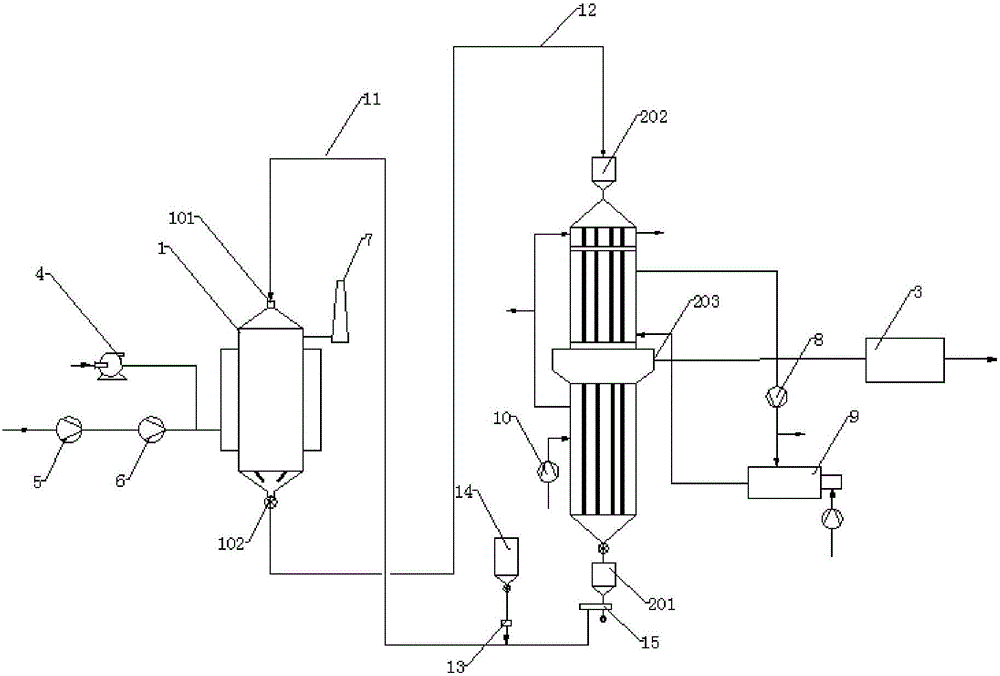
本发明属于环保
技术领域:
,涉及烟(废)气集成净化技术,具体而言,涉及一种活性焦烟气脱硫脱硝副产物转化装置和脱硫脱硝系统及方法。
背景技术:
:随着人类社会经济的发展和工业化进程的加快,钢铁冶金、有色金属冶炼、燃煤火电、化工建材及燃烧锅炉等领域排放的烟(废)气中含有大量SO2、NOx等有害气体,造成严重的大气硫污染和酸雨危害。虽然经过“十一五”时期的烟气脱硫建设,我国的SO2、NOx排放量已有一定幅度下降,但是在“十二五”和今后的更长时间里,我国的SO2、NOx等减排压力依然较重;在“十二五”期间,国家对SO2和NOx的减排量分别为8%和10%,成为我国进一步发展的约束性指标。此外,随着对环保要求的日趋严格,排放到大气中的汞和二噁英等有毒物质也开始受到关注和控制,开发能够联合脱除SO2、NOx、汞及二噁英等多种污染物,资源化回收的烟(废)气净化技术具有重要意义。现有的脱硫脱硝技术主要分为湿法、半干法和干法,湿法或半干法技术虽比较成熟,但其脱硫、脱硝效果达不到目前的环标要求。目前湿法技术比较常用的是采用钙法吸收烟气,半干法技术多采用双碱法即钠碱和生石灰粉吸收烟气,这两种方法均不能进行脱硝处理,即还需增加额外的设备才能脱硝,并且其处理后烟气会带有明显的水汽外排,并夹杂CaO、NaOH和硫化物等,对周边环境影响较大,会造成二次污染,产生大量废水和固废需要二次处理;且对设备的防腐要求高,还会造成硫酸等资源的浪费。在各种烟气净化技术中,活性焦烟气净化技术具有其独有的特点,具有高度环保、深度节水、集成净化和可资源化等优点;然而现有的活性焦烟气脱硫脱硝系统存在流程复杂、能耗偏高等缺点。此外,现有的活性焦脱硫脱硝系统中副产物转化装置,大多采用将该系统中解析中的SO2气体依次经过转化器、冷凝器等装置制成浓硫酸。然而,借助解析出的SO2气体制备副产物浓硫酸在实际应用中往往会存在以下问题:由于各地区的条件不同,对硫酸的需求也不尽相同,因此,在某些地区会造成硫酸销售困难,从而造成经济效益低,并且对环境也会造成一定的污染。技术实现要素:本发明的第一目的在于,提供一种活性焦烟气脱硫脱硝副产物转化装置和方法,采用该装置可以生产亚硫酸钠、焦硫酸钠、连二亚硫酸钠等系列高附加值产品,提高整个活性焦烟气脱硫脱硝系统的生产附加值,提高资源的利用率,进而提高经济效益,既经济又环保。本发明的第二目的在于,提供一种活性焦烟气脱硫脱硝系统和方法,该系统工艺简单,布局紧凑,能耗低,并且没有废水、没有固废、没有二次污染,实现了资源再生利用。为实现上述目的,本发明采用的技术方案为:一种活性焦烟气脱硫脱硝副产物转化装置,包括吸收塔、配碱单元、中间品储罐、中和釜、蒸发器、浓料罐、离心单元和干燥装置;所述吸收塔设置有进气端,所述进气端与活性焦烟气脱硫脱硝系统中解析出的二氧化硫气体输出端相连接;所述配碱单元、吸收塔、中间品储罐、中和釜、蒸发器、浓料罐、离心单元与干燥装置依次相连接。本发明提供的副产物转化装置可以生产亚硫酸钠、焦硫酸钠、连二亚硫酸钠(保险粉)等系列高附加值产品,本发明将以生产亚硫酸钠为例,做进一步说明,但不限于此。本发明生产亚硫酸钠的整个副产物转化工艺简单,副产物产品价值高,能耗低,产品效益高,经济又环保。在本发明的可选方案中,所述进气端与所述二氧化硫气体输出端之间设置有冷却池,用于降低二氧化硫气体温度;所述吸收塔还与真空装置相连接,用于排出吸收塔内的空气。为方便配置不同浓度的碱液,本发明的可选方案中,所述配碱单元包括相互连接的配碱罐和碱液储罐,所述碱液储罐与所述吸收塔相连接,且所述配碱罐与碱液储罐之间设有第一输送泵,所述碱液储罐与吸收塔之间设有第二输送泵。为使二氧化硫气体与碳酸钠溶液的吸收反应更加充分、完全,本发明的可选方案中,所述吸收塔包括依次相连接的一级吸收塔、二级吸收塔、三级吸收塔和尾气吸收塔,所述第二输送泵与尾气吸收塔相连接,所述一级吸收塔与所述中间品储罐相连接。在本发明的可选方案中,所述中和釜包括相互连接的一级中和釜和二级中和釜,所述一级中和釜分别与所述中间品储罐和第二输送泵相连接,所述二级中和釜与氢氧化钠输送泵相连接。其中在一级中和釜内中间品亚硫酸氢钠溶液与碳酸钠溶液发生反应,在二级中和釜内亚硫酸氢钠溶液与氢氧化钠溶液发生反应,两步中和反应使得亚硫酸氢钠反应更加完全,提高反应效率。在本发明的可选方案中,所述干燥装置包括依次连接的干燥塔、旋风干燥器、旋风分离器和振动筛,所述离心单元与干燥塔相连接,所述旋风干燥器与用于吸收干燥尾气的洗涤塔相连接,所述振动筛与成品包装装置相连接。本发明还提供一种活性焦烟气脱硫脱硝副产物转化方法,采用上述
发明内容所述的活性焦烟气脱硫脱硝副产物转化装置进行副产物转化,包括如下步骤:(1)自活性焦烟气脱硫脱硝系统中解析出的二氧化硫气体,从进气端进入吸收塔,与从配碱单元输送至吸收塔内的碱液进行吸收反应,得到的中间反应液输送至中间品储罐;(2)中间品储罐内的中间反应液输送至中和釜,与碱液在中和釜内进行中和反应,得到反应溶液;(3)步骤(2)中得到的反应溶液经蒸发器蒸发后输送至浓料罐中,浓料罐中的料液经过离心单元离心以及干燥装置干燥后得到成品。在本发明的可选方案中,进入至所述吸收塔内的碱液为浓度为20%~30%的碳酸钠溶液,优选浓度为22%~24%。进入至所述一级中和釜内的碱液为浓度为30%~40%的碳酸钠溶液,优选浓度为36%~38%。进入至所述二级中和釜内的氢氧化钠溶液为浓度为30%~40%的碳酸钠溶液,优选浓度为32%~35%。本发明还提供一种活性焦烟气脱硫脱硝系统,包括上述
发明内容所述的活性焦烟气脱硫脱硝副产物转化装置,还包括吸附塔和解析塔;所述吸附塔下部设有烟气入口,上部设有烟气出口,顶部和底部分别设有活性焦入口和活性焦出口;所述解析塔顶部和底部分别设有进料口和出料口;所述吸附塔的活性焦入口与解析塔的出料口连接,所述吸附塔的活性焦出口与解析塔的进料口连接;所述解析塔侧壁上设有二氧化硫气体输出端,所述二氧化硫气体输出端与所述吸收塔的进气端相连接。在本发明的可选方案中,所述活性焦烟气脱硫脱硝系统还包括氨气系统、除尘系统和电气控制系统,其中,氨气系统与吸附塔相连接,用于提高脱硫脱硝效果;除尘系统设置于吸附塔的外侧,并与吸附塔的烟气入口连通,所述除尘系统为电除尘器或者高温布袋除尘器;电气控制系统包括电机回路、阀门回路和电源回路,电气控制系统与吸附塔、解析塔、氨气系统、除尘系统和副产物转化装置相连接。在本发明的可选方案中,所述活性焦烟气脱硫脱硝系统还包括物料输送系统,物料输送系统包括第一输送带和第二输送带,其中,吸附塔的活性焦入口与解析塔的出料口通过第一输送带连接,第一输送带包括带有第一闭锁料斗的输送带和第一电机,第一闭锁料斗设置于解析塔底部;吸附塔的活性焦出口与解析塔的进料口通过第二输送带连接,所述第二输送带包括带有第二闭锁料斗的输送带和第二电机,所述第二闭锁料斗设置于解析塔底部。进一步地,还包括为活性焦烟气脱硫脱硝系统添加新鲜活性焦的给料机、储料仓以及筛分装置,给料机和储料仓设置在第一输送带上;筛分装置与解析塔的出料口连通,且筛分合格粒径的出口与吸附塔的活性焦入口连通。在本发明的可选方案中,所述吸附塔为逆流床结构。在本发明的可选方案中,所述解析塔由上至下依次包括预热区、再生区和冷却区,解析塔外侧设有与预热区和再生区导通的高温换热风机,以及与高温换热风机连接的热源,热源为电加热器或热风炉;解析塔外侧设有与冷却区导通的低温换热风机。本发明还提供一种活性焦烟气脱硫脱硝方法,采用上述
发明内容所述的活性焦烟气脱硫脱硝系统进行烟气脱硫脱硝的工艺方法,包括如下步骤:(1)烟气脱硫脱硝:将烟气从烟气入口送入吸附塔中,活性焦依靠重力在吸附塔内自上而下移动,与烟气充分接触,脱除烟气中的SO2、NOx、汞和二噁英,净化后的烟气通过烟气出口排放;(2)活性焦再生与循环:活性焦从吸附塔底部的活性焦出口下落后进入解析塔,在解析塔内活性焦将吸附的含硫元素解析并产生二氧化硫气体,解析出的二氧化硫气体从吸收塔的进气端进入到吸收塔中,进行副产物转化处理;再生后的活性焦从解析塔底部的出料口下落后进入吸附塔,进行下一次循环。在本发明的可选方案中,所述烟气的温度为90~190℃。本发明提供的活性焦烟气脱硫脱硝方法,具体包括以下步骤:(1)烟气脱硫脱硝:将烟气从烟气入口送入吸附塔中,活性焦依靠重力在吸附塔内自上而下移动,与烟气充分接触,脱除烟气中的SO2、NOx、汞和二噁英,净化后的烟气通过烟气出口排放;(2)活性焦再生与循环:活性焦从吸附塔底部的活性焦出口下落后进入解析塔,在解析塔内活性焦将吸附的含硫元素解析出来,再生后的活性焦从解析塔底部的出料口下落后进入吸附塔,进行下一次循环;(3)副产物转化:在解析塔内解析出的二氧化硫气体,进入副产物转化装置中,经过副产物转化装置生产亚硫酸钠。(4)副产物生成:解析出的二氧化硫气体进入至吸收塔与碱液进行吸收反应,得到的中间品反应液与碱液在中和釜内进行中和反应,得到的反应液经过蒸发、离心及干燥后得到成品亚硫酸钠。活性焦(或者活性炭)烟气脱硫脱硝技术属于干法技术,具有不耗水,能够同时脱除SO2和NOx等污染物,无二次污染,是一种适合我国国情、高效且经济的烟气污染综合治理技术。活性焦干法烟气脱硫脱硝技术以其卓越的技术性能和相对较低的经济成本,可以应用在烟(废)气净化、硫资源回收和清洁生产方面。因此,选择活性焦(或者活性炭)干法烟气脱硫脱硝技术,对相关行业进行SO2、NOx减排和资源化利用,对于转变经济发展方式和发展循环经济,具有十分重要的意义。活性焦脱硫脱硝工艺的原理是基于SO2在活性焦表面的吸附和催化作用,烟气中SO2在一定温度下,与烟气中的氧气、水蒸气发生化学反应生产硫酸吸附在活性焦孔隙内。活性焦脱硝工艺的原理是利用活性焦的催化特性,采用选择性催化还原反应法,在烟气中配入少量NH3,促使NOx发生选择性催化还原反应生产N2直接排放。具体反应如下:(1)物理吸附SO2→SO2(SO2吸附在活性焦微细孔中)(2)化学吸附SO2+O2+H2O→H2SO4(3)向硫酸盐转化(靠NH3/SO2)H2SO4+NH3←→NH4HSO4NH4HSO4+NH3←→(NH4)2SO4(4)脱硝反应:SCR反应NO+NH3+1/2O2→N2+3/2H2Onon-SCR(与脱离时生成的还原性物质直接反应)NO+C…Red→N2(C-Red:为活性焦表面的还原性物质)(5)再生反应H2SO4→H2O+SO3NH4HSO4→H2O+SO3+NH3(NH4)2SO4→H2O+SO3+2NH3SO3+C-AC→SO2+1/2CO23SO3+2NH3→3SO2+3H2O+N2本发明中,活性焦烟气脱硫脱硝副产物转化装置可以为亚硫酸钠生成装置,且亚硫酸钠生产的反应方程式如下:吸收的反应方程式:第一步反应过程,Na2CO3+SO2=Na2SO3+CO2;第二步反应过程,Na2SO3+H2O+SO2=2NaHSO3;中和的反应方程式:第一步反应过程,Na2CO3+2NaHSO3=Na2SO3+CO2+H2O;第二步反应过程,NaOH+NaHSO3=Na2SO3+H2O。与现有技术相比,本发明的有益效果在于:1、本发明的活性焦烟气脱硫脱硝副产物转化装置与解析塔相连接,借助解析塔解析出的SO2气体生产亚硫酸钠,由于亚硫酸钠是工业上用途广泛的产品,广泛应用于医药、橡胶、印染等工业,具有较好的市场前景。具体地,医药工业可用于生产氯仿、苯丙砜和苯甲醛;橡胶工业可用做凝固剂;印染工业可用作棉布漂白后的脱氯剂、棉布煮炼剂;制革工业可用于皮革处理,能使皮革柔软,丰满、坚韧,具有防水、抗折、耐磨等性能;化学工业可用于生产羟基香草醛、盐酸羟胺等;感光工业可用作显影剂等;食品工业用作漂白剂、防腐剂、疏松剂、抗氧化剂、护色剂及保鲜剂。2、本发明提供的活性焦烟气脱硫脱硝副产物转化装置,工艺简单、能耗低,不仅可以生产亚硫酸钠,还可以生产焦硫酸钠、连二亚硫酸钠(保险粉)等系列高附加值产品,进而提高整个活性焦烟气脱硫脱硝系统的生产附加值,降低生产成本,提高资源的利用率,进而提高经济效益,且无废水排放,既经济又环保。3、本发明提供的活性焦烟气脱硫脱硝系统,采用活性焦作为吸附剂,烟囱无明显水汽外排,无固废、废水和二次污染,并且可实现同时脱除SO2、NOx、汞、二噁英和粉尘的一体化,降低了运行成本;同时工艺简单,简化流程,有效提高了脱硫脱销效率,并且投资抵,能耗低。4、本发明采用活性焦为吸附剂,活性焦为碳基粒状,具有高强度、可再生、原料广泛等优点,对烟气中的污染物SO2、NOx、汞或其他重金属有很强的吸附性;脱硫效率达到95%以上,脱硝效率达到60%以上,汞和二噁英的脱除效率均达到90%以上,除尘效率达到75%以上;并且如果烟气中SO2含量浓度提高,活性焦的脱除效率将会进一步提高,副产品收益进一步增加,运行成本明显下降,同时原料(高硫煤、高硫矿石等)选择的余地将进行一步扩大,进而降低生产成本。5、本发明中,净化后的烟气由烟囱排出,吸附SO2后的活性焦,在加热的情况下,其所吸附的H2SO4与活性焦反应被还原为SO2,同时活性焦恢复吸附性能,循环使用;活性焦的加热再生反应相当于对活性焦进行再次活化,吸附和催化活性不但不会降低,还会有一定程度的提高。6、本发明提供的活性焦烟气脱硫脱硝系统烟气处理前无需加热,整体能耗低,无需工艺水和废水处理,因而无二次污染;设备腐蚀低,维护费用低,并且运行维护方便;同时工艺简单,布局紧凑,结构设计合理,排出的主要污染物的排放量和排放浓度均已达到国家最高排放标准的要求,并且运行成本低,节能环保,具有良好的社会效益、经济效益和环境效益,值得广泛推广和应用。为使本发明的上述目的、特征和优点能更明显易懂,下文特举较佳实施例,并配合所附附图,作详细说明如下。附图说明为了更清楚地说明本发明具体实施方式或现有技术中的技术方案,下面将对具体实施方式或现有技术描述中所需要使用的附图作简单地介绍,显而易见地,下面描述中的附图是本发明的一些实施方式,对于本领域普通技术人员来讲,在不付出创造性劳动的前提下,还可以根据这些附图获得其他的附图。图1为本发明提供的活性焦烟气脱硫脱硝副产物转化装置示意图;图2为本发明提供的活性焦烟气脱硫脱硝系统工艺流程图。附图标记:1-吸附塔;2-解析塔;3-副产物转化装置;4-氨气系统;5-送风机;6-增压风机;7-烟囱;8-高温换热风机;9-热源;10-低温换热风机;11-第一输送带;12-第二输送带;13-给料机;14-储料仓;15-筛分装置;101-分配器;102-卸料器;201-第一闭锁料斗;202-第二闭锁料斗;203-二氧化硫气体输出端;31-吸收塔;32-配碱单元;33-中间品储罐;34-中和釜;35-蒸发器;36-浓料罐;37-离心单元;38-干燥装置;39-计量装置;310-包装装置;311-尾气吸收塔;312-三级吸收塔;313二级吸收塔;314-一级吸收塔;315-冷却池;316-真空装置;321-第二输送泵;322-碱液储罐;323-第一输送泵;324-配碱罐;341-一级中和釜;342-二级中和釜;343-氢氧化钠输送泵;351-冷却器;381-干燥塔;382-旋风干燥器;383-旋风分离器;384-振动筛;385-洗涤塔。具体实施方式为使本发明实施例的目的、技术方案和优点更加清楚,下面将结合本发明实施例中附图,对本发明实施例中的技术方案进行清楚、完整地描述,显然,所描述的实施例仅仅是本发明一部分实施例,而不是全部的实施例。通常在此处附图中描述和示出的本发明实施例的组件可以以各种不同的配置来布置和设计。因此,以下对在附图中提供的本发明的实施例的详细描述并非旨在限制要求保护的本发明的范围,而是仅仅表示本发明的选定实施例。基于本发明的实施例,本领域技术人员在没有做出创造性劳动的前提下所获得的所有其他实施例,都属于本发明保护的范围。下面结合实施例和具体实施方式对本发明做进一步详细的说明。实施例1图1为本发明提供的活性焦烟气脱硫脱硝副产物转化装置示意图,如图1所示,一种活性焦烟气脱硫脱硝副产物转化装置,包括吸收塔31、配碱单元32、中间品储罐33、中和釜34、蒸发器35、浓料罐36、离心单元37和干燥装置38;吸收塔31设置有进气端,进气端与活性焦烟气脱硫脱硝系统中解析出的二氧化硫气体输出端203相连接;配碱单元32、吸收塔31、中间品储罐33、中和釜34、蒸发器35、浓料罐36、离心单元37与干燥装置38依次相连接。其中,配碱单元32为碳酸钠溶液配制单元,配碱单元32包括相互连接的配碱罐324和碱液储罐322,碱液储罐322与吸收塔31相连接,且配碱罐324与碱液储罐322之间设有第一输送泵323,碱液储罐322与吸收塔31之间设有第二输送泵321。吸收塔31包括依次相连接的一级吸收塔314、二级吸收塔313、三级吸收塔312和尾气吸收塔311,第二输送泵321与尾气吸收塔311相连接,用于向尾气吸收塔311中输送配制好的碳酸钠溶液;一级吸收塔314与中间品储罐33相连接,经过三级吸收反应后得到的亚硫酸氢钠溶液输送至中间品储罐33中,从而可以使得吸收反应更加充分、完全。中和釜34包括相互连接的一级中和釜341和二级中和釜342,一级中和釜341分别与中间品储罐33和第二输送泵321相连接,二级中和釜342与氢氧化钠输送泵343相连接;二级中和釜342还与蒸发器35相连接,蒸发器35与冷凝器351相连接。其中在一级中和釜341内中间品亚硫酸氢钠溶液与碳酸钠溶液发生反应,在二级中和釜342内亚硫酸氢钠溶液与氢氧化钠溶液发生反应,两步中和反应使得亚硫酸氢钠反应更加完全,提高反应效率。干燥装置38包括依次连接的干燥塔381、旋风干燥器382、旋风分离器383和振动筛384,离心单元37与干燥塔381相连接,旋风干燥器382与用于吸收干燥尾气的洗涤塔385相连接,振动筛384与成品包装装置310相连接,其振动筛384与成品包装装置310之间还设置有计量装置39。本实施例中,进气端与二氧化硫气体输出端203之间设置有冷却池315,用于降低二氧化硫气体温度;吸收塔31还与真空装置316相连接,用于排出吸收塔31内的空气。采用以上活性焦烟气脱硫脱硝副产物转化装置进行副产物转化,具体包括如下步骤:(1)在配碱罐324中配置一定浓度的碳酸钠溶液(本实施例中碳酸钠溶液浓度为22%~24%),经第一输送泵323送往碱液储罐322,然后经第二输送泵321送往尾气吸收塔311、三级吸收塔312、二级吸收塔313和一级吸收塔314,在三级吸收塔312、二级吸收塔313和一级吸收塔314中,控制温度和酸度,碳酸钠溶液与来自活性焦烟气脱硫脱硝系统中解析出的二氧化硫气体发生吸收反应。其中,尾气吸收塔311的吸收液送至三级吸收塔312,三级吸收塔312的吸收液送至二级吸收塔313,二级吸收塔313的吸收液送至一级吸收塔314,在一级吸收塔314中得到合格的亚硫酸氢钠溶液(PH值4-5,浓度450-500g/L),合格的亚硫酸氢钠溶液送至中间品储罐33。(2)中间品储罐33中的亚硫酸氢钠溶液送至一级中和釜341,与经第二输送泵321送至一级中和釜341的碳酸钠溶液(浓度为36%~38%)发生反应,在PH达到5-6时进入二级中和釜342,与经氢氧化钠输送泵343送至二级中和釜342的氢氧化钠溶液(浓度为32%~35%)发生反应,生成亚硫酸钠中和液,合格的亚硫酸钠中和液送至中和液储罐或者蒸发器35。(3)亚硫酸钠中和液经蒸发器35蒸发后得到悬浮液,该悬浮液经过输送泵送至浓料罐36,浓料罐36内的料液再送往离心单元37进行离心,经过离心得到亚硫酸钠固体,而离心的母液则进入母液罐。(4)经离心单元37得到的亚硫酸钠固体送至干燥装置38进行干燥,而干燥尾气通过洗涤塔385吸收后达标排放,尾气吸收液再送回至配碱罐324中再利用,经干燥得到的亚硫酸钠固体经计量、包装后得到亚硫酸钠成品。实施例2图2为本发明提供的活性焦烟气脱硫脱硝系统工艺流程图,如图2所示,本实施例提供一种活性焦烟气脱硫脱硝系统,包括实施例1中的活性焦烟气脱硫脱硝副产物转化装置3,还包括吸附塔1和解析塔2;吸附塔1下部侧壁上设有烟气入口,上部侧壁上设有烟气出口,顶部和底部分别设有活性焦入口和活性焦出口,吸附塔1与氨气系统4相连接;解析塔2顶部和底部分别设有进料口和出料口,吸附塔1的活性焦入口与解析塔2的出料口连接,吸附塔1的活性焦出口与解析塔2的进料口连接;解析塔2侧壁上设有排气口,排气口与副产物转化装置3连接。解析塔2侧壁上设有二氧化硫气体输出端203,二氧化硫气体输出端203与吸收塔31的进气端相连接。本实施例中,烟气入口通过管路与用于输送烟气的送风机5连接,其连接管路上设有增压风机6;烟气出口与烟囱7连接,其连接管路上设有用于控制烟气流量的风门。吸附塔1为逆流床结构,吸附塔1顶部设有与活性焦入口连通的料仓和分配器101,底部设有与活性焦出口连通的卸料器102。解析塔2由上至下依次包括预热区、再生区和冷却区,解析塔2外侧设有与预热区和再生区导通的高温换热风机8,以及与高温换热风机8连接的热源9,热源9为电加热器或热风炉;解析塔2外侧设有与冷却区导通的低温换热风机10。吸附塔1的活性焦入口与解析塔2的出料口通过第一输送带11连接,第一输送带11包括带有第一闭锁料斗201的输送带和第一电机,第一闭锁料斗201设置于解析塔2底部;吸附塔1的活性焦出口与解析塔2的进料口通过第二输送带12连接,第二输送带12包括带有第二闭锁料斗202的输送带和第二电机,第二闭锁料斗202设置于解析塔2底部。本实施例提供的活性焦烟气脱硫脱硝系统还包括为脱硫脱硝系统添加新鲜活性焦的给料机13、储料仓14以及筛分装置15,给料机13和储料仓14设置在第一输送带11上;筛分装置15与解析塔2的出料口连通,且筛分合格粒径的出口与吸附塔1的活性焦入口连通。进一步地,还包括氨气系统4、除尘系统和电气控制系统,其中,氨气系统4与吸附塔1相连接,除尘系统设置于吸附塔1的外侧,并与吸附塔1的烟气入口连通,除尘系统为电除尘器或者高温布袋除尘器;电气控制系统包括电机回路、阀门回路和电源回路,电气控制系统与吸附塔1、解析塔2、副产物转化装置3、氨气系统4和除尘系统连接。本实施例中的活性焦烟气脱硫脱硝方法,具体包括如下步骤:(1)烟气脱硫脱硝:在烟气进入吸附塔1之前先通过除尘系统进行除尘,然后分别通过送风机5和增压风机6将烟气送入吸附塔1中,同时将氨气通过氨气输送装置送入吸附塔1中。活性焦从吸附塔1的活性焦入口进入吸附塔1,活性焦依靠重力在吸附塔1内自上而下移动,与烟气和氨气充分接触,脱除烟气中的SO2、NOx、汞和二噁英,净化后的烟气通过烟气出口从烟囱7排放;(2)活性焦再生与循环:活性焦从吸附塔1底部的活性焦出口下落后通过第二输送带12进入解析塔2,在解析塔2内活性焦将吸附的含硫元素解析并产生二氧化硫气体,解析出的二氧化硫气体从吸收塔31的进气端进入到吸收塔31中,进行副产物转化处理,再生后的活性焦通过第一输送带11从解析塔2底部的出料口下落后进入吸附塔1,进行下一次循环。在本发明的可选方案中,烟气的温度为90~190℃。根据上述所提供的活性焦烟气脱硫脱硝系统及方法,进行烟气处理,处理后的相关数据如表1所示。表1活性焦烟气脱硫脱硝主要特性参数项目单位数据SO2脱除率%98NOx脱除率%60氟化物排放mg/Nm3<4二噁英排放ng/Nm3<2烟气含尘浓度mg/Nm3<20对比例采用现有的半干法脱硫+SCR脱硝技术与本发明提供的活性焦烟气脱硫脱硝技术做对比,并进行经济技术分析,结果如表2所示。表2活性焦烟气脱硫脱硝技术与半干法脱硫+SCR脱硝技术的对比根据表2可以看出,活性焦烟气脱硫脱硝技术与半干法脱硫+SCR脱硝技术相比具有明显的优势,其基本无固体废物、废水的产生,无二次污染,并且烟囱7无明显水汽外排,年运行费用低,产生的主要副产物亚硫酸钠具有较高的利用价值,是有效的循环经济。同时,活性焦烟气脱硫脱硝技术采用活性焦为吸附剂,可以同时进行脱硝,其他二种技术均无法完成,需新增设备,增加一大笔的投资进行脱硝处理。最后应说明的是:以上实施例,仅为本发明的具体实施方式,用以说明本发明的技术方案,而非对其限制,本发明的保护范围并不局限于此,尽管参照前述实施例对本发明进行了详细的说明,本领域的普通技术人员应当理解:任何熟悉本
技术领域:
的技术人员在本发明揭露的技术范围内,其依然可以对前述实施例所记载的技术方案进行修改或可轻易想到变化,或者对其中部分技术特征进行等同替换;而这些修改、变化或者替换,并不使相应技术方案的本质脱离本发明实施例技术方案的精神和范围。都应涵盖在本发明的保护范围之内。因此,本发明的保护范围应以权利要求的保护范围为准。当前第1页1 2 3