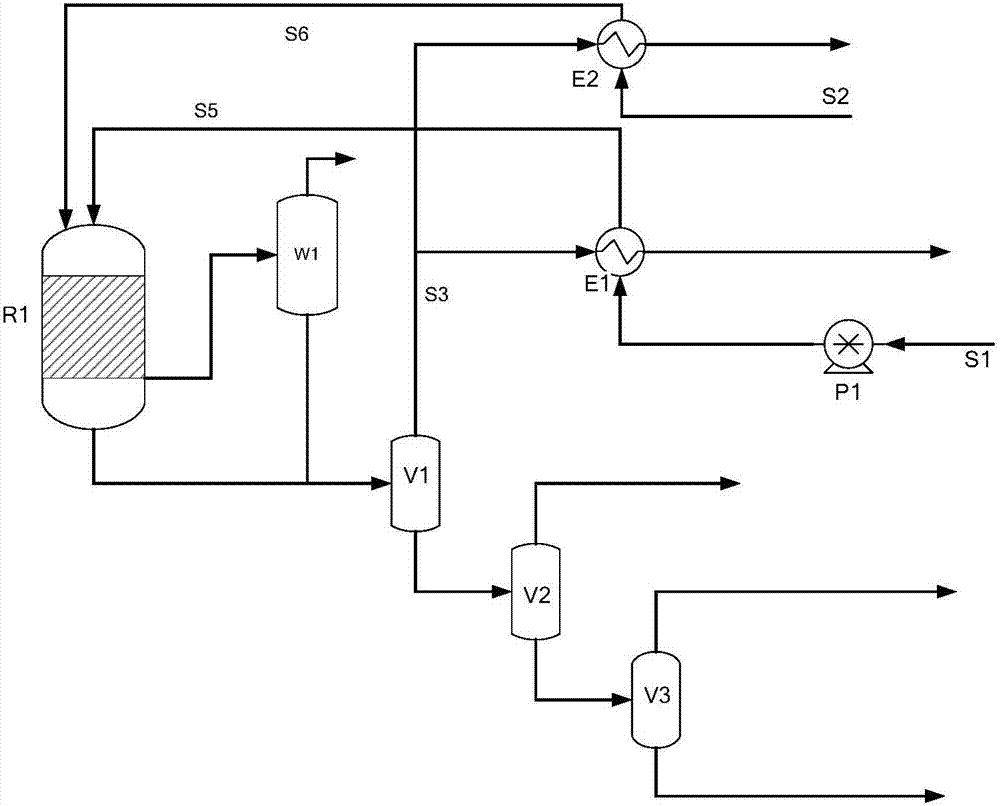
本发明涉及煤化工领域,特别是涉及碳氢化合物气化系统及其内部热量整合利用方法。
背景技术:
:利用碳氢化合物气化制备合成气或燃料气是一种成熟的化工工艺。为了提高单位时间内气化反应器的生产能力,满足原料灰分的排出条件,气化反应器必须维持较高的操作温度。通常这一操作温度依赖碳氢化合物原料与气化剂的燃烧提供。这一方面需要消耗一部分碳氢化合物原料与气化剂;另一方面气化反应产生的1300℃左右的气体在水中激冷至240℃左右,产生了大量的高温黑水,黑水闪蒸生成的闪蒸气中蕴含的大量热量没有充分利用,甚至需要消耗循环冷却水进行冷却后才能进一步处理或排放,系统能量利用效率比较低。并且燃烧产生的co2使产品气体中的有效气(h2、co)含量降低,增加了下游处理装置的规模与处理难度。技术实现要素:本发明要解决的技术问题之一是提供一种碳氢化合物气化系统,它可以提高系统能量利用率,降低生产成本。为解决上述技术问题,本发明的碳氢化合物气化系统,包括气化反应器、洗涤塔、高压闪蒸罐、低压闪蒸罐和真空闪蒸罐,其特征在于,还包括有原料换热器,所述原料换热器设置在碳氢化合物原料的进料管路上,并与高压闪蒸罐顶部出口相连。较佳的,在本发明的碳氢化合物气化系统中,还可以包括有气化剂换热器,所述气化剂换热器设置在气化剂的进气管路上,可以与原料换热器连接,也可以与高压闪蒸罐顶部出口或低压闪蒸罐顶部出口连接。在一较佳实施例中,碳氢化合物原料的进料管路上、所述原料换热器的前面还设置有用于提升碳氢化合物原料压力的高压计量进料泵。所述原料换热器可以使用管壳式、套管式、翅片管式或其他形式的间壁式换热器;所述气化剂换热器可以使用管壳式、套管式、翅片管式、绕管式、板式或其他形式的间壁式换热器。本发明要解决的技术问题之二是提供上述碳氢化合物气化系统内部热量整合利用方法。为解决上述技术问题,本发明的碳氢化合物气化系统内部热量整合利用方法,是在将碳氢化合物原料送入气化反应器进行气化反应前,用碳氢化合物气化系统产生的闪蒸气体与碳氢化合物原料进行热交换,提升碳氢化合物原料的温度。较佳的,在将气化剂送入气化反应器进行气化反应前,也同时用碳氢化合物气化系统产 生的闪蒸气体和气化剂进行热交换,提升气化剂的温度。所述碳氢化合物原料可以是由煤、石油焦、沥青、生物质、固体废弃物中的一种或多种与水或液态烃类物质形成的悬浮流体,或者渣油、沥青、重油、天然气、炼厂干气碳氢化合物流体原料。所述气化剂可以使用空气、富氧空气、纯氧、水蒸气、二氧化碳中的一种或几种的混合物。所述闪蒸气体为气化系统产生的高温液体通过减压闪蒸副产的高温气体,包括高压闪蒸蒸汽、低压闪蒸蒸汽或真空闪蒸蒸汽,闪蒸气体的主要组成成分为水蒸气。与现有碳氢化合物气化系统及其热量处理方式相比,本发明的碳氢化合物气化系统及其内部热量整合利用方法具有以下优点和有益效果:1.传统工艺碳氢化合物进料和气化剂温度与气化反应温度温差很大,本发明通过增加气化反应器进料预热步骤,利用碳氢化合物气化系统的副产物——闪蒸气中的热量,对要进入气化反应器的碳氢化合物原料与气化剂进行预热,在相同的反应条件下,节约了反应系统的热量,降低了碳氢化合物原料和气化剂的消耗以及二氧化碳的排放量;2.传统工艺产生的闪蒸气体需要采用循环水冷却后进一步处理,本发明的气化系统产生的闪蒸气体由于经过了与碳氢化合物原料及气化剂之间的换热,不需要再额外使用循环水冷却,这样就使气化系统中循环冷却水的用量得以显著降低,不仅降低了系统的能耗与水耗,也提高了整个气化系统的能量利用率。附图说明图1是本发明实施例1的碳氢化合物气化系统结构示意图。图2是本发明实施例2的碳氢化合物气化系统结构示意图。图3是本发明实施例3的碳氢化合物气化系统结构示意图。图4是本发明实施例4的碳氢化合物气化系统结构示意图。图中附图标记说明如下:r1:气化反应器e1:原料换热器e2:气化剂换热器p1:高压计量进料泵v1:高压闪蒸罐v2:低压闪蒸罐v3:真空闪蒸罐w1:洗涤塔s1:碳氢化合物原料s2:气化剂s3:高压闪蒸气s4:低压闪蒸气s5:预热后的碳氢化合物原料s6:预热后的气化剂具体实施方式为对本发明的技术内容、特点与功效有更具体的了解,现结合附图及具体实施例,对本发明做进一步详细的说明。本发明并不限于实施例1~4所示的组合形式,其它利用闪蒸蒸汽对气化原料进行加热的组合形式也在本发明保护的范围内。实施例1本实施例利用高压闪蒸气体对串联的碳氢化合物原料和气化剂进行预热。其碳氢化合物气化系统结构参见图1所示,在高压闪蒸罐v1顶部高压闪蒸气s3的流路上串联了两个换热器——原料换热器e1和气化剂换热器e2。其中,原料换热器e1为间壁式换热器。本实施例的碳氢化合物原料s1为煤与水混合形成的水煤浆悬浮流体,其煤质信息参见表1所述,初始温度为60℃。气化剂s2采用界区外的空气分离装置送来的高压纯氧,氧气纯度为99.6%摩尔百分比,初始温度为10℃。气化反应器r1为系统关键装置,用于发生气化反应。本实施例中,气化反应条件为压力6.5mpa(g),温度1332℃。气化反应器r1最终输出一股366000标准立方/小时,以氢气、一氧化碳、二氧化碳、水蒸气为主的合成气,该合成气被送往下游作进一步处理。气化反应器r1以140吨/小时的速度排放一股温度为248℃的黑水。这股黑水在高压闪蒸罐v1中、0.91mpa(g)压力下发生闪蒸分离,产生的高压闪蒸气s3用作碳氢化合物原料s1和气化剂s2的预热热源。上述反应条件下,s3流量约为18吨/小时。高压闪蒸气s3中的水蒸气含量为98%摩尔百分比,其余为一氧化碳、二氧化碳等不凝气体。碳氢化合物原料s1经过高压计量进料泵p1提升压力后,以101吨/小时的流量输入到碳氢化合物原料换热器e1中。在原料换热器e1中,碳氢化合物原料s1与高压闪蒸罐v1顶部出来的高压闪蒸气s3发生热量交换,碳氢化合物原料s1的温度被优选地提高至135℃。同时,从气化系统外输送来的高压纯氧气化剂s2通过气化剂换热器e2与高压闪蒸气s3进行换热,气化剂s2的温度被提优选地升至100℃。使用常规碳氢化合物气化系统,每生产1000标准立方有效气(co和h2)需要消耗所述的原料煤560千克,氧气353标准立方;而在使用本实施例的碳氢化合物气化系统,对煤浆 进行预热后,每生产1000标准立方有效气只需要消耗煤549千克,氧气337标准立方,氧耗和煤耗分别下降了1.9%和4.7%。冷煤气效率由77.2%提升为79.0%,增加了1.7个百分点。可见,通过改进碳氢化合物气化系统,集成系统内的热量,在不改变反应条件、不牺牲产品质量的情况下,使系统能量利用率获得了提高。表1原料煤的性质碳元素含量%74氢元素含量%4.5氮元素含量%0.8总硫元素含量%1氧元素含量%8.7灰分含量%11发热量mj/kg29.32煤浆浓度wt%62注:表1中数值均是在干基煤情况下测定得到。实施例2本实施例中将高压闪蒸气体分作两股,并联地对碳氢化合物原料和气化剂进行预热,具体可以参考图2所示。碳氢化合物原料s1、气化剂s2、高压闪蒸气s3量与性质同实施例1。碳氢化合物原料s1通过高压计量进料泵p1提升压力后,进入原料换热器e1。在原料换热器e1中,碳氢化合物原料s1与高压闪蒸气s3发生换热,温度由60℃提升为135℃。同时,高压纯氧气化剂s2与高压闪蒸气s3分流出的另一股在气化剂换热器e2中进行换热,温度由10℃提升至135℃。预热后的碳氢化合物原料与气化剂进入气化反应器r1中发生气化反应。反应条件与实施例1相同。相比常规碳氢化合物气化系统,使用本实施例的碳氢化合物气化系统对煤浆进行预热后,生产单位体积的有效气(co、h2)煤耗可降低2.1%,氧耗可降低5.0%,系统冷煤气效率可提高1.6个百分点。实施例3本实施例分别利用高压闪蒸气体和低压闪蒸气体对碳氢化合物原料和气化剂进行预热。其碳氢化合物气化系统结构参见图3所示,在高压闪蒸罐v1顶部的高压闪蒸气s3流路上接入了一个原料换热器e1,在低压闪蒸罐v2顶部的低压闪蒸气s4的流路上接入了一个气化剂换热器e2。碳氢化合物原料s1、气化剂s2、高压闪蒸气s3同实施例1。低压闪蒸气s4由高压闪蒸罐v1底部出来的黑水在低压闪蒸罐v2中进一步减压闪蒸获得,流量为16吨/小时,温度为134℃。碳氢化合物原料s1通过高压计量进料泵p1提升压力后,进入原料换热器e1。在原料换热器e1中,碳氢化合物原料s1与高压闪蒸气s3发生换热,温度由60℃提升为150℃。同时,高压纯氧气化剂s2与低压闪蒸气s4在气化剂换热器e2中进行换热,温度由10℃提升至100℃。预热后的碳氢化合物原料与气化剂进入气化反应器r1中发生气化反应,反应条件与实施例1相同。相比常规碳氢化合物气化系统,使用本实施例的碳氢化合物气化系统对煤浆进行预热后,生产单位体积的有效气(co、h2)煤耗可降低2.2%,氧耗可降低5.5%,系统冷煤气效率可提高1.8个百分点。实施例4本实施例仅利用高压闪蒸气体对碳氢化合物原料进行预热,系统结构参见图4所示,在高压闪蒸罐v1顶部的高压闪蒸气s3流路上接入了一个原料换热器e1。碳氢化合物原料s1、气化剂s2、高压闪蒸气s3同实施例1。碳氢化合物原料s1通过高压计量进料泵p1提升压力后,进入原料换热器e1。在原料换热器e1中,碳氢化合物原料s1与高压闪蒸气s3发生换热,温度由60℃提升为150℃。预热后的碳氢化合物原料直接与界区外的气化剂进入气化反应器r1中发生气化反应。反应条件与实施例1相同。相比常规碳氢化合物气化系统,使用本实施例的碳氢化合物气化系统对煤浆进行预热后,生产单位体积的有效气(co、h2)煤耗可降低1.9%,氧耗可降低4.6%,系统冷煤气效率可提高1.5个百分点。当前第1页12