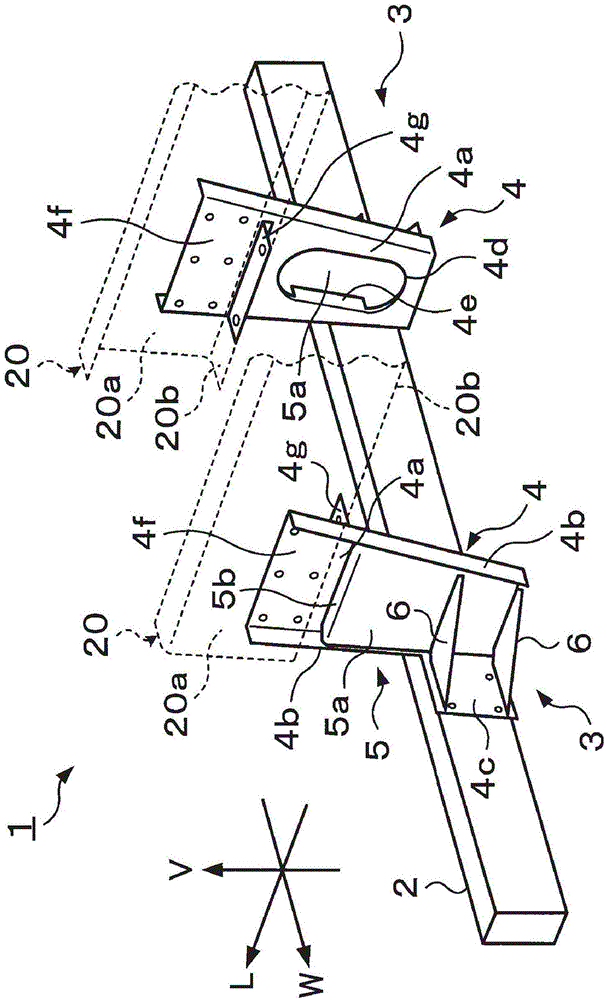
本发明涉及在汽车等车辆彼此碰撞时防止一方车辆钻入到另一方车辆的下方的防钻护栏(underrunprotector)的支承构造。
背景技术:
:例如,在乘用车与卡车等的大型车正面碰撞或追尾那样的情况下,因为在相互的车辆上设置的横梁等强度部件的设置高度的差异,有可能乘用车会钻入到大型车的下方。因此,在大型车的前部及后部,设置有与乘用车具备的强度部件的设置高度匹配而配置的称作防钻护栏的强度部件。由此,防止碰撞时的乘用车的钻入。作为以往的防钻护栏,有在专利文献1~3中记载的结构。这些防钻护栏为将沿车宽方向延伸的梁经由托架或撑杆(支承构造)螺栓紧连到车体框架上的构造。防钻护栏被要求具有充分的承载性能。作为评价承载性的1个方法,有在比梁的撑杆安装位置靠车宽方向外侧的位置向梁的碰撞面(对方车辆碰撞的面)施加载荷、评价最大能够输入何种程度的载荷的方法。由于作为防钻护栏的制品的性能受承载性能的优劣影响,所以希望开发出承载性评价试验中的最大输入载荷变得比以往更大那样的防钻护栏。还希望更加轻量。在上述载荷输入时,对于梁希望有抵抗以车辆上下方向为轴的弯曲力矩的构造,对于撑杆希望抵抗以车辆上下方向为轴的扭转力矩的构造。在专利文献1中,公开了通过撑杆和框架的固定构造将侧框架从轻微的碰撞时的冲击载荷保护的构造,所述撑杆具备:“第一部件,由固定在框架腹板面上并铅直地取向的腹板面、和从该腹板面的车辆前后方向的一端向车宽方向外侧延伸设置并固定在防钻护栏上的第一凸缘面构成”;以及“第二部件,由水平地取向并相对于框架凸缘面及该腹板面固定的上表面、从该上表面的车辆前后方向的一端向铅直下方延伸设置并固定在防钻护栏上的前表面、和从该前表面中的车宽方向外侧的端部向车辆前后方向弯曲形成并相对于该第一部件的腹板面固定的侧面构成”。在专利文献2中,公开了以下的构造:撑杆由“将车体框架与梁连结的撑杆主体”、“将撑杆主体加强的撑杆加强体”和“将撑杆与梁的连接部加强的角撑板”构成;通过跨架设置在梁与撑杆之间的角撑板,提高梁对于弯曲变形的抵抗。此外,在专利文献2中还公开了以下构造:通过在撑杆主体的较短方向两端设置弯折部而在撑杆主体上形成凹部;通过在上述凹部中嵌入上述撑杆加强体而形成闭截面形状的撑杆构造,提高撑杆对于扭转变形的抵抗。专利文献3公开了以下的构造:通过具有将梁连接到车体框架上的连接构造体、沿铅直方向延伸而形成的撑杆、设置在梁与撑杆之间的l字形的托架、加强件和加强板的构造,当对梁输入了载荷时,产生阻碍由经由梁传递来的载荷带来的撑杆向内方的变形的作用。现有技术文献专利文献专利文献1:日本特开2010-132059号公报专利文献2:日本特开2010-120512号公报专利文献3:国际公开wo2016/125745号技术实现要素:发明要解决的课题但是,专利文献1是关于对侧框架进行保护的固定构造的,仅通过该技术,承载性能不会提高。在专利文献2的支承构造中,通过从角撑板的载荷输入及撑杆的扭转变形,撑杆加强部的铅直配置的撑杆加强部腹板面的面外变形发展。由此不能得到充分的承载性能的提高。在专利文献3的连接构造体中,在从加强板的车辆宽度方向内侧到托架或撑杆的车辆前后方向的某侧或两侧设置有开口部的情况下,承载性能下降。即,在托架的车辆前后方向的某侧或两侧设置有开口部的情况下,由于托架因开口部的形成而刚性变低,所以从托架输入的载荷没有被传递给托架的车体框架侧的面整体。由此,承载性能下降。此外,在撑杆的车辆前后方向的某侧或两侧设置有开口部的情况下,由于承受来自加强部件的输入的面积减小,所以承载性能下降。本发明是鉴于以往的技术具有的这样的问题而做出的,目的是提供一种即使对比梁的撑杆安装位置靠车宽方向外侧的位置施加了载荷、也能够抑制对于输入到撑杆中的扭转力矩的变形、并且轻量且承载性能较好的防钻护栏的支承构造。用来解决课题的手段本发明者们对于由将梁及框架间连接的撑杆主体、将撑杆主体加强的撑杆加强体和设置在撑杆加强体及梁间的角撑板构成的防钻护栏的支承构造,专门研究了在比梁的撑杆安装位置靠车宽方向外侧的位置处在梁的碰撞面(对方车辆碰撞的面)上施加了载荷的情况下的撑杆的扭转变形的发生状况,结果拥有了以下的认识并完成了本发明。即,在撑杆主体的与车辆上下方向平行取向的撑杆主体腹板面上设置开口部,进而将从开口部的两端朝向车辆宽度方向外侧延伸设置的一对壁面部以相互对置的方式设置,通过在至少1个角撑板的车辆上下方向的高度位置处使壁面部与撑杆加强体抵接,能够解决上述问题。本发明的主旨是以下这样的。(1)一种防钻护栏的支承构造,具备:撑杆主体,将梁及框架间连接;撑杆加强体,将上述撑杆主体从车辆宽度方向的外侧加强;以及角撑板,设置在上述撑杆加强体及上述梁间;在上述撑杆主体的撑杆主体腹板面上设置有开口部;从上述开口部的车辆前后方向的两端朝向车辆宽度方向外侧延伸设置的一对壁面部以相互对置的方式设置;上述各壁面部设置在与上述角撑板的设置位置对应的高度,抵接在上述撑杆加强体的车辆宽度方向内侧的面上。此外,也可以是以下(2)~(8)那样的结构。(2)如上述(1)所述的防钻护栏的支承构造,上述开口部具有由相互对置的一对直边部和相互对置的一对圆状部构成的大致圆角四边形的形状,从上述各直边部的两方朝向车辆宽度方向外侧延伸设置的上述各壁面部抵接在上述撑杆加强体的车辆宽度方向内侧的面上。(3)如上述(1)或(2)所述的防钻护栏的支承构造,上述壁面部将上述撑杆主体腹板面弯折而形成。(4)如上述(2)或(3)所述的防钻护栏的支承构造,上述开口部的长度l1、上述开口部的平均宽度w1、从上述框架下表面的凸缘起的上述撑杆主体的长度l0、上述撑杆主体的平均宽度w0、由上述撑杆主体和上述撑杆加强体形成的闭截面的车辆宽度方向的高度h之间的关系满足0.5≤l1/l0≤0.8及2×h≤w1≤0.85×w0。(5)如上述(2)~(4)的任一项所述的防钻护栏的支承构造,从上述圆状部的车辆宽度方向外侧的面朝向车辆宽度方向外侧延伸设置的壁面部的高度h1是5mm≤h1≤15mm。(6)如上述(1)~(5)的任一项所述的防钻护栏的支承构造,设置有从上述撑杆加强体的车辆上下方向两端朝向车辆宽度方向内侧延伸设置的撑杆加强体的上下表面部,上述上下表面部抵接在上述撑杆主体上。(7)上述(1)~(6)的任一项所述的防钻护栏的支承构造,上述框架具有铅直地取向的框架腹板面、和从上述框架腹板面的下端朝向车辆宽度方向外侧延伸设置的框架下表面的凸缘;上述撑杆主体被用上述框架腹板面及上述凸缘固定。(8)如上述(1)~(7)的任一项所述的防钻护栏的支承构造,上述撑杆主体和上述撑杆加强体由具有780mpa级以上的强度的钢板构成。发明效果根据本发明,能够得到一种即使在比梁的撑杆安装位置靠车宽方向外侧的位置施加了载荷、也能够抑制输入到撑杆中的扭转力矩所导致的变形、并且轻量且承载性能较好的防钻护栏的支承构造。附图说明图1是表示有关本发明的一实施方式的防钻护栏的立体图。图2是图1的纸面左侧的防钻护栏的支承构造的放大立体图。图3是图2的a-a剖视图。图4是图3的c部放大图。图5是图2的b-b剖视图。图6是表示向防钻护栏的载荷输入条件的平面图。图7是表示比较例1的防钻护栏的支承构造的立体图。图8是比较例1的防钻护栏的变形例的立体图。图9是实施例1的防钻护栏的变形例的立体图。图10是对实施了比较例1和实施例1的承载评价试验模拟时的、变位(压头推入量)和此时的载荷比的关系进行比较的曲线图。图11是表示开口部的圆状部的壁面部4h的高度h1与最大载荷效率的关系的曲线图。具体实施方式以下,参照附图对有关本发明的一实施方式的防钻护栏的支承构造进行说明。另外,在本说明书及附图中,对于实质上具有相同的功能结构的要素通过赋予相同的标号而省略重复说明。如图1所示,本发明的一实施方式的防钻护栏1由沿车辆宽度方向w延伸的梁2和用来将梁2及框架20间连接的防钻护栏的支承构造3构成。防钻护栏的支承构造3由将梁2及框架20间连接的撑杆主体4、撑杆加强体5和角撑板6构成。撑杆主体4具有铅直地取向的撑杆主体腹板面4a和从撑杆主体腹板面4a的车辆前后方向l的端部向车辆宽度方向w的外侧延伸的撑杆主体前后面部4b而呈大致u字型的形状。撑杆主体4通过框架腹板面安装部4f和框架下表面安装部4g与框架20连接,通过梁安装部4c与梁2连接。在撑杆主体4与梁2、框架20的连接中使用螺栓紧连。如图2~图5所示,撑杆加强体5具有铅直地取向的撑杆加强体腹板面5a和从撑杆加强体腹板面5a的车辆上下方向v的端部向车辆宽度方向w的内侧延伸的撑杆加强体上下表面部5b而呈大致u字型的形状。撑杆加强体5配置为,将撑杆主体4的除了框架腹板面安装部4f以外的部分的该撑杆主体4的开口覆盖。通过将撑杆加强体腹板面5a的车辆前后方向l的端部与撑杆主体前后面部4b、以及撑杆加强体上下表面部5b的端部与撑杆主体腹板面4a连接,形成闭截面。在这些连接中使用电弧焊接。在本实施方式中,通过这样将撑杆加强体5固定,将撑杆主体4从车辆宽度方向w的外侧加强。角撑板6是大致三角形形状的板,跨越梁安装部4c和撑杆加强体腹板面5a的车辆宽度方向w的外侧的面而沿着车辆上下方向v排列配置有多片(在本实施方式中是2片)。如图2及图3所示,有关本发明的一实施方式的防钻护栏的支承构造3在撑杆主体腹板面4a上设置有大致圆角四边形形状的开口部4d,具有从开口部4d的车辆前后方向l的两端部向车辆宽度方向w的外侧延伸设置的壁面部4e。壁面部4e以相互对置的方式设置。从大致圆角四边形的开口部4d的相互对置的直边部延伸设置的壁面部4e被抵接在撑杆加强体5上,经由撑杆加强体5的腹板面5a支承上段的角撑板6。对于壁面部4e与撑杆加强体5的连接,使用电弧焊接。另外,所谓“大致圆角四边形”,是由对置的直边部和具有将各直边部的端点彼此连接的任意的曲率半径的圆状部构成的大致四边形。有关本发明的一实施方式的防钻护栏的支承构造3如以上这样构成。在使用具有该防钻护栏的支承构造3的防钻护栏1进行承载试验的情况下,例如如图6那样,在比梁2的撑杆安装位置靠车宽方向外侧的位置(图6中的箭头的位置),将压头碰抵在梁2的碰撞面上而输入载荷。此时,根据本实施方式的防钻护栏的支承构造3,如后述的实施例所示,由于与撑杆加强体5连接的壁面部4e以与角撑板6的设置位置对应的高度支承着撑杆加强体腹板面5a,所以通过对于来自角撑板6的载荷输入的、撑杆加强体5的腹板面5a的面外变形的减少及由撑杆主体4及撑杆加强体5的扭转变形带来的撑杆加强体5的腹板面5a的面外变形的减少,抑制了撑杆加强体5的压曲。这里,“与角撑板6的设置位置对应的高度”,是与撑杆加强体5连接的壁面部4e在车辆上下方向v上在角撑板6的设置位置处重叠的高度。由此,防钻护栏的支承构造3对于扭转力矩的抵抗变高,所以防钻护栏1的承载性能提高。此外,根据本实施方式的防钻护栏的支承构造3,由于设置有开口部4d,所以还能够实现轻量化。以上,对本发明的优选的实施方式进行了说明,但本发明并不仅限定于该例子。应了解的是,显然只要是本领域技术人员就能够在权利要求书所记载的技术思想的范畴内想到各种变更例或修正例,关于它们当然也属于本发明的技术的范围。例如,在图1的防钻护栏的支承构造3中,将大致圆角四边形形状的开口部4d的直边部与车辆上下方向v大致平行地取向,但也可以做成将该直边部与车辆前后方向l大致平行地取向、与撑杆加强体5连接的壁面部4e以与角撑板6的设置位置对应的高度对撑杆加强体腹板面5a进行支承的构造。另外,所述的“与角撑板6的设置位置对应的高度”是与撑杆加强体5连接的壁面部4e在车辆上下方向v上在角撑板6的设置位置处重叠的高度。但是,从由撑杆主体4及撑杆加强体5的扭转变形带来的撑杆加强体5的腹板面5a的面外变形的降低的观点出发,优选的是将能够在车辆上下方向v的较大的范围中对撑杆加强体腹板面5a进行支承的直边部与车辆上下方向v大致平行地取向。例如,在图1的防钻护栏的支承构造3中,使撑杆主体前后面部4b和梁安装部4c为一体,但也可以使梁安装部4c为分体而与撑杆主体4或撑杆加强体5连接。此外,在图1的防钻护栏的支承构造3中,使撑杆主体腹板面4a和框架腹板面安装部4f为一体,使框架下表面安装部4g为分体,但也可以使框架腹板面安装部4f为分体,使框架下表面安装部4g与撑杆主体4或撑杆加强体5一体。此外,也可以是不设置框架下表面安装部4g的构造。另一方面,通过具有框架下表面安装部4g,能够将防钻护栏的支承构造3受到的载荷以剪切变形地传递给框架20,承载性能变高,所以只要根据作为防钻护栏1的需要的性能适当设定框架下表面安装部4g就可以。此外,也可以是不设置撑杆加强体5的上下表面部5b的构造。另一方面,通过设置撑杆加强体5的上下表面部5b,撑杆主体4和撑杆加强体5的车辆上下方向v的开口消失,撑杆主体4和撑杆加强体5的对于扭转变形的抵抗变高,承载性能变高,所以只要根据作为防钻护栏1的需要的性能适当设定撑杆加强体5的上下表面部5b就可以。另外,在上述实施方式中,将设置在撑杆主体腹板面4a上的开口部4d的形状做成大致圆角四边形,但只要能够将撑杆加强体腹板面5a用壁面部4e支承,开口部4d的形状没有被特别限定。这样,只要是防钻护栏1的支承构造3在撑杆主体腹板面4a上设置有开口部4d、具有从开口部4d的两端向车辆宽度方向w的外侧延伸的壁面部4e、使该壁面部4e在与角撑板6的设置位置对应的高度与撑杆加强体5的车辆宽度方向w的内侧的面抵接的结构,就能够获得上述效果。另外,在设置有多片角撑板6的情况下,也只要壁面部4e在与至少1个角撑板的设置位置对应的高度将撑杆加强体5支承,就能够抑制支承的部分对于来自角撑板6的载荷输入的面外变形。换言之,在设置有多个角撑板6的情况下,也即使壁面部4e不以与全部角撑板6的设置高度对应的方式将撑杆加强体5支承,也与以往构造相比能够使承载性能提高。但是,在设置有多个角撑板6的情况下,优选的是如在上述实施方式中说明的那样,用具有从最上段的角撑板6到最下段的角撑板6的长度的壁面部4e将撑杆加强体5支承。这里,所述的“与角撑板的设置位置对应的高度”,是与撑杆加强体5连接的壁面部4e在车辆上下方向v上在角撑板6的设置位置处重叠的高度。此外,大致圆角四边形的开口部4d优选的是形成为,图2~图5所示的撑杆主体开口部长度l1(车辆上下方向v的长度)撑杆主体开口部的平均宽度w1(车辆前后方向l的长度)、撑杆主体4的距框架下表面20b的凸缘的长度l0(mm)(车辆上下方向v的长度)、撑杆主体的平均宽度w0(mm)(车辆前后方向l的长度)、以及由撑杆主体4和上述撑杆加强体5形成的闭截面的车辆宽度方向w的高度h(mm)的关系满足0.5≤l1/l0≤0.8及2×h≤w1≤0.85×w0。撑杆主体的平均宽度w0,是撑杆主体的宽度(车辆前后方向l的长度)的最大值和最小值的平均值。所述的撑杆主体开口部的平均宽度w1,是撑杆主体开口部的宽度(车辆前后方向l的长度)的最大值和最小值的平均值。如果l1/l0不到0.5,则缺乏轻量化效果。相反,如果l1/l0超过0.8,则有可能因撑杆主体腹板面4a的面积减小而承载性能提高的效果变小。如果w1不到2×h,则壁面部4e的高度(车辆宽度方向w的长度)不能形成为h以上,不能使壁面部4e与撑杆加强体腹板面5a抵接。另一方面,在w1超过0.85×w0的情况下,通过撑杆主体腹板面4a的面积减小而承载性能提高的效果变小。此外,大致圆角四边形的圆状部的曲率半径r(mm)优选的是r=0.5×w1。这相当于直边部与圆状部平滑地连接的状态,能够避免由因不连续地连接带来的成形时的应变集中造成的断裂。此外,图2~图4所示的从大致圆角四边形的开口部4d的圆状部的车辆宽度方向外侧的面朝向车辆宽度方向w的外侧延伸设置的壁面部4h的高度h1优选的是5mm≤h1≤15mm。通过设置圆状部的壁面部4h,有利于防止撑杆主体4的面外变形。在后述的实施例中表示,但通过将开口部4d的直边部的壁面部4e用圆状部的壁面部4h连结,承载性能变高。在圆状部的壁面部4h的高度h1不到5mm时,缺乏其效果,在圆状部的壁面部4h的高度h1为15mm以上时,除了与效果相比更导致重量增加以外,在应用780mpa以上的钢板的情况下,在圆状部的壁面部4h的成形时边缘断裂的可能性较高。圆状部的壁面部4h的高度h1更优选的是8mm≤h1≤12mm。这样,不是仅为了轻量化而设置开口部4d,而是设置开口部4d,进而开口部4d的圆状部的壁面部4h将撑杆主体4加强,进而壁面部4e将撑杆加强体5支承,由此防钻护栏支承构造的承载性能变高。[实施例]使用具有以往的防钻护栏的支承构造的防钻护栏和具有有关上述实施方式的防钻护栏的支承构造的防钻护栏实施了承载性评价试验的模拟。以往构造的防钻护栏支承构造是在图7所示那样的撑杆主体54上没有形成开口部的构造(比较例1)。有关本实施方式的防钻护栏的支承构造,是图1所示的构造(实施例1)。撑杆主体使用780mpa级/3.6mm厚的钢板,撑杆加强体使用780mpa级/2.9mm厚、角撑板使用780mpa级/3.2mm厚、框架下表面安装部使用780mpa级/3.2mm厚的钢板。此外,实施例1中的由撑杆主体和撑杆加强体形成的闭截面的车辆宽度方向的高度h是40mm,开口部的圆状部的壁面部4h的高度h1是8.2mm,将撑杆主体的开口部的平均宽度w1用撑杆主体的平均宽度w0除的w1/w0是0.65,将撑杆主体的开口部长度l1用从框架下表面的凸缘起的撑杆主体的长度l0除的l1/l0是0.73。评价试验通过如图6那样将压头碰抵在比撑杆安装位置靠车宽方向外侧的位置处的梁侧面部上而输入载荷来进行。载荷的输入位置在比较例1和实施例1中相同。并且,记录压头的推入量(变位量)和输入载荷,对比较例1和实施例1的防钻护栏的承载性进行了评价。通过图8和图9,对比较例1和实施例1的防钻护栏支承构造的变形进行比较。在图8中在撑杆加强体的腹板面部上能看到面外变形(压曲),而在图9中看不到其面外变形。因此,在本发明中,确认了撑杆加强体的腹板面的面外变形(压曲)被抑制。图10中表示比较例1和实施例1的输入载荷相对于压头推入量的关系。图10所示的承载比是将记录的载荷用比较例1的最大载荷标准化的值。根据图10,确认了实施例1的载荷与比较例1相比提高。表1中表示实施例1相对于比较例1的最大载荷比及防钻护栏的支承构造的重量比。表1中的载荷比是将实施例1的最大载荷用比较例1的最大载荷除的值。表1中的重量比是将实施例1的防钻护栏的支承构造的重量用比较例1的防钻护栏的支承构造的重量除的值。[表1]载荷比重量比实施例11.100.94如表1所示,与比较例1相比,实施例1的最大载荷提高了10%,重量减小了5%以上。即,实施例1的防钻护栏的支承构造与以往相比,显示出在使承载性能提高的同时实现了轻量化。接着,对于从比较例1的构造去掉了框架下表面安装部4g和撑杆加强体5的上下表面部5b的构造(比较例2)及从实施例1的构造去掉了框架下表面安装部4g和撑杆加强体的上下表面部5b的构造(实施例2)实施同样的评价试验。在表2中表示实施例2相对于比较例2的最大载荷比及防钻护栏的支承构造的重量比。[表2]载荷比重量比实施例21.100.94如表2所示,与比较例2相比,实施例2的最大载荷提高了10%,重量减小了5%以上。即,显示出实施例2的防钻护栏的支承构造与以往相比,能够在使承载性能提高的同时实现轻量化的效果并不取决于框架下表面安装部4g和撑杆加强体5的上下表面部5b的有无。接着,对于在实施例1的构造体中将开口部的圆状部的壁面部4h的高度h1设定为0mm和38.2mm的构造体(实施例3、实施例4)实施了同样的评价试验。将圆状部的壁面部4h的高度h1与最大载荷效率的关系表示在图11中。最大载荷效率是将输入到梁中的最大载荷用防钻护栏的支承构造的总重量除的值,该值越高,意味着重量与承载性能的平衡越好。根据图11,与圆状部的壁面部4h的高度h1为0mm的构造相比,在8.2mm的构造中,最大载荷效率变高。因此,显示出通过将直边部的壁面部用圆状部的壁面部连结而承载性能变高。另一方面,与圆状部的壁面部4h的高度h1为38.2mm的构造相比,在8.2mm的构造中最大载荷效率变高。因此,显示出即使圆状部的壁面部过高,与最大载荷提高的效果相比重量增加更大,显示了最优的范围。产业上的可利用性本发明由于能够应用于安装在汽车等车辆上的防钻护栏的支承构造,所以产业上的可利用性较大。标号说明1防钻护栏2梁3防钻护栏支承构造4撑杆主体4a撑杆主体腹板面4b撑杆主体前后面部4c梁安装部4d开口部4e壁面部4f框架腹板面安装部4g框架下表面安装部4h圆状部的壁面部5撑杆加强体5a撑杆加强体腹板面5b撑杆加强体上下表面部6角撑板20框架20a框架腹板面20b框架下表面l0从框架下表面部起的撑杆主体的车辆上下方向长度l1撑杆主体开口部长度w0撑杆主体的平均宽度w1撑杆主体开口部的平均宽度h由撑杆主体和撑杆加强体形成的闭截面的高度h1从开口部圆状部延伸的壁面部的高度l车辆前后方向w车辆宽度方向v车辆上下方向当前第1页12