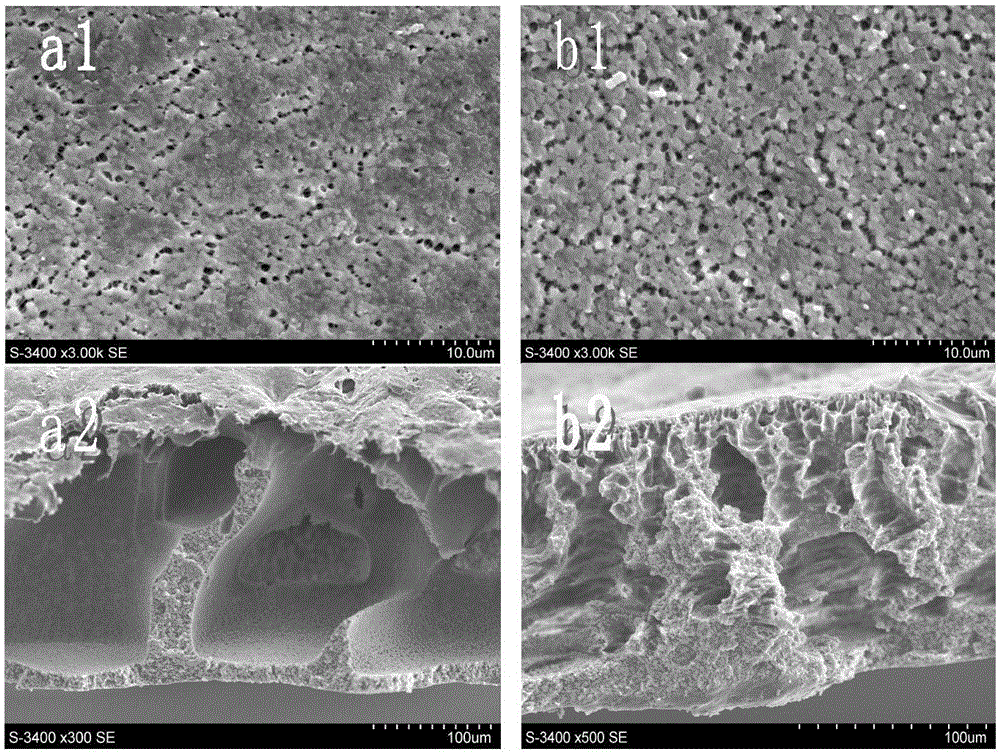
本发明涉及水处理领域,尤其涉及一种油水分离膜及其制备方法。
背景技术:
:聚偏氟乙烯(PVDF)是一种具有良好热稳定性、机械性能和耐化学腐蚀性的高分子材料,被广泛应用于工业水处理膜分离领域。疏水的PVDF膜存在表面能低,水通量小、易污染等问题,制约其在油水分离领域中的应用。现有技术将无机纳米粒子引入PVDF膜材料中进行亲水改性,进一步提高PVDF膜的抗污性能。已报道的无机材料主要有SiO2、Al2O3、Fe3O4、TiO2、ZrO2等无机粒子。其中纳米二氧化硅(SiO2)具有无毒、强亲水性和化学稳定性等优良性能,添加二氧化硅纳米粒子成为科研人员研究的热点之一。目前制备SiO2改性PVDF膜的方法是:将纳米SiO2颗粒或SiO2的前驱物(TEOS)直接共混在铸膜液里,通过浸没沉淀相转移法制得聚偏氟乙烯共混二氧化硅油水分离膜。该方法对SiO2颗粒的粒径要求高,且分散无机颗粒耗时长,易团聚;共混前驱物的使用虽然避免了SiO2颗粒的团聚,可是并没有消除PVDF膜在使用过程中二氧化硅易脱落,膜抗污性能下降的弊端。技术实现要素:本发明的目的在于提供一种PVDF-g-SiO2油水分离膜及其制备方法。采用本发明提供的制备方法所得到的PVDF-g-SiO2油水分离膜中PVDF与SiO2通过化学键连接,SiO2不易脱落,具有优异的抗污染性能。本发明提供了一种PVDF-g-SiO2油水分离膜的制备方法,包括以下步骤:(1)提供PVDF醇溶液;(2)将季铵类有机强碱醇溶液滴加至所述步骤(1)得到的PVDF醇溶液中,加热得混合溶液;(3)将所述步骤(2)所得的混合溶液与高锰酸钾酸性水溶液混合进行氧化反应,得到改性PVDF;(4)将所述步骤(3)得到的改性PVDF与SiCl4、水和有机溶剂混合,加热进行接枝反应,得到PVDF-g-SiO2聚合物;(5)将所述步骤(4)得到的PVDF-g-SiO2聚合物溶于有机溶剂中,得到铸膜液,将所述铸膜液制膜,得到PVDF-g-SiO2油水分离膜。优选的,所述季铵类有机强碱为四甲基氢氧化铵、四乙基氢氧化铵、四丙基氢氧化铵或四丁基氢氧化铵。优选的,所述高锰酸钾酸性水溶液的pH值为1~6。优选的,所述高锰酸钾酸性水溶液中高锰酸钾的浓度为0.05~1.00mol/L,PVDF的质量与高锰酸钾酸性水溶液的体积比以g:mL计为1:3~8。优选的,所述PVDF与季铵类有机强碱、SiCl4和水的质量比为100:0.5~3.0:10~20:2~10。优选的,所述步骤(2)中加热的具体过程为:先在45~60℃下恒温加热0.5~2.0h,再升温至110~130℃,恒温5~10min,然后冷却至45~60℃。优选的,所述步骤(3)中氧化反应的温度为45~60℃,氧化反应的时间为1.0~2.5h。优选的,所述步骤(4)中的有机溶剂为N-甲基吡咯烷酮或二甲基亚砜。优选的,所述步骤(4)中接枝反应的温度为145~175℃,反应时间为1.5~3.0h。本发明提供了一种采用上述技术方案所述的制备方法得到的PVDF-g-SiO2油水分离膜,所述PVDF-g-SiO2油水分离膜为网络状结构,SiO2质量百分含量为3.5~7.5%,孔隙度为65~75%,平均孔径为65~95nm。本发明提供了一种PVDF-g-SiO2油水分离膜的制备方法,将季铵类有机强碱醇溶液滴加至PVDF醇溶液中,加热得到混合溶液;将所述混合溶液与高锰酸钾酸性水溶液混合进行氧化反应,得到改性PVDF;将所述改性PVDF与SiCl4、水和有机溶剂混合,加热进行接枝反应,得到PVDF-g-SiO2聚合物;将所述PVDF-g-SiO2聚合物溶于有机溶剂中,得到铸膜液,然后将所述铸膜液制膜,得到PVDF-g-SiO2油水分离膜。本发明所提供的制备方法中,季铵类有机强碱能使PVDF通过消去反应脱去氟化氢产生碳碳双键,酸性高锰酸钾进一步将碳碳双键氧化为羟基,得到含羟基的改性PVDF,SiCl4水解产生原硅酸,原硅酸与改性PVDF链上的羟基发生接枝反应,生成C-O-Si键,形成网络结构,得到PVDF-g-SiO2油水分离膜。在本发明中,PVDF和SiO2通过化学键连接,SiO2不易脱落,具有优异的抗污染性能和耐用性。采用本发明所提供的制备方法得到的PVDF-g-SiO2油水分离膜为网络状结构,SiO2质量百分含量为3.5~7.5%,孔隙度为65~75%,平均孔径为65~95nm。实施例效果表明,使用浓度为1.0g/L的乳化油溶液对油水分离膜的性能进行测试,水通量可达889.5L/(m2·h),截留率在93%以上,且恒定压力下过滤60min,其水通量衰减率仅为9%~11%,使用一次后测试其纯水通量恢复率可达91.2%。此外,本发明提供的制备方法工艺简单、操作简便、成本低、产率高,易于工业化生产。附图说明下面结合附图和具体实施方式对本发明作进一步详细的说明。图1实施例1中纯PVDF(a)、四乙基氢氧化铵处理后的PVDF(b)、改性PVDF(c)和PVDF-g-SiO2聚合物(d)的FTIR谱图。图2对比例所制备的纯PVDF油水分离膜的表面SEM图(a1)、截面SEM图(a2)和实施例1所制备的PVDF-g-SiO2油水分离膜的表面SEM图(b1)、截面SEM图(b2)具体实施方式本发明提供了一种PVDF-g-SiO2油水分离膜的制备方法,包括以下步骤:(1)提供PVDF醇溶液;(2)将季铵类有机强碱醇溶液滴加至所述步骤(1)得到的PVDF醇溶液中,加热得混合溶液;(3)将所述步骤(2)所得的混合溶液与高锰酸钾酸性水溶液混合进行氧化反应,得到改性PVDF;(4)将所述步骤(3)得到的改性PVDF与SiCl4、水和有机溶剂混合,加热进行接枝反应,得到PVDF-g-SiO2聚合物;(5)将所述步骤(4)得到的PVDF-g-SiO2聚合物溶于有机溶剂中,得到铸膜液,将所述铸膜液制膜,得到PVDF-g-SiO2油水分离膜。本发明首先提供PVDF醇溶液。在本发明中,所述PVDF醇溶液的制备方法为本领域技术人员常用的方法,具体为将PVDF分散于醇溶剂中,通过加热的方式使PVDF溶解于醇溶剂中,得到均相PVDF醇溶液。本发明对加热的温度和时间没有特殊要求,能够使PVDF充分溶解于醇溶剂中即可,在本发明实施例中,所述加热的温度优选为45~80℃,更优选为50~60℃;所述加热的时间优选为0.5~1.5h,更优选为0.8~1h。在本发明中,对所述制备PVDF醇溶液所用的溶剂没有特殊要求,采用本领域技术人员熟知的醇溶剂即可,优选为甲醇、乙醇、丙醇、丁醇或戊醇。在本发明中,对所述制备PVDF醇溶液所用的醇溶剂的量没有特殊要求,足以溶解PVDF的量即可,在本发明实施例中PVDF的质量与醇溶剂的体积比以g:mL计优选为1:7~15,更优选为1:8~10。在本发明中,得到PVDF醇溶液后,将季铵类有机强碱醇溶液滴加至所述PVDF醇溶液中,加热得混合溶液。在本发明中,所述季铵类有机强碱优选为四甲基氢氧化铵、四乙基氢氧化铵、四丙基氢氧化铵或四丁基氢氧化铵,更优选为四乙基氢氧化铵。本发明对所述季铵类有机强碱醇溶液所用的醇溶剂的种类没有特殊要求,采用本领域技术人员所熟知的能够溶解季铵类有机强碱的醇溶剂即可。本发明对所述季铵类有机强碱醇溶液的浓度没有特殊要求,在本发明的实施例中采用市售质量浓度为25%的季铵类有机强碱甲醇溶液。在本发明中,所述季铵类有机强碱的质量优选为PVDF的质量的0.5%~3.0%,更优选为PVDF的质量的0.8%~1.6%。本发明对所述季铵类有机强碱醇溶液的滴加速度没有特殊要求,可根据反应情况适当调节,在本发明中季铵类有机强碱醇溶液的滴加速度优选为1~10s/滴,更优选为2~4s/滴。在本发明中,所述步骤(2)中加热过程为先在较低温度加热一段时间,季铵类有机强碱中的OH-使PVDF分子链上的-CH2-基团失去质子生成活性自由基-CH·-,失去质子的PVDF分子链发生消去反应失去F-,生成带有双键的PVDF,反应结束后升高温度,以除去季铵类有机强碱,恒温一段时间后再降低温度,得到混合溶液,优选的加热的具体过程为:先在45~65℃下恒温加热0.5~2.0h,再升温至110~130℃,恒温5~10min,然后冷却至45~65℃,更优选的加热的过程为:先在50~55℃下恒温加热1.0~1.5h,再升温至120~125℃,恒温5~10min,然后冷却至50~55℃。在本发明中,所述升温的速率优选为1~15℃/min,更优选为3~10℃/min。本发明对降温的的方式没有特殊的限定,可以采用一定的降温速率外力辅助降温,也可以选择自然降温;在本发明中,所述降温的速率优选为1~10℃/min,更优选为2~5℃/min。在本发明中,加热得到混合溶液后,将所述的混合溶液与高锰酸钾酸性水溶液混合进行氧化反应,得到改性PVDF。本发明中高锰酸钾酸性水溶液可将所述混合溶液中的PVDF分子链上的双键氧化为羟基,得到带有羟基的改性PVDF。在本发明中,所述高锰酸钾酸性水溶液的pH值优选1~6,更优选4~5。本发明对调节高锰酸钾酸性水溶液所用的酸的种类没有特殊要求,本领域技术人员所熟知的制备酸性高锰酸钾溶液常用的酸即可,在本发明中,所述高锰酸钾酸性水溶液所用的酸优选硝酸或硫酸,在本发明实施例中使用了1mol/L的硝酸调节高锰酸钾酸性水溶液的pH值。在本发明中,高锰酸钾酸性水溶液中高锰酸钾的浓度优选0.05~1.00mol/L,更优选0.08~0.2mol/L。在本发明中,PVDF的质量与高锰酸钾酸性水溶液的体积比以g:mL计优选为1:3~8,更优选1:5~6。在本发明中,所述氧化反应的温度优选45~60℃,更优选50~55℃;所述氧化反应的时间优选1.0~2.5h,更优选1.5~2h。在本发明中,所述氧化反应过程中,改性PVDF逐渐析出,反应结束后,本发明优选将得到的氧化反应液自然冷却至室温后过滤,将所述过滤得到的固体经洗涤和干燥,得到改性PVDF,所述改性PVDF为粉体。在本发明实施例中洗涤过滤得到的固体时所用的溶剂为去离子水,干燥条件优选真空干燥,真空干燥的条件为:压力5×104~6×104Pa,温度70~90℃,时间0.5~1.5h。得到改性PVDF后,本发明将所述改性PVDF与SiCl4、水和有机溶剂混合,加热进行接枝反应,得到PVDF-g-SiO2聚合物。在本发明中,所述改性PVDF与SiCl4、水和有机溶剂混合后,SiCl4水解生成原硅酸,原硅酸与改性PVDF链上的羟基发生接枝反应,生成C-O-Si键,进而形成网络结构,得到PVDF-g-SiO2聚合物。在本发明中,优选的反应过程为:先将所述改性PVDF溶于有机溶剂中,再加入SiCl4和水,然后升温至接枝反应所需温度,进行接枝反应。本发明对升温的速率没有特殊要求,采用本领域技术人员常用的升温速率即可,在本发明中,升温速率优选为1~15℃/min,更优选为3~10℃/min。在本发明中,所述PVDF与SiCl4、水的质量比为100:10~20:2~10,更优选为100:14~17:3~7。在本发明中,有机溶剂优选N-甲基吡咯烷酮或二甲基亚砜。本发明对所述步骤(4)中有机溶剂的用量没有特殊要求,能够溶解改性PVDF即可,在本发明中,所述步骤(4)中有机溶剂的用量优选为每克PVDF对应4~8mL有机溶剂。在本发明中,所述接枝反应的温度优选为145~175℃,更优选为155~165℃;所述接枝反应的时间优选为1.5~3.0h,更优选为2.0~2.5h。所述接枝反应后,本发明优选将得到的接枝反应液与析出溶剂混合,析出接枝反应产物,将所述接枝反应产物洗涤、过滤和干燥,得到PVDF-g-SiO2聚合物。本发明中对所述析出溶剂的种类没有特殊的限定,能够降低聚合物在溶液中溶解度即可。在本发明实施例中,通过向接枝反应后的混合溶液中加水以使PVDF-g-SiO2聚合物析出,在本发明中,所述洗涤过程可将PVDF-g-SiO2聚合物中混入的游离SiO2除去,得到纯净的PVDF-g-SiO2聚合物,优选的洗涤过程可施以超声震荡辅助,以更彻底的除去游离SiO2。在本发明实施例中,所述接枝反应结束后,将接枝反应后的溶液降至室温,加入去离子水,PVDF-g-SiO2聚合物析出,过滤得PVDF-g-SiO2聚合物粗品,然后使用去离子水洗涤2-4次,具体洗涤方法为:将PVDF-g-SiO2聚合物粗品分散于去离子水中,超声震荡10~15min,洗涤结束后经过滤、干燥得到纯净的PVDF-g-SiO2聚合物。本发明中优选的真空干燥,真空干燥条件为压力5×104~6×104Pa,温度80~110℃,时间1~2h。得到PVDF-g-SiO2聚合物后,将所述PVDF-g-SiO2聚合物溶于有机溶剂中得到铸膜液,将所述铸膜液制膜,得到PVDF-g-SiO2油水分离膜。在本发明中,所述铸膜液的制备中有机溶剂的体积与PVDF的质量比优选为(4~8)mL:1g有机溶剂,更优选为(5~6)mL:1g。在本发明中,溶解PVDF-g-SiO2聚合物的有机溶剂优选N-甲基吡咯烷酮、二甲基亚砜。本发明对PVDF-g-SiO2聚合物溶于有机溶剂的手段没有特殊要求,采用本领域技术人员常用的促进溶解的技术手段即可,在本发明实施例中,PVDF-g-SiO2聚合物溶于有机溶剂的技术手段为在搅拌条件下,加热混合溶液以使PVDF-g-SiO2聚合物完全溶解于有机溶剂,得到均一相的铸膜液,具体加热温度为45~60℃,更优选50~55℃,搅拌时间为2~2.5h。在本发明中,所述铸膜液制膜的方法可采用本领域技术人员所熟知的制膜方法,如流延法、挤出法、浸没沉淀相转化法,本发明实施例中优选浸没沉淀相转化法,具体过程为:将所述铸膜液脱泡后涂覆于平板玻璃上,在空气中水平静置;以水为凝固浴经浸没沉淀相转化得到薄膜;将所述薄膜在去离子水中浸泡,以除去溶剂,即得PVDF-g-SiO2油水分离膜。本发明对铸膜液脱泡的方式没有特殊要求,采用本领域技术人员所熟知的脱泡方式即可,如真空脱泡、超声脱泡、加热脱泡等,在本发明中,所述脱泡的方式优选真空脱泡,具体条件为5×104~6×104Pa的压力下保持20~30min。在本发明中,所述涂覆厚度为0.15~0.25mm;所述静置的时间优选为25~35s;在凝固浴中浸没的时间优选为0.5~1.5h;所述去离子水中浸泡的时间优选为12~24h,更优选为15~20h;在本发明中,对油水分离膜性能的测试采用如下方法:膜通量的测定方法:以直径为3cm的膜样品为测试膜,使用高纯氮钢瓶提供压力,先将测试膜在0.15MPa下预压30min,然后在0.1MPa下测定一定时间△t(单位为h)的透过液体积V(单位为L),膜通量J(单位为L/(m2·h))的计算公式如下:其中A为膜的有效面积(7.065×10-4m2)。膜截留率的测定方法:使用紫外-可见分光光度仪在233nm波长下测出乳化油浓度-吸光度标准曲线,然后测定透过测试膜的模拟含油废水透过液的吸光度,由乳化油浓度-吸光度标准曲线得到透过测试膜的透过液的乳化油浓度c1(g/L),膜截留率R的计算公式如下:其中c0为模拟含油废水的浓度(g/L),本发明实施例中以浓度为1g/L的乳化油水溶液为模拟含油废水。纯水膜通量恢复率的测试方法:将使用后的测试膜用纯水清洗2~3次,每次超声清洗5min,清洗完毕后再次测试其纯水通量,测试膜的纯水通量恢复率FFR的计算公式如下:式中,J0为测试膜使用前的纯水膜通量(L/(m2·h));Jc表示使用测试膜过滤模拟含油废水1h后经清洗再次测得的纯水膜通量(L/(m2·h))。膜通量衰减率的测试方法:将1.0g/L的乳化油溶液在0.1MPa下过滤1h,分别记录开始时的膜通量J1和结束时的膜通量J2,其膜通量衰减率AR的计算公式如下:式中AR为水通量衰减率;J1为初始过滤乳化油时的膜通量;J2为过滤乳化油1h后的膜通量。下面将结合本发明中的实施例,对本发明中的技术方案进行清楚、完整地描述。显然,所描述的实施例仅仅是本发明一部分实施例,而不是全部的实施例。基于本发明中的实施例,本领域普通技术人员在没有做出创造性劳动前提下所获得的所有其他实施例,都属于本发明保护的范围。实施例1(1)称量3gPVDF粉末分散于25mL甲醇中,在45℃下搅拌1.5h,得到PVDF甲醇溶液;(2)将0.0968g质量浓度为25%的四乙基氢氧化铵甲醇溶液以2s/滴的速度滴加至PVDF甲醇溶液中,在45℃下恒温加热2.0h,以3℃/min的升温速率升温至115℃,恒温10min,然后以5℃/min的降温速率将体系冷却至50℃,得到混合溶液;(3)将pH值为2浓度为0.1mol/L的高锰酸钾酸性水溶液加入至所述步骤(2)得到的混合溶液中,在50℃下反应2.5h,反应结束后,降至室温,过滤后使用去离子水洗涤,在压力为6×104Pa、温度为80℃的真空干燥箱中干燥0.5h得到含醇羟基的改性PVDF粉体;(4)将步骤(3)得到的改性PVDF粉体溶于23mLN-甲基吡咯烷酮中,加入0.3g的SiCl4和0.1mL去离子水,搅拌,加热至145℃恒温反应3.0h,反应结束后,将反应液降至室温,向反应液中加入25mL去离子水,PVDF-g-SiO2聚合物析出,过滤得PVDF-g-SiO2聚合物粗品,将所得PVDF-g-SiO2聚合物粗品分散于去离子水中,超声振荡10min洗涤,重复洗涤3次,然后过滤,将过滤后的PVDF-g-SiO2聚合物置于压力为6×104Pa、温度为100℃的真空干燥箱中干燥1.5h,得到纯净的PVDF-g-SiO2聚合物;(5)将步骤(4)得到的PVDF-g-SiO2聚合物加入至20mLN-甲基吡咯烷酮中,在45℃下加热2.5h,得到均相铸膜液,然后将铸膜液在5×104Pa下保持30min进行脱泡,将脱泡后的铸膜液在平板玻璃上涂覆0.2mm厚,在空气中水平静置30s,然后在水中浸没1h得到薄膜,将所得薄膜在去离子水中浸泡15h,除去溶剂,即得PVDF-g-SiO2油水分离膜,得到PVDF-g-SiO2油水分离膜。将本实施例所用的纯PVDF粉体原料、步骤(2)四乙基氢氧化铵处理后的PVDF、步骤(3)得到的改性PVDF以及步骤(4)得到的PVDF-g-SiO2聚合物进行红外测试,结果见图1。对本实施例所得的PVDF-g-SiO2油水分离膜进行SEM测试,结果见图2。图1为本实施例中纯PVDF(a)、四乙基氢氧化铵处理后的PVDF(b)、改性PVDF(c)和PVDF-g-SiO2聚合物(d)的FTIR谱图。图1中纯PVDF和四乙基氢氧化铵处理后的PVDF的FTIR曲线在1406cm-1、1178cm-1、870cm-1和841cm-1处均出现了PVDF分子的特征吸收峰,说明本发明的改性过程没有破坏PVDF的主链结构;四乙基氢氧化铵处理后的PVDF在1621cm-1处出现双键的伸缩振动峰,表明PVDF脱去HF产生碳碳共轭双键;改性PVDF的FTIR曲线上1621cm-1处的双键峰消失,在1215cm-1和1194cm-1处出现了C-O伸缩振动峰,表明四乙基氢氧化铵处理后的PVDF分子链上的双键被氧化为C-OH键;PVDF-g-SiO2聚合物在1080cm-1和839cm-1处出现Si-O键的振动峰,在1270cm-1处出现C-O键的振动峰,说明PVDF-g-SiO2聚合物中含有C-O-Si键,即SiO2是以化学键的形式结合在PVDF的骨架上;改性PVDF的FTIR曲线上1660cm-1处出现分子内结晶水H-O-H键的特征吸收峰,说明SiO2结构中的硅醇键在分子间形成分子间氢键,分子间氢键可增强膜材料的亲水性从而提高膜的抗污性能。图2为对比例所制备的纯PVDF油水分离膜的表面SEM图(a1)、截面SEM图(a2)和实施例1所制备的PVDF-g-SiO2油水分离膜的表面SEM图(b1)、截面SEM图(b2),由图2可知,由本申请实施例1所得PVDF-g-SiO2油水分离膜表面的孔和内部孔道分布均匀,截面呈现出孔道分布均匀的海绵状,而纯PVDF油水分离膜则表面孔及内部孔道分布不均匀。对本实施例所得PVDF-g-SiO2油水分离膜的SiO2含量、孔隙度、平均孔径进行测试,其中SiO2含量通过能量色散X射线光谱仪(EDX)进行测试得到,具体结果见表1。对本实施例所得PVDF-g-SiO2油水分离膜的纯水通量(J0)、截留率(R)、水通量恢复率(FFR)和衰减率(AR)进行测试,结果见表2。实施例2(1)称量3gPVDF粉末分散于35mL乙醇中,在65℃下搅拌40min,得到PVDF乙醇溶液;(2)将0.1212g浓度为25%的四甲基氢氧化铵的甲醇溶液以4s/滴的速度滴加至PVDF乙醇溶液中,在65℃下恒温加热1.0h,再以15℃/min的升温速率升温至110℃,恒温10min,然后以8℃/min的降温速率冷却至65℃,得到的混合溶液;(3)将pH值为3浓度为0.02mol/L的高锰酸钾酸性水溶液加入至所述步骤(2)得到的混合溶液中,在65℃下反应2.5h,反应结束后,降至室温,过滤,使用去离子水洗涤,然后在压力为5×104Pa、温度为70℃的真空干燥箱中干燥1.5h得到含醇羟基的改性PVDF粉体;(4)将步骤(3)得到的改性PVDF粉体溶于20mLN-甲基吡咯烷酮中,加入0.6g的SiCl4和0.2mL去离子水,搅拌,加热至170℃恒温反应1.5h,反应结束后,将反应液降至室温,向反应液中加入20mL去离子水,PVDF-g-SiO2聚合物析出,过滤得PVDF-g-SiO2聚合物粗品,将所得PVDF-g-SiO2聚合物粗品分散于去离子水中,声振荡10min进行洗涤,重复洗涤3次,然后过滤,将过滤后的PVDF-g-SiO2聚合物置于压力为5×104Pa、温度为80℃的真空干燥箱中干燥2h,得到纯净的PVDF-g-SiO2聚合物;(5)将步骤(4)得到的PVDF-g-SiO2聚合物加入至20mLN-甲基吡咯烷酮中,在45℃下加热2.5h,得到均相铸膜液,然后将铸膜液在5.5×104Pa下保持30min进行脱泡,将脱泡后的铸膜液在平板玻璃上涂覆0.2mm厚,在空气中水平静置25s,然后在水中浸没0.5h得到薄膜,将所得薄膜在去离子水中浸泡15h,除去溶剂,即得PVDF-g-SiO2油水分离膜,得到PVDF-g-SiO2油水分离膜。对本实施例所得PVDF-g-SiO2油水分离膜的SiO2含量、孔隙度、平均孔径进行测试,其中SiO2含量通过能量色散X射线光谱仪(EDX)进行测试得到,具体结果见表1。对本实施例所得PVDF-g-SiO2油水分离膜的纯水通量(J0)、截留率(R)、水通量恢复率(FFR)和衰减率(AR)进行测试,结果见表2。实施例3(1)称量3gPVDF粉末分散于22mL甲醇中,在60℃下搅拌1.5h,得到PVDF甲醇溶液;(2)将0.1456g浓度为25%的四甲基氢氧化铵的甲醇溶液以3s/滴的滴加速度滴加至PVDF甲醇溶液中,在60℃下恒温加热2.0h,再以5℃/min的升温速率升温至130℃,恒温5min,然后以5℃/min的降温速率降温至60℃,得到的混合溶液;(3)将pH值为6浓度为0.05mol/L的高锰酸钾酸性水溶液加入至所述步骤(2)得到的混合溶液中,在60℃下反应2.5h,反应结束后,降至室温,过滤,使用去离子水洗涤,然后在压力为5.5×104Pa、温度为90℃的真空干燥箱中干燥50min得到含醇羟基的改性PVDF粉体;(4)将步骤(3)得到的改性PVDF粉体溶于15mLN-甲基吡咯烷酮中,加入0.4g的SiCl4和0.1mL去离子水,搅拌,加热至150℃恒温反应1.5h,反应结束后,将反应液降至室温,向反应液中加入20mL去离子水,PVDF-g-SiO2聚合物析出,过滤得PVDF-g-SiO2聚合物粗品,将所得PVDF-g-SiO2聚合物粗品分散于去离子水中进行洗涤,超声振荡10min进行洗涤,重复洗涤3次,然后过滤,将过滤后的PVDF-g-SiO2聚合物置于压力为5.5×104Pa、温度为110℃的真空干燥箱中干燥1h,得到纯净的PVDF-g-SiO2聚合物;(5)将步骤(4)得到的PVDF-g-SiO2聚合物加入至15mLN-甲基吡咯烷酮中,在45℃下加热2.5h,得到均相铸膜液,然后将铸膜液在5×104Pa下保持20min进行脱泡,将脱泡后的铸膜液在平板玻璃上涂覆0.15mm厚,在空气中水平静置35s,然后在水中浸没1.5h得到薄膜,将所得薄膜在去离子水中浸泡24h,除去溶剂,即得PVDF-g-SiO2油水分离膜,得到PVDF-g-SiO2油水分离膜。对本实施例所得PVDF-g-SiO2油水分离膜的SiO2含量、孔隙度、平均孔径进行测试,其中SiO2含量通过能量色散X射线光谱仪(EDX)进行测试得到,具体结果见表1。对本实施例所得PVDF-g-SiO2油水分离膜的纯水通量(J0)、截留率(R)、水通量恢复率(FFR)和衰减率(AR)进行测试,结果见表2。实施例4(1)称量3gPVDF粉末分散于30mL甲醇中,在50℃下搅拌1.0h,得到PVDF甲醇溶液;(2)将0.1704g浓度为25%的四乙基氢氧化铵的甲醇溶液以5s/滴的滴加速度滴加至PVDF甲醇溶液中,在50℃下恒温加热1.5h,再以8℃/min的升温速率升温至120℃,恒温10min,然后以4℃/min的降温速率冷却至50℃,得到的混合溶液;(3)将pH值为4浓度为0.1mol/L的高锰酸钾酸性水溶液加入至所述步骤(2)得到的混合溶液中,在50℃下反应2.0h,反应结束后,降至室温,过滤,使用去离子水洗涤,然后在压力为6×104Pa、温度为70℃的真空干燥箱中干燥1h得到含醇羟基的改性PVDF粉体;(4)将步骤(3)得到的改性PVDF粉体溶于17mLN-甲基吡咯烷酮中,加入0.5g的SiCl4和0.2mL去离子水,搅拌,加热至155℃恒温反应2.5h,反应结束后,将反应液降至室温,向反应液中加入25mL去离子水,PVDF-g-SiO2聚合物析出,过滤得PVDF-g-SiO2聚合物粗品,将所得PVDF-g-SiO2聚合物粗品分散于去离子水中,超声振荡10min进行洗涤,重复洗涤3次,然后过滤,将过滤后的PVDF-g-SiO2聚合物置于压力为6×104Pa、温度为110℃的真空干燥箱中干燥1.5h,得到纯净的PVDF-g-SiO2聚合物;(5)将步骤(4)得到的PVDF-g-SiO2聚合物加入至17mLN-甲基吡咯烷酮中,在50℃下加热2.5h,得到均相铸膜液,然后将铸膜液在6×104Pa下保持25min进行脱泡,将脱泡后的铸膜液在平板玻璃上涂覆0.25mm厚,在空气中水平静置30s,然后在水中浸没1h得到薄膜,将所得薄膜在去离子水中浸泡20h,除去溶剂,即得PVDF-g-SiO2油水分离膜。对本实施例所得PVDF-g-SiO2油水分离膜的SiO2含量、孔隙度、平均孔径进行测试,其中SiO2含量通过能量色散X射线光谱仪(EDX)进行测试得到,具体结果见表1。对本实施例所得PVDF-g-SiO2油水分离膜的纯水通量(J0)、截留率(R)、水通量恢复率(FFR)和衰减率(AR)进行测试,结果见表2。实施例5(1)称量3gPVDF粉末分散于25mL乙醇中,在55℃下搅拌50min,得到PVDF乙醇溶液;(2)将0.1952g浓度为25%的四乙基氢氧化铵的甲醇溶液以2s/滴的滴加速度滴加至PVDF乙醇溶液中,在55℃下恒温加热1.0h,再以10℃/min的升温速率升温至125℃,恒温7min,然后以5℃/min的降温速率冷却至50℃,得到的混合溶液;(3)将pH值为5浓度为0.2mol/L的高锰酸钾酸性水溶液加入至所述步骤(2)得到的混合溶液中,在53℃下反应1.5h,反应结束后,降至室温,过滤,使用去离子水洗涤,然后在压力为6×104Pa、温度为70℃的真空干燥箱中干燥1h得到含醇羟基的改性PVDF粉体;(4)将步骤(3)得到的改性PVDF粉体溶于12mL二甲基亚砜中,加入0.5g的SiCl4和0.2mL去离子水,搅拌,加热至160℃恒温反应2.5h,反应结束后,将反应液降至室温,向反应液中加入20mL去离子水,PVDF-g-SiO2聚合物析出,过滤得PVDF-g-SiO2聚合物粗品,将所得PVDF-g-SiO2聚合物粗品分散于去离子水,超声振荡10min进行洗涤,重复洗涤3次,然后过滤,将过滤后的PVDF-g-SiO2聚合物置于压力为5×104Pa、温度为90℃的真空干燥箱中干燥2h,得到纯净的PVDF-g-SiO2聚合物;(5)将步骤(4)得到的PVDF-g-SiO2聚合物加入至12mL二甲基亚砜中,在55℃下加热2.0h,得到均相铸膜液,然后将铸膜液在5×104Pa下保持30min进行脱泡,将脱泡后的铸膜液在平板玻璃上涂覆0.2mm厚,在空气中水平静置30s,然后在水中浸没1h得到薄膜,将所得薄膜在去离子水中浸泡20h,除去溶剂,即得PVDF-g-SiO2油水分离膜,得到PVDF-g-SiO2油水分离膜。对本实施例所得PVDF-g-SiO2油水分离膜的SiO2含量、孔隙度、平均孔径进行测试,其中SiO2含量通过能量色散X射线光谱仪(EDX)进行测试得到,具体结果见表1。对本实施例所得PVDF-g-SiO2油水分离膜的纯水通量(J0)、截留率(R)、纯水通量恢复率(FFR)和衰减率(AR)进行测试,结果见表2。对比例称量3gPVDF粉体溶于20mLN-甲基吡咯烷酮中,在50℃下搅拌2.5h,得到均一的铸膜液,采用与实施例1相同的制膜方法制膜得到纯PVDF油水分离膜。测量其膜的纯水通量(J0)、截留率(R)、纯水通量恢复率(FFR)和衰减率(AR)。对本实施例所得PVDF-g-SiO2油水分离膜的纯水通量(J0)、截留率(R)、纯水通量恢复率(FFR)和衰减率(AR)进行测试,结果见表2。表1实施例所得PVDF-g-SiO2油水分离膜的SiO2含量、孔隙度、平均孔径SiO2含量/(wt.%)孔隙度/%平均孔径/nm实施例13.8967.868实施例24.4269.375实施例35.5170.784实施例46.2572.789实施例57.3173.582表2实施例和对比例效果数据J0/(L/(m2·h))R/%FFR/%AR/%实施例1457.493.588.610.2实施例2589.794.289.79.6实施例3757.893.891.210.5实施例4889.594.390.49.6实施例5776.294.890.69.4对比例128.585.758.941.1由表1可以看出采用本发明所提供的方法制备的PVDF-g-SiO2油水分离膜的亲水性、油水分离效果、抗污染性能相对于纯PVDF制备的油水分离膜均得到了显著提高,其纯水通量可达889.5L/(m2·h),乳化油的截留率均高于93.0%,使用PVDF-g-SiO2油水分离膜过滤模拟含油废水1h后,经清洗后其纯水通量恢复率可达91.2%,连续使用1h过滤模拟含油废水,膜通量衰减率仅在11%以内。以上所述仅是本发明的优选实施方式,应当指出,对于本
技术领域:
的普通技术人员来说,在不脱离本发明原理的前提下,还可以做出若干改进和润饰,这些改进和润饰也应视为本发明的保护范围。当前第1页1 2 3