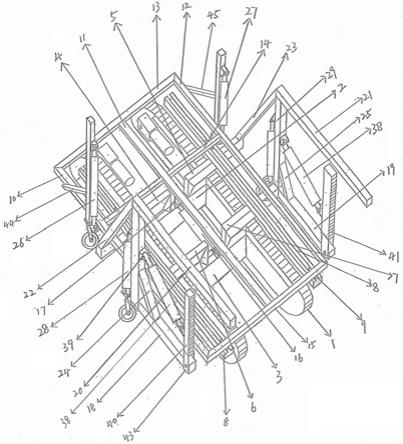
升降车体,车轮、履带复合式爬楼车
1、技术领域
[0001]
本发明专利涉及到一种升降车体,车轮、履带复合式爬楼车,属于爬楼车的一种。
2、
背景技术:[0002]
目前已知的爬楼车大体上分为无动力和有动力两大类。无动力的爬楼车都为手拖车,在此不做描述。有动力类的爬楼车整体结构呈“l”形,在“l”形的底部有两个脚轮,在两个脚轮之间有模拟人腿部爬楼的动作机构和电池,在“l”形“一”的位置是放置货物的货架。他的工作方式是:操作人员拉着车辆在路面行驶时使用脚轮;在遇到楼梯时将脚轮与楼梯垂直面接触,此时打开爬楼动作机构开关,动作机构开始工作,爬上一个台阶之后由操作人员拉着车辆沿着台阶水平面移动,使车辆脚轮与下一个台阶的垂直面接触,如此往复。这种爬楼车的弊端有如下几点:1、载重量小,对于一些体积较大,重量较重的货物无能为力。2、操作人员体力消耗较大,因为车辆和货物的重量有部分施加在操作人员身上。3、操作人员需要控制好车辆的重心,否则有可能造成车辆翻覆。4、下楼梯时安全隐患较大,由于下楼梯时货物遮挡视线,而且车辆需要行驶到台阶拐角特定的位置,才能顺利完成下楼梯动作,稍有不慎就会造成车辆冲下楼梯。5、对于台阶的高度要求严苛。台阶的高度超出动作机构运动的高度之后,车辆将难以行驶。6、车辆在楼梯上的行驶轨迹为波浪形,这就必然导致消耗的能量高且行驶不够平顺,连续工作的能力差。
3、
技术实现要素:[0003]
为了解决目前爬楼车载重量小、操作人员体力消耗大、下楼安全性不高以及行驶不够平稳等明显缺点,本发明提供了一套技术解决方案,使目前爬楼车的缺点可以得到有效解决。
[0004]
本发明的技术解决方案是:将全负载式、高通过性、低磨损履带式行走装置(备注:已单独申请发明专利,申请号或专利号:201811569330.7,此种履带非常适合在楼梯上行驶,在此不做详述,以下简称履带)与底座和连接架连接组成底盘系统,用以在楼梯上行驶;升降系统包含可以伸缩的脚轮,用以在路面或者楼梯平台行驶;在车体的合适位置安装升降系统,用以升降车体实现车轮、履带的切换和辅助履带攀爬楼梯;车体上的货架可以向前水平移动,将货物的重心前移,增加车辆在楼梯上行驶的安全性;在车体尾部左右两边安装可收放式双独立安全尾,车辆在楼梯上行驶时将安全尾放下,进一步增加车辆在楼梯上行驶的安全性,防止翻覆。
[0005]
本发明的工作方式是:当车辆在路面或者平面行驶时,升降系统伸出脚轮,将车体升起,把履带抬离地面,脚轮与地面接触,操作人员推动车辆即可行驶;当车辆需要攀爬楼梯时,可以将车辆推行到楼梯旁,操作升降系统将车体呈水平状态升起一定高度(备注:使履带下平面超过第三级台阶的踏面高度即可,通常升起高度设定为50cm-55cm之间,这样面对大部分楼梯时可以满足使用要求),由于前级升降系统距车体前端预留有一定的有效悬空距离(备注:假设货架系统为复位状态,当脚轮与履带平行时,此时前部轮面垂直于履带
边缘线的点设为a,前部履带边缘线直线部分的起始点设为b,那么从b点到a点之间的最短距离称之为有效悬空距离,用字母表示为ba,楼梯台阶踏深设为c,那么需ba≥2c。由于台阶的尺寸各异,攀爬楼梯的难度受台阶的踏高、台阶踏深、楼梯倾斜角度、车体长度宽度、以及履带高度等因素的影响;根据本人对居民区楼梯的实地调查,通常情况是:台阶踏高≤18cm、踏深≤25cm、楼梯倾斜角度≤36度;由于楼梯平台处空间有限,为了便于车辆在此转弯掉头,通常设定车体长度≤120cm、车体宽度≤75cm;由于车辆在楼梯上行驶时,为了降低重心增加安全性,履带设计的尽可能低、矮,高度被严格控制,综合各方面因素来看,对于本履带式车辆来说前一、二、三级台阶的攀爬难度最高,所以当车辆从平面行驶过度到楼梯行驶时,前三级台阶如果仅仅使用履带攀爬是不可行的,而设计可以升降车体的目的:一是可以实现车轮和履带的切换,二是辅助履带攀爬前三级台阶,所以只需操作升降系统将车辆抬升一定高度,使履带下平面高于前三级台阶的垂直高度,然后将车体往前推行使履带尽可能处于第三级台阶的正上方,此时收回脚轮,履带就会落在第三级台阶上,升降系统就可以辅助履带攀爬前三级最难以攀爬的台阶。当台阶踏深≤25cm、车体长度≤120cm、车体宽度≤75cm时,通常有效悬空距离设定为45cm-50cm之间,这个参数的设定可以满足车辆在攀爬大部分楼梯时,升降系统通过一次升降动作就可以辅助履带攀爬前三级台阶,如果遇到特殊情况升降系统可能需要进行第二次升降动作,目的是使车体的倾斜角度尽量与楼梯的倾斜角度接近,降低履带在攀爬下一级台阶时的难度。后级升降系统安装位置无有效悬空距离的要求,只是在预留出安全尾系统安装空间的情况下,尽量靠近车体后部。)所以当车体被抬升起之后,履带处于悬空状态,此时将车辆往楼梯前推行使履带下平面位于第三级台阶正上方,此时升降系统收回脚轮,使履带与楼梯接触,并将货架前移,放下安全尾,操作车辆使用履带行驶即可;当车辆行驶到楼梯与楼梯平台交接处,此时将货架往回收一些,将车辆继续往前行驶,当最后一级台阶的拐角到达履带中心位置附近时,此时将前级左右两边的升降系统伸出,但不要使脚轮与楼梯平面接触,这时再将货架前移利用货物的重量将车体向下压,当脚轮接触到地面时收回脚轮,车辆整体又回到水平状态,在车辆行驶到确保车辆不会向后方翻转时收回货架,收回安全尾,这样做的目的是防止车辆在行驶到重心临界点时砸向楼梯平面。车辆不管是上楼还是下楼在楼梯上的状态是不变的,只是上楼时是前进状态,下楼时是后退状态。当下楼梯从楼梯平台往楼梯行驶时,此时需先将安全尾放下,然后将货架伸出,当车辆行驶到平台台阶拐角在履带中心位置附近时,将后级升降系统伸出到脚轮接触楼梯,此时将货架收回,利用货物的重量将车体下压,此时收回后级升降系统,随着后级升降系统的慢慢收回,车体也缓慢的从水平状态转为与楼梯倾斜角度相同的倾斜状态(备注:当车辆在下楼梯时,需要将车辆从水平状态转换到与楼梯倾斜角度相同的倾斜状态,这种转换方式有两种,以上所述为其中一种,另一种方式是:先将安全尾放下,然后将货架伸出,当车辆行驶到平台台阶拐角在履带中心位置附近时,此时将前级升降系统伸出,利用前级升降系统的抬升力将车体前部抬起,此时操作履带行驶,当车辆的重心已经越过楼梯平台的拐角,依靠车辆自身的重量能够将车体保持在倾斜状态时,收起前级升降系统。),当履带完全与楼梯接触时伸出货架,利用履带下楼;当车辆行驶到楼梯平台时,最先与楼梯平面接触的是安全尾,此时可以将安全尾收起,用履带继续行驶,当行驶到前级升降系统伸出的脚轮可以接触到楼梯平面,这时收回货架,将前、后级升降系统伸出,并利用升降系统将车体从倾斜状态调整到水平状态,使用脚轮在楼梯平台行驶并转弯。根据所载
货物体积和重量的不同,车辆升降系统的数量和位置也不同,安全系统的配置也不同,并由此发展出三种车体结构,分别是:(1)、一级两点式车体(通俗称:轻型)。这种车体结构简单轻便,升降系统位于车体左、右两侧中间位置,与货架连接,由于所载货物为轻小物品,操作人员完全可以控制车辆,所以取消了货架可水平移动和安全尾两项安全配置。(2)、两级三点式车体(通俗称:中型)。两级指的是升降系统分为前级和后级,三点指的是前级升降系统有两个升降点位分别位于货架左、右两侧,与货架连接并与货架一起运动;后级升降系统只有一个升降点位位于车体后部中间位置。安全配置设置了可水平移动货架。(3)、两级四点式车体(通俗称:重型)。两级指的是升降系统分为前级和后级,四点指的是前、后级共四个升降点位。前级升降系统位于货架前部左、右两侧与货架连接,且随货架一起运动;后级升降系统位于车体后部左、右两侧,与扶手架连接。安全配置设置了可水平移动货架和双独立可收放式安全尾。
[0006]
本发明的有益效果是:(1)、车辆可以实现大载重量、大体积货物在楼梯上的运输,实用价值高。
[0007]
(2)、行驶安全性高。车辆在设计的时候就着重考虑行驶的安全性,车体上配置有可水平移动货架,当车辆在楼梯上行驶时货架上移,将货物的重心上移,使车辆和货物的重心保持在履带中心点附近的位置;为了增加安全性车辆又进一步配置了双独立可收放式安全尾,即使有一个安全尾发生故障,另一个也可以确保车辆的安全,防止车辆翻覆。
[0008]
(3)、操作人员体力消耗小。
[0009]
(4)、改装潜力大。例如重型车,增加升降系统的抬升高度,使车体能够抬升到超过货车车厢底板的高度,车辆就可以直接行驶到货车车厢里,装载货物之后可以实现从货车车厢到仓库间的直接运输,即使运输过程中遇到楼梯(例如:仓库在二楼或者三楼等情况)也不受影响。例如中型车,可以改装成爬楼轮椅。
[0010]
(5)、车辆发展成体系,涵盖轻、中、重型车,应用范围广。
4、附图说明
[0011]
图1:两级四点式车体结构左后45度立体视图
[0012]
图2:两级四点式车体结构左侧平面视图
[0013]
图3:“c”形轨道后侧视图
[0014]
图4:滑轮组左侧平面视图
[0015]
图5:货架水平移动机构左侧平面视图
[0016]
图6:升降系统左侧平面视图
[0017]
图7:安全尾后侧平面视图
[0018]
图8:安全尾左侧平面视图
[0019]
图9:两级三点式车体结构左后45度立体视图
[0020]
图10:一级两点式车体结构左后45度立体视图
5、具体实施方式
[0021]
实施例1:两级四点式车体(通俗称:重型)
[0022]
其实施方式是:如图1所示,在前底座横梁(2)左右两边分别焊接左前连接架(4)和
右前连接架(5),在后底座横梁(3)左右两边分别焊接左后连接架(6)和右后连接架(7),四条连接架需高出履带上表面(如图2所示),并向左、右两边伸出一定距离。将一条“c”形轨道(8)焊接在左前连接架(4)和左后连接架(6)上(如图2所示),另一条“c”形轨道焊接在右前连接架(5)和右后连接架(7)上,并使两条“c”形轨道(8)保持合适的距离,且与车体纵向中心线对称,在每条“c”形轨道(8)内分别放入两个滑轮组(9)(如图3、图4所示);将左纵梁(10)、右纵梁(12)、前横梁(13)、后横梁(15)焊接在一起,形成一个矩形框架,并在纵向中间位置焊接一条中纵梁(11),并使它位于车体纵向中心线上,在前部合适处焊接两根中横梁(14),用以加强货架的结构强度,将前部两个滑轮组(9)分别与货架中横梁(14)左右两边合适位置连接,将后部两个滑轮组(9)分别与货架后横梁(15)左右两边合适位置连接,在中纵梁(11)前部合适处下方焊接货架推拉动作机构安装支架(17),另一个货架推拉动作机构安装支架(17)焊接在后底座横梁(3)中间处,并将货架推拉动作机构(16)底端与后底座横梁(3)上的货架推拉动作机构安装支架(17)通过插销连接,前端与中纵梁(11)下部的货架推拉动作机构安装支架(17)通过插销连接(如图5所示),当货架推拉动作机构(16)推出时,货架会带动滑轮组(9)沿着“c”型轨道(8)向前水平移动,拉回时货架会向后水平移动。
[0023]
如图6所示,升降系统部件包含:伸缩外管(30)、伸缩内管(31)、伸缩动作机构(32)、伸缩动作机构安装支架(33)、脚轮(34)、脚轮连接板(35)、连接螺栓(36)。其实施方式是:将伸缩内管(31)和伸缩动作机构安装支架(33)分别与脚轮连接板(35)合适处焊接,将另一个伸缩动作机构安装支架(33)焊接在伸缩外管(30)上部合适处,将伸缩内管(31)插入伸缩外管(30)的空腔内,并通过插销将伸缩动作机构(32)头尾分别与下部和上部的伸缩动作机构安装支架(33)连接,将脚轮(34)与脚轮连接板(35)通过连接螺栓(36)固定。在车体合适位置需要设置升降系统时,只需将伸缩外管(30)焊接在车体合适处,并通过支架加强其结构强度即可。当伸缩动作机构(32)伸出时,带动伸缩内管(31)从伸缩外管(30)中伸出,脚轮(34)也会被推出并与地面接触,车体被抬升。
[0024]
如图1、图2所示,在货架左纵梁(10)前部设置左前升降系统(26)(备注:需预留出有效悬空距离。),将伸缩外管(30)与货架左纵梁(10)焊接固定,将左前升降系统加强支架(44)两端分别与货架左纵梁(10)和伸缩外管(30)焊接,进一步加强其结构强度;在货架右纵梁(12)前部设置右前升降系统(27)(备注:需预留出有效悬空距离。),将伸缩外管(30)与货架右纵梁(12)焊接固定,将右前升降系统加强支架(45)两端分别与货架右纵梁(12)和伸缩外管(30)焊接,加强其结构强度;左前升降系统(26)和右前升降系统(27)会随货架一起水平移动。在左后连接支架(6)左边端部设置左后升降系统(28),将伸缩外管(30)下端与左后连接支架(6)左边端部焊接,顶端与左上纵向架(20)前部焊接,下部与左下纵向架(18)前部焊接,将左中加强支架(22)两端分别与左前连接架(4)端部和左上纵向架(20)前部焊接,将左后加强支架(24)两端分别于伸缩外管(30)和左下纵向架(18)焊接,以加强扶手架系统和升降系统的结构强度;在右后连接支架(7)右边端部设置右后升降系统(29),将伸缩外管(30)和右后连接支架(7)右边端部焊接,上部与右上纵向架(21)前部焊接,下部与右下纵向架(19)前部焊接,将右中加强支架(23)两端分别与右前连接架(5)端部和右上纵向架(21)前部焊接,将右后加强支架(25)两端分别与伸缩外管(30)和右下纵向架(19)焊接,以加强扶手架系统和升降系统的结构强度。
[0025]
如图1、图7和图8所示,安全尾系统部件包含:收放动作机构(38)、收放动作机构安
装支架(39)、强度管(40)、橡胶防滑条(41)、防滑条紧固螺丝(42)、u形连接架(43)、u形连接架插销(46)。其实施方式是:在强度管(40)的底端焊接u形连接架(43),在其后面铺设橡胶防滑条(41),并通过防滑条紧固螺丝(42)固定,在其前面焊接一个收放动作机构安装支架(39),将u形连接架(43)通过插销(46)分别与左下纵向架(18)和右下纵向架(19)连接,将另一个收放动作机构安装支架(39)焊接在伸缩外管(30)合适处,并通过插销将收放动作机构(38)头部和尾部分别与强度管(40)和伸缩外管(30)连接。当收放动作机构(38)放下时,推动安全尾放下,使安全尾朝向地面,接近但不接触地面,起到对车体的支撑作用防止翻覆。
[0026]
实施例2:两级三点式车体(通俗称:中型)
[0027]
其实施方式是:在实施例2中,只有扶手架系统结构与后级升降系统的位置与实施例1不同,其它系统实施方式相同,在此不做详述。
[0028]
如图9所示,左纵向架(50)前端与左前连接架(4)焊接,中间部位与左后连接架(6)焊接,后端与左垂直架(52)焊接,并用左加强支架(51)分别焊接在左纵向架(50)和左垂直架(52)上,以加强其结构强度,右边部分的实施方式与左边相同;把上横架(57)的左右两端分别与左垂直架(52)和右垂直架(55)的顶端焊接,将后级升降系统(59)设置在上横架(57)的中间,并将伸缩外管(30)顶端与上横架(57)中间处焊接,将下左横架(53)左右两端分别与左垂直架(52)底端和伸缩外管(30)左侧面焊接,将下右横架(54)左右两端分别与伸缩外管(30)右侧面和右垂直架(55)底端焊接,用以加强后级升降系统(59)的结构强度。
[0029]
实施例3:一级两点式车体(通俗称:轻型)
[0030]
其实施方式是:如图10所示,在前底座横梁(2)上焊接左前连接架(4)和右前连接架(5),在后底座横梁(3)上焊接左后连接支架(6)和右后连接支架(7),在左前连接架(4)和右前连接架(5)上焊接一根下横架(71),在左后连接支架(6)和右后连接支架(7)上也焊接一根下横架(71),在这两根下横架(71)的两端分别焊接两根下纵向架(70),并在两根下纵向架(70)的前后两端分别焊接两根下横架(71),形成货架。在左边下纵向架(70)与后部三根下横架(71)焊接处分别焊接三根垂直架(72),并在这三根垂直架(72)的上部焊接一根上纵向架(75),右边部分也是同样的实施方式,上横架(78)左右两端分别焊接在左右上纵向架(75)内侧,并与最后两根垂直架(72)保持在一个垂直面上,形成扶手架。将左升降系统(76)设置在车体左边中间位置,伸缩外管(30)底端与左边的下纵向架(70)焊接,顶端与左边上纵向架(75)焊接;将右升降系统(77)设置在车体右边中间位置,伸缩外管(30)底端与右边的下纵向架(70)焊接,顶端与右边上纵向架(75)焊接。由于是轻型车,人力可以完全控制车辆,所以取消了可水平移动货架和双独立可收放式安全尾这两项安全配置。