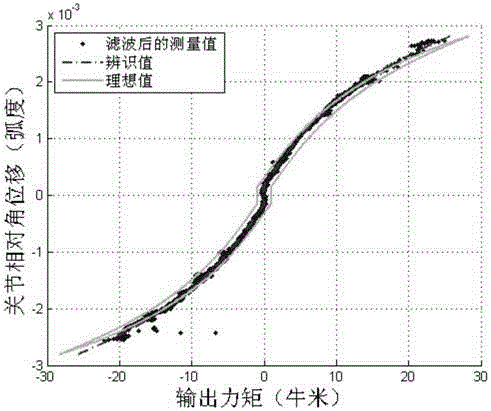
本发明涉及谐波减速器
技术领域:
,具体涉及一种谐波减速器传动刚度测试方法。
背景技术:
:谐波减速器是一种依靠柔性齿轮的弹性变形来实现力和运动传递的减速器,因此,也可称为“应变波传动装置”。谐波减速器由三个相互独立的部件组成,即波发生器、柔轮和刚轮;正确装配情况下,三个部件均能根据传动比确定的传递关系进行同轴转动。一般情况下,采用刚轮固定,波发生器作为输入、柔轮作为输出的减速传动形式。波发生器为椭圆形构件,安装在柔轮内部,迫使柔轮按照一定规律在长轴端产生径向变形成为椭圆状;由于柔轮比刚轮少2个轮齿,因此,当波发生器旋转一圈时,柔轮相对刚轮后退2个齿距,从而实现大减速比传动。目前,对谐波减速器传动刚度的测试不能通过推广普通齿轮的计算公式实现,而主要依赖于实验法来进行;主要测试方法有加载码盘与光学测量系统配合的手动测量法(谭立,从强,王长胜等.高低温环境下谐波减速器刚度测试技术研究[J].真空与低温,2013,19(2):117-120.)和利用工作在力矩控制模式下的伺服电机与光电码盘配合的连续测量法(刚轮轮齿有倾角的短筒柔轮谐波减速器及其传动刚度测试装置,CN102777546B)。前者需要人工反复操作、比较繁琐,得到的数据较为离散;后者可以较为快速、连续地测量谐波减速器的扭转刚度特性。然而,目前不管是手动离散测量方法,还是自动连续测量方法均是进行静态或准静态加载、获得的是谐波减速器的静态刚度,在测试时要么固定输入端、要么固定输出端,然后在另一端加载静态或准静态扭转载荷,再通过测量扭转变形来获得其传动刚度特性。由实验研究(TuttleT.D.UnderstandingandModelingtheBehaviorofaHarmonicDriveGearTransmissionR.MITArtificialIntelligenceLaboratory,1993.ReportNo.:AD-A259610.)可知,静态刚度和产品实际运行过程中谐波减速器表现出来的动态刚度存在一定差异。特别是对谐波传动减速器,由于其既受关节装配预紧力、系统摩擦力和关节间隙等固有因素的影响,又受实际负载、运行速度、系统共振、波发生器转角等使用条件的影响,这种差异会更大。Tuttle根据大量实验得出结论指出,这些因素会导致谐波传动系统的静态刚度和动态刚度之间的差异波动幅度会超过30%。工程实际应用也表明:这种差异往往导致实际产品的启动力矩往往大于理论预测值和模型预测值、启动或制动阶段还存在失步现象,且动态运行的实际响应和理论预测响应存在一定的偏离。技术实现要素:有鉴于此,本发明提供了一种谐波减速器传动刚度测试方法,能够准确地获得谐波减速器传动关节的动态刚度。一种谐波减速器传动刚度测试方法,包括如下步骤:步骤一、以谐波减速器关节构成的产品作为对象,利用其控制系统,对产品的输出端控制,使其作规律的往复运动;步骤二、根据影响传动刚度的相关因素以及产品的测试环境,建立产品中的谐波减速器关节传动刚度的动力学模型,并建立相应的约束条件;步骤三、启动待测量产品,开始测试:根据步进电机参数获得谐波减速器关节输入角度;直接测量谐波减速器关节输出角度;利用差分算法,根据各时刻谐波减速器关节输入角度和各时刻谐波减速器关节输出角度,获得输入角速度和输出角速度;根据获得的输入角速度和输出角速度获得相对角速度;根据获得的输入角度和输出角度获得相对角位移;共测试n组,获得n组运动学参数;步骤四、根据步骤三中获得的n组运动学参数,利用输出角速度信息,采用差分法估计输出角加速度信息,并利用滑动平均滤波器对所得的输出角加速度数据进行滤波处理,获得滤波后的输出角加速度;将谐波减速器关节输出端惯量与滤波后的输出角加速度数据相乘,获得谐波减速器关节输出端力矩;并求所有相对角位移和关节输出力矩的平均值,获得平均相对角位移和平均关节输出力矩;步骤五、根据步骤三和步骤四中获得的参数,代入步骤二中建立的传动刚度动力学模型中,进行刚度参数辨识,进而获得传动刚度动力学模型的最终表达式;在实际测试传动刚度时,将谐波减速器的相对角位移代入,即可获得谐波减速器关节的输出力矩,进而确定输出力矩与相对角位移之间的关系,即传动刚度。较佳地,当测试条件允许使用附加测试设备时,利用力矩传感器获得步骤四中的谐波减速器关节输出力矩。较佳地,步骤三中,利用产品中的光电编码器直接测量谐波减速器关节输出角度。有益效果:基于动力学模型和系统辨识方法,在利用与产品实际服役工况相仿的周期性、带载激励作用下,本发明所述方法能够连续、自动、准确地测试谐波减速器的动态传动刚度。与传统静态测量方法所得结果和动态刚度之间的差异波动幅度可能会超过30%的情况相比,本发明所测传动刚度即是产品实际任务中的动态传动刚度,两者具有一致性。同时,本发明无需对谐波减速器一端进行固定,对输出力矩测量条件也较为宽松(输出力矩可以通过运动学参数估计),因此,本发明可以直接利用产品的实际工作数据进行在线或离线测量,而无需特定的实验测量装置。这一方面可以节省专用测试装置,大大节省成本、提高产品研制效率,另一方面可以根据任务需要,在产品不同服役阶段来实时测量谐波减速器动态传动刚度的变化情况,从而掌握其实际服役过程中的性能退化规律,为产品传动精度、输出力矩精度保持与可靠性提升提供指导。此外,本发明还可以在给出谐波减速器动态传动刚度参数的同时,给出其间隙(或回差)的估计。附图说明图1为单轴驱动天线产品组成示意图;图2为谐波减速器关节示意图;图3为谐波减速器关节动态传动刚度特性曲线在轨在线辨识结果;图4为谐波减速器关节动态传动刚度线性项在轨在线辨识结果;图5为谐波减速器关节动态传动刚度非线性项在轨在线辨识结果;图6为谐波减速器关节间隙大小在轨在线辨识结果;图7为谐波减速器传动刚度地面试验测试装置;图8为谐波减速器关节动态传动刚度特性曲线地面离线辨识结果;图9为谐波减速器关节动态传动刚度线性项地面离线辨识结果;图10为谐波减速器关节动态传动刚度立方项地面离线辨识结果;图11为谐波减速器关节动态传动刚度迟滞项参数A的地面离线辨识结果;图12为谐波减速器关节动态传动刚度迟滞项参数α的地面离线辨识结果;图13为谐波减速器关节动态传动刚度迟滞项参数c的地面离线辨识结果;图14为辨识过程适应度函数变化曲线。1-航天器本体,2-天线伸出杆,3-天线反射面,4-步进电机,5-谐波减速器,6-光电编码器,7-输出轴,8-力矩传感器,9-惯量盘。具体实施方式下面结合附图并举实施例,对本发明进行详细描述。本发明提供了一种谐波减速器传动刚度测试方法,其主要思想在于:为了避免静态状态下测量出的传动刚度带来的误差,本发明通过控制使谐波减速器在带载条件下进行规律的正弦运动,之后,通过测量其输入、输出角度便可估计出刚度测量所需的扭转变形和加载力矩等信息,进而,利用相应的优化算法对构建的谐波减速器传动刚度动力学模型进行参数辨识,便可获得传动刚度参数的测量结果,即可获得谐波减速器的动态传动刚度。实施例1:针对在轨应用产品的在线测量传动刚度的获取方法:步骤一、配置实验测试硬件系统,通过驱动机构控制系统的控制,使输出端作规律的正弦运动或产品执行真实任务时的往复运动;其中,测量激励既可以设置给定规律、也可以直接利用产品实际服役中的往复运动,这使得谐波减速器传动刚度测量在产品研制和服役过程中均可方便进行。如图1所示,本实施例以航天器单轴驱动机构天线产品为对象,其包含驱动机构控制系统(在航天器本体1一侧,图中未画出)、天线伸出杆2、谐波减速器5关节和天线反射面3。其中,谐波减速器关节如图2所示,由步进电机4、谐波减速器5、光电编码器6和输出轴7四部分组成;其中,驱动机构控制系统既负责控制天线末端按给定规律运动,又负责谐波减速器关节刚度参数辨识过程的数据处理工作。为简明起见,单轴驱动机构天线实际产品中包含的压紧释放机构、线缆等部件没有在图1中画出。与传统测量方法不同的是:由于传统方法测量过程中谐波减速器关节处于准静止状态,其获得的传动刚度与其实际的传动刚度存在较大误差。为了避免出现上述问题,本发明根据谐波减速器关节的实际运动规律,进而获得在运动状态下谐波减速器关节的传动刚度。具体为:实际进行动态传动刚度测量时,将谐波减速器关节输出轴、天线反射面3及其支架组件作为谐波减速器的负载;将谐波减速器钢轮及相应的壳体组件固定;谐波减速器波的波发生器及步进电机4的输出轴作为输入端。输入端在驱动机构控制系统的控制下,使输出端按式(1)规律作正弦运动。其中,θoutput为输出角度;tCon为系统运行时间;根据航天器计算能力的实际情况,控制系统采用PD控制算法、控制周期为1ms。步骤二、建立谐波减速器关节传动刚度的动力学模型,并设置约束条件。S21、考虑到航天器在轨有限的测量条件,本发明建立如式(2)所示的三次方多项式作为谐波减速器关节传动刚度的动力学模型,该模型考虑了传动刚度的非线性因素和关节间隙。T=a1θ'+a2θ'3(2)其中,θ′=θ-Δ,θ>Δ0,|θ|≤Δθ+Δ,θ<-Δ]]>其中,a1,a2为待估计的刚度参数;T为输出力矩的测量值;θ为表征关节变形的相对角位移(含间隙),由输入/输出角度的测量值计算获得;Δ为谐波减速器关节间隙;θ'为关节的真实变形量(不含间隙),即关节扭转角;为了计算过程连续、方便,实际测试或应用中,式(2)中表征关节扭转角的分段函数可以用双曲线函数近似。S22、基于S21中建立的动力学模型,建立如式(3)所示的约束条件;该约束条件(收敛准则)为系统的实际输出数据序列和动力学模型预测输出序列的误差平方和最小为辨识优化准则;即:实际与模拟误差最小;J(θ′)=Σk=1L[Tk-f(θ′k)]2---(3)]]>其中,θ′k==θk-Δ,θk>Δ0,|θk|≤Δθk+Δ,θk<-Δ---(4)]]>f(θ'k)=a1θ'k+a2θ'k3式中,θ'k、θk、Tk分别为第k个扭转角、第k个相对角位移和第k个输出力矩值,L为数据长度;f(θ'k)为式(2)表征的动态传动刚度辨识模型在代入第k个相对角位移数据后的形式。步骤三、测试初始数据,获得运动学参数。由于任务执行过程和谐波减速器传动刚度测量过程合二为一,因此,要待系统运行一段时间后开始刚度参数的估计工作。通常情况下,根据上述控制系统的能力,选择待系统运行6~7秒后开始刚度参数辨识工作。这时,积累的可供参数辨识的原始数据有6000个。故根据公式(5)至公式(8),共获得6000组运动学参数。具体运动学参数的获取方法如下:利用步进电机参数计算谐波减速器关节输入角度θInput,见式(5)。θInput=qθ0n(5)式中,q为步进电机细分驱动器的倍频数,θ0为步进电机步距角,n为采样时间内控制系统给步进电机发出的脉冲个数。利用光电编码器6直接测量谐波减速器关节输出角度θoutput。利用差分算法,由采样时间序列、各时刻谐波减速器关节输入角度和各时刻谐波减速器关节输出角度分别计算输入角速度和输出角速度差分算法公式如下:θ·Input,k=θInput,k-θInput,k-1t,k=2,3,4,...,Lθ·Output,k=θOutput,k-θOutput,k-1t,k=2,3,4,...,L---(6)]]>其中,θInput,k、θOutput,k分别为第k个输入角度和输出角度测量值,分别为第k个输入角速度和输出角速度值,L为数据长度;t为第k个和第k-1个数据之间的时间间隔。由于均匀采样中各相邻两个数据之间的时间间隔相等,因此,下文t统一表示为两个相邻数据之间的时间间隔。根据输入角度和输出角度值,获得表征关节变形的相对角位移θk和相对角速度见式(7)、式(8)。其中,下标表示第k个值。θk=θOutput,k-θInput,kN,k=2,3,4,...,L---(7)]]>θ·k=θ·Output,k-θ·Input,kN,k=2,3,4,...L---(8)]]>式中,N为谐波减速器减速比。实际测试过程中,本发明的驱动机构控制系统采用非线性最小二乘算法进行动态传动刚度的在线估计。为了能够获得更加准确的运动学参数,本发明设置了数据滑动窗口,驱动机构控制系统在原始测量数据达到6000个以后就启动刚度参数辨识工作;后续,随着控制过程的执行,通过数据滑动窗口,不断地利用最新测量的运动学参数替换最早的测量的运动学参数,从而始终确保用于辨识的原始运动学参数为6000个。步骤四、根据步骤三中获得的6000组运动学参数,获得动力学参数。利用步骤三中的输入和输出角速度信息,采用差分法估计角加速度信息,并利用滑动平均滤波器对所得的角加速度数据进行滤波处理。θ··Output,k=θ·Output,k-θ·Output,k-1t,k=3,4,...,L---(9)]]>其中,为输出角加速度的第k个值。滑动平均滤波器的滑动步长一般可选择为5,其滤波公式见式(10):θ··‾Output,3=θ··Output,3]]>θ··‾Output,4=θ··Output,3+θ··Output,4+θ··Output,53]]>θ··‾Output,k=θ··Output,k-2+θ··Output,k-1+θ··Output,k+θ··Output,k+1+θ··Output,k+25,k=5,6,7,...,L-2---(10)]]>其中,为第k个滑动平均滤波处理后的输出角加速度值。利用谐波减速器关节输出端惯量(已知条件),直接用输出端惯量与输出角加速度数据相乘,获得谐波减速器关节输出端力矩Tk。其中,谐波减速器关节输出端惯量为产品的有效载荷和谐波减速器输出轴系组件的惯量之和,即测试时所需的加载力矩为产品实际运动过程中自身产生的惯性力矩,无需使用额外的加载设备。Tk=Jθ··‾Output,k---(11)]]>由相对角位移和关节输出力矩,计算平均相对角位移和关节平均输出力矩。具体为:先找出相对角位移的最小、最大值,然后由小到大按一定间隔找出给定相对角位移中心值附近对应的所有关节输出力矩和所有相对角位移,然后由这两组数据可以分别求出其平均值。将相对角位移θk(k=3,4,5,...,L)从小到大的排序处理,同时,获得其对应的输出力矩Tk(k=3,4,5,...,L),形成新的队列,分别定义为:θkk(kk=3,4,5,...,L)和Tkk(kk=3,4,5,...,L)。则对于k0到k0+λ范围内的一组相对角位移和输出力矩数据,可以求得该数据范围段内的平均相对角位移和平均输出力矩θ‾kNew=Σkk=k0k0+λθkkλ+1T‾kNew=Σkk=k0k0+λTkkλ+1---(12)]]>式中,k0的取值范围为3,λ+4,2λ+5,3λ+6,...,其最后一个取值为L-λ;λ表征平均处理时的数据间隔大小,为小于L的正整数,考虑到数据测量个数和平均处理精度的均衡,一般建议取值为4;下标kNew是新引入的计数标志,从自然数1开始取值,其最大取值kNewmax由L和λ决定,见式(13):kNewmax=L-2λ+1---(13)]]>数据长度L和λ为取值须确保kNewmax为正整数。步骤五、根据步骤三和步骤四中获得的参数,对步骤二中的建立的动力学模型进行参数辨识,获得传动刚度动力学模型刚度参数的估计值,即谐波减速器传动刚度的测量结果。在获得上述平均相对角位移和平均输出力矩序列后,式(2)所示的动态传动刚度模型可以改写为式(14)的形式。这时,可以利用带数据滑动窗口的非线性最小二乘算法对该模型进行参数估计,从而获得谐波减速器关节刚度的线性项a1和非线性项a2,以及关节间隙Δ的估计值。T‾kNew=a1θ‾′kNew+a2θ‾′kNew3,kNew=1,2,3,...,L-2λ+1---(14)]]>其中,θ‾′kNew=θ‾kNew-Δ,θ‾kNew>Δ0,|θ‾kNew|≤Δθ‾kNew+Δ,θ‾kNew<-Δ]]>其中,为关节平均扭转角。将获得的谐波减速器关节刚度线性项a1、刚度非线性项a2和间隙Δ的估计值代入公式(2)中,即获得传动刚度动力学模型表达式;在实际测试传动刚度时,将谐波减速器的相对角位移代入,即可获得谐波减速器关节输出力矩,进而确定输出力矩与相对角位移之间的关系,即传动刚度。利用上述方法获得的谐波减速器动态传动刚度结果如图3至图6所示。图3为根据刚度参数和间隙大小的辨识结果画出的谐波减速器关节传动刚度的特性曲线。其中,绿色实线为对谐波减速器关节的非线性刚度、迟滞效应、间隙、非线性摩擦、低频运动误差和阻尼等6种非线性因素进行精确测量后,建立的精确动力学模型给出的动态传动刚度的理想曲线(即产品实际曲线的最佳逼近值);蓝色实点为本实施例步骤四中,根据运动学参数估计给出的平均输出力矩和平均相对角位移数据序列;红色点画线为根据辨识的动态传动刚度参数和关节间隙值给出的刚度曲线。图4为谐波减速器关节动态传动刚度线性项a1的辨识结果。其中,红色点画线为实际辨识过程中的刚度线性项辨识结果的实际变化曲线;绿色直线为根据辨识结果给出的刚度线性项的平均值,该值也就是谐波减速器动态传动刚度线性项的最终测量值;蓝色实线为考虑上述6种非线性因素后的高精度动力学模型给出的理想值(即产品实际特性的最佳逼近值)。图5和图6各条曲线含义和图4类似。由图3至图6可以看出,谐波减速器关节动态传动刚度的测量过程随着任务的执行能逐渐趋于稳定;和产品最佳逼近值对比可知,测量与辨识过程给出的动态传动刚度模型参数a1,a2和谐波减速器关节间隙Δ的稳态精度分别优于94%、92%和85%。实施例2:针对地面测量传动刚度的获取方法:步骤1、配置实验测试硬件系统,通过驱动机构控制系统的控制,使输出端作规律的正弦运动:对于地面测量传动刚度的获取方法,其采用的装置可以与在轨在线测量时所采用的装置相同,也可以按照如图7所示的结构,采用增加附加测量设备的方法:由于无需考虑航天器的测量条件,故在地面测量传动刚度时,采用惯量盘9替代实施例1中的天线反射面3及其支架组件,以模拟有效载荷的惯量,其测量硬件系统还增加了力矩传感器8和力矩采集卡。实际进行动态传动刚度测量时,将惯量盘和谐波减速器关节输出轴作为谐波减速器的负载;将谐波减速器钢轮及相应的壳体组件固定;谐波减速器波的波发生器及步进电机4输出轴作为输入端。输入端在驱动机构控制系统的控制下,使输出端按实施例1的公式(1)规律作正弦运动。步骤2、建立谐波减速器关节传动刚度的动力学模型,并设置约束条件。第21步、考虑地面较为宽裕的测量条件,本发明建立如式(15)所示的谐波减速器关节的动力学模型,该模型考虑了传动刚度的非线性因素、刚度迟滞效应和关节间隙。T=a1(θ′)+a2(θ′)3+sign(θ·′)Aα+sign(θ·′)ce-sign(θ·′)αθ′]]>其中其中,a1,a2,A,α,c为待辨识的刚度参数;T为输出力矩的测量值;Δ为谐波减速器关节间隙;θ'、分别为扭转角和扭转角速度;θ、分别为表征关节变形的相对角位移和相对角速度,由输入/输出角度、输入/输出角速度、关节间隙等测量值计算获得。A,α,c为表征谐波减速器关节动态刚度迟滞效应的3个刚度参数;第22步、按照S22的方法,建立基于第21步中获得的动力学模型的约束条件。步骤3、采用步骤三的方法获取相关参数。步骤4、对于安装力矩传感器的,可采用力矩传感器8测量获得谐波减速器关节输出力矩。步骤5、根据步骤3和步骤4中获得的参数,对步骤二中的建立的动力学模型进行参数辨识,获得动力学模型刚度参数的估计值,即谐波减速器传动刚度的测量结果。采用加权系数(或称压缩因子)的粒子群优化算法,根据步骤2中建立的动力学模型,结合步骤3和步骤4中获得的参数,对动态传动刚度参数a1,a2,A,α,c进行估计,并最终代入步骤2中建立的动力学模型,最终在实际测量中获得传动刚度。利用上述方法获得的谐波减速器动态传动刚度结果如图8至图14所示。图8为根据刚度参数和间隙大小的辨识结果画出的谐波减速器关节传动刚度的特性曲线。其中,蓝色实点为对谐波减速器关节的非线性刚度、迟滞效应、间隙、非线性摩擦、低频运动误差和阻尼等6种非线性因素进行精确测量后,建立的精确动力学模型给出的动态传动刚度的理想曲线(即产品实际曲线的最佳逼近值);红色空心圈为根据辨识的动态传动刚度参数和关节间隙值给出的刚度曲线。图9至图13分别为动态传动刚度各参数的辨识结果,其中红色点画线为根据测量数据和动力学模型所获得的辨识值,蓝色实线为产品实际曲线的最佳逼近值。由图可知,谐波减速器关节动态传动刚度各参数a1,a2,A,α,c的辨识精度分别为99.51%、98.27%、97.56%、97.69%、97.22%。图14为粒子群算法辨识过程中,适应度函数的动态变化过程。由图可知,适应度函数在辨识过程中快速下降(越小越好),且最终趋于稳定值。说明辨识过程收敛快,辨识过程稳定。综上所述,以上仅为本发明的较佳实施例而已,并非用于限定本发明的保护范围。凡在本发明的精神和原则之内,所作的任何修改、等同替换、改进等,均应包含在本发明的保护范围之内。当前第1页1 2 3