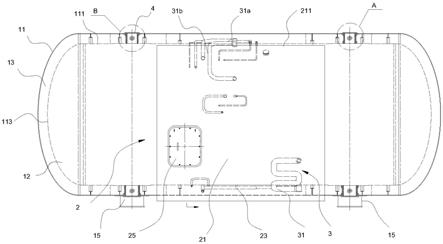
[0001]
本实用新型涉及船用运输罐体技术领域,特别涉及一种船用液罐。
背景技术:[0002]
目前,为应对日益严峻的环境挑战,降低污染排放控制区的硫氧化物排放,国际海事组织(international maritime organization,简称imo)出台了一系列规定来控制环境污染,而天然气作为清洁能源,又比柴油等传统燃料更加经济,因此lng(液化天然气)燃料动力船近年来发展十分迅速。
[0003]
船用lng燃料罐通常采用真空卧式容器,其罐体连接所处(tank connection space,简称tcs)位于罐体尾部,其内罐与外罐之间的夹层管路布置在内封头和外封头之间。这种方案应用广泛,制造工艺成熟。但如果船体长度方向的空间比较有限,宽度方向空间比较富余,该方案就不能充分利用船体上的空间,导致船舶装载的lng燃料罐容积大大减少,进而导致短程航运的船舶补充燃料频率增加,远航船舶的单次航行距离减小。
技术实现要素:[0004]
本实用新型的目的在于提供一种船用液罐,以解决现有技术中燃料罐的布置受限于船体的长度空间而导致容积减小的问题。
[0005]
为解决上述技术问题,本实用新型采用如下技术方案:
[0006]
一种船用液罐,包括:罐体,其包括用于储存低温液体的内罐和包覆于内罐外部的外罐,所述内罐和所述外罐之间形成有绝热夹层;罐体连接处所,其包括外壳和固定于所述外壳内的连接管路;所述外壳位于所述外罐的侧部并沿外罐的轴向延伸,所述外壳设于所述外罐上沿轴向的中部区域,所述外壳与所述外罐之间围合形成一中空的收容腔;夹层管路,包括位于所述绝热夹层中的多个依次折弯相连的管段,所述夹层管路的内端与所述内罐连通,所述夹层管路的外端穿过所述外罐并伸入所述收容腔内与所述连接管路连接。
[0007]
根据本实用新型的一个实施例,所述外壳沿所述罐体横向上位于所述罐体的中心轴线的一侧。
[0008]
根据本实用新型的一个实施例,所述外壳的下端超出所述外罐的最低点,所述外壳的上端超出所述外罐的中部。
[0009]
根据本实用新型的一个实施例,所述外壳包括依次连接的顶板、外侧围板、底板和底部侧板;所述顶板和所述底板水平间隔,所述顶板沿轴向位于所述外罐的顶部和中部之间,并与所述外罐的外壁连接固定,所述底部侧板设于所述外罐的底部,所述底板通过所述底部侧板与所述外罐连接固定,以位于所述外罐的最低点的下方;所述外侧围板位于所述外罐的外侧,并分别连接所述顶板、所述底板和所述外罐的外壁,从而围合形成一密封的收容腔。
[0010]
根据本实用新型的一个实施例,所述底部侧板沿所述外罐的最低点所在的中心竖向轴线竖直设置。
[0011]
根据本实用新型的一个实施例,多个所述管段包括多个轴向管段和多个过渡管段;多个所述轴向管段间隔且错位布置,各所述轴向管段平行于所述罐体的轴向,各所述过渡管段的两端分别与相邻两所述轴向管段折弯相连。
[0012]
根据本实用新型的一个实施例,所述夹层管路还包括多个加强件;各所述加强件对应设于相邻两所述管段之间的连接处。
[0013]
根据本实用新型的一个实施例,所述外罐包括筒体和分别设于所述筒体轴向两端的两个封头;所述外壳与所述筒体连接,所述外壳沿轴向的两端分别与两所述封头之间具有间距。
[0014]
根据本实用新型的一个实施例,所述船用液罐还包括沿所述罐体的轴向间隔分布的两个鞍座,各所述鞍座支撑设于所述外罐的筒体底部;所述外壳在沿所述罐体的轴向上设于两所述鞍座之间。
[0015]
根据本实用新型的一个实施例,所述船用液罐还包括设于所述绝热夹层中用以连接所述内罐和外罐的两组支撑结构,两组所述支撑结构沿所述罐体的轴向间隔分布;每组所述支撑结构包括沿所述罐体的同一横截面周向分布的多个支撑管组,其中位于所述罐体下部的任意两相邻所述支撑管组之间的圆心夹角小于位于罐体上部的两相邻所述支撑管组之间的圆心夹角。
[0016]
由上述技术方案可知,本实用新型提供的一种船用液罐至少具有如下优点和积极效果:
[0017]
1、其罐体连接处所设于外罐的侧壁上,相较于设于罐体尾部的布置方案,充分利用了船体的宽度方向上的空间,而不占据罐体安装所需要的长度方向上的空间,增加了罐体的装载容积,保证了船舶海上运行的续航能力。
[0018]
2、其夹层管路包括多个折弯相连的管段,该折弯设计能够缓解管路在内、外罐因温差应力发生轴向上的相对位移时受到的剪切力,避免夹层管路受牵扯过大而变形、破损等问题,改善管路的受力状态,确保管路的使用正常以及保证lng不泄露。
附图说明
[0019]
图1为本实用新型实施例中船用液罐呈卧式放置的示意图。
[0020]
图2为本实用新型实施例中船用液罐的横向剖面示意图。
[0021]
图3为图1的a处放大图。
[0022]
图4为图1的b处放大图。
[0023]
附图标记说明如下:1-罐体、11-外罐、12-内罐、13-绝热夹层、111-筒体、113-封头、15-鞍座、2-罐体连接处所、21-外壳、211-顶板、213-外侧围板、2131-板体、2133-围板、215-底板、217-底部侧板、23-连接管路、25-气密门、3-夹层管路、31-管段、31a-轴向管段、31b-过渡管段、4-支撑结构、41-支撑管组、411-外罐固定管、413-内罐固定管、415-支撑管。
具体实施方式
[0024]
体现本实用新型特征与优点的典型实施方式将在以下的说明中详细叙述。应理解的是本实用新型能够在不同的实施方式上具有各种的变化,其皆不脱离本实用新型的范围,且其中的说明及图示在本质上是当作说明之用,而非用以限制本实用新型。
[0025]
本实施例提供一种船用液罐,是集lng液罐和罐体连接处所于一体的船用设备。
[0026]
其罐体连接处所(tcs)设于lng液罐的外周侧壁上,充分利用了船体的宽度方向上的空间,而不占据罐体安装所需要的长度方向上的空间,增加了罐体的装载容积,尤其适用于船体宽度方向较为富余的船舶,扩大应用范围,保证了海上船舶具有足够的续航能力。
[0027]
该船用液罐包括罐体、罐体连接处所和夹层管路。其中,罐体包括用于储存低温液体的内罐和包覆于内罐外部的外罐,内罐和外罐之间形成有绝热夹层。罐体连接处所包括外壳和固定于外壳内的连接管路,外壳设于外罐的外周侧壁上并沿外罐的轴向延伸,外壳与外罐之间围合形成一中空的收容腔。夹层管路包括多个依次折弯相连的管段,夹层管路的内端与内罐连通,夹层管路的外端穿过外罐并伸入收容腔内与连接管路连接。
[0028]
请参照图1,图1示出了本实施例提供的一种船用液罐的具体结构,其包括罐体1、设于罐体1上的罐体连接处所2和设于罐体夹层中的夹层管路3。
[0029]
罐体1包括用于储存低温液体lng的内罐12、包覆于内罐12外部的外罐11和两个相对设置的鞍座15,内罐12和外罐11之间形成有绝热夹层13。
[0030]
当罐体1呈卧式安装设于船体上,罐体1的轴向与船体的长度方向一致,罐体1的横向与船体的宽度方向一致。外罐11和内罐12均包括筒体111和分别设于筒体111轴向两端的两个封头113。两个鞍座15沿罐体1的轴向方向间隔分布,以支撑设于外罐11的筒体111的底部。
[0031]
罐体连接处所2设于罐体1的侧壁上。具体为,罐体连接处所2主要包括外壳21和固定于外壳21内的用于为船舶的动力系统供气的连接管路23。其中,外壳21覆盖设于外罐11的外周侧壁上并沿外罐11的轴向延伸,外壳21沿罐体1横向上位于罐体1的中心轴线的一侧。外壳21与外罐11之间围合形成一中空的收容腔。该收容腔供夹层管路3的外端伸入,与连接管路23对接,其目的是为了在lng发生泄漏时作为应急的lng储存空间。外壳21上还设有能够供工人进出的气密门25。在本实施例中,罐体1连接所处还包括设于收容腔内的仪表、电气设备、通风设备等各种设备。
[0032]
不同于传统的tcs设于罐体1封头113处尾部的设计,本实施例中的tcs于罐体1的侧布式设计能够充分利用船体的宽度方向上的空间,而不占据罐体1安装所需要的长度方向上的空间,可使得罐体1沿船体的长度方向尽量延伸、扩展,实现罐体1的体积最大化,提高了罐体1的装载容积,保证了海上船舶具有足够的续航能力。
[0033]
进一步的,外壳21设于外罐11上沿轴向的中部区域,即沿轴向设于两鞍座15之间,以分别与外罐11的两封头113之间具有间距。
[0034]
同时,外壳21相对于外罐11的中部轴线呈对称设置。如此,以尽量平衡罐体1的重心,保证罐体1在船舶运行过程中的稳定。
[0035]
请结合图2,外壳21的下端超出外罐11的最低点,外壳21的上端超出外罐11的中部,以尽量包覆住外罐11上的连接部分。
[0036]
具体的,外壳21包括依次连接的顶板211、外侧围板213、底板215和底部侧板217。其中,顶板211和底板215呈上下水平间隔。顶板211沿轴向位于外罐11的顶部和中部之间,并与外罐11的外壁连接固定,底部侧板217设于外罐11的底部,底板215通过底部侧板217与外罐11连接固定,以位于外罐11的最低点的下方。外侧围板213位于外罐11的外侧,并分别连接顶板211、底板215和外罐11的外壁,从而围合形成一密封的收容腔。
[0037]
外侧围板213包括板体2131和从板体2131两侧折弯相对突伸出的两围板2133,其中,板体2131和两围板2133的上下两端分别与顶板211、底板215焊接固定。两围板2133远离板体2131的一端与外罐11的外侧壁焊接固定。在本实施例中,板体2131和围板2133之间的夹角为90度,围板2133垂直连接于外罐11的侧壁。当然,上述夹角可以根据使用需求而适应性改变。
[0038]
请再次参照图1,夹层管路3包括多个位于绝热夹层13中的依次折弯相连的管段31。夹层管路3的内端与内罐12连通,夹层管路3的外端穿过外罐11并伸入收容腔内与连接管路23连接。
[0039]
由于lng属于低温液体,储存温度最低达-163℃。而储存lng的内罐12在经常装卸的情况下,温度变化很大,其产生较大的温差应力导致内罐12结构收缩,进而相对于外罐11产生轴向位移。夹层管路3一端连接内罐12,另一端连接外罐11,管路在该工况下被倾斜着拉伸,容易因剪切应力而扭曲变形,管路一旦破坏就易产生泄露问题,造成安全事故。
[0040]
因此上述夹层管路3的折弯设计能够缓解管路在内、外罐11因温差应力发生轴向上的相对位移时受到的剪切力,避免夹层管路3受牵扯过大而变形、破损等问题,改善管路的受力状态,确保管路的使用正常以及保证lng不泄露。
[0041]
具体的,多个管段31包括多个轴向管段31a和多个过渡管段31b。多个轴向管段31a间隔且错位布置,各轴向管段31a平行于罐体1的轴向,各过渡管段31b的两端分别与相邻两轴向管段31a折弯相连。最终,多个轴向管段31a和多个过渡管段31b围合形成的结构在罐体1的纵向截面上的投影呈u形或s形。并且,夹层管路3还包括有多个加强件,各加强件对应设于相邻两轴向管段31a和过渡管段31b之间的连接处,以提高连接强度。
[0042]
船用液罐还包括设于绝热夹层13中用以连接内罐12和外罐11的两组支撑结构4。
[0043]
两组支撑结构4沿罐体1的轴向间隔分布,每一组的支撑结构4包括沿罐体1的同一横截面周向分布的多个支撑管组41,其中位于罐体1下部的任意相邻两支撑管组41之间的圆心夹角小于位于罐体1上部的两支撑管组41之间的圆心夹角。
[0044]
如图2所示出的位于罐体1下部的支撑管组41为六个,该六个支撑管组41均匀分布,其圆心夹角为30度。当然,在其他实施例中,支撑管组41的数量不限,在罐体1的下方尽量布置多个支撑管组41,能够缓解tcs侧布后重心偏离导致横向应力过大的问题。
[0045]
请参照图3示出的支撑管组41的横向剖视图,其中位于罐体1轴向的一端的各支撑管组41包括:突伸设于外罐11的内周壁上的外罐固定管411、突伸设于内罐12的外周壁上的内罐固定管413,以及支撑管415。两固定管的开口相对,分别供支撑管415分别对应固定卡设于外罐固定管411和内罐固定管413中,以形成内罐12和外罐11之间的支撑固定端。
[0046]
请进一步参照图4,位于罐体1轴向另一端的各支撑管组41包括:突伸设于外罐11的内周壁上的外罐固定管411和支撑管415。该支撑管415的一端与内罐12的外周壁连接固定。另一端伸入至外罐固定管411中并可相对于该外罐固定管411轴向滑动,以形成内罐12和外罐11之间的支撑滑动端。该支撑滑动端的作用是在内罐12受到低温收缩时允许内罐12向固定端方向发生位移。
[0047]
综上所述,本实用新型提供的一种船用液罐至少具有如下优点和积极效果:
[0048]
首先,其罐体连接处所2设于外罐11的侧壁上,相较于设于罐体1尾部的布置方案,充分利用了船体的宽度方向上的空间,而不占据罐体1安装所需要的长度方向上的空间,增
加了罐体1的装载容积,保证了船舶海上运行的续航能力。
[0049]
其次,罐体连接处所2的外壳21设于外罐11上沿轴线方向的中部区域,即设于两鞍座15之间,以分别与外罐11的两封头113之间具有间距。同时,外壳21相对于外罐11的中部轴线呈对称设置;如此,以尽量平衡罐体1的重心,保证罐体1在船舶运行过程中的稳定。
[0050]
然后,夹层管路3包括多个折弯相连的管段31,该折弯设计能够缓解管路在内、外罐11因温差应力发生轴向上的相对位移时受到的剪切力,避免夹层管路3受牵扯过大而变形、破损等问题,改善管路的受力状态,确保管路的使用正常以及保证lng不泄露。
[0051]
虽然已参照几个典型实施方式描述了本实用新型,但应当理解,所用的术语是说明和示例性、而非限制性的术语。由于本实用新型能够以多种形式具体实施而不脱离实用新型的精神或实质,所以应当理解,上述实施方式不限于任何前述的细节,而应在随附权利要求所限定的精神和范围内广泛地解释,因此落入权利要求或其等效范围内的全部变化和改型都应为随附权利要求所涵盖。