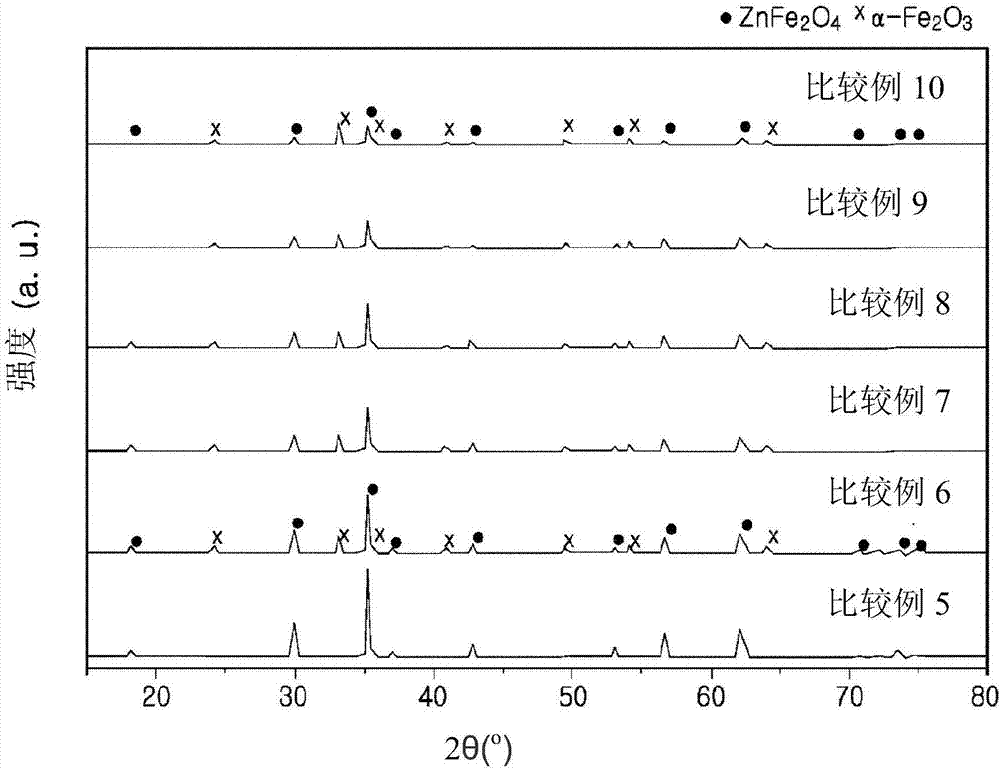
[相关申请的交叉引用]本申请要求于2016年03月25日在韩国知识产权局提交的韩国专利申请no.10-2016-0036238的优先权权益,该申请的公开内容通过引用并入本申请中。本发明涉及一种氧化脱氢用催化剂及其制备方法。更具体地,本发明涉及一种能确保氧化脱氢反应性并提高直通率(firstpassyield)的氧化脱氢用催化剂及其制备方法。
背景技术:
:在全球范围内,对石化产品的中间体1,3-丁二烯的需求及其价值正在逐渐增加。为了生产这种1,3-丁二烯,已经使用诸如石脑油裂解、丁烯直接脱氢和丁烯的氧化脱氢的方法。然而,在石脑油裂解的情况下,由于较高的反应温度,能量损耗高。此外,由于石脑油裂解不是为生产1,3-丁二烯产品专门设计的工艺,因此,除1,3-丁二烯以外,不利地产生作为剩余产物的其它基础油。同时,正丁烯的直接脱氢在热力学上不利。此外,由于正丁烯的直接脱氢是吸热反应,因此,为了生产高产率的1,3-丁二烯需要高温和低压条件。因此,正丁烯的直接脱氢不适合作为生产1,3-丁二烯的商业方法。同时,在丁烯的氧化脱氢的情况下,丁烯与氧在金属氧化物催化剂的存在下反应生成1,3-丁二烯和水,由于生成稳定的水,因此,丁烯的氧化脱氢在热力学上有利。此外,由于与丁烯的直接脱氢不同,丁烯的氧化脱氢是放热反应,因此,与丁烯的直接脱氢相比,即使在较低的反应温度下,丁烯的氧化脱氢也可以生产高产率的1,3-丁二烯。此外,由于丁烯的氧化脱氢不需要额外的热供应,因此,丁烯的氧化脱氢可以被认为是仅生产1,3-丁二烯从而满足对1,3-丁二烯的需求的有效的生产工艺。金属氧化物催化剂通常通过沉淀方法合成。然而,由于金属氧化物催化剂的直通率因技术和空间的限制而较小,因此需要多次重复相同的过程才能得到需要量的催化剂。这种通过多个过程制备的催化剂根据制备过程通过率对反应物可能具有不同的反应性,催化剂之间的这种反应性差异与产物(丁二烯)的产率直接相关。因此,降低催化剂之间的反应性差异是重要的研究目标。因此,需要一种能够提供提高的直通率且在所制备的催化剂之间没有反应性差异的催化剂的制备方法。[相关技术文献][专利文献](专利文献1)us8513479b2技术实现要素:技术问题因此,鉴于上述问题而做出本发明,本发明的一个目的是提供一种能够确保氧化脱氢反应性并提高直通率的氧化脱氢用催化剂,以及该催化剂的制备方法。上述和其它目的可以通过下面描述的本公开实现。技术方案根据本发明的一个方面,提供一种氧化脱氢用催化剂的制备方法,该方法包括:混合三价阳离子铁(fe)前体和二价阳离子金属(a)前体以形成浓度大于16.5重量%并小于53.5重量%的混合水溶液的步骤;将所述混合水溶液和碱性水溶液以2g/min以上并且小于32g/min的滴加速率一起逐滴加入共沉淀槽中以得到同时包含afe2o4和fe2o3的共沉淀溶液的步骤,所述共沉淀槽中含有大于0℃且小于40℃的蒸馏水并且ph大于6且小于10;过滤所述共沉淀溶液得到共沉淀物的步骤;以及烧制所述共沉淀物得到afe2o4-fe2o3产物的步骤。根据本发明的另一方面,提供一种氧化脱氢用催化剂的制备方法,该方法包括:混合三价阳离子铁(fe)前体与二价阳离子金属(a)前体以形成浓度为23重量%至35重量%的混合水溶液的步骤;将所述混合水溶液和碱性水溶液以2g/min至10g/min的滴加速率一起逐滴加入共沉淀槽中以得到其中同时包含afe2o4和fe2o3的共沉淀溶液的步骤,所述共沉淀槽中含有含量为所述混合水溶液中含有的蒸馏水的含量(重量)的0.5倍以上且小于3倍的5℃至30℃的蒸馏水且ph为8至9;过滤所述共沉淀溶液得到共沉淀物的步骤;以及烧制所述共沉淀物得到afe2o4-fe2o3产物的步骤。根据本发明的另一方面,提供一种氧化脱氢用催化剂,包含afe2o4结构和fe2o3结构,其中a是选自铜(cu)、镭(ra)、钡(ba)、锶(sr)、钙(ca)、铍(be)、锌(zn)、镁(mg)、锰(mn)和钴(co)中的一种或多种,其中afe2o4结构的含量为20重量%至99重量%,fe2o3结构的含量为1重量%至80重量%。有益效果从上面的描述显而易见的是,本发明有利地提供一种催化剂的制备方法,该制备方法调节包含三价阳离子铁前体和二价阳离子金属前体的混合水溶液的浓度以合成高浓度的混合水溶液,从而提高直通率,降低废水排放量,并提供具有提高的反应性的催化剂。此外,根据本发明的催化剂可应用于固定床反应器、移动床反应器和流化床反应器,并且具有广泛的用途。附图说明图1示出了根据实施例1至6制备的锌铁氧体催化剂的znfe2o4结构和α-fe2o3结构的xrd数据。图2示出了根据比较例5至10制备的锌铁氧体催化剂的znfe2o4结构和α-fe2o3结构的xrd数据。具体实施方式为了克服在
背景技术:
部分讨论的氧化脱氢用催化剂的常规制备方法的技术和空间的限制,本发明人开发了一种催化剂的制备方法,该制备方法调节包含三价阳离子铁前体和二价阳离子金属前体的混合水溶液的浓度以合成高浓度的混合水溶液,从而提高直通率,降低废水排放量,并提供具有改善的反应性的催化剂,由此完成本发明。本发明的氧化脱氢用催化剂可以根据下面的工艺制备。在步骤1中,三价阳离子铁(fe)前体和二价阳离子金属(a)前体混合,从而形成大于16.5重量%并小于53.5重量%的混合水溶液。三价阳离子铁(fe)前体和二价阳离子金属前体各自独立地可以是,例如,选自硝酸盐、铵盐、硫酸盐和氯化物中的一种或多种。就成本、可获得性和大规模催化剂生产成本而言,优选硝酸盐或氯化物。二价阳离子金属(a)可以是,例如,选自铜(cu)、镭(ra)、钡(ba)、锶(sr)、钙(ca)、铍(be)、锌(zn)、镁(mg)、锰(mn)和钴(co)中的一种或多种。优选锌(zn)或锰(mn)。关于本发明的氧化脱氢用催化剂,重要的是铁与二价阳离子金属之间通过离子交换获得共沉淀物。因此,粉末不适合用于分散铁和二价阳离子,并且难于产生理想的活性物质。另一方面,由于混合水溶液是液体,可以促进铁和二价阳离子金属之间的离子交换,因此可以容易地制备理想的共沉淀物。关于水溶液中铁前体和二价阳离子金属前体之间的适当的混合比,基于1mol的二价阳离子金属(a)前体,三价阳离子铁(fe)前体一般使用的量为1.5mol至10mol,1.5mol至4mol或1.5mol至2.5mol。在该范围内,可以产生理想的活性物质。混合水溶液以大于16.5重量%且小于53.5重量%,18重量%至50重量%,20重量%至40重量%,或23重量%至35重量%的浓度存在。在该范围内,氧化脱氢用催化剂的反应性得到提高并大幅提高直通率。混合水溶液可以使用,例如,10重量%至30重量%、10重量%至25重量%、15重量%至25重量%或20重量%至25重量%的三价阳离子铁(fe)前体和3重量%至10重量%、3重量%至8重量%、4重量%至7重量%或4重量%至6重量%的二价阳离子金属前体在60重量%至87重量%、67重量%至87重量%、68重量%至81重量%或71重量%至76重量%的蒸馏水中制备。混合水溶液的ph可以为,例如,0至4、1至3或1至2。在该范围内,在催化剂的合成过程中可以稳定地产生理想的活性成分。在步骤2中,将混合水溶液和碱性水溶液一起逐滴加入含有蒸馏水并且具有ph经调节的共沉淀槽中,由此得到afe2o4和fe2o3同时存在的共沉淀溶液。表述“逐滴加入”是指,例如,将两种或更多种溶液逐滴加入同一位置或容器中。作为蒸馏水,可以提供大于0℃且小于40℃、大于0℃至30℃或5℃至25℃的蒸馏水。在该范围内,直通率得以提高并且活性催化剂的含量得以调节,由此使根据氧化脱氢的丁二烯的选择性和产率变得优异。在一个实施方案中,蒸馏水的供应量可以为步骤1中的混合水溶液中含有的蒸馏水的重量的0.5倍以上、0.5倍以上且小于3倍或0.5倍以上且小于2倍。在该范围内,直通率得以提高,共沉淀溶液的ph得以恒定保持,并且制备过程中产生的废水的排放量下降。作为蒸馏水,可以使用例如各种碱性物质如氢氧化钠或氨的水溶液,这样可以先调节共沉淀槽的ph。碱性水溶液各自以0.001重量%至0.01重量%、0.001重量%至0.008重量%或0.003重量%至0.007重量%的浓度存在。这些碱性水溶液可以降低由于在初始催化剂合成步骤加入混合水溶液而引起的ph变化的幅度,从而产生具有均匀组成的催化剂。共沉淀槽的ph可以调节到,例如,大于6且小于11、7至小于11、8至10或8至9。在该范围内,afe2o4的含量可以在逐滴加入混合水溶液时调节到预定的范围内。前体水溶液可以以2g/min以上、2g/min以上且小于32g/min、2g/min至10g/min或2g/min至7g/min的速率逐滴加入共沉淀槽中。在该范围内,直通率得以提高并将活性成分的含量调节在预定范围内,这样使根据氧化脱氢的丁二烯的选择性和产率变得优异。对与前体水溶液分开提供的碱性水溶液没有特别的指定,只要它是例如各种碱性物质如氢氧化钠和氨的各自水溶液即可。碱性水溶液的浓度可以是,例如,10重量%至35重量%、20重量%至33重量%或者25重量%至30重量%。在该范围内,共沉淀溶液的ph可以得到适当保持。共沉淀溶液的ph可以保持在例如7以上且小于11、8至10或者8至9。在该范围内,共沉淀物的直通率得以提高并使根据氧化脱氢的丁二烯的选择性和产率变得优异。在进行步骤3中的过滤之前,在步骤2中得到的共沉淀溶液还可以进行搅拌步骤;熟化步骤;或者搅拌和熟化步骤。在这种情况下,共沉淀溶液中的前体的共沉淀可以充分地进行。搅拌和熟化步骤各自可以进行,例如,30分钟至3小时、30分钟至2小时或30分钟至1小时30分钟。在步骤3中,过滤共沉淀溶液得到共沉淀物。对过滤没有具体的限制,只要它是本领域中常规使用的方法即可。过滤可以是,例如,真空过滤。作为具体的实例,可以在100毫巴至300毫巴或者160毫巴至250毫巴的减压下过滤共沉淀溶液。过滤后,根据需要可以洗涤共沉淀物。过滤后,进行洗涤工艺,排出废水,得到固体共沉淀物。由于在高浓度下进行催化剂合成工艺,步骤2中产生的废水的排放量下降。共沉淀物可以通过常规干燥器在60至100℃、70至100℃或者80至100℃下干燥12至20小时、14至20小时或者14至18小时。固体可以以各种形式提供,如粉末、模制品形状或在铺展在基底上的薄膜。在步骤4中,烧制共沉淀物得到afe2o4-fe2o3产物。过滤后的共沉淀物可以通过常规烧制炉在例如400至800℃、500至800℃或者550至750℃下烧制1至10小时、3至8小时或者5至7小时。过滤后的共沉淀物可以通过常规的干燥器在,例如,60至100℃、70至100℃或80至100℃下干燥12至20小时、14至20小时或者14至18小时。此外,干燥后的共沉淀物可以通过常规的烧制炉在,例如,400至800℃、500至800℃或550至750℃下烧制1至10小时、3至8小时或5至7小时。烧制可以通过本领域中常规使用的热处理方法进行。本发明的氧化脱氢用催化剂也可以通过下面的工艺制备。也就是说,三价阳离子铁(fe)前体与二价阳离子金属(a)前体混合形成浓度为23重量%至35重量%的混合水溶液。所述混合水溶液和碱性水溶液以2g/min至10g/min的滴加速率一起逐滴加入共沉淀槽中以得到同时包含afe2o4和fe2o3的共沉淀溶液,所述共沉淀槽中含有含量为所述混合水溶液中含有的蒸馏水的量(重量)的0.5倍以上且小于3倍的5℃至30℃的蒸馏水且ph为8至9。过滤所述共沉淀溶液得到共沉淀物。烧制所述共沉淀物得到afe2o4-fe2o3产物。根据前述制备方法,本发明的特征在于使用高浓度合成代替常规的低浓度合成。根据本发明的方法制备的催化剂包含同时存在的afe2o4和fe2o3。因此,当将该催化剂用于氧化脱氢时,转化率提高,同时产物的选择性提高,并防止了副反应。也就是说,本发明采用高浓度合成代替低浓度合成的简单方法。因此,当本发明的催化剂用于氧化脱氢时,催化剂的反应性得到提高,同时提高了工艺的单位产量。根据本发明的氧化脱氢用催化剂包含afe2o4结构和fe2o3结构。此处,a是选自铜(cu)、镭(ra)、钡(ba)、锶(sr)、钙(ca)、铍(be)、锌(zn)、镁(mg)、锰(mn)和钴(co)中的一种或多种。afe2o4结构的含量为20重量%至99重量%,fe2o3结构的含量为1重量%至80重量%。在一个实施方案中,afe2o4结构的含量可以为50重量%至95重量%,fe2o3结构的含量可以为5重量%至50重量%。在一个实施方案中,afe2o4结构的含量可以为83重量%至95重量%,fe2o3结构的含量可以为5重量%至17重量%。在一个实施方案中,afe2o4结构的含量可以为85重量%至95重量%,fe2o3结构的含量可以为5重量%至15重量%。作为xrd分析的结果,afe2o4结构具有最大峰值强度在34.5°至35.5°范围内的第一峰,第二峰值强度在29.5°至30.5°的第二峰,以及第三峰值强度在62°至63°的第三峰。afe2o4结构可以是,例如,znfe2o4或mnfe2o4。作为xrd分析的结果,fe2o3结构具有最大峰值强度在33°至34°范围内的第一峰,第二峰值强度在35°至36°范围内的第二峰,以及第三峰值强度在53.5°至54.5°范围内的第三峰。fe2o3结构可以是,例如,α-fe2o3。所述催化剂可应用于氧化脱氢用的固定床反应器、移动床反应器和流化床反应器,并且作为催化剂具有广泛的用途。现在,将参照下面优选的实施例更详细地描述本发明。然而,提供这些实施例仅用于说明的目的。本领域技术人员应当理解的是,在不脱离本发明的范围和精神的情况下,可以进行各种修改、添加和替换。因此,显而易见的是,这些修改、添加和替换在本发明的范围之内。[实施例]<实施例1至6>在实施例1至6中,锌用作二价金属阳离子并根据高浓度合成法制备催化剂。实施例1在步骤1中,将18.029g的氯化锌(zncl2)和71.495g的氯化铁(fecl3)溶于233.39g的蒸馏水中,由此制备322.914g的ph1的金属前体水溶液(前体溶液的浓度:27.7重量%)。此处,金属前体水溶液中包含的金属成分的摩尔比为fe:zn=2:1。在步骤2中,将0.005重量%的氨溶液加入共沉淀槽中233.39g的室温(25℃)的蒸馏水中,将ph调节到8,共沉淀槽配备有用于金属前体水溶液的出口和用于氨的水溶液的出口。通过金属前体水溶液出口以2g/min的速率逐滴加入制备的金属前体水溶液混合物的同时,通过氨的水溶液出口在室温下提供浓度为28%至30%的氨的水溶液(ph13.6),由此使共沉淀槽中的共沉淀溶液的ph恒定地保持在8。在金属前体水溶液的加入完成后,搅拌共沉淀溶液1小时以使共沉淀充分。停止搅拌后,使沉淀物在室温下静置1小时直到沉淀物完全沉淀,由此完成相分离。在步骤3中,共沉淀溶液通过真空过滤器在200毫巴的压力条件下真空过滤,由此得到共沉淀物。洗涤得到的共沉淀物。接下来,排出废水并在90℃下干燥16小时。在步骤4中,将干燥后的共沉淀物放入烧制炉中并在650℃下热处理6小时。结果,制得锌铁氧体催化剂。实施例2除了在步骤2中以7g/min的滴加速率加入前体溶液之外,以与实施例1相同的方式制备锌铁氧体催化剂。实施例3除了在步骤2中以10g/min的滴加速率加入前体溶液之外,以与实施例1相同的方式制备锌铁氧体催化剂。实施例4除了在步骤2中提供到共沉淀槽中的水的温度为5℃代替室温(25℃)以外,以与实施例1相同的方式制备锌铁氧体催化剂。实施例5除了在步骤1中前体溶液的浓度为35重量%代替27.7重量%以外,以与实施例1相同的方式制备锌铁氧体催化剂。实施例6除了在步骤1中前体溶液的浓度为23重量%代替27.7重量%以外,以与实施例1相同的方式制备锌铁氧体催化剂。<比较例1至5>在比较例1至5中,锌用作二价金属阳离子并根据各种低浓度合成法合成催化剂。具体地,除了使用下表1中总结的在步骤1中制备的构成金属前体水溶液的氯化锌(zncl2)、氯化铁(fecl3)和蒸馏水的含量、提供到共沉淀槽中的水的含量以及搅拌步骤中的ph之外,以与实施例1相同的方式制备锌铁氧体催化剂。【表1】<比较例6至10>在下面的比较例中,锌用作二价金属阳离子并根据高浓度合成法制备催化剂。比较例6使用比比较例5高30倍的高浓度合成法,比较例7至10通过改变实施例1的高浓度合成法的条件进行。比较例6以与比较例5相同的方式制备锌铁氧体催化剂,不同的是,在步骤1中使用71.495g的fecl3.6h2o、18.029g的zncl2和41.8g的蒸馏水制备68.18重量%的前体溶液,共沉淀槽中的共沉淀溶液的ph保持在8、搅拌步骤中的ph也保持在8,并将425g的水提供到共沉淀槽中。比较例7除了在步骤2中,以32g/min的滴加速率加入前体溶液外,以与实施例1相同的方式制备锌铁氧体催化剂。比较例8除了在步骤2中,提供到共沉淀槽中的水的温度是40℃代替室温(25℃)之外,以与实施例1相同的方式制备锌铁氧体催化剂。比较例9除了在步骤2中,使共沉淀槽中的共沉淀溶液的ph保持在10之外,以与实施例1相同的方式制备锌铁氧体催化剂。比较例10除了在步骤2中,使共沉淀槽中的共沉淀溶液的ph保持在11之外,以与实施例1相同的方式制备锌铁氧体催化剂。<实验例>使用根据实施例1至6和比较例1至10的锌铁氧体催化剂,如下进行各种实验。<实验例1:xrd实验>为了研究各锌铁氧体催化剂的含量和结构,对锌铁氧体催化剂进行xrd分析。结果示于图1和2中。参考图1和2,实施例1至6的锌铁氧体催化剂的xrd分析结果(图1)和比较例5至10的锌铁氧体催化剂的xrd分析结果(图2)如下:作为xrd分析的结果,afe2o4结构具有最大峰值强度在34.5°至35.5°范围内的第一峰,第二峰值强度在29.5°至30.5°范围内的第二峰,和第三峰值强度在62°至63°范围内的第三峰;fe2o3结构具有最大峰值强度在33°至34°范围内的第一峰,第二峰值强度在35°至36°范围内的第二峰强度,和第三峰值强度在53.5°至54.5°范围内的第三峰。具体地,当图1的实施例1(前体溶液的浓度:27.7重量%)和图2的比较例5(前体溶液的浓度:6.67重量%)和比较例6(前体溶液的浓度:68.18重量%)相互比较时,可以证实,当前体溶液的浓度太低(对应于比较例5)或太高(对应于比较例6)时,znfe2o4结构的结晶度下降,而fe2o3结构的结晶度升高。此外,当图1的实施例1(混合水溶液的滴加速度:2g/min)、实施例2(混合水溶液的滴加速度:7g/min)和实施例3(混合水溶液的滴加速度:10g/min)和图2的比较例7(混合水溶液的滴加速度:32g/min)相互比较时,可以证实随着前体溶液的滴加速度增加,znfe2o4结构的结晶度下降,而fe2o3结构的结晶度升高。此外,当图1的实施例1(提供到共沉淀槽中的水的温度:25℃)、实施例4(提供到共沉淀槽中的水的温度:5℃)和图2的比较例8(提供到共沉淀槽中的水的温度:40℃)相互比较时,可以证实,当提供到共沉淀槽中的水的温度超出合适的温度范围时,znfe2o4结构的结晶度下降,而fe2o3结构的结晶度升高。此外,当图1的实施例1(共沉淀溶液的ph:8)和图2的比较例6(共沉淀溶液的ph:8)、比较例9(共沉淀溶液的ph:10)和比较例10(共沉淀溶液的ph:11)相互比较时,可以证实,随着共沉淀溶液的ph升高fe2o3结构增加,并且znfe2o4结构在共沉淀溶液的ph为8的实施例1中形成的最多。由这些结果可以证实,前体溶液的浓度、前体溶液的滴加速率、提供到共沉淀槽中的水的温度以及在共沉淀槽中的共沉淀溶液保持的ph分别影响znfe2o4结构和fe2o3结构的结晶度。通过xrd分析测量的znfe2o4结构含量和fe2o3结构含量(重量%)总结在下面的表2中。【表2】如表2所示,可以证实,在实施例1至6和比较例5至10中,znfe2o4结构的含量为20重量%至99重量%,fe2o3结构的含量为1重量%至80重量%。特别是,可以证实,在根据本发明的实施例1至6中,znfe2o4结构的含量为75重量%至95重量%,fe2o3结构的含量为5重量%至25重量%。由该结果可以证实,znfe2o4结构的结晶度显著增加。<实验例2:直通率实验>根据实施例1的高浓度合成方法合成的锌铁氧体的直通率和根据比较例1至5的低浓度合成方法合成的锌铁氧体催化剂的直通率相互比较。为了易于比较,在含有9335.5g蒸馏水的反应器中测量了对于各催化剂的znfe2o4结构的产量(单位:mol)。结果总结在下面的表3中。【表3】如表3所示,可以证实根据本发明的实施例1的催化剂的直通率比根据比较例1至5的催化剂的直通率提高5倍以上至33倍以上。<实验例3:合成的催化剂中元素的分析实验>在实施例1至6和比较例5至10中分别合成的锌铁氧体催化剂通过能量色散光谱仪(eds)进行元素分析。结果总结在下面的表4中。【表4】分类实施例1实施例2实施例3实施例4实施例5实施例6fe73.6173.7674.1670.0770.1669.37zn26.3926.2425.849.9320.8430.63fe/zn2.792.812.842.342.352.26分类比较例5比较例6比较例7比较例8比较例9比较例10fe68.376.5578.6478.2279.2386.02zn31.723.4521.3621.7820.7713.98fe/zn2.23.263.683.593.826.15如表4所示,可以证实,与根据比较例6至10的使用高浓度前体溶液合成的催化剂相比,使用根据本发明的实施例1至6的高浓度前体溶液合成的催化剂达到理想的fe/zn摩尔比(理想的fe/zn摩尔比=2)。<实验例5:氧化脱氢>分别使用实施例1和4中合成的锌铁氧体催化剂和比较例5中合成的锌铁氧体催化剂,通过下面的氧化脱氢生成丁二烯。结果总结在下面的表5中。使用直径为1.8cm的金属管式反应器作为反应器,并将实施例或对比例中制备的催化剂固定为催化剂层体积为30立方厘米。包含40重量%的顺式-2-丁烯和60重量%的反式-2-丁烯的2-丁烯混合物和氧气用作反应物,将氮气和水蒸气注入反应器中。反应物之间的摩尔比如下设定:氧气/丁烯:0.75,水蒸气/丁烯:12,氮气/丁烯:3。通过汽化器在340℃下使水汽化产生的水蒸气与反应物一起注入反应器中。通过用于液体的质量流量控制器将丁烯混合物的量调节到0.625立方厘米/分钟,通过用于气体的质量流量控制器调节氧气和氮气的量,通过液体泵控制注入速率来调节水蒸汽的量。将反应器的气体时空速度(ghsv)设定为500h-1,反应在大气压(压力表:0)和表5总结的温度下进行。反应后,产物进行气相色谱(gc)分析,混合物中各丁烯的转化率(x)、1,3-丁二烯选择性(s_bd)、1,3-丁二烯产率(y)、cox选择性(s_cox)以及其它的选择性(s_其它)根据下面的等式1至3计算:[等式1]转化率(%)=(反应的丁烯的摩尔数/提供的丁烯的摩尔数)×100[等式2]选择性(%)=(生成的1,3-丁二烯或cox的摩尔数/反应的丁烯的摩尔数)×100[等式3]产率(%)=(生成的1,3-丁二烯的摩尔数/提供的丁烯的摩尔数)×100【表5】分类t(℃)xs_bdys_coxs_其它实施例133077.4389.0668.969.801.14实施例432080.6188.8571.6210.380.77比较例533771.9091.5665.837.011.43如表5所示,可以证实根据本发明的实施例1和4显示出优异的丁烯转化率和产率。作为参考,可以证实实施例4(提供到共沉淀槽中的水的温度:5℃)的丁烯转化率和产率优于实施例1(提供到共沉淀槽中的水的温度:25℃)的丁烯转化率和产率。同时,可以证实使用根据低浓度合成方法的催化剂的比较例5显示出较差的丁烯转化率和丁二烯产率。总之,根据本发明,通过使用高浓度的催化剂代替低浓度的催化剂,制备工艺简化,因此具有催化效率和成本方面的优点。也就是说,可以制备能够保持催化剂反应性并提高直通率的催化剂。当前第1页12