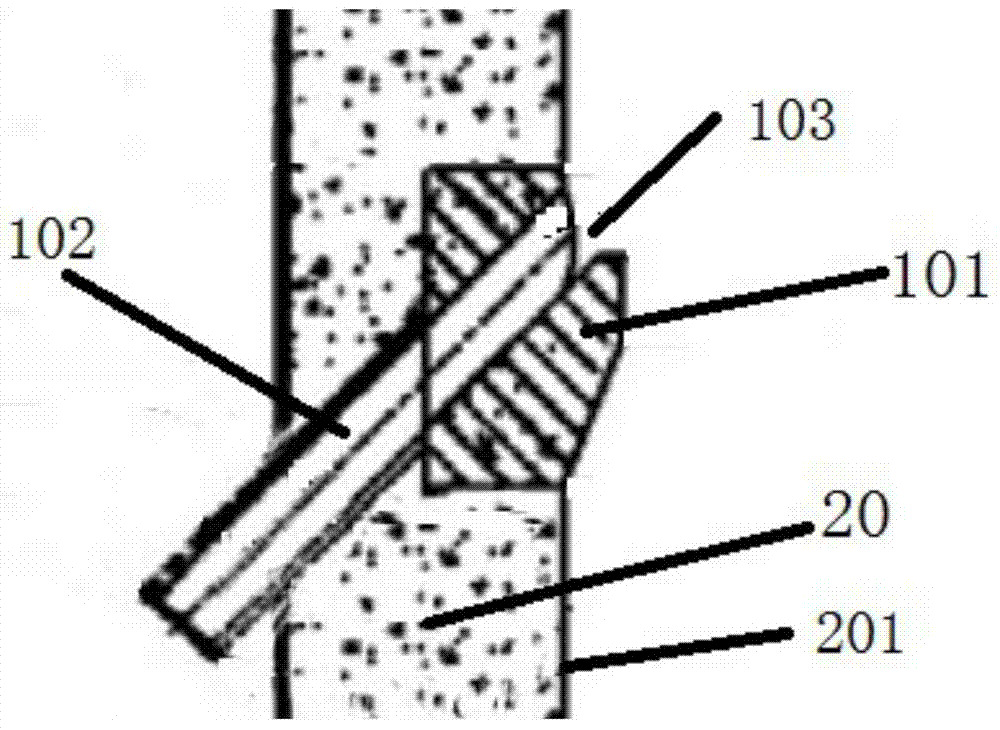
本发明涉及流化反应器领域,尤其涉及一种用于连续流化床反应器的熔融物收集槽。
背景技术:流化床反应器是一种利用气体或液体通过颗粒状固体层而使固体颗粒处于悬浮运动状态,并进行气固相反应过程或液固相反应过程的反应器,可以实现固体物料的连续输入和输出。但是由于流化床反应器往往为封闭式结构,反应物及产物的连续输入和输出限制条件较多,特别是在反应产物相态复杂的情况下,液态的物料,比如高温的熔融物,往往会凝聚在反应器壁上难以参与反应也难以导出,如果流至物料的进出口会形成堵塞,如果粘附在监控类部件上还会形成包覆膜影响监控的准确性。通常通过在反应器上扩大排渣口或通过抽吸装置形成负压的方式来加快物料的排除,从而防止堵塞。但是由于反应器内通常为高温高压,排渣口与相对低压低温的外界环境连通,扩大排渣口后,一方面排渣口内部温度降低过快,高温的液态物料冷却后粘度增大或直接凝固,使物料更难以排出,堵塞仍然容易形成;另一方面在连续生产过程中,需要使排渣口保持畅通状态,以连续排除物料,排渣口过大或者在排渣口抽吸形成负压会使反应器内压力难以保持,破坏反应条件,也使得反应器内的气流方向受到干扰,影响反应的进行。流化床反应器内的反应往往比较复杂,不同位置的生成物也有差异,比如液态物料和固体其中含有的副产物种类往往差异较大,未反应原料的含量也各不相同。但是考虑到增加分别回收液态和固态物料的装置往往会使反应器内部结构更加复杂,提高制造成本;而流化床反应器需要反应器内部尽量平整光滑,避免形成死角,另外也要避免形成挡板效应扰乱气流,因此现有技术中往往采用混合回收后再分离的方法,这就增加了物料分离成本。因此,迄今为止的高温流化床都存在因液态废料冷凝堵塞气孔或出渣口,而导致无法连续生产的问题。由于连续生产对于生产成本和最终产品一致性有着重要影响,因此这也是本领域亟待解决的问题。中国专利CN203803474U公布了一种气液固三项流化床反应器,通过设置一条备用的反应器进料管,返回管堵塞时,在不影响正常进料的前提下,开启备用管利用溶剂疏通进料管。但是该技术方案并不能将液态物料与固态物料分离,只是在发生堵塞时进行疏通,并不能从根源上解决堵塞的问题。而且如果液态物料由于粘度过大不能及时导出凝固在反应器壁上,清理更加困难。
技术实现要素:针对现有技术之不足,本发明提供一种用于连续流化床反应器的熔融物收集槽,其特征在于,所述收集槽包括设置在反应器的侧壁部上的至少两个截流槽和穿过所述反应器壁的至少两个导流管,其中所述截流槽被构成为位于侧壁部上向反应腔凸出的凸肩与侧壁部形成的环绕侧壁部的槽体,所述截流槽在水平方向上环绕所述侧壁部至少一部分以收集沿侧壁部流下的熔融物;所述凸肩从所述侧壁部斜向上凸出。凸肩的靠近侧壁部的一面与竖直的侧壁部呈一定的角度,从而形成可以容纳流体的沟槽。所述凸肩的背向所述侧壁部的一面,即凸肩的外侧,其在竖直截面上的轮廓呈非直线型,该轮廓的下部与侧壁部相接,上部伸入反应腔中。所述凸肩的背向所述侧壁部的一面,即凸肩的外侧,其在竖直方向的上端比下端更为靠近反应腔中心轴线。即凸肩靠近反应腔中心线的一侧的上端比靠近反应腔中心线的一侧的下端距离与之相接的反应器的侧壁部更远。从而由所述凸肩形成上部开口比下部开口窄的腔体结构。根据一个优选的实施方式,所述反应器的进料口上方至少有一个截流槽以收集进料口上方的侧壁部流下的熔融物,所述截流槽处至少有一个导流管以使截流槽与反应器外部连通;和/或所述反应器排渣口的上方至少有一个截流槽以收集排渣口上方的侧壁部流下的熔融物,所述截流槽处至少有一个导流管以使截流槽与反应器外部连通。根据一个优选的实施方式,所述凸肩的外侧在竖直方向上部为竖直面形,下部为斜面形。从而使所述凸肩的外侧在竖直方向上分为大致呈直筒状的上部,和大致呈截顶空心锥形的下部。根据一个优选的实施方式,所述反应器的顶部与侧壁部平滑曲线连接处的曲率最大部与所述凸肩的外侧的上端大致位于同一竖直面上。优选的,与所述凸肩的外侧相比,在所述反应器的顶部与侧壁部连接区域中的曲率最大部在径向上处于更为靠外的位置。即相比于所述凸肩的外侧,所述曲率最大部距离所述反应腔中心轴线较远。根据一个优选的实施方式,所述导流管位于反应器壁外侧的一端连接保压装置,以使导流管的两端保持气压大致相同。优选的导流管位于反应器壁外侧的一端伸出反应器壁一定的长度,方便收集流出的熔融物,和/或连接保压装置。更优选的,所述保压装置为抽气机或气压罐。根据反应器内的压力适时调节,使得反应器内气压保持大致平衡,防止由于导流管泄压而是反应器内气流收到不良扰动。或者调节导流管位于反应器壁外侧的一端的气压以形成微负压,使得导流管内的熔融物能够在气压差的辅助下导出反应器。根据一个优选的实施方式,所述导流管在与所述侧壁部相接处和与所述凸肩的相接处平滑过渡;所述导流管斜向下穿过所述反应器的侧壁部连通至反应器的外部,以将截流槽中收集的熔融物从反应器中导出。根据一个优选的实施方式,所述截流槽至少呈部分螺旋形环绕所述侧壁部的至少一部分;或所述截流槽呈至少两段相接的螺旋形环绕所述侧壁部的至少一部分。根据一个优选的实施方式,所述导流管位于反应器内部的侧壁部的一端至少设置在所述截流槽在竖直方向的最低处。根据一个优选的实施方式,所述凸肩的面对所述侧壁部的内侧与侧壁部形成竖直横截面大致为V字形的凹槽,所述凸肩的外侧与所述侧壁部的连接处平滑过渡,所述凸肩的外侧在竖直方向呈流线型、斜直线型、弧形或折线型。根据一个优选的实施方式,在所述导流管口处,所述侧壁部向反应器壁内部凹陷,使导流管处侧壁部与凸肩形成的截流槽的单位长度容量比其他部分截流槽的单位长度容量更大,以形成蓄积池结构。如果通过截流槽流动至导流管处的熔融物过多,没有及时通过导流管排出至反应器外部时,所述蓄积池结构能够暂时蓄积未排出的熔融物,起到缓冲作用,从而防止熔体溢出。根据一个优选的实施方式,所述凸肩由耐高温性比所述侧壁部更好的材料制成。所述凸肩在与所述侧壁部相接处有一部分嵌埋在所述反应器的侧壁中,以使凸肩固定在所述反应器壁上。本发明通过在侧壁部上设置熔融物收集槽,将反应器壁上粘附的高温液态物质收集起来,通过引流导出反应器,一方面有效的分离回收物料,防止与固态残渣混合,另一方面防止液态熔融物堵塞物料的进出口。同时在反应器壁上多个位置设置收集槽,使得不同的熔融物料分开回收,减少了物料分离程序,节约了成本。而且本发明通过设置熔融物收集槽,使得流化床反应器得以在1600摄氏度左右的工作环境下实现连续生产。附图说明图1是本发明连续流化床反应器的结构示意图;和图2是本发明用于连续流化床反应器的熔融物收集槽的结构示意图。附图标记列表1:反应器401:排渣口10:收集槽50:喷气室101:凸肩501:喷射拱102:导流管502:进气管103:截流槽60:出口管20:反应器壁70:反应腔201:侧壁部701:第一反应区30:进料管702:第二反应区301:进料口80:检测器40:排渣管801:探针具体实施方式下面结合附图进行详细说明。图1是本发明的用于连续流化床反应器的熔融物收集槽结构示意图。如图所示,流化床反应器1包括:收集槽10、反应器壁20、进料管30、排渣管40、喷气室50、出口管60、反应腔70;其中,收集槽10位于侧壁部201上用以收集反应器壁20上流下的熔融物;进料管30用以将反应物输入反应腔;排渣管40用以将反应后的残渣导出反应器;进料管30、排渣管40穿过反应器壁20将反应腔70与外部环境连通起来;喷气室50通中通过燃烧生成高温气体,通过穿过反应器壁20与外部环境连通的进气管502补充空气或氧气,喷气室50的喷射拱501用以将气体从喷气室50中高速喷入反应腔70内。在生产过程中,固态的反应物通过进料管30进入反应腔70中,位于反应器下部的喷气室50通过喷射拱501形成高温高速的气流,将的固体反应物吹起来。反应物在反应腔70中呈沸腾状,与反应气体和/或催化剂充分接触,反应生成密度更小或者颗粒更小的产物。产物随着高温高速的气流通过上部的出口管60导出反应器收集起来。反应后的固体残渣沉积下来,落入反应腔70底部,通过排渣管40导出反应器。其他产物或未反应物的熔融物凝集在反应器壁20上,被收集槽10收集起来导出反应器。收集槽10包括截流槽103和导流管102,其中,截流槽103被构成为位于侧壁部201上向反应腔70凸出的凸肩101和反应器的侧壁部201共同形成的槽体(参见图2)。该槽体在水平方向上围绕侧壁部201一圈,以收集沿侧壁部201流下的熔融物。所述导流管102设置在槽体的某一位置,贯穿反应器壁20,将截流槽103与外界环境连通,使得进入截流槽103内的熔融物能够通过导流管102转移至反应器外部。对于最简单的情况,在该流化床反应器1中设置一个截留槽,其位于流化床反应器1某个物料进出口301的上方,用以避免阻塞。根据一个优选实施方式,在该流化床反应器1中设置若干截留槽,这些截留槽可以彼此连通,也可以彼此独立。根据另一个优选实施方式,至少一个截留槽是通过呈裙边状镶嵌于侧壁部201的凸肩101构成的。根据另一个优选实施方式,至少一个截留槽是通过可拆卸地固定于侧壁部201的环状凸肩101构成的。根据本发明的一个另选或附加的实施方式,通过从侧壁部201沿径向倾斜向上凸起的凸肩形成的环形挡圈以及与该环形挡圈相邻的侧壁部201来共同限定至少一个截留槽。在该实施方式中,该截流槽103也可呈至少部分螺旋状围绕侧壁部201。可在螺旋状截留槽的最低处设置唯一个导流管102,以使槽体内的熔融物能够在重力的作用下流动至导流管102。优选地,为防止熔融物过多而溢出,可在螺旋状截留槽的中部区域再设置一个或多个导流管102。根据本发明的一个另选或附加的实施方式,所述截流槽103被设置成波浪形环绕侧壁部201的槽体,所述波浪形槽体具有至少两个波谷,每个波谷处至少设置一个导流管102。反应器1可含有用以监测反应器1内的环境或反应状态的检测器80,检测器80的探针801伸入反应腔70中。通常情况下,熔融物粘度较大,沿着反应器的侧壁部流下时容易包覆在探针上,形成熔融物膜,从而降低检测的灵敏度。根据本发明的一个优选实施方式,探针801设置在截流槽103的下方,用以减少探针与熔融物接触。位于探针801上方的侧壁部201流下的熔融物会被截流槽103收集起来,不容易流到探针801上。根据本发明的一个另选或附加的实施方式,探针801位于截流槽103竖直方向最高点的下方。由于粘附在侧壁部201的熔融物会在重力的作用下向下流动,因此越靠近反应器的侧壁部201的下方,熔融物越多。因此需将探针801尽量设置在检测区的上方。截流槽103的最高点处可收集到的熔融物较少,且熔融物能立刻顺着截流槽103流向导流管102处,不容易因为溢出而流到下方的探针801上,保证了探针801受到熔融物的不良干扰最小化。其中在反应器1中部进料管30的进料口301上方和反应器1下部排渣管40的排渣口401上方分别有一圈收集槽10。在反应器1的不同位置通常由于温度不同可能会有不同类型的熔融物形成,这些熔融物的成分不同,粘度和温度也不相同。分成两个收集槽,一方面可以分开收集两个反应区域中不同的熔融物,简化熔融物导出后的分离处理程序;另一方面可以防止熔融物流到进料口301和排渣口401时与固体物料混合后造成堵塞。而且对于某些生产过程,反应腔的上部即第二反应区702和下部的第一反应区701往往温度相差较大,第二反应区702的高温熔融物可能在未流至第一反应区701的导流管102处就已经冷却凝固,或者在流至温度较低的第一反应区701区域处粘度变大难以导出,因此在反应器的上下两个部分分别设置收集槽,以有效地收集到液态的熔融物,防止由于导出不及时而在反应器中凝固或形成堵塞。图2是本发明连续流化床反应器的熔融物收集槽的结构示意图。截留槽用于收集在高温生产环境下附着在侧壁部201上的熔融物。因此在理想情况下,截留槽沿径向向内伸出越多就越有利于收集熔融物。然而,图1所示的流化床需要利用热空气将竖向靠下的第一反应区701内生成的物质送往上方,以便在该反应器的第二反应区702进行后续的反应。所以,截留槽不宜沿径向过于向内突出,而是应当有利于热气流上升。根据一个优选实施方式,如图所示,凸肩101的背向侧壁部201的一侧(即外侧部分),在图2所示的剖视图中,上部为竖直面,下部为斜面,使得凸肩101处大致形成一个上部呈直筒状,下部呈截顶锥形的腔体。反应器1下部喷射上来的气流经过凸肩101处时由于横截面积变窄,流速提升,被气流带上来的物料不容易再通过此处沉降下去,使反应腔70分成两个不同的区域,从而在两个区域中进行两种不同的反应过程时能够较稳定地保持相对平衡状态。下部的斜面结构可减弱高温高速气流对凸肩101结构的冲击作用。根据本发明的一个另选或附加的实施方式,凸肩101的外侧也可呈由侧壁部201处向反应腔70自下向上延伸的曲面型。优选为流线型曲面,可减弱对气流的阻力,从而减轻高温高速气流冲击作用对凸肩101的损害。根据本发明的一个另选或附加的实施方式,凸肩101外侧下部与反应器内壁20的相接处平滑过渡,一方面进一步减弱对气流的阻力;另外下部喷射上的粉体物料能沿着平滑过渡面向上移动,不容易在连接处聚集而形成死角。该反应器壁20的顶部呈竖直方向上中部高边缘低的形状。在与侧壁部201相交处为平滑的弧面。凸肩101外侧的竖直面在竖直方向向上延伸大致与反应器壁20顶部相交于该弧面的曲率最大部,或者该曲率最大部相比凸肩101的外侧更靠近侧壁部201。凝聚于反应器壁20顶部的熔融物在重力和中心喷射上来的气流的吹动作用下从中部相周边滑动,大部分液滴会滑动至竖直的侧壁部201处流下,少部分液滴可能提前在顶部与侧壁部201相交处,特别是在曲率最大部滴落下来,刚好落入截流槽103中,可更为完全的收集到熔融物。位于侧壁部201处的导流管102的上缘在竖直方向上略高于凸肩101的外侧。导流管102与侧壁部201平滑过渡。导流管口上方流下的熔融物液滴可不进入收集槽而直接流入导流管102中。导流管102在竖直方向上斜向下穿过反应器壁20从反应器内部连通至反应器外部。熔融物在导流管102中由于重力作用大于与导流管102内壁的摩擦力,从而能顺利的流出。导流管102采用与熔融物表面亲和力较弱的材质。另外导流管102内壁需平整光滑。根据本发明的一个优选实施方式,导流管102与竖直方向呈45度角向下穿出。一方面熔融物在导流管102中受到的重力作用大于与导流管102内壁的摩擦力;另一方面导流管102穿过反应器壁20的路径长度较短,熔融物经历的路径也较短,不容易因为在导流管102中经历时间过长而冷却下来,粘度增大甚至凝固而堵塞导流管102。根据本发明的一个另选或附加的实施方式,导流管102位于反应器壁20外侧的一端伸出反应器壁20一定的长度连接熔融物收集装置。该熔融物收集装置与保压装置连接。该保压装置可以是抽气机或者气囊式气压罐。通过调节保压装置,使得导流管102两端的气压保持平衡,即反应器内部与熔融物收集装置内的气压保持平衡。熔融物既能在重力的作用下通过导流管102流出,又不会因为导流管102泄压而给反应器中反应造成不良影响。或者调节保压装置,使得熔融物收集装置内形成微负压。在不扰乱反应器内气流的前提下,熔融物在导流管102两端气压差形成的动力辅助作用下导出反应器。根据本发明的一个另选或附加的实施方式,导流管102可呈上部半径大下部半径小的截顶空心锥形,或呈上下孔径均一的斜圆柱状。凸肩101面对侧壁部201的一侧,及内侧部分呈与侧壁部201呈一定夹角的斜面状,形成大致为V字形的截流槽103,也可以是呈略向反应腔70凹陷的弧面状,从而增大截流槽103的容量。导流管口与凸肩101内侧的接触的地方平滑过渡,尤其是导流管口与凸肩101内侧相切,使得熔融物可以顺利的流入导流管102中。另外导流管口周围的侧壁部201向反应器壁20外侧方向略微凹陷,一方面起到引流作用使得流至导流管102处的熔融物更容易流入导流管102中,另一方面增大了导流管102处可容纳的熔融物的量。导流管口处的凸肩101内侧可比其它地方凹陷更深,使得容量进一步增大,形成蓄积池结构,防止熔融物过多,排出不及时而溢出。形成截流槽103的凸肩101在与侧壁部201相接处有一部分位于所述反应器壁20中,使得其能够固定在侧壁部201上,优选的凸肩101在制造反应器时与侧壁部201一体成型。由于凸肩101的一部分伸入反应腔70中,而反应腔70的温度通常会比反应器壁20高,另外收集到的熔体往往温度很高,会释放出一部分热量,因此制造凸肩101的材料的耐高温性要比侧壁部201的耐高温性更好一些。另外通常进料口301位于反应器的中部或上部,排渣口401位于反应器的下部,对于某些放热反应,反应腔70上部的温度会比反应腔70下部的温度要高,上部熔融物的组分可能也与下部熔融物的组分不同,考虑到耐高温材料的价格等因素,根据需要选择适合的材料制备耐高温性能达到要求的凸肩101。优选对位于进料口301上方的凸肩101采用比位于排渣口401上方凸肩101耐高温性更好的材料制备。需要注意的是,上述具体实施例是示例性的,在本发明的上述教导下,本领域技术人员可以在上述实施例的基础上进行各种改进和变形,而这些改进或者变形落在本发明的保护范围内。本领域技术人员应该明白,上面的具体描述只是为了解释本发明的目的,并非用于限制本发明。本发明的保护范围由权利要求及其等同物限定。