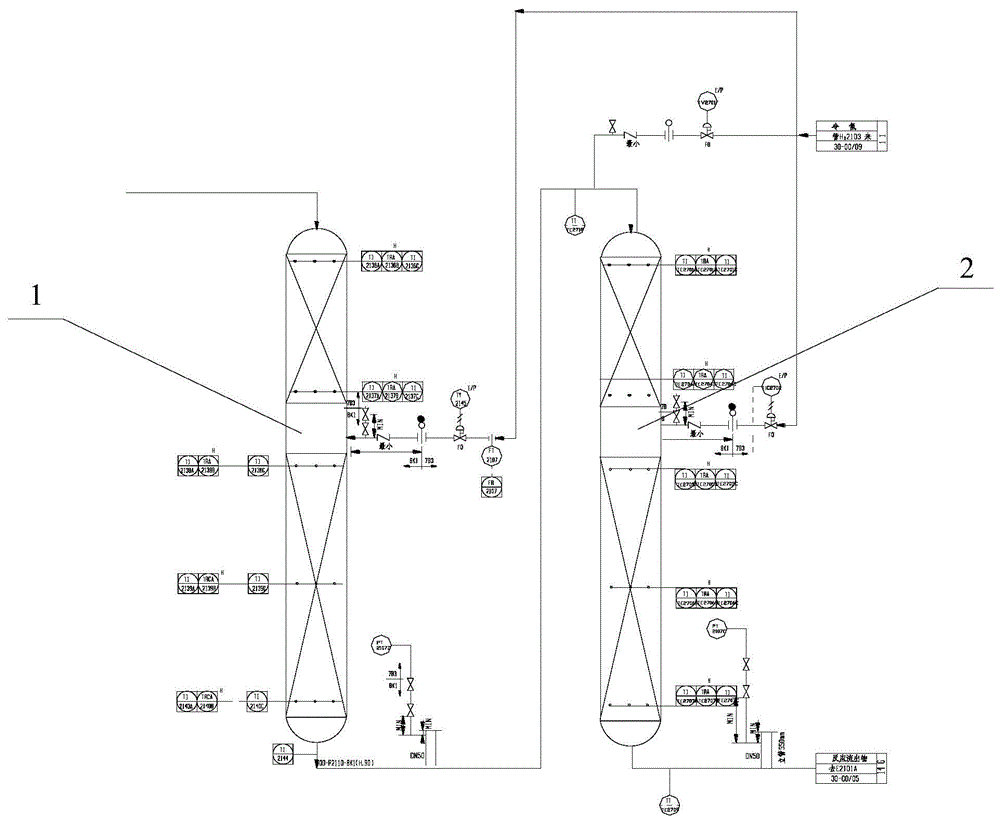
本发明涉及石油生产工艺领域,具体是涉及一种以焦化焦汽、直馏汽油、焦化柴油、直馏柴油、催化柴油的物料为原料,采用加氢精制技术生产的低硫柴油及石脑油的脱硫方法。
背景技术:
:在可持续发展、低碳环保的形势下,为了应对全球气候的变暖,世界各国对生产过程中低碳节能和石油产品(主要指汽柴油)清洁环保的要求也越来越严格。目前美国执行清洁柴油硫含量小于15μg/g的标准。欧盟在2009实施了比美国还要严格的车用燃料油标准,标准要求硫含量低于10μg/g。为了减少机动车尾气造成的环境污染,我国也加快了汽柴油产品质量升级的步伐。北京在2012年开始执行国ⅴ车用汽柴油标准。由此可见,生产超低硫清洁汽柴油将是未来的发展趋势。目前我国炼油企业改善柴油产品质量主要依靠脱硫工艺,应用较为广泛的是加氢脱硫工艺。随着柴油加氢装置运行时间的延长,加氢脱硫催化剂的活性将下降,从而影响产品质量。因此,研究开发新型加氢脱硫催化剂对延长装置的运行周期、提升企业经济效益具有重要作用。柴油成品燃料其中的含硫化合物主要有脂肪族硫化物、硫醚、二苯并噻吩,烷基苯并噻吩和烷基二苯并噻吩等。其中较难脱除的是二苯并噻吩、烷基苯并噻吩和烷基俄苯并噻吩等噻吩类化合物。尤其以有位阻的4,6-二甲基二苯并噻吩(4,6-dmdbt)最难脱除。世界上低硫原油仅占17%,高硫原油比例高达58%、并且这种原油高硫化趋势还将进一步增大。目前人们对低硫柴油的需求不断增长,给炼油厂加工技术带来了较大的压力,需要通过加氢脱硫工艺将柴油中的硫杂质尽可能多地脱除。加氢工艺是应对产品低硫化最有效的途径。烷基取代的反应主要经过两条反应路径:一条是原子直接从噻吩分子中脱除;另一条是一个芳香环先加氢饱和,然后才发生-键的断裂两条反应路线都经过一个共同的部分加氢的中间体这两条反应路径同时进行,至于哪一个占主导地位要看硫化物的性质,反应条件和所用的催化剂等方面的情况。另外,柴油深度和超深度加氢脱硫在反应机理上与常规的加氢脱硫有显著的差异,需要脱除4,6-二甲基二苯并噻吩及2,4,6-三甲基二苯并噻吩类结构复杂且有位阻效应影响的硫化物,这一点也需要在考虑范围内。技术实现要素:发明目的:本发明目的在于针对现有技术的不足,提供一种深度脱硫系统,通过优化加氢反应,实现柴油成品燃料的深度脱硫,提高原料适宜性,提高加氢精制的经济性;本发明的另一目的在于,提供一种利用上述系统进行脱硫的方法。技术方案:本发明所述深度脱硫系统,包括通过管线连通的第一加氢反应器和第二加氢反应器;所述第一加氢反应器和第二加氢反应器均具有两个催化剂床层;其中:第一加氢反应器的上催化剂床层包括密相的脱硫/脱芳催化剂,以及稀相的片状紧压式顶层催化剂、环状脱金属保护剂、环状硅保护剂、四叶草形状的脱金属保护剂和四叶草形状的硅保护剂;第一加氢反应器的下催化剂床层包括密相的脱硫/脱芳催化剂,该层的脱硫/脱芳催化剂与第一加氢反应器的上催化剂床层的脱硫/脱芳催化剂为同一催化剂;第二加氢反应器的上催化剂床层包括密相的脱硫剂;第二加氢反应器的下催化剂床层包括密相的脱硫剂,且该层的脱硫剂与第二加氢反应器的上催化剂床层的脱硫剂为同一催化剂。本发明进一步优选地技术方案为,第二加氢反应器的上催化剂床层和下催化剂床层采用的脱硫剂为高活性镍钼催化剂。作为优选地,所述高活性镍钼催化剂使用前进行硫化处理,在使用状态下其活性组分为硫化态。优选地,所述第一加氢反应器和第二加氢反应器的各催化剂床层均包括有多种不同规格的瓷球,瓷球的装填方式均为稀相。优选地,各催化剂床层包括3mm瓷球、6mm瓷球、13mm瓷球、15mm瓷球和19mm瓷球中的两种或两种以上。优选地,所述第二加氢反应器为单层结构,采用卧式安装形式。一种上述的深度脱硫系统的脱硫方法为,将原料油送入第一加氢反应器内进行加氢精制反应,再经管线将反应后的原料油送入第二加氢反应器进行连续加氢精制反应。。优选地,第一加氢反应器和第二加氢反应器进行加氢精制反应的工艺条件为:反应器入口温度280-320℃,反应压力5.0-8.0mpa,体积空速1.5-4.0h-1,轻油比200-800nm3/m3,可用氢比5.0-8.0,反应系统循环氢循环量30000-60000nm3/h。有益效果:(1)本发明的脱硫系统具有连续设置两个加氢反应器,原料油通过第一加氢反应器加氢精制反应完成后立即进入第二加氢反应器进行连续加氢精制,配合本发明不同的催化剂选择,实现深度脱硫,使得产品指标得到很大改善,最终产品硫含量<10ppm,产品指标优,经济效益好;(2)本发明的催化剂床层的搭配可以在一定程度上弥补催化剂的选择条件苛刻的缺陷,对原料性质的要求大幅度降低,使得原料配比可在大范围内进行调整,而原料配比实现可以根据原料库存及社会需求随时调整原料配比,能够极大的提高生产装置的生产适应能力和应变能力,有利于提高经济效益。附图说明图1为本发明的深度脱硫系统的结构示意图。具体实施方式下面通过附图对本发明技术方案进行详细说明,但是本发明的保护范围不局限于所述实施例。实施例:一种深度脱硫系统,包括通过管线连通的第一加氢反应器1和第二加氢反应器2。所述第一加氢反应器1和第二加氢反应器2均具有两个催化剂床层;其中:第一加氢反应器1的上催化剂床层包括密相的脱硫/脱芳催化剂tk-568,以及稀相的片状紧压式顶层催化剂tk-10、环状脱金属保护剂tk-711、环状硅保护剂tk-437、四叶草形状的脱金属保护剂tk-743、四叶草形状的硅保护剂tk-437、3mm瓷球、6mm瓷球和13mm瓷球。第一加氢反应器1的下催化剂床层包括密相的脱硫/脱芳催化剂tk-568,以及稀相的3mm瓷球、6mm瓷球、13mm瓷球和15mm瓷球。第二加氢反应器2的上催化剂床层包括密相的高活性镍钼催化剂tk-609,以及稀相的3mm瓷球、6mm瓷球和19mm瓷球第二加氢反应器2为单层结构,采用卧式安装形式。第二加氢反应器2的下催化剂床层包括密相的高活性镍钼催化剂tk-609,以及稀相的3mm瓷球、6mm瓷球、13mm瓷球和19mm瓷球。第二加氢反应器2内tk-609为贵金属催化剂,使用前先进行硫化处理,在使用状态下其活性组分为硫化态。各催化剂床层的具体安装配比如表1所示:上述系统具体的脱硫方法为:将原料油送入第一加氢反应器内进行加氢精制反应,再经管线将反应后的原料油送入第二加氢反应器进行连续加氢精制反应。第一加氢反应器和第二加氢反应器进行加氢精制反应的工艺条件为:反应器入口温度280-320℃,反应压力5.0-8.0mpa,体积空速1.5-4.0h-1,轻油比200-800nm3/m3,可用氢比5.0-8.0,反应系统循环氢循环量30000-60000nm3/h。对比例:作为本发明实施例的对比,选择目前市场常见的单加氢反应器。其结构和催化层与本申请第一加氢反应器类似,上催化剂床层包括密相的脱硫/脱芳催化剂tk-568,以及稀相的片状紧压式顶层催化剂tk-10、环状脱金属保护剂tk-711、环状硅保护剂tk-437、四叶草形状的脱金属保护剂tk-743、四叶草形状的硅保护剂tk-437、3mm瓷球、6mm瓷球和13mm瓷球。下催化剂床层包括密相的脱硫/脱芳催化剂tk-568,以及稀相的3mm瓷球、6mm瓷球、13mm瓷球和15mm瓷球。本申请的实施例与对比例处理相同的原料油。原料油中各种类原油的性质如表2所示:原料油的各种类原油的配比如表3所示:实施例与对比例的操作工艺操作条件对比如表4所示:对比例实施例反应器入口温度℃300280反应器出口温度℃370362系统压力mpa6.56.0氢油比500400原料油s含量%0.420.42反应器平均温度℃360352原料油进脱硫反应后,最终产品的指标对比如表5所示:通过以上对比,可以发现本发明的系统和工艺降低了加氢反应所需要的反应温度,降低了燃料气的消耗,同时产品指标柴油硫含量得到明显的降低,甚至获得超低硫含量,市场竞争力明显。本实施例中,tk-568、tk-10、tk-711、tk-437、tk-743和tk-609均为haldortopsoe公司市售产品。如上所述,尽管参照特定的优选实施例已经表示和表述了本发明,但其不得解释为对本发明自身的限制。在不脱离所附权利要求定义的本发明的精神和范围前提下,可对其在形式上和细节上作出各种变化。当前第1页12