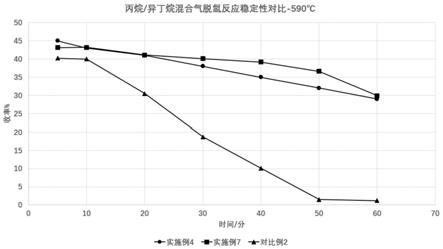
[0001]
本发明属于催化裂化技术领域,具体涉及一种含有尖晶石结构的低碳烷烃铬系脱氢催化剂及其制备方法。
背景技术:[0002]
近年来,随着国际石化行业的飞速发展,对低碳烯烃的需求也日益增长。获取低碳烯烃的主要途径包括以下几个方面:目前生产的主要工艺为催化裂化技术和蒸汽裂解技术,但这两种技术均存在着能耗大和烯烃收率低等缺点;而经过煤制烯烃技术和甲醇制烯烃技术所获得的低碳烯烃,由于成本高等问题,不具备市场竞争力。与其他制取低碳烯烃的技术相比,直接脱氢反应制取烯烃技术的设备投资费用比蒸气裂解低33%,并且该技术的原料低碳烷烃成本占丙烯全部生产成本的70%以上,可以直接用于连续生产低碳烯烃的下游衍生物,因此,迄今为止,直接脱氢反应制取烯烃是获取低碳烷烃的最有效手段。
[0003]
迄今为止,直接脱氢工艺主要集中于lummus的catofin固定床工艺和uop的oleflex移动床工艺。其中lummus的catofin固定床工艺采用cr/al2o3的条形催化剂,低碳烷烃原料先进入反应工段在催化剂作用下生成丙烯,其反应器由4至8个绝热的固定床管式反应器组成,反应后该工段出来的高温物料由低碳烷烃原料降温后迚入压缩工段由多级压缩机迚行压缩,经回收工段处理后,低碳烷烃、低碳烯烃和其他重组分被送入精馏塔迚行分离,塔顶的低碳烯烃进行回收,塔底的低碳烷烃组分进行循环利用,对于该工艺而言,其现阶段面临的最大问题是催化剂的选择性较低,积碳较快,稳定性较低等问题。而uop的oleflex移动床工艺则是采用pt-sn/al2o3的球形催化剂,该工艺反应系统采用的是四级串联径向绝热床反应器,每一级反应器之间会有一个加热器将上一级反应器出来的未反应的低碳烷烃气体重新加热,该工艺中氢气作为稀释剂。但是,贵金属的高成本以及移动床催化剂的所需要的高强度固定床载体则降低了该工艺的经济性,同时由于氢气的使用,在进行低碳烷烃脱氢反应时,也存在一定的安全隐患。因此,由于催化剂活性、稳定性、使用寿命、成本、破碎强度以及安全性等问题,lummus的catofin固定床工艺,是一种产率高,稳定性高,经济性好的低碳烷烃直接脱氢反应工艺,因此开发出一种高效,高稳定性,高活性以及低成本的固定床低碳烷烃脱氢催化剂是极有必要的。
[0004]
直接脱氢反应是热力学限制的高吸热反应,低碳烷烃c-h键活化是决定脱氢催化性能的关键步骤。但是低碳烷烃的c-h键高度稳定,因此需要较高的反应温度(550-700℃)来实现c-h键断裂。然而,高温下c-c键比c-h键断裂更容易,容易发生裂化、深度脱氢或聚合反应等副反应,导致低选择性和结焦。
[0005]
现有的传统铬系催化剂,多采用碱金属等元素进行改性,以氧化铝做固定床载体制备得到。然而,由于碱金属的碱性较强,稳定性较差等原因,现阶段,铬系催化剂的选择性和稳定性都需要改进。在丙烷直接脱氢的反应中,副产物主要为c1和c2的轻质烃,这些轻质烃的产生源自裂解。
[0006]
中国专利cn110560043,cn103769078,美国专利us20030232720和us7279611提及
了碱金属在脱氢催化剂中的作用,并公开了在催化剂中加入了少量的碱金属元素的方法,试图降低催化剂自身的酸性。但是由于碱金属的碱性较强,不仅降低了酸性,同时也降低了催化剂的稳定性。
[0007]
中国专利cn110560060在脱氢催化剂中加入第ib族元素,中国专利cn110560042在脱氢催化剂中加入第ivb族元素,中国专利cn110563537在脱氢催化剂中加入第vb族元素以改善脱氢催化剂的脱氢性能,但是由于上述元素仅能在单一方面对催化剂的性能进行调整,从而限制了其在其他工艺上的应用。
[0008]
中国专利cn104226321混合低碳烷烃脱氢催化剂及其制备方法公开了镁元素等碱土金属的添加,但是其使用的固定床载体为纳米氧化铝(2~200nm),该纳米氧化铝材料制备工艺复杂,生产成本较高,且由于尺寸限制,很能进行实际应用。因此上述催化剂并不适用于现阶段世界范围内主流的两种脱氢工艺。
[0009]
中国专利cn105363484用于低碳烷烃脱氢制低碳烯烃的催化剂及其应用公开了稀土元素的添加,但是其核心组分为铑,钯,铂等贵金属元素,上述元素制成的脱氢催化剂主要应用于移动床脱氢装置。但是,由于贵金属的高成本以及移动床催化剂的所需要的高强度固定床载体则降低了该工艺的经济性,同时由于氢气的使用,在进行低碳烷烃脱氢反应时,也存在一定的安全隐患。
[0010]
美国专利us8835347将部分碱金属和碱土金属加入脱氢催化剂中,以期待改变其选择性。但是,根据其催化剂的制备方法和性能表现,可以看出,该专利中加入的碱土元素的作用仅为在覆盖催化剂表面的酸性位点,提高了选择性,然而碱土元素未与固定床载体形成尖晶石结构,因此其催化剂的使用寿命并未得到增强。
技术实现要素:[0011]
针对现有的固定床中的低碳烷烃铬系脱氢催化剂存在的稳定性差,选择性低,破碎强度低,使用范围单一的问题,本发明提供一种含有尖晶石结构的低碳烷烃铬系脱氢催化剂。
[0012]
本发明的技术方案为:一种含有尖晶石结构的低碳烷烃铬系脱氢催化剂,该低碳烷烃铬系脱氢催化剂用于固定床中,反应压力为0.01~1mpa、温度为530~660℃、质量空速为0.3~8h-1;
[0013]
该低碳烷烃铬系脱氢催化剂包括按低碳烷烃铬系脱氢催化剂干基总质量为基准计的以下质量分数的组分:氧化铬0.1~30%,第一助剂0.1~10%,第二助剂0.1~10%,第三助剂0.1~10%,余量为固定床载体;
[0014]
所述第三助剂为稀土元素中的一种或几种的混合物。
[0015]
进一步限定,所述第一助剂为碱土金属元素中的一种或几种的混合物。
[0016]
进一步限定,所述第二助剂为第ivb族元素中的一种或几种的混合物。
[0017]
进一步限定,所述尖晶石结构包括镁铝尖晶石结构,钙铝尖晶石结构或含钛尖晶石结构中的至少一种。
[0018]
进一步限定,所述固定床载体为具有多级孔道的氧化铝,氧化硅或分子筛,所述固定床载体的比表面为50~500m
2
/g,孔径范围为5~40nm。
[0019]
进一步限定,所述氧化铬中的铬来源于铬酸钠,重铬酸钠,铬酸钾,重铬酸钾,重铬
酸铵,铬酸,氯化铬,乙酰丙酮铬酸,硫酸铬钾,三氧化铬,过氧化铬,氯化铬,铬酸铅,氮化铬,硝酸铬以及氟化铬中的一种或多种。
[0020]
进一步限定,所述碱土金属元素来源于碱土金属粉末,碱土金属卤化物,碱土金属氧化物,碱土金属硫化物,碱土金属硫酸盐,碱土金属硝酸盐,碱土金属乙酸盐以及碱土金属草酸盐中的一种或多种。
[0021]
进一步限定,所述第ivb族元素来源于第ivb族元素金属粉末,第ivb族元素卤化物,第ivb族元素氧化物,第ivb族元素硫化物,第ivb族元素硫酸盐,第ivb族元素硝酸盐,第ivb族元素乙酸盐以及第ivb族元素草酸盐中的一种或多种。
[0022]
进一步限定,所述稀土金属元素来源于稀土金属粉末,稀土金属卤化物,稀土金属氧化物,稀土金属硫化物,稀土金属硫酸盐,稀土金属硝酸盐,稀土金属乙酸盐以及稀土金属草酸盐中的一种或多种。
[0023]
与现有技术相比,本发明的有益效果为:本发明公开的含有尖晶石结构的低碳烷烃铬系脱氢催化剂适用于固定床工艺,a)碱土元素为与固定床载体形成更加稳定的尖晶石结构,增强了催化剂的稳定性,使导致催化剂永久失活的“铬铝相”不容易形成。
[0024]
b)第ivb族元素和稀土元素的使用增强了固定床载体的骨架结构,同时为脱氢反应提供了更多的路易斯酸位点。
[0025]
c)稀土元素的加入既稳定了铬系的晶体结构,又提高了催化剂的稳定性和破碎强度,从而解决了催化剂使用过程中,破碎,掉粉而导致的压降增大等问题。
[0026]
d)碱土元素和稀土元素为铬元素提供了更加稳定的电子结构,平衡了催化剂的酸性,降低了酸裂解,提高了催化剂的丙烷脱氢反应的选择性。
[0027]
e)对固定床载体的种类,尺寸,粒径均无明显要求,更易于工业化生产,具有良好的应用前景。
[0028]
f)本发明仅仅使用了氧化铬,第一助剂,第二助剂,第三助剂以及余固定床载体即可明显提高催化剂的稳定性,破碎强度达到150n/cm以上。
[0029]
g)具有良好的酸性,使得催化剂具有更高的目标产物选择性,且最大程度上的避免酸性裂解。由于催化剂具有稳定的尖晶石结构,因此显著的增强了催化剂的强度和稳定性,使得催化剂具有更长的使用寿命。由于其优异的选择性和稳定性,显著地增强了其在低碳烷烃反应过程中的抗积碳能力。
[0030]
本发明还提供一种含有尖晶石结构的低碳烷烃铬系脱氢催化剂的制备方法,包括以下步骤:
[0031]
1)将铝石粉或硅胶粉或分子筛,浓硝酸,田菁粉和软化水以100:5-10:5-10:10-80的质量比混合,在4.5mm孔板挤条,长度为1-10cm,并在80-150℃下进行干燥8-12小时,得到条形固定床载体;
[0032]
2)将条形固定床载体在400-1000℃下进行焙烧1-10小时,得到具有比表面为50~500m
2
/g,孔径范围为5~40nm的固定床载体;
[0033]
3)配置所需含铬的可溶性溶液,碱土金属盐的可溶性溶液,第ivb族元素的可溶性溶液以及稀土元素的可溶性溶液,并混合成混合液;
[0034]
4)将步骤2)所制备得到的固定床载体与混合液在真空条件下进行浸渍,搅拌,再陈化0.5-8小时,得到半成品;
[0035]
5)将半成品干燥0.5-8小时,然后在650-1000℃下焙烧0.5-12小时即可。
附图说明
[0036]
图1是实施4、实施例7以及对比例2所得的各催化剂对丙烷/异丁烷混合物脱氢反应的稳定性能图。
具体实施方式
[0037]
为使本发明实施例的目的、技术方案和优点更加清楚,下面对本发明的实施例进行详细、完整的描述,显然,所描述的实施例是本发明一部分实施例,而不是全部的实施例。基于本发明中的实施例,本领域普通技术人员在没有作出创造性劳动前提下所获得的所有其他实施例,都属于本发明保护的范围。
[0038]
本技术领域技术人员可以理解,除非另外定义,这里使用的所有术语(包括技术术语和科学术语),具有与本发明所属领域中的普通技术人员的一般理解相同的意义。还应该理解的是,诸如通用字典中定义的那些术语,应该被理解为具有与现有技术的上下文中的意义一致的意义,并且除非被特定定义,否则不会用理想化或过于正式的含义来解释。
[0039]
为了解决固定床中的低碳烷烃铬系脱氢催化剂存在的稳定性差,选择性低,破碎强度低,使用范围单一的问题,提供一种含有尖晶石结构的低碳烷烃铬系脱氢催化剂,该低碳烷烃铬系脱氢催化剂用于固定床中,反应压力为0.01~1mpa、温度为530~660℃、质量空速为0.3~8h-1
;
[0040]
该低碳烷烃铬系脱氢催化剂包括按低碳烷烃铬系脱氢催化剂干基总质量为基准计的以下质量分数的组分:氧化铬0.1~30%,优选为1%~25%;第一助剂0.1~10%,优选为1~5%;第二助剂0.1~10%,优选为1~5%;第三助剂0.1~10%,优选为1~5%;余量为固定床载体;
[0041]
第三助剂为稀土元素中的一种或几种的混合物。
[0042]
第一助剂为碱土金属元素中的一种或几种的混合物。
[0043]
第二助剂为第ivb族元素中的一种或几种的混合物。
[0044]
尖晶石结构包括镁铝尖晶石结构,钙铝尖晶石结构或含钛尖晶石结构中的至少一种。
[0045]
固定床载体为具有多级孔道的氧化铝,氧化硅或分子筛,所述固定床载体的比表面为50~500m
2
/g,优选为50~150m
2
/g;孔径范围为5~40nm,优选为10~30nm。
[0046]
氧化铬中的铬来源于铬酸钠,重铬酸钠,铬酸钾,重铬酸钾,重铬酸铵,铬酸,氯化铬,乙酰丙酮铬酸,硫酸铬钾,三氧化铬,过氧化铬,氯化铬,铬酸铅,氮化铬,硝酸铬以及氟化铬中的一种或多种。
[0047]
碱土金属元素来源于碱土金属粉末,碱土金属卤化物,碱土金属氧化物,碱土金属硫化物,碱土金属硫酸盐,碱土金属硝酸盐,碱土金属乙酸盐以及碱土金属草酸盐中的一种或多种。
[0048]
第ivb族元素来源于第ivb族元素金属粉末,第ivb族元素卤化物,第ivb族元素氧化物,第ivb族元素硫化物,第ivb族元素硫酸盐,第ivb族元素硝酸盐,第ivb族元素乙酸盐以及第ivb族元素草酸盐中的一种或多种。
[0049]
稀土金属元素来源于稀土金属粉末,稀土金属卤化物,稀土金属氧化物,稀土金属硫化物,稀土金属硫酸盐,稀土金属硝酸盐,稀土金属乙酸盐以及稀土金属草酸盐中的一种或多种。
[0050]
一种含有尖晶石结构的低碳烷烃铬系脱氢催化剂的固定床载体的制备方法,包括以下步骤:
[0051]
a)将铝石粉、硅胶粉或分子筛与浓硝酸,田菁粉和软化水以100:5-10:5-10:10-80的质量比混合,在4.5mm孔板挤条,并干燥,得到条形固定床载体;
[0052]
b)将条形固定床载体在400-1000℃下进行焙烧1-10小时,得到具有比表面为50~500m2/g,孔径范围为5~40nm的固定床载体;
[0053]
c)配置所需含铬的可溶性溶液,碱土金属盐的可溶性溶液,第ivb族元素的可溶性溶液以及稀土元素的可溶性溶液,并混合成混合液;
[0054]
d)固定床载体与混合液在真空条件下进行浸渍,搅拌,再陈化0.5-8小时,干燥0.5-8小时,650-1000℃下焙烧0.5-12小时,得到所需的一种含有尖晶石结构的低碳烷烃脱氢催化剂。
[0055]
上述技术方案中,配置所需含铬的可溶性溶液,其铬源可以使用铬的氧化物、铬的硝酸盐、铬的醋酸盐和铬的草酸盐中的一种;配置所需含钙或镁的可溶性溶液,镁源可以使用含镁的氯化物、含镁的硝酸盐和含镁的硫酸盐中的一种,钙源配制时可以使用含钙的氯化物、含钙的硝酸盐和含钙的硫酸盐中的一种。
[0056]
上述技术方案中,将固定床载体与混合液的浸渍过程中,其真空度优选为0.1kpa-50kpa,更优选为0.1kpa-5kpa;陈化时间优选为1-5小时,更优选为2-4小时;干燥时间优选为1-5小时,更优选为2-4小时;焙烧温度优选为700-1000℃,更优选为600-900℃;焙烧时间优选为2-8小时,更优选为4-6小时。
[0057]
实施例1-氧化铝固定床载体制备
[0058]
在捏合机内加入100g铝石粉,其中加入3g田菁粉混合均匀;称取2.8g浓硝酸加到45g水中,配置成硝酸溶液,并将此溶液加入到拟薄水铝石和田菁粉混合物中,捏合1小时,并在4.5mm孔板上挤条;将挤好的条状固定床载体在120℃下干燥2小时,切粒,以3℃每分的速度升温至900℃,在该温度下焙烧4-8小时,得到固定床载体i;测得其吸水量为40%。
[0059]
实施例2-氧化硅固定床载体制备
[0060]
在捏合机内加入88g硅胶粉,其中加入3g田菁粉混合均匀;称取2.8g浓硝酸加到45g水中,配置成硝酸溶液,并将此溶液加入到拟薄水铝石和田菁粉混合物中,捏合1小时,并在4.5mm孔板上挤条;将挤好的条状固定床载体在120℃下干燥2小时,切粒,以3℃每分的速度升温至900℃,在该温度下焙烧4-8小时,得到固定床载体ii;测得其吸水量为40%。
[0061]
实施例3-分子筛固定床载体制备
[0062]
在捏合机内加入50g,zsm-5分子筛,其中加入3g田菁粉混合均匀;称取2.8g浓硝酸加到45g水中,配置成硝酸溶液,并将此溶液加入到拟薄水铝石和田菁粉混合物中,捏合1小时,并在4.5mm孔板上挤条;将挤好的条状固定床载体在120℃下干燥2小时,切粒,以3℃每分的速度升温至900℃,在该温度下焙烧4-8小时,得到固定床载体iii;测得其吸水量为40%。
[0063]
实施例4
[0064]
称取37g铬酸酐,5g六水硝酸镁,1g八水氯化氧锆,2g六水硝酸钇溶于40g水中,得到浸渍液;将100g固定床载体i加入抽滤瓶中,抽真空2小时,真空度为-100kpa;将40g浸渍液缓慢加入抽滤瓶中,将湿润的催化剂每10分钟进行一次搅拌,直至催化剂表面风干。放入120℃烘箱中烘干8小时,得到干燥的催化剂;将干燥的催化剂在马弗炉中进行焙烧,焙烧温度为650℃,焙烧时间为4小时,升温速率为5℃每分,待催化剂自然降温至200℃以下时,得到固定床催化剂1。
[0065]
实施例5
[0066]
称取23g铬酸酐,6g四水乙酸镁,1g一水草酸氧钛胺,2g六水硝酸镧,溶于40g水中,得到浸渍液;将100g固定床载体ii加入抽滤瓶中,抽真空2小时,真空度为-100kpa;将40g浸渍液缓慢加入抽滤瓶中,将湿润的催化剂每10分钟进行一次搅拌,直至催化剂表面风干。放入120℃烘箱中烘干8小时,得到干燥的催化剂;将干燥的催化剂在马弗炉中进行焙烧,焙烧温度为800℃,焙烧时间为8小时,升温速率为5℃每分,待催化剂自然降温至200℃以下时,得到固定床催化剂2。
[0067]
实施例6
[0068]
称取47g铬酸酐,7g四水硝酸钙,1g八水氯化氧锆,2g六水硝酸铈,溶于40g水中,得到浸渍液;将100g固定床载体iii加入抽滤瓶中,抽真空2小时,真空度为-100kpa;将40g浸渍液缓慢加入抽滤瓶中,将湿润的催化剂每10分钟进行一次搅拌,直至催化剂表面风干。放入120℃烘箱中烘干8小时,得到干燥的催化剂;将干燥的催化剂在马弗炉中进行焙烧,焙烧温度为750℃,焙烧时间为6小时,升温速率为5℃每分,待催化剂自然降温至200℃以下时,得到固定床催化剂3;
[0069]
实施例7
[0070]
称取34g铬酸酐,8g二水氯化钡,1g一水草酸氧钛胺,1g六水硝酸铈,溶于40g水中,得到浸渍液;将100g固定床载体i加入抽滤瓶中,抽真空2小时,真空度为-100kpa;将40g浸渍液缓慢加入抽滤瓶中,将湿润的催化剂每10分钟进行一次搅拌,直至催化剂表面风干。放入120℃烘箱中烘干8小时,得到干燥的催化剂;将干燥的催化剂在马弗炉中进行焙烧,焙烧温度为550℃,焙烧时间为8小时,升温速率为5℃每分,待催化剂自然降温至200℃以下时,得到固定床催化剂4;
[0071]
对比例1
[0072]
称取25g铬酸酐,8g六水硝酸镁,2g八水氯化氧锆,溶于40g水中,得到浸渍液;将100g固定床载体i加入抽滤瓶中,抽真空2小时,真空度为-100kpa;将40g浸渍液缓慢加入抽滤瓶中,将湿润的催化剂每10分钟进行一次搅拌,直至催化剂表面风干。放入120℃烘箱中烘干8小时,得到干燥的催化剂;将干燥的催化剂在马弗炉中进行焙烧,焙烧温度为650℃,焙烧时间为4小时,升温速率为5℃每分,待催化剂自然降温至200℃以下时,得到固定床对比剂1。
[0073]
对比例2
[0074]
称取31g铬酸酐,8.7g氯化钾溶于40g水中,得到浸渍液;将100g固定床载体i加入抽滤瓶中,抽真空2小时,真空度为-100kpa;将40g浸渍液缓慢加入抽滤瓶中,将湿润的催化剂每10分钟进行一次搅拌,直至催化剂表面风干。放入120℃烘箱中烘干8小时,得到干燥的催化剂;将干燥的催化剂在马弗炉中进行焙烧,焙烧温度为750℃,焙烧时间为6小时,升温
速率为5℃每分,待催化剂自然降温至200℃以下时,得到固定床对比剂2。
[0075]
一、丙烷脱氢试验
[0076]
实施例4,5,6,7中得到的固定床催化剂1-4与对比例1,2中的固定床对比剂1-2分别进行丙烷脱氢试验;
[0077]
采用的工艺流程为现有的工艺流程,实施例中不作详细阐述,工艺流程中的控制参数如下:丙烷空速为1h-1
,通入适量氮气,保持丙烷分压为50kpa,反应体系总压力为常压;床层温度为550-600℃;结果如表1所示,
[0078]
表1
[0079][0080]
由表1可知,含有尖晶石结构的低碳烷烃铬系脱氢催化剂在600℃丙烷脱氢反应中丙烯选择性均有提高。
[0081]
二、实施例4中固定床催化剂1在不同温度下的丙烷脱氢性能试验
[0082]
采用的工艺流程为现有的工艺流程,实施例中不作详细阐述,工艺流程中的控制参数如下:丙烷空速为1h-1
,通入适量氮气,保持丙烷分压为50kpa,反应体系总压力为常压;床层温度为550-600℃;结果如表2所示,
[0083]
表2
[0084][0085]
三、实施例4中固定床催化剂1在不同温度下的异丁烷脱氢性能试验
[0086]
采用的工艺流程为现有的工艺流程,实施例中不作详细阐述,工艺流程中的控制参数如下:保持异丁烷空速为1h-1
,通入适量氮气,保持丙烷分压为50kpa,反应体系总压力为常压;床层温度为550-600℃,结果如表3,
[0087]
表3
[0088][0089][0090]
四、实施例4中固定床催化剂1在不同温度下的丙烷/异丁烷混合气脱氢性能试验
[0091]
采用的工艺流程为现有的工艺流程,实施例中不作详细阐述,工艺流程中的控制参数如下:保持丙烷/异丁烷混合气总空速为1h-1
,通入适量氮气,保持丙烷分压为50kpa,反应体系总压力为常压;床层温度为550-600℃,结果如表4,
[0092]
表4
[0093][0094]
由表2-4可知,用于固定床的含有尖晶石结构的低碳烷烃铬系脱氢催化剂具有较高的稳定性以及对丙烷、异丁烷和丙烷/异丁烷混合物均有较好的脱氢性能。
[0095]
五、实施例4制备得到固定床催化剂1,实施例7制备得到固定床催化剂4,以及对比例2制备得到的固定床对比剂2的稳定性
[0096]
如图1所示,由图1可得出,相比于现有的传统铬系脱氢催化剂具有更好的稳定性,因此可以在条件允许的情况下调整调整再生时间,以降低运行成本。
[0097]
综上所述,用于固定床的含有尖晶石结构的低碳烷烃铬系脱氢催化剂在丙烷脱氢反应,异丁烷脱氢反应以及丙烷/异丁烷混合气反应中均有较好的脱氢性能,且相比于现有的传统铬系脱氢催化剂,用于固定床的含有尖晶石结构的低碳烷烃铬系脱氢催化剂具有更高的活性,选择性和更好的稳定性。此外用于固定床的含有尖晶石结构的低碳烷烃铬系脱氢催化剂生产原料简单易得,制备工艺简单,并可以使用现有的生产线高效,稳定,经济进行生产,可以有效的代替现有的传统铬系脱氢催化剂。
[0098]
以上所述的具体实施方式,对本发明的目的、技术方案和有益效果进行了进一步详细说明,所应理解的是,以上所述仅为本发明的具体实施方式而已,并不用于限定本发明的保护范围,凡在本发明的精神和原则之内,所做的任何修改、等同替换、改进等,均应包含在本发明的保护范围之内。