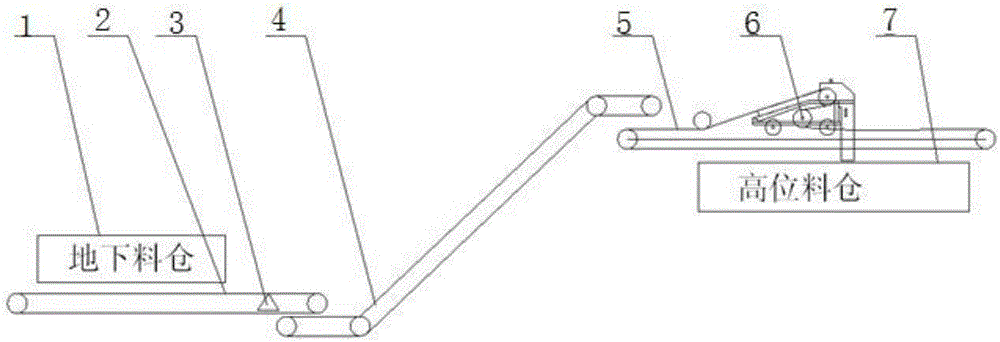
本本发明涉及一种处理方法,特别涉及一种转炉高位料仓料位处理方法,属于自动化控制
技术领域:
。
背景技术:
:目前梅钢拥有两个炼钢厂共5座转炉,转炉炼钢过程中,需要加入石灰等辅料以及合金原料,所有辅料和合金都由地下料场通过皮带运输并加入到高位料仓。地下料场向高位料仓加料,需要操作工必须到现场人工确认仓位料位情况,估算可以上料的重量,再进行上料,人工估算存在不确定性和误差比较大,容易造成上料不足或铺料等,都将影响转炉的生产,因此在上料过程中需要操作人员查看料位情况。现场大量的粉尘,环境极其恶劣,不适合人员长时间停留。本发明通过对料仓的料位进行监控和计算,实时监控高位料仓的物料情况,为操作人员上料提供依据,大大减少操作强度,为实现自动上料提供数据支撑,进一步提升生产效率。技术实现要素:本本发明正是针对现有技术中存在的技术问题,提供一种转炉高位料仓料位处理方法,该方法通过对转炉高位料仓的物料的料位进行计算处理,实时掌握当前料仓的物料,为自动化上料提供数据,减少操作人员对料仓料位判断误差,提高上料的准确性,避免上料不足或上料过多造成堆料,提升劳动效率。为了实现上述目的,本本发明的技术方案如下,一种炼钢高位料仓料位处理方法,其特征在于,所述处理方法包括以下步骤:1)料仓的容积计算,2)虚拟密度计算,3)料仓物料重量计算,4)料仓料位报警设定,5)料位报警输出,6)料位信息显示,7)上料优先计算。作为本发明的一种改进,所述步骤1)料仓的容积计算具体如下,由于料位最高点是下料口的位置,不适合安装料位探测装置,一般选择在稍远离下料口,探测物料较低的位置,避免下料时的振动影响料位探测装置的准确性,也避免堆料时损坏料位探测装置,根据料仓的形状,将料仓分为上部的立方体和下部的台体。将料仓分为6个平面,分别是a、a0、a1、a2、a3、和a4平面,a0平面为设定的料位o平面,a2平面为料位探测装置探测的料面,a4平面为设定料位的最高平面,各平面的长/宽分别是a/b、a0/b0、a1/b1、a2/b2、a3/b3和a4/b4;a0平面和a1平面的高度为h22;a0平面和a2平面的高度为h;a平面和a4平面的高度为h11;a平面和a3平面的高度为h1;a0平面和a4平面之间是实际应用时,探测装置的量程(lc),计算料仓中物料重量(m)和上料需求量(m_sp);当设定值a>0,b>0,h1>0,h11>0,a1>0,b1>0,h2>0,h22>0都同时满足,系统认为设定值正确;如有一项不满足,系统认为设定值错误,系统发出报警信号(alarm_sp);计算a0平面的长和宽:a0=a1+(a-a1)*h22/h2;b0=b1+(b-b1)*h22/h2;计算台体的理论总容积:v0=(h2-h22)*(a*b+sqrt(a*b*a0*b0)+a0*b0);计算台体和立体理论总容积:v3=h2*(a*b+sqrt(a*b*a1*b1)+a1*b1)/3+a*b*h1;计算实际使用仪表量程:lc=h1+h2-h11-h22;计算实际使用仪表量程内台体和立体理论总容积;v4=(h2-h22)*(a*b+sqrt(a*b*a0*b0)+a0*b0)/3+a*b*(h1-h11);计算实际料位容积:v:为料仓总容积;v1:为立体实际容积;v2:为台体实际容积;当h≦0时,v1=0,v2=0,v=v1+v2=0;当0<h≦(h2-h22)时,a2=a0+(a-a1)*h/h2;b2=b0+(b-b1)*h/h2;v2=h*(a2*b2+sqrt(a2*b2*a0*b0)+a0*b0)/3;v1=0;v=v1+v2=v2;当(h2-h22)<h≦(h1-h11+h2-h22)时;a2=a;b2=b;v1=a*b*(h-h2+h22);v2=v0;v=v1+v2=v1+v0。作为本发明的一种改进,所述步骤2)虚拟密度计算具体如下,物料的重量w等于物料的容积v乘以物料的密度ρ,在实际应用时,由于物料为颗粒状,颗粒之间存在缝隙,相同重量的物料实际占用的空间比理论空间要大,在料仓中物料的密度比物料理论密度要小,在计算中用虚拟密度ρ'代替理论密度ρ,使得物料的重量计算更接近真实值。当皮带系统开启,卸料小车开始对位;当卸料小车达到设定料仓,系统自动记录当前仓的料位h,同时给皮带秤系统发出信号自动对累积重量清零;当地下料仓的对应振动给料机开始振动,开始下料,皮带秤系统开始累积上料重量;当累积重量达到设定重量时,振动给料机自动停止振动,皮带秤系统继续累积上料重量;当该批次料全部进仓,小车离开当前仓,系统自动记录当前仓的料位h'和皮带秤累积重量w';通过卸料前后两次料位变化(h→h'),系统计算出料仓的容积变化v';最后系统计算该次上料的物料虚拟密度ρ'=w'/v';虚拟密度ρ'准确性判断:如果mρ≦ρ'≦ρ(0<m<1),系统认为虚拟密度ρ'计算合理,自动记录该数据;否则系统认为数据有误,发出报警(物料累积重量有误或物料料位探测有误)。系统自动记录该料仓物料n次虚拟密度有效数据,然后取平均值作为该物料在该料仓的虚拟密度ρ'。在计算模块中density为虚拟密度ρ'的输入点。作为本发明的一种改进,所述步骤3)料仓物料重量计算具体步骤如下,m4:仪表设定量程范围内物料理论总重量;m4=v4*ρ',单位kg;m:仪表设定量程范围内料仓内物料重量,m=v*ρ',单位kg;mt:仪表设定量程范围内料仓内物料重量,mt=v*ρ'/1000,单位t;m_sp(mt_sp):到达设定高料位wh,给料仓上料的需求量单位kg(t);m_sp=m4-m;num:料仓所剩物料还够转炉炼几炉,num=m/m1。作为本发明的一种改进,所述步骤4)料仓料位报警设定具体如下,料仓料位共设4个等级的料位,分别为:低低料位报警al、低料位报警wl、高料位报警wh、高高料位报警ah,由hmi画面设定;n1为低低料位时,还足够炼钢使用的炉数;n2为低料位时,还够炼钢使用德炉数;n1和n2左前方打“√”选择,为mode的选择;低低料位报警al、低料位报警wl有两种方式设定,由mode选择;当无“√”选择,mode=o,根据料位值设定判断al和wl;当有“√”选择,mode=1,目前料仓还够炼钢使用炉数设定,计算模块中输入点m1,为炼钢转炉每炉使用量,来自炼钢l2系统;t即temp1延时输出报警,当t前方的打“√”,根据设定值延时输出报警信号。作为本发明的一种改进,所述步骤5)料位报警输出具体如下,当h≧ah,系统输出:qlim_ua=1料仓高高料位报警;qlim_ua_if料仓高高料位报警值;qlim_ua_num料仓高高料位预计可以炼多少炉;当wh≦h<ah,系统输出:qlim_uw=1料仓高料位报警信号;qlim_uw_if料仓高料位报警值;qlim_uw_num料仓高料位预计可以炼多少炉;当al≦h<wl,系统输出:qlim_lw=1料仓低料位报警信号;qlim_lw_if料仓低料位报警值;qlim_lw_num料仓低料位可以炼多少炉;当h≦al,系统输出:qlim_lw=1料仓低低料位报警信号;qlim_lw_if料仓低低料位报警值;qlim_lw_num料仓低低料位预计可以炼多少炉。作为本发明的一种改进,所述步骤6)料位信息显示具体如下:61)料仓的料位值显示;62)料仓料位的条形显示:当料位接近“0”时,条形显示为灰色;当料位不超过高料位时,条形显示为浅蓝色;当料位超过高料位,且低于高高料位时,条形显示为粉红色;当超过高高料位时,条形显示为深红色;通过不同颜色直观显示料仓的料位状态;63)上料优先级显示;根据料位状态、够转炉使用的炉数、料仓号顺序、料仓投用选择等计算出一个数值,然后根据数值的比较得出料仓的上料优先级,作为上料时先后次序。64)上料量mt_sp显示;65)料仓号,就是该料仓的编号,与料仓顺序号对应:料仓号f501f502f503f504f505f506f507f508f509f510顺序号12345678910料仓号f511f512f513f514f401f402f403f404顺序号1112131415161718料仓号f405f406f407f408f409f410f411f412f413f414顺序号1920212223242526272866)料仓投用选择,当选中时,表示该料仓需要上料,qdis_if=1;显示为绿色;当未选中时,表示该料仓禁止上料,qdis_if=0;显示为红色。作为本发明的一种改进,所述步骤7)上料优先计算具体如下:计算料仓优先值n;n=(30-n0)*10+(10-n3)*100+n4n0:为料仓顺序号n1:为当前料仓的料还够转炉炼多少炉num(m/m1)当n3≧10,n3=10;n2:当料位h≧ah时,n4=-1000;当料位wl<h<ah时,n4=0;当料位al≦h<wl时,n4=500;当料位h≦al时,n4=1000;当料仓投用未选中时,n4=-1000;料仓优先值比较:根据优先值越大,顺序越靠前的原则,对料仓进行排序。当n<0时,该料仓的顺序为99,表示该料仓不需要上料。相对于现有技术,本发明具有如下优点,该技术方案首先进行参数设定,根据料仓和生产情况设定高高料位ah、高料位wh、低料位wl和低低料位al.mode选择和是否延时输出报警。系统自动计算并显示出料位值和可上料量等,供操作人员上料时设定加料重量;然后选择高位料仓那些料仓需要加料,系统对已选的料仓进行排序。供操作人员上料时参考。在上料过程中,根据料位信息实时给出报警信息,提醒操作人员及时采取应对措施。通过该方法,实时监控高位料仓的物料情况,为操作人员上料提供依据,提高了上料的准确性,避免了上料不足和铺料,同时也不需要安排专人在环境恶劣的高位料仓平台观察料位,大大减少操作强度,进一步提升生产效率。附图说明图1为整个系统结构示意图;图2为高位料仓示意图;图3为高位料仓料位计算模块示意图;图4为料位报警设定示意图;图5为料仓料位信息显示示意图;图中:1、地下料仓,2、第一皮带,3、皮带秤系统,4、第二皮带,5、第三皮带,6、卸料小车,7、高位料仓。具体实施方式:为了加深对本本发明的理解,下面结合附图对本实施例做详细的说明。实施例1:参见图1-图5,一种炼钢高位料仓料位处理方法,所述处理方法包括以下步骤:1)料仓的容积计算;由于料位最高点是下料口的位置,不适合安装料位探测装置,一般选择在稍远离下料口,探测物料较低的位置,避免下料时的振动影响料位探测装置的准确性,也避免堆料时损坏料位探测装置。根据料仓的形状,将料仓分为上部的立方体和下部的台体。如图所示,将料仓分为6个平面,分别是a、a0、a1、a2、a3、和a4平面,a0平面为设定的料位o平面,a2平面为料位探测装置探测的料面,a4平面为设定料位的最高平面。各平面的长/宽分别是a/b、a0/b0、a1/b1、a2/b2、a3/b3和a4/b4;a0平面和a1平面的高度为h22;a0平面和a2平面的高度为h;a平面和a4平面的高度为h11;a平面和a3平面的高度为h1;a0平面和a4平面之间是实际应用时,探测装置的量程(lc),计算料仓中物料重量(m)和上料需求量(m_sp)。当设定值a>0,b>0,h1>0,h11>0,a1>0,b1>0,h2>0,h22>0都同时满足,系统认为设定值正确;如有一项不满足,系统认为设定值错误,系统发出报警信号(alarm_sp)。计算a0平面的长和宽:a0=a1+(a-a1)*h22/h2b0=b1+(b-b1)*h22/h2计算台体的理论总容积:v0=(h2-h22)*(a*b+sqrt(a*b*a0*b0)+a0*b0)计算台体和立体理论总容积:v3=h2*(a*b+sqrt(a*b*a1*b1)+a1*b1)/3+a*b*h1计算实际使用仪表量程:lc=h1+h2-h11-h22;计算实际使用仪表量程内台体和立体理论总容积v4=(h2-h22)*(a*b+sqrt(a*b*a0*b0)+a0*b0)/3+a*b*(h1-h11);计算实际料位容积:v:为料仓总容积;v1:为立体实际容积;v2:为台体实际容积;当h≦0时,v1=0,v2=0,v=v1+v2=0;当0<h≦(h2-h22)时,a2=a0+(a-a1)*h/h2;b2=b0+(b-b1)*h/h2;v2=h*(a2*b2+sqrt(a2*b2*a0*b0)+a0*b0)/3;v1=0;v=v1+v2=v2当(h2-h22)<h≦(h1-h11+h2-h22)时a2=a;b2=b;v1=a*b*(h-h2+h22);v2=v0;v=v1+v2=v1+v02)虚拟密度计算;物料的重量w等于物料的容积v乘以物料的密度ρ。在实际应用时,由于物料为颗粒状,颗粒之间存在缝隙,相同重量的物料实际占用的空间比理论空间要大,在料仓中物料的密度比物料理论密度要小,在计算中用虚拟密度ρ'代替理论密度ρ,使得物料的重量计算更接近真实值。具体计算方法如下:当皮带系统开启,卸料小车开始对位;当卸料小车达到设定料仓,系统自动记录当前仓的料位h,同时给皮带秤系统发出信号自动对累积重量清零;当地下料仓的对应振动给料机开始振动,开始下料,皮带秤系统开始累积上料重量。当累积重量达到设定重量时,振动给料机自动停止振动,皮带秤系统继续累积上料重量。当该批次料全部进仓,小车离开当前仓,系统自动记录当前仓的料位h'和皮带秤累积重量w'。通过卸料前后两次料位变化(h→h'),系统计算出料仓的容积变化v'最后系统计算该次上料的物料虚拟密度ρ'=w'/v'。虚拟密度ρ'准确性判断:如果mρ≦ρ'≦ρ(0<m<1),系统认为虚拟密度ρ'计算合理,自动记录该数据。否则系统认为数据有误,发出报警(物料累积重量有误或物料料位探测有误)。系统自动记录该料仓物料n次虚拟密度有效数据,然后取平均值作为该物料在该料仓的虚拟密度ρ'。在计算模块中density为虚拟密度ρ'的输入点;3)料仓物料重量计算;m4:仪表设定量程范围内物料理论总重量;m4=v4*ρ',单位kg;m:仪表设定量程范围内料仓内物料重量,m=v*ρ',单位kg;mt:仪表设定量程范围内料仓内物料重量,mt=v*ρ'/1000,单位t;m_sp(mt_sp):到达设定高料位wh,给料仓上料的需求量单位kg(t);m_sp=m4-m;num:料仓所剩物料还够转炉炼几炉。num=m/m1;4)料仓料位报警设定;如图,料仓料位共设4个等级的料位,分别为:低低料位报警al、低料位报警wl、高料位报警wh、高高料位报警ah,由hmi画面设定;n1为低低料位时,还够炼钢使用炉数;n2为低料位时,还够炼钢使用炉数;n1和n2左前方打“√”选择,为mode的选择;低低料位报警al、低料位报警wl有两种方式设定,由mode选择;当无“√”选择,mode=o,根据料位值设定判断al和wl;当有“√”选择,mode=1,目前料仓还够炼钢使用炉数设定。计算模块中输入点m1,为炼钢转炉每炉使用量,来自炼钢l2系统;t(temp1)延时输出报警,当t前方的打“√”,根据设定值延时输出报警信号。5)料位报警输出;当h≧ah,系统输出:qlim_ua=1料仓高高料位报警;qlim_ua_if料仓高高料位报警值;qlim_ua_num料仓高高料位预计可以炼多少炉;当wh≦h<ah,系统输出:qlim_uw=1料仓高料位报警信号;qlim_uw_if料仓高料位报警值;qlim_uw_num料仓高料位预计可以炼多少炉;当al≦h<wl,系统输出:qlim_lw=1料仓低料位报警信号;qlim_lw_if料仓低料位报警值;qlim_lw_num料仓低料位可以炼多少炉;当h≦al,系统输出:qlim_lw=1料仓低低料位报警信号;qlim_lw_if料仓低低料位报警值;qlim_lw_num料仓低低料位预计可以炼多少炉;6)料位信息显示,如图5;61)料仓的料位值显示。62)料仓料位的条形显示:当料位接近“0”时,条形显示为灰色;当料位不超过高料位时,条形显示为浅蓝色;当料位超过高料位,且低于高高料位时,条形显示为粉红色当超过高高料位时,条形显示为深红色通过不同颜色直观显示料仓的料位状态。63)上料优先级显示根据料位状态、够转炉使用的炉数、料仓号顺序、料仓投用选择等计算出一个数值,然后根据数值的比较得出料仓的上料优先级,作为上料时先后次序。64)上料量mt_sp显示65)料仓号,就是该料仓的编号,与料仓顺序号对应:料仓号f501f502f503f504f505f506f507f508f509f510顺序号12345678910料仓号f511f512f513f514f401f402f403f404顺序号1112131415161718料仓号f405f406f407f408f409f410f411f412f413f414顺序号1920212223242526272866)料仓投用选择,当选中时,表示该料仓需要上料,qdis_if=1;显示为绿色。当未选中时,表示该料仓禁止上料,qdis_if=0;显示为红色。7)上料优先计算;计算料仓优先值n;n=(30-n0)*10+(10-n3)*100+n4;n0为料仓顺序号;n1为当前料仓的料还够转炉炼多少炉num(m/m1);当n3≧10,n3=10;n2当料位h≧ah时,n4=-1000;当料位wl<h<ah时,n4=0;当料位al≦h<wl时,n4=500;当料位h≦al时,n4=1000;当料仓投用未选中时,n4=-1000;料仓优先值比较:根据优先值越大,顺序越靠前的原则,对料仓进行排序。当n<0时,该料仓的顺序为99,表示该料仓不需要上料。通过该方法,实时监控高位料仓的物料情况,为操作人员上料提供依据,提高了上料的准确性,避免了上料不足和铺料,同时也不需要安排专人在环境恶劣的高位料仓平台观察料位,大大减少操作强度,进一步提升生产效率。需要说明的是上述实施例,并非用来限定本本发明的保护范围,在上述技术方案的基础上所作出的等同变换或替代均落入本本发明权利要求所保护的范围。当前第1页12