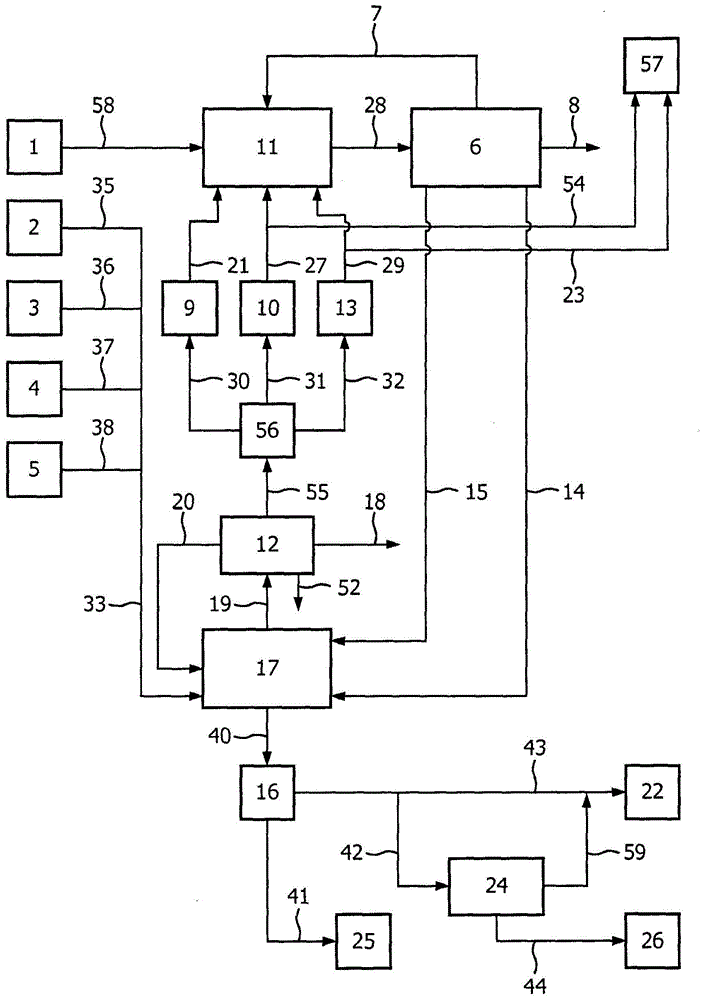
本发明涉及在蒸汽裂解器单元中裂解烃原料的方法。
背景技术:
:通常,将原油经由蒸馏处理成许多馏分例如石脑油,瓦斯油和残留物。每个这些馏分具有许多潜在的用途,例如用于生产运输燃料例如汽油,柴油和煤油或者作为到一些石化和其他处理单元的进料。轻质原油馏分例如石脑油和一些瓦斯油可以用于经由方法例如蒸汽裂解来生产轻质烯烃和单环芳香族化合物,在其中烃进料流蒸发,并且用蒸汽稀释,然后在短的停留时间(<1秒)暴露于非常高的炉(反应器)管的温度(800℃-860℃)。在这样的方法中,当与进料分子相比时,进料中的烃分子被转化成(平均)更短的分子和具有较低的氢:碳比的分子(例如烯烃)。这种方法也产生了氢作为有用的副产物和大量的较低价值辅助产物例如甲烷和c9+芳烃和缩合芳族物质(包含两个或者更多个共享边的芳环)。通常,更重质(或者更高沸点),更高芳族含量的流例如残留物是在原油精炼厂进一步处理,来使得来自原油的更轻质(可蒸馏)产物的收率最大化。这种处理可以通过方法例如加氢裂解来进行(由此将加氢裂解器进料在这样的条件下暴露于合适的催化剂,所述条件导致进料分子的一些部分破裂成更短的烃分子,同时添加氢)。重质精炼流加氢裂解通常在高压和高温进行的,和因此具有高的资金成本。原油蒸馏和轻质蒸馏馏分的蒸汽裂解的这样的组合的一个方面是资金和与原油分馏相关的其他成本。重质原油馏分(即沸点超过~350℃)是相对富含取代的芳族物质的,特别是取代的缩合的芳族物质(包含两个或更多个共享边的芳环),并且在蒸汽裂解条件下,这些材料将产生大量的重质副产物例如c9+芳烃和缩合的芳烃。因此,原油蒸馏和蒸汽裂解的常规组合的结果是大部分原油没有经由蒸汽裂解器处理,因为来自于重质馏分的有价值的产物的裂解收率不被认为是足够高的。上述技术的另一方面是甚至当仅仅轻质原油馏分(例如石脑油)经由蒸汽裂解处理时,显著部分的进料流也被转化成低价值重质副产物例如c9+芳烃和缩合的芳烃。使用通常石脑油和瓦斯油,这些重质副产物会占总产物收率的2%-25%(表vi,第295页,pyrolysis:theoryandindustrialpractice,lylef.albright等人,academicpress,1983)。虽然这表示了在常规蒸汽规模上低价值材料中昂贵的石脑油的明显财政降级,但是这些重质副产物通常不值得这样的资金投入,即,将这些材料提质(例如通过加氢裂解)成能够产生大量更高价值的化学品的流所需的资金投入。这部分是因为加氢裂解设备具有高的资金成本,并且当使用大部分的石化方法时,这些单元的资金成本通常与以0.6或者0.7的次方增加的通过量成比例的。因此,小规模加氢裂解单元的资金成本通常被认为过高,而不值得这样的投资来处理蒸汽裂解器重质副产物。重质精炼流例如残留物的常规加氢裂解的另一方面是这通常在选择来实现期望的整体转化率的折衷条件下进行的。因为进料流包含一定范围内易于裂解的物质的混合物,因此这导致通过相对容易加氢裂解的物质的加氢裂解所形成的可蒸馏产物的一些部分在这样的条件下进一步转化,该条件是加氢裂解更难以加氢裂解的加氢裂解物质所必需的。这增加了与所述方法有关的氢的消耗和热管理难度,以及以更有价值的物质为代价,增加了轻质分子例如甲烷的收率。更轻质蒸馏馏分的原油蒸馏和蒸汽裂解的这样的组合的一个特征是蒸汽裂解炉管通常不适于处理这样的馏分,其包含显著量的沸点大于~350℃的材料,因为它难以确保在混合烃和蒸汽流暴露于促进热裂解所需的高温之前,这些馏分完全蒸发。如果液体烃的小滴存在于裂解管的热区中,则焦炭快速沉积到该管表面,其降低了传热并且增加了压降并且最终减少了裂解管的运行,使得必需使该管停机来进行脱焦。归因于这种难点,显著比例的初始原油不能经由蒸汽裂解器处理成轻质烯烃和芳族物质。us2009173665涉及催化剂和增加烃原料(其包括多核芳烃)的单芳族含量的方法,其中单芳烃的增加可以使用如下方式来实现:增加汽油/柴油收率和同时降低不想要的化合物,由此提供用于提质烃的路线,该烃包括显著量的多核芳烃。fr2364879涉及选择性方法,用于生产每个分子分别具有2和3个碳原子的轻质烯烃,特别是乙烯和丙烯,其是通过氢解或者加氢裂解,随后用蒸汽裂解来获得的。de2708412涉及用于生产乙烯的整合的方法,其包括在510-815℃的温度,15-70大气压的压力和5-60秒的停留时间条件下,将烃原料引入没有非热加氢裂解催化剂的加氢裂解反应器中的步骤,分离芳香族烃的步骤,通过低温技术分离基本上由c2-c3烃组成的流的步骤;和将所述的流引入裂解区中,其保持在将主要包含乙烯的流中的烃进行转化的条件下。us3944481涉及通过如下来将原油馏分转化成烯烃产物的方法:将该原油馏分加氢裂解成c2-c5链烷烃和将它们热裂解成c2-c3烯烃混合物,其中将氢,甲烷和c6-c9组分与c2-c5馏分分离,并且该c2-c5馏分然后与蒸汽混合和注入到热裂解器中。ep0023802涉及生产轻质链烷烃的方法,其包括在高于2859kpa的压力,300-565℃的温度,氢/烃摩尔比4:1-50:1和在催化剂上的停留时间1-180秒的条件下,加氢裂解沸点为93℃-538℃的原油馏分,并且回收c2-c5烷烃产物,其中将所述的烷烃产物热裂解成乙烯和丙烯。gb1148967涉及制备乙烯的方法,其包括在高温在氢和催化剂存在下,加氢裂解沸点低于250℃的烃油,将烃混合物与加氢裂解的反应产物分离,在高温在蒸汽存在下热裂解这种混合物,和从热裂解的反应产物中分离乙烯。作为加氢裂解的结果,由烃油所形成的烃混合物是作为液体存在于气体/液体分离系统中的,并且送过管线到蒸汽裂解炉。gb1250615涉及芳烃提取方法,由此芳烃可以从含芳烃的加氢裂解物中提取。us3842138涉及氢存在下热裂解石油的烃加料的方法,其中该加氢裂解方法是在5-70巴的压力,在反应器的出口使用0.01-0.5秒的非常短的停留时间和在反应器出口处从625延至1000℃的温度范围进行的。技术实现要素:本发明一个目标是提供将石脑油提质成芳烃和包含c2-c4链烷烃的蒸汽裂解器原料的方法。本发明的另一目标是提供这样的方法,其用于将相对重质液体进料例如柴油和常压瓦斯油转化来生产包含单芳烃和c2-c4链烷烃的加氢裂解产物流。本发明的另一目标是处理重质液体原料,同时使得重质c9+副产物的产生最小化。本发明涉及裂解蒸汽裂解器单元中的烃原料的方法,其包括下面的步骤:将液体烃原料进料到加氢裂解单元中,将因此在所述的加氢裂解单元中加氢裂解的流分离成高含量芳烃流和包含c2-c4链烷烃、氢和甲烷的气态流,从所述的气态流中分离c2-c4链烷烃,将因此分离的所述的c2-c4链烷烃进料到蒸汽裂解器单元的炉区。基于这样的方法,实现了本发明的一种或多种目标。根据这样的方法,该加氢裂解的原料可以作为原料用于蒸汽裂解器单元。该芳烃与所述气态流分离,并且将不送到蒸汽裂解器单元,而是将在分别的单元中进一步处理。甲烷和其他轻质组分可以在分离器中预处理,来将c2-c4链烷烃从所述的气态流中分离,并且将该c2-c4链烷烃送到蒸汽裂解器单元。在蒸汽裂解器单元中所产生的通常气体通常包含许多氢,其经常作为燃料来满足蒸汽裂解器的能量需求。这因此将改进能量性能和氢平衡。因此本发明的主要目标是生产lpg(乙烷,丙烷,丁烷),其可以在气体蒸汽裂解器单元中处理。通过将合适设计的加氢裂解器单元置于气体蒸汽裂解器前面,和将液体烃原料例如石脑油进料到所述的加氢裂解器单元,它有效地充当了到气体蒸汽裂解器的进料预处理单元,来使得否则会不合适的进料适于在现有的气体蒸汽裂解器中处理。根据本发明的方法,待处理的潜在进料可以是烃流例如柴油,煤油,常压瓦斯油(ago),气体冷凝物,石脑油和蜡状材料。根据本发明,该用于生产c2-c4烯烃和具有一个芳环的芳烃的方法包括在氢存在下,将沸点为20-350℃的液体烃原料与加氢裂解催化剂接触,来生产包含具有一个芳环的芳香族烃和c2-c4链烷烃的加氢裂解产物流的步骤,从该加氢裂解产物流中分离具有一个芳环的芳香族烃的步骤;和从该加氢裂解产物流中分离c2-c4链烷烃,并且优选将所述的分离的c2-c4链烷烃供入专用热解炉来进行热解反应,来生产包含c2-c4烯烃的热解产物流的步骤。在优选的实施方案中,将包含在该热解产物流中的一部分的氢分离,并且进料到加氢裂解步骤,分离包含在该热解产物流中的c5+烃并且进料到加氢裂解步骤,使用分离器,例如蒸馏方法或溶剂提取方法,将具有一个芳环的芳香族烃从加氢裂解产物流中分离,使用分离器例如蒸馏方法将c2-c4链烷烃从该加氢裂解产物流气态级分中分离。根据其他优选的实施方案,可以预处理该烃进料(例如通过溶剂提取)来分离芳烃+环烷烃(提取物)和链烷烃(提余物)。因此,可以经由加氢裂解器处理该芳烃+环烷烃流(来进行hds和除去任何痕量的链烷烃和脱氢所述环烷烃来制造销售规格的芳烃),和将该链烷烃送到蒸汽裂解器来制造轻质烯烃。方法的这种组合将使得氢消耗最小化和使得由蒸汽裂解器单元产生的燃料气体最小化。如上所述,本发明的方法进一步包括将所述的高含量芳烃流分离成重质芳烃的流和高单芳烃的流,特别是使用蒸馏类型的分离器。根据本发明的另一实施方案,本发明的方法进一步包括将气态流(即,主要包含c2-c4链烷烃)进料到脱氢单元,来获得氢,c3-烯烃和c4-烯烃。这意味着在加氢裂解单元中所生产的气态流可以送到不同的路线,即,到蒸汽裂解器单元或者到脱氢单元。这种路线选择提供了本发明方法的灵活性。用于脱氢低级烷烃例如丙烷和丁烷的方法被描述为低级烷烃脱氢方法。在优选的实施方案中,本发明的方法进一步包括将c2-c4链烷烃分离成个体流,每个流分别主要包含c2链烷烃,c3链烷烃和c4链烷烃,和将每个个体流进料到所述的蒸汽裂解器单元的具体炉区。这意味着将c2流(该流主要包含c2链烷烃)送到蒸汽裂解器单元的具体c2炉区。对c3流和c4流进行同样的措施。这样的分离成具体流对于蒸汽裂解器单元的产物收率具有积极的作用。在优选的实施方案中,将该c3流和c4流(作为分别的流或者作为合并的c3+c4流)送到脱氢单元。更详细地,本发明的方法进一步包括将c2-c4链烷烃分离成个体流,每个流分别主要包含c2链烷烃,c3链烷烃和c4链烷烃,并且将主要包含c2链烷烃的流进料到蒸汽裂解器,同时将主要包含c3链烷烃流进料到丙烷脱氢单元,和将主要包含c4链烷烃流进料到丁烷脱氢单元。如上所述,在加氢裂解单元中所生产的气态流包含宽谱的加氢裂解产物。在优选的实施方案中,不仅c2-c4链烷烃将从该气态产物中回收,而且回收其他有价值的组分例如氢以及甲烷。含有氢和甲烷的流将优选再循环到该加氢裂解单元。另外,还优选的是在加氢裂解单元中具有净化流,来防止不想要的组分的聚集。用于从所述的气态流中分离所述的c2-c4链烷烃的方法优选是通过选自低温蒸馏或者溶剂提取的类型的分离来进行的。所述的加氢裂解中优选的工艺条件包括温度300-550℃,压力300-5000kpa表压和重时空速0.1-10h-1。更优选的加氢裂解条件包括温度350-550℃,压力600-3000kpa表压和重时空速0.2-2h-1。所述的加氢裂解单元的反应器类型设计选自固定床类型,沸腾床反应器类型和浆料类型,其中固定床类型是优选的。到所述的加氢裂解单元的烃原料的例子是石脑油,煤油,柴油,常压瓦斯油(ago),气体冷凝物,石脑油,蜡或者其组合的类型。高含量芳烃流的分离优选是蒸馏类型。根据优选的实施方案,本发明的方法进一步包括从高单芳烃的流中分离c7-c9芳烃,例如富含甲苯和二甲苯的馏分,和将所述的c7-c9芳烃转化成富含苯的馏分。此外,本发明的方法进一步包括从所述的蒸汽裂解器单元的产物流中回收一部分的氢,和将所述的氢进料到所述的加氢裂解单元。如上所述,本发明的方法进一步包括从所述的蒸汽裂解器单元的产物流中回收c5+烃,和将所述的c5+烃进料到所述的加氢裂解单元。作为此处使用的,术语“原油”指的是从地质地岩层中提取的处于它的未精炼形式的石油。任何原油适于作为本发明方法的原材料,包括阿拉伯重质油,阿拉伯轻质油,其他海湾原油,布伦特,北海原油,北非和西非原油,印尼原油,中国原油及其混合物,但是还可以是页岩油,沥青砂和生物基油。该原油优选是api比重大于20°api的常规石油,如通过astmd287标准来测量的。更优选所用的原油是api比重大于30°api的轻质原油。最优选该原油包含阿拉伯轻质原油。阿拉伯轻质原油通常api比重是32-36°api并且硫含量是1.5-4.5wt%。作为此处使用的,术语“石化品”或者“石化产品”涉及来源于原油的化学产品,其不用作燃料。石化产品包括烯烃和芳烃,其被用作生产化学品和聚合物的基本原料。高价值石化品包括烯烃和芳烃。通常高价值烯烃包括但不限于乙烯,丙烯,丁二烯,丁烯-1,异丁烯,异戊二烯,环戊二烯和苯乙烯。通常高价值芳烃包括但不限于苯,甲苯,二甲苯和乙基苯。作为此处使用的,术语“燃料”涉及用作能量载体的原油来源的产品。不同于石化品(其是明确限定的化合物的集合),燃料通常是不同的烃化合物的复杂混合物。通过炼油厂通常所生产的燃料包括但不限于汽油,喷气机燃料,柴油燃料,重质燃料油和石油焦。术语“芳香族烃”或者“芳烃”是本领域公知的。因此,术语“芳香族烃”涉及成环共轭烃,其具有大于假设的定域结构(例如kekulé结构)的稳定性(归因于离域)。测定给定烃的芳香性最常用的方法是观察1hnmr光谱中的横向性,例如就苯环质子而言的7.2-7.3ppm范围的化学位移的存在。作为此处使用的,术语“环烷的烃”或者“环烷烃”或者“环烷”具有它公知的含义,并且因此涉及在它们的分子化学结构中具有一个或多个碳原子环的烷烃类型。作为此处使用的,术语“烯烃”具有它公知的含义。因此,烯烃涉及含有至少一个碳-碳双键的不饱和的烃化合物。优选术语“烯烃”涉及包含下面的两种或更多种的混合物:乙烯,丙烯,丁二烯,1-丁烯,异丁烯,异戊二烯和环戊二烯。作为此处使用的,术语“lpg”指的是术语“液化石油气”的公知的首字母缩写。lpg通常由c2-c4烃的共混物组成,即,c2,c3和c4烃的混合物。作为此处使用的,术语“btx”涉及苯、甲苯和二甲苯的混合物。作为此处使用的,术语“c#烃”(其中“#”是正整数)意指描述了具有#个碳原子的全部烃。此外,术语“c#+烃”意指描述了具有#或者更多个碳原子的全部烃分子。因此,术语“c5+烃”意指描述具有5或更多个碳原子的烃的混合物。术语“c5+烷烃”因此涉及具有5或者更多个碳原子的烷烃。作为此处使用的,术语“加氢裂解器单元”或者“加氢裂解器”涉及精炼单元,在其中进行加氢裂解方法,即通过高的氢分压存在来辅助的催化裂解方法;参见例如alfke等人(2007)loc.cit。这种方法的产物是饱和烃,并且取决于反应条件例如温度,压力和空速和催化剂活性,芳香族烃包括btx。用于加氢裂解的工艺条件通常包括处理温度200-600℃,高压0.2-20mpa,空速0.1-10h-1。加氢裂解反应通过需要酸功能的双功能机构来进行,其提供裂解和异构化并且其提供了进料所含的烃化合物所含的碳-碳键的断裂和/或重排,和加氢功能。用于加氢裂解方法的许多催化剂是通过将各种的过渡金属或者金属硫化物与固体载体例如氧化铝,二氧化硅,氧化铝-二氧化硅,氧化镁和沸石复合(compositing)来形成的。作为此处使用的,术语“进料加氢裂解单元”或者“fhc”指的是精炼单元,其用于进行加氢裂解方法,该方法适于将复杂的烃进料(其相对富含环烷烃和链烷烃化合物,例如直馏馏分,包括但不限于石脑油)转化成lpg和烷烃。优选地,进行进料加氢裂解的烃进料包含石脑油。因此,通过进料加氢裂解所生产的主产物是lpg,其被转化成烯烃(即,作为进料用于烷烃到烯烃的转化)。该fhc方法可以优化来保持fhc进料流中所含芳烃的一个芳环的完整性,但是从所述的芳环上除去大部分侧链。在这样的情况中,用于fhc的工艺条件是与用于上述的ghc方法的工艺条件相当的。可选择地,该fhc方法可以优化来打开fhc进料流所含芳香族烃的芳环。这可以通过增加催化剂的加氢活性,任选地与选择较低工艺温度相组合,任选地与降低空速相组合,来改变此处所述的ghc方法而实现。在这样的情况中,优选的进料加氢裂解条件因此包括温度300-550℃,压力300-5000kpa表压和重时空速0.1-10h-1。更优选的进料加氢裂解条件包括温度300-450℃,压力300-5000kpa表压和重时空速0.1-10h-1。优化来使芳香族烃开环的甚至更优选的fhc条件包括温度300-400℃,优选温度350-450℃,更优选375-450℃,压力600-3000kpa表压和重时空速0.2-2h-1。“芳族开环单元”指的是精炼单元,在其中进行芳族开环方法。芳族开环是特定的加氢裂解方法,其特别适于将进料(其相对富含沸点处于煤油和汽油沸点范围的芳香族烃)转化来生产lpg,并且取决于工艺条件,轻质馏出物(aro来源的汽油)。这样的芳族开环方法(aro方法)例如描述在us3256176和us4789457中。这样的方法可以包括单固定床催化反应器或者串联的两个这样的反应器以及一个或多个分馏单元,来从未转化的材料中分离期望的产物,并且还可以并入将未转化的材料再循环到反应器之一或者二者的能力。反应器可以在温度200-600℃,优选300-400℃,压力3-35mpa,优选5-20mpa以及5-20wt%的氢(相对于烃原料)进行,其中所述的氢可以在用于加氢-脱氢和环破裂二者的双功能催化剂活性的存在下与烃原料顺流或者与烃原料的流动方向逆流,其中可以进行所述的芳环饱和和环破裂。用于这样的方法中的催化剂包含选自下面的一种或多种元素:pd,rh,ru,ir,os,cu,co,ni,pt,fe,zn,ga,in,mo,w和v,其处于金属或者金属硫化物的形式,并且负载于酸性固体例如氧化铝,二氧化硅,氧化铝-二氧化硅和沸石上。在这方面,要注意的是作为此处使用的,术语“负载于”包括任何常规方式来提供催化剂,其将一种或多种元素与催化载体相组合。另一芳族开环方法(aro方法)描述在us7513988中。因此,该aro方法可以包括在芳族加氢催化剂存在下,在100-500℃,优选200-500℃和更优选300-500℃的温度,2-10mpa的压力用5-30wt%,优选10-30wt%的氢(相对于烃原料)进行芳环饱和,和在环破裂催化剂存在下,在200-600℃,优选300-400℃的温度,1-12mpa的压力,用5-20wt%的氢(相对于烃原料)进行环破裂,其中所述的芳环饱和和环破裂可以在一个反应器或者在两个连续的反应器中进行。该芳族加氢催化剂可以是常规的加氢/加氢处理催化剂例如这样的催化剂,其包含难熔载体(通常氧化铝)载ni,w和mo的混合物。该环破裂催化剂包含过渡金属或者金属硫化物组分和载体。优选该催化剂包含选自下面的一种或多种元素:pd,rh,ru,ir,os,cu,co,ni,pt,fe,zn,ga,in,mo,w和v,其处于金属或者金属硫化物的形式,负载于酸性固体例如氧化铝,二氧化硅,氧化铝-二氧化硅和沸石上。通过采用单个或者相组合的催化剂组合物,运行温度,运行空速和/或氢分压,可以使所述方法朝向完全饱和并且随后裂解全部的环,或者朝向保持一个芳环不饱和和随后裂解除一个环外的全部环。在后者的情况中,该aro方法产生了轻质馏出物(“aro汽油”),其相对富含具有一个芳环的烃化合物。作为此处使用的,术语“脱芳构化单元”涉及精炼单元,其用于从混合的烃进料中分离芳香族烃例如btx。这样的脱芳构化方法描述在folkins(2000)benzene,ullmann'sencyclopediaofindustrialchemistry中。因此,存在这样的方法,其用于将混合的烃流分离成第一流(其富含芳烃)和第二流(其富含链烷烃和环烷烃)。优选的从芳香族烃和脂肪族烃混合物中分离芳香族烃的方法是溶剂提取;参见例如wo2012135111a2。用于芳族溶剂提取中的优选的溶剂是环丁砜,四甘醇和n-甲基吡咯烷酮,其是商业芳烃提取方法中通常使用的溶剂。这些物质经常与其他溶剂或者其他化学品(有时候称作助溶剂)例如水和/或醇组合使用。不含氮的溶剂例如环丁砜是特别优选的。商业应用的脱芳构化方法对于沸点超过250℃,优选200℃的烃混合物的脱芳构化是不太优选的,因为这样的溶剂提取中所用的溶剂的沸点需要低于待提取的芳香族化合物的沸点。重质芳烃的溶剂提取是本领域描述的;参见例如us5880325。可选择地,除了溶剂提取,其他已知的方法例如分子筛分离或者基于沸点的分离,可以用于脱芳构化方法中的分离重质芳烃。将混合的烃流分离成主要包含链烷烃的流和包含主要芳烃和环烷烃的第二流的方法包括在溶剂提取单元中处理所述的混合烃流,该提取单元包含三个主要的烃处理塔:溶剂提取塔,汽提塔和提取塔。选择用于提取芳烃的常规的溶剂也是就溶解轻质环烷烃和较少程度的轻质链烷烃物质而言有选择性的,因此离开溶剂提取塔底部的流包含溶剂以及溶解的芳烃,环烷烃和轻质链烷烃物质。离开溶剂提取塔顶部的流(经常称作提余物流)包含相对不溶性的(相对于所选择的溶剂而言)链烷烃物质。该离开溶剂提取塔底部的流然后在蒸馏塔中进行蒸发汽提,在其中在溶剂存在下物质是基于它们的相对挥发性来分离的。在溶剂存在下,轻质链烷烃物质具有相比于具有相同数目的碳原子的环烷烃物质和特别是芳族物质更高的相当挥发性,因此大部分轻质链烷烃物质会在来自于蒸发性汽提塔的顶部流中浓缩。这种流可以与来自于溶剂提取塔的提余物流合并或者作为单独的轻质烃流收集。归因于它们相对低的挥发性,大部分环烷烃和特别是芳族物质保留在合并的溶剂和离开这个塔底部的溶解烃流中。在提取单元最后的烃处理塔中,通过蒸馏将溶剂与溶解的烃物质分离。在这个步骤中,具有相对高的沸点的溶剂是作为来自于所述塔的底部流回收的,而溶解的烃(主要包含芳烃和环烷烃物质)是作为离开该塔顶部的蒸气流回收的。这种后者的流经常称作提取物。本发明的方法会需要从某些原油级分中除硫,来防止在下游精炼方法例如催化重整或者流体催化裂解中催化剂失活。这样的加氢脱硫方法是在“hds单元”或者“加氢处理器”中进行的;参见alfke(2007)loc.cit。通常,该加氢脱硫反应在固定反应器中,在200-425℃,优选300-400℃的高温和1-20mpa表压,优选1-13mpa表压的高压,在催化剂存在下进行的,该催化包含选自ni,mo,co,w和pt的元素,具有或者不具有促进剂,负载于氧化铝上,其中该催化剂处于硫化物的形式。在另一实施方案中,该方法进一步包括加氢脱烷基化步骤,其中将btx(或者仅仅所生产的所述btx的甲苯和二甲苯级分)与氢在合适的条件下接触,来生产包含苯和燃料气体的加氢脱烷基化产物流。由btx生产苯的处理步骤可以包括这样的步骤,其中在加氢脱烷基化之前,将该加氢裂解产物流中所含的苯与甲苯和二甲苯进行分离。这种分离步骤的优点是增加了加氢脱烷基化反应器的能力。苯可以通过常规蒸馏来与btx流分离。用于包含c6-c9芳烃的烃混合物的加氢脱烷基化方法是本领域公知的,并且包括热加氢脱烷基化和催化加氢脱烷基化;参见例如wo2010/102712a2。催化加氢脱烷基化是优选的,因为这种加氢脱烷基化方法通常相比于热加氢脱烷基化而言具有对于苯更高的选择性。优选使用催化加氢脱烷基化,其中该加氢脱烷基化催化剂选自负载的氧化铬催化剂,负载的氧化钼催化剂,二氧化硅或氧化铝载铂和二氧化硅或氧化铝载氧化铂。用于加氢脱烷基化的工艺条件(在此也称作“加氢脱烷基化条件”)可以由本领域技术人员容易地确定。用于热加氢脱烷基化的工艺条件例如描述在de1668719a1中,并且包括温度600-800℃,压力3-10mpa表压和反应时间15-45秒。用于优选的催化加氢脱烷基化的工艺条件描述在wo2010/102712a2中,并且优选包括温度500-650℃,压力3.5-8mpa表压,优选3.5-7mpa表压和重时空速0.5-2h-1。该加氢脱烷基化产物流通常通过冷却和蒸馏的组合,分离成液体流(包含苯和其他芳族物质)和气体流(包含氢,h2s,甲烷和其他低沸点烃)。该液体流可以通过蒸馏进一步分离成苯流,c7-c9芳烃流和任选的中质馏出物流,其是相对富含芳烃的。该c7-c9芳族流可以作为再循环供给回反应器区,来增加整体转化率和苯收率。该芳族流(其包含聚芳族物质例如联苯基)优选没有再循环到反应器,而是可以作为单独的产物流输出和作为中质馏出物(“通过加氢脱烷基化生产的中质馏出物”)再循环到整合的方法。该气体流包含大量氢,其可以经由再循环气体压缩机再循环回到加氢脱烷基化单元或者到任何其他使用氢作为进料的精炼器。再循环气体净化可以用于控制反应器进料中甲烷和h2s的浓度。作为此处使用的,术语“气体分离单元”涉及精炼单元,其分离了通过粗蒸馏单元所生产的气体和/或来源于精炼单元的气体中的不同的化合物。可以在气体分离单元中分离成单独的流的化合物包含乙烷,丙烷,丁烷,氢和主要包含甲烷的燃料气体。可以使用任何适用于分离所述气体的常规方法。因此,所述气体可以经历多个压缩阶段,其中在压缩阶段之间可以除去酸性气体例如co2和h2s。在随后的步骤中,所产生的气体可以在级联的冷冻系统的阶段中部分冷凝到大约其中仅仅氢保留在气态相中。不同的烃化合物可以随后通过蒸馏进行分离。用于将烷烃转化成烯烃的方法包括“蒸汽裂解”或者“热解”。作为此处使用的,术语“蒸汽裂解”涉及石化方法,在其中饱和烃分裂成较小的,经常不饱和的烃例如乙烯和丙烯。在蒸汽裂解气态烃进料如乙烷,丙烷和丁烷或者其混合物中,(气体裂解)或者液体烃进料如石脑油或者汽油(液体裂解)是用蒸汽稀释和在炉中短暂加热的,并且不存在氧。通常,反应温度是750-900℃,但是该反应仅仅允许非常短暂的发生,通常停留时间是50-1000毫秒。优选选择相对低的处理压力,所述相对低的处理压力是大气压到最高175kpa表压。优选烃化合物乙烷,丙烷和丁烷是在因此专用的炉中分别裂解的,来确保在最佳条件裂解。在达到裂解温度后,使用骤冷油将该气体快速骤冷来停止转移管线热交换器中或者冷却集管内的反应。蒸汽裂解导致焦炭(碳的形式)缓慢沉积到反应器壁上。脱焦需要将所述炉子与所述方法分离,然后将蒸汽或者蒸汽/空气混合物流送过该炉盘管。这将硬固体碳层转化成一氧化碳和二氧化碳。一旦这个反应完成,则将所述炉返回投入使用。通过蒸汽裂解所产生的产物取决于进料的组成,烃与蒸汽之比和裂解温度和炉停留时间。轻质烃进料例如乙烷,丙烷,丁烷或者轻质石脑油产生了富含轻质聚合物级烯烃的产物流,包括乙烯,丙烯和丁二烯。重质烃(全馏程和重质石脑油和瓦斯油级分)也产生了富含芳香族烃的产物。为了分离蒸汽裂解所产生的不同的烃化合物,将裂解的气体经历分馏单元。这样的分馏单元是本领域公知的,并且可以包含所谓的汽油分馏器,在这里重质馏出物(“炭黑油”)和中质馏出物(“裂解的馏出物”)与轻质馏出物和气体分离。在随后任选的骤冷塔中,蒸汽裂解所产生的大部分轻质馏出物(“热解汽油”或者”热解气”)可以通过冷凝该轻质馏出物而与气体分离。随后,该气体可以经历多个压缩阶段,其中在该压缩阶段之间其余的轻质馏出物可以与气体分离。同样酸性气体(co2和h2s)可以在压缩阶段之间除去。在随后的步骤中,热解所产生的气体可以在级联的冷冻系统的阶段中部分冷凝到大约其中仅仅氢保留在气态相中。不同的烃化合物可以随后通过简单蒸馏进行分离,其中乙烯,丙烯和c4烯烃是蒸汽裂解所产生的最重要的高价值化学品。蒸汽裂解所产生的甲烷通常用作燃料气体,氢可以分离和再循环到消耗氢的方法,例如加氢裂解方法。蒸汽裂解所产生的乙炔优选选择性加氢成乙烯。裂解气体中所含的烷烃可以再循环到用于烯烃合成的方法。作为此处使用的,术语“丙烷脱氢单元”涉及石化处理单元,其中将丙烷进料流转化成包含丙烯和氢的产物。因此,术语“丁烷脱氢单元”涉及处理单元,用于将丁烷进料流转化成c4烯烃。两者在一起,用于对低级烷烃例如丙烷和丁烷进行脱氢的方法被称作低级烷烃脱氢方法。用于对低级烷烃脱氢的方法是本领域公知的,并且包括氧化性脱氢方法和非氧化性脱氢方法。在氧化性脱氢方法中,工艺热是通过进料中(一种或多种)低级烷烃的部分氧化来提供的。在非氧化性脱氢方法中(其在本发明上下文中是优选的),用于吸热性脱氢反应的工艺热是通过外部热源提供的,例如通过燃料气体燃烧所获得的热烟道气体或者蒸汽。在非氧化性脱氢方法中,该工艺条件通常包含温度540-700℃和绝对压力25-500kpa。例如uopoleflex方法能够在移动床反应器中,在负载于氧化铝上的含铂催化剂存在下将丙烷脱氢来形成丙烯和将(异)丁烷脱氢来形成(异)丁烯(或其混合物);参见例如us4827072。uhdestar方法能够在负载于锌-氧化铝尖晶石上的促进的铂催化剂存在下,将丙烷脱氢来形成丙烯或者将丁烷脱氢来形成丁烯;参见例如us4926005。该star方法最近已经通过应用氧脱氢的原理而得以改进。在反应器的第二绝热区,来自于中间产物的部分氢用所加入的氧选择性转化来形成水。这将热力学平衡位移到更高转化率和实现了更高的收率。同样吸热性脱氢反应所需的外部热是通过放热性氢转化来部分提供的。lummuscatofin方法使用了许多基于循环来运行的固定床反应器。该催化剂是用18-20wt%铬浸渍的活性氧化铝;参见例如ep0192059a1和gb2162082a。catofin方法具有优点,即,它是强力的和能够处理杂质(该杂质将使得铂催化剂中毒)。通过丁烷脱氢方法所生产的产物取决于丁烷进料的性质和所用的丁烷脱氢方法。同样catofin方法能够将丁烷脱氢来形成丁烯;参见例如us7622623。本发明将在下面的实施例中讨论,该实施例不应当解释为限制了保护范围。附图说明唯一的附图提供了本发明实施方案的示意性流程图。具体实施方式实施例将原料33(其可以包括不同类型的原料,例如分别来源于槽2,3,4,5的石脑油35,煤油36,柴油37,常压瓦斯油(ago)38)送到加氢裂解器单元17。在加氢裂解单元17中,原料33是在氢存在下加氢裂解的。该加氢裂解方法导致形成了气态流19,其包含c2-c4链烷烃,氢和甲烷和高含量芳烃流40。将气态流19送到分离器12,例如低温蒸馏或者溶剂提取,并且分离成不同的流,即,包含c2-c4链烷烃的流55,包含氢和甲烷的流20和净化流18。流20可以再循环到加氢裂解单元17。如前所述,流55可以直接送到(未示出)脱氢单元57或者直接送到(未示出)蒸汽裂解器单元11。但是,在将流55送到蒸汽裂解器单元11之前,优选的是首先在流55上进行分离。在分离器56中,将c2-c4链烷烃分离成个体流30,31和32。这意味着流30主要包含c2链烷烃,流31主要包含c3链烷烃并且流32主要包含c4链烷烃。如果需要,则可以在单元9,10,13中进行不想要的组分的进一步的分离或者温度调节。该个体流21,27和29将送到蒸汽裂解器单元11的具体炉区。虽然蒸汽裂解器单元11显示为一个单个单元,但是在本发明的方法中应当理解在优选的实施方案中,蒸汽裂解器单元11包含不同的炉区,每个专门用于具体化学组成,即,用于c2的炉区,用于c3的炉区和用于c4的炉区。在优选的实施方案中,将主要包含c3链烷烃的流27和主要包含c4链烷烃的流29分别作为流54和流23送到脱氢单元57。在另一实施方案中,可以从流55中仅仅分离c3和c4,并且将合并的c3和c4流送到脱氢单元57。在蒸汽裂解器单元11中,处理流21,27和29和原料58,例如来自于单元1的c2-c4气体,并且将它的反应产物28在分离区6中分离。包含c2-c6烷烃的气体流7再循环到蒸汽裂解器单元11。氢15和热解气14可以送到加氢裂解单元17。包含不饱和烃例如轻质烷烃(包括乙烯,丙烯和丁二烯)的有价值的产物流8被送到进一步的石化处理。在重质烃例如炭黑油,裂解的馏出物和c9+烃是在蒸汽裂解器单元11中生产的情况中,这些产物也可以任选地再循环到加氢裂解单元17。将高含量芳烃流40送到分离器16,例如蒸馏方法,并且分离成重质芳烃的流41和高单芳烃的流43。流42(其主要包含c7-c9芳烃)可以在单元24中转化成富含苯的部分59和富含甲烷的级分44。此处所公开的实施例在下面的方法之间是有区别的:其中石脑油仅仅通过蒸汽裂解器单元处理的方法(情况1),和其中将石脑油送到加氢裂解单元的方法(情况2),其中在气态流中,因此形成的c2-c4链烷烃分离并且进料到蒸汽裂解器单元的炉区。情况1是比较例并且情况2是本发明的实施例。用于该蒸汽裂解器的条件如下:乙烷和丙烷炉:盘管出口温度=845℃,蒸汽:油比例=0.37,c4-炉:盘管出口温度=820℃,蒸汽:油比例=0.37,液体炉:盘管出口温度=820℃,蒸汽:油比例=0.37。关于用于加氢裂解单元17的具体条件:进行建模来用于加氢裂解反应器运行条件:平均反应器温度510℃,重时空速是1hr-1和反应器压力1379kpa表压。该催化剂包含负载在γ氧化铝上的pt和hzsm-5(si:al比是100:1)。该石脑油进料的组成可以在见于表1中。表1:作为进料的石脑油的组成对于情况1和情况2的每一者的一组产品组成(进料的wt%)可见于表2中。表2:一组产品组成(进料的wt%)进料:石脑油情况1情况2一组限定产品组成scfhc+sch20.90.5ch417.918.3乙烯35.150.1丙烯19.312.8丁二烯5.32.0异丁烯3.30.3苯9.18.3tx馏分3.47.0苯乙烯0.90.1其他c7-c80.40.0c9树脂进料0.70.0cd1.50.2cbo2.00.3%高价值化学品76.980.5从表2中可以看出根据本发明的方法,在加氢裂解单元中处理石脑油(情况2)导致总btx(苯,甲苯加上二甲苯)增加。因此。表2公开的结果显示了btx从情况1(对比例)到情况2(本发明)的大的增加。分别地,cd表示裂解的馏出物,和cbo表示炭黑油。表2进一步说明了与常规处理手段(情况1)所能够实现的收率相比,当石脑油根据本发明(情况2)处理时,高价值化学品(乙烯+丙烯+丁二烯+异丁烯,苯,tx馏分,苯乙烯和其他c7-c8)的收率是明显较高的。因为在加氢裂解单元(情况2)中,重质链烷烃全部还原成轻质组分例如c2-c4链烷烃,因此通过在加氢裂解单元中预处理石脑油,乙烯的收率从35%增加到50%。因此情况2提供了比情况1明显更高的乙烯收率。表2还显示了通过在加氢裂解单元中预处理石脑油(情况2),降低了重质产物(c9树脂进料,裂解的馏出物和炭黑油)的产生。这意味着根据本发明的方法,不想要的重质副产物的形成可以降低到最小。另一实施例显示了加氢裂解单元的运行温度对于产物组成的影响。该催化剂混合物是2g的zsm-5和2g的氧化铝催化剂载pt的物理混合物,其中0.4-0.8mmsic碎片已经并入到催化剂床中,来确保良好的接近于栓塞流和降低轴向/径向温度差异。烯烃6石脑油被用作原料(参见表3)。表3:原料的组成在这个实施例中,温度在425℃到500℃变化(whsv=1,h:hc=3,200psig)。流出物组成显示在表4中。表4:流出物组成500℃475℃450℃425℃甲烷12.437.454.422.28lpg(c2–c4)72.6678.5080.2978.10正链烷烃(c5+)0.080.240.581.22异链烷烃(c5+)0.020.060.241.03烯烃<0.01<0.01<0.01<0.01环烷烃<0.010.040.430.43芳烃14.8112.239.989.98总共100100100100表4的数据表明较高的温度产生了高的甲烷收率(低价值值副产物)。当前第1页12