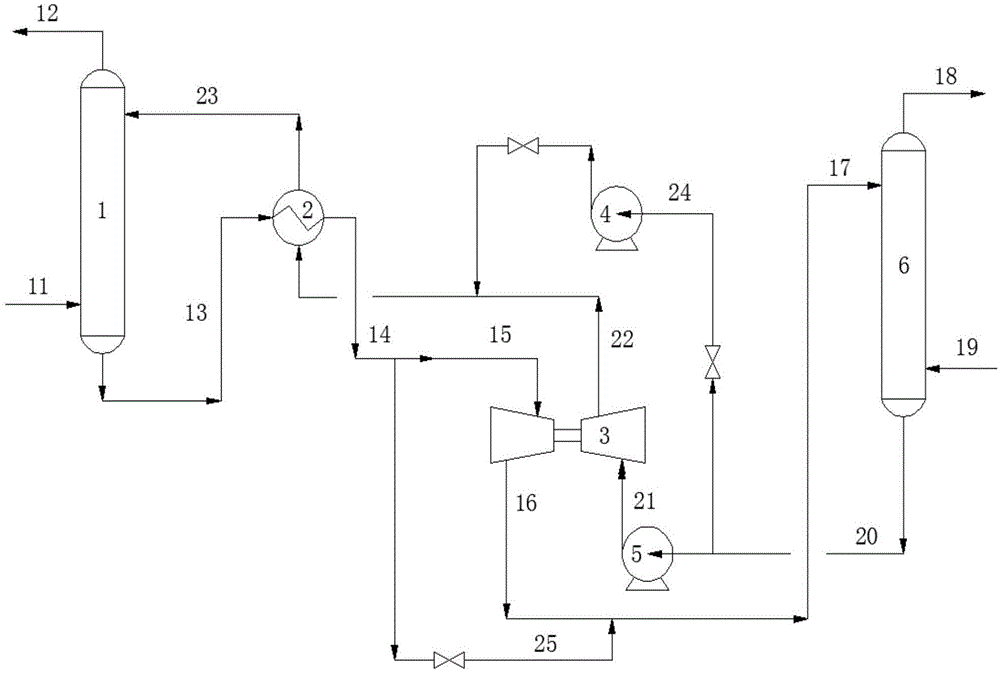
本发明涉及一种甲醇制烯烃装置压力能量的回收方法。
背景技术:
:甲醇制烯烃mto装置是传统煤化工与传统石油化工结合的“桥梁”,在煤制烯烃工程中起着“承前启后”的作用,也是煤制烯烃工程中最为关键、最为核心的工艺生产装置。甲醇制烯烃装置由催化反应单元和烯烃分离单元二部分组成,甲醇经催化反应单元生成乙烯、丙烯等目标产品,这些目标产品组成的产品气含有微量二氧化碳组分需要在烯烃分离单元中加以脱除。由于烯烃分离单元与国内外成熟的乙烯装置分离单元类似,通常采用氢氧化钠naoh水溶液碱洗方法脱除产品气中的二氧化碳组分。但是在产品气碱洗过程中,会产生废碱液和高分子聚合物黄油,这些废碱液和高分子聚合物黄油需要进行无害化处理,达标之后才能排放,由此增加了工艺装置的运行成本。现有技术中,cn200910212788.1从气体混合物中深度脱除二氧化碳的方法,公开了一种从气体混合物中深度脱除二氧化碳的方法。采用一种复合胺水溶液作为吸收剂,将含22vol%的原料气进行脱除二氧化碳的吸收处理,净化后的混合气二氧化碳含量降至0.04~0.80vol%。cn201310032509.x低温甲醇洗烷烃脱氢组合系统及其与烯烃分离系统的耦合系统,公开了一种回收脱除一氧化碳后的生成气中的氢气系统,同时减少二氧化碳的排放。cn201510965864.1一种适用于含高烃富二氧化碳气体的脱烃工艺,公开了一种通过聚酰亚胺膜将二氧化碳气体脱烃的工艺,得到工业级液体二氧化碳和食品级液体二氧化碳。cn201610404569.3海水淡化废水压力回收装置,公开了海水淡化废水压力利用和压力回收的方法,达到了节能减排的目的。选择吸收剂吸收-解吸的方法脱除甲醇制烯烃装置烯烃分离单元产品气中的二氧化碳组分,通常采用不同压力、不同温度工艺参数的吸收剂分离产品气二氧化碳,吸收剂需要反复循环使用。在循环使用时,高压吸收塔塔底出口的高压富液吸收剂通过减压阀减压后送入低压解吸塔塔顶入口,富液吸收剂这部分压力能量被白白浪费;而低压解吸塔塔底出口的低压贫液吸收剂需要通过外部输入能量增压后才能送入高压吸收塔塔顶入口,贫液吸收剂增压不得不使用外部输入的能量。cn200910212788.1和cn201310032509.x以及cn201510965864.1仅仅公开了完成脱除二氧化碳的技术方案,没有甲醇制烯烃装置脱除二氧化碳过程中压力回收的技术方法,也没有将现有的压力能量通过压力回收装置进行压力回收的技术手段,cn201610404569.3仅仅是压力回收的技术方案和工艺路线,无具体工程实施的技术手段,无法应用到工业化生产规模的甲醇制烯烃装置中。由此,现有技术甲醇制烯烃装置脱除二氧化碳操作运行过程中,存在动力电费高、运行能耗大的问题。技术实现要素:本发明所要解决的技术问题是现有技术中动力电费高、运行能耗大的问题,提供一种新的甲醇制烯烃装置压力能量的回收方法,具有动力电费低、运行能耗小的优点。为解决上述问题,本发明采用的技术方案如下:一种甲醇制烯烃装置压力能量的回收方法,包括如下步骤:(a)来自界外甲醇制烯烃装置的产品气11进入吸收塔1塔底,同时经过温度降低、压力增加后的低温贫液吸收剂23进入吸收塔1塔顶,在吸收塔1内,产品气11与低温贫液吸收剂23逆流接触,产品气11中的二氧化碳被低温贫液吸收剂23吸收,脱除二氧化碳的净化产品气12从吸收塔1塔顶流出送到界外;(b)吸收二氧化碳的高压富液吸收剂13从吸收塔1塔底流出,经过贫富吸收剂热交换器2换热升温为高温富液吸收剂14;在正常工况条件下,旁路管线25阀门关闭,该高温富液吸收剂14流到高温富液吸收剂15进入到压力回收装置3减压端入口;(c)高温富液吸收剂15进入压力回收装置3减压端入口,高温富液吸收剂15的压力从高压转换成低压富液吸收剂16,从压力回收装置3流出的低压富液吸收剂16流到低压富液吸收剂17进入解吸塔6塔顶;(d)低压富液吸收剂17送入解吸塔6塔顶,外供直接蒸汽19进入解吸塔6塔底;在解吸塔6内,外供直接蒸汽19降低低压富液吸收剂17的分压,并提高低压富液吸收剂17的温度,富液吸收剂17与外供直接蒸汽19逆流接触,进行气提再生,富液吸收剂17中的二氧化碳被外供直接蒸汽19解吸,二氧化碳18从解吸塔6塔顶流出送到界外;(e)脱除二氧化碳的低压贫液吸收剂20从解吸塔6塔底流出。在正常工况条件下,旁路管线24的备用增压泵4和备用增压泵4进口阀门、出口阀门都关闭,该低压贫液吸收剂20进入到前置增压泵5增压后,成为低压贫液吸收剂21再进入压力回收装置3升压端入口;(f)低压贫液吸收剂21进入压力回收装置3升压端入口,在压力回收装置3内,低压贫液吸收剂21的压力从低压转换成高压贫液吸收剂22;(g)从压力回收装置3流出的高压贫液吸收剂22流到贫富吸收剂热交换器2换热降低温度,降温之后的低温贫液吸收剂23返回进入吸收塔1塔顶再次循环反复使用,重新吸收产品气11中的二氧化碳;压力回收装置3为采用液力透平原理的在线回收压力设备,该设备在同一个泵体内通过转轴将减压端高压侧叶轮与升压端低压侧叶轮直接相连,减压端的高压富液吸收剂驱动减压端高压侧叶轮,并通过转轴驱动升压端低压侧叶轮转动,增加升压端低压贫液吸收剂的压力。由此将减压端高压侧的“压力能”转化为转轴的“机械能”再转化为升压端低压侧的“压力能”,而且压力回收装置3中的转轴是唯一运转部件,因此压力回收装置3无轴密封、无额外润滑系统。上述技术方案中,优选地,在压力回收装置3内,减压端高压侧的高温富液吸收剂15“压力能”转化为转轴的“机械能”,再转化为升压端低压侧的低压贫液吸收剂21“压力能”,低压贫液吸收剂21的压力增高,转变成高压贫液吸收剂22,该压力满足吸收塔1吸收操作运行要求的压力,从而减少了前置增压泵5的输出压力,降低了电机的动力消耗。上述技术方案中,优选地,当设置的压力回收装置3出现故障工况时,同时开启压力回收装置3正常工况时处于旁路关闭状态的阀门并打开备用增压泵4,高温富液吸收剂14从贫富吸收剂热交换器2通过管线25到解吸塔6塔顶,低压贫液吸收剂20通过管线24和备用增压泵4增压后到吸收塔1塔顶;启动不使用压力回收装置3的运行工况,从而保证吸收剂在吸收塔1与解吸塔6之间正常循环运行。上述技术方案中,优选地,甲醇制烯烃装置产品气中的乙烯/丙烯质量比范围是e/p=0.8~1.2:1。上述技术方案中,优选地,吸收塔1操作压力范围1.5~2.5mpa,塔顶操作温度范围55~72℃,塔底操作温度范围58~75℃;吸收塔1采用摩尔分数为15~20%一乙醇胺mea或摩尔分数为25%~35%二乙醇胺dea为吸收剂。上述技术方案中,优选地,解吸塔6操作压力范围0.1~1.1mpa,塔顶操作温度范围100~115℃,塔底操作温度范围104~119℃;解吸塔6采用外供直接蒸汽操作压力范围0.2~1.2mpa,操作温度范围140~208℃。上述技术方案中,优选地,压力回收装置3减压端入口操作压力范围1.5~2.5mpa,出口操作压力范围0.4~1.4mpa;升压端入口操作压力范围0.9~1.9mpa,出口操作压力范围1.9~2.9mpa。上述技术方案中,优选地,开启前置增压泵5,入口操作压力范围0.1~1.1mpa,出口操作压力范围0.9~1.9mpa。本发明涉及一种甲醇制烯烃装置回收压力能量的方法,对于生产规模180万吨/年~360万吨/年甲醇制烯烃装置来说,处理乙烯/丙烯质量比为e/p=0.8~1.2:1.0的产品气时,在吸收塔1与解吸塔6之间增设压力回收装置3,将高温富液吸收剂15的压力从高压转换成低压富液吸收剂16,同时将来自解吸塔6塔底低压贫液吸收剂21的压力从低压转变成高压贫液吸收剂22,由此相对节约外供能量60.09~64.97%以上,节省电力费用22~44万元/年以上,取得较好的技术效果。附图说明图1为本发明所述方法的流程示意图。图1中,1-吸收塔;2-贫富吸收剂热交换器;3-压力回收装置;4-备用增压泵;5-前置增压泵;6-解吸塔;11-产品气;12-净化产品气;13-高压富液吸收剂;14-高温富液吸收剂;15-高温富液吸收剂;16-低压富液吸收剂;17-低压富液吸收剂;18-二氧化碳;19-外供直接蒸汽;20-低压贫液吸收剂;21-低压贫液吸收剂;22-高压贫液吸收剂;23-低温贫液吸收剂;24-低压贫液吸收剂旁路管线;25-高温富液吸收剂旁路管线。下面通过实施例对本发明作进一步的阐述,但不仅限于本实施例。具体实施方式【对比例1】分别以生产规模180万吨/年、240万吨/年、360万吨/年甲醇制烯烃装置为例,甲醇制烯烃装置采用现有技术,在脱除二氧化碳过程中,没有采用压力回收技术,也没有考虑通过压力回收装置回收压力能量,吸收剂输送泵的电力消耗和经济效益,见表1。表1输送泵电力消耗和经济效益汇总表【实施例1】以生产规模180万吨/年甲醇制烯烃装置为例,采用本发明一种甲醇制烯烃装置压力能量的回收方法,甲醇制烯烃反应生成的产品气组成,见表2。表2甲醇制烯烃装置产品气组成一览表组分名称氢气甲烷乙烯乙烷丙烯丙烷碳四水二氧化碳合计产率/摩尔%2.813.6446.510.8730.161.958.195.810.06100.00如图1所示,工艺流程如下:来自界外甲醇制烯烃装置的产品气11进入吸收塔1塔底,同时经过温度降低、压力增加后的低温贫液吸收剂23进入吸收塔1塔顶,在吸收塔1内,产品气11与低温贫液吸收剂23逆流接触,产品气11中的二氧化碳被低温贫液吸收剂23吸收,脱除二氧化碳的净化产品气12从吸收塔1塔顶流出送到界外。吸收二氧化碳的高压富液吸收剂13从吸收塔1塔底流出,经过贫富吸收剂热交换器2换热升温为高温富液吸收剂14,该高温富液吸收剂14流到高温富液吸收剂15进入到压力回收装置3减压端入口,高温富液吸收剂15的压力从高压转换成低压富液吸收剂16。从压力回收装置3流出的低压富液吸收剂16流到低压富液吸收剂17进入解吸塔6塔顶,外供直接蒸汽19进入解吸塔6塔底。在解吸塔6内,外供直接蒸汽19降低了低压富液吸收剂17的分压,并提高了低压富液吸收剂17的温度,富液吸收剂17与外供直接蒸汽19逆流接触进行气提再生,富液吸收剂17中的二氧化碳被外供直接蒸汽19释放解吸,二氧化碳18从解吸塔6塔顶流出送到界外。脱除二氧化碳的低压贫液吸收剂20从解吸塔6塔底流出,进入到前置增压泵5增压后,成为低压贫液吸收剂21进入压力回收装置3升压端入口。在压力回收装置3内,低压贫液吸收剂21的压力从低压转换成高压,从压力回收装置3流出的高压贫液吸收剂22流到贫富吸收剂热交换器2换热降低温度,降温之后的低温贫液吸收剂23返回进入吸收塔1塔顶再次循环反复使用,重新吸收产品气11中的二氧化碳。当压力回收装置3出现故障时,可同时开启旁路阀门并打开备用增压泵4,高温富液吸收剂14从贫富吸收剂热交换器2通过管线25到解吸塔6塔顶,低压贫液吸收剂20通过管线24和备用增压泵4增压后到吸收塔1塔顶。工艺参数如下:甲醇制烯烃装置产品气中的乙烯/丙烯质量比范围是e/p=1.0:1.0。吸收塔1操作压力1.9mpa,塔顶操作温度63℃,塔底操作温度67℃。吸收塔1采用摩尔分数为17%一乙醇胺mea为吸收剂。解吸塔6操作压力0.5mpa,塔顶操作温度107℃,塔底操作温度111℃。解吸塔6采用外供直接蒸汽操作压力0.6mpa,操作温度179℃。压力回收装置3减压端入口操作压力1.9mpa,出口操作压力0.8mpa;升压端入口操作压力1.3mpa,出口操作压力2.3mpa。开启前置增压泵5,入口操作压力0.5mpa,出口操作压力1.3mpa。采用本发明一种甲醇制烯烃装置压力能量的回收方法,脱除二氧化碳净化后的产品气再进一步分离精制,得到二氧化碳摩尔分数≤2.0ppm和纯度≥99.95mol%的聚合级乙烯产品,二氧化碳摩尔分数≤5.0ppm和纯度≥99.6mol%的聚合级丙烯产品。节省电力费用22万元/年,相对节约外供能量60.52%,其它取得的技术效果和经济效益,见表6。【实施例2】同【实施例1】,生产规模仍然为180万吨/年甲醇制烯烃装置,仅仅工艺参数改变如下:甲醇制烯烃装置产品气中的乙烯/丙烯质量比范围是e/p=1.0:1.0。吸收塔1操作压力1.5mpa,塔顶操作温度55℃,塔底操作温度58℃。吸收塔1采用摩尔分数为15%一乙醇胺mea为吸收剂。解吸塔6操作压力0.1mpa,塔顶操作温度100℃,塔底操作温度104℃。解吸塔6采用外供直接蒸汽操作压力0.2mpa,操作温度140℃。压力回收装置3减压端入口操作压力1.5mpa,出口操作压力0.4mpa;升压端入口操作压力0.9mpa,出口操作压力1.9mpa。开启前置增压泵5,入口操作压力0.1mpa,出口操作压力0.9mpa。采用本发明一种甲醇制烯烃装置压力能量的回收方法,脱除二氧化碳净化后的产品气再进一步分离精制,得到二氧化碳摩尔分数≤2.0ppm和纯度≥99.95mol%的聚合级乙烯产品,二氧化碳摩尔分数≤5.0ppm和纯度≥99.6mol%的聚合级丙烯产品。节省电力费用22万元/年,相对节约外供能量60.09%,其它取得的技术效果和经济效益,见表6。【实施例3】同【实施例1】,生产规模仍然为180万吨/年甲醇制烯烃装置,仅仅工艺参数改变如下:甲醇制烯烃装置产品气中的乙烯/丙烯质量比范围是e/p=1.0:1.0。吸收塔1操作压力2.5mpa,塔顶操作温度72℃,塔底操作温度75℃。吸收塔1采用摩尔分数为35%二乙醇胺dea为吸收剂。解吸塔6操作压力1.1mpa,塔顶操作温度115℃,塔底操作温度119℃。解吸塔6采用外供直接蒸汽操作压力1.2mpa,操作温度208℃。压力回收装置3减压端入口操作压力2.5mpa,出口操作压力1.4mpa;升压端入口操作压力1.9mpa,出口操作压力2.9mpa。开启前置增压泵5,入口操作压力1.1mpa,出口操作压力1.9mpa。采用本发明一种甲醇制烯烃装置压力能量的回收方法,脱除二氧化碳净化后的产品气再进一步分离精制,得到二氧化碳摩尔分数≤2.0ppm和纯度≥99.95mol%的聚合级乙烯产品,二氧化碳摩尔分数≤5.0ppm和纯度≥99.6mol%的聚合级丙烯产品。节省电力费用22万元/年,相对节约外供能量61.38%,其它取得的技术效果和经济效益,见表6。【实施例4】同【实施例1】,生产规模仍然为180万吨/年甲醇制烯烃装置,工艺参数不变,只是甲醇制烯烃装置反应生成的产品气中乙烯/丙烯比为e/p=0.8:1.0,见表3。表3甲醇制烯烃装置产品气组成一览表组分名称水氢气甲烷乙烷乙烯丙烷丙烯碳四二氧化碳合计产率/质量%2.980.110.581.3332.914.6641.8815.400.15100.00采用本发明一种甲醇制烯烃装置压力能量的回收方法,脱除二氧化碳净化后的产品气再进一步分离精制,得到二氧化碳摩尔分数≤2.0ppm和纯度≥99.95mol%的聚合级乙烯产品,二氧化碳摩尔分数≤5.0ppm和纯度≥99.6mol%的聚合级丙烯产品。节省电力费用22万元/年,相对节约外供能量60.53%,其它取得的技术效果和经济效益,见表6。【实施例5】同【实施例1】,生产规模仍然为180万吨/年甲醇制烯烃装置,工艺参数不变,只是甲醇制烯烃装置反应生成的产品气中乙烯/丙烯比为e/p=1.0:1.0,见表4。表4甲醇制烯烃装置产品气组成一览表组分名称水氢气甲烷乙烷乙烯丙烷丙烯碳四二氧化碳合计产率/质量%3.140.171.570.7839.122.5738.0614.510.08100.00采用本发明一种甲醇制烯烃装置压力能量的回收方法,脱除二氧化碳净化后的产品气再进一步分离精制,得到二氧化碳摩尔分数≤2.0ppm和纯度≥99.95mol%的聚合级乙烯产品,二氧化碳摩尔分数≤5.0ppm和纯度≥99.6mol%的聚合级丙烯产品。节省电力费用22万元/年,相对节约外供能量60.58%,其它取得的技术效果和经济效益,见表6。【实施例6】同【实施例1】,生产规模仍然为180万吨/年甲醇制烯烃装置,工艺参数不变,只是甲醇制烯烃装置反应生成的产品气中乙烯/丙烯比为e/p=1.2:1.0,见表5。表5甲醇制烯烃装置产品气组成一览表组分名称水氢气甲烷乙烷乙烯丙烷丙烯碳四二氧化碳合计产率/质量%3.250.371.811.4741.823.1534.1813.820.13100.00采用本发明一种甲醇制烯烃装置压力能量的回收方法,脱除二氧化碳净化后的产品气再进一步分离精制,得到二氧化碳摩尔分数≤2.0ppm和纯度≥99.95mol%的聚合级乙烯产品,二氧化碳摩尔分数≤5.0ppm和纯度≥99.6mol%的聚合级丙烯产品。节省电力费用22万元/年,相对节约外供能量60.65%,其它取得的技术效果和经济效益,见表6。【实施例7】同【实施例1】,回收压力能量的工艺参数不变,甲醇制烯烃反应生成的产品气组成也不变,仅仅甲醇制烯烃装置生产规模扩大为240万吨/年,采用本发明一种甲醇制烯烃装置压力能量的回收方法,脱除二氧化碳净化后的产品气再进一步分离精制,得到二氧化碳摩尔分数≤2.0ppm和纯度≥99.95mol%的聚合级乙烯产品,二氧化碳摩尔分数≤5.0ppm和纯度≥99.6mol%的聚合级丙烯产品。节省电力费用30万元/年,相对节约外供能量63.62%,其它取得的技术效果和经济效益,见表6。【实施例8】同【实施例1】,回收压力能量的工艺参数不变,甲醇制烯烃反应生成的产品气组成也不变,仅仅甲醇制烯烃装置生产规模扩大为360万吨/年,采用本发明一种甲醇制烯烃装置压力能量的回收方法,脱除二氧化碳净化后的产品气再进一步分离精制,得到二氧化碳摩尔分数≤2.0ppm和纯度≥99.95mol%的聚合级乙烯产品,二氧化碳摩尔分数≤5.0ppm和纯度≥99.6mol%的聚合级丙烯产品。节省电力费用44万元/年,相对节约外供能量64.97%,其它取得的技术效果和经济效益,见表6。综上所述,【实施例1】~【实施例8】采用本发明一种甲醇制烯烃装置压力能量的回收方法,所取得的技术效果和经济效益,见表6。表6本发明技术效果和经济效益汇总表本发明实施例1实施例2实施例3实施例4实施例5实施例6实施例7实施例8生产规模(万吨/年)180180180180180180240360压力装置回收功率(千瓦)36.4636.2036.9836.4736.5036.5452.9783.89输送泵消耗功率(千瓦)23.7924.0523.2723.7823.7523.7130.2945.23输送泵电机功率(千瓦)3030303030304060计算电机效率(%)79.2980.1677.5679.2679.1679.0375.7375.38年电力消耗(千瓦时)240000240000240000240000240000240000320000480000年电力费用(万元)1515151515152030年减少外供电力(千瓦时)360000360000360000360000360000360000480000720000年节省电力费用(万元)2222222222223044相对减少外供能量(%)60.0060.0060.0060.0060.0060.0060.0060.00相对节约外供能量(%)60.5260.0961.3860.5360.5860.6563.6264.97当前第1页12