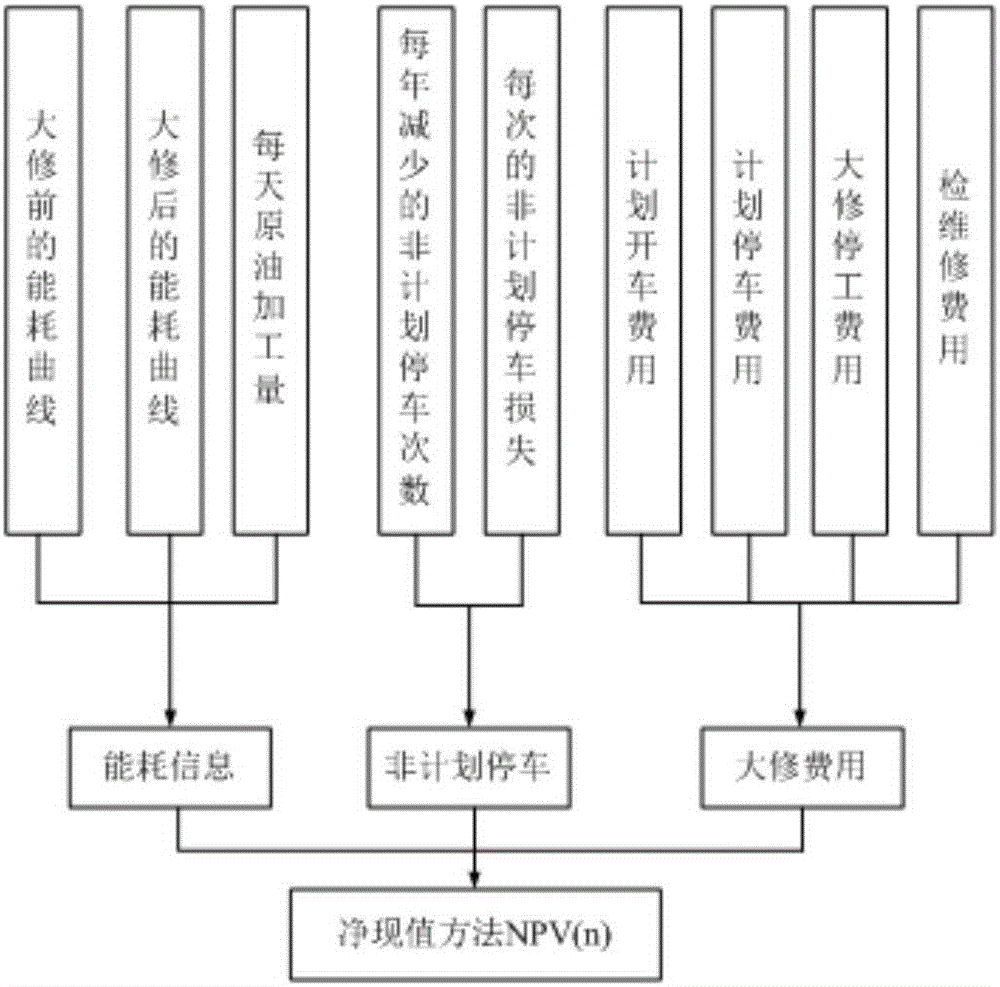
本发明涉及一种石油化工装置检修周期的经济性评价方法,属于石油化工的风险管理
技术领域:
。
背景技术:
:为满足国内能源日益增长的需求,国内石油石化企业生产规模不断扩大,生产技术不断提升,使得装置日趋大型化、连续化和自动化,且装置的结构也更加复杂。而随着使用时间的增加,装置或多或少会发生一些故障,这些故障会给企业的运行带来一定的影响。企业因设备故障产生的维修费用和生产损失已占到其生产总成本的30%~40%。某些行业已位居生产总成本的第二位,甚至更高。据统计,我国每年仅用于设备维修的支出就高达800多亿元,占我国资产总额的7%~9%,这导致企业的运行成本急剧上升,不利于的企业的可持续发展。目前,我国石油石化行业主要采用事后维修和预防维修等传统维修方式。而随着石油石化装置日趋大型化、复杂化和连续化的生产,企业对维护管理方面的要求也越来越高。传统维修方式主要依靠维修人员的经验,而不是依据设备的实际使用状态、使用条件和设备的失效风险来进行维修,不仅容易产生维修过剩和维修不足的现象,而且也没有考虑故障对社会和环境影响的严重程度。因此,如何有效地提高设备可靠性,降低企业维修费用,做到可靠性与经济性的平衡已成为现代石油石化企业检维修所面临的首要问题。技术实现要素:为解决上述技术问题,本发明提供一种能够根据设备的实际使用状态、使用条件和设备的失效风险来对石油化工装置进行维修的石油化工装置检修周期的经济性评价方法。本发明采用的技术方案为:本发明提供一种石油化工装置检修周期的经济性评价方法,包括:采集关于石油化工装置的运行状况数据,根据采集的运行状况数据来设定对所述石油化工装置进行检修的最长检修周期T;确定每个检修周期n内的大修费用、每年的非计划停车损失降低带来的收益和每年的能耗减少带来的收益;基于确定的大修费用、每年的非计划停车损失降低带来的收益和每年的能耗减少带来的收益,利用折现法确定每个检修周期内的年平均成本NPV(n);基于确定的年平均成本NPV(n),选取最佳的年平均成本所对应的检修周期作为最优检修周期;其中,检修周期n表示每隔n年对所述石油化工装置进行检修,n=1,2,…T。可选地,基于确定的大修费用、每年的非计划停车损失降低带来的收益和每年的能耗减少带来的收益,利用折现法确定每个检修周期n内的年平均成本NPV(n)的步骤具体包括:基于确定的大修费用、每年的非计划停车损失降低带来的收益和每年的能耗减少带来的收益来确定非大修年收益和大修年收益,其中非大修年收益=每年的非计划停车损失降低带来的收益+每年的能耗减少带来的收益,大修年收益=每年的非计划停车损失降低带来的收益+每年的能耗减少带来的收益-大修费用;基于确定的非大修年收益和大修年收益,计算折现后的年现值N(t),其中,其中r为折现率,t=1,2,…n;基于折现后的年现值N(t),计算每个检修周期n内的年平均成本NPV(n)=∑N(i)/n,i=1,2,…n。可选地,所述大修费用包括检维修费用、计划性开车费用、计划性停车费用和大修停工损失费用。可选地,所述检维修费用、计划性开车费用、计划性停车费用基于实际情况来确定,所述大修停工损失费用等于大修时间、检修周期修正因子、每天的利润三者的乘积。可选地,所述非计划停车损失降低带来的收益通过每年减少的非计划停车次数和每次的非计划停车损失来确定。可选地,所述每年减少的非计划停车次数随着石油化工装置的运行状况而动态更新,所述每次的非计划停车损失基于石油化工装置的风险等级状况来确定。可选地,所述能耗减少带来的收益随着石油化工装置的运行状况而动态更新。本发明的另一实施例还提供一种最优石油化工装置检修周期评价系统,包括:检修周期设定模块,采集关于石油化工装置的运行状况数据,根据采集的运行状况数据来设定对所述石油化工装置进行检修的最长检修周期T;费用和收益确定模块,确定每个检修周期n内的大修费用、每年的非计划停车损失降低带来的收益和每年的能耗减少带来的收益;年平均成本确定模块,基于确定的大修费用、每年的非计划停车损失降低带来的收益和每年的能耗减少带来的收益,利用折现法确定每个检修周期内的年平均成本NPV(n),其中,检修周期n表示每隔n年对所述石油化工装置进行检修,n=1,2,…T;最优检修周期确定模块,基于确定的年平均成本NPV(n),选取最佳的年平均成本所对应的检修周期作为最优检修周期。可选地,所述年平均成本确定模块基于以下步骤来确定每个检修周期内的年平均成本NPV(n):基于确定的大修费用、每年的非计划停车损失降低带来的收益和每年的能耗减少带来的收益来确定非大修年收益和大修年收益,其中非大修年收益=每年的非计划停车损失降低带来的收益+每年的能耗减少带来的收益,大修年收益=每年的非计划停车损失降低带来的收益+每年的能耗减少带来的收益-大修费用;基于确定的非大修年收益和大修年收益,计算折现后的年现值N(t),其中,其中r为折现率,t=1,2,…n;基于折现后的年现值N(t),计算每个检修周期n内的年平均成本NPV(n)=∑N(i)/n,i=1,2,…n。本发明的石油化工装置检修周期的确定由于不是单纯依靠维修人员的经验来确定最佳大修周期,而是根据装置的实际运行状况来计算每个检修周期的年平均成本,选取年平均成本最大的检修周期为最佳检修周期,考虑了经济性,对企业制定检修策略给出了可参考的经济性指标,避免由于经验判断失误所带来的经济损失,降低了企业的维修费用。附图说明图1是本发明的最优石油化工装置检修周期评价方法的流程图。图2是本发明的最优石油化工装置检修周期的评价方法的概括性示意图。图3是本发明的一实施例的非计划停车次数与大修周期关系图。图4是本发明的一实施例的能耗与大修周期关系图。图5是本发明的最优石油化工装置检修周期评价系统的结构示意图。图6至图12是本发明一实施例的最优石油化工装置检修周期评价的示意图。具体实施方式以下结合附图对本发明的具体实施方式进行描述。【本发明的技术思想】本发明的技术思想是通过计算每个检修周期内的大修费用、非计划停车损失降低带来的收益和能耗减小带来的收益,然后计算将这三者折合到实际大修年的现值之和的年平均值,选取年平均值最大值所对应的检修周期作为石油化工装置的最优检修周期,即实际检修周期。需要注意的是,在阅读本发明后,本领域的技术人员可以基于企业的运营状况和企业的石化装置承压设备的运行状况来确定每个检修周期内的大修费用、非计划停车损失降低带来的收益和能耗减小带来的收益。【最优石油化工装置检修周期评价方法】如图1所示,本发明的一实施例提供的最优石油化工装置检修周期评价方法可包括以下步骤:S101:采集关于石油化工装置的运行状况的数据,根据采集的运行状况数据来设定最长的检修周期T;S102:确定每个检修周期n内的大修费用、非计划停车损失降低带来的收益和能耗减少带来的收益;S103:基于确定的大修费用、每年的非计划停车损失降低带来的收益和每年的能耗减少带来的收益,利用折现法确定每个检修周期n内的年平均成本NPV(n);S104:基于确定的年平均成本NPV(n),选取最大的年平均成本所对应的检修周期作为实际的检修周期。其中,在上述步骤中,检修周期n表示每隔n年对石油化工装置进行检修,n=1,2,…T,例如,n=2表示在第2年开始进行检修,以后每隔2年对石油化工装置进行一次检修。以下,对上述步骤S101至S104进行具体说明。S101:采集关于石油化工装置的运行状况的数据,根据采集的运行状况数据来设定最长检修周期T具体地,可采集关于企业的石油化工装置的运行状况的数据,根据采集的运行状况数据来设定最长的检修周期T,然后基于采集企业的运营状况和企业的石化装置的运行状况数据来设定最长检修周期T,如可根据企业的经济状况、未来的战略规划、设备的运行状况等来制定出一个合适的最长的检修周期。S102:确定每个检修周期n内的大修费用、非计划停车损失降低带来的收益和能耗减少带来的收益1.确定大修费用确定大修费用是指确定大修当年所发生的维修费用,可包括检维修费用、计划性开车费用、计划性停车费用和大修停工损失(如图2所示),即大修费用=计划开车费用+计划停车费用+大修停工费用+检维修费用。以下分别对这些子费用的计算进行介绍。(1)检维修费用。可根据大修有效性制定,最终由企业的设备检维修滚动计划模块读入或拟合得出。大修有效性是指所制定的检修策略所带来的效果,即不同的检修策略会产生不同的检修效果。可根据大修有效性来确定检维修费用,具体的确定步骤可基于实际情况来确定,一般是大修有效性越高,表示检修准备得越充分,需要检修的时间(大修天数)会更长,相应的检维修费用会越高。在本发明的一实施例中,为更形象的体现所制定的检修策略的有效性,采用大修有效性因子来表示,即通过赋予大修有效性因子不同的数值来表示大修有效性的等级,在一示例中,0.2表示最差,1表示最好。大修有效性、检维修费用、大修天数和大修有效性因子的关系可如下表1所示。表1检维修费用与大修有效性的关系表大修有效性(检修策略)检维修费用大修天数大修有效性因子无效果(临时大修)aa10.2差(一般准备常规大修)bb10.4一般有效(充分准备常规大修)cc10.6通常有效(一般准备基于风险大修)dd10.8高度有效(充分准备基于风险大修)ee11备注:表1中的检维修费用和大修天数的具体数值需要基于实际情况给出,即企业可根据实际情况来确定。(2)计划性开车费用,需要企业根据实际情况来确定。(3)计划性停车费用,需要企业根据实际情况来确定。(4)大修停工损失费用可根据下述公式确定:大修停工损失费用=大修时间×检修周期修正因子×每天的利润。其中,大修时间可根据上述表1得到,一般,在相同的有效性的前提下,检修周期越长,大修的时间就越长。检修周期修正因子为对检修周期的修正系数,是指随着检修周期的增加,大修时间内的维修费用也随之增加的系数,一般检修周期越长,相应的检修周期修正因子也越大,检修周期修正因子可根据具体的检修周期来确定,在本发明的一实施例中,检修周期修正因子与检修周期n之间的关系可如下表2所示。表2检修周期修正因子每天的利润可基于每天的原油加工量和每吨油的利润来计算,每天的利润=每天的原油加工量×每吨油的利润,每吨油的利润和每天的原油加工量可基于实际情况确定。2.确定非计划停车次数减少带来的收益在本发明中,非计划停车次数减少带来的收益是指由于对设备进行了检修而给企业带来的非计划停车次数的减少次数。每个检修周期n内的每年的非计划停车次数减少带来的收益可为每年减少的非计划停车次数×每次的非计划停车损失。(1)每年减少的非计划停车次数随着设备运行时间的增长,设备的非计划停车次数会增加。需要对基于设备运行的非计划停车次数记录进行拟合,拟合曲线会随着设备的运行可动态更新。例如:以3年为一个检修周期。第一年的第1-6个月,统计的非计划停车为1次;第一年的第7-12个月,统计的非计划停车为2次,第二年的第1-6个月,统计的非计划停车为3次;第二年的第7-12个月,统计的非计划停车为5次,第三年的第1-6个月,统计的非计划停车为5次;第三年的第7-12个月,统计的非计划停车为6次。则将统计的非计划停车次数1、2、3、5、5、6这些点进行直接连线或最小二乘法拟合。这里的拟合曲线会随着设备的运行可动态更新是指:随着不断增加的统计点,曲线会不停的变化。在本发明中,非计划停车次数曲线可分为大修前Pb(t)和大修后Pa(t)两种。本发明中,大修后非计划停车概率曲线可表示为:Pa(t)=Pb(t)-(Pb(t)-Pmin)×IF,其中,Pmin为最低的非计划停车概率,单位次/年;IF为大修有效性因子;t为检修周期n内的年数,t=1,2,…n,n=1,2,…T。其中,计划停车概率Pmin可为企业期望的数值,例如,可根据每年的年度指标等来确定,大修前非计划停车次数曲线为Pb(t)可根据实际情况来确定,大修有效性因子IF可根据前述表1来确定。可根据大修前后非计划停车次数曲线Pb(t)和Pa(t),计算大修后检修周期内,每年减少的非计划停车次数P(t)=(Pb(t)-Pa(t))。本发明以最简单的线性关系为例进行说明,如图3所示,非计划停车次数与大修周期t之间的关系为简单的线性关系,图3中示出的最长大修周期为8年,但并不局限于此。参考图3可知:1)大修前非计划停车概率较高,大修后停车次数降低。以两年修一次为例,对于每一个检修周期,非计划停车概率曲线均是相同的,因此可只选取1个检修周期为计算对象。2)若不大修,非计划停车次数为Pb(t),大修后每年非计划停车天数降低为Pa(t),非计划停车减少的次数为Pb(t)-Pa(t)。(2)每次的非计划停车损失每次的非计划停车损失可包括非计划开车、停车和非计划停工损失。其中,非计划开车损失和非计划停车损失,可根据企业的实际情况来得出。非计划停工损失=每次非计划停工小时数×每小时的利润。每次非计划停车小时数,可通过基于装置设备风险等级状况来确定。一般设备风险等级越高,每次非计划停车小时数会相应增加。装置设备风险等级可根据以可靠性为中心的维修(RCM)来确定设备的风险等级,一般可分为A、B、C类,其中A类对应风险级别为高和中高的设备,B类对应风险级别为中的设备,C类对应风险级别为低的设备,具体的风险等级确定方法可参阅如公告号为CN103632058A、发明名称为“承压设备动态风险评估系统”的中国专利申请所揭示的内容。每小时利润损失=每天的原油加工量×每吨油的利润/24。如此,可计算每次的非计划停车损失:每次的非计划停车损失=非计划开车费用+非计划停车费用+非计划停工损失。这样,可得到每年非计划停车次数减少带来的收益,每年非计划停车次数减少带来的收益=每年减少的非计划停车次数×每次的非计划停车损失3.确定能耗减少带来的收益能耗可包括燃料、动力和热输出。随着设备运行时间的增长,能耗会增大,需要对设备运行的能耗记录拟合,并且拟合曲线可根据设备的运行数据动态更新,能耗记录拟合与前述非计划停车次数记录拟合一样。能耗减少带来的收益可根据石化装置所使用的单吨油的能耗来计算。单吨油的能耗曲线可分为大修前eb(t)和大修后ea(t)两种,大修后单吨油能耗曲线可表示为:ea(t)=eb(t)-(eb(t)-emin)×IF。其中,emin为单吨油的最低能耗,单位为元/吨,可根据实际情况得出;t为检修周期;IF为大修有效性因子,可根据上述表1得出;t为检修周期n内的年数,t=1,2,…n,n=1,2,…T。首先,确定大修前单吨油能耗随时间的变化曲线为eb(t)。然后,根据大修前后能耗曲线eb(t)和ea(t),计算大修后检修周期内每年能耗降低带来的收益E(t)=(eb(t)-ea(t))×每天的原油加工量×一年的天数(例如365)。本发明以最简单的线性关系为例进行说明,如图4所示,每吨油的能耗与大修周期t之间的关系为简单的线性关系,图4中示出的最长大修周期为8年,但并不局限于此。参考图4可知:(1)大修前能耗较高,大修后能耗降低。以两年修一次为例,对于每一个检修周期,能耗曲线均是相同的,因此为简单起见,选取1个检修周期为计算对象。(2)若不大修,单吨油能耗为eb(t),大修后单吨油的能耗为ea(t),单吨油的能耗降低收益为eb(t)-ea(t)。S103:基于确定的大修费用、每年的非计划停车损失降低带来的收益和每年的能耗减少带来的收益,利用折现法确定每个检修周期n内的年平均成本NPV(n)具体地,S103可包括以下步骤:(1)基于确定的大修费用、每年的非计划停车损失降低带来的收益和每年的能耗减少带来的收益来计算非大修年收益和大修年收益,其中非大修年收益=每年的非计划停车损失降低带来的收益+每年的能耗减少带来的收益,大修年收益=每年的非计划停车损失降低带来的收益+每年的能耗减少带来的收益-大修费用。(2)基于确定的非大修年收益和大修年收益,计算折现后的年现值N(t),即计算检修周期n内的各年现值,也就是说,从时间t为1年到n年逐年计算各年现值。其中,折现后的年现值N(t)=年收益(非大修年的收益或者大修年的收益)×年折现系数,其中,以大修年为基准,年折现系数可为其中r为折现率,t=1,2,…n,这样其中r为折现率,t=1,2,…n,折现率可根据企业期望盈利来确定。假如设定的检修周期为2年,第1年为大修年,则N(1)=大修年收益×年折现系数。假设大修年收益为100万元,根据年折现系数公式可知年折现系数为则N(1)=100×1.1=110万元。N(2)=非大修年收益×年折现系数,假设非大修年收益为120万元,根据年折现系数公式可知年折现系数为则N(2)=120×0.826=99.12万元。(3)基于折现后的年现值N(t),计算每个检修周期n内的年平均成本NPV(n)=∑N(i)/n,i=1,2,…n。S104:基于确定的年平均成本NPV(n),选取最大的年平均成本所对应的检修周期作为实际的检修周期比较步骤S103计算的每个检修周期内年平均成本,即分别比较NVP(1),NPV(2),NVP(3)…NPV(n),选取最大的年平均成本,用公式表示如下:MAX=Max﹛NVP(1),NPV(2),NVP(3)…NPV(n)﹜,n=1,2…T选择NPV(n)值最大时对应的检修周期为最优检修周期,并将每个检修周期的NPV(n)值进行输出,供企业参考使用。【最优石油化工装置检修周期评价系统】本发明的另一实施例提供一种最优石油化工装置检修周期评价系统,如图5所示,可包括:检修周期设定模块1,采集关于石油化工装置的运行状况的数据,根据采集的运行状况数据来设定对所述石油化工装置进行检修的最长检修周期T;费用和收益确定模块2,确定每个检修周期n内的大修费用、每年的非计划停车损失降低带来的收益和每年的能耗减少带来的收益;年平均成本确定模块3,基于确定的大修费用、每年的非计划停车损失降低带来的收益和每年的能耗减少带来的收益,利用折现法确定每个检修周期内的年平均成本NPV(n),其中,检修周期n表示每隔n年对所述石油化工装置进行检修,n=1,2,…T;最优检修周期确定模块4,基于确定的年平均成本NPV(n),选取最佳的年平均成本所对应的检修周期作为最优检修周期。所述年平均成本确定模块3可基于以下步骤来确定每个检修周期内的年平均成本NPV(n):基于确定的大修费用、每年的非计划停车损失降低带来的收益和每年的能耗减少带来的收益来确定非大修年收益和大修年收益,其中非大修年收益=每年的非计划停车损失降低带来的收益+每年的能耗减少带来的收益,大修年收益=每年的非计划停车损失降低带来的收益+每年的能耗减少带来的收益-大修费用;基于确定的非大修年收益和大修年收益,计算折现后的年现值N(t),其中,其中r为折现率,t=1,2,…n;基于折现后的年现值N(t),计算每个检修周期n内的年平均成本NPV(n)=∑N(i)/n,i=1,2,…n。本实施例的最优石油化工装置检修周期评价系统对石油化工装置的最优检修周期的具体确定方法与上述最优石油化工装置检修周期评价方法一样,为避免赘述,在此省略对其详细介绍。【实施例】某炼化企业常减压装置需要进行大修,设定的大修时间为2008年6月1日,计划大修天数为14天,大修有效性为一般有效,数据来源与该企业的企业估算库及企业滚动计划。在数据库中得到历时的非计划停车信息如图6所示,从数据库中得到的历时能耗曲线如图7所示,根据这些信息设定最长检修周期为8年。图8至图12分别是根据选择的大修有效性来计算的净现值的示意图,其中图8为大修有效性选择无效果所计算的净现值,参照图8可知,最优的检修周期为2年。图9为大修有效性选择差所计算的净现值,参照图9可知,最优的检修周期为2年。图10为大修有效性选一般有效所计算的净现值,参照图10可知,最优的检修周期为3年。图11为大修有效性选通常有效所计算的净现值,参照图11可知,最优的检修周期为2年。图12为大修有效性选高度有效所计算的净现值,参照图12可知,最优的检修周期为2年。以上所描述的装置实施例仅仅是示意性的,其中所述作为分离部件说明的单元可以是或者也可以不是物理上分开的,作为单元显示的部件可以是或者也可以不是物理单元,即可以位于一个地方,或者也可以分布到多个网络单元上。可以根据实际的需要选择其中的部分或者全部模块来实现本实施例方案的目的。本领域普通技术人员在不付出创造性的劳动的情况下,即可以理解并实施。通过以上的实施方式的描述,本领域的技术人员可以清楚地了解到各实施方式可借助软件加必需的通用硬件平台的方式来实现,当然也可以通过硬件。基于这样的理解,上述技术方案本质上或者说对现有技术做出贡献的部分可以以软件产品的形式体现出来,该计算机软件产品可以存储在计算机可读存储介质中,如ROM/RAM、磁碟、光盘等,包括若干指令用以使得一台计算机设备(可以是个人计算机,服务器,或者网络设备等)执行各个实施例或者实施例的某些部分所述的方法。最后应说明的是:以上实施例仅用以说明本发明的技术方案,而非对其限制;尽管参照前述实施例对本发明进行了详细的说明,本领域的普通技术人员应当理解:其依然可以对前述各实施例所记载的技术方案进行修改,或者对其中部分技术特征进行等同替换;而这些修改或者替换,并不使相应技术方案的本质脱离本发明各实施例技术方案的精神和范围。当前第1页1 2 3