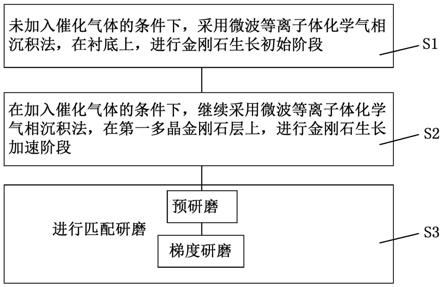
1.本发明涉及半导体领域,特别涉及一种金刚石半导体结构的形成方法。
背景技术:2.金刚石特殊的晶体结构和强的碳
‑
碳键作用,使其具有许多出类拔萃的特性,具备现有其他半导体材料不可比拟的物理、化学、电子、光学、热学和机械性能。它的带隙宽、热导率高、击穿场强高、载流子迁移率高、耐高温、抗酸碱、抗腐蚀且抗辐照,这些优越性使其在高功率、高频和高温领域等方面发挥重要作用。然而,自然界中天然存在的金刚石无法满足广泛的应用需求。
3.人工培育金刚石的方法包括高压高温法(hpht)与化学气相沉积法(cvd)等。高压高温法制备的金刚石合成尺寸小,纯度低,不易掺杂。化学气相沉积法既能够制备单晶,也能够制备多晶,还可进行掺杂,且在理论上化学气相沉积法制备的金刚石尺寸不受限制。
4.化学气相沉积法对金刚石的制备又有三种方法:热丝化学气相沉积法、直流等离子体喷射化学气相沉积法和微波等离子体化学气相沉积法(mpcvd)。微波等离子体化学气相沉积法具有微波能量无污染和气体原料纯净等优势,在众多金刚石制备方法中脱颖而出,成为制备大尺寸和高品质多晶金刚石最有发展前景的技术。
5.更多有关金刚石半导体结构形成方法的内容可以参考cn1705775a、gb2584010a、cn109911894a、us20190326030al和cn107004639a的专利文献。
技术实现要素:6.为进一步提高金刚石半导体结构的形成效率并保证结构品质,本发明提供一种新的金刚石半导体结构的形成方法。
7.本发明是这样实现的:在提供氢气和甲烷的条件下,且在未加入催化气体的条件下,采用微波等离子体化学气相沉积法,在衬底上,进行金刚石生长初始阶段,以在衬底上生长第一多晶金刚石层;在提供氢气和甲烷的条件下,且在加入催化气体的条件下,继续采用微波等离子体化学气相沉积法,在第一多晶金刚石层上,进行金刚石生长加速阶段,以在第一多晶金刚石层上生长第二多晶金刚石层;对第二多晶金刚石层进行匹配研磨。
8.可选的,在金刚石生长加速阶段结束时,第一多晶金刚石层和第二多晶金刚石层的总厚度为30
‑
100μm;在金刚石生长初始阶段结束时,第一多晶金刚石层的厚度达到总厚度的60
‑
75%。然后进行金刚石生长加速阶段。
9.可选的,在金刚石生长加速阶段,加入的催化气体为氮气,催化气体占气源的比例为0.8
‑
1.2%。
10.可选的,对第二多晶金刚石层进行的匹配研磨包括预研磨和梯度研磨;预研磨包括将金刚石磨粒砂浆(金刚石磨粒调配成相应砂浆)喷洒(充分喷洒)在磨盘上,对磨盘进行修盘研磨;梯度研磨先使用粒径为20μm的金刚石磨粒砂浆进行第一梯度研磨,再使用粒径为10μm的金刚石磨粒砂浆进行第二研磨。
11.可选的,在金刚石生长加速阶段结束时,第一多晶金刚石层和第二多晶金刚石层的总厚度为250
‑
600μm;在金刚石生长初始阶段结束时,第一多晶金刚石层的厚度达到总厚度的60
‑
80%。然后进行金刚石生长加速阶段。
12.可选的,在金刚石生长加速阶段,加入的催化气体为氮气,催化气体占气源的比例为0.04
‑
0.2%。
13.可选的,对第二多晶金刚石层进行的匹配研磨包括预研磨和梯度研磨;预研磨包括将将金刚石磨粒砂浆喷洒在磨盘上,对磨盘进行修盘研磨;梯度研磨先使用粒径为40μm的金刚石磨粒砂浆进行第一梯度研磨,再使用粒径为20μm的金刚石磨粒砂浆进行第二梯度研磨,之后使用粒径为10μm的金刚石磨粒砂浆进行第三梯度研磨。
14.本发明上述不同可选方案中,采取不同粒径的金刚石磨料进行组合研磨,能够使快速生长(8
‑
10μm/h)的2英寸多晶金刚石的表面粗糙度,从微米级别降低至几十纳米以下(例如30nm以下或者20nm以下)。
15.为了减少生长和研磨金刚石的整体时间,本发明在多晶金刚石层生长的最后一步一个阶段,提高生长速率,使这个阶段成为金刚石生长加速阶段,从而生长出一个以备研磨的快速生长层,此快速生长层即为第二多晶金刚石层。
16.本发明还针对不同的生长层形貌(主要是由于厚度不同而导致的不同生长层形貌),选用不同磨料粒径的金刚石磨料组合,以达到较高的去除效率和研磨效果。
17.本发明使用的衬底的材料可以为硅、钼、铱、氮化硼、氮化镓或者碳化硅。
18.可选的,金刚石生长初始阶段采用的微波功率可以为3000
‑
5000w,采用的气压可以为100
‑
200torr,衬底的温度可以控制在600
‑
1200℃,气源包括氢气和甲烷,气体总流量可以为300
‑
600sccm,甲烷浓度可以为1
‑
5%。
19.可选的,金刚石生长加速阶段采用的微波功率可以为3000
‑
5000w,采用的气压可以为100
‑
200torr,衬底的温度可以控制在800
‑
1200℃,气源包括氢气、甲烷和催化气体,气体总流量可以为300
‑
600sccm,甲烷浓度可以为1
‑
5%;催化气体可以为氮气。
20.可选的,金刚石生长加速阶段的进行时间可以是1.25
‑
12.5h,即在多晶金刚石生长结束前的1.25
‑
12.5h内添加相应的氮气作为催化气体,以加快本应被研磨去除的材料部分的生长速率。
21.可选的,控制第二多晶金刚石层的生长速率为8
‑
10μm/h,即本发明控制本应被研磨去除的材料部分的生长速度为8
‑
10μm/h。
22.可选的,匹配研磨可以采用游星轮式铸铁研磨盘进行研磨,研磨盘的转速为20
‑
40rpm,磨粒砂浆的磨料质量分数为5
‑
10wt%,研磨液的流量为10
‑
20ml/min,研磨压力为200
‑
2000g。
23.本发明的有益效果如下。
24.鉴于微波等离子体化学气相沉积法生长金刚石的难点在于生长速率较低,且对金刚石进行研磨加工的主要难点在于材料硬度极大,耗时极长。因此,本发明选择将金刚石生长的过程分为两个阶段,分别是金刚石生长初始阶段和金刚石生长加速阶段。金刚石生长初始阶段采用氢气和甲烷作为气源。而在金刚石生长加速阶段添加氮气,起到强催化作用,明显增加沉积速率(即生长速率),且沉积形成的层结构中非金刚石相不断增多,生长质量不断降低,而这一降低正是本发明所利用的。因为,本发明利用此时出现的大量无定形碳结
构,使得第二多晶金刚石层的结晶度变差,在后续匹配研磨过程中,能够更加容易被去除,从而降低了研磨工序的难度,提高研磨效率,提升了相应方法的产业价值。可见,本发明从产业化的角度提供一种工艺效率高(生长速率和研磨效率均提高)且产品质量好的金刚石半导体结构的形成方法。
25.由于电子元件的表面通常非常光滑和平坦,为了使其和金刚石之间形成无间隙的界面,在器件应用中获得金刚石最大的散热效果,会使用先研磨后抛光的方法对金刚石进行表面加工,即研磨是抛光重要的前处理工序,为后续抛光提供良好的表面质量基础。而本发明提供的金刚石半导体结构的形成方法,相应的多晶金刚石层的生长加工效率极高,设备简单易于操作,技术方案容易实施,成本较低,并且对所制作的金刚石表面损伤非常小,为后续的抛光提供了良好的初始抛光表面。
26.由于金刚石的研磨是必不可少的加工工序,因此,对于生长过程不加入氮气的金刚石多晶片来说,会造成此时金刚石的生长速率仍然较低,晶粒尺寸更大(继续增大),晶粒更完整。这些晶粒更完整的晶粒,在固定的生长加研磨的时间周期内,会严重占用后续研磨的时间,增加了研磨的难度。而本发明在生长过程的最后一步加入氮气,使这一阶段金刚石的生长速率显著提高,且晶粒尺寸反而降低,晶粒完整性下降。此时的层结构是第二多晶金刚石层,是作为本应去除的表面材料层,因此能够节省后续研磨的时间,降低了研磨难度,提高了生产效率,并且仍然能够保证相应金刚石半导体结构的使用需求,即仍然能够保证相应多晶金刚石层的质量。
27.本发明采用梯度研磨和混合磨料研磨的匹配研磨方法,针对不同氮气比例的样品,选择不同的研磨磨料组合和配比,进一步保证了最终研磨后的表面粗糙度低,更好地满足后续抛光需求。通过本发明微波等离子体化学气相沉积法生长的金刚石更适于高功率器件的散热,可以作为氮化镓基高电子迁移率晶体管(hemt)的散热衬底、卫星相控阵组件的核心热管理元件、半导体激光器散热片、超高功率led光源散热片等。
附图说明
28.图1是金刚石半导体结构的形成方法步骤示意图;
29.图2是金刚石生长加速阶段后金刚石薄膜的扫描电子显微镜照片;
30.图3是金刚石生长加速阶段后金刚石厚膜的扫描电子显微镜照片;
31.图4是金刚石薄膜研磨后的扫描电子显微镜照片;
32.图5是金刚石厚膜研磨后的扫描电子显微镜照片;
33.图6是金刚石薄膜研磨后的原子力显微镜照片;
34.图7是金刚石厚膜研磨后的原子力显微镜照片。
具体实施方式
35.下面通过参考附图描述的实施例是示例性的,旨在用于解释本发明,而不能理解为对本发明的限制。
36.为了提高金刚石的生长质量,在金刚石制备过程中,通入适量的氧气;为了提高金刚石的生长速度,通入适量的氮气;交替通入氧气和氮气的方法,或者在制备过程中调整氢气和甲烷的比例、调整微波功率、沉积压力、温度这些生长参数的方法(微波等离子体化学
气相沉积法主要工艺参数包括微波功率、沉积气压、基片温度、气体种类、气体流量,一般均是对这些参数做出调整);然而,这些均无法达到相应的金刚石半导体结构生长需求,上述方法缺乏产业化角度考虑问题,缺乏对生长过程和研磨过程的配合考虑,未能从产业化的角度提出整体性的质量保证和效率提高双重保障的形成方法。
37.实施例
38.请参考图1,本实施例包括步骤s1至步骤s3。
39.在步骤s1之前,本实施例先在微波供能的气相环境下,使气源(此时的气源可以包括氢气和甲烷)发生反应,从而在衬底表面沉积金刚石薄膜。更加具体的,本实施例选用硅片作为衬底,并对硅衬底进行预处理以增强形核。对硅衬底的预处理包括:将2英寸硅片分别经过金刚石粉悬浮液超声波种晶,采用丙酮、酒精和去离子水超声波清洗后,放入微波等离子体化学气相沉积设备腔体中;生长前,先使用氢气等离子体刻蚀去除表面的吸附杂质,随后进行金刚石生长。
40.步骤s1中,在提供氢气和甲烷的条件下,且在未加入催化气体的条件下,采用微波等离子体化学气相沉积法,在衬底上,进行金刚石生长初始阶段,以在所述衬底上生长第一多晶金刚石层;本实施例在金刚石生长初始阶段的参数为:微波功率3700w,气压140torr,硅衬底温度830℃,气源为氢气和甲烷,气体总流量500sccm,甲烷浓度为3%,生长速率为2μm/小时。
41.步骤s2中,在提供氢气和甲烷的条件下,且在加入所述催化气体的条件下,继续采用微波等离子体化学气相沉积法,在所述第一多晶金刚石层上,进行金刚石生长加速阶段,以在所述第一多晶金刚石层上生长第二多晶金刚石层;本实施例在金刚石生长加速阶段的参数为:微波功率3700w,气压140torr,硅衬底温度835℃,气源为氢气、甲烷和氮气,氢气与甲烷气体总流量500sccm,甲烷浓度3%。
42.对于第一多晶金刚石层和第二多晶金刚石层的总厚度为30
‑
100μm的多晶金刚石层,本说明书后续称为金刚石薄膜。晶粒尺寸不超过10μm的第二多晶金刚石层,对应的即金刚石薄膜的情况。
43.对于第一多晶金刚石层和第二多晶金刚石层的总厚度为250
‑
600μm的多晶金刚石层,本说明书后续称为金刚石厚膜。晶粒尺寸超过100μm的第二多晶金刚石层,对应的即金刚石厚膜的情况。
44.可知,本发明的金刚石生长初始阶段和金刚石生长加速阶段完成的是对金刚石薄膜和金刚石厚膜的生长,后续匹配研磨阶段则是分别对金刚石薄膜和金刚石厚膜的匹配研磨。本发明能够将金刚石薄膜的金刚石生长加速阶段和梯度研磨整体时间控制在10h以内,能够将金刚石厚膜的金刚石生长加速阶段和梯度研磨整体时间控制在25h以内。
45.具体的,本实施例生成的金刚石薄膜总厚度为30μm。在生长第一多晶金刚石层达到20μm后,引入催化气体氮气,氮气的浓度为0.8%并保持1.25h,第二多晶金刚石层的生长速率保持为8μm/h;生长的第二多晶金刚石层为10μm。可知,生长的第一多晶金刚石层占总厚度的66.7%,生长的第二多晶金刚石层占总厚度的33.3%。
46.本实施例在生成金刚石厚膜总厚度为400μm。在生长第一多晶金刚石层达到320μm后,引入催化气体氮气,氮气的浓度先由0.04%并保持6.2h,再由0.1%并保持2.2h,之后由0.2%并保持1.6h,此时第二多晶金刚石层的生长速率保持为8μm/h左右;生长的第二多晶
金刚石层为80μm。可知,生长的第一多晶金刚石层占总厚度的80%,生长的第二多晶金刚石层占总厚度的20%。
47.上述过程中,在金刚石生长初始阶段使用甲烷和氢气作为气源,其中氢原子促进甲烷的离解形成甲基等有利于金刚石膜沉积的极性基团,这些基团与金刚石膜表面未饱和的碳原子悬挂键相结合形成具有正四面体结构的sp3杂化键并连续生成,形成金刚石膜层(第一多晶金刚石层)。而在金刚石生长加速阶段通入氮气,使生长速率大幅提高,并产生大量的无定形碳结构,薄层的结晶度变差(变差的部分为第二多晶金刚石层),在研磨工序中变差的部分更易被去除。上述过程中,本实施例在金刚石加速生长阶段过程中,在金刚石生长加速阶段通过控制氮气含量,来控制金刚石的表面形貌。
48.结果显示,运用本实施例两段式生长方法得到的多晶金刚石层,由工作人员都可以直接观察看到,无论是金刚石薄膜,还是金刚石薄膜厚膜,最终的表面形貌均较为良好,有利于后续研磨。
49.图2进一步显示金刚石薄膜的扫描电子显微镜(sem)图,图2显示的是在放大1000倍尺度下金刚石薄膜的表面形貌。从中可见,对于金刚石薄膜,在金刚石生长加速阶段通入氮气含量较高(0.8
‑
1.2%)后,金刚石表面形貌中,表面晶粒细致平整,晶粒尺寸不超过10μm,这对于后续研磨有利。
50.图3进一步显示金刚石厚膜的扫描电子显微镜照片,图3显示的是在放大1000倍尺度下金刚石厚膜的表面形貌。从中可见,对于金刚石厚膜,在金刚石生长加速阶段通入氮气含量较低(0.04
‑
0.2%)后,金刚石表面形貌中,表面晶粒膨大粗糙,晶粒尺寸超过100μm并伴有开裂,这对于后续研磨有利。
51.步骤s3中,在金刚石生长加速阶段后,本实施例对第二多晶金刚石层进行匹配研磨。
52.本实施例研磨设备的研磨盘,采用带沟槽的铸铁盘,铸铁盘直径可以为300mm,这种尺寸适于2英寸直径晶片的研磨。
53.匹配研磨包括预研磨,即进行研磨工序的准备工作。包括将磨浆充分喷洒在研磨盘上进行所述预研磨,以提高研磨盘表面的平整度(即进行修盘)。
54.预研磨后,根据金刚石生长后的形貌(即第二多晶金刚石层的形貌),对多晶金刚石片(即生长在2英寸硅衬底上的多晶金刚石层)进行不同的梯度研磨。
55.梯度研磨主要是利用第二多晶金刚石层和铸铁研磨盘之间的游离金刚石磨料,在一定压力作用下,使金刚石和研磨盘发生相对运动,以对金刚石表面材料进行切削加工。在研磨过程中,将直径为2英寸的多晶金刚石片(即生长在2英寸硅衬底上的多晶金刚石层)置于游星轮内,做既公转又自转的游星运动,磨浆通过供液系统,供给到研磨盘上,通过控制面板使研磨盘以一定的速度开始旋转,游离磨料在离心力作用下均匀分布在金刚石表面,由滚动、滑动的金刚石磨粒对第二多晶金刚石层的表面材料进行划刻和去除,达到研磨效果。
56.梯度研磨阶段,选用粒径为40μm、20μm、10μm的金刚石磨粒调配成砂浆备用。对于金刚石薄膜表面(即晶粒尺寸不超过10μm的第二多晶金刚石层表面)和金刚石厚膜表面(即晶粒尺寸超过100μm的第二多晶金刚石层表面),分别先使用不同的组合进行研磨。
57.梯度研磨的研磨条件为:研磨盘转速为30rpm,磨料质量分数为10wt%,研磨液流
量为20ml/min,研磨压力为1500g。
58.对于金刚石薄膜(即晶粒尺寸不超过10μm的金刚石膜层)表面,在梯度研磨过程中,先使用粒径为20μm的金刚石磨粒砂浆进行第一梯度研磨,再使用粒径为10μm的金刚石磨粒砂浆进行第二研磨,因此,这样的两种小尺寸磨料研磨步骤,适于加工平滑且晶粒尺寸小的金刚石表面。
59.对于金刚石厚膜(即晶粒尺寸超过100μm的金刚石膜层)表面,在梯度研磨过程中,先使用粒径为40μm的金刚石磨粒砂浆进行第一梯度研磨,再使用粒径为20μm的金刚石磨粒砂浆进行第二梯度研磨,之后使用粒径为10μm的金刚石磨粒砂浆进行第三梯度研磨,这种包括大尺寸多梯度式的磨料研磨步骤,适于加工粗糙且晶粒尺寸较大的金刚石表面。
60.上述不同第一多晶金刚石层和第二多晶金刚石层的总厚度采用具体不同工艺参数,原因是化学气相沉积法生长金刚石的厚度对热管理很重要。对于高功率密度的小型器件,100μm以下的厚度足够散热。但是,对于尺寸超过10毫米数量级且具有较大产热区域的器件,必须增加金刚石厚度以获得更好的散热效果。例如,对于能产生几千瓦光输出功率的碟片激光器,就需使用毫米级别厚度的金刚石散热。多晶金刚石膜层的厚度直接影响研磨工序,对于30
‑
100μm厚度的上述金刚石薄膜,可以添加0.8
‑
1.2%比例的氮气。这种添加0.8
‑
1.2%比例氮气的生长的上述薄膜,相对于不添加氮气的金刚石薄膜,会出现表面晶粒细化的现象,晶粒尺寸不超过10μm,薄膜表面平滑,后续可以使用粒径10
‑
20μm的磨粒研磨,研磨时间和成本降低;对于250
‑
600μm厚度的上述金刚石厚膜,可以添加0.04
‑
0.2%比例的氮气,这种添加0.04
‑
0.2%比例氮气生长的上述厚膜,相对于不添加氮气的金刚石厚膜,其表面晶粒伴有开裂的现象,可以使用粒径10
‑
40μm的磨粒,研磨难度降低。即,对上述金刚石薄膜而言,金刚石晶粒越小,表面越平,越有利于研磨;对上述金刚石厚膜而言,晶粒越开裂,越有利于研磨。
61.本实施例在上梯度研磨后,还包括将最终的金刚石半导体结构表面清洗干净,然后用扫描电子显微镜(sem)检测,检测研磨后金刚石膜层的表面质量。
62.其中,梯度研磨后,获得的金刚石薄膜表面形貌扫描电子显微镜照片和金刚石厚膜表面形貌扫描电子显微镜照片分别如图4和图5。
63.图4的sem检测结果可见,本实施例研磨后的金刚石层表面更加平滑,未见明显机械划痕和凹坑。图5的sem检测结果可见,本实施例研磨后的金刚石层金刚石厚膜表面明显平整,几乎没有破碎凹坑。可见,本实施例中,金刚石薄膜和金刚石厚膜均在短工艺时间内,就获得了完整的平面结构,形成了良好的金刚石半导体结构。
64.本实施例在上梯度研磨后,还包括将最终的金刚石半导体结构表面清洗干净,然后用原子力显微镜(afm)检测,检测研磨后金刚石膜层的表面质量。原子力显微镜照片显示了金刚石膜层表面的粗糙度值,如图6和图7所示。
65.图6显示的金刚石薄膜的原子力显微镜照片,显示了在
‑
400nm至400nm标尺下,金刚石薄膜表面的粗糙度,此时的粗糙度值为20nm,测量区域均为5μm
×
5μm。图7显示的金刚石薄膜的原子力显微镜照片,同样显示了在
‑
400nm至400nm标尺下,金刚石厚膜表面的粗糙度,此时的粗糙度值为30nm,测量区域均为5μm
×
5μm。因此,本实施例的形成方法,无论是形成金刚石薄膜,还是金刚石厚膜,均能够使相应的金刚石膜层表面的粗糙度较小。
66.本实施例在上述梯度研磨后,还包括用厚度测量仪检测最终金刚石层的材料去除
情况,并记录每片金刚石研磨耗时,本实施例得到金刚石薄膜的梯度研磨耗时为8h,金刚石厚膜的梯度研磨耗时为15h。
67.综上所述,本发明实施例可以根据不同的金刚石散热片厚度要求,在金刚石半导体结构生长过程的最后一个阶段,根据膜厚的不同,添加不同含量的氮气,以提高相应生长速率,并形成更利于研磨的表面形貌,之后选择相应的匹配研磨参数,使生长和研磨起到相互配合的作用,提高整体工艺效率并保证最终产品的质量。
68.其它实施例中,可以替换衬底的尺寸,也就是替换金刚石的尺寸,不限于是2英寸硅衬底上形成的多晶金刚石层。其它实施例中,磨粒的种类以及研磨盘的材质和尺寸等可以根据相应金刚石膜层的不同而进行相应调整。
69.尽管上面已经示出和描述了本发明的实施例,本领域的普通技术人员在本发明的范围内可以对上述实施例进行变化、修改、替换和变型,本发明保护范围以权利要求为准。