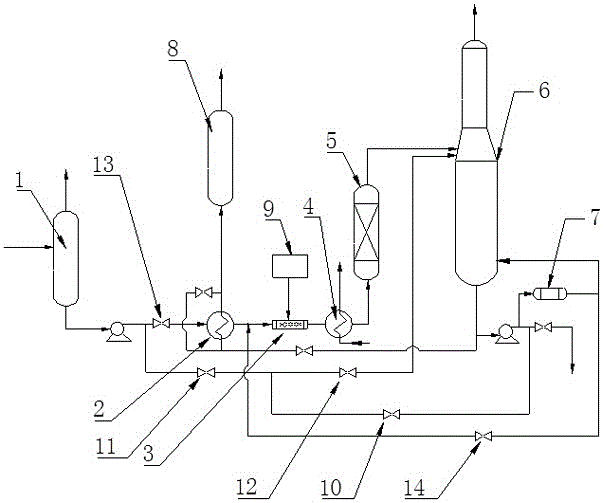
本发明涉及一种生产乙烯的方法,具体地说是一种以芳烃抽余油为原料生产乙烯的方法。
背景技术:
:芳烃抽提是石油炼制过程中提纯芳烃的重要工艺技术,其主要目的是从催化重整或裂解加氢汽油中分离出btx(苯,甲苯,二甲苯)。抽提工艺具有芳烃质量好、回收率高及原料有适应性好等特点,而抽余油基本不含芳烃,富含链烷烃,并含有部分环烷烃和少量烯烃,是很好的乙烯裂解原料。近年来,随着我国乙烯生产规模的不断扩大,乙烯原料紧缺的问题日益突出,这严重制约了国民经济发展和企业经济效益的提高。某些企业将芳烃抽余油生产6#或120#溶剂油,也有的企业用作车用汽油调和组分,由于芳烃抽余油研究法辛烷值(ron)较低,作为车用汽油调和组分时受到限制。因此,芳烃抽余油做乙烯裂解装置原料是提高经济效益的有效方法之一,但目前关于生产乙烯裂解原料的相关报道较少。cn1621497a公开了一种石脑油重组处理方法,其步骤如下:(1)先将石脑油进行萃取分离,分离出抽余油和抽出油;(2)抽余油进乙烯蒸汽裂解装置;(3)抽出油进入重整装置重整。该方法能够将芳烃产量提高30%以上,乙烯产量提高40%以上。cn103374395a公开了一种以石脑油为原料生产芳烃和乙烯的方法,包括如下步骤:(1)在氢气存在下,将石脑油在0.15~3.0mpa、300~540℃,体积空速为2.1~50h-1的条件下在催化重整区与重整催化剂接触进行浅度催化重整反应,使石脑油中的环烷烃转化率大于85质量%,链烷烃转化为芳烃和c4-烃的转化率小于30质量%;(2)将催化重整得到的重整生成油在第一芳烃分离区进行芳烃分离,得到富含芳烃的馏分和富含链烷烃的馏分;(3)将富含链烷烃的馏分及催化重整产生的液化气送入蒸汽裂解区进行裂解反应生产乙烯。该法通过浅度催化重整可以充分利用石脑油在生产芳烃的同时最大化地生产乙烯。但是,上述方法对芳烃抽余油进行裂解生产乙烯时,裂解炉管内容易结焦,导致裂解能耗增加,乙烯收率下降,而且停炉清焦周期短,又会缩短炉管和耐火砖的寿命。技术实现要素:针对现有技术的不足,本发明提供了一种以芳烃抽余油为原料生产乙烯的方法。该方法不但可减缓裂解炉管生焦速率,延长清焦周期,保证乙烯裂解装置的稳定运行,而且有效解决跨线阀门内漏造成的产品不合格或装置运转周期缩短的问题,以及解决了加氢处理装置开工初期引起的产品质量不达标问题。本发明提供了一种以芳烃抽余油为原料生产乙烯的方法,该方法包括:芳烃抽余油进入加氢反应器,在加氢精制催化剂存在的条件下进行加氢反应,加氢反应流出物通入稳定塔进行气液分离处理,然后塔底物料通入乙烯裂解装置,进行裂解反应生产乙烯;设置跨线用于将加氢反应器与稳定塔隔离时,将芳烃抽余油直接引入稳定塔,跨线为设置在加氢反应器入口前的管线与稳定塔进口之间的连通管线;设置防漏管线,防漏管线一端与跨线连通,另一端与稳定塔底循环泵出口管线连通,防漏管线上设置第一阀门;跨线与防漏管线连通位置的跨线两侧分别设置有第二阀门、第三阀门;正常运转时,将第二阀门、第三阀门中的至少一道阀门关闭,优选地将第二阀门、第三阀门均关闭,第一阀门处于打开状态,防漏管线内液相压力高于跨线内压力,优选地高于跨线内液相压力0.1mpa~0.3mpa。本发明方法中,在加氢反应器开工时,芳烃抽余油先进入稳定塔,然后将稳定塔的塔底物料引入到加氢反应器并进行加氢反应,加氢反应流出物通入稳定塔5分钟~24小时,优选为1~10小时,停止将芳烃抽余油直接通入稳定塔和停止将稳定塔的塔底物料引入加氢反应器,将芳烃抽余油直接引入到加氢反应器,进行正常的加氢反应过程。本发明方法中,加氢反应采用液相加氢反应,即在反应条件下,芳烃抽余油至少80wt%保持液相状态,进一步优选地,芳烃抽余油至少90wt%保持液相状态。本发明方法中,稳定塔设置的塔底再沸器为稳定塔提供热源,引入加氢反应器的稳定塔底物料在塔底再沸器之后引出,优选地,在塔底再沸器之后引出的稳定塔底物料的温度为100℃~240℃。本发明方法中,稳定塔的塔底设置物料输送装置(可以为输送泵),通过物料输送装置将稳定塔塔底出口的物料输送至加氢反应器入口前的管路。本发明方法中,在进入加氢反应器前的管路上沿流向依次设置有第一换热器、气液混合器和第二换热器,第一换热器、第二换热器用于加热芳烃抽余油,气液混合器用于将氢气和芳烃抽余油进行充分混合,气液混合器优选为静态混合器或动态混合器,静态混合器选自sv型静态混合器、sk型静态混合器、sx型静态混合器、sh型静态混合器、sl型静态混合器中的一种或者几种组合,动态混合器选自混合泵、超临界混合器、搅拌混合器中一种或者几种组合。本发明方法中,与第一换热器的第一进口连接的管路设置有第四阀门。本发明方法中,稳定塔塔底物料出口连接有再沸器,再沸器的物料出口与气液混合器的进口管路连接,其管路上安装有第五阀门。本发明方法中,稳定塔的塔底出口管路与第一换热器的第二进口连接。本发明方法中,加氢反应器所需的氢气采用自psa(变压吸附)单元排出的氢气。本发明方法中,催化剂床层上面从下向上依次设置有金属网和/或第一金属格栅、粒径逐渐变大的两层以上瓷球,加氢反应器的壁体在金属网和/或第一金属格栅之上设置有上卸剂口;催化剂床层下面从上向下依次设置有金属网和/或第二金属格栅、粒径逐渐变大的两层以上瓷球、鸟巢支撑剂、第三金属格栅,加氢反应器的壁体在金属网和/或第二金属格栅与第三金属格栅之间设置有下卸剂口;加氢反应器的壁体在催化剂床层区域设置有中卸剂口。本发明方法中,反应物料自加氢反应器底部进入加氢反应器内进行加氢反应。本发明方法中,加氢反应的操作条件如下:反应压力为0.5mpa~6.0mpa,优选为1.2mpa~3.0mpa;反应温度为100℃~240℃,优选为140℃~200℃;液时体积空速为1.0h-1~12.0h-1,优选为4.0h-1~8.0h-1;氢油体积比为20:1以下,优选为2:1~5:1。本发明方法中,氢油体积比与现有常规方法相比可以明显降低。本发明方法中,使用的加氢精制催化剂可以是商品加氢精制催化剂,如以贵金属或还原态镍为活性组分的加氢精制催化剂,此类催化剂具有较高的加氢活性,可以在相地较低的温度下进行加氢反应。优选采用以贵金属为活性组分的加氢精制催化剂,如抚顺石油化工研究院研制生产的hdo-18催化剂。贵金属加氢精制催化剂一般以氧化铝为载体,以pt和/或pd为活性组分,活性组分以重量计在催化剂中的含量不小于0.1%,一般为0.1%~1.5%。对于以还原态镍为活性组分的加氢精制催化剂,一般以氧化铝或改性氧化铝为载体,以镍氧化物为活性组分(以镍氧化物重量计占催化剂重量的15%~70%,优选为25%~45%),在使用前对催化剂进行还原活化,将镍氧化物转化为还原态,以提高催化剂加氢活性。对芳烃抽余油馏分原料来说,使用该加氢精制催化剂可以使芳烃抽余油烯烃小于0.5wt%,满足后续乙烯裂解装置的进料指标要求。本发明方法中,在开工初期,稳定塔的塔底物料部分或全部通入加氢反应器。本发明方法中,芳烃抽余油的芳烃含量小于2wt%,优选地,小于1wt%,烯烃含量小于6wt%。本发明方法中,芳烃抽余油可以为重整油的芳烃抽余油和/或裂解汽油的芳烃抽余油。本发明方法中,乙烯裂解装置可以采用本领域常规使用的乙烯裂解装置,在常规条件下进行裂解反应生产乙烯。与现有技术相比,本发明的有益技术效果如下:(1)如果跨线阀门稍有内漏,稳定塔的塔底物料烯烃含量就会明显上升,而阀门内漏是较普遍、较难发现、难以完全根治的难题,如果欲彻底解决阀门内漏,需付出较高代价。本发明中,巧妙采用防漏管线设计,结合该装置的实际特点,即稳定塔底循环泵出口压力比跨线压力稍高,引入防漏管线后,防漏管线内液相压力稍高于跨线内压力,在这种状态下,即使跨线上阀门稍有内漏,也是防漏管线内物料泄漏进入加氢反应器或泄漏进入稳定塔,因为防漏管线内物料是经过加氢处理的,物料中的烯烃含量是非常低的,因此哪种内漏均不影响加氢处理后的烯烃含量等性质,巧妙解决了阀门内漏引起的物料烯烃含量就会明显上升的问题。本发明方法构思巧妙,易于实现,维护成本低,有利于装置长周期稳定运转。(2)本发明方法,芳烃抽余油通过液相加氢处理的方法,脱除其中的不饱和烯烃,芳烃抽余油加氢处理过程中,可将芳烃抽余油的烯烃由6wt%左右降低至0.1wt%,然后再将其作为乙烯裂解装置的原料,从而减缓裂解炉管结焦速率,大幅延长清焦周期,从而保证乙烯裂解装置的稳定运行。在开工初期,芳烃抽余油先进入稳定塔进行气液分离处理,然后将稳定塔的塔底物料引入到加氢反应器,进行加氢反应,加氢流出物进入稳定塔进行气液分离处理,这样既可以保证初期产品质量要求,避免产品不合格稳定期,又可以利用稳定塔的塔底再沸器快速升温芳烃抽余油,达到加氢反应的温度要求,从而不需要增加额外的加热器,并克服换热器在开工初期换热不稳定性、升温慢的缺点,而且不影响后续的正常加氢反应过程。(3)对于炼油企业的乙烯裂解装置,只需增加一个加氢反应器即可,不必单独新建一套加氢反应装置,氢气采用自psa单元引入的高纯度氢气,取消了新氢机、循环氢压缩机等动设备,并采用稳定塔取代了分馏塔,可以提高气液混合器的氢气混合效果,提高反应氢分压,有助于加氢脱烯烃反应,同时可以降低稳定塔顶负荷,减少稳定塔投资;抽余油原料与产品稳定塔底生成油换热,省去加热炉。本发明通过上述工艺流程优化,操作条件较为缓和,可实施性强,可以大幅度降低投资和操作费用。(4)本发明加氢反应器采用上流式操作方式,反应器顶部和底部装有金属网和/或金属格栅,可以起到固定催化剂床层,防止催化剂和瓷球跑漏的问题,在此基础上,在催化剂与多层不同粒径的瓷球之间设置有金属网和/或金属格栅,进一步防止催化剂与瓷球出现返混现象,彻底解决了加氢催化剂跑漏以及加氢催化剂和瓷球返混的问题,同时加氢反应器再配合设置有上卸剂口、中卸剂口、下卸剂口,这样分别卸出瓷球和催化剂,避免了卸出瓷球与催化剂的后续分离。(5)本发明方法工艺流程简单,设备投资较低,维护成本较低,有利于下游乙烯装置长周期稳定运转。附图说明图1为本发明的以芳烃抽余油为原料生产乙烯的组合装置示意图;其中:1-缓冲罐,2-第一换热器,3-气液混合器,4-第二换热器,5-加氢反应器,6-稳定塔,7-再沸器,8-乙烯裂解装置,9-psa单元,10-第一阀门,11-第二阀门,12-第三阀门,13-第四阀门,14-第五阀门。具体实施方式下面结合附图和具体实施例对本发明方法进行详细的描述。如图1所示,本发明设置跨线用于将加氢反应器与稳定塔6隔离时,将芳烃抽余油直接引入稳定塔6,跨线为设置在加氢反应器入5口前的管线与稳定塔6进口之间的连通管线;设置防漏管线,防漏管线一端与跨线连通,另一端与稳定塔底6循环泵出口管线连通,防漏管线上设置第一阀门10;跨线与防漏管线连通位置的跨线两侧分别设置有第二阀门12、第三阀门12;正常运转时,将第二阀门11、第三阀门12中的至少一道阀门关闭,优选地将第二阀门11、第三阀门12均关闭,第一阀门10处于打开状态,防漏管线内液相压力高于跨线内压力,优选地高于跨线内液相压力0.1mpa~0.3mpa。由于稳定塔底6循环泵出口压力比跨线压力稍高,即使跨线上阀门稍有内漏,也是防漏管线内物料通过发生泄漏的阀门进入加氢反应器5或进入稳定塔6,因为防漏管线内物料是经过加氢处理的,物料中的烯烃含量是非常低的,因此哪种内漏均不影响加氢处理后的烯烃含量等性质,巧妙解决了阀门内漏引起的物料烯烃含量就会明显上升的问题。芳烃抽余油的加氢反应采用本发明方法的新建装置,在加氢反应器5开始运行时,芳烃抽余油先进入缓冲罐1,关闭第一阀门10、第四阀门13,打开第二阀门11、第三阀门12,芳烃抽余油直接进入稳定塔6,稳定塔6的塔底物料进入再沸器7并加热至反应所需温度,打开第五阀门14,经过再沸器7加热的物料通入第一换热器2,然后经过气液混合器3与psa单元9输送来的高浓度氢气体进行充分混合,混合后再经过第二换热器4,然后自加氢反应器5的底部进入,与加氢精制催化剂接触,在加氢反应的条件下进行加氢反应,使芳烃抽余油中的烯烃饱和,反应结束后,加氢反应流出物进入稳定塔6进行气液分离,塔顶得到碳五以下的轻烃,而塔底物料先期全部引入加氢反应器5,后期可部分通入乙烯裂解装置8,然后进行裂解。当加氢反应器5进入正常工况后,打开第一阀门10、第四阀门13,关闭第二阀门11、第三阀门12和第五阀门14,加氢反应部分进入正常生产工艺流程,这种灵活的工艺流程避免了开工初期产品不合格稳定期。正常生产工艺流程为:芳烃抽余油进入加氢反应器5,在加氢精制催化剂存在、液相状态(芳烃抽余油至少80wt%保持液相状态)的条件下进行加氢反应,加氢反应流出物通入稳定塔6进行气液分离处理,然后塔底物料通入乙烯裂解装置8。经过本发明方法处理的芳烃抽余油,其烯烃含量可降低至0.1wt%,可减缓裂解炉管生焦速率,延长清焦周期,保证乙烯裂解装置8的稳定运行。下面的实施例将对本发明作进一步说明。实验使用催化剂为工业应用的加氢反应催化剂,为抚顺石油化工研究院研制生产的hdo-18加氢催化剂,其理化性质指标见表1。表1催化剂的理化性质指标催化剂编号hdo-18金属组成pt-pd物理性质孔容,ml/g≥0.45比表面积,m2/g≥170耐压强度,n/cm≥90形状圆柱条形实施例1按图1所示新建装置。芳烃抽余油经过进料泵、第一换热器2与氢气在sx型静态混合器中充分混合溶解后,再经第二换热器4换热后,自加氢反应器5的底部进入,与加氢精制催化剂接触,在加氢反应的条件下进行加氢反应,使芳烃抽余油中的烯烃饱和,芳烃抽余油为液相状态。反应结束后,加氢反应流出物进入稳定塔6进行气液分离,塔顶得到碳五以下的轻烃,而塔底物料通入乙烯裂解装置8,然后进行裂解。加氢反应前后芳烃抽余油中的烯烃的含量列于表2。采用本发明方法对加氢装置进行开工处理,开工时,先将芳烃抽余油先进入稳定塔6进行气液分离,稳定塔6的塔底物料(在塔底再沸器7之后引出的稳定塔6底物料的温度为168℃)先全部引入加氢反应器5,后部分引入加氢反应器5,进行加氢反应,在加氢反应流出物进入稳定塔5小时后,停止引入稳定塔6的塔底物料,以及停止直接向稳定塔6通入芳烃抽余油,切换为正常的操作流程。防漏管线内液相压力高于跨线内压力0.2mpa。由表2可见,在加氢反应装置正常操作时,采用该工艺技术可以使芳烃抽余油的烯烃含量降低至0.1wt%,并且整个开工过程产品质量也保持稳定。实施例2按图1所示新建装置。芳烃抽余油经过进料泵、第一换热器2与氢气在sx型静态混合器中充分混合溶解后,再经第二换热器4换热后,自加氢反应器5的底部进入,与加氢精制催化剂接触,在加氢反应的条件下进行加氢反应,使芳烃抽余油中的烯烃饱和,芳烃抽余油为液相状态。反应结束后,加氢反应流出物进入稳定塔6进行气液分离,塔顶得到碳五以下的轻烃,而塔底物料通入乙烯裂解装置8,然后进行裂解。加氢反应前后芳烃抽余油中的烯烃的含量列于表2。采用本发明方法对加氢装置进行开工处理,开工时,先将芳烃抽余油先进入稳定塔6进行气液分离,稳定塔6的塔底物料(在塔底再沸器7之后引出的稳定塔6底物料的温度为173℃)先全部引入加氢反应器5,后部分引入加氢反应器5,进行加氢反应,在加氢反应流出物进入稳定塔5小时后,停止引入稳定塔6的塔底物料,以及停止直接向稳定塔6通入芳烃抽余油,切换为正常的操作流程。防漏管线内液相压力高于跨线内压力0.2mpa。由表2可见,在加氢反应装置正常操作时,采用该工艺技术可以使芳烃抽余油的烯烃含量降低至0.1wt%,并且整个开工过程产品质量也保持稳定。对比例1本对比例1与本发明实施例1的方法基本相同,不同点在于:没有加氢反应过程,重整油的抽余油加热到乙烯裂解所需温度后,直接通入乙烯裂解装置中的蒸汽裂解炉。对比例2按照实施例1的方案,只是在开工时,重整油的抽余油直接进入加氢反应器,直接进行正常操作。在开工过程中,加氢反应生成物有约30小时高于0.5wt%。表2加氢反应的工艺条件及测定结果项目实施例1实施例2对比例1芳烃抽余油原料芳烃含量,wt%0.80.70.8烯烃含量,wt%4.85.04.8加氢反应器的工艺条件反应温度,℃168173-反应压力,mpa1.51.7-液时体积空速,h-15.76.5-油品性质开工初期,加氢反应后的中的烯烃含量,wt%<0.5<0.5-正常操作,加氢反应后的芳烃抽余油中的烯烃含量,wt%0.10.1-乙烯裂解装置炉出口温度,℃840840840停留时间,s0.50.50.5炉出口压力,kpa505050运行周期,天909042乙烯收率,wt%32.733.232.0经过本发明方法处理的芳烃抽余油,产品可以达到如下性质:开工阶段,精制油(加氢反应后的芳烃抽余油)烯烃含量小于0.5wt%,正常操作时,精制油烯烃含量可低至0.1wt%。本发明的系统在运行90天时,乙烯收率下降幅度较小,而对比例1乙烯裂解装置运行周期仅为42天,裂解炉内已经结焦严重。因此,本发明实施例1和2的清焦周期可以为90天,而对比例1的清焦周期为42天。实施例3试验运转过程中,打开跨线上的第二阀门11、第三阀门12,且使第二阀门11、第三阀门12保持很小开度,模拟阀门内漏工况,在不启用防漏管线(不打开第一阀门10)时,加氢反应流出物中的烯烃含量大于0.5wt%,而启用防漏管线(打开第一阀门10)后,加氢反应流出物的烯烃含量稳定,低至0.1wt%。经过计算,在某些工况下,当催化剂性能良好时(产品指标远低于控制指标),如果有10%的内漏,加氢反应流出物中的烯烃含量大于0.5wt%;在催化剂使用后期(加氢反应流出物中的烯烃含量接近0.5wt%),稍有内漏,就会高于0.5wt%。当前第1页12