涉及一种集成式一体化湿垃圾原位资源化处理系统和处理方法。
背景技术:
:目前全国已安排了46个生活垃圾强制分类试点城市,如北京市、上海市已经实行了生活垃圾分类。生活垃圾分类过程中会产生大量湿垃圾,湿垃圾重量能占到垃圾总重量40-60%以上。湿垃圾为易腐垃圾,是指食材废料、剩菜剩饭、瓜皮果核、中药药渣等易腐的生物质生活废弃物。湿垃圾中除了易腐组分外,还含有一定的纤维素、半纤维素和木质素等生物难降解成分。目前,湿垃圾的处理一般是经环卫收集、运输后送至大型集中式的湿垃圾处理厂进行处理,常用的处理技术包括好氧堆肥和厌氧发酵等技术。但是,对于偏远或分散的城市、城镇小区或农村地区,这些地区距离集中处理厂较远,运输距离长、运输费用高;且湿垃圾在存放、收集、长时间转运及处置过程中,因含水率和有机物含量较高,极易在较短时间内腐烂发臭和滋生蚊蝇,容易导致恶臭、微生物气溶胶及沥出液等二次污染问题,影响城市环境和人们身体健康。因此,在偏远、不易收集和运输生活垃圾的地区,急需在垃圾产生地进行原位或原地资源化处理的技术。湿垃圾处理技术包括好氧堆肥技术、厌氧发酵技术等。相较于厌氧发酵技术,好氧堆肥技术具有发酵周期短、堆体温度高、臭味小、占地面积小、分解彻底等优点,更适合于小规模的湿垃圾就地处理。然而,目前的湿垃圾原位好氧堆肥技术和设备效率不高,发酵周期长,占地面积大,资源化程度低,堆肥产物不能较好的实现就地使用,而且可能存在沥出液和恶臭污染二次等问题,并不能有效解决偏远、不易进行垃圾收集地区的湿垃圾的减量化、无害化和资源化处理。因此,如何提供一种可实现原位或原地资源化处理的技术成为本领域亟待解决的技术问题。技术实现要素:有鉴于此,本发明提供了一种集成式一体化湿垃圾原位资源化处理系统和处理方法,该系统工艺流程简洁,结构简单,集预处理、堆肥、沥出液及恶臭和微生物气溶胶处理为一体,有效提高了湿垃圾处理效率和资源化利用率。为了实现上述目的,本发明采用如下技术方案:一种集成式一体化湿垃圾原位资源化处理系统,包括:进料与卸料单元、预处理单元、快速干式发酵单元、肥料制备单元、沥出液处理和回用单元、含恶臭和微生物气溶胶气体处理单元及自动监测和控制单元;所述预处理单元位于所述进料与卸料单元的底部;所述快速干式发酵单元位于所述预处理单元的一侧;所述肥料制备单元与所述快速干式发酵单元的出料口连接;所述沥出液处理和回用单元与所述快速干式发酵单元的出液口连接;所述含恶臭和微生物气溶胶气体处理单元与所述快速干式发酵单元的排气口连接;所述自动监测和控制单元分别与所述进料与卸料单元、预处理单元、快速干式发酵单元、肥料制备单元、沥出液处理和回用单元和含恶臭和微生物气溶胶气体处理单元连接。本发明以不易实现集中收集和处理的偏远或分散的城市,城镇或农村地区产生的湿垃圾为对象,针对常规湿垃圾堆肥处理技术堆肥效率低和发酵时间长,尤其是对纤维素、半纤维素和木质素等生物难降解成分降解效率低,占地面积大、堆肥产物资源化程度低,不能很好的实现就地利用,以及存在沥出液、恶臭和病原微生物污染等问题,提出了集成式一体化资源化处理系统,该系统工艺流程简洁,结构简单,集预处理、堆肥、沥出液以及恶臭和微生物气溶胶处理为一体;一方面缩短了堆肥时间,有效提高堆肥效率,提高资源化程度,大大减少堆肥设施的体积;另一方面,该系统对沥出液和含恶臭和微生物气溶胶气体进行循环利用和无害化处理,避免了产生的恶臭和沥出液污染对周边环境和人体健康的危害;系统化配置的自动监测和控制单元,通过云平台操作软件实现pc端、手机端和云数据交互及远程控制,信息化程度更高,便于监控和管理。优选的,所述进料与卸料单元包括:进料单元和卸料单元;进一步,所述进料单元设置有暂存单元和沥水槽;所述暂存单元至少设置有两个,所述暂存单元外壁设置有暂存单元入料口,湿垃圾通过暂存单元入料口投入到所述暂存单元中,储存时间为2-3h,沥出液进入所述暂存单元,并通过位于底部的所述沥水槽收集,开启集成所述自动监测和控制单元,将所述暂存单元中的湿垃圾传输至所述卸料单元;所述卸料单元内设置有给料机,湿垃圾通过所述给料机传输至预处理单元,所述卸料单元底部设置有可开关的阀门。优选的,所述预处理单元包括依次连接的分选单元、破碎装置和螺旋压榨脱水机;所述分选单元包括分选装置和磁选机;所述分选装置安装于所述给料机的底部,所述磁选机位于传送带上方;所述破碎装置安装于所述磁选机底部;所述螺旋压榨脱水机安装于所述破碎装置的一侧,且与所述快速干式发酵单元的进料口连接。进一步,所述分选装置为一体式滚筒与重力分选装置;更进一步,所述一体式滚筒与重力分选装置设计的滚筒为中空圆柱筒,所述滚筒的底部设置有移动支撑组件,且所述滚筒呈倾斜安装;进一步,所述移动支撑组件为轮胎或滑轮。所述滚筒顶端设置有进料口,且设置有筛上物出料口和筛下物出料口;所述滚筒侧壁上设置有若干个均匀分布的筛孔,所述筛孔直径为80mm。进一步,所述磁选机至少设置有磁选机1和磁选机2;所述滚筒筛下物出料口下部设置有传送带,所述传送带的上方安装有磁选机1;所述筛上物出料口连接有风选机,所述风选机出料口设置有传送带,所述传送带上安装有磁选机2;所述磁选机1和所述磁选机2内均设置有金属收集柜;进一步,所述破碎装置为剪式和锤式破碎组合式破碎机,且安装在所述磁选机2的底部;更进一步,所述剪式和锤式破碎组合式破碎机包括:剪式破碎单元和锤式破碎单元;其中,所述剪式破碎单元位于所述锤式破碎单元上方,湿垃圾先进入所述剪式破碎单元,破碎后自上而下进入所述锤式破碎单元;且所述锤式破碎单元设置有筛板;其中,所述剪式破碎单元包括切割刀片、轴和电机二;所述轴包括两个主动轴和一个从动轴,且所述主动轴和所述从动轴上均设置有可移动的螺旋型锯齿所述切割刀片,且所述切割刀片交错排列;且所述电机二与所述轴连接;上述技术方案的有益效果:双轴设计交替重叠相互剪切,根据刀片角度排列形成螺旋形粉碎区,更加有效地对固体物料和杂质进行全方位的咬肌撕裂;同时湿垃圾在固定刀片和移动刀片的撕、剪、拉伸作用下,能够实现湿垃圾,特别是纤维、半纤维物料,例如纸张、木材的破碎,粉碎的更加彻底。进一步,所述锤式破碎单元包括:锤部、转盘、主轴和筛板;其中所述锤部设置有平锤头和尖锤头,且所述平锤头和尖锤头交错设置;其中,所述主轴连通转盘支撑在机壳两侧滚动轴承座上,电动机带动转子在破碎腔内高速旋转;所述锤部与所述转盘活动铰接;更进一步,所述锤部的中心与打击中心间距为30-50mm;所述筛板设置在锤式破碎单元的机壳的底部,筛板上设置有均匀分布的筛孔,所述筛孔直径为30mm,所述磁选机2的出料口与所述剪式破碎单元的进料口连接。上述技术方案的有益效果:本发明采用尖锤头和平锤头交互的方式且在高速冲击的作用下破碎湿垃圾,破碎后的垃圾粒径为30mm,粉碎物料中大于筛孔直径的,会继续返回至破碎装置继续破碎,直至符合破碎要求。此外,所述螺旋压榨脱水机的出液口连接污水收集箱;所述螺旋压榨脱水机的出料口下方设置有链板输送机,所述链板输送机与所述快速干式发酵单元的进料口连接。优选的,所述快速干式发酵单元包括:腐熟仓;所述肥料制备单元与所述腐熟仓出料口连接;所述沥出液处理和回用单元与所述腐熟仓出液口连接;所述螺旋压榨脱水机的出料口通过链板输送机与所述腐熟仓进料口连接。其中,所述腐熟仓采用双层不锈钢结构,中间填充有保温层,所述保温层为聚氨酯保温层,厚度为30mm;进一步,所述腐熟仓设置有翻堆搅拌机、进料口、出料口、排气口和出液口;所述翻堆搅拌机设置有搅拌轴,所述搅拌轴从所述腐熟仓顶部,并垂直布置在所述腐熟仓内部;所述搅拌轴上设置有所述搅拌片,且所述翻堆搅拌机与所述电机一连接;所述螺旋压榨脱水机与所述进料口连接;所述排气口连接所述含恶臭和微生物气溶胶气体处理单元;所述出液口连接所述沥出液处理和回用单元。更进一步,所述腐熟仓还设置有:布气板和传感器;其中,所述布气板位于所述腐熟仓内部的底端;所述传感器位于所述腐熟仓的内侧壁;且所述传感器包括但不限于:温度传感器、湿度传感器和氧气浓度传感器。优选的,还包括:第一进液系统、起爆剂储存罐和微生物菌剂储存罐;所述第一进液系统安装在所述腐熟仓顶部;所述第一进液系统与所述微生物菌剂储存罐连接;所述起爆剂储存罐安装在所述腐熟仓的外侧壁。更进一步,所述第一进液系统包括:第一进液管和第一雾化喷头,所述第一雾化喷头设置有若干个,且在所述第一进液管上均匀排列。且,所述第一进液管通过泵与所述微生物菌剂储存罐连接;所述起爆剂储存罐通过泵连通到所述腐熟仓内部;此外,所述第一雾化喷头为实心锥喷嘴,喷嘴喷淋角度为70度。上述技术方案的有益效果:优选的,所述肥料制备单元包括依次连接的滚筒振动筛和生物干化机;其中,所述滚筒振动筛连接所述腐熟仓的出料口,连接处设置有阀门;进一步,所述滚筒振动筛筛孔为20mm,旋转速度为20-25r/min;粒径大于20mm的制肥基料作为所述滚筒振动筛筛上物由出料口进入所述腐熟仓内进行处理,小于20mm的制肥基料作为所述滚筒振动筛筛下物由收集槽收集后输送至所述生物干化机;更进一步,还包括:鼓风机和进料仓,其中所述鼓风机安装在所述生物干化机的一侧;所述进料仓设置在所述生物干化机的顶部;所述生物干化机的内部安装有搅拌装置;此外,所述进料仓可以设计为喇叭口形状;优选的,所述沥出液处理和回用单元包括依次连接的:絮凝池、电化学反应器和氧化池;所述絮凝池与所述腐熟仓出液口连接,且连接处设置有阀门;进一步,所述絮凝池内安装有搅拌机构,所述搅拌机构至少设置有三档转速调节;且所述絮凝池底部设置有排污口,沉淀的腐殖酸从所述排污口输送至烘干箱内进行干燥,干燥完成后收集;此外,所述絮凝池一侧还设置有排水口,上层清液从所述排水口进入所述电化学反应器内。还包括:絮凝池储存罐,所述絮凝池储存罐通过泵连接至所述絮凝池内部;且所述絮凝池储存罐位于所述絮凝池顶部;所述絮凝池储存罐内部有絮凝剂氯化铁。所述电化学反应器设置有出液口,且所述出液口处设置有阀门,阀门连接分流管路,一路连接所述氧化池;所述氧化池内设置有酸碱调节剂、自动加料装置、ph传感器和搅拌装置;且所述氧化池的出水口连接吸附槽,所述吸附槽的一侧设置有沥出液排出口。所述电化学反应器出液口端的分流管路其中一路与所述腐熟仓底部连通,且设置有水泵;其中絮凝池和电化学反应器阶段为沥出液预处理阶段,氧化池为沥出液深度处理阶段,经预处理阶段沥出液一部分由水泵回灌至腐熟仓,剩余沥出液经氧化池深度处理后排放。优选的,还包括:回流管和风机,且所述含恶臭和微生物气溶胶气体处理单元包括:生物喷淋箱、干燥除雾箱和uv光解装置;所述生物喷淋箱和所述回流管一端分别与所述腐熟仓排气口端的分流管路连接;所述风机一端与分流管路连接,另一端与回流管连接,且所述回流管另一端延伸至所述所述布气板的下端;所述生物喷淋箱依次与所述干燥除雾箱和所述uv光解装置连接;进一步,所述生物喷淋箱内设置有第二进液系统和臭气传感器,其中第二进液系统包括第二进液管和第二雾化喷头;所述第二雾化喷头安装在第二进液管上,且所述第二进液管通过泵连接植物液储存罐;所述第二雾化喷头的喷淋角度为70度,可喷洒在空间扩散为直径≤0.04mm的液滴。进一步,所述干燥除雾箱包括:箱体、进风口、吸附段和出风口;其中所述吸附段填置的吸附剂为sdg-ⅰ和sdg-ⅱ的混装,且呈u型填料;此外,更换的吸附剂可作为一般垃圾处理,不会造成二次污染。进一步,所述uv光解装置设置有气体排放口,且所述uv光解装置的内紫外灯、恶臭检测器及镶嵌有纳米tio2泡沫镍网;其中,所述紫外灯可发射波长为185nm和254nm的光;所述纳米tio2泡沫镍网的tio2负载量为40g/m2;所述恶臭检测器设置有若干个。进一步,所述自动监测和控制单元包括:在线监测系统,智能反馈控制系统和人机交互系统;所述在线监测系统用于采集所述进料与卸料单元、预处理单元、快速干式发酵单元、肥料制备单元、沥出液处理和回用单元和含恶臭和微生物气溶胶气体处理单元中关于温度,氧浓度、温度、湿度、臭气、ph值等信息,所述在线监测系统将收集的信息输送至所述智能反馈控制系统,所述智能反馈控制系统根据收集的数据信息对各个单元进行参数的调整和控制;更进一步,所述人机交互系统设定各个单元的运行参数,并进行实时显示,实时记录,具有记载和查询历史记录的功能;此外,所述人机交互系统可以与移动终端、云数据进行对接,实现远程控制。本发明还提供了一种用于原位处理的湿垃圾资源化处理方法,具体包括:s1:进料与卸料,开启自动监测和控制单元;s2:预处理:s21:分选:分选装置将湿垃圾进行筛分,其中粒径≤80mm的湿垃圾经磁选机分离金属物质后进行填埋处理;粒径>80mm的湿垃圾经磁选机分离金属物质后进入破碎装置;进一步,分离出的金属物质输送至金属收集槽;此外,粒径>80mm的湿垃圾从筛上物出料口落入风选机,将湿垃圾中的塑料、纸张及玻璃物质及砖瓦等无机物料分选出来后再经磁选机分离出金属物质后进入破碎装置;s22:破碎:破碎装置采用剪切破碎和锤式破碎的协同作用对纤维素、半纤维素、木质素进行破碎,且破碎至粒径为15-20mm后输送至螺旋压榨脱水机;s23:脱水:螺旋压榨脱水机对破碎后的物料进行挤压,物料的含水率至45-50%后输送至快速干式发酵单元;进一步,破碎后的物料是经过链板输送机输送至螺旋压榨脱水机中,脱水操作完毕后的物料经链板输送机输送至快速干式发酵单元;s3:干式好氧发酵:堆肥1-2天后添加起爆剂和微生物菌剂1;堆肥5-7天后投加微生物菌剂2;且发酵初期温度<45℃;发酵中期高温阶段温度控制在60-65℃,且持续时间>3天;发酵后期温度降至<45℃;发酵周10-13天;堆体含水率控制在45-55%,由于经沥出液处理和回用单元处理后产生的沥出液会回灌至干式好氧发酵单元,会提高堆体含水率,通过加入秸秆、锯末等物质降低堆体含水率;氧气浓度控制在15-20%;发酵期间通风速率0.5-0.6l/min.kg;进一步,所述干式好氧发酵间歇运行,每天12h,整个过程在12-13天内完成;优选的,步骤s3所述起爆剂为葡萄糖;进一步,所述微生物菌剂1包括:枯草芽孢杆菌、短小芽孢杆菌、埃式放线菌和酿酒酵母菌,配比为2:1:1:1,且每种菌浓度均为(2.0-4.0)*108cfu/ml;所述微生物菌剂2包括:黑曲霉、拟康宁木霉和黄孢原毛平革菌,配比为1:1:1,且每种菌浓度均为(5.0-7.0)*107cfu/ml;其中起爆剂接种量为1-2%,所述微生物菌剂1和微生物菌剂2接种量均为3-5‰;s4:肥料制备:干式好氧发酵处理后的物料输送至肥料制备单元,经筛分后的筛下物进行生物干化处理,含水率<15%,冷却后得有机肥料;此外,经筛分后的筛上物作为辅料回用;进一步,所述筛下物进行生物干化处理之前,先根据其n、p、k等的含量与有机质适量混合,混合后再进行生物干化处理;s5:沥出液处理和回用:干式好氧发酵处理后产生的沥出液输送至絮凝池,调节ph,并投加絮凝剂,搅拌,沉降,经沉淀、分离后,提取腐殖酸用于肥料制备,上清液打入电化学反应器进行脱氮处理,处理后的一部分返回至腐熟仓,剩余部分调节ph值经氧化吸附后回用;优选的,步骤s5所述絮凝剂为氯化铁,且按照沥出液体积的0.03%投加,进一步,絮凝剂投加完毕后分三个阶段搅拌,其中,第一搅拌阶段:搅拌速度200-220r/min,搅拌时间10-13min;第二搅拌阶段:搅拌速度100-120r/min,搅拌时间5-8min;第三搅拌阶段:搅拌速度50-70r/min,搅拌时间5-8min;且,投加絮凝剂之前所述ph调节至2-5。优选的,步骤s5所述剩余部分调节ph至6-7,氧化剂为feso4·7h2o和h2o2,且feso4·7h2o和h2o2质量体积比为0.5g:1ml;进一步,所述氧化吸附过程中的吸附剂采用10g/l的活性炭,吸附时间为3h;s6:含恶臭和微生物气溶胶气体处理;进一步,干式好氧发酵处理过程中产生的含恶臭和含菌微生物气溶胶,首先会在快速干式发酵单元内循环利用,且大部分气体以内循环的方式向快速干式发酵单元鼓风曝气,在快速干式发酵单元内多次循环,调节其氧浓度和温度;同时恶臭气体部分在堆肥微生物作用下发生降解;此外,通过快速干式发酵单元内循环供氧还可以充分利用堆肥产生的热蒸汽,提高堆肥处理效率,促进堆肥产品的进一步干化和腐熟;其不能循环利用的含恶臭和微生物气溶胶的气体则进入含恶臭和微生物气溶胶气体处理单元进行处理后排放;更进一步,不能循环利用的含恶臭和微生物气溶胶的气体先经过生物喷淋箱除尘除臭,其中通过喷淋植物液,粉尘被拦截下来;同时,恶臭气体通过润湿、多孔和充满活性微生物的滤层,利用微生物对恶臭物质的吸附、吸收和降解作用,将恶臭气体物质吸附后分解成co2、h2o、h2so4等物质;生物喷淋箱处理完毕后的气体进入干燥除雾箱,废气通过吸附段的吸附及干燥,提高恶臭气体和微生物气溶胶的净化速率,最后经uv光解装置处理,通过uv光可以催化氧气生成臭氧和氧活性基因,在高能紫外光、臭氧和氧活性基因的协同作用下将恶臭和微生物气溶胶气体充分净化达标后排放。由此可知,含恶臭和微生物气溶胶气体处理单元和整个系统融为一体,能够大大减少系统对恶臭和病原微生物的去除,保证系统的生物安全性。综上所述,本发明与现有技术相比至少取得以下技术效果:1)实现了湿垃圾的原位就地处理,即产即清,垃圾不需要贮存和运输,且堆肥产物就地使用,大大节省了传统垃圾收集、转运的费用;2)采用集成式一体化湿垃圾原位资源化处理系统进行湿垃圾的处理,同步得到高品质的有机肥,并进行沥出液和恶臭气体的处理,提高了整体垃圾的处理效率和处理质量;且在湿垃圾堆肥过程中,分阶段接种起爆剂和高效的微生物菌剂,利用两者的协同作用,有益于增加发酵微生物的活性,提高堆体温度,提高对纤维素、半纤维素和木质素等生物难降解成分的降解速率,缩短了堆肥时间;同时加速有机质矿化和腐殖化,进一步促进堆肥腐熟,提高了堆肥品质,保证了堆肥的原位和就地利用;3)实现了对含恶臭物质和微生物气溶胶气体的高效处理,最大程度上减少了二次污染,系统中设置的快速干式发酵单元减少了病原微生物的排放,气体以内循环的方式向发酵单元鼓风曝气,实现在发酵过程中的多次循环,且部分在堆肥物料微生物作用下发生降解;同时,通过内循环供氧还可以充分利用堆肥产生的热量,提高堆肥处理效率,促进堆肥产品的进一步干化和腐熟;通过启动自动监测和控制单元实时检测和调整参数,优化有机组分好氧发酵需氧量与恶臭气体排放量,最大化地利用恶臭气体为湿垃圾供气;且高温阶段高温提升了病原微生物的去除率,不能循环利用的恶臭气体和微生物气溶胶则进入含恶臭和微生物气溶胶气体处理单元进行处理后排放,实现恶臭和微生物气溶胶的高效处理;4)经过本系统设置的沥出液处理和回用单元处理过程中产生的沥出液在回用前进行了预处理,分离出腐殖酸作为制肥料基料,并去除氨氮,防止返回至快速干式发酵单元后氨氮的积累,与传统沥出液直接回灌和回喷自来水堆肥相比,预处理后的沥出液回灌堆肥处理的温度更高,进一步促进堆肥的稳定,同时也加速堆肥腐熟的进程;5)本系统设置了开启自动监测和控制单元,包括多参数在线监测系统、智能反馈控制系统和人机交互系统,具备在线监测、数据导出、无线通讯和智能反馈控制功能;可实现发酵过程参数的监测和反馈控制、含恶臭和气溶胶气体回用以及沥出液回用的监测控制;且在实际应用中,通过集中控制系统和云数据互通,实现远程控制,同样适用于分散式垃圾处理系统,实现较高的好氧堆肥发酵智能化控制水平。附图说明为了更清楚地说明本发明实施例中的技术方案,下面将对实施例中所需要使用的附图作简单地介绍,显而易见地,下面描述中的附图仅仅是本发明的实施例,对于本领域普通技术人员来讲,在不付出创造性劳动的前提下,还可以根据提供的附图获得其他的附图。图1附图为本发明实施例快速干式发酵单元腐熟仓的结构示意图。图2附图为本发明实施例集成式一体化湿垃圾原位资源化处理系统结构流程图。图3附图为本发明实施例破碎装置整体结构图。图4附图为本发明实施例锤式破碎单元结构图。图5附图为本发明实施例剪式破碎单元结构图。其中,附图1-5中的标记:31为腐熟仓、32为进料口、33为出料口、34为排气口、35为出液口、36为温度传感器、37为湿度传感器、38为氧气浓度传感器、39为聚氨酯保温层、310为第一进液系统、311为起爆剂储存罐、312为翻堆搅拌机、313为搅拌轴、314为搅拌片、315为电机一、316为含恶臭和微生物气溶胶气体处理单元、317为风机、318为布气板、319为絮凝池、320为电化学反应器、321为水泵、322为氧化池;40为暂存单元、41为沥水槽、42为给料机、43为一体式滚筒与重力分选装置、44为磁选机1、45为风选机、46为磁选机2、47为破碎装置、48为螺旋压榨脱水机、49为链板输送机、51为生物喷淋箱、52为干燥除雾箱、53为uv光解装置、54为滚筒振动筛、55生物干化机、56污水收集箱;a为剪式破碎单元、b为锤式破碎单元;221为锤部、2211为平锤头、2212为尖锤头、222为转盘、223为主轴、224为筛板;225为切割刀片、226为轴、227为电机二。具体实施方式下面将结合本发明实施例中的附图,对本发明实施例中的技术方案进行清楚、完整地描述,显然,所描述的实施例仅仅是本发明一部分实施例,而不是全部的实施例。基于本发明中的实施例,本领域普通技术人员在没有做出创造性劳动前提下所获得的所有其他实施例,都属于本发明保护的范围。实施例1附图1-5所示,一种集成式一体化湿垃圾原位资源化处理系统,包括:进料与卸料单元、预处理单元、快速干式发酵单元、肥料制备单元、沥出液处理和回用单元、含恶臭和微生物气溶胶气体处理单元316及自动监测和控制单元;预处理单元位于进料与卸料单元的底部;快速干式发酵单元位于预处理单元的一侧;肥料制备单元与快速干式发酵单元的出料口连接;沥出液处理和回用单元与快速干式发酵单元的出液口连接;含恶臭和微生物气溶胶气体处理单元与快速干式发酵单元的排气口连接;自动监测和控制单元分别与进料与卸料单元、预处理单元、快速干式发酵单元、肥料制备单元、沥出液处理和回用单元和含恶臭和微生物气溶胶气体处理单元连接。在另一个实施例中,进料与卸料单元包括:进料单元和卸料单元;在另一个实施例中,进料单元设置有暂存单元40和沥水槽41;暂存单元40至少设置有两个,暂存单元40外壁设置有暂存单元入料口,湿垃圾通过暂存单元入料口投入到暂存单元40中,储存时间为2-3h,沥出液进入暂存单元40,并通过位于底部的沥水槽41收集,开启集成自动控制单元,将暂存单元40中的湿垃圾传输至卸料单元;卸料单元内设置有给料机42,湿垃圾通过给料机42传输至预处理单元,卸料单元底部设置有可开关的阀门。在另一个实施例中,预处理单元包括依次连接的分选单元、破碎装置47和螺旋压榨脱水机48;分选单元包括分选装置和磁选机;分选装置安装于给料机42的底部,磁选机位于传送带上方;破碎装置47安装于磁选机底部;螺旋压榨脱水机48安装于破碎装置47的一侧,且与快速干式发酵单元的进料口连接。为了进一步优化上述技术方案,分选装置为一体式滚筒与重力分选装置43;为了进一步优化上述技术方案,一体式滚筒与重力分选装置43设计的滚筒为中空圆柱筒,滚筒的底部设置有移动支撑组件,且滚筒呈倾斜安装;为了进一步优化上述技术方案,移动支撑组件为轮胎或滑轮。滚筒顶端设置有进料口,且设置有筛上物出料口和筛下物出料口;滚筒侧壁上设置有若干个均匀分布的筛孔,筛孔直径为80mm。为了进一步优化上述技术方案,磁选机至少设置有磁选机144和磁选机246;为了进一步优化上述技术方案,滚筒筛下物出料口下部设置有传送带,传送带的上方安装有磁选机144;筛上物出料口连接有风选机45,风选机45出料口设置有传送带,传送带上安装有磁选机246;磁选机144和磁选机246内均设置有金属收集柜;为了进一步优化上述技术方案,破碎装置47为剪式和锤式破碎组合式破碎机,安装在磁选机246的底部;更进一步,剪式和锤式破碎组合式破碎机包括:剪式破碎单元a和锤式破碎单元b;其中,剪式破碎单元a包括切割刀片225、轴226和电机二227;轴226包括两个主动轴和一个从动轴,且主动轴和从动轴上均设置有可移动的螺旋型锯齿切割刀片225,切割刀片225交错排列;且电机二227与轴226连接;为了进一步优化上述技术方案,锤式破碎单元b包括:锤部221、转盘222、主轴223和筛板224;其中锤部221设置有平锤头2211和尖锤头2212,且平锤头2211和尖锤头2212交错设置;其中,主轴223连通转盘222支撑在机壳两侧滚动轴承座上,电动机带动转子在破碎腔内高速旋转;锤部221与转盘222活动铰接;更进一步,锤部221的中心与打击中心间距为30-50mm;筛板224设置在锤式破碎单元b的机壳的底部,筛板224上设置有均匀分布的筛孔,筛孔直径为30mm,磁选机246的出料口与剪式破碎单元a的进料口连接。此外,螺旋压榨脱水机48的出液口连接污水收集箱56;螺旋压榨脱水机48的出料口下方设置有链板输送机49,链板输送机49与快速干式发酵单元的进料口连接。为了进一步优化上述技术方案,快速干式发酵单元包括:腐熟仓31;肥料制备单元与腐熟仓31出料口33连接;沥出液处理和回用单元与腐熟仓31出液口35连接;螺旋压榨脱水机48的出料口通过链板输送机49与腐熟仓31进料口32连接。其中,腐熟仓31采用双层不锈钢结构,中间填充有保温层,保温层为聚氨酯保温层39,厚度为30mm;进一步,腐熟仓31设置有翻堆搅拌机312、进料口32、出料口33、排气口34和出液口35;翻堆搅拌机312设置有搅拌轴313,搅拌轴313从腐熟仓31顶部,并垂直布置在腐熟仓31内部;搅拌轴313上设置有搅拌片314,且翻堆搅拌机312与电机一315连接;排气口34连接含恶臭和微生物气溶胶气体处理单元316;出液口35连接沥出液处理和回用单元。更进一步,腐熟仓31还设置有:布气板318和传感器;其中,布气板318位于腐熟仓31内部的底端;传感器位于腐熟仓的内侧壁;且传感器包括但不限于:温度传感器36、湿度传感器37和氧气浓度传感器38。为了进一步优化上述技术方案,还包括:第一进液系统310、起爆剂储存罐311和微生物菌剂储存罐;第一进液系统310安装在腐熟仓31顶部;第一进液系统310与微生物菌剂储存罐连接;起爆剂储存罐311安装在腐熟仓31的外侧壁。更进一步,第一进液系统310包括:第一进液管和第一雾化喷头,第一雾化喷头设置有若干个,且在第一进液管上均匀排列。且,第一进液管通过泵与微生物菌剂储存罐连接;起爆剂储存罐311通过泵连通到腐熟仓31内部;此外,第一雾化喷头为实心锥喷嘴,喷嘴喷淋角度为70度。为了进一步优化上述技术方案,肥料制备单元包括依次连接的滚筒振动筛54和生物干化机55;其中,滚筒振动筛54连接腐熟仓31的出料口33,连接处设置有阀门;进一步,滚筒振动筛54筛孔为20mm,旋转速度为20-25r/min;粒径大于20mm的制肥基料作为滚筒振动筛54筛上物由出料口进入腐熟仓内进行处理,小于20mm的制肥基料作为所述滚筒振动筛54筛下物由收集槽收集后输送至生物干化机55;为了进一步优化上述技术方案,还包括:鼓风机和进料仓,其中鼓风机安装在生物干化机55的一侧;进料仓设置在生物干化机55的顶部;生物干化机55的内部安装有搅拌装置;此外,进料仓可以设计为喇叭口形状;为了进一步优化上述技术方案,沥出液处理和回用单元包括依次连接的:絮凝池319、电化学反应器320和氧化池322;絮凝池319与腐熟仓31出液口35连接,且连接处设置有阀门;为了进一步优化上述技术方案,絮凝池319内安装有搅拌机构,搅拌机构至少设置有三档转速调节;且絮凝319底部设置有排污口,沉淀的腐殖酸从排污口输送至烘干箱内进行干燥,干燥完成后收集;此外,絮凝池319一侧还设置有排水口,上层清液从排水口进入电化学反应器320内。为了进一步优化上述技术方案,还包括:絮凝池储存罐,絮凝池储存罐通过泵连接至絮凝池内部;且絮凝池储存罐位于絮凝池319顶部;絮凝池储存罐内部有絮凝剂氯化铁。电化学反应器320设置有出液口,且出液口处设置有阀门,阀门连接分流管路,一路连接氧化池322;另一路与腐熟仓31连通,且设置有水泵321;氧化池322内设置有酸碱调节剂、自动加料装置、ph传感器和搅拌装置;且氧化池322的出水口连接吸附槽,吸附槽的一侧设置有沥出液排出口。为了进一步优化上述技术方案,还包括:回流管和风机317,且含恶臭和微生物气溶胶气体处理单元包括:生物喷淋箱51、干燥除雾箱52和uv光解装置53;生物喷淋箱51和回流管一端分别与腐熟仓31排气口34端的分流管路连接;风机一端与分流管路连接,另一端与回流管连接,且回流管另一端延伸至布气板318的下端;生物喷淋箱51依次与干燥除雾箱52和uv光解装置53连接;进一步,生物喷淋箱51内设置有第二进液系统和臭气传感器,其中第二进液系统包括第二进液管和第二雾化喷头;第二雾化喷头安装在第二进液管上,且第二进液管通过泵连接植物液储存罐;为了进一步优化上述技术方案,第二雾化喷头的喷淋角度为70度,可喷洒在空间扩散为直径≤0.04mm的液滴。为了进一步优化上述技术方案,干燥除雾箱52包括:箱体、进风口、吸附段和出风口;其中吸附段填置的吸附剂为sdg-ⅰ和sdg-ⅱ的混装,且呈u型填料;此外,更换的吸附剂可作为一般垃圾处理,不会造成二次污染。为了进一步优化上述技术方案,uv光解装置53设置有气体排放口,且uv光解装置53的内紫外灯、恶臭检测器及镶嵌有纳米tio2泡沫镍网;其中,紫外灯可发射波长为185nm和254nm的光;纳米tio2泡沫镍网的tio2负载量为40g/m2;恶臭检测器设置有若干个。为了进一步优化上述技术方案,自动监测和控制单元包括:在线监测系统,智能反馈控制系统和人机交互系统;在线监测系统用于采集进料与卸料单元、预处理单元、快速干式发酵单元、肥料制备单元、沥出液处理和回用单元和含恶臭和微生物气溶胶气体处理单元中关于温度,氧浓度、温度、湿度、臭气、ph值等信息,在线监测系统将收集的信息输送至智能反馈控制系统,智能反馈控制系统根据收集的数据信息对各个单元进行参数的调整和控制;更进一步,人机交互系统设定各个单元的运行参数,并进行实时显示,实时记录,具有记载和查询历史记录的功能;此外,人机交互系统可以与移动终端、云数据进行对接,实现远程控制。实施例2请参阅附图2,还提供了一种用于原位处理的湿垃圾资源化处理方法,具体包括:s1:进料与卸料,开启自动监测和控制单元;s2:预处理:s21:分选:分选装置将湿垃圾进行筛分,其中粒径≤80mm的湿垃圾经磁选机分离金属物质后进行填埋处理;粒径>80mm的湿垃圾经磁选机分离金属物质后进入破碎装置;进一步,分离出的金属物质输送至金属收集槽;此外,粒径>80mm的湿垃圾从筛上物出料口落入风选机,将湿垃圾中的塑料、纸张及玻璃物质及砖瓦等无机物料分选出来后再经磁选机分离出金属物质后进入破碎装置;s22:破碎:破碎装置采用剪切破碎和锤式破碎的协同作用对纤维素、半纤维素、木质素进行破碎,且破碎至粒径为15-20mm后输送至螺旋压榨脱水机48;s23:脱水:螺旋压榨脱水机对破碎后的物料进行挤压,物料的含水率至45-50%后输送至快速干式发酵单元;进一步,破碎后的物料是经过链板输送机输送至螺旋压榨脱水机中,脱水操作完毕后的物料经链板输送机输送至快速干式发酵单元;s3:干式好氧发酵:堆肥1-2天后添加起爆剂和微生物菌剂1;堆肥5-7天后投加微生物菌剂2;且发酵初期温度<45℃;发酵中期高温阶段温度控制在60-65℃,且持续时间>3天;发酵后期温度降至<45℃;发酵周期10-13天;堆体含水率控制在45-55%,由于经沥出液处理和回用单元处理后产生的沥出液会回灌至干式好氧发酵单元,会提高堆体含水率,通过加入秸秆、锯末等物质降低堆体含水率;氧气浓度控制在15-20%;发酵期间通风速率0.5-0.6l/min.kg;进一步,干式好氧发酵间歇运行,每天12h,整个过程在12-13天内完成;此外,步骤s3起爆剂为葡萄糖;进一步,微生物菌剂1包括:枯草芽孢杆菌、短小芽孢杆菌、埃式放线菌和酿酒酵母菌,配比为2:1:1:1,且每种菌浓度均为(2.0-4.0)*108cfu/ml;微生物菌剂2包括:黑曲霉、拟康宁木霉和黄孢原毛平革菌,配比为1:1:1,且每种菌浓度均为(5.0-7.0)*107cfu/ml;其中起爆剂接种量为1-2%,微生物菌剂1和微生物菌剂2接种量均为3-5‰;s4:肥料制备:干式好氧发酵处理后的物料输送至肥料制备单元,经筛分后的筛下物进行生物干化处理,含水率<15%,冷却后得有机肥料;此外,经筛分后的筛上物作为辅料回用;进一步,筛下物进行生物干化处理之前,先根据其n、p、k等的含量与有机质适量混合,混合后再进行生物干化处理;s5:沥出液处理和回用:干式好氧发酵处理后产生的沥出液输送至絮凝池,调节ph,并投加絮凝剂,搅拌,沉降,经沉淀、分离后,提取腐殖酸用于肥料制备,上清液打入电化学反应器进行脱氮处理,处理后的一部分返回至腐熟仓,剩余部分调节ph值经氧化吸附后回用;进一步,步骤s5絮凝剂为氯化铁,且按照沥出液体积的0.03%投加,进一步,絮凝剂投加完毕后分三个阶段搅拌,其中,第一搅拌阶段:搅拌速度200-220r/min,搅拌时间10-13min;第二搅拌阶段:搅拌速度100-120r/min,搅拌时间5-8min;第三搅拌阶段:搅拌速度50-70r/min,搅拌时间5-8min;且,投加絮凝剂之前ph调节至2-5。进一步,步骤s5剩余部分调节ph至6-7,氧化剂为feso4·7h2o和h2o2,且feso4·7h2o和h2o2质量体积比为0.5g:1ml;进一步,氧化吸附过程中的吸附剂采用10g/l的活性炭,吸附时间为3h;s6:含恶臭和微生物气溶胶气体处理;进一步,干式好氧发酵处理过程中产生的含恶臭和含菌微生物气溶胶,首先会在快速干式发酵单元内循环利用,且大部分气体以内循环的方式向快速干式发酵单元鼓风曝气,在快速干式发酵单元内多次循环,调节其氧浓度和温度;同时恶臭气体部分在堆肥微生物作用下发生降解;此外,通过快速干式发酵单元内循环供氧还可以充分利用堆肥产生的热蒸汽,提高堆肥处理效率,促进堆肥产品的进一步干化和腐熟;其不能循环利用的含恶臭和微生物气溶胶的气体则进入含恶臭和微生物气溶胶气体处理单元进行处理后排放;更进一步,不能循环利用的含恶臭和微生物气溶胶的气体先经过生物喷淋箱除尘除臭,其中通过喷淋植物液,粉尘被拦截下来;同时,恶臭气体通过润湿、多孔和充满活性微生物的滤层,利用微生物对恶臭物质的吸附、吸收和降解作用,将恶臭气体物质吸附后分解成co2、h2o、h2so4等物质;生物喷淋箱处理完毕后的气体进入干燥除雾箱,废气通过吸附段的吸附及干燥,提高恶臭气体和微生物气溶胶的净化速率,最后经uv光解装置处理,通过uv光可以催化氧气生成臭氧和氧活性基因,在高能紫外光、臭氧和氧活性基因的协同作用下将恶臭和微生物气溶胶气体充分净化达标后排放。实施例3采用实施例1和实施例2的处理系统和处理方法进行原位湿垃圾的处理,对照组1在实施例2的基础上,将快速干式发酵单元中接种的微生物菌剂1和菌剂2均替换为酵母菌菌液,菌液浓度为3.0×108cfu/ml,接种量为5‰。通过10d的发酵周期,根据测定所获得肥料的各项指标,对堆肥产品的质量进行比较,结果如表1所示。表1依据实施例1和实施例2处理系统和处理方法进行原位湿垃圾的处理,得到的肥料各项指标较好,优于按《城镇垃圾农用控制标准》(gb8172-87)中的指标值;并且优于对照组1堆肥产品的质量。实施例4依据实施例1和实施例2处理系统和处理方法对堆肥沥出液进行处理,对照组2为在本发明实施例2的基础上,对s5沥出液处理和回用步骤中的feso4·7h2o/h2o2比值、活性炭浓度和吸附时间进行调整,改为feso4·7h2o/h2o2=1(g/ml),活性炭浓度为6g/l,沥出液在吸附槽内停留1h;并对沥出液进行各项指标测定,结果如表2所示。表2项目实施例4对照组2bod5/(mg/l)1318cod/(mg/l)4570浊度/ntu510氨氮/(mg/l)812总氮/(mg/l)1315总磷/(mg/l)0.50.8由表2可见,实施例4的出水水质可达到《城市污水再生利用城市杂用水水质》(gb/t18920-2002)中城市绿化、道路清扫、车辆冲洗标准;并且比对照组2对沥出液的处理效果好。实施例5依据实施例1和实施例2处理系统和处理方法对堆肥沥出液预处理后回灌发酵单元,对照组3在实施例2的基础上,将预处理后的沥出液替换为不经预处理的沥出液,对照组4在实施例2的基础上,将预处理后的沥出液替换为自来水。根据测定发酵过程的各项指标,对堆肥效果进行比较,结果如表3所示。表3项目实施例5对照组3对照组4氨氮/(mg/g)0.550.70.5最高堆肥温度/(℃)626050挥发性固体含量下降比例/(%)403025堆料高度减少比例/(%)605545nh4+-n/no3--n0.0190.030.08由表3可知,实施例5将垃圾堆肥过程中产生的沥出液预处理后回灌到堆肥物料中,与直接回灌和回灌自来水堆肥相比,更能促进堆肥的稳定、加速堆肥腐熟的进程。本说明书中各个实施例采用递进的方式描述,每个实施例重点说明的都是与其他实施例的不同之处,各个实施例之间相同相似部分互相参见即可。对于实施例公开的装置而言,由于其与实施例公开的方法相对应,所以描述的比较简单,相关之处参见方法部分说明即可。对所公开的实施例的上述说明,使本领域专业技术人员能够实现或使用本发明。对这些实施例的多种修改对本领域的专业技术人员来说将是显而易见的,本文中所定义的一般原理可以在不脱离本发明的精神或范围的情况下,在其它实施例中实现。因此,本发明将不会被限制于本文所示的这些实施例,而是要符合与本文所公开的原理和新颖特点相一致的最宽的范围。当前第1页12