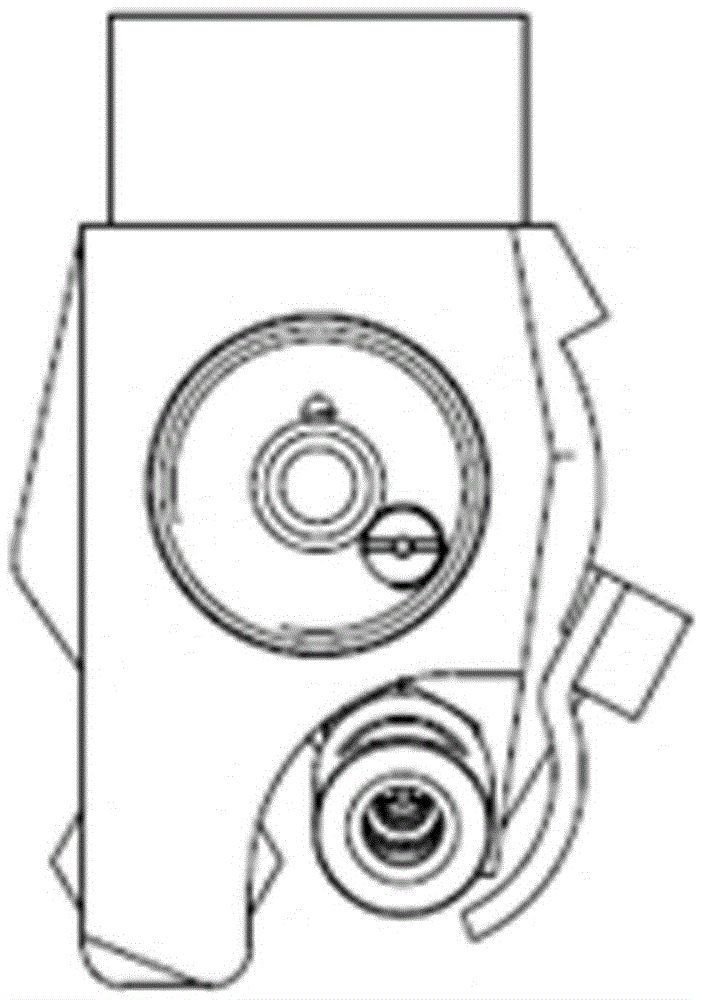
本发明属于机械领域的储气容器充气供气控制元件,具体涉及一种多功能集成阀。
背景技术:应用在航空、航天领域中的气体元器件,不仅对气体元器件的耐候性、可靠性有苛刻要求,而且对气体元器件的体积、重量有严格限制。但现有的用于实现储气容器的充气阀和供气阀大多采用各功能部件分体实现,整体集成化程度较低,使得整个气源系统体积庞大,过多的占用有限的空间资源。在公开号为CN101418910A的中国发明专利申请中公开了一种一体式瓶阀,该瓶阀包括阀体,阀体上具有用于与适配的气瓶连通的充气口及供气口,阀体中设有与充气口连通的充气支路,充气支路的一端与充气口连通、另一端则与阀体上设有的充气接口连通,在充气支路上设有充气单向阀,阀体中还设有与供气口连通的供气支路,供气支路的一端与供气口连通、另一端则与阀体上设有供气接口连通,在供气支路上分别设有减压阀及用于控制供气支路通断的电磁阀。充气时,电磁阀关闭,供气支路断开,将充气接头与外部高压气源连通,高压气体冲开充气单向阀对气瓶进行充气。供气时,将外部用气设备与供气接口连通,电磁阀打开,气瓶中的高压气体经供气支路排出,实现对外部用气设备的供气。但上述瓶阀的集成度不高,在其上分别设置有不同的充气接口和进气接口,在阀体上设有单独的充气支路和供气支路,这样就使得整个瓶阀体积较大,占用空间较大,不适合应用在安装空间有限的场所。
技术实现要素:本发明的目的是提供一种具有充气和供气功能的集成化程度高的多功能集成阀。为实现上述目的,本发明所提供的多功能集成阀的技术方案是:一种多功能集成阀,包括阀体,阀体上设有用于与储气容器连通的充气口和供气口,所述的阀体上设有用于在由外界气源向储气容器进行充气时作为进气口与外界气源连通及在由储气容器向外供气时作为出气口的通断接头,阀体内部设有与通断接头连通的总气路及连通总气路与所述充气口的充气支路和连通总气路与所述供气口的供气支路,充气支路上设有用于控制充气支路通断的充气控制阀,供气支路上设有用于控制供气支路通断的供气控制阀。所述的阀体上还设有用于与外界大气连通的排空口及排空支路,排空支路一端与所述排空口连通、另一端连通于所述总气路上或连通于总气路与充气控制阀之间的充气支路上或连通于总气路与供气控制阀之间的供气支路上,在排空支路上设有用于控制排空支路通断的排空控制阀。所述的通断接头为常闭接头,所述充气控制阀为使高压气路由总气路流向充气口并防止回流的充气单向阀,所述阀体上还设有用于控制供气控制阀和排空控制阀交替打开、关闭以使集成阀在充气或供气状态与排空状态进行切换的切换装置。所述的供气支路上于所述供气控制阀及所述供气口之间串接有使高压气体由供气口流向总气路并防止回流的供气单向阀,在阀体中还设有测压气路,测压气路的一端连通于供气控制阀与供气单向阀之间的供气支路上、另一端连通有压力表。所述的供气控制阀及排空控制阀均为手动机械控制阀,供气控制阀及排空控制阀中分别设有密封阀芯、传动阀杆及驱动密封阀芯复位进行密封的复位弹簧,所述切换装置包括转动装配在所述阀体上以控制所述供气控制阀及排空控制阀交替打开的手动凸轮,手动凸轮的转动中心线与所述复位弹簧的伸缩方向平行,将手动凸轮的转动中心线的延伸方向定义为上下方向,所述供气控制阀及排空控制阀的密封阀芯位于所述手动凸轮下方,手动凸轮具有沿上下方向延伸的用于与所述供气控制阀及排空控制阀的传动阀杆顶压配合的顶压斜面,顶压斜面具有位于下部的与相应传动阀杆顶压时克服复位弹簧作用力以驱动相应密封阀芯打开的打开顶压部和位于上部的与相应传动阀杆顶压时由对应复位弹簧驱动相应密封阀芯关闭的关闭顶压部,所述手动凸轮在转动过程中具有用于实现充气或供气状态与排空状态进行切换的第一、二工作位,手动凸轮在第一工作位时由顶压斜面的打开顶压部与供气控制阀的传动阀杆顶压以打开供气控制阀且排空控制阀的传动阀杆顶压在顶压斜面的关闭顶压部以控制排空控制阀关闭,手动凸轮在第二工作位时由顶压斜面的打开顶压部与排空控制阀的传动阀杆顶压以打开排空控制阀且供气控制阀的传动阀杆顶压在顶压斜面的关闭顶压部以控制供气控制阀关闭。所述的供气控制阀和排空控制阀均为用于防止高压回流的单向阀。所述的阀体上设有用于与储气容器连通的卸荷进气口和用于与外界大气连通的卸荷排气口,阀体内部设有两端分别与卸荷进气口及卸荷排气口连通的用于排空储气容器以使其紧急卸荷的卸荷气路,卸荷气路上设有用于控制卸荷气路通断的卸荷控制阀。本发明的有益之处是:本发明所提供的多功能集成阀的阀体上设置通断接头,且该通断接头通过总气路分别与供气支路及充气支路连通,具体使用时,外界气源可通过通断接头、总气路与充气支路连通,进而向安装有该集成阀的储气容器进行充气操作,而在需要由安装有该集成阀的储气气瓶向外供气时,将需要使用高压气体的器件与通断接头连通,储气容器通过供气支路、总气路向外供气,这样可以仅通过单个通断接头实现充气、供气操作,使得整个集成阀体积较小、集成化程度高。进一步的,通断接头为常闭接头,这样,为减小总气路中高压气体对各控制阀的影响,在阀体上还设置排空支路,这样可以在不需要进行充气、供气操作时,可以将总气路中的高压气体排空,进而延长集成阀使用寿命,提高集成阀安全性。进一步的,充气控制阀为充气单向阀,通过切换装置控制供气控制阀和排空控制阀交替打开、关闭,这样可以方便对集成阀处于充气或供气状态与排空状态之间进行切换。进一步的,切换装置采用手动凸轮来控制供气控制阀和排空控制阀的切换打开、关闭,控制可靠,操作简单方便。进一步的,在供气支路上设置测压气路,可以对供气支路中的高压气体的气压进行实时监控,保证向外供气的效果,同时,在供气控制阀被打开,同时整个集成阀处于充气状态时,由于供气支路上设置供气单向阀,供气单向阀此时关闭,测压气路可以对总气路及充气支路中的高压气体的气压进行实时监控,保证充气效果。进一步的,阀体上还设置有卸荷气路,以提高使用集成阀的储气容器的安全性。附图说明图1是本发明所提供的多功能集成阀的一种实施例的结构示意图;图2是图1中K向视图;图3是图1中A-A剖视图;图4是图1中B-B剖视图;图5是图1中C-C剖视图;图6是图1的俯视图;图7是图6中D-D剖视图(去除切换装置);图8是图6中E-E剖视图(去除切换装置);图9是图1所示多功能集成阀中的气路原理图。具体实施方式如图1至图9所示,一种多功能集成阀的实施例,该实施例中的集成阀包括沿竖向延伸的阀体1,阀体1的上部设有用于在由外界气源向储气容器进行充气时作为进气口与外界气源连通及在由储气容器向外供气时作为出气口的通断接头,具体使用时,可采用高压气瓶作为用于与集成阀适配的储气容器。该通断接头为常闭接头28,在阀体上设于与阀体内部的总气路27连通的螺旋安装孔,常闭接头28螺旋装配在该螺旋安装孔中,常闭接头28与阀体1的连接处布置有密封垫36以保证连接处的气密性,且在密封垫36和常闭接头28之间布置有用于防止大颗粒杂质进入集成阀中的滤网35。具体来说,在阀体1的内部具有与常闭接头29连通的总气路27,相应的,在阀体1上还设有用于与适配的储气容器连通的充气口37和供气口11,在阀体1中设有连通总气路27与所述充气口37的充气支路26及连通总气路27与所述供气口11的供气支路15。在充气支路26设有控制充气支路26通断的充气控制阀,该充气控制阀具体为使高压气体由常闭接头28经总气路27流向充气口37并防止回流的充气单向阀25。在供气支路15上设有用于控制供气支路通断的供气控制阀24,另外,在供气支路15上于所述供气控制阀24及所述供气口11之间串接有使高压气体由供气口11流向总气路27并防止回流的供气单向阀34。因为通断接头采用常闭接头,为防止总气路中高压气体对各控制阀的影响,在阀体1上还设有用于与外界大气连通的排空口,阀体1中设有与排空口连通以用于将总气路27中的高压气排空的排空支路19,排空支路19的一端与排空口连通、另一端连通在总气路27与充气单向阀25之间的充气支路26上,排空支路19上设有用于控制排空支路通断的排空控制阀21,该排空控制阀21为可受控打开以实现双向导通的单向阀,排空支路19上的排空口处设有使排空支路19内的高压气体排出并防止外部大气经排空支路进入阀体内部的单向阀20。为便于将集成阀对应安装在储气容器的高压气瓶上,将充气口11设置在供气口37的一侧,此处的供气口位于充气口的下方,当将阀体安装在高压气瓶上时,供气口延伸入高压气瓶内部,进而可以提高向外供气效率。此处的排空控制阀21和供气控制阀24均为设在阀体1的顶部的单向阀,且为便于对排空控制阀及供气控制阀的打开、关闭状态进行切换,供气控制阀24位于排空控制阀21的一侧,阀体1上还设有用于控制供气控制阀24和排空控制阀21交替打开、关闭以使集成阀在充气或供气状态与排空状态进行切换的切换装置,本实施例中的供气控制阀24及排空控制阀21均为手动机械控制阀,供气控制阀24及排空控制阀21中分别设有密封阀芯、传动阀杆及驱动密封阀芯复位进行密封的复位弹簧,切换装置包括转动装配在所述阀体上以控制所述供气控制阀及排空控制阀交替打开的手动凸轮31,手动凸轮31的转动中心线与所述复位弹簧的伸缩方向平行,将手动凸轮31的转动中心线的延伸方向定义为上下方向,所述供气控制阀24及排空控制阀21的密封阀芯位于所述手动凸轮31下方,手动凸轮31具有沿上下方向延伸的用于与所述供气控制阀24及排空控制阀21的传动阀杆顶压配合的顶压斜面,顶压斜面具有位于下部的与相应传动阀杆顶压时克服复位弹簧作用力以驱动相应密封阀芯打开的打开顶压部和位于上部的与相应传动阀杆顶压时由对应复位弹簧驱动相应密封阀芯关闭的关闭顶压部,所述手动凸轮在转动过程中具有用于实现充气或供气状态与排空状态进行切换的第一、二工作位,两工作位分别对应手动凸轮上的ON及OFF位置,手动凸轮在第一工作位时由顶压斜面的打开顶压部与供气控制阀的传动阀杆顶压以打开供气控制阀且排空控制阀的传动阀杆顶压在顶压斜面的关闭顶压部以控制排空控制阀关闭,手动凸轮在第二工作位时由顶压斜面的打开顶压部与排空控制阀的传动阀杆顶压以打开排空控制阀且供气控制阀的传动阀杆顶压在顶压斜面的关闭顶压部以控制供气控制阀关闭。本实施例中的手动凸轮可通过转动手柄32驱动转动。为监控充气压力和高压气瓶2的供气压力,在阀体1内部还设有测压气路22,测压气路22的一端连通于供气控制阀24与供气单向阀34之间的供气支路15上、另一端连通有压力表23。此处的压力表23通过螺纹联接在阀体1上,压力表23和阀体1之间设置有密封结构。事实上,此处的压力表23还起到检测高压气瓶2中的气体压力的作用。因为通常情况下,供气控制阀24处于关闭状态,而此时,高压气瓶2中的高压气体会冲开供气单向阀34从而进入供气支路15和测压支路22中,这样压力表23可以对高压气瓶中的气体压力进行实时检测,当气体压力较低时,可以及时对高压气瓶充气。另外,当需要监控充气压力时,此时供气控制阀24打开,高压气体进入测压气路22中,但此时供气单向阀34并不打开。事实上,在其他实施例中,如果不需要监控充气压力时,也可以不设置供气单向阀,而仅由供气控制阀24控制供气支路的通断。本实施例中的供气控制阀和排空控制阀均为用于防止高压回流的单向阀。同时,为提高储气容器的安全性,阀体1上设有用于与储气容器连通的卸荷进气口16和用于与外界大气连通的卸荷排气口,阀体内部设有两端分别与卸荷进气口及卸荷排气口连通的用于排空储气容器以使其紧急卸荷的卸荷气路17,卸荷气路上设有用于控制卸荷气路通断的卸荷控制阀18,此处的卸荷控制阀为具有防止高压气体回流功能的单向阀。使用时,将集成阀对应安装在作为储气容器的高压气瓶2上,此时,集成阀的充气口11、供气口37及卸荷进气口16均与作为储气容器的高压气瓶2的内腔连通。充气或供气时,将切换装置3切换到ON位置即第一工作位,打开供气控制阀24,此时,排空控制阀21关闭。充气时,使外部高压气源与常闭接头27连通,进入总气路17的高压气体经充气支路26进入高压气瓶2中,此时,充气单向阀25保证高压气体流向储气容器并防止其出现回流,同时,一部分高压气体经供气控制阀24、供气支路15进入测压支路22中,由压力表对充气气压进行测量,此时,供气单向阀34处于关闭状态,保证正常充气。充气完成后,将外部气源与常闭接头分离,将切换装置3切换到OFF位置即第二工作位,关闭供气控制阀24,打开排空控制阀21,总气路27中的高压气体经排空支路19排走。供气时,重新将切换装置3切换到ON位置即第一工作位,打开供气控制阀24,此时,排空控制阀21关闭,使外部用气设备与常闭接头28连通,高压气瓶2中的高压气体冲开供气单向阀34,经供气支路15、总气路27进入外部用气设备中,实现供气,此时,一部分高压气体进入测压支路22中,由压力表23对供气压力进行测量。在供气完毕后,转动切换装置3,将切换装置3切换到OFF位置即第二工作位,关闭供气控制阀24,打开排空控制阀21,总气路27中的高压气体经排空支路19排走,再将集成阀与外部用气设备断开即可。而当储气容器因故无法正常排气时,通过专用工装将卸荷控制阀18打开,进而可将储气容器的高压气瓶2中的高压气体排出,提高储气容器的安全性。本实施例中,排空控制阀和供气控制阀均为由切换装置控制的单向阀,切换装置采用机械式手动凸轮结构。在其他实施例中,排空控制阀和供气控制阀也可以为电磁阀,此时,切换装置可以为电磁切换装置,只要可以保证对充气或供气状态及排空状态的正常切换即可。本实施例中,各控制阀均采用单向阀,控制阀结构简单,使得整个集成阀体积较小,集成化程度高,有利于集成阀的小型化设计。本实施例中,设置常闭接头可以有效减少外界对集成阀内容各气路的影响,同时,为消除常闭接头常闭状态导致残存在总气路中的高压气体对各控制阀的影响,在阀体上设置排空支路来减小这种影响,提高各控制阀的使用寿命,有效降低了集成阀内容压强,有效延长了整个集成阀的使用寿命。本实施例中,因为设置有测压气路,所以需要在供气支路上设充气单向阀,在其他实施例中,当不需要对充气气压进行监控时,也可以不设置充气单向阀,而仅由供气控制阀控制控制供气支路的通断。本实施例中,由切花装置实现排空控制阀和供气控制阀的切换导通断开,在其他实施例中,也可以不设置切换装置,而由手动控制两者分别打开或关闭,只是没有切换装置的安全性好。本实施例中,排空支路的一端与排空口连通、另一端连通于总气路与充气单向阀之间的充气支路上。在其他实施例中,排空支路的另一端也可以与总气路连通或连通于或连通于总气路与供气控制阀之间的供气支路上。