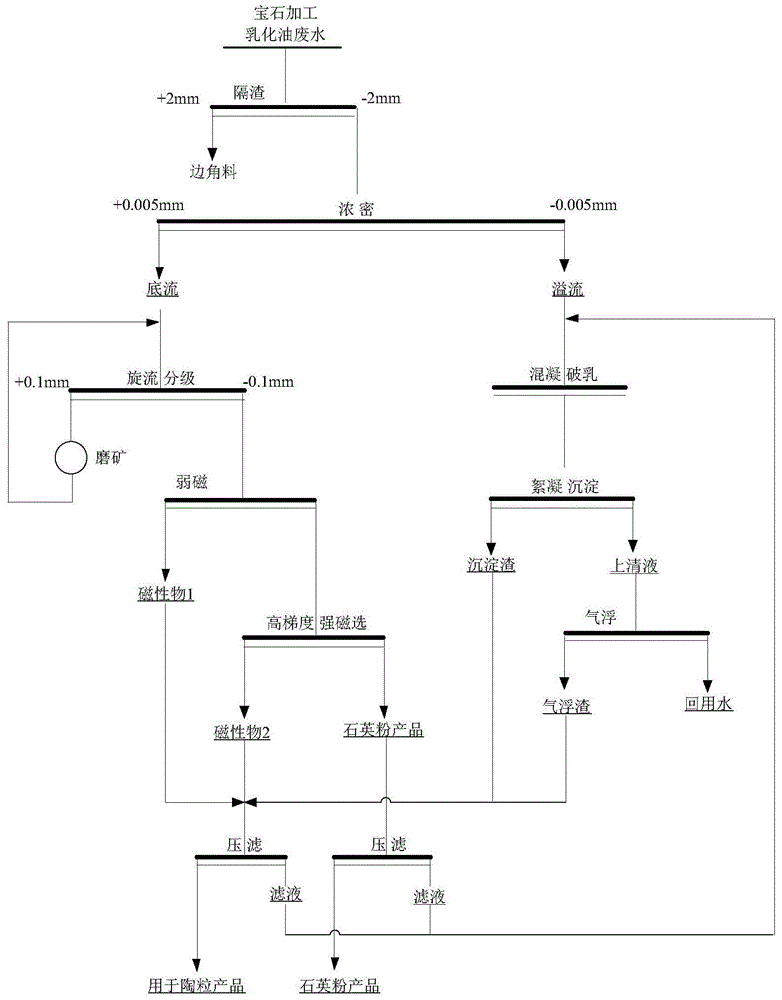
本发明涉及工业废水处理
技术领域:
,特别是涉及一种宝石加工行业产生的含乳化油泥废水的处理方法。
背景技术:
:我国是珠宝生产和消费大国,全国共有30多个具有世界影响力的较大不同类型的宝石加工基地。例如广东博罗四角楼就是国内较大的彩色宝石加工贸易集散地,高峰时期有3000多家小作坊式加工厂。广东博罗四角楼宝石加工贸易集散地处理加工的原料均为质地较纯、颜色多彩的宝石石料。宝石石料来自世界各地,其中包括许多珍贵且稀少的宝石原料。加工原料主要有玛瑙、水晶、石英石和各种带色高硅宝石。宝石加工采用的工艺操作主要有石料开料、切割定型、磨珠、钻孔、抛光等工序。在加工过程中为了保护切割刀具,加工厂一般向切割冷却水中添加少量的乳化油。切割冷却水在循环使用一段时间后,就需要清理循环池中的含乳化油泥浆。还以广东博罗四角楼为例,长期以来四角楼地区的宝石加工厂加工过程中产生的大量含乳化油泥的废液浆,只是经过简单的沉淀处理,沉淀渣到处乱倒,废水随意排放,给当地带来了严重的环境污染,并制约着宝石加工产业的可持续性发展。为有效解决宝石加工产业带来的环境污染问题,有必要开发一种加工废水的处理工艺,尤其是含有乳化油泥的加工废水的处理方法,使宝石加工过程中产生的废水得到合理利用,变废为宝。技术实现要素:本发明主要解决的技术问题是提供一种宝石加工行业产生的含乳化油泥废水的处理方法,以有效利用目前宝石加工行业产生的废水,并解决困扰已久的环境污染问题。为解决上述技术问题,本发明采用的技术方案是:一种宝石加工行业含乳化油泥废水的处理方法,包括步骤:将宝石加工行业产生的含乳化油泥废水收集后先隔渣去除粗颗粒,隔渣后的料浆经浓密机浓密处理,得到浓密机底流和浓密机溢流;所述浓密机底流用旋流器分级,旋流器分级得到的沉砂粗颗粒进入球磨机形成闭路磨矿,磨细至-0.10mm,旋流器分级得到颗粒粒径-0.10mm的旋流器溢流;所述旋流器溢流先弱磁选、之后强磁选进行除铁,分别得到磁性产品和石英粉产品;所述浓密机溢流经混凝破乳,之后再絮凝沉淀,得到沉淀渣和上清液;所述上清液再进行气浮处理,分离得到气浮渣和可作为宝石加工过程用水的回用水;所述磁性产品、沉淀渣、气浮渣合并后过滤,得到用于生产陶粒产品的原料,所得滤液返回与所述浓密机溢流混合;所述石英粉产品过滤,得到石英粉固体产品和滤液,所得滤液返回与所述浓密机溢流混合。作为本发明一种优选的实施方案,宝石加工行业含乳化油泥废水的处理方法具体包括以下步骤:s1:将宝石加工行业产生的含乳化油泥废水收集后进行隔渣处理,采用孔径为2mm的隔网,分离得到的+2mm的粗颗粒产品可作为宝石边角料使用,隔渣后的料浆中所含颗粒物粒径小于2mm;s2:所述隔渣后的料浆经浓密机浓密处理,得到浓密机底流和浓密机溢流,所述浓密机底流中所含颗粒物的粒径为+0.005mm,所述浓密机溢流中所含颗粒物的粒径为-0.005mm;s3:所述浓密机底流用旋流器分级,旋流器分级得到的+0.10mm的沉砂粗颗粒进入球磨机形成闭路磨矿,磨细至-0.10mm,旋流器分级得到颗粒粒径为-0.10mm的旋流器溢流;s4:所述旋流器溢流先弱磁选除铁,得到磁性物1和弱磁选尾矿,所述弱磁选尾矿再经强磁选进行除铁,分别得到磁性物2和石英粉产品;s5:所述浓密机溢流添加混凝剂进行混凝破乳,之后再使用絮凝剂絮凝沉淀,得到沉淀渣和上清液;所述上清液再进行气浮处理,分离得到气浮渣和可作为宝石加工过程用水的回用水;s6:所述磁性物1、磁性物2、沉淀渣、气浮渣合并后过滤,得到用于生产陶粒产品的原料,所得滤液返回与所述浓密机溢流混合;s7:所述石英粉产品过滤,得到石英粉固体产品和滤液,所得滤液返回与所述浓密机溢流混合。优选地,所述球磨机采用陶瓷内衬球磨机,球磨机磨矿介质采用陶瓷球,可以减少铁质二次污染。优选地,所述弱磁选的磁选强度为0.1~0.3t。优选地,所述强磁选采用高梯度磁选机,磁选强度为0.8t~1.0t。优选地,所述浓密机溢流混凝破乳时添加的混凝剂为聚合氯化铝、聚合硫酸铝、硫酸铁、氯化铁、石灰中的一种或多种的混合,添加量为200~800mg/l(每升浓密机溢流);之后再絮凝沉淀时,添加的絮凝剂为阴离子聚丙烯酰胺,添加量为1~4mg/l(每升浓密机溢流)。优选地,所述上清液气浮处理时,先加入混凝剂,之后加絮凝剂,然后再进行气浮处理。进一步优选地,所述混凝剂为聚合氯化铝、聚合硫酸铝、硫酸铁、氯化铁、石灰中的一种或多种的混合,用量为10~60mg/l(每升上清液);所述絮凝剂为阴离子聚丙烯酰胺,用量为1~3mg/l(每升上清液)。本发明得到的所述石英粉固体产品中sio2的含量为98.00~99.70%,fe2o3的含量为0.05~0.30%,所述含量均为质量百分比含量。处理得到的所述回用水中codcr的去除率为98.00~99.80%,可作为宝石加工过程用水使用。本发明提供了一种宝石加工含乳化油泥浆废水集中处理的方法,首先将宝石加工产生的含乳化油泥的废水集中收集,之后隔渣处理,将粒径大于2mm的颗粒物分离出来,可以作为边角料再使用;隔渣得到的料浆中所含颗粒物粒径小于2mm。之后隔渣后料浆进入浓密机浓密处理,将料浆中-0.005mm的难沉微细粒级直接脱除,直接进入废水处理工序,料浆废水得到浓缩。得到的浓密机底流所含颗粒物粒径在0.005mm以上,采用“磨矿-磁选除铁”工艺处理,可保证分选的浓度。首先采用旋流器和陶瓷球磨机组成闭路磨矿系统,磨细至-0.10mm粒级,使料浆废水中粗颗粒磨细至磁选分离选别适宜的粒级,采用陶瓷球磨机和陶瓷球进行磨矿可以避免铁质二次污染。旋流器溢流通过“弱磁-强磁”选别工艺进行除铁,得到磁性物1、磁性物2和石英粉产品。强磁选作业选用非金属矿物除杂和提纯效果显著的周期式高梯度磁选机,保证除铁效率,提高石英粉产品质量。浓密机溢流中含微细悬浮物,通过添加混凝剂破坏其稳定体系并生成微小聚集体,再添加絮凝剂进行絮凝,微细悬浮物起到“凝聚核”作用,增大絮团粒径,加速固液分离,显著提升混凝破乳的效果,降低混凝剂用量,分离得到沉淀渣和上清液;上清液中含有少量极细粒油分子和微粉颗粒难以沉淀,通过气浮法进一步去除,采用气浮法可以让该部分微粒上浮去除,弥补只进行混凝沉降处理不能有效去除少量极细粒油分子和微粉颗粒的难题,处理后废水达到回用标准。处理得到的磁性物、沉淀渣、气浮渣合并后过滤,可得到用于生产陶粒产品的原料;所得滤液返回与所述浓密机溢流混合后继续进入后续流程。石英粉产品经压滤后得到石英粉固体产品,其中sio2的含量为98.00~99.70%,fe2o3的含量为0.05~0.30%,所得滤液返回与所述浓密机溢流混合后继续进入后续流程。处理得到的回用水中codcr的去除率为98.00~99.80%,可作为宝石加工过程用水使用。本发明是针对含乳化油泥的宝石加工废水的处理方法,结合选矿和废水处理技术,使固废渣得到资源化综合利用,处理后废水达到回用标准,工艺简单,药剂省,流程易操作,便于推广。附图说明图1是本发明提供的一种宝石加工行业含乳化油泥废水的处理工艺流程图。具体实施方式下面通过具体实施例对本发明的技术方案进行详细说明。在以下实施例中,未特别说明时,使用的药剂均为市售商品。各实施例中的浓度或含量均为质量百分比。实施例1采用图1所示的工艺流程进行处理,所处理的对象是石英石加工过程中产生的含乳化油泥浆废水,废水浓度为6.01%,其中多元素分析见表1所示。表1元素al2o3sio2fe2o3k2omgocaona2otio2含量(%)0.1999.10.300.0110.0210.0120.0090.02将所示含乳化油泥浆废水进行下列处理:(1)乳化油泥浆废水通过隔渣,隔除+2mm粗颗粒,隔渣后泥浆废水进入浓密机浓密,得到浓密机溢流和浓密机底流;浓密机底流通过旋流器分级,沉砂粗颗粒进入球磨机形成闭路磨矿,磨细至-0.10mm,分离得到旋流器溢流。球磨机采用陶瓷内衬球磨机,球磨机磨矿介质采用陶瓷球,可以减少铁质二次污染。(2)旋流器溢流通过“弱磁-强磁”选别工艺进行除铁;弱磁选作业磁选强度为0.2t,强磁选作业选用周期式高梯度磁选机,磁选强度为0.8t;旋流器溢流通过弱磁选得到磁性物1和弱磁尾矿;弱磁尾矿再进行高梯度强磁选得到磁性物2和石英粉产品。(3)浓密机溢流水质成分分析详见表2,浓密机溢流通过慢速搅拌,先添加混凝剂聚合氯化铝400mg/l,之后添加絮凝剂阴离子聚丙烯酰胺2mg/l;通过沉淀得到沉淀渣和上清液。表2分析项目计量单位检测结果ph值无量纲6.56悬浮物mg/l22500浊度ntu7590codcrmg/l10600(4)所得上清液成分分析见表3,上清液中含有少量极细粒油分子和微粉颗粒,进一步混凝处理,添加的混凝剂为聚合氯化铝25mg/l,之后添加絮凝剂阴离子聚丙烯酰胺,用量为1mg/l;然后通过气浮法处理得到气浮渣和回用水,回用水成分详见4。表3分析项目计量单位检测结果ph值无量纲6.55悬浮物mg/l30浊度ntu41codcrmg/l296.6表4分析项目计量单位检测结果ph值无量纲7.00悬浮物mg/l5浊度ntu3codcrmg/l24(5)将“弱磁-强磁”除铁作业的磁性物1、磁性物2,混凝沉淀的沉淀渣和气浮得到的气浮渣合并,之后压滤得到用于生产陶粒产品的原料。所得滤液返回与浓密机溢流混合后继续进入后续流程。石英粉产品经压滤后得到石英粉固体产品,其中sio2的含量为99.43%,fe2o3的含量为0.09%,所得滤液返回与浓密机溢流混合后继续进入后续流程。处理得到的回用水中codcr的去除率为99.77%,可作为宝石加工过程用水使用。实施例2采用图1所示的工艺流程进行处理,所处理的对象是高硅杂石加工过程中产生的含乳化油泥浆废水,废水浓度为6.37%,其中多元素分析见表5所示。表5元素al2o3sio2fe2o3k2omgocaona2otio2含量(%)0.2298.810.570.070.010.010.08<0.01将所示含乳化油泥浆废水进行下列处理:(1)乳化油泥浆废水通过隔渣,隔除+2mm粗颗粒,隔渣后泥浆废水进入浓密机浓密,得到浓密机溢流和浓密机底流;浓密机底流通过旋流器分级,沉砂粗颗粒进入球磨机形成闭路磨矿,磨细至-0.10mm,分离得到旋流器溢流。球磨机采用陶瓷内衬球磨机,球磨机磨矿介质采用陶瓷球,可以减少铁质二次污染。(2)旋流器溢流通过“弱磁-强磁”选别工艺进行除铁;弱磁选作业磁选强度为0.15t,强磁选作业选用周期式高梯度磁选机,磁选强度为1.0t;旋流器溢流通过弱磁选得到磁性物1和弱磁尾矿;弱磁尾矿再进行高梯度强磁选得到磁性物2和石英粉产品。(3)浓密机溢流水质成分分析详见表6,浓密机溢流通过慢速搅拌,先添加混凝剂石灰100mg/l和聚合硫酸铝300mg/l,之后添加絮凝剂阴离子聚丙烯酰胺3mg/l;通过沉淀得到沉淀渣和上清液。表6分析项目计量单位检测结果ph值无量纲7.05悬浮物mg/l16400浊度ntu7740codcrmg/l11600(4)所得上清液成分分析见表7,上清液中含有少量极细粒油分子和微粉颗粒,进一步混凝处理,添加的混凝剂为聚合硫酸铝40mg/l,之后添加絮凝剂阴离子聚丙烯酰胺,用量为1mg/l;然后通过气浮法处理得到气浮渣和回用水,回用水成分详见8。表7分析项目计量单位检测结果ph值无量纲6.66悬浮物mg/l36浊度ntu45codcrmg/l326.5表8分析项目计量单位检测结果ph值无量纲7.00悬浮物mg/l6浊度ntu3codcrmg/l31(5)将“弱磁-强磁”除铁作业的磁性物1、磁性物2,混凝沉淀的沉淀渣和气浮得到的气浮渣合并,之后压滤得到用于生产陶粒产品的原料。所得滤液返回与浓密机溢流混合后继续进入后续流程。石英粉产品经压滤后得到石英粉固体产品,其中sio2的含量为99.27%,fe2o3的含量为0.16%,所得滤液返回与浓密机溢流混合后继续进入后续流程。处理得到的回用水中codcr的去除率为99.73%,可作为宝石加工过程用水使用。虽然,上文中已经用一般性说明、具体实施方式及试验,对本发明作了详尽的描述,但在本发明基础上,可以对之作一些修改或改进,这对本领域技术人员而言是显而易见的。因此,在不偏离本发明精神的基础上所做的这些修改或改进,均属于本发明要求保护的范围。当前第1页12