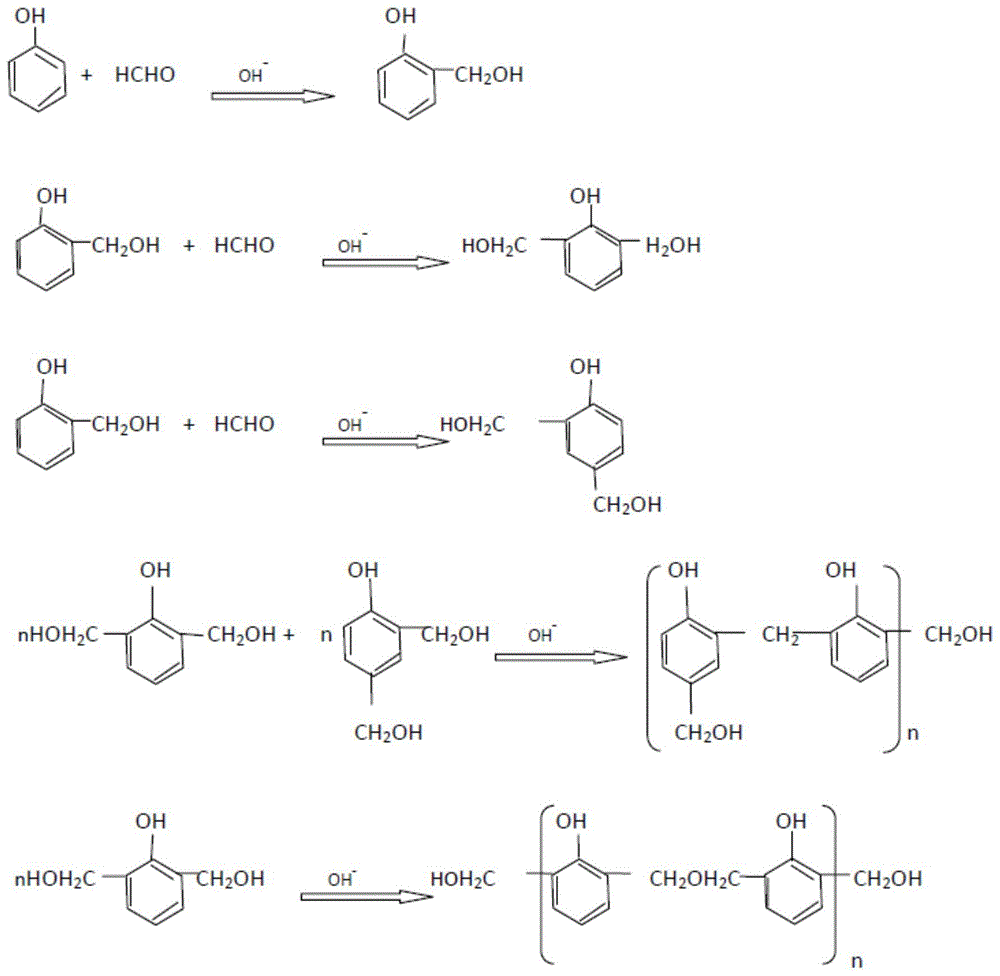
本申请涉及锦纶帘子布专用改性酚醛树脂的制备领域,具体涉及一种锦纶帘子布专用改性酚醛树脂的生产方法。
背景技术:
:橡胶骨架材料是含骨架材料复合橡胶制品中受力的主要部件,同时也对这类橡胶制品在使用中形状的稳定起了重要的作用。如轮胎、胶带、部分胶管、密封及减震橡胶制品就是由橡胶弹性体部件与高模量高强度的骨架材料复合而成的,这些橡胶制品对其骨架材料的要求各异,所以就有了不同材质不同结构的骨架材料。不同的材质主要有天然纤维、合成纤维、金属材料。不同的结构主要有线绳、帘布、帆布、无纺布等。骨架材料的表面处理及与橡胶基质的黏合也是十分重要的问题。橡胶材料是一种拥有高弹性、大变形、低模量的高分子材料。如充足的弹性可以吸收冲击震动、提供较高的耐磨性、摩擦系数和优异的附着性等。但是在大多数情况下纯橡胶制品是不能满足实际使用需要的,橡胶制品在大多数情况下都要承受较大的负荷,如轮胎、输送带等这些橡胶制品就需要使用纤维、钢丝等骨架材料来复合,从而使得橡胶材料得到了更为广泛的应用。橡胶与其骨架材料牢固地结合,不仅可以保护骨架材料,同时骨架材料的增强作用也得到了更充分的发挥。骨架材料的作用是承受来自橡胶制品内部和外部的作用力,提高橡胶制品的强度,并限制其变形量。它在很大程度上决定着橡胶制品的使用性能和使用价值,因此绝大多数的橡胶制品,如轮胎、传输带等均需采用骨架材料作增强材料。橡胶制品骨架材料的分类和作用:(1)棉纤维,棉纤维基本性能是强力较低,与橡胶的黏合性好;(2)人造丝纤维,其中的高强度黏胶纤维是橡胶工业常用的。人造丝干强度较高,但湿强度较低;(3)维纶纤维,维纶纤维强度高,耐磨性、耐光性好,但其耐湿热性不好;(4)聚酰胺纤维,或称尼龙,也称锦纶,该纤维强度较高,断裂伸长率也较高,弹性好,屈挠性,耐磨性优于其他纤维,但其热稳定性差,目前已大量使用在斜交轮胎等制品中;(5)聚酯纤维,聚酯纤维合了尼龙的强力与伸长特性以及人造丝的模量特性,所以适用于很多用途,如半钢丝子午线轮胎中胎体骨架基本选用聚酯帘布;(6)芳族聚酰胺纤维,或称芳纶,芳族聚酰胺纤维强度高、延伸率低、耐热性好,有“人造钢丝”之称,但其价格较高,目前已在轮胎和高强力输送带等制品中使用;(7)玻璃纤维,玻璃纤维有较高的模量和耐热性,但耐屈挠性和与橡胶的黏合性均较差;(8)钢丝,钢丝帘线、钢丝绳及普通单根钢丝都具有极高的强度和模量,表面镀铜或镀锌的钢丝已很好的解决了与橡胶的黏合问题,在轮胎、钢丝绳输送带、钢编胶管等制品中已大量使用。钢丝的优点是耐热性和导热性都极好。初始弹性模量高。但比重大,耐疲劳性能、与橡胶的粘着性能及耐化学腐蚀性能很差。橡胶制品对骨架材料的基本要求:(1)强度、模量和回弹性要高;(2)耐热性能好;(3)耐疲劳性好;(4)尺寸稳定性好;(5)和橡胶粘着性好(表面浸胶处理);(6)价格低廉;(7)相对密度小,有利于轻量化;(8)8.有良好的耐腐蚀性和阻燃性能。尼龙是聚酰胺纤维(锦纶)的一种说法,可制成长纤或短纤。聚酰胺(pa,俗称尼龙)是最先开发用于纤维的树脂,于1939年实现工业化。20世纪50年代开始开发和生产注塑制品,以取代金属满足下游工业制品轻量化、降低成本的要求。聚酰胺主链上含有许多重复的酰胺基,用作塑料时称尼龙,用作合成纤维时我们称为锦纶,锦纶是聚酰胺纤维的商品名称,又称耐纶(nylon)。英文名称polyamide(简称pa),其基本组成物质是通过酰胺键-[nhco]-连接起来的脂肪族聚酰胺。聚酰胺可由二元胺和二元酸制取,也可以用ω-氨基酸或环内酰胺来合成。根据二元胺和二元酸或氨基酸中含有碳原子数的不同,可制得多种不同的聚酰胺,聚酰胺品种多达几十种,其中以聚酰胺-6和聚酰胺-66应用最广泛。聚酰胺-6、聚酰胺-66的链节结构分别为[nh(ch2)5co]、[nh(ch2)6nhco(ch2)4co]。聚酰胺-6和聚酰胺-66主要用于纺制合成纤维,称为锦纶-6和锦纶-66。其具有良好的综合性能,包括力学性能、耐热性、耐磨损性、耐化学药品性和自润滑性,且摩擦系数低,有一定的阻燃性,易于加工。锦纶6和锦纶66纤维的强度为4~5.3cn/dtex,高强锦纶可达7.9cn/dtex以上,伸长率18%~45%,在10%伸长时的弹性回复率在90%以上。据测定,锦纶纤维的耐磨为棉纤维的20倍、羊毛的20倍、粘胶的50倍。耐疲劳性能居各种纤维之首。因此被认为是很有发展前途的纤维材料。工业上锦纶大量用来制造帘子线、工业用布、缆绳、传送带、帐篷、渔网等。在国防上主要用作降落伞及其他军用织物。锦纶帘子布断裂强度高、抗冲击性能和耐疲劳性能好,被大量用在子午线轮胎的冠带层及斜交轮胎的胎体和缓冲层,尤其是越野轮胎、大中型载重轮胎、航空轮胎、工程机械轮胎、工业车辆轮胎、农业车辆轮胎等使用条件比较苛刻的轮胎中,锦纶帘子布作为橡胶骨架材料还用在轮胎小部件上,比如肩带条、胎圈芯包布、胎圈包布、胎圈加强层用布等方面。不同骨架材料和橡胶之间的粘合力可以通过下述三种途径获得:机械粘合力、物理粘合力、化学粘合力。(1)机械粘合力在粘合力不高的场合,或采用机织、经编的网格布作骨架材料,以及胶管中采用螺旋缠绕或针织的结构,才仅仅依靠机械粘合力。纺织骨架材料纱线埋压在橡胶中,并被橡胶所包围,上下层的橡胶可以相互连接,其粘合力有时实际依靠橡胶之间的粘合力。(2)物理粘合力物理粘合力由材料之间的相互作用获得:偶极之间的结合力、分子之间的引力、氢键的结合力。当采用粘胶或锦纶作为骨架材料时,其物理粘合力是总粘合力的25%。由于涤纶和芳纶的分子中缺乏活性基团,其物理粘合力则是相当低的。(3)化学粘合力骨架材料采用粘合剂处理后,如:rfl乳胶液(苯二酚r、甲醛f、乳胶l),可以改善骨架材料的物理和化学粘合力。主要是骨架材料中反应基团如羟、羧、胺端基与rfl树脂发生了化学反应,反应程度取决于这些反应基团的活性。锦纶帘子布是光滑的表面,与橡胶粘合力较差,因此它不适合跟橡胶直接粘合在一起,为了提高锦纶线与橡胶的粘结程度,避免内部脱层而导致制品损坏。锦纶绳织物必须预先浸胶才能获得良好的粘合效果。纤维骨架材料和橡胶材料的粘合是在硫化时发生的,主要利用间苯二酚给予体和甲醛给予体在硫化温度下,产生的聚合反应,形成的树脂进行粘合的。因此硫化温度和时间会影响粘合力。硫化温度提高以及硫化时间的延长可以提高粘合力;直接粘合体系的粘合力比rfl浸胶骨架材料的低许多,但延长反应时间,其粘合力可大幅度提高,但依然不到浸胶骨架材料的一半。为了保证获得较高的粘合力,通常采用浸胶rfl相结合。早期的胶乳浸渍体系中的树脂是帘子布浸胶厂由间苯二酚与甲醛在碱性环境中25±1℃缩合而成的。由于间苯二酚与甲醛在碱性条件下剧烈反应,因此需严格控制反应温度和溶液ph值,反应时间一般需要6-8小时,这就要求帘子布浸胶厂严格控制生产工艺;一般会出现两种情况,一种是树脂反应程度不够,树脂粘合力低,另一种是树脂反应过度,甚至造成树脂报废(生产大量胶渣),严重影响树脂性能。鉴于以上原因,发明了预缩合树脂;由专业树脂生产厂商进行合成,从而保证树脂质量稳定,这种树脂可长时间保存。不会发生交联。纤维骨架材料制造商在使用前以浓氨水、软化水或氢氧化钠溶液稀释并补加一定量的甲醛,即可在很短时间内生成网状结构的树脂。纤维骨架材料制造厂采用这种方法可简化配制工艺,保证产品性能稳定。技术实现要素:本申请提供一种锦纶帘子布专用改性酚醛树脂的生产方法,提高锦纶纤维与橡胶的粘结性能,实现锦纶纤维作为骨架材料制品的应用,充分发挥锦纶纤维的性能优势。一种锦纶帘子布专用改性酚醛树脂的生产方法,各原料按配比计量,包括:(1)先加入预热熔融的苯酚,再加入甲醛,混合均匀加入改性剂1,充分溶解后,加入碱性催化剂,20-30分钟内升温至50~55℃,恒温反应0.8~1.2小时;所述改性剂1为亚硫酸氢钠、亚硫酸钠、亚磷酸钠中的至少一种;(2)步骤(1)中所得反应体系中加入改性剂2,20-30分钟内升温至100±1℃,恒温反应至第一预设粘度值;所述改性剂2为对-叔丁基苯酚、对-特苄基苯酚和对-特辛基苯酚中的至少一种;(3)10-15分钟内降温至75~80℃加入间苯二酚,20~30分钟内升温至100±1℃,恒温反应至达到第二预设粘度值;(4)10-15分钟内降温至80~85℃,加入软化水,降温至60~65℃后加入溶剂,降温至40℃或以下即得所述锦纶帘子布专用改性酚醛树脂。以下还提供了若干可选方式,但并不作为对上述总体方案的额外限定,仅仅是进一步的增补或优选,在没有技术或逻辑矛盾的前提下,各可选方式可单独针对上述总体方案进行组合,还可以是多个可选方式之间进行组合。可选的,所述改性剂1的添加量与苯酚的质量比为0.1~0.25:1;所述改性剂2的添加量与苯酚的质量比为0.2~0.375:1。进一步地,所述改性剂1的添加量与苯酚的质量比为0.125~0.185:1;所述改性剂2的添加量与苯酚的质量比为0.2~0.375:1。更进一步地,所述改性剂1的添加量与苯酚的质量比为0.15:1;所述改性剂2的添加量与苯酚的质量比为0.25~0.375:1。更进一步地,所述改性剂1的添加量与苯酚的质量比为0.15:1;所述改性剂2的添加量与苯酚的质量比为0.375:1。可选的,改性剂1和改性剂2的组合为:所述改性剂1为亚硫酸钠;所述改性剂2为对-叔丁基苯酚。改性剂1的作用:可防止纤维局部氧化而影响纤维强度,人造纤维的稳定剂;可防止反应过程中半成品的氧化。对-叔丁基苯酚甲醛树脂是各种合成胶和天然胶的粘合增进剂,特别是对丁苯、丁腈、氯丁胶效果更好,主要用于合成胶用量大且要求加工粘合性能好的橡胶制品,如轮胎、输送带、胶管、胶辊等橡胶制品,尤其可以有效解决胶料粘性问题,提高橡胶制品成型质量及成品性能,还兼具增塑剂和软化剂作用。本申请结合间苯二酚甲醛树脂的耐热性好和高粘结强度特性和对-叔丁基苯酚甲醛树脂的拉伸强度高和耐老化性能好的特性,通过对酚醛树脂进行双改性,提高锦纶纤维与橡胶的粘结性能,实现锦纶纤维为骨架材料制品的应用,充分发挥锦纶纤维的性能优势。反应机理机理:苯酚与甲醛的反应机理如图1所示;对叔丁基苯酚(改性剂1)与甲醛的反应机理如图2所示;苯酚与甲醛反应产物与间苯二酚的反应机理如图3所示;对叔丁基苯酚(改性剂1)与甲醛反应产物与间苯二酚的反应机理如图4所示。进一步地,本申请还通过控制合成树脂所需原材料配比、反应条件等因素,通过粘度的控制,间接控制树脂分子量,进一步优化本树脂的浸润性和粘结力。可选的,以重量份计,各原料的配比如下:可选的,以重量份计,各原料的配比如下:可选的,所述碱性催化剂为氢氧化钠、氢氧化钾和碳酸钠中的至少一种。可选的,所述溶剂为甲醇、乙二醇、二乙二醇和丙三醇氨水中的至少一种。可选的,所述第一预设粘度值为600~700mpa.s/25℃。可选的,所述预设粘度值2为180~200mpa.s/25℃。本申请还提供一种如要求所述生产方法制备得到的锦纶帘子布专用改性酚醛树脂。与现有技术相比,本申请至少具有如下有益效果之一:(1)本申请将传统的锦纶帘子布用酚醛树脂生产工艺作重大改进,同时根据实际应用的需要,对其进行化学改性,并采用灵活的方法,通过过程控制来实现树脂最优化和工艺过程的可重现性;(2)本申请结合间苯二酚甲醛树脂的耐热性好和高粘结强度特性和对-叔丁基苯酚甲醛树脂的拉伸强度高和耐老化性能好的特性,通过对酚醛树脂进行双改性,提高锦纶纤维与橡胶的粘结性能,实现锦纶纤维为骨架材料制品的应用,充分发挥锦纶纤维的性能优势。附图说明图1为苯酚与甲醛的反应机理图。图2为对叔丁基苯酚(改性剂1)与甲醛的反应机理图。图3为苯酚与甲醛反应产物与间苯二酚的反应机理图。图4为对叔丁基苯酚(改性剂1)与甲醛反应产物与间苯二酚的反应机理图。图5为1#样品粘合剥离后图片。图6为2#样品粘合剥离后图片。图7为3#样品粘合剥离后图片。图8为4#样品粘合剥离后图片。图9为5#样品粘合剥离后图片。具体实施方式下面将结合本申请实施例中的附图,对本申请实施例中的技术方案进行清楚、完整地描述,显然,所描述的实施例仅仅是本申请一部分实施例,而不是全部的实施例。基于本申请中的实施例,本领域普通技术人员在没有做出创造性劳动前提下所获得的所有其他实施例,都属于本申请保护的范围。除非另有定义,本文所使用的所有的技术和科学术语与属于本申请的
技术领域:
的技术人员通常理解的含义相同。本文中在本申请的说明书中所使用的术语只是为了描述具体的实施例的目的,不是旨在于限制本申请。通用浸渍液实施方案对比例1间苯二酚、甲醛树脂(rf)合成工艺:反应釜加入500g软化水,30g间苯二酚充分溶解后,加入45g甲醛(37%),搅拌10分钟,分批加入2g氢氧化钠溶液(50%),25~27℃恒温反应5小时。降温备用。本申请实施方案(prf):实施例1:先将经准确计量的熔融的苯酚800kg投入反应釜内,接着加入甲醛溶液(37%)800kg,加入亚硫酸钠120kg,充分溶解后,加入碳酸钠40kg,20~30分钟内升温至50~55℃,进行恒温反应1小时,然后加入200kg对-叔丁基苯酚,20~30分钟内升温至100±1℃,进行恒温反应,控制树脂粘度为600~700mpa.s/25℃,10-15分钟降温至75~80℃加入间苯二酚2000kg,20~30分钟内升温至100±1℃,进行恒温反应,控制树脂粘度为180~200mpa.s/25℃;10-15分钟降温至80~85℃后加入软化水1000kg,10-15分钟降温至60~65℃,分别加入甲醇500kg,二乙二醇100kg,降温至40℃以下,即得所述锦纶帘子布专用改性酚醛树脂(prf树脂溶液)。实施例2:先将经准确计量的熔融的苯酚800kg投入反应釜内,接着加入甲醛溶液(37%)850kg,加入亚硫酸钠120kg,充分溶解后,加入碳酸钠40kg,20~30分钟内升温至50~55℃,进行恒温反应1小时,然后加入300kg对-叔丁基苯酚,20~30分钟内升温至100±1℃,进行恒温反应,控制树脂粘度为600~700mpa.s/25℃,10-15分钟降温至75~80℃加入间苯二酚2000kg,20~30分钟内升温至100±1℃,进行恒温反应,控制树脂粘度为180~200mpa.s/25℃;10-15分钟降温至80~85℃后加入软化水1100kg,10-15分钟降温至60~65℃,分别加入甲醇500kg,二乙二醇100kg,降温至40℃以下,即得所述锦纶帘子布专用改性酚醛树脂(prf树脂溶液)。实施例3:先将经准确计量的熔融的苯酚800kg投入反应釜内,接着加入甲醛溶液(37%)900kg,加入亚硫酸钠120kg,充分溶解后,加入碳酸钠40kg,20~30分钟内升温至50~55℃,进行恒温反应1小时,然后加入400kg对-叔丁基苯酚,20~30分钟内升温至100±1℃,进行恒温反应,控制树脂粘度为600~700mpa.s/25℃,10-15分钟降温至75~80℃加入间苯二酚2000kg,20~30分钟内升温至100±1℃,进行恒温反应,控制树脂粘度为180~200mpa.s/25℃;10-15分钟降温至80~85℃后加入软化水1100kg,10-15分钟至60~65℃,分别加入甲醇500kg,二乙二醇100kg,降温至40℃以下,即得所述锦纶帘子布专用改性酚醛树脂(prf树脂溶液)。实施例4(未改性):先将经准确计量的熔融的苯酚800kg投入反应釜内,接着加入甲醛溶液(37%)800kg,加入碳酸钠40kg,20~30分钟内升温至50~55℃,进行恒温反应1小时,20~30分钟内升温至100±1℃,进行恒温反应,控制树脂粘度为600~700mpa.s/25℃,10-15分钟降温至75~80℃加入间苯二酚2000kg,20~30分钟内升温至100±1℃,进行恒温反应,控制树脂粘度为180~200mpa.s/25℃;10-15分钟降温至80~85℃后加入软化水1000kg,10-15分钟降温至60~65℃,分别加入甲醇500kg,二乙二醇100kg,降温至40℃以下,即得传统锦纶帘子布用酚醛树脂(prf树脂溶液)。以上四个实施例树脂产品与通用产品作实验数据分析,其结果如下:树脂指标检测报告如表1所示:表1通过对表1数据的分析对比,实施例1~4的树脂检测指标相差不大,都在许可范围之内。产品性能测试一、h抽出力测试(一)帘线浸渍液的配制1、(1)1#prf液的配制:配方:各组分数量以表2为准。配制工艺:加入软水,开启搅拌,加入氢氧化钠溶液,搅拌20分钟,加入prf树脂溶液(实施例1),搅拌30分钟,加入甲醛(37.0%),25~30℃熟化2小时,备用。表2(2)1#浸渍液的配制:配方:各组分数量以表3为准。配制工艺:加入丁吡胶乳,开启搅拌,加入配制好的prf液,搅拌30分钟,加入甲醛(37.0%),25~30℃熟化8小时,备用。表32、(1)2#prf液的配制:配方:各组分数量以表4为准。配制工艺:加入软水,开启搅拌,加入氢氧化钠溶液,搅拌20分钟,加入prf树脂溶液(实施例2),搅拌30分钟,加入甲醛(37.0%),25~30℃熟化2小时,备用。表4(2)2#浸渍液的配制:配方:各组分数量以表5为准。配制工艺:加入丁吡胶乳,开启搅拌,加入配制好的prf液,搅拌30分钟,加入甲醛(37.0%),25~30℃熟化8小时,备用。表5注:*为[2(1)]配制的prf树脂溶液。3、(1)3#prf液的配制:配方:各组分数量以表6为准。配制工艺:加入软水,开启搅拌,加入氢氧化钠溶液,搅拌20分钟,加入prf树脂溶液(实施例3),搅拌30分钟,加入甲醛(37.0%),25~30℃熟化2小时,备用。表6(2)3#浸渍液的配制:配方:各组分数量以表7为准。配制工艺:加入丁吡胶乳,开启搅拌,加入配制好的prf液,搅拌30分钟,加入甲醛(37.0%),25~30℃熟化8小时,备用。表7注:*为[3(1)]配制的prf树脂溶液。4、(1)4#prf液的配制:配方:各组分数量以表8为准。配制工艺:加入软水、氢氧化钠溶液,搅拌20分钟,加入prf树脂溶液(实施例4),搅拌30分钟,加入甲醛(37.0%),25~30℃熟化2小时,备用。表8(2)4#浸渍液的配制:配方:各组分数量以表9为准。配制工艺:加入丁吡胶乳,开启搅拌,加入配制好的prf液,搅拌30分钟,加入甲醛(37.0%),25~30℃熟化8小时,备用。表9注:*为[4(1)]配制的prf树脂溶液。5、(1)5#rf液的配制:配方:各组分数量以表10为准。配制工艺:加入软水,开启搅拌,加入氢氧化钠溶液,搅拌20分钟,加入rf树脂溶液(对比例1),搅拌30分钟,加入甲醛(37.0%),25~30℃熟化2小时,备用。表10(2)5#浸渍液的配制:配方:各组分数量以表11为准。配制工艺:加入丁吡胶乳,开启搅拌,加入配制好的rf液,搅拌30分钟,加入甲醛(37.0%),25~30℃熟化8小时,备用。表11注:*为[5(1)]配制的rf树脂溶液。(二)帘线的浸渍帘线通过浸渍液,使帘线附着一定量的树脂,附胶量约为4.0%。(三)帘线的固化浸胶后的帘线用1.5~2.0kg张力,依次通过150±2℃干燥炉和230±2℃固化炉,通过时间1分钟。(四)固化后帘线与胶料的硫化实验用胶料按照gb/t6038-2006执行。硫化温度150±1℃,硫化时间30分钟。(五)样品h抽出力的测试方法按照gb/t2942-2009执行;实验用胶料按照gb/t6038-2006执行。(六)样品h抽出力测试报告样品编号1#、2#、3#、4#分别对应实施例1、实施例2、实施例3和实施例4的产品;样品编号5#为对比例1的产品。测试结果如表12~16所示。表16二、粘合剥离强度测试(一)帘子布浸渍液的配制按照上述测试h抽出力的浸渍液配制标准执行。(二)帘子布的浸渍帘子布通过浸渍液池、挤压辊、真空吸料器等设备,使帘子布均匀附着一定量的树脂,附胶量约为3.0%。(三)浸胶帘子布的固化浸胶后的帘子布用1.5~2.0kg张力依次通过150±2℃干燥炉和230±2℃固化炉,通过时间5分钟。(四)固化后帘子布与胶料的硫化实验用胶料按照gb/t6038-2006执行。浸胶帘线子线与胶料的硫化温度150±1℃,硫化时间3分钟。(五)帘子布浸胶剥离强度按照gb/t32109-2015执行。(六)样品粘合剥离强度检测报告样品编号1#、2#、3#、4#分别对应实施例1、实施例2、实施例3和实施例4的产品;样品编号5#为对比例1的产品。测试结果如表17~表21所示。表21通过对表17-21的数据对比分析,1#、2#样品性能优势明显。1-5#样品粘合剥离后图片如图5~图9所示,图5~图9依次为1-5#样品粘合剥离后图片,其中1-4#样品依次对应实施例1~实施例4的产品,5#样品对应对比例1的产品。通过对图5~图9中1-5#样品粘合剥离强度后试片的表面看,能直观的看出1#、2#样品的粘合性能好。三、产品原材料成本:表22序号原材料成本(元/吨)差价(元/吨)实施例137515.600实施例236929.30-586.30实施例336622.90-892.70实施例436772.50-743.20对比例139290.301774.70注:原材料成本依照每吨成品树脂为基准。结果分析:(1)本申请所述的具体实施方法,均采用专业合成工艺,摒弃了传统的预聚体合成工艺,因此,产品的稳定性和可重现性得到保证。(2)由于本申请采用专业合成工艺,生成稳定的产品,客户在产品使用过程中,避免了客户自行合成预聚体的生产流程,降低了产成品的质量波动,保证产成品的质量稳定。(3)本申请所述的具体实施方法,树脂中游离酚含量低,避免了游离酚在混炼过程中因高温升华而恶化生产环境,减少了对操作者的健康危害;以及胶料表面出现“喷霜”现象等问题。(4)本申请所述的具体实施方法,合成过程中无工艺废水产生,符合绿色、环保理念。(5)数据分析:(a)通过对表12~16的数据对比分析,1#、2#样品性能优势明显。(b)通过对表17~21的数据对比分析,1#、2#样品性能优势明显。(c)通过对图5~图9中1~5#样品粘合剥离强度后试片的表面看,能直观的看出1#、2#样品的粘合性能好。(d)在保证产品性能的前提下,通过对表22的对比分析,实施例2为最佳方案。以上所述实施例仅表达了本申请的几种实施方式,其描述较为具体和详细,但并不能因此而理解为对发明专利范围的限制。应当指出的是,对于本领域的普通技术人员来说,在不脱离本申请构思的前提下,还可以做出若干变形和改进,这些都属于本申请的保护范围。因此,本申请专利的保护范围应以所附权利要求为准。当前第1页12