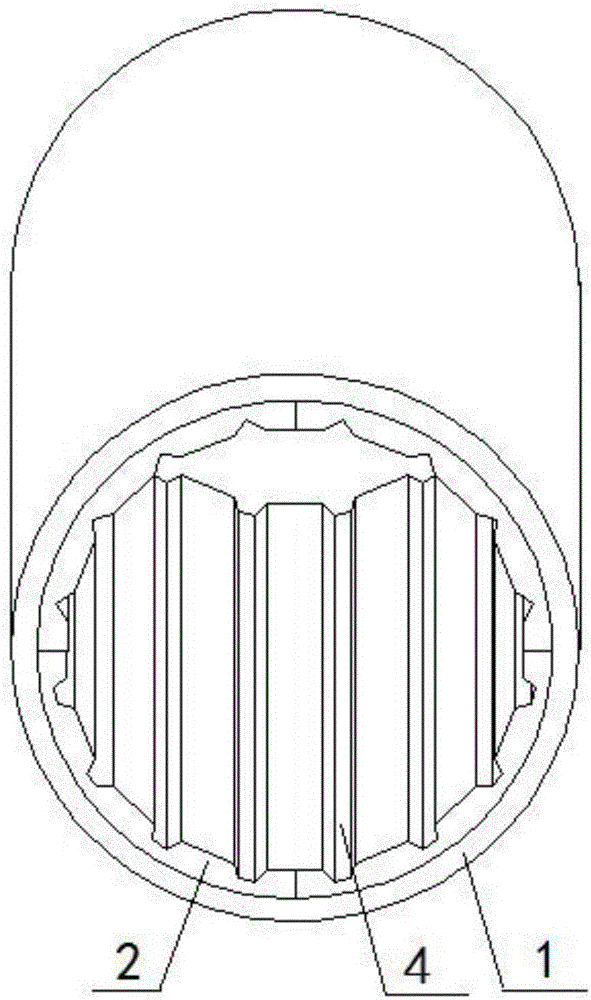
本发明属于大型舰船低速重载轴承
技术领域:
,具体涉及一种船用混合槽水润滑橡胶轴承。
背景技术:
:随着滑动轴承应用的逐步推广,水润滑橡胶轴承作为其发展的一个重要种类,改变了以往机械传动系统中都是以金属结构构成摩擦副的传统思想,不但节省了大量原油和贵重金属材料,而且大大简化了轴承轴系结构,避免因油污泄漏而严重污染水环境的情况。目前水润滑橡胶轴承开槽单一,一般都用于高速、轻载以及长径比比较小的轴承。水润滑橡胶轴承以其无污染、省材料、低成本;耐磨损、耐泥沙、耐腐蚀等一系列优点而在船舶、水泵业获得广泛应用,成为水下最适宜的轴承之一。它对于解决目前水介质中使用金属滑动轴承频繁出现密封失效、轴瓦磨损问题,对于简化机械润滑与密封系统结构和节约贵重有色金属轴瓦材料,都具有重要的意义。一直以来,还没有一个合理的设计程序和设计规范来指导水润滑橡胶轴承的设计。一般水润滑橡胶轴承结构设计考虑长径比、是否开槽、橡胶层厚度、板条形状、连接面形状、开槽类型等好多方面。所以其结构设计还有待进一步的完善。对于摩擦面形状,段芳莉认为在轻载或者低速工况凹面型的摩擦性能显著优于平面型,且凹面型轴承的摩擦性能对速度和载荷的变化更为敏感。戴明城的试验与仿真研究表明,平面型优于凹面型或凸面型,在于它更易形成弹-塑流体动压润滑,具有更好的启动性和低速运转性能。故从降低尾管轴承振鸣音发生的临界速度和摩擦因数的角度,推荐使用平面型。R.L.Daugherty等认为橡胶层厚度越小,摩擦系数越小,因此从降低水润滑尾轴承振鸣音发生的临界转速工况的角度,推荐使用平面型薄橡胶板条。硬度越小,橡胶表面摩擦系数越低,选择合适硬度的橡胶板条也很重要。周忆等通过仿真与实验对比,研究结果表明,水润滑橡胶合金轴承的水槽半径大小、摩擦面形状以及摩擦副的摩擦系数对水润滑橡胶合金轴承的摩擦噪声有较大影响,而水槽的形状对轴承摩擦噪声的影响不大。周欢欢等对比分析了三种不同板条类型下硬度分区对接触性能的影响效果,结果表明,硬度分区能显著改善轴承的接触性能,凹面型板条型式的静态接触性能较佳。综上,凹面型承载能力较好,明显优于平面型和凸面型,平面型有较好的导水效果,容易形成弹流润滑水膜,凸面型有利于水的周向循环,但是会导致较大的摩擦与磨损,适用于低硬度、厚度大的橡胶衬层。对于水槽类型,为了润滑、冷却、排出泥沙,水润滑橡胶尾管轴承工作表面一般都开有水槽,且以U和V型轴向槽最为通用。刘宇等人对于轴向开槽水润滑尾管轴承的润滑性能进行了数值计算与分析,结果表明:开槽后轴承周向压力分布不连续,水槽处压力降低为0,轴承的承载能力降低;且槽的宽度越大,个数越多,轴承的承载能力也就越小。不仅如此,U型槽有利于流体流动,而梯形槽有较好的承载特性,形成连续水膜,不易破裂。这些都是基于基本水槽的研究,没有考虑不同水槽形状以及没有对不同水槽结构进行对比优化。以上都是单一研究水槽摩擦面形状或者水槽类型,没有综合考虑两者结合后的耦合影响。对于普通开沟槽轴承,由于其沟槽种类的不同,对轴承承载力、流体流动等都有不同的影响,但是都未考虑轴承周向压力分布以及水膜流动变化。对于单一轴承进行单一分析单一设计,没有考虑其混合后结果。对于开槽方向的选择,螺旋槽可以引导海水沿着沟槽进行螺旋运动,进而产生了一定的螺旋向心力,容易形成弹性流体动压润滑,并且螺旋槽所产生的沟槽内水流流动性较为平稳,对船舶螺旋桨轴的冲击影响较小,但是在低速重载作用下,由于螺旋角太大又会对其流动产生抵抗作用;纵向式沟槽,由于供水量充足,其润滑效果良好,冷却均匀可靠,泥沙容易冲出艉轴承外,摩擦功损较小,加工制造相对容易。但其所产生的沟槽内水流流动性较大,不稳定,易对船舶螺旋桨轴产生较大的冲击影响。一般水润滑橡胶轴承都开有纵向沟槽或者螺旋形沟槽,但都存在各方面优势和不足。对于导水槽的细化设计还有待进一步研究。对于普通开沟槽轴承,由于其沟槽种类的不同,对轴承承载力、流体流动等都有不同的影响,但是都未考虑轴承周向压力分布以及水膜流动变化。对于单一轴承进行单一分析单一设计,没有考虑其混合后结果。在轴承加工以及安装过程中,工艺和方法都对水润滑橡胶轴承后续的工作及故障有着至关重要的影响。一般水润滑橡胶轴承多采用板条式轴承螺栓固定的方式,在长期的工作交变应力下,容易出现错动,导致舰船尾部产生异常噪声和轴系安全问题。以及安装时也需要考虑轴承的偏心率,如不考虑可能造成轴承转子系统的不平衡响应。所以安装过程及方法还有待改进。技术实现要素:本发明的目的是提供一种船用混合槽水润滑橡胶轴承,以克服现有水润滑橡胶轴承弹流润滑特性不佳的问题。本发明采用的技术方案为:一种船用混合槽水润滑橡胶轴承,包括橡胶衬层,橡胶衬层外圆周面上套有合金轴套,橡胶衬层内壁上设置有多条沟槽,多条沟槽沿着橡胶衬层内壁的圆周方向均匀分布,多条沟槽由多条V型沟槽和多条梯型沟槽组成;相邻两条沟槽之间形成连接面。上述沟槽在橡胶衬层内壁上呈直线状,其延伸方向与合金轴套的中轴线平行。上述沟槽在橡胶衬层内壁上呈螺旋状。其中,螺旋状沟槽的螺旋角为α,tanα=Vτ/Vn,其中,Vn为流体在水润滑橡胶轴承里轴向流动速度,Vτ为水润滑橡胶轴承周向旋转速度的线速度;螺旋角α的方向为Vτ和Vn的合成方向。另外,连接面为平面,且所有连接面的长度b一致。并且,V型沟槽的数目与梯型沟槽的数目相等。再者,橡胶衬层由四个橡胶衬层单体组成,每个橡胶衬层单体的形状为四分之一圆环状。本发明的有益效果是:改善了以往沟槽开槽方式的单一性,结合V型和梯型两种沟槽润滑效果的优势,提高了水润滑橡胶轴承的弹流润滑特性,其润滑效果好,摩擦损耗小,改善沟槽内水流的流动,提高船舶推进轴系的稳定性。附图说明图1是本发明实施例1船用混合槽水润滑橡胶轴承的结构示意图;图2是本发明实施例1混合槽水润滑橡胶轴承的立体图;图3是本发明实施例1混合槽水润滑橡胶轴承的另一个立体图;图4a为本发明实施例1中,梯型直向沟槽的水润滑橡胶轴承的橡胶衬层沿着轴承轴向方向的最大变形量曲线图;图4b为本发明实施例1中,U型直向沟槽的水润滑橡胶轴承的橡胶衬层沿着轴承轴向方向的最大变形量曲线图;图4c为本发明实施例1中,V型直向沟槽的水润滑橡胶轴承的橡胶衬层沿着轴承轴向方向的最大变形量曲线图;图4d为本发明实施例1中,本发明混合型直向沟槽的水润滑橡胶轴承的橡胶衬层沿着轴承轴向方向的最大变形量曲线图;图5a为本发明实施例1中,沿着轴承轴向方向,梯型直向沟槽的水润滑橡胶轴承的最大压应力分布曲线图;图5b为本发明实施例1中,沿着轴承轴向方向,U型直向沟槽的水润滑橡胶轴承的最大压应力分布曲线图;图5c为本发明实施例1中,沿着轴承轴向方向,V型直向沟槽的水润滑橡胶轴承的最大压应力分布曲线图;图5d为本发明实施例1中,沿着轴承轴向方向,本发明混合型直向沟槽的水润滑橡胶轴承的最大压应力分布曲线图;图6a为本发明实施例1中,沿着轴承周向方向,梯型直向沟槽的水润滑橡胶轴承的最大压应力分布曲线图;图6b为本发明实施例1中,沿着轴承周向方向,U型直向沟槽的水润滑橡胶轴承的最大压应力分布曲线图;图6c为本发明实施例1中,沿着轴承周向方向,V型直向沟槽的水润滑橡胶轴承的最大压应力分布曲线图;图6d为本发明实施例1中,沿着轴承周向方向,本发明混合型直向沟槽的水润滑橡胶轴承的最大压应力分布曲线图;图7a为本发明实施例1中,沿着轴承轴向方向,梯型直向沟槽的水润滑橡胶轴承的流体流动速度曲线图;图7b为本发明实施例1中,沿着轴承轴向方向,U型直向沟槽的水润滑橡胶轴承的流体流动速度曲线图;图7c为本发明实施例1中,沿着轴承轴向方向,V型直向沟槽的水润滑橡胶轴承的流体流动速度曲线图;图7d为本发明实施例1中,沿着轴承轴向方向,本发明混合型直向沟槽的水润滑橡胶轴承的流体流动速度曲线图;图8a为本发明实施例1中,沿着轴承周向方向,梯型直向沟槽的水润滑橡胶轴承的流体流动速度的曲线图;图8b为本发明实施例1中,沿着轴承周向方向,V型直向沟槽的水润滑橡胶轴承的流体流动速度的曲线图;图8c为本发明实施例1中,沿着轴承周向方向,本发明混合型直向沟槽的水润滑橡胶轴承的流体流动速度的曲线图;图9是本发明实施例2船用混合槽水润滑橡胶轴承的结构示意图;图10是图9的A-A剖视图;图11是本发明实施例2混合槽水润滑橡胶轴承的立体图;图12是本发明实施例2混合槽水润滑橡胶轴承的另一个立体图。图中:1-合金轴套,2-橡胶衬层,3-V型沟槽,4-梯型沟槽,5-连接面,6-转子,7.橡胶衬层单体。具体实施方式实施例1如图1所示,本发明提供一种船用混合槽水润滑橡胶轴承,包括橡胶衬层2,橡胶衬层2外圆周面上套有合金轴套1;橡胶衬层2内壁上设置有多条沟槽,多条沟槽沿着橡胶衬层2内壁的圆周方向均匀分布,多条沟槽由多条V型沟槽3和多条梯型沟槽4组成,V型沟槽3的数目与梯型沟槽4的数目相等;相邻两条沟槽之间形成连接面5,连接面5为平面,所有连接面5的长度b一致。当本发明水润滑橡胶轴承套在转子6上时,转子6与所有的连接面5接触,且所有的连接面5与转子6的外圆周相切。如图2和图3所示,本发明实施例混合槽水润滑橡胶轴承的沟槽为直向沟槽,其延伸方向与合金轴套1的中轴线平行。下面通过对比分析U型直向沟槽的水润滑橡胶轴承(Ⅰ)、V型直向沟槽的水润滑橡胶轴承(Ⅱ)、梯型槽直向沟槽的水润滑橡胶轴承(Ⅲ)和本发明实施例1提供的混合型直向沟槽的水润滑橡胶轴承(Ⅳ)这四种轴承的润滑特性,其分析结果如下:图4a、图4b、图4c和图4d为上述四种不同形状直向沟槽的橡胶衬层2最大变形量沿着轴向方向的分布,从这四个图中可以看出,沿轴向分布的衬层变形呈“马蹄型”,即在入口处最大,出口次之,中间很小,并且这四种开槽结构的最大变形量只在开口处的大小区别较大,其分布趋势基本一致;(Ⅳ)号水润滑橡胶轴承的橡胶衬层2变形与(Ⅰ)号水润滑橡胶轴承的橡胶衬层变形近似,(Ⅳ)号水润滑橡胶轴承的橡胶衬层2变形介于(Ⅲ)号水润滑橡胶轴承和(Ⅱ)号水润滑橡胶轴承中间,是综合了二者的较佳选择,但是(Ⅳ)号水润滑橡胶轴承结构对其整体趋势分布的影响相对较小。从图5a~图6d可以看出,由于给定进口速度,所以入口处的压应力最大,给定出口压强为静压强,从而呈现一种从入口到出口,压强递减的状况,但总体趋势来说,(Ⅳ)号水润滑橡胶轴承压应力变化较为平缓,有利于压力稳定线性变化,沿轴向方向转子运转更为稳定。而且,(Ⅱ)号水润滑橡胶轴承结构压应力明显最大,(Ⅳ)号水润滑橡胶轴承次之。压应力是轴承承载能力的一种表现方式,(Ⅱ)号水润滑橡胶轴承由于压力过高,润滑水膜不足以支承,造成水膜破裂,部分轴承形成干摩擦,造成轴承摩擦磨损;(Ⅲ)号水润滑橡胶轴承承载力最小,轴承的负担较轻;随着压应力的增加达到一定程度时,(Ⅳ)号水润滑橡胶轴承的橡胶衬层2产生弹性变形并形成润滑水膜,出现弹流润滑,降低了摩擦系数,其润滑效果优于(Ⅱ)号轴承和(Ⅲ)号轴承;所以,(Ⅳ)号水润滑橡胶轴承为最佳选择。从图7a~图8c可以看出,沿着轴向方向,流体在(Ⅱ)号水润滑橡胶轴承内的最大流动速度最佳,但结合周向流动对比,(Ⅱ)号水润滑橡胶轴承分布波动较大,流体稳定性差;流体在(Ⅲ)号水润滑橡胶轴承内最大流动速度较低,但是周向流动稳定性较好。综上,流体在(Ⅳ)号水润滑橡胶轴承内的最大流动速度仅次于(Ⅱ)号,并且有很好的周向流动稳定性,综合了这三种轴承的优点,(Ⅳ)号水润滑橡胶轴承在流体流动特性上结果理想。综上分析,选取本发明混合槽结构对水润滑橡胶轴承弹流润滑效果有明显的改进。实施例2如图9所示,本发明提供一种船用混合槽水润滑橡胶轴承,包括橡胶衬层2,橡胶衬层2外圆周面上套有合金轴套1;橡胶衬层2内壁上设置有多条沟槽,多条沟槽沿着橡胶衬层2内壁的圆周方向均匀分布,多条沟槽由多条V型沟槽3和多条梯形沟槽4组成,V型沟槽3的数目与梯形沟槽4的数目相等;相邻两条沟槽之间形成连接面5,连接面5为平面,所有连接面5的长度b一致。当本发明水润滑橡胶轴承套在转子6上时,转子6与所有的连接面5接触,且所有的连接面5与转子6的外圆周相切。如图11和图12所示,本实施例水润滑橡胶轴承的每条沟槽在橡胶衬层2内壁上呈螺旋状。如图10所示,其螺旋状沟槽的螺旋角为α,tanα=Vτ/Vn,其中,Vn为流体在水润滑橡胶轴承里轴向流动速度,Vτ为水润滑橡胶轴承周向旋转速度的线速度;螺旋角α的方向为Vτ和Vn的合成方向,根据螺旋角α和螺旋公式确定螺旋状沟槽在橡胶衬层2内壁上的走势,其螺旋公式为:x=r1×cos(t/(π2-α))y=r1×sin(t/(π2-α))z=L×t]]>其中,t∈[0,1],x、y和z为三维空间的长宽高三个坐标轴,r1为轴颈半径,L为轴承长度。下面结合试验对本发明实施例2提供的混合槽水润滑橡胶轴承的润滑特性作进一步详细的说明:本发明基于大型船舶轴承系统,以图9~图12所示的混合螺旋型沟槽的水润滑橡胶轴承为例,具体参数如表1所示:表1水润滑橡胶轴承结构参数表其中,Vn=3m/s,Vτ=Ω×r1=15.7×0.161=2.5277m/s;tanα=Vτ/Vn=0.843,α=40.11637°;因为本发明为一种低速重载轴承,所以开角不宜过大,选取螺旋角为理想值40.11637°、45度以及60度做对比分析,计算结果如表2所示:表2不同螺旋角轴承润滑特性分析结果由表2可知,螺旋角对轴承衬层最大变形量影响较小,三者比较近似,而压应力和速度却有明显的变化。压应力是轴承承载能力的一种表现方式,承载力越小轴承的负担越轻,当压力达到一定程度时,橡胶衬层2产生弹性变形并形成润滑水膜,出现弹流润滑,降低摩擦系数;但当压力过高时,润滑水膜不足以支承,造成水膜破裂,形成干摩擦,造成轴承摩擦磨损。随着螺旋角的增大,一般最大应力也会增大,但是在理想值下,略大于45度应力值,为最优螺旋角布置。同时,对比三者流体最大速度,螺旋角为设定值的速度最大,流体流动特性最佳,为最适宜螺旋角。综上,开螺旋槽角度选择轴向流动方向与周向旋转方向的线速度方向的合成方向,可以很大程度上提高轴承润滑特性。本发明实施例2给定了低速重载螺旋轴承开槽角度方向,改变了以往只能靠实验或经验来确定沟槽角度的窘境,并给定开槽角度确定方式,以应用于低速重载水润滑橡胶轴承。本发明实施例1和实施例2提供混合槽水润滑橡胶轴承的橡胶衬层2由四个橡胶衬层单体7组成,每个橡胶衬层单体7的形状为四分之一圆环状。安装制作时,采用四剖分形式,先把1/4的橡胶衬层2硫化好,然后进行硫化组装,这样在横向和纵向受力处于稳定状态,一方面受力均匀、减小了加工难度,另一方面也改善了以往板条式橡胶轴承长期运转出现松动的情况。当前第1页1 2 3