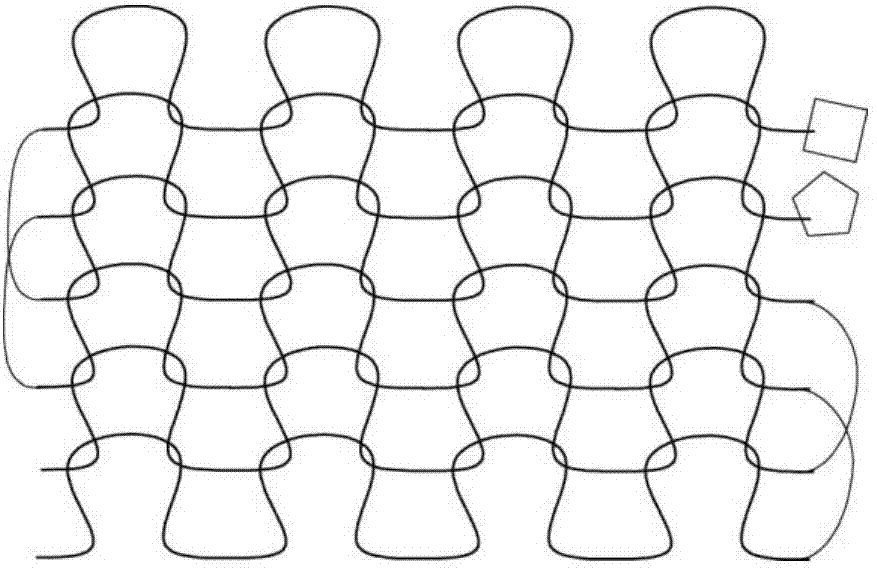
本发明涉及气体分离
技术领域:
,尤其涉及一种氮氧气体分离复合膜及其制备方法。
背景技术:
过去30年,气体膜分离技术得了较大的发展,已广泛应用于许多气体的分离及提纯工艺。混合气体在压力驱动下,基于不同组分在膜材料中的溶解-扩散能力不同而得到分离。膜分离法由于可靠性高,能耗低,且设备制造使用简便等优点,正在逐步取代其他传统气体分离工艺。特别在中小型分离项目中,膜分离法的经济优势突出,独特的性价比是传统工艺无法比拟的。在膜法气体分离研究中,氧氮分离是其中的一大重点。早在上世纪70年代,由于石油危机的发生,促使各国投入大量人力物力来研究膜材料及膜法富氧燃烧技术,用于节能减排,已实现工业化应用。目前广泛应用的氧氮分离膜材料多为高分子分离膜,其主要为采用具有选择透过性的高分子材料作为分离层,来实现氮氧的分离。通常使用树脂(或共聚物)包括聚有机硅氧烷类树脂、聚四氟乙烯树脂或聚烯烃树脂、无定形氟树脂、全氟二氧杂环戊烯二元共聚物等,来制备多孔质支撑膜或分离膜,但是这些树脂制备的膜或多或少存在一些问题,如气体分离效率相对不高、气体透过速度慢、膜的强度不充分等方面的问题。有些为了提高膜的机械强度而增大膜的厚度或者将分离膜与支撑材料进行复合,但是膜厚度过大,则气体性能降低,气体分离性的显著变差;若支撑材料与分离膜之间的黏结较差时,将会在两相之间出现缝隙(这种缝隙可能是因为支撑材料与分离膜之间的排斥力或是支撑材料与分离膜之间的热膨胀系数的差异导致的)。这种缝隙是没有分离能力的,缝隙的存在大大影响了膜的分离性能。所以由于受现有高分子材料特性的制约,很难找到选择性、透过性、高强度相统一的材料应用于氧氮分离。目前使用最广泛的为硅橡胶复合分离膜,其氧氮选择性仅为2.1,而其他氧氮选择性高的膜材料,在相同条件下其透过性远远低于硅橡胶复合分离膜。这些都无法满足大规模工业化应用的需要。如何设计并制备分离效率高、分离速度快、膜强度大、支撑物与分离膜黏结性好,并且选择性高的气体分离复合膜显得尤为重要。技术实现要素:有鉴于此,本发明的目的是提供一种氮氧气体分离复合膜及其制备方法,利用薄层基底材料支撑膜,并且膜与基底材料之间复合紧密,粘结度好,基底材料与金属凝胶复合而成的复合膜具有分离效率高、强度大,并且选择性高的特点。本发明通过以下技术手段解决上述技术问题:一种氮氧气体分离复合膜,所述复合膜是以不锈钢纤维和玻璃纤维混合编织制备成基底材料,与金属凝胶浸渍涂覆到基底材料上经高温烧结后,形成具有定向微孔结构分离膜复合而成的。不锈钢纤维和玻璃纤维混合编织成网状的基底材料,不仅具有高强度、耐高温的特点,还具有耐腐蚀、抗氧化等性能,可以为复合膜提供很好的支撑效果,而金属凝胶浸渍涂覆到基底材料上,经过高温烧结后,金属凝胶可以形成很多纳米级定向微孔,具有较高的氮氧选择分离性。玻璃纤维不具有明显的熔点,在烧结过程中,玻璃纤维有软化迹象,与金属凝胶黏结在一起,形成不可分离的复合膜,不会因为之间存在缝隙而影响分离性能。进一步,所述基底材料中不锈钢纤维和玻璃纤维的质量比为(0.5-0.8):1,所述不锈钢纤维的单丝直径为2-3μm,所述玻璃纤维为中碱玻璃纤维,单丝直径为2-3μm。进一步,所述金属凝胶的制备原料包括:乙醇硅、异丙醇钛、乙醇铝、乙醇、丁醇、氯化镁、硝酸钠。进一步,所述乙醇、丁醇的体积比为0.5:1。进一步,所述复合膜的厚度为20-50μm。进一步,所述复合膜的孔隙率为60-80%,平均孔径为0.350-0.360nm,氮氧分离系数为3.6以上。o2的直径为0.346nm左右,n2的直径为0.364nm左右,本发明制备的复合膜的有效孔径为0.350-0.360nm,复合膜允许o2分子通过,拦截n2分子,所以对氧氮具有较好的分离作用,氮氧分离系数较高。进一步,氮氧气体分离复合膜的制备方法包括以下步骤:基底材料制备:将不锈钢纤维和玻璃纤维混合交叉编织成网状基底材料;金属凝胶制备:将乙醇硅、异丙醇钛、乙醇铝溶解于乙醇和丁醇的混合溶液中,并以1200-1500r/min的速率搅拌3-5min后加入氯化镁、硝酸钠得到混合物,调节混合物ph=4-5,并加热至90-100℃,同时以2000-2500r/min的搅拌速率搅拌至胶状,得到金属凝胶;复合膜制备:将基底材料置于金属凝胶中搅拌均匀,平铺后置于10-15℃的温度下冷却干燥,完全干燥后于温度为800-950℃,压强为3mpa的条件下烧结3-3.5h,取出后于5-10℃风冷降温,完全冷却后得到复合膜。金属的醇盐溶解在溶剂中时,经过水解会形成凝胶状,胶体粒子之间相互连接形成了空间网状结构,在网状空间内会充满了溶液,在溶液里面加入改性剂氯化镁和硝酸钠,在金属凝胶烧结成孔的过程中,水会快速的被蒸发掉,这些化合物具有良好的晶型,进而修饰网状结构,形成定向均一的孔。进一步,所述基底材料制备步骤中,可将1-5层网状基底材料共同压制使用,且压制的压力不超过2mpa。基底材料的叠加厚度越多,强度越高,氮氧分离系数越大,但是分离速率越缓慢,所以,叠加层数不超过5层时,具有较高的分离效率和强度。进一步,所述金属凝胶制备步骤中,混合物的含水量为25-30%。形成的纳米微孔的粒径、孔隙率与含水量有一定的相关性。在高温烧制过程中,含水量越多,凝胶固化形成的冰晶增多,经升华后,得到的复合膜孔径大、孔隙率也大,但随含水量的增加,孔隙率增长缓慢。根绝氮、氧气体分子的粒径可知所以,若孔径较大,分离效果下降,所以在混合物的含水量为20-30%的时候,复合膜的孔径最为合适,且孔隙率较高。有益效果:本发明提供的一种氮氧气体分离复合膜,采用不锈钢纤维和玻璃纤维混合编织成网状的基底材料,与金属凝胶混合烧结制备而成,形成强度高、支撑性好、且黏结度好的复合膜,并且金属凝胶在高温烧结后形成的微孔,孔径小,孔隙率大,具有分离效率高、分离速度快、选择性高的特点。附图说明图1为基底材料的编织效果图;具体实施方式以下将结合具体实施例和附图1对本发明进行详细说明:实施例1:复合膜的制备一:本实施例采用以下方法制备复合膜:按照以下重量称取原料:50g不锈钢纤维、100g玻璃纤维、120g乙醇硅、60g异丙醇钛、100g乙醇铝、300ml乙醇、600ml丁醇、50g氯化镁、40g硝酸钠。基底材料制备:将不锈钢纤维和玻璃纤维混合交叉编织成如图1所示的网状基底材料;金属凝胶制备:将乙醇硅、异丙醇钛、乙醇铝溶解于乙醇和丁醇的混合溶液中,并以1200r/min的速率搅拌5min后,加入氯化镁、硝酸钠搅拌均匀,得到混合物,调节混合物ph=4,混合物的含水量为40%,并加热至100℃,同时以2000r/min的搅拌速率搅拌至胶状,得到金属凝胶;复合膜制备:将2层基底材料于1.5mpa下压制在一起后,置于金属凝胶中搅拌均匀,使基底材料被金属凝胶完全包裹,然后平铺后置于15℃的温度下冷却干燥,完全干燥后于温度为950℃,压强为3mpa的条件下烧结3h,取出后于10℃风冷降温,完全冷却后得到复合膜。实施例2:复合膜的制备二:本实施例采用以下方法制备复合膜:按照以下重量称取原料:50g不锈钢纤维、100g玻璃纤维、120g乙醇硅、60g异丙醇钛、100g乙醇铝、300ml乙醇、600ml丁醇、50g氯化镁、40g硝酸钠。基底材料制备:将不锈钢纤维和玻璃纤维混合交叉编织成如图1所示的网状基底材料;金属凝胶制备:将乙醇硅、异丙醇钛、乙醇铝溶解于乙醇和丁醇的混合溶液中,并以1200r/min的速率搅拌5min后,加入氯化镁、硝酸钠搅拌均匀,得到混合物,调节混合物ph=4,混合物的含水量为30%,并加热至100℃,同时以2000r/min的搅拌速率搅拌至胶状,得到金属凝胶;复合膜制备:将2层基底材料于1.5mpa下压制在一起后,置于金属凝胶中搅拌均匀,使基底材料被金属凝胶完全包裹,然后平铺后置于15℃的温度下冷却干燥,完全干燥后于温度为950℃,压强为3mpa的条件下烧结3h,取出后于10℃风冷降温,完全冷却后得到复合膜。实施例3:复合膜的制备三本实施例采用以下方法制备复合膜:按照以下重量称取原料:80g不锈钢纤维、100g玻璃纤维、120g乙醇硅、60g异丙醇钛、100g乙醇铝、300ml乙醇、600ml丁醇、50g氯化镁、40g硝酸钠。基底材料制备:将不锈钢纤维和玻璃纤维混合交叉编织成如图1所示的网状基底材料;金属凝胶制备:将乙醇硅、异丙醇钛、乙醇铝溶解于乙醇和丁醇的混合溶液中,并以1200r/min的速率搅拌5min后,加入氯化镁、硝酸钠搅拌均匀,得到混合物,调节混合物ph=4,混合物的含水量为30%,并加热至100℃,同时以2000r/min的搅拌速率搅拌至胶状,得到金属凝胶;复合膜制备:将2层基底材料于1.5mpa下压制在一起后,置于金属凝胶中搅拌均匀,使基底材料被金属凝胶完全包裹,然后平铺后置于15℃的温度下冷却干燥,完全干燥后于温度为950℃,压强为3mpa的条件下烧结3h,取出后于10℃风冷降温,完全冷却后得到复合膜。实施例4:复合膜的制备四:本实施例采用以下方法制备复合膜:按照以下重量称取原料:80g不锈钢纤维、100g玻璃纤维、120g乙醇硅、60g异丙醇钛、100g乙醇铝、300ml乙醇、600ml丁醇、50g氯化镁、40g硝酸钠。基底材料制备:将不锈钢纤维和玻璃纤维混合交叉编织成如图1所示的网状基底材料;金属凝胶制备:将乙醇硅、异丙醇钛、乙醇铝溶解于乙醇和丁醇的混合溶液中,并以1500r/min的速率搅拌3min后,加入氯化镁、硝酸钠搅拌均匀,得到混合物,调节混合物ph=5,混合物的含水量为25%,并加热至90℃,同时以2500r/min的搅拌速率搅拌至胶状,得到金属凝胶;复合膜制备:将6层基底材料于1.5mpa下压制在一起后,置于金属凝胶中搅拌均匀,使基底材料被金属凝胶完全包裹,然后平铺后置于10℃的温度下冷却干燥,完全干燥后于温度为800℃,压强为3mpa的条件下烧结3.5h,取出后于5℃风冷降温,完全冷却后得到复合膜。实施例5:复合膜的制备五:本实施例采用以下方法制备复合膜:按照以下重量称取原料:80g不锈钢纤维、100g玻璃纤维、120g乙醇硅、60g异丙醇钛、100g乙醇铝、300ml乙醇、600ml丁醇、50g氯化镁、40g硝酸钠。基底材料制备:将不锈钢纤维和玻璃纤维混合交叉编织成如图1所示的网状基底材料;金属凝胶制备:将乙醇硅、异丙醇钛、乙醇铝溶解于乙醇和丁醇的混合溶液中,并以1500r/min的速率搅拌3min后,加入氯化镁、硝酸钠搅拌均匀,得到混合物,调节混合物ph=5,混合物的含水量为25%,并加热至90℃,同时以2500r/min的搅拌速率搅拌至胶状,得到金属凝胶;复合膜制备:将5层基底材料于1.5mpa下压制在一起后,置于金属凝胶中搅拌均匀,使基底材料被金属凝胶完全包裹,然后平铺后置于10℃的温度下冷却干燥,完全干燥后于温度为800℃,压强为3mpa的条件下烧结3.5h,取出后于5℃风冷降温,完全冷却后得到复合膜。实施例6:复合膜的制备六:本实施例采用以下方法制备复合膜:按照以下重量称取原料:80g不锈钢纤维、100g玻璃纤维、120g乙醇硅、60g异丙醇钛、100g乙醇铝、300ml乙醇、600ml丁醇、50g氯化镁、40g硝酸钠。基底材料制备:将不锈钢纤维和玻璃纤维混合交叉编织成如图1所示的网状基底材料;金属凝胶制备:将乙醇硅、异丙醇钛、乙醇铝溶解于乙醇和丁醇的混合溶液中,并以1500r/min的速率搅拌3min后,加入氯化镁、硝酸钠搅拌均匀,得到混合物,调节混合物ph=5,混合物的含水量为25%,并加热至90℃,同时以2500r/min的搅拌速率搅拌至胶状,得到金属凝胶;复合膜制备:将单层基底材料置于金属凝胶中搅拌均匀,使基底材料被金属凝胶完全包裹,然后平铺后置于10℃的温度下冷却干燥,完全干燥后于温度为800℃,压强为3mpa的条件下烧结3.5h,取出后于5℃风冷降温,完全冷却后得到复合膜。将以上实施例制备的复合膜分别进行厚度、孔隙率、平均孔径、膜面积测量;复合膜强度实验:分别对制备的复合膜进行通气,然后将气体增压,记录复合膜破损时的气体压强,气体采用氮气;分离系数实验:分离系数反映膜对气体各组分透过的选择性,对于含有a、b两组分的混合物,分离系数定义为aa/b=(ya/yb)/(xa/xb),式中xa、xb为原料中组分a与组分b的浓度;ya、yb为透过物中组分a与组分b的浓度;aa/b越大,表明两组分的透过速率相差越大,膜的选择性越好,分离程度越高其中,a为氧气,b为氮气。将以上所有实施例制备的复合膜进行10l氮氧混合气体分离实验,记录实验数据,得到表1所示的结果;实施例xaxbyayb分离时间(min)分离系数实施例120806139906.26实施例220807030909.33实施例320807129909.80实施例42080722818010.29实施例5208070301209.33实施例620806535707.42表1记录的实验数据计算结果和测量得到的实验数据如表2所示:实施例1与实施例2制备过程中,控制变量为混合物的含水量,分别为40%和30%,得到的复合膜厚度分为26μm,孔隙率分别为82%和76%,平均孔径分别为0.370和0.355nm,复合膜强度为3mpa,分离时间分别为70min、90min,分离系数分别为6.26、9.33,由以上数据说明,混合物含水量越多,孔隙率越大,平均孔径越大,分离时间越短,但是孔径越大,气体分离效果下降,分离系数越小。实施例2与实施例3制备过程中,控制变量为不锈钢纤维和玻璃纤维的质量比分别为0.5:1和0.8:1,得到的复合膜厚度为26μm,孔隙率分别为76%和75%,平均孔径为0.355nm,复合膜强度分别为3mpa和3.4mpa,分离时间为90min,分离系数分别为9.33、9.80,由以上数据说明,不锈钢纤维含量越多,复合膜强度越大,且分离系数大,分离效果好,但分离时间相同,孔隙率相差不大。实施例4与实施例5、实施例6制备过程中,控制变量为基底材料层数分别为6层和5层、1层,得到的复合膜厚度分别为63μm和48μm、21μm,孔隙率分别为71%和72%、73%,平均孔径为0.351nm,复合膜强度分别为4.2mpa和3.8mpa、2.9mpa,分离时间分别为180min、120min、70min,分离系数分别为10.29、9.33、7.42,由以上数据说明,基底材料层数越多,膜厚度越厚,复合膜强度越大,分离时间越长,分离系数越大,氮氧的分离程度越高。以上实施例仅用以说明本发明的技术方案而非限制,尽管参照较佳实施例对本发明进行了详细说明,本领域的普通技术人员应当理解,可以对本发明的技术方案进行修改或者等同替换,而不脱离本发明技术方案的宗旨和范围,其均应涵盖在本发明的权利要求范围当中。本发明未详细描述的技术、形状、构造部分均为公知技术。当前第1页12