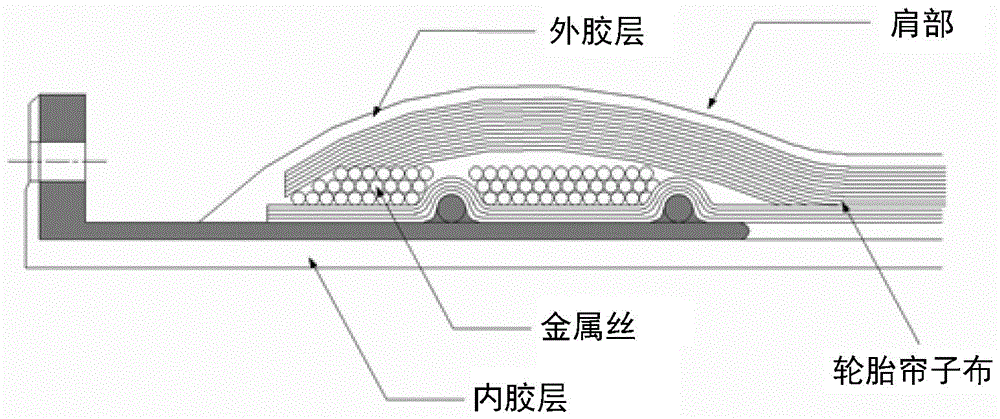
本发明涉及一种对海绵进行粘附且缠绕钢化丝而制成的浮式胶管的结构。
背景技术:本发明涉及一种容易制备且具有缓冲效果的浮式胶管的结构。浮式胶管为输油及疏浚用胶管之一,疏浚胶管大致分为两种方法,即使用浮筒而使管和胶管漂浮的方法和借助磁力漂浮的方法(浮式胶管,FloatingHose),并根据其用途具有带式(bandtype)、凸缘式(flangetype)等,根据使用条件及挖泥船的大小区分为海上管用、潜管用、船内管用等。这种疏浚用胶管需要容易地与铁管相连接,同时不仅其内胶的耐磨耗性要好,耐压、拉伸要强,而且也要有可溶性等弯曲性。特别是,最近,处于疏浚距离逐渐变长的趋势,随着疏浚距离变长可以疏浚至远距离大海,因而就需要更好的耐磨耗性或耐压、拉伸性等。目前,广为使用的凸缘形态的疏浚用胶管为大口径(大约760mm~1100mm的直径)胶管,通常由内部橡胶层、外部橡胶层、内部橡胶层与外部橡胶层之间的加强布及加强材料形成,上述疏浚用胶管的末端具有金属材料的凸缘,上述凸缘是将胶管与连接于泵侧的吸入用或排出用钢管之间相连接,或者将胶管与胶管的末端相连接而细长地延伸并排出的,通常,凸缘的外缘向外部暴露,从而可通过紧固紧固螺栓来将其他胶管或管(Pipe)相连接,并由内外部的橡胶层构成。图1a及图1b示出了以往的胶管的截面。在韩国实用新型公告号第1980-0001371号中,胶管仅指借助磁力漂浮的胶管(浮式胶管),将由橡胶层、钢化层及表皮层构成的胶管的加强布层与在普通尼龙(Nylon)或涤纶帘子布(PolyesterCorde)前置(Topping)橡胶的垂直和以逐渐接近于54、45的相反角进行接合,但因很难使垂直和符合要求角度且因可能会在不规定的接合部位产生的压力偏差,致使胶管的内部压力失衡。在上述实用新型的胶管制作方法中,钢化层的制作方法是利用帘子布来粘附的手工作业的方法,是目前通常所使用的手工作业方式。这种方法不仅需要较长的时间,也有很多帘子布之间的重叠,使得胶管的厚度变厚,并由此使胶管的柔韧性成为问题。在韩国专利公开号2001-0052849号中的“高压橡胶胶管及其制造方法”中,在内胶层的外周配置将有机纤维帘线编织成两层的螺旋形或一层的叶片形态的有机纤维钢化层,在有机纤维钢化层的外周侧配置将钢化丝编织成两层的螺旋形的钢化丝钢化层,并使有机纤维钢化层的编织角度小于钢化丝钢化层的编织角度,使有机纤维钢化层的编织张力大于钢化丝钢化层的编织张力,来增强柔韧性,实现轻量化,并提高耐久性。但是,这种胶管结构更加增强了钢化层,以使相对于向胶管的径向上的断裂不向内侧扩散,从而与以往的胶管相比可以说耐久性增强了,但是,胶管的外侧部分会因搬运或使用发生折叠,并且根据胶管的用途、使用长度,切断而使用的胶管或两侧连接用金属联轴器以液压式联接接合的方式使用,因而对于联接部位的漏水不良没有任何解决方法。在疏浚用胶管中,凸缘部位的金属部分和对胶管的橡胶粘附的钢化丝部分最为重要,但上述胶管结构没有具体地记载对胶管和凸缘的连接部位的粘附方法。最近,在本申请人所申请的申请中,在内胶内插入金属环,使长度方向上的损伤不再扩散,因而可以对胶管内部的损伤进行处理,但是,上述申请也具有无法对因高压环境或内部物体而发生的内胶的损伤进行处理,并且没有弯曲性的缺点。并且,本发明的浮式胶管不仅包括疏浚胶管,还可以包括浮式输油管胶管。浮式输油管胶管以连接于船与船之间或者与船和港口相连接的方式用在迁移流类。当形成内胶层时,浮式输油管胶管利用挤出机将内胶层以管式的方式形成于心轴,以防止漏油,并且内胶层使用耐油性橡胶,疏浚胶管使用耐磨耗性橡胶。
技术实现要素:本发明是为了克服如上所述的手工作业的缺点而提出的,其目的在于,提供一种胶管,使用海绵,具体地利用与以往不同一边缠绕海绵一边热熔敷的方法进行粘贴并缠绕钢化丝,从而缠绕钢化丝来固定凸缘和橡胶胶管部分,而不使用金属丝(Wire),因而浮力较好且不容易损伤。并且,形成一种胶管,将缠绕自动化,以容易制作,并且因自动化而与现有的制作方法相比缩短制作时间、减少原料、增强胶管的耐久性、不损伤柔韧性,并将与另一管之间的连接偶合一体型,以使不存在连接部位的缺点,并且可同时缠绕钢化丝和橡胶板,来形成胶管。为了达成上述目的,提供一种将海绵热熔敷且缠绕钢化丝的浮式输油及疏浚胶管的制造方法,该方法可包括如下步骤:第一步骤,在缠绕胶管缠绕胶带而进行硫化;第二步骤,解开胶带,并将海绵粘附于缠绕胶管的表面,来形成地板材料海绵层;第三步骤,在地板材料海绵层上形成热熔敷海绵层;第四步骤,在热熔敷海绵层上形成第二外胶层。上述第四步骤中,可通过同时缠绕钢化丝和橡胶板而形成第二外胶层。上述缠绕胶管包括如下步骤:第A-1步骤,缠绕机自动缠绕橡胶板,或者通过手工作业来形成内胶层,并在形成有内胶层的胶管的内胶层的上侧搁放凸缘,来提供给缠绕机,第A-2步骤,向上述缠绕机提供多根钢化丝,并在上述内胶层的上侧缠绕钢化丝,使缠绕之前的上述钢化丝和缠绕的上述钢化丝不超过预先设定的角度,来形成钢化层,并固定凸缘,第A-3步骤,向上述钢化层上提供橡胶,并形成外胶层而进行硫化;上述内胶层及外胶层中的某一种可通过同时缠绕钢化丝和橡胶板之后经过硫化过程而形成。上述第A-2步骤与上述第A-3步骤之间还可以包括如下步骤:形成中胶层的步骤;在中胶层与外胶层之间形成另一钢化层的步骤。上述中胶层可以是同时缠绕钢化丝和橡胶板的形态。上述钢化丝可以是涤纶、尼龙、凯夫拉(Kevlar)、芳纶中的某一种,并由树脂涂敷而成,使得橡胶和钢化丝容易粘附。当同时缠绕橡胶板和钢化丝时,橡胶板能够以与沿着轴向旋转中的辊相接触的方式旋转,上述钢化丝沿着轴向和直角方向被供给,并沿着轴向左右移动,来调节缠绕角度。上述钢化丝可经由引导件之后被缠绕之前经过排序的步骤,每个钢化丝的张力独立地被控制。缠绕上述钢化丝的方法可使用倾斜方向及直线方向中的某一种以上。并且,本发明提供一种将海绵热熔敷且缠绕钢化丝的浮式输油及疏浚胶管,上述浮式胶管在缠绕胶管的外周面依次形成地板材料海绵层和热熔敷海绵层;缠绕胶管形成有胶管本体和凸缘部,上述胶管本体由内侧的内胶层和外侧的外胶层构成,上述凸缘部由金属构成,并位于上述胶管本体的两侧,能够与另一套管或金属管相连接;上述内胶层与外胶层之间形成有一个以上的钢化层,上述钢化层通过以规定角度缠绕多根钢化丝状体而形成,上述内胶层与外胶层之间形成有中胶层;上述内胶层及外胶层中的某一种通过同时缠绕钢化丝和橡胶板之后经过硫化过程而形成。当同时缠绕橡胶板和钢化丝时,橡胶板能够以与沿着轴向旋转中的辊相接触的方式旋转,上述钢化丝沿着轴向和直角方向被供给,并沿着轴向左右移动,来调节缠绕角度。根据本发明,具有如下效果:提供一种即具有较高的浮力又容易耐于内部的压力,并且增强耐久性和柔韧性,具有较薄的直径的凸缘一体型胶管。附图说明图1a及图1b是示出以往的胶管的截面的图。图2a、图2b及图2c是示出本发明的胶管的结构的图。图3是示出根据本发明所制作的胶管的一实施例的图。图4a、图4b及图4c是示出制作本发明的胶管时所使用的装置的图。图4d表示维持钢化丝的个别张力并供给钢化丝的装置。图5是示出以往手工作业工序中利用粘合剂对海绵进行粘附的过程的照片。图6是示出根据本发明对海绵进行热熔敷的机械的图。图7及图8是示出本发明的制作过程的图。附图标记的说明11:内胶层12:中胶层13:外胶层14:钢化层15:胶管肩部21:钢化层22:辅助层具体实施方式下面,参照附图,对本发明进行详细的说明。图2a示出了根据本发明所制作的胶管的截面。本发明的胶管从下侧到上侧构成为内胶层-钢化丝缠绕层-第一外胶层-热熔敷海绵层-钢化丝缠绕层-第二外胶层。以往的方式为在制作具有内胶层-钢化层-外胶层的胶管之后,缠绕胶带而进行硫化,再向外胶层的外侧形成热熔敷海绵层,并重新形成第二外胶层。当形成第二外胶层时,可与钢化丝一起缠绕,或者可以在第二外胶层的下侧还形成一个钢化层。为了制造本发明的胶管,通过以往的方法所制成的缠绕胶管在缠绕胶带而进行硫化之后安装于缠绕机。此时,对缠绕胶管进行硫化之后,对海绵进行粘附,这是为了施加压力并进行硫化来放出存在于胶管的内胶、钢化层、外胶的各个层及橡胶之间的空气,并帮助橡胶之间的粘附。如此进行硫化的胶管的外面和海绵面的最初粘附不进行热熔敷,因而起到热熔敷底面作用的海绵利用粘合剂进行粘附,并以热熔敷用海绵厚度的1/2左右进行粘附。并且,可通过计算胶管的规格和重量、经由物的重量,来计算胶管需要具有的浮力而设定所使用的热熔敷用海绵的厚度。通常,作为海绵的宽度使用200至450mm内的宽度,但可根据厚度也以缠绕在辊的形态形成,或者也能够以不被缠绕的形态形成。为了缠绕海绵,在导纱眼部分的上下附着有所需的宽度的导辊,被缠绕的一侧的下侧以使散热器朝向海绵的方式散发海绵的熔点的温度,缠绕成型机一边旋转一边使海绵熔敷。图6示出了与此相关的概念图。为了使海绵熔敷,在缠绕海绵之前,海绵从导纱眼脱落,并经过导辊支撑散热器,以容易进行熔敷。并且,当缠绕海绵时,海绵层的数量优选为偶数,并缠绕成相对于胶管的旋转轴成45°左右。若缠绕与所需的厚度相对应的海绵层,则在平整胶管的两侧末端部分之后,缠绕钢化丝(此时,可缠绕外胶层,并同时缠绕钢化丝和橡胶板而形成第二外胶层)。若形成至第二外胶层,并缠绕绷带,再进行硫化之后,解开绷带,则完成浮式胶管。通过这种方法制成的浮式胶管具有较高的耐久性,并且不仅对外力的阻力较大,而且具有较高的浮力,并且也可以适用于以往的胶管。但是,通常,当制作胶管时,若胶管的厚度太厚或宽度太大,则很难处理,因而胶管的宽度及厚度根据胶管的规格而定。但是,浮式胶管需要具有一定程度的浮力,因而,在使浮力变大的情况下,胶管的强度会下降,但在把重点放在胶管的强度的情况下,浮力会下降。本发明的胶管可利用如上所述的方法通过对海绵(乙烯-醋酸乙烯EVA,ethylene-vinylacetate)进行热熔敷,来减少胶管的厚度。为了防止胶管所具有的耐久性降低,并为了形成胶管,可形成钢化层。在本发明的胶管中,可独立地仅形成钢化层,也可以利用同时缠绕橡胶板和钢化丝的方法,来形成第一外胶层及第二外胶层。对本发明的胶管中钢化层的形成进行详细的说明。本发明的钢化层在以往的胶管形态形成热熔敷海绵层,也可以一边形成为在其外部具有外胶层一边形成钢化层,也可以最初就利用以下的方法来形成。图2b及图2c示出了形成钢化层的例子,作为钢化层可使用由涤纶、尼龙、凯夫拉、芳纶中的某一种制成的钢化丝,也可以涂敷钢化丝而使用。通过继续在内胶层上缠绕上述钢化丝,来形成钢化层,可形成多个缠绕钢化丝而成的钢化层。图2b示出了本发明的胶管的形状及其截面。形成钢化层时所使用的线为涤纶、尼龙、凯夫拉、芳纶,可以作为钢化丝,使用大约1000旦尼尔以上的。优选地,使用1000旦尼尔以上且2000旦尼尔以下的。并且,也可以涂敷钢化丝而使用。当涂敷时,存在如下缺点:将聚脲树脂涂敷于钢化丝的外部,由于1000旦尼尔以下的钢化丝太细,致使受到外部的压力而容易断开,当实际制作产品时,2000旦尼尔以上的钢化丝太厚,致使很难缠绕,并且在缠绕之后厚度变得太厚。涂敷时所使用的树脂并不局限于聚脲,树脂使橡胶和钢化丝的粘附变得容易。并且,进行缠绕作业时所使用的钢化丝以使未分离的多根钢化丝不断开的方式缠绕,被缠绕的钢化丝形成的角度以45°至53°的角度继续缠绕。若以超过45°至53°的角度缠绕,则钢化丝与钢化丝之间变得太密,使得缠绕后的厚度变得太厚或钢化丝之间离得太远,从而减少钢化层的效果。由于上述角度为不超过最大许可膨胀5%的角度,因而随着膨胀的效果也较少。缠绕钢化丝的卷绕角度可根据一次被缠绕的钢化丝的数量而不同,但可以为上述45°至53°的角度,一次被缠绕的钢化丝的数量减少,并且胶管的直径越大卷绕角度越大。作为以往的胶管中的加强层使用被织造或编织的布,若使用被织造或编织的布,则层的厚度不再变厚,即使进行织造,也容易分离下层和上层,并通过尖锐的物体容易地分离所织造的纬丝和经丝,但是,像本发明一样,若利用钢化丝来缠绕胶管的外部,则与用布形成时一样,上层的布与下侧的布之间发生区分,上层和下层的布可以无任何结合地重叠,但是,像本发明一样,在以规定角度缠绕的情况下,缠绕其本身为一种结合,因而与使用所织造或编织的布时不同,会产生较强的结合力。并且,通过在钢化丝涂敷树脂,来容易地粘附钢化丝和橡胶,因而与区别橡胶层和钢化层的以往的产品不同。因此,即使胶管内部进入尖锐的异物,也不会容易地经由钢化层。并且,对从内外部施加的压力的阻力变大,从内外部施加的压力均匀地分配到胶管整体。并且,为了耐于高压力,从刚开始缠绕到结束缠绕为止,需要防止钢化丝断开。除了这种钢化丝之外,也可以考虑缠绕由聚乙烯或轮胎帘子布制成的薄片,但是,在使用薄片的情况下,需要缠绕成薄片的一部分重叠,使得最终产品的厚度变厚,为了耐于高压力,需要缠绕成很稠密,因而与使用钢化丝相比其效率下降,致使不得不使用更多的薄片。因此,在使用钢化丝而缠绕的情况下,所使用的线的量变少,并可以使胶管的厚度变薄。在图1b的实施例中,为了连接凸缘,在相当于胶管的末端的内胶层上放置凸缘,并用钢化丝沿着径向缠绕,以使胶管与凸缘相结合,并单纯地将轮胎帘子布缠绕在外面橡胶内,但是,在要根据本申请的情况下,如图2c所示,即使不使用上述钢化丝,也可以将凸缘与胶管相连接。即,若在内胶层上侧放置凸缘的状态下从凸缘一端起点利用圆形(Hoop)方式开始,并在胶管部分利用螺旋形(helical)方式设为45~53°之后,在对面凸缘部分利用圆形方式继续缠绕钢化丝,则即使没有钢化丝等连接单元也可以使凸缘结合,这种情况下,以往的胶管被钢化丝缠绕,解决因橡胶和钢化丝的粘附问题而所松弛的问题,并且可以在薄于以往的胶管的形态的胶管形状体现凸缘和橡胶钢化丝一体型的套管胶管。但是,能够提供一种可承受更高的压力且没有肩部而更薄的胶管,而不是向以往一样又厚且向凸缘内侧具有肩部的胶管。并且,若通过这种方法来形成内胶层,则橡胶与钢化丝相混合,耐于因经过胶管内部的异物而发生的损伤。在图3中,所形成的胶管虽然稍微具有肩部,但与以往的胶管相比呈稍微薄的形态。当形成内胶层时,普通疏浚胶管可通过手工作业而成,但输油管胶管利用挤压机以管式的方式将内胶层形成于心轴。并且,普通疏浚胶管使用耐磨耗性橡胶,输油管胶管使用耐油性橡胶。图3示出了通过这种方法来制成的胶管的一实施例。图3的实施例是未形成外胶层,而形成至钢化层的状态,并用橡胶层覆盖其上面。图中,可能会看到钢化丝交叉地形成与覆盖所织造的加强布相似,但是,就本发明的钢化丝而言,一边持续转动胶管一边缠绕维持所需的角度的钢化丝,当缠绕加强布时,沿着径向施加的规定的作用力的量受限制,从而不能像缠绕钢化丝一样,持续施加作用力,以使固定凸缘或者紧紧拉住加强层,以提高耐久性。并且,当形成外胶层时,在形成加强层之后,与以往相同,也可以经过硫化过程形成外胶层,但是,当缠绕多根钢化丝时,可以与具有类似于上述多根钢化丝的程度的宽度的生橡胶板一起缠绕而形成。图4a、图4b及图4c示出了这种装置。此时,也可以省略钢化层,但外胶层起到钢化层的作用。图4a、图4b及图4c的装置也可以使用于缠绕钢化丝状体,示出了当形成外胶层时,利用与橡胶板一起形成而缠绕的方法形成的状态。若橡胶板具有一次缠绕钢化丝状体时所占的宽度左右的宽度,则不会特别地局限于该宽度。在结束缠绕作业之后,经过硫化过程将橡胶板形成为一体,因而该宽度不重要。以往,具有将金属丝插入于橡胶板之间之后,缠绕该金属丝而形成橡胶层的情况,但在本发明中,一边缠绕钢化丝状体一边形成橡胶板,以往的插入有金属丝的橡胶板以适合橡胶板的宽度的方式缠绕,使得金属丝不重叠,因而与本发明有所差异。并且,在本发明中,经过硫化过程将橡胶层制成一层,因而与以往的技术有所差异,即使是最终结果物,也呈以规定的角度缠绕的钢化丝之间被橡胶填满的形态,因而与插入有钢化丝的橡胶板有所差异。图3为无橡胶板地仅缠绕钢化丝的形态,但可视为在上述形态下钢化丝与钢化丝之间的空的部分被橡胶板填满。并且,不仅是外胶层,中胶层也通过如上所述的方法在同时缠绕橡胶板和钢化丝之后经过硫化过程而制成,如此所制作的中胶层或外胶层不仅可以承受来自内外部的较强的压力,而且因橡胶特有的弹性而确保柔韧性,也可以承受来自胶管内部的冲击。如图3所示,当缠绕钢化丝时,可在两端以垂直于轴向的方式缠绕,但在内侧部分(不是末端)以形成规定的经丝的方式缠绕。在硫化过程中,除了以橡胶板形态缠绕橡胶之外,也持续将橡胶与140℃至150℃的蒸汽一起供给,来提高胶管的橡胶密度。为此,也可以使用单独的模具。在均形成内胶层、中胶层、外胶层等橡胶层之后,施行硫化。并且,也可以在进行硫化之后,用钢化丝再从外胶层外侧缠绕,来追加地制造钢化丝层。图4a是在钢化丝缠绕机旁边示出的图,图4b是从上侧示出的图。若除去向钢化丝供给机的下侧供给的橡胶板,则可以使用于形成如上所述的钢化层。上述缠绕机将芯的一端固定于移动台,以使从为了维持胶管的形态而插入胶管的芯与芯的中心部延伸的旋转轴旋转并移动。并且,在芯的正面形成细丝供给部,若从被钢化丝缠绕的绕线筒供给到钢化丝,并紧紧地维持张力,则会被芯缠绕。在图4a中,用于缠绕等的机械包括:主轴,用于使产品旋转运动,放线车,缠绕有纤维,并用于一边左右移动一边缠绕,副轴,根据产品的长度移动的同时把持产品,以使该产品可旋转运动;副轴可具有前后轴或旋转轴,以校准缠绕纤维的角度,并前后移动(与产品的轴向垂直的方向)。即,在主轴和副轴的上部安装放线车,在放线车一侧安装前后轴及旋转轴,以使利用轴心的轴承座和副轴的轴承座使产品上升,并在主轴一侧利用三爪卡盘(3-jawchuck)固定产品轴。在图4b中,当供给钢化丝时,可向a方向供给橡胶板,从而一起缠绕。并且,即使向钢化丝的上端同时供给橡胶板,也可以使橡胶板双向供给。当缠绕时,图4b中所示的辊使橡胶板平整,导纱眼(eye)使在通过导正销之后被产品缠绕之前的纤维排序,并且当根据缠绕角度旋转时,纤维排列在导纱眼中心,以使起到维持缠绕角度的同时缠绕的作用。图4c示出了用于缠绕钢化丝的装置的整体状态。细丝供给部持续供给缠绕在外部的钢化丝,芯持续旋转的同时以预先设定的速度左右移动,并缠绕钢化丝。从左侧到右侧或者沿着其反方向移动的同时缠绕一层钢化丝之后,转换移动方向,而向反方向移动并缠绕钢化丝。但是,一根钢化丝在不断开的状态下持续缠绕,并一边左右移动一边缠绕。普通的钢化层通过这种方式而成,并缠绕大约10至15层左右,在连续形成多个钢化层的情况下,在这种主钢化层之间缠绕一层用于区分钢化层之间的辅助钢化层。如图4c所示,当缠绕纤维和橡胶时,组合倾斜方向(螺旋形)和直线方向(圆形)这两种进行缠绕,图4c中所示的图案示出了产品两侧部分向直线方向缠绕,产品中间部分向倾斜方向缠绕的状态。在通过如上所述的方法来形成内胶层、中胶层、外胶层中的某一种以上的情况下,与以往的胶管进行比较,胶管整体的厚度变薄,同时因缠绕在钢化层和橡胶层的钢化丝而使柔韧性增加,并且承受来自胶管内外部的压力的作用力也变强。特别是,即使存在胶管外部的损伤或内面的损伤,也不会向长度方向或径向扩散损伤,因而胶管的耐久性急剧增加。图4d示出了纤维张力装置,当缠绕产品时,需要时常维持纤维的张力,而纤维的数量为24~72个,需要独立地控制每个纤维的张力,当缠绕时,将纤维的张力控制为1.5kgf~1.8kgf左右而使用。.张力装置使缠绕在粗纱(Roving)的纤维经由安装有负荷传感器的导辊进入产品,每一单元(unit)单独安装有24个。用于控制张力的张力调节器面板由24ch构成,并独立地可调节张力值及其他设定值。并且,就张力装置而言,机构部由要经由粗纱的粗纱外罩、旋转外罩的直流电动机、测定张力的负荷传感器及纤维构成,电学上由可调节张力值及其他设定值的24ch面板和直流电动机的伺服机构试验台及电源装置构成。若从面板选择为了控制这种张力装置而安装粗纱的ch之后,将纤维固定于产品,再从PC将准备缠绕纤维的信号发送到面板,则直流电动机与面板中所设定的张力值相对应地实时控制,若决绝纤维,则检测拒绝信号并传递到PC,使得机械以暂停的形态工作。并且,当缠绕钢化丝时,与凸缘一起缠绕,因而相对于以往需要通过单独的钢化丝等而附着凸缘,本发明可通过钢化丝缠绕凸缘,来以无单独的工序的方式容易制造。图7及图8示出了本发明的胶管的制作工序。本发明的浮式胶管在制作缠绕胶管之后,经过硫化将存在于缠绕胶管内部的空气放出,并在其上面粘附地板材料海绵之后,对热熔敷海绵进行熔敷。在结束海绵热熔敷之后,形成第二外胶层,再进行硫化。并且,与以往不同,能够以具有角度地缠绕钢化丝的方式或者与橡胶板一起缠绕的方式形成缠绕胶管,以提高耐久性和柔韧性。这种胶管的制造方法包括如下步骤:缠绕机自动缠绕橡胶板,或者通过手工作业在形成有内胶层的胶管的内胶层上侧放置凸缘,从而提供给缠绕机的步骤;向缠绕机提供多根钢化丝,并在上述内胶层的上侧缠绕钢化丝,使缠绕之前的上述钢化丝和缠绕的上述钢化丝不超过预先设定的角度,来形成钢化层,并固定凸缘的步骤;向钢化层上提供橡胶,并形成外胶层而进行硫化的步骤;可通过仅借助以往的橡胶的硫化方法分别制作内胶层和外胶层,也可以同时缠绕橡胶板和钢化丝而形成。像这样,与其他产品不同,本申请提供钢化丝,以提高耐久性和柔韧性。图7详细地示出了橡胶部分的成型过程,在图8中,为了使浮式部分成型,对海绵进行热熔敷,缠绕钢化丝,并缠绕尼龙带之后,进行硫化并除去尼龙带,从而完成浮式胶管。