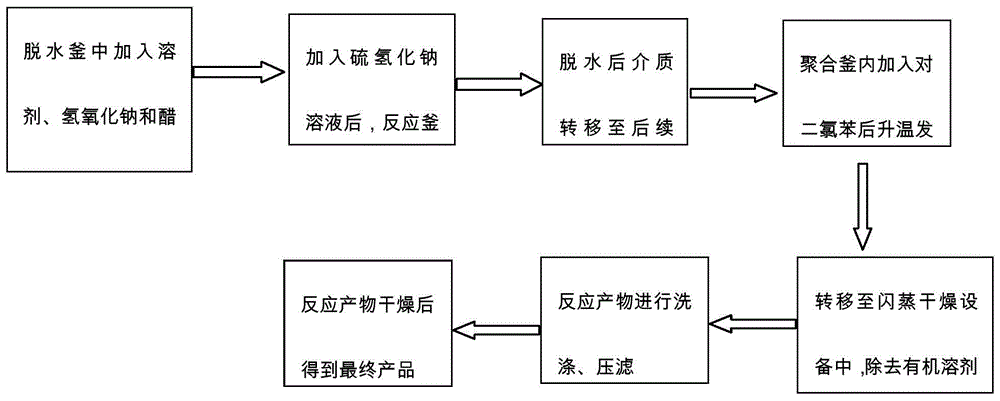
本发明属于化工合成领域,具体而言,涉及一种注塑级聚苯硫醚树脂的工业化生产工艺。
背景技术:
:聚苯硫醚由苯环和硫原子交替排列构成,使得其结构规整,拥有较高的结晶度,同时苯环为提供良好的刚性和耐热性,而硫醚键赋予其一定的柔顺性,因此具有优异的综合性能,被誉为是继聚碳酸酯、聚酯、聚甲醛、尼龙、聚苯醚之后的第6大工程塑料,也是8大宇航材料之一,广泛应用于航天航空、电子、汽车、环保、化工等领域。为探索该材料的合成方法,是各国的研究者们一直在不断努力的追求。目前,国内合成聚苯硫醚树脂的主流工艺仍然停留在以氯化锂为助剂的第一代工艺上。由于氯化锂非常昂贵,回收又很困难,使得生产聚苯硫醚树脂的成本居高不下,难以和国外的聚苯硫醚产品竞争。因此仍然需要开发新的更为经济、环保的注塑级聚苯硫醚的生产工艺。技术实现要素:针对上述现有技术存在的问题,根据本发明的一个方面,本发明的一个目的是提供一种注塑级聚苯硫醚树脂的工业化生产新工艺,该工艺中采用便宜的有机酸盐作为催化剂制备聚苯硫醚,更为经济环保,同时产品中残留催化剂非常少,无需复杂的后处理步骤。根据本发明的生产工艺的特点是采用硫氢化钠与二卤代芳香化合物为原料,在极性溶剂中采用有机酸盐单一催化体系,通过溶液缩聚反应,制备高性能注塑级聚苯硫醚树脂。为了实现本发明的上述目的,根据本发明的所述注塑级聚苯硫醚树脂的中试级别的生产工艺包括以下步骤:1)将10-50重量份的乙酸酐,100-200重量份的氢氧化钠和300-600重量份的有机溶剂由进料泵加入到脱水反应釜中,在氮气保护和搅拌条件下,将温度逐渐升高至100-150℃,发生脱水及酸碱中和反应生成醋酸钠,然后再向反应釜中加入100-200重量份的硫氢化钠,将温度控制在200-210℃进行脱水反应1.5至3h,得到脱水后的硫氢化钠溶液;2)将上述硫氢化钠溶液从脱水反应釜转移到后续的聚合反应釜中,加入100-200重量份的二卤代苯,将聚合反应釜升温至265-280℃,搅拌条件下保持1h进行聚合反应,然后在相同温度和压力下将物料转移至闪蒸干燥设备中,反应产物直接从高温高压状态闪蒸到接近常压,有机溶剂和水闪蒸出来,得到粗产物;3)将步骤2)中得到的粗产物经去离子水多次洗涤和压滤;4)将步骤3)中得到的反应产物置于温度120-130℃的烘箱内干燥3h以上,即获得注塑级聚苯硫醚树脂。优选地,步骤1)中所述有机溶剂为氮甲基吡咯烷酮(nmp)。优选地,步骤1)中所述乙酸酐用量为20-40重量份。优选地,步骤1)中所述氢氧化钠用量为120-180重量份。优选地,步骤1)中所述有机溶剂用量为400-500重量份。优选地,步骤1)中所述硫氢化钠用量为150-200重量份。进一步优选地,步骤1)中所述乙酸酐用量为20-30重量份。进一步优选地,步骤1)中所述氢氧化钠用量为140-150重量份。进一步优选地,步骤1)中所述有机溶剂用量为440-460重量份。进一步优选地,步骤1)中所述硫氢化钠用量为170-180重量份。优选地,步骤2)中所述二卤代苯为对二氯苯。优选地,步骤2)中所述二卤代苯用量为150-200重量份。进一步优选地,步骤2)中所述二卤代苯用量为190-200重量份。根据本发明的另一个方面,本发明的另一个目的是提供所述注塑级聚苯硫醚树脂的生产工艺的生产装置,所述装置包括:脱水反应釜,用于进行脱水反应,所述脱水反应釜外部包裹油浴加热套用于加热,内部设置搅拌器,顶部设有出气口,用于将水和少量的溶剂氮甲基吡咯烷酮及硫化氢从顶部蒸出;聚合反应釜,用于进行聚合反应,接收来自所述脱水反应釜的产物和对二氯苯作为反应物,所述聚合反应釜外部包裹油浴加热套用于加热,内部设置搅拌器,底部设置有排出管线,用于将反应浆料送至后续闪蒸干燥机;冷凝罐,连接所述聚合反应釜的顶部的出气口,用于接收来自所述脱水反应釜和所述聚合反应釜的水蒸气和氮气等气体,以便冷凝。闪蒸干燥机,用于通过重力和压差接收所述聚合反应釜内的高温物料,通过闪蒸过程除去水和nmp,留下pps聚合物、乙酸钠和盐(nacl),所述闪蒸干燥机外部包裹油浴加热套用于加热,内部设置搅拌器,顶部设有气相溶剂出气口,底部设置有排出管线,用于将反应粗产物送至后续筛分、洗涤系统。优选地,所述脱水反应釜的产物不经过其他处理,直接导入所述聚合反应釜中。本发明具有如下优点:1.本发明采用硫氢化钠与二卤代芳香化合物(对二氯苯)合成聚苯硫醚树脂,原料价廉易得、产率较高、产品质量稳定,适合工业化大规模生产。2.生产过程采用了单一的有机酸盐催化体系,相对于复合催化体系,其溶剂较易回收,产品成本低,具有安全性好、环保等优点。3.采用本发明方法合成的聚苯硫醚具有熔点高、易加工和耐高温的优点。4.本发明的生产过程操作简单,反应条件易于控制,可重复性好,能耗合理。附图说明为了更清楚地说明本发明具体实施方式或现有技术中的技术方案,下面将对具体实施方式或现有技术描述中所需要使用的附图作简单的介绍,显而易见地,下面描述中的附图是本发明的一些实施方式,对本领域普通技术人员而言,在不付出创造性劳动的前提下,还可以根据这些附图获得其他的附图。图1为根据本发明的所述注塑级聚苯硫醚树脂的生产工艺的流程框图;图2为根据本发明的所述注塑级聚苯硫醚树脂的生产工艺的生产装置的结构示意图;图3为实施例1产品的dsc分析图图4为实施例1产品的tga分析图图5为实施例2产品的dsc分析图图6为实施例2产品的tga分析图图7为实施例3产品的dsc分析图图8为实施例3产品的tga分析图具体实施方式在下文中,将参照附图详细地描述本公开的优选的实施方式。在描述之前,应当了解在说明书和所附权利要求中使用的术语,并不应解释为局限于一般及辞典意义,而是应当基于允许发明人为最好的解释而适当定义术语的原则,基于对应于本发明技术层面的意义及概念进行解释。因此,在此的描述仅为说明目的的优选实施例,而并非是意指限制本发明的范围,因而应当了解的是,在不偏离本发明的精神和范围下可以做出其他等同实施和修改。为了阐明本发明,在附图中省略了与描述无关的部分,并且在整个说明书中,相同或相似的部件由相同的附图标记表示。另外,为了便于说明,任意地示出了附图中所示的每个部件的尺寸和厚度,因此本发明不必限于附图中所示的那些。在整个说明书中,当提到某个元件“连接”到另一个元件时,它不仅包括“直接连接”,还包括其他构件之间的“间接连接”。另外,当提到某个元件“包括”某个部件时,这意味着该元件可以进一步包括其他部件而不是排除其他部件,除非相反地明确描述。根据本发明的所述注塑级聚苯硫醚树脂的中试级别的生产工艺的包括以下步骤:1)将10-50重量份的乙酸酐,100-200重量份的氢氧化钠和300-600重量份的有机溶剂由进料泵加入到脱水反应釜中,在氮气保护和搅拌条件下,将温度逐渐升高100-150℃,发生脱水及酸碱中和反应生成醋酸钠,然后再向反应釜中加入100-200重量份的硫氢化钠,将温度控制在200-210℃进行脱水反应1.5至3h,得到脱水后的硫氢化钠溶液;2)将上述硫氢化钠溶液从脱水反应釜转移到后续的聚合反应釜中,加入100-200重量份的二卤代苯,将聚合反应釜升温至265-280℃,搅拌条件下保持1h进行聚合反应,然后在相同温度和压力下将物料转移至闪蒸干燥设备中,反应产物直接从高温高压状态闪蒸到接近常压,有机溶剂和水闪蒸出来,得到粗产物;3)将步骤2)中得到的粗产物经去离子水多次洗涤和压滤后;4)将步骤3)中得到的反应产物置于温度120-130℃的烘箱内干燥3h以上,即获得聚苯硫醚树脂。其中,优选地,步骤1)中所述乙酸酐用量为20-40重量份,更优选为20-30重量份。优选地,步骤1)中所述氢氧化钠用量为120-180重量份,更优选为140-150重量份。优选地,步骤1)中所述有机溶剂用量为400-500重量份,更优选为440-460重量份。优选地,步骤1)中所述硫氢化钠用量为150-200重量份,更优选为170-180重量份。当上述反应物的用量控制在上述范围内时,可以实现最优的反应效率,并且产物中杂质含量可以降到最低。其中可以看到,氢氧化钠用量与乙酸酐用量的比例要高于乙酸钠的摩尔原子比。如果氢氧化钠不足,则后续反应不能顺利进行;如果乙酸酐用量过大则,则产物中杂质太多,后续洗涤等处理较为繁琐,增加成本。同样地,为了达到反应的最优化,优选地,步骤2)中所述二卤代苯用量为150-200重量份,更优选为190-200重量份。当在此范围内时,聚合反应最为经济,二卤代苯用量过多或过少都会造成反应效率的下降。优选地,步骤2)中待在265-280℃下的聚合反应完成后需要在相同温度和压力下将物料转移至闪蒸干燥设备中,反应产物直接从高温高压状态闪蒸到接近常压,有机溶剂和水闪蒸出来,得到粗产物。所述闪蒸过程在闪蒸干燥机中进行,通过重力和压差将所述聚合反应釜内的高温物料送入闪蒸干燥机,在闪蒸干燥器中除去水和nmp,留下pps聚合物、乙酸钠和盐(nacl)。高温反应混合物从高反应压力“闪蒸”到大约常压的闪蒸带式干燥器中。随着额外热量加入,水和大多数nmp从聚合物中蒸发。最终的结果是,所有不同分子量的聚合物从水和有机相中被捕捉,并均匀分布。从闪蒸干燥机出来的湿固体再送至后续洗涤纯化系统。根据本发明的注塑级聚苯硫醚树脂的工业化生产工艺设计能力为生产80吨/年聚苯硫醚产品,反应循环时间为12小时。反应部分由所述脱水反应釜、所述聚合反应釜和所述闪蒸干燥机组成,容量均为1.5m3。在脱水反应釜中,水和少量的溶剂氮甲基吡咯烷酮及硫化氢从顶部蒸出。用做氮封的氮气,在反应釜加注原料过程中在反应器顶部排出,脱水后原料转移至后续聚合反应釜中。在聚合反应釜中,热反应产物直接从高温高压状态闪蒸到接近常压。溶剂氮甲基吡咯烷酮和水从容器中闪蒸出来,然后将粗产物聚苯硫醚送至后续洗涤、压滤系统。以下实施例仅是作为本发明的实施方案的例子列举,并不对本发明构成任何限制,本领域技术人员可以理解在不偏离本发明的实质和构思的范围内的修改均落入本发明的保护范围。除非特别说明,以下实施例中使用的试剂和仪器均为市售可得产品。各种物质的性能测试如下进行,所述方法均为本领域常规检测方法:1、通过调控反应物浓度、物料配比及反应温度,制备不同熔流率的聚苯硫醚,采用熔体指数仪测定聚苯硫醚的熔融指数(温度:316℃,载荷:5kg)。2、采用差示扫描量热分析方法(dsc)测试聚苯硫醚树脂的熔点。3、采用热失重分析方法(tga)测试聚苯硫醚树脂的加热重量损失。4、采用马弗炉燃烧法测试聚苯硫醚树脂的灰分。5、采用加热减量法测试聚苯硫醚树脂的挥发度。起始原料的种类和纯度如下所示:种类纯度硫氢化钠43.12%对二氯苯99.99%氮甲基吡咯烷酮99.86%氢氧化钠49.97%乙酸酐99.34%实施例1将20kg乙酸酐,142kg氢氧化钠和445kg有机溶剂加入脱水反应釜中,在氮气保护下,将温度逐渐升高,发生脱水及酸碱中和反应生成醋酸钠。再在反应釜中加入172kg硫氢化钠,于温度200-210℃脱水反应2h,得到脱水后的溶液。将上述溶液从脱水反应釜转移到后续的聚合反应釜中,加入192kg对二氯苯,将反应釜升温至260-270℃,然后在温度260-270℃下保持1h后,将聚合釜内物料转移至后续闪蒸干燥机内。将干燥后的粗产物经去离子水多次洗涤和压滤后,于温度115-130℃烘箱内干燥3h,即获得注塑级聚苯硫醚树脂。所得产品粒径约为0.2至2mm,产率为95.6%,熔体指数为582g/10min(按照国标gb/t3682-2000测量)。dsc分析见图3所示:其熔点为276.2℃。热失重分析见图4所示:300℃下的加热重量损失为0.16%。550℃的灰分为0.39%(按照国标gb/t9345.1-2008测量)。150℃下挥发度为0.652%。具有较好的热性能。实施例2将22kg乙酸酐,145kg氢氧化钠和450kg有机溶剂加入脱水反应釜中,在氮气保护下,将温度逐渐升高,发生脱水及酸碱中和反应生成醋酸钠。再在反应釜中加入178kg硫氢化钠,于温度200-210℃脱水反应2h,得到脱水后的溶液。将上述溶液从脱水反应釜转移到后续的聚合反应釜中,加入195kg对二氯苯,将反应釜升温至260-270℃,然后在温度260-270℃下保持1h后,将聚合釜内物料转移至后续闪蒸干燥机内。将干燥后的粗产物经去离子水多次洗涤和压滤后,于温度115-130℃烘箱内干燥3h,即获得注塑级聚苯硫醚树脂。所得产品粒径约为0.2至2mm,产率为96.7%,熔体指数为595g/10min(按照国标gb/t3682-2000测量)。dsc分析见图5所示:其熔点为276.1℃。热失重分析见图6所示:300℃下的加热重量损失为0.18%。550℃的灰分为0.39%(按照国标gb/t9345.1-2008测量)。150℃下挥发度为0.436%。具有较好的热性能。实施例3将26kg乙酸酐,148kg氢氧化钠和460kg有机溶剂加入脱水反应釜中,在氮气保护下,将温度逐渐升高,发生脱水及酸碱中和反应生成醋酸钠。再在反应釜中加入180kg硫氢化钠,于温度200-210℃脱水反应2h,得到脱水后的溶液。将上述溶液从脱水反应釜转移到后续的聚合反应釜中,加入198kg对二氯苯,将反应釜升温至260-270℃,然后在温度260-270℃下保持1h后,将聚合釜内物料转移至后续闪蒸干燥机内。将干燥后的粗产物经去离子水多次洗涤和压滤后,于温度115-130℃烘箱内干燥3h,即获得注塑级聚苯硫醚树脂。所得产品粒径约为0.2至2mm,产率为95.8%,熔体指数为703g/10min(按照国标gb/t3682-2000测量)。dsc分析见图7所示:其熔点为277.1℃。热失重分析见图8所示:300℃下的加热重量损失为0.19%。550℃的灰分为0.39%(按照国标gb/t9345.1-2008测量)。150℃下挥发度为0.56%。具有较好的热性能。与现有文献采用常规的无机盐例如氯化锂等作为催化剂相比,通过上述实施例证明本发明的生产工艺可以实现了工业规模级别的高效生产,同时由于原料廉价易得,工艺流程设计简洁,因此克服了产品较难纯化、催化剂回收困难,且溶剂回收率低,使得其生产成本较高等现实问题。当前第1页12