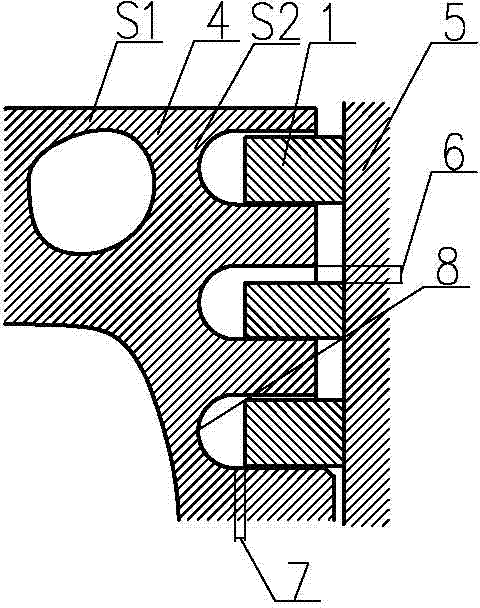
本发明涉及一种内燃机,具体地说是一种内燃机活塞环及生产方法和活塞环组件,特别是涉及一种具有钨钴合金和碳化铬涂层的内燃机活塞环及生产方法和活塞环组件。
背景技术:
:内燃机活塞的主要作用是承受汽缸中的燃烧压力,并将此力通过活塞销和连杆传给曲轴,从而完成预定的工作。在活塞头部加工有多道安装活塞环的环槽,其作用防止高温、高压燃气从燃烧室窜入曲轴箱,同时阻止机油窜入燃烧室。活塞环数量取决于密封的要求,一般采用2~4道气环、1道油环,其中远离燃烧室端的活塞环为油环,其他的活塞环为气环。活塞环在高温、高压、动载、化学腐蚀环境中工作,是发动机易损件,因此人们一直研究提高活塞环使用寿命的方法。最新的研究成果表明,通过对活塞环表面热处理或加涂层的方法,可以增加活塞环的耐磨性,涂层材料一般为氮化铬或碳化钨。但氮化铬或碳化钨耐磨性能仍有待提高,且涂层在重载时会出现微裂纹,造成活塞环的失效。如申请号为200910182353.7的专利公开了一种有复合涂层的内燃机活塞环,涂层厚度为5~30μm,硬度为hv800~1600,涂层为镍基复合物、金属氮化物、金属碳化物或陶瓷复合物。又如申请号为201280051055.4的专利公布了一种涂有碳化钨和碳化铬的活塞环,碳化钨粒度为0.15~0.45μm,含有金属镍的喷涂层,镍的重量比为12.5﹪,碳化铬的重量比为37.5﹪,提高了活塞的耐磨性。再如申请号为cn201410820218.1的专利公布了一种强化涂层硬度、提高活塞表面涂层性能的方法,用镍钴硫化钨纳米晶合金对表面进行电镀。从以上现有技术文献可以看出,碳化钨/碳化铬/氮化铬等涂层已广泛应用于内燃机活塞环的外涂层中,以便提高其耐磨性和承载能力。但是,在高速内燃机(转速大于1000rpm)或重型内燃机(功率大于300马力)中,人们发现涂层强度和承载能力不够,造成磨损加剧,并产生微裂纹,微裂纹一直发展,直到涂层开始剥离活塞环基体(称为起鳞),而造成活塞环的破坏。由于涂层剥离形成的坚硬杂质物会在内燃机内部(随润滑油一起)移动,因此可能造成活塞环的严重磨损,甚至造成内燃机的严重事故。技术实现要素:本发明的目的是提供一种具有钨钴合金和碳化铬涂层的内燃机活塞环及生产方法和活塞环组件。活塞环的装配端隙即活塞环装到气缸内后,在开口处呈现的间隙,以防活塞环受热膨胀后卡死。一般为0.29~0.49㎜,油环为0.50~1.0㎜。活塞环的装配侧隙(边隙)指活塞环在环槽内的上下间隙;侧隙过大会影响活塞的密封作用,侧隙过小活塞环会卡死在环槽内;一般第一道气环的侧隙为0.05~0.11㎜,其余两道气环及油环均为0.03~0.09㎜。活塞环的装配背隙是指活塞装入气缸后活塞环背面与活塞环槽直边底部之间的间隙,一般用槽深与环厚之差来表示,一般在0~0.75㎜范围,是活塞环在工作时靠燃烧时的高压气体进入背隙对活塞环产生压力,来加强活塞环与气缸工作面的密封作用。本发明是采用如下技术方案实现其发明目的的,一种内燃机活塞环,它包括由金属材料制成的基体,所述基体与缸体接触部表面设有耐磨涂层,耐磨涂层材料为钨钴合金和碳化铬的组合;以重量百分比计,钨钴合金的重量比为60﹪~80﹪,碳化铬的重量比为20﹪~40﹪,各组分之和为100﹪,其中钴元素为总组分的25﹪~45﹪。为提高基体与耐磨涂层之间的结合力和耐磨涂层的承载能力,本发明基体与耐磨涂层之间设有硬化涂层,所述硬化涂层的厚度为5μm~25μm,硬化涂层的孔隙度小于6﹪。本发明所述钨钴合金中的钨可为铑或铪或钽或钛或锆或钼或铌或铱中的一种或多种。本发明所述耐磨涂层的晶状结构为柱状晶体结构,是钨钴合金和碳化铬的组合晶相。本发明所述耐磨涂层的厚度为10μm~50μm,耐磨涂层的孔隙度为3﹪~12﹪,耐磨涂层的硬度为维氏1850~2350。一种如上所述的内燃机活塞环生产方法,所述耐磨涂层是将钨钴合金和碳化铬采用物理气相沉积方法沉积到活塞环基体与缸体接触部表面。一种如上所述的内燃机活塞环生产方法,所述硬化涂层是对活塞环基体与缸体接触部表面进行渗碳处理。为降低活塞头部和环槽底部的应力集中,一种采用如上所述的内燃机活塞环的活塞环组件,它包括安装在活塞头部的活塞环,活塞头部至少设有用于安装活塞环的三道环槽,与燃烧室相邻的第二道活塞环的装配侧隙为0.15㎜~0.65㎜。本发明第二道活塞环的装配侧隙优选为0.35㎜~0.65㎜,结合活塞环槽部的高度设计,最优为0.35㎜~0.45㎜。为进一步降低环槽底部的应力集中,本发明所述环槽底部为圆弧底形状。由于采用上述技术方案,本发明较好的实现了发明目的,活塞环耐磨涂层中加入金属钴后,其涂层的硬度、耐磨性能和承载能力都有了很大程度的提高,经试验,与传统的碳化钨/碳化铬涂层比较,活塞环硬度提高了45.4﹪~73.1﹪,耐磨性提高了26.5﹪~61.8﹪,承载能力提升也提高了19.7﹪~78.5﹪;同时,在活塞组件中增加第二道活塞环的装配侧隙,且环槽底部改为圆弧底,也降低了活塞头部和环槽底部的应力集中。附图说明图1是本发明活塞环的涂层结构示意图;图2是本发明活塞组件的结构示意图;图3是本发明第二环槽在燃烧负载下变形后的示意图。具体实施方式下面结合附图及实施例对本发明作进一步说明。实施例1:由图1可知,一种内燃机活塞环,它包括由金属材料制成的基体1,所述基体1与缸体5接触部表面设有耐磨涂层2,耐磨涂层2材料为钨钴合金和碳化铬的组合;以重量百分比计,钨钴合金的重量比为60﹪~80﹪,碳化铬的重量比为20﹪~40﹪,各组分之和为100﹪,其中钴元素为总组分的25﹪~45﹪。为提高基体1与耐磨涂层2之间的结合力和耐磨涂层2的承载能力,本发明基体1与耐磨涂层2之间设有硬化涂层3,所述硬化涂层3的厚度为5μm~25μm,硬化涂层3的孔隙度小于6﹪。本发明所述钨钴合金中的钨可为铑或铪或钽或钛或锆或钼或铌或铱中的一种或多种。本发明所述耐磨涂层2的晶状结构为柱状晶体结构,是钨钴合金和碳化铬的组合晶相。本发明所述耐磨涂层2的厚度为10μm~50μm,耐磨涂层2的孔隙度为3﹪~12﹪,耐磨涂层2的硬度为维氏1850~2350。一种如上所述的内燃机活塞环生产方法,所述耐磨涂层2是将钨钴合金和碳化铬采用物理气相沉积方法沉积到活塞环基体1与缸体5接触部表面。一种如上所述的内燃机活塞环生产方法,所述硬化涂层3是对活塞环基体1与缸体5接触部表面进行渗碳处理。由图2可知,为降低活塞4头部区域(即s1区域)和第一环槽底部区域(即s2区域)的应力集中,一种采用如上所述的内燃机活塞环的活塞环组件,它包括安装在活塞4头部的活塞环,活塞4头部至少设有用于安装活塞环的三道环槽,与燃烧室相邻的第二道活塞环的装配侧隙6为0.15㎜~0.65㎜。为进一步降低环槽底部8区域的应力集中,本发明所述环槽底部8为圆弧底形状。本发明活塞环的装配背隙7为0.00㎜~0.15㎜。本实施例活塞环的基体1为金属合金,如铸铁、不锈钢、硬质铝合金材料等。为减少活塞环与缸体5接触面积,便于提高表面涂层质量,降低表面处理成本,活塞环设计成锥形轴状。这样,可以减少贵金属消耗,降低了活塞环的制造成本。同时,也降低了活塞环的质量,从而降低了活塞的惯性力,有利于提高活塞组件的使用寿命。首先对活塞基体1与缸体5接触部表面进行渗碳处理,形成一个热处理硬化涂层3。硬化涂层3的厚度为10μm,孔隙度为6﹪。为提高活塞环与缸体5接触部表面的机械性能,采用物理气相沉积工艺(pvd)将钨钴合金(wc-co)和碳化铬(cr3c2)沉积到硬化涂层3上,形成一个耐磨涂层2。耐磨涂层2的晶状结构为柱状晶体结构,是钨钴合金和碳化铬的组合晶相,耐磨涂层2的厚度为18μm,耐磨涂层2的孔隙度为6﹪。本实施例在活塞环基体1上采用不同含量钴元素的钨钴合金(wc-co)和碳化铬((cr3c2)制备耐磨涂层2并与采用碳化钨/碳化铬(wc/cr3c2)制备的耐磨层进行了对比试验。试验方法:以铸铁为基材制做活塞环基体1,大小为40×20×20㎜的长方体,对长方体的一个40×20㎜的表面先进行渗碳处理,形成硬化涂层3,然后,采用物理气相沉积方法在硬化涂层3制备耐磨涂层2,耐磨涂层2中钴合金(wc-co)为70﹪,碳化铬(cr3c2)为30﹪,其中钴元素的重量比分别取25﹪、30﹪、35﹪,40﹪,45﹪。同样,为进行对比试验,按现有技术也制作了试件,即在相同大小的铸铁活塞环基体1上先进行渗碳处理,形成硬化涂层3,然后,采用物理气相沉积方法在硬化涂层3制备耐磨涂层2,耐磨涂层2采用wc/cr3c2混合物,其中碳化钨(wc)的重量百分比为48﹪,碳化铬(cr3c2)的重量百分比为52﹪,耐磨层的厚度为18μm,耐磨层的孔隙度为6﹪。本实施例使用维氏硬度计测量试件耐磨涂层2的表面硬度。试验条件:压力98n(10千克),方锥形金刚石相对面夹角为136°,保持时间10s,检验压痕并计算耐磨涂层2表面的维氏硬度。本实施例在旋转试验台上对上述试件进行磨损试验,试验条件为:压力100千克,转速500rpm,试验时长6小时,测量耐磨涂层2的磨损情况。本实施例耐磨涂层2的承载能力试验。试验条件:用一定压力将金刚石球型刀头压在试件表面上,球型刀头为rockwellc型,刀具角度为120º,刀头半径120μm,刀具与试件相对速度为5㎜/min,压力从100n开始,每次增加1n,试验时间1分钟。用超声波检验试件表面是否出现裂纹。一旦出现裂纹,即认为耐磨涂层2被破坏了,此时的压力即为耐磨涂层2的承载能力。试验结果如表1所示。表1:从表1可知,在活塞环的耐磨涂层2中加入金属钴后,耐磨涂层2的表面硬度、抗磨损能力和承载能力都有了较大的提高。当钴含量较低时,随着钴元素重量比的增加,耐磨涂层2的硬度、耐磨损能力和承载能力都增加,到达一个峰值(钴的重量比为40﹪左右)后,随着钴元素重量比的增加,耐磨涂层2的硬度、耐磨损能力和承载能力反而会下降。这是因为从理论上说,在钨钴铬涂层中,钴能将碳化钨和铬碳化物晶粒结合在一起,使晶体结构更致密,在不增加表面材料的内应力的情况下,提高了耐磨涂层2的密度和韧性,因而提高了耐磨涂层2表面抗裂纹生成能力和承载能力。但钴含量过大时,降低了钨和铬的含量,因此,耐磨涂层的性能反而下降了。试验结果表明,采用wc/cr3c2材料的涂层硬度为hv1300,涂层的磨损量为3.4μm,涂层的承载能力为223n;采用wc-co/cr3c2材料的耐磨涂层2硬度为hv1890~2250,耐磨涂层2的磨损量为1.3μm~2.5μm,耐磨涂层2的承载能力为267n~398n。也就是说硬度提高了45.4﹪~73.1﹪,耐磨性提高了26.5﹪~61.8﹪,承载能力提升也提高了19.7﹪~78.5﹪。理论和实验分析表明,在活塞4的s1、s2区域(如图2所示)会产生比较大的应力集中。发明人利用unigraphics软件建立活塞组件的三维数值模型,利用anasys软件进行活塞组件的网格划分和数值计算工作。计算结果表明:一是活塞环的装配背隙7越大,应力集中越大。二是活塞环的装配侧隙6越大,应力集中则越小。三是环槽底部8的过渡圆角越小,环槽底部8区域应力集中越明显。四是各环岸高度(即环槽之间的距离或间隔)越大,应力集中越低。因此,增加活塞环装配侧隙6、增加环岸高度有利于降低应力集中,但是,增加环岸高度,会增加活塞头部裂纹总量,同时,也增加了活塞质量,因此是不可取的。增加活塞环装配侧隙6,会导致该处密封性能的下降。但在内燃机中,第一道活塞环为防火主环,第三道活塞环为防油主环,第二道活塞环起辅助防火和防油的作用,因此,适当增加其装配侧隙是可行的。根据有限元分析结果,为降低活塞4的s1、s2区域的应力,发明人提出以下技术方案:一是将与燃烧室相邻的第二道活塞环的装配侧隙6设计为0.15㎜~0.55㎜,使活塞4头部能接受一定的弹性变形;这是因为,在内燃机中,第一道活塞环(气环)为防火主环,第三道环(油环)为防油主环,第二道环起辅助防火和防油的作用。增加与燃烧室相邻的第一道活塞环的装配侧隙6,有可能造成燃烧室中的高温高压气体窜入曲轴箱,增加最后一道活塞环的装配侧隙,则会有可能增加内燃机润滑油的损耗;因此,为保证密封性能,不能增加第一道活塞环和第三道活塞环的装配侧隙;但第二道活塞环是起辅助密封作用,因此,适当增加其装配侧隙是可行的。二是将环槽底部8设计为圆弧底形状,同时,尽可能减小活塞环的装配背隙,活塞环的装配背隙设计为0.00㎜~0.15㎜,远低于现有技术的0.5㎜~1.0㎜,以有效降低活塞头部区域内的热应力和机械应力的耦合总应力。本实施例为验证有限元分析的有效性,发明人将按现有技术制造的活塞组件在发动机台架试验进行测试。相关参数为:第一道活塞环(气环)的装配侧隙为0.07㎜,第二道活塞环(气环)的装配侧隙为0.06㎜,第三道活塞环(油环)的装配侧隙为0.05㎜,活塞环的装配背隙均为0.6㎜~0.75㎜;第一道环槽至第二道环槽之间的高度(第一环岸高度)为3.5㎜,第二道环槽至第三道环槽之间的高度(第二环岸高度)为3.25㎜。试验结果测得活塞4的s1、s2区域的最大应力分别为85.3mpa和78.1mpa。而按有限元方法计算得到的最大应力分别为83.6mpa和76.7mpa,误差分别为2.00﹪和1.80﹪。因此,发明人认为,有限元方法计算得到的结果是有效的。因此,发明人利用anasys软件对现有技术制造的活塞组件与本实施例的活塞组件采用有限元方法对活塞4的s1、s2区域分别进行了应力变形数值计算。本实施例的第一道活塞环(气环)的装配侧隙为0.07㎜,第三道活塞环(油环)的装配侧隙为0.05㎜,第二道活塞环(气环)的装配侧隙分别为0.15、0.25、0.35、0.45、0.55、0.65㎜,第二环岸高度分别为3.25㎜、4.25㎜;为进行对比分析,现有技术的活塞第一道活塞环(气环)的装配侧隙为0.07㎜,第二道活塞环(气环)的装配侧隙为0.06㎜,第三道活塞环(油环)的装配侧隙为0.05㎜,装配背隙均为0.65㎜,第二环岸高度分别为3.25㎜、4.25㎜。计算结果如表2、表3所示。表2:(第二环岸高度为3.25㎜)序号环槽底部形状第二活塞环装配侧隙(㎜)s1区域最大应力(mpa)s2区域最大应力(mpa)第二环槽槽口变形(㎜)1圆弧底0.1572.664.20.152圆弧底0.2569.262.70.253圆弧底0.3566.560.90.354圆弧底0.4565.660.30.455圆弧底0.5564.959.90.516圆弧底0.6564.759.70.517圆弧底0.0679.965.80.068平底0.0683.676.70.06表3:(第二环岸高度为4.25㎜)序号环槽底部形状第二活塞环装配侧隙(㎜)s1区域最大应力(mpa)s2区域最大应力(mpa)第二环槽槽口变形(㎜)1圆弧底0.1566.758.50.152圆弧底0.2563.656.10.253圆弧底0.3559.853.60.354圆弧底0.4558.652.90.455圆弧底0.5558.352.60.486圆弧底0.6558.152.40.487圆弧底0.0672.960.10.068平底0.0675.366.80.06由表2可知,在第二环岸高度为3.25㎜时,本实施例在增加第二道活塞环装配侧隙6的情况下,s1区域的最大应力降低幅度为13.16﹪~22.61﹪,s2区域的最大应力降低幅度为16.30﹪~22.16﹪。由表3可知,在第二环岸高度为4.25㎜时,本实施例在增加第二道活塞环装配侧隙6的情况下,s1区域的最大应力降低幅度为11.42﹪~22.84﹪,s2区域的最大应力降低幅度为12.43﹪~21.56﹪。由计算结果分析可知,第二道活塞环装配侧隙6优选为0.35㎜~0.65㎜;综合考虑应力集中降低程度和活塞环的密封性能,第二道活塞环装配侧隙最优为0.35㎜~0.45㎜。由表2、表3可知,在活塞环装配侧隙6不变的条件下,仅将活塞环槽底采用圆弧底结构时,s1区域的应力最大值分别下降4.43﹪(第二环岸高度为3.25㎜)和3.19﹪(第二环岸高度为4.25㎜);s2区域的应力最大值分别下降14.21﹪(第二环岸高度为3.25㎜)和10.03﹪(第二环岸高度为4.25㎜)。因此,将活塞环槽底部8改为圆弧底形状,能有效地改善活塞冠部区域的应力分布。由表2、表3可知,增加第二环岸高度(由3.25㎜增加至4.25㎜),也可以减少s1区域、s2区域内的应力集中。对现有技术制造的活塞组件,s1区域应力最大值减少9.93﹪,s2区域内应力最大值减少12.80﹪。对本实施例,s1区域应力最大值减少8.09﹪~10.67﹪,s2区域内应力最大值减少8.87﹪~12.27﹪。本发明在活塞环耐磨涂层中加入金属钴后,其涂层的硬度、耐磨性能和承载能力都有了很大程度的提高,经试验,与传统的碳化钨/碳化铬涂层比较,活塞环硬度提高了45.4﹪~73.1﹪,耐磨性提高了26.5﹪~61.8﹪,承载能力提升也提高了19.7﹪~78.5﹪;且增加第二道活塞环的装配侧隙6,环槽底部8改为圆弧底,也大大降低了活塞4头部和环槽底部8的应力集中;同时,增加第二道活塞环装配侧隙,当内燃机工作时,由于第二环槽槽口的变形将相应减少装配侧隙(如图3所示),对第二活塞环的密封性能影响较小。当前第1页12