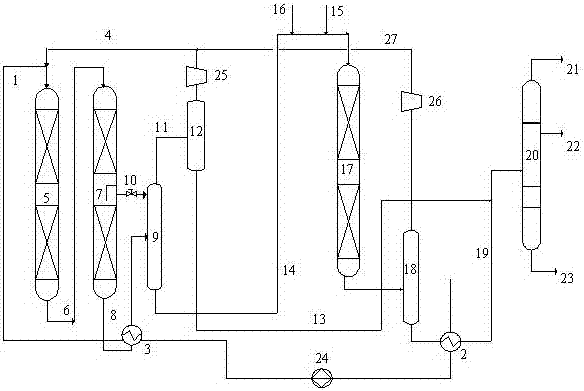
本发明涉及一种烃类加氢处理方法,具体的说是一种催化柴油加氢转化与催化汽油选择性加氢组合方法。
背景技术:进入新世纪以来,随着人们环保意识的日益增强、国家环保法规的日趋严格以及国民经济的快速发展,世界各国对清洁马达燃料的需求都在不断增加。催化裂化(FCC)技术是重油轻质化的主要工艺手段之一,在世界各国的炼油企业中都占有比较重要的地位。我国催化裂化装置年加工能力目前已经超过1亿吨,仅次于美国。在汽柴油品构成中,催化裂化汽油占80%左右,催化柴油占30%左右。近年来,随着国内所加工原油质量的日益重质化,催化裂化所加工的原料也日趋重质化和劣质化,加之许多企业为了达到改善汽油质量或增产丙烯的目的,对催化裂化装置进行了改造或提高了催化裂化装置的操作苛刻度,导致催化裂化的产品,特别是催化柴油的质量更加恶化。为提高石油资源的利用率,提高汽柴油燃料的整体质量水平,实现产品调合最优化和产品价值最大化的目标,满足国内对清洁燃料不断增长的需求,高芳烃柴油加氢转化生产高附加值石脑油组分和低硫清洁柴油燃料的加氢裂化新工艺技术具有很好的应用前景。国内外科研工作者也进行了大量的研究工作。国外已有采用加氢裂化工艺技术将催化裂化轻循环油转化为超低硫柴油和高辛烷值汽油调合组分的相关报道。如:1995年NPRA年会,DavidA.Pappal等人介绍了由Mobil、AkzoNobel/NipponKetjen和M.W.Kellogg公司开发的一种单段加氢裂化工艺技术;2005年NPRA年会,VasantP.Thakkar等人介绍了UOP公司开发的LCOUnicrackingTM技术。据报道,以上两种技术均可将低价值的催化循环油组分转化为高辛烷值汽油组分和优质柴油调合组分。但目前,现有技术也存在着一些问题,高芳烃柴油转化技术主要目的是将高芳烃柴油转化为高辛烷值汽油组分,同时,降低柴油的硫含量和改善柴油十六烷值,汽油组分和柴油组分的加氢存在着矛盾,当裂化段催化剂加氢能力过强时,裂化生成的汽油组分过度加氢,产品辛烷值较低,而裂化段催化剂加氢能力不足时,柴油产品质量较差,同时,会使得催化剂积碳速率加快,影响长周期运转。在此过程中,就涉及到了选择性加氢的问题,改善汽油组分与柴油组分的加氢选择性成为这类加氢裂化过程需要面对的问题。此外,催化汽油选择性加氢过程是高辛烷值汽油生产过程的另一个主要工艺技术,而该过程存在着反应压降上升迅速装置运转周期短及反应温升高致使催化汽油加氢过程辛烷值损失大的问题。中国专利02110319.4公开了一种降低催化裂化汽油硫含量的方法,该发明方法通过将部分催化重汽油组份掺入催化柴油中,进催化柴油加氢精制装置进行加氢精制处理,获取的加氢粗汽油作为催化重整原料进行催化重整处理,获得高辛烷值重整汽油。但是,由于重整装置对汽油进料杂质含量要求较为严格,催化汽油重汽油与柴油组分在苛刻操作条件下混合加氢,对催化裂化重汽油中原有的烯烃、芳烃等高辛烷值组分深度加氢饱和,再通过重整过程恢复芳烃,造成了催化裂化重汽油这部分高辛烷值组分的浪费。
技术实现要素:针对现有高辛烷值汽油生产过程中存在的问题,本发明提供了一种催化柴油加氢转化与催化汽油选择性加氢组合方法,以改善高辛烷值汽油生产过程。本发明的催化柴油加氢转化与催化汽油选择性加氢组合方法,包括如下内容:(1)所述方法包括催化柴油加氢转化部分和催化汽油选择性加氢脱硫部分;(2)在加氢精制工艺条件下,催化裂化柴油与氢气的混合物先进入加氢精制反应器进行加氢精制反应;(3)步骤(2)得到加氢精制反应流出物不经分离,直接进入裂化反应器,与裂化反应器内级配装填的催化剂床层接触反应;所述催化剂的级配方式为:每个催化剂床层均由高加氢活性的体相法加氢精制催化剂与裂化催化剂混合装填,其中催化剂床层的加氢活性按照反应床层由上至下的顺序逐渐下降;(4)步骤(3)所得反应流出物进入热高分进行气液分离,得到气相与液相,气相进一步分离得到石脑油馏分和富氢气体;液相部分即未转化柴油经减压后,与催化裂化汽油及新氢混合,不经加热直接进入催化汽油选择性加氢反应器,对催化汽油进行选择性加氢脱硫反应;(5)步骤(4)得到反应流出物进入分离器进行气液分离,得到气相经脱硫化氢处理后引入加氢转化的新氢压缩机入口,所得液相经分馏得到汽油和柴油产品。根据本发明的方法,其中步骤(4)中的催化汽油选择性加氢脱硫装置取消循环氢压缩机的设置。氢气管网引入的氢气(即新氢)进入催化汽油选择性加氢反应器反应后,经脱除硫化氢后直接进入催化柴油加氢转化部分的新氢压缩机入口,经升压后为催化柴油加氢转化装置反应补充氢气。根据本发明的方法,步骤(3)中所述催化剂床层的加氢活性的调整通过改变加氢裂化反应器不同床层(部位)中体相法加氢精制催化剂和加氢裂化催化剂的混合比例来实现。一般按照加氢裂化反应器从上到下的方向,体相法加氢精制在混合催化剂床层体系中的比例逐渐下降。在裂化反应器内的不同混合催化剂床层中,体相法加氢精制催化剂与加氢裂化催化剂的比例可以是0~5:1。其中所述的加氢裂化催化剂可以为同一种裂化催化剂,或者为不同的裂化催化剂。在本发明方法中,催化柴油加氢转化部分选用的加氢精制催化剂和加氢裂化催化剂可以使用市售产品,也可以根据本领域常规知识制备。本发明所用的加氢精制催化剂可采用常规加氢裂化预处理催化剂,一般以ⅥB族和/或第Ⅷ族金属为活性组分,以氧化铝或含硅氧化铝为载体。第ⅥB族金属一般为Mo和/或W,第Ⅷ族金属一般为Co和/或Ni。以催化剂的重量为基准,第ⅥB族金属含量以氧化物计为8wt%~28wt%,第Ⅷ族金属含量以氧化物计为2wt%~15wt%。裂化段选用的体相法精制催化剂含有W、Mo、Ni三种活性组分,催化剂在硫化氢W、Ni以复合:NixWyOz,z=x+3y,Mo以氧化物MoO3的形式存在。复合物NixWyOzx和y的原子摩尔比为1:8~8:1,优选1:4~4:1。复合物NixWyOz与MoO3重量比1:10~10:1,优选1:5~5:1。体系催化剂中NixWyOz与MoO3的总重量含量为40%~100%,优选50%~80%。加氢裂化催化剂为含有改性Y型分子筛的加氢裂化催化剂,以重量计催化剂含有WO315~30%,NiO或CoO2~15%,改性Y性分子筛30~90%,优选40~70%。载体为氧化铝或无定形硅铝。在本发明方法中,催化汽油选择性加氢部分选用的加氢脱硫催化剂可以使用市售产品,也可以根据本领域常规知识制备。一般以氧化铝或含硅氧化铝为载体,Mo、Co为加氢活性组分。以催化剂的重量为基准,金属Mo含量以氧化物计为6wt%~20wt%,金属Co含量以氧化物计为1wt%~12wt%。根据本发明的方法,还可以进一步包括以下内容:在步骤(3)中至少两个相邻的裂化催化剂床层之间设置气相引出管线,部分气相物流可以经由气相引出管线引出至高压分离器催化柴油加氢转化部分高压分离器,而液相和剩余气相混合物继续进行加氢裂化反应。一般情况下,在反应条件下原料反应后气化率(气化率指在反应条件下,转化为气相的原料占原料总质量的比例,不含氢气)超过30质量%,优选超过50质量%的裂化催化剂床层间设置气相引出管线。所述的气相引出管线优选设置在催化剂床层间气液分配盘或冷氢箱的下方,气相引出管线安装有流量控制阀。正常操作时,气液分配盘或冷氢箱的下部会形成一个气相空间,气相引出管线在反应器内的开口设置在该气相空间中,液相物料基本不进入气相引出管线。本发明中优选在气相引出管线开口处设置折流档板,以进一步防止液相进入气相引出管线。在气相引出管线上面催化剂床层的氢油体积比一般为700:1~3000:1,优选800:1~1500:1;气相引出管线下面催化剂床层的氢油体积比一般为220:1~2000:1,优选300:1~1000:1。优选加氢裂化反应器的氢油比高于加氢精制反应器的氢油比200~800,最优选高出300~600。所述气相引出管线引出的气相物料量一般为循环氢气量(以体积计)的20%~70%,优选30%~60%。本发明方法中,所述的加氢精制反应的工艺条件包括:反应温度为320℃~440℃,优选340℃~420℃;反应压力为4.0MPa~15.0MPa,优选6.0MPa~12.0MPa;液时体积空速为0.2h-1~6.0h-1,优选0.5h-1~3.0h-1;氢油体积比为100~2000,优选500~1500。本发明中方法中,所述的催化汽油选择性加氢的工艺条件包括:反应温度为200℃~400℃,优选220℃~320℃;反应压力为0.5MPa~4.0MPa,优选1.0MPa~3.0MPa;液时体积空速为0.2h-1~10.0h-1,优选0.5h-1~6.0h-1;氢油体积比为10~500,优选30~300。本发明的方法中,所述催化裂化柴油的性质一般为:密度为0.88~0.99g/cm3,其干点一般为360~400℃,芳烃含量一般为50wt%~95wt%。催化裂化柴油的硫含量一般为0.2wt%~2wt%,氮含量为500μg/g~2000μg/g。催化裂化汽油的性质一般为:密度为0.70~0.80g/cm3,其干点一般为180~220℃,芳烃含量一般为5wt%~20wt%,烯烃含量一般为20wt%~50wt%。催化裂化汽油的硫含量一般为0.01wt%~0.2wt%,氮含量为10μg/g~200μg/g。与现有技术相比较,本发明的催化裂化柴油转化方法的优点是:1、在加氢裂化反应器内,由上至下随着裂化深度的加深,裂化反应器内反应物组分中裂解生成的石脑油含量由上至下逐渐增加,未裂化柴油部分由上至下逐渐下降。因此,采用本发明方法,裂化段催化剂床层加氢活性由上至下逐渐下降,在保证了催化裂化柴油加氢效果的同时,减少了石脑油的加氢,降低了氢耗,提高了石脑油产品辛烷值。2、本发明方法在加氢裂化催化剂混合床层级配装填的基础上,在相邻的混合催化剂床层之间设置气相引出管线,同样可以将部分已经裂化的气相(主要包括气体轻和汽油组分)直接引出加氢裂化催化剂床层,也可以在一定程度上进一步减少了汽油的进一步加氢或裂化反应,一方面能够提高汽油的辛烷值,同时还可以提高加氢裂化的液体产品收率。3、通过提高裂化反应器的氢油比,更多地携带轻组分排出反应器,可进一步减少轻组分的二次或多次裂化反应,进而增加加氢裂化反应液收,提高汽油馏分的辛烷值。4、加氢裂化反应器下部催化剂床层中轻组分的二次或多次裂化反应减少,也有利于降低催化剂床层的积炭,延长装置的运转周期。5、催化汽油原料与催化柴油加氢转化部分未转化柴油混合后直接进入催化汽油选择性加氢脱硫反应器反应,与常规催化汽油选择性加氢工艺相比,催化汽油原料不经过换热器及加热炉加热,因此减少了换热器及加热炉内结焦的问题,另一方面未转化催化柴油馏分与催化汽油一起进入催化汽油选择性加氢脱硫装置反应,起到了吸收反应热的作用,降低了床层温升,避免了常规装置中底部过高温度对催化汽油过度加氢增加催化汽油辛烷值损失的问题。6、催化汽油选择性加氢脱硫部分取消循环氢压缩机的设置,直接利用管网氢气作为反应用氢,加氢转化部分与催化汽油选择性加氢装置共用一套分馏系统,与两套装置分别运转相比节省了投资。附图说明图1为本发明方法的一种原则工艺流程图。图2为本发明方法的另一种原则工艺流程图。具体实施方式下面结合附图和具体实施例对本发明的方法作更进一步的描述。如图1所示,催化裂化柴油首先进入催化汽油选择性加氢脱硫部分低压换热器2,与催化汽油选择性加氢脱硫装置流出物进行换热;然后,经升压泵24升压后进入催化柴油加氢转化部分的换热器3,与催化柴油加氢转化部分的反应流出物换热后经管线1与经管线4引入的氢气混合进入预处理反应器5进行加氢精制反应,精制反应器反应流出物经管线6直接进入裂化反应器7内与裂化反应器内级配的催化剂床层接触反应,反应流出物经管线8与经低压换热器2换热后的催化柴油原料在高压换热器3中换热后进入热高分9分离出气相和液相,气相部分经管线11进入分离器12分出石脑油馏分和氢气,分离所得的石脑油经管线13进入下游分馏塔20,分离得到的氢气经循环氢压缩机25和管线4循环回催化柴油预处理反应器;液相部分即未转化的催化柴油经减压后,经管线10与经管线15引入的低压新氢和经管线14引入的催化裂化汽油混合后直接进入催化汽油选择性加氢装置17对催化汽油进行选择性加氢脱硫反应,反应流出物进入分离器18进行气、液分离。分离得到的氢气经脱硫化氢处理后经新氢压缩机26加压后、经管线16循环回催化柴油加氢转化部分精制反应器入口作为催化柴油加氢转化部分的新氢使用,分离所得液相经低压换热器2和管线19,与加氢转化部分分离获得的石脑油馏分混合后进入分馏塔20,经分馏得到气体产品21、高辛烷值汽油22和低硫柴油组分23。如图2所示,本发明方法的另一种工艺流程为:催化裂化柴油首先进入催化汽油选择性加氢脱硫部分低压换热器2,与催化汽油选择性加氢脱硫装置流出物进行换热;然后,经升压泵24升压后进入催化柴油加氢转化部分的换热器3,与催化柴油加氢转化部分的反应流出物换热后经管线1与经管线4引入的氢气混合进入预处理反应器5进行加氢精制反应,精制反应器反应流出物经管线6直接进入裂化反应器7内与裂化反应器内级配的催化剂床层接触反应;在相邻的两个裂化催化剂床层之间,通过管线10引出部分气体至热高分9;反应流出物与经低压换热器2换热后的催化柴油原料在高压换热器3中换热后经管线8进入热高分9分离出气相和液相,气相部分经管线11进入分离器12分出石脑油馏分和氢气,分离所得的石脑油经管线13进入下游分馏塔20,分离得到的氢气经循环氢压缩机25、管线4循环回催化柴油预处理反应器;液相部分即未转化的催化柴油经减压后、经管线14与经管线15引入的低压新氢和经管线16引入的催化裂化汽油混合后直接进入催化汽油选择性加氢装置17对催化汽油进行选择性加氢脱硫反应,反应流出物进入分离器18进行气、液分离。分离得到的氢气经脱硫化氢处理后经新氢压缩机26加压后、经管线27循环回催化柴油加氢转化部分精制反应器入口作为催化柴油加氢转化部分的新氢使用,分离所得液相经换热器2和管线19与加氢转化部分分离获得的石脑油馏分混合后进入分馏塔20,分离出高辛烷值汽油22、低硫柴油组分23及气体产品21。下面通过实施例和比较例说明本发明的方案和效果。本发明中,实施例1-3中精制段采用常规的加氢预处理催化剂,通过调整精制段反应条件控制精制段流出油氮含量为30μg/g。裂化段分别选用了不同比例的体相法加氢精制催化剂与加氢裂化催化剂的级配方式。裂化段及催化汽油选择性加氢部分的催化剂的物化性质如下表1所示。实施例1-3实施例1-3采用本发明的流程如图1。本发明中,催化柴油加氢转化部分精制段采用的预处理催化剂为本领域应用较为广泛的FF-36加氢预处理催化剂。该非贵金属催化剂在使用前一般以氧化态形式存在,需要进行预硫化,使非贵金属氧化物转化为硫化物才具有反应活性。因此,非贵金属催化剂在使用过程中要保持硫化态。实施例1-3中采用的体相法催化剂为工业应用的FTX催化剂、裂化剂为采用常规方法制备的裂化催化剂,实施例1-3中对加氢裂化反应器进行梯度混合装填,反应器内共包括装填体积相等的3个混合催化剂床层,按照与反应物料的接触顺序(即由上而下),在三个实施例中,三个混合催化剂床层中体相法催化剂与裂化催化剂1的比例分别为3:1、1:1、0;3:1、2:1、1:1和1:1、1:2、1:3。催化汽油选择性加氢部分催化剂选用Mo-Co型催化剂2。催化剂的组成及性质见表1,所用原料性质见表2,实施例1-3反应条件及反应结果见下表3和表4。实施例4采用图2所示流程。原料油、及所使用催化剂同实施例3。其中在第二和第三裂化催化剂床层之间设置气体引出管线,其他同实施例3。气相引出管线引出的气相物料量为循环氢气量的30%。实施例的工艺条件与结果分别列于表3和表4。表1实施例裂化催化剂的组成及主要性质。表2原料油性质。表3实施例1-4所采用操作条件。表4实施例1-4评价结果。实施例1实施例2实施例3实施例4催化柴油加氢转化部分产品分布,wt%石脑油馏分馏分(<210℃)39385254柴油馏分(>210℃)55554040产品性质石脑油(<210℃)密度,g/cm-30.76000.76100.76020.7602S,μg/g<0.5<0.5<0.5<0.5N,μg/g<0.5<0.5<0.5<0.5辛烷值91.892.591.591.9柴油(>210℃)密度,g/cm-30.88410.88700.87950.8788硫含量,μg/g101298十六烷值25283126催化汽油选择性加氢部分密度,g/cm-30.74020.74390.74000.7401馏程,℃38~20538~20538~20538~205硫含量,μg/g3451211辛烷值92.291.291.892.0比较例1-2比较例1-2催化柴油转化部分采用与实施例1-3相同的工艺条件,比较例1-2加氢预处理反应器内装填与实施例1-3中相同的预处理催化剂,并通过控制操作条件调整精制段流出油的氮含量为30μg/g,裂化段催化剂装填裂化催化剂1。比较例1-2中使用的原料油与实施1-3相同。比较例1催化汽油选择性加氢部分分别控制与实施例1相同的产品硫含量,调整反应条件。与比较例1-2操作条件及产品性质列于表5、表6。表5比较例1-3所采用操作条件。比较例1比较例2催化柴油加氢转化部分反应温度,℃362390反应压力,MPa8.08.0体积空速,h-11.01.0氢油体积比12001200裂化段进料氮含量,μg/g3030单程转化率,%4560化学氢耗,wt%3.103.38催化汽油选择性加氢部分平均反应温度,℃275反应压力,MPa1.5体积空速,h-12.0氢油体积比300表6比较例1-2试验结果。比较例1表较例2产品分布,wt%石脑油馏分馏分(<210℃)3749柴油馏分(>210℃)5540产品性质石脑油(<210℃)密度,g/cm-30.76110.7604S,μg/g<0.5<0.5N,μg/g<0.5<0.5辛烷值89.887.5柴油(>210℃)密度,g/cm-30.88020.8750硫含量,μg/g1512十六烷值2227催化汽油选择性加氢部分密度,g/cm-30.7438馏程,℃29~205硫含量,μg/g32辛烷值91.2催化柴油加氢转化部分通过实施例1、实施例3与比较例1和比较例2对比发现,在采用相同工艺条件加工表2中原料时,比较例1和比较例2在控制与实施例1和实施例3相同转化率的情况下,石脑油收率分别比实施例1和实施例3降低别降低2和3个单位,石脑油组分辛烷值分别下降2个单位和4个单位。总体来看催化柴油转化部分实施例相比比较例表现出了很好裂化及加氢选择性,使用效果明显好于比较例。催化汽油选择性加氢部分比较结果表明,比较例1与实施例1达到相同的脱硫深度时,由于温升较大致使其平均反应温度相同的情况下,出口温度更高,因此,加大了辛烷值损失,产品辛烷值损失明显高于实施例,产品硫含量控制与实施例相当时,辛烷值损失比实施例1高出1个单位。此外,相比于实施例3,实施例4通过在裂化床层间抽出裂化生成的石脑油,避免了石脑油在裂化反应器下部的进一步裂化和加氢饱和,因此,相比于实施例3,实施例4催化柴油加氢转化部分重石脑油收率及辛烷值明显增加。