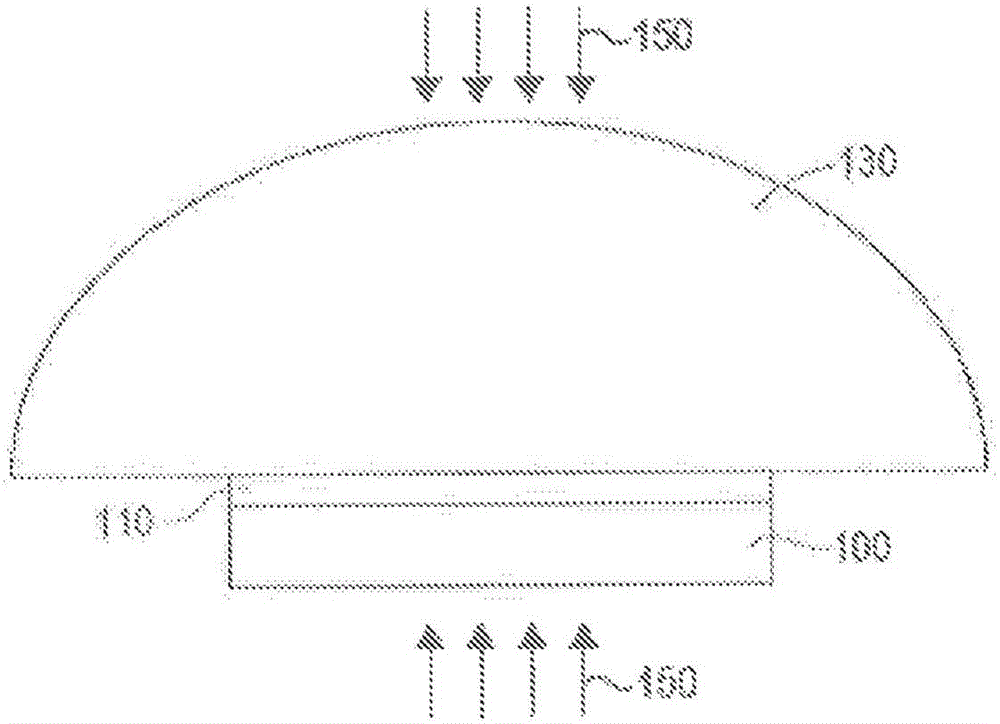
本申请要求于2014年7月23日提交的美国临时专利申请号No.62/027,968的权益和优先权,其所有的公开内容通过引用合并于本申请。
技术领域:
在各个实施例中,本发明涉及一种发出紫外(UV)辐射的光发射器。
背景技术:
:由于有源区的高缺陷水平,基于氮化物的半导体系统的短波紫外发光二极管(UVLED)(即发射小于350nm波长的光的LED)的输出功率、效率和寿命仍是有限的。这种限制在设计波长小于270nm的器件中尤其成问题(且显著)。大部分的研发努力在形成于异质衬底(诸如蓝宝石)上的器件上进行,尽管采用创新的缺陷减小策略,缺陷密度仍然很高。这些高缺陷密度限制了生长在这种衬底上的器件的效率和可靠性。最近提出的低缺陷、结晶氮化铝(AlN)衬底具有显著改进基于氮化物的光电半导体器件的潜力,尤其是铝浓度高的器件,因为这些器件的有源区具有较少的缺陷。例如,相比于形成在其它衬底上的类似器件,伪共晶地生长在AlN衬底上的UVLED显示出更高的效率、更高的功率和更长的寿命。通常,这些伪共晶UVLED被安装成封装在“倒装芯片”结构中,其中器件有源区产生的光通过AlN衬底发射,同时LED芯片的前表面结合到多晶(陶瓷)AlN底座。由于这种器件的有源器件区可实现较高的晶格完整性,其内效率可达到60%以上。然而,这些器件中的光子提取效率仍然通常很低,使用表面图案化技术可达到约4%至约15%。由于一些原因,相比于可见光LED,短波长UVLED的光子提取效率较低。因此,目前的短波长UVLED的电光转化效率(WPE)较低,最高仅几个百分点,其中WPE被定义为二极管可实现的可用光功率(在本案中指发射的UV光)除以加到器件上的电功率。LED的WPE可通过电效率(ηel)、光子提取效率(ηex)和内效率(IE)的乘积计算出来,即WPE=ηel×ηex×IE。IE本身是电流注入效率(ηinj)和内量子效率(IQE)的乘积,即IE=ηinj×IQE。因此,低的ηex会负面地影响WPE,甚至是在通过降低内部晶格缺陷(通过使用例如上述AlN衬底作为器件平台)提高IE之后。几个因素可能与较低的光子提取效率有关。首先,即使是能够获得的最高质量的AlN衬底,通常也在UV波长范围内具有一些吸收,甚至在比AlN的带边更长的波长(其约为210nm)处。这种吸收会导致器件有源区产生的一些UV光在衬底中被吸收,因此会减少从衬底表面发出的光的量。另外,因为产生的光子中的约一半被导向p型接触并被该接触的p-GaN吸收,因此UVLED会变差。即使当光子被导向AlN表面时,由于AlN的较大的折射率,通常仅约9.4%能从未处理的表面逃逸,这导致较小的逃逸锥面。由于AlN衬底的吸收,另一部分光子在到达出射表面的过程中损失。这种损失是逐渐增加的,并且光子提取效率的平均值是仅约2.5%。在标准的LED制造中,LED结构与空气之间的折射率的较大差异(及其导致的光子提取的不足)可通过使用具有中间折射率的封装而大大改善。特别地,许多现有的设计的特点在于置于LED上且至少部分地围绕LED(接下来通过热处理固化)的封装材料“穹顶”。封装增加了经过半导体芯片的顶表面的全内反射的临界角,这从而使可见光LED的光子提取效率显著提高。然而,LED密封剂和粘合剂容易被UV辐射损坏,导致密封剂和粘合剂的退化。这种退化在暴露于UVC辐射(即,波长小于300nm的辐射)下尤其严重。因此,使用密封剂来改善光子提取通常对于UVLED没有效果。此外,尽管已经开发出了抗UV密封剂,但这些化合物暴露于UV光时显示出退化,远达不到UVLED所需的使用寿命。例如,纽约埃尔姆斯福德的SchottNorthAmerica有限公司的DeepUV-200密封剂在暴露于300nm的光仅1000小时之后,显示透明度降低了15%。因此,需要一种容易实施的方法来有效地增加UVLED的光子提取效率,该方法解决了缺乏对于UV辐射(特别是UVC辐射)透明的稳定密封剂的问题。这种方法能够令人满意地实现UVLED的高透明度和高可靠性,且在这些器件的预期使用寿命期间无明显的退化,例如约10,000小时或甚至更长时间。技术实现要素:在本发明的多个实施例中,通过使用一层薄的密封剂(例如,有机化合物)将无机透镜(通常是刚性的)直接接附到LED芯片来提高UV发光器件(诸如UVLED)的光子提取效率。在一些实施例中,密封剂为液体或凝胶,例如硅油和/或硅树脂。透镜通常包括UV透明材料(诸如蓝宝石、熔融二氧化硅或石英),或基本上由UV透明材料构成,或由UV透明材料构成。也可使用其他透镜材料,例如,折射率大于1.3、透明且在暴露于高强度短波长UV辐射时稳定的材料。透镜的使用使得提取出来的UVLED的准连续波输出功率至少加倍(甚至高达2.6倍或甚至更高)。此外,器件的远场图案(FWHM)可变窄至少20%。透镜优选地被成形为使将经受全内反射的辐射的量最小化。通常,透镜为圆形或半球形,但是其他形状也落入本发明的范围内。在多个实施例中,透镜的形状具有圆柱形部件和半球形部件,以例如使远场图案更窄。在其他实施例中,透镜包括(或基本由以下部件构成,或由以下部件构成):大致平的板,或表面被图案化或纹理化以增强其光子提取的平板。例如,平板可被图案化以形成菲涅耳透镜,从而改善对于以较大角度接近表面的光子的光子提取。本发明的多个实施例具有初始暴露于UV光下就会退化的有机密封剂。特别地,这种有机密封剂在暴露于UV光时(例如,在由器件发光的初期)可能经历部分氧化,改变密封剂的折射率和/或形成小的局部区域,来自器件芯片的光在该局部区域散射,从而降低到达透镜并从该处最终发射的UV光的量。根据本发明的多个实施例,通过额外地暴露于UV光,这种密封剂出人意料且有益地至少部分地被转化为非化学计量比二氧化硅材料,改善了其输出特性。特别地,当密封剂在暴露于UV光的该初始“老化”阶段被至少部分地转化成非化学计量比二氧化硅材料时,密封剂的碳含量降低至例如约40at.%(原子百分比)或更低,约30at.%或更低,或甚至约20at.%或更低,之后密封剂的透光度显著地改善,且能够稳定至少数千小时的器件操作时间。在多个实施例中,转化为非化学计量比二氧化硅材料后的密封剂的碳含量为约5at.%或更大,约10at.%或更大,或者约15at.%或更大。因此,根据本发明的多个实施例,在被暴露于UV光一初始阶段(例如,高至约200小时,高至约300小时,或约100小时至约200-300小时之间)后,转化的密封剂对于UV导致的透射率进一步下降基本免疫。根据本发明的多个实施例,非化学计量比二氧化硅材料包括硅、氧和碳,或基本由硅、氧和碳构成或甚至由硅、氧和碳构成。其中碳含量大于1ppm(且通常大于1at.%),且约为30at.%或更低,或甚至约20at.%或更低。随着长时间地暴露于UV光,非化学计量比二氧化硅材料的成份接近纯二氧化硅的成份,但是通过诸如二次离子质谱(SIMS)的表征方法可检测到微量的碳。本发明的实施例使用UV光的波长选自约100nm至约400nm的范围。优选的实施例使用波长选自约100nm至约280nm,或者甚至更优选地约210nm至约280nm的范围的UVC光。其它实施例使用UVA光(即,波长选自约315nm至约400nm的范围的光)或者UVB光(即,波长选自约280nm至约315nm的范围的光)。在一些实施例中,密封剂的转化会使得密封剂变脆,因此透镜很可能会变松或者从发光芯片上脱离。在这种实施例中,一种额外的接附件可被用于进一步确保透镜与芯片的接触。例如,接附件可以为树脂(例如,可为不透明的环氧树脂),器件部分地浸入其中。树脂优选地至少轻微地(例如,约0.3mm或更少)延伸到芯片(或变脆的密封剂)与透镜之间的界面上方,从而在器件操作和处理期间进一步稳定透镜。在多个实施例中,接附件可包括(或基本由以下部件构成或由以下部件构成)于2015年4月6日提交的美国专利申请序列号No.14/679,655(‘655号申请)中描述的不透明树脂(和/或其他阻挡层),其全部公开通过引用合并于本申请。接附件和/或阻挡层基本防止UV光穿过大部分这种密封剂,因此防止了其退化和裂纹(或其他机械失效)。在本发明多个实施例中,接附件和/或阻挡层包括所述密封剂自身的一部分,或基本由密封剂自身的一部分构成,或由密封剂自身的一部分构成,所述密封剂自身的一部分与所述LED芯片邻接且对所述LED芯片发出的UV光不透明。(在这种实施例中,远离所述LED芯片的密封剂的其余部分也可以是对UV光不透明的或透明的,因为这种较远的密封剂一般不会传播所发出的UV光。)本文所用的“不透明”材料基本上不传播某一特定波长或波长范围的光(例如UV光),而是对所述特定波长或波长范围的光呈反射性和/或较强的吸收性(例如在较小的厚度上)。在本发明的其他实施例中,所述阻挡层包括固体不透明遮蔽物,或基本由固体不透明遮蔽物构成,或由固体不透明遮蔽物构成,所述固体不透明遮蔽物置于所述LED芯片和所述密封剂之间,因此所述密封剂自身对UV光可以是透明的或不透明的。例如,所述遮蔽物可以由对UV光基本呈反射性的金属(例如铝)构成。通过这种方式,本发明的实施例包括具有较长的寿命,较高的输出功率和较高的可靠性的封装的UVLED。一方面,本发明的实施例的特征在于一种组装和老化照明器件的方法。在紫外(UV)发光半导体芯片上提供一层有机密封剂。将所述密封剂的至少一部分暴露于UV光以将所述密封剂的所述部分中的至少一些转化为非化学计量比二氧化硅材料。非化学计量比二氧化硅材料包括硅、氧和碳,或基本由硅、氧和碳构成,或由硅、氧和碳构成。非化学计量比二氧化硅材料的碳含量大于1ppm且小于40原子百分比。本发明的实施例可以以任意各种组合包括以下中的一个或多个。暴露于UV光可在标称器件操作(即,由用户和/或在较大装置中的器件操作,和/或在电流水平下的器件操作,操作温度和/或器件周围环境的氧含量是“标称的”,即基于器件的设计和结构的推荐的正常操作)之前进行。密封剂所暴露的UV光可由半导体芯片发出,在至少一部分暴露期间,半导体芯片可以被操作在不同于(例如,高于或低于)标称电流水平的电流水平、不同于(例如,高于或低于)标称操作温度的操作温度、和/或在不同于(例如,高于或低于)标称氧含量的周围环境的氧含量中。暴露于UV光可在封装器件(例如,用于交运)和/或交运到用户之前进行。暴露于UV光可在将器件放置在使用半导体芯片发出的UV光的较大系统(例如,用于切割,成像,消毒等)之中或之上的步骤之前进行。器件在将密封剂暴露于UV光之前可以初始输出功率发射UV光,和/或一旦将密封剂暴露于UV光就立刻以初始输出功率发射UV光,输出功率可降低至最小值(即,低于初始值的值)并恢复到接近初始值(即,约70%至约100%)的最终值。密封剂可被暴露于UV光至少一段足以使器件的输出功率恢复到最终值的时间。密封剂暴露于UV光可导致气态副产物(例如甲醛)从密封剂中形成和/或其他副产物扩散出密封剂。密封剂可被暴露于UV光至少一段足以使气态副产物的形成和/或扩散基本停止(例如,检测不到)的时间。密封剂暴露于UV光可导致密封剂的碳含量的降低。密封剂可被暴露于UV光至少一段足以使密封剂的碳含量降低到约40原子百分比或更低,约30原子百分比或更低,约20原子百分比或更低,约10原子百分比或更低,约5原子百分比或更低,或甚至约1原子百分比或更低的时间。密封剂所暴露的UV光的波长可以与半导体芯片所发出的UV光的波长相同。密封剂所暴露的UV光的波长可以与半导体芯片所发出的UV光的波长不同。非化学计量比二氧化硅材料的碳含量可大于1原子百分比。非化学计量比二氧化硅材料的碳含量可小于30原子百分比,小于20原子百分比,小于10原子百分比,或甚至小于5原子百分比。刚性透镜可被放置在相对于所述半导体芯片的密封剂上。刚性透明可为无机的。所述刚性透镜可包括熔融二氧化硅、石英和/或蓝宝石,或由熔融二氧化硅、石英和/或蓝宝石构成,或基本由熔融二氧化硅、石英和/或蓝宝石构成。接附材料可被放置在所述半导体芯片的至少一部分的周围以及所述刚性透镜的至少一部分的周围。接附材料可包括树脂,或由树脂构成,或基本上由树脂构成。接附材料可对UV光不透明。接附材料的顶表面可放置为比所述刚性透镜的底表面高不大于0.5mm。接附材料的顶表面可放置为比所述刚性透镜的底表面高不大于0.3mm。通过施加足以使所述刚性透镜和所述半导体芯片之间的所述密封剂的厚度最小化的力,可以使所述刚性透镜接附到所述半导体芯片。在所述刚性透镜被接附之后,所述密封剂的厚度可不足以阻挡所述刚性透镜与所述半导体芯片之间的由热膨胀失配引入的应变的传递。在刚性透镜接附之后,密封剂的厚度可为约10μm或更小,约8μm或更小,或甚至约5μm或更小。所述刚性透明可为至少部分地半球形。所述刚性透明可为基本半球形。所述刚性透镜具有基本半球形的部分以及置于其下方的基本圆柱形的部分。所述刚性透镜可为平板。所述刚性透镜的顶表面的至少一部分被图案化或纹理化以增强从中的光发射。所述密封剂在暴露于UV光之前可包括有机硅,或由有机硅构成,或基本上由有机硅构成。所述密封剂在暴露于UV光之前可包括硅油或硅树脂,或由硅油或硅树脂构成,或基本上由硅油或硅树脂构成。在暴露于UV光之前,密封剂可具有大于40原子百分比的碳含量。在暴露于UV光之后,非化学计量比二氧化硅材料可具有小于30原子百分比的碳含量。阻挡可被置于半导体芯片和密封剂的至少一部分之间。阻挡可包括(或主要由以下材料构成,或由以下材料构成)对UV光不透明的材料。阻挡可包括(或主要由以下材料构成,或由以下材料构成)对UV光不透明的树脂。阻挡可包括(或主要由以下材料构成,或由以下材料构成)对UV光呈反射性的材料。阻挡材料可包括铝和/或聚四氟乙烯,或由铝和/或聚四氟乙烯构成,或基本上由铝和/或聚四氟乙烯构成。半导体芯片可为发光二极管芯片或激光芯片。密封剂的至少一部分可被暴露于UV光一段时间,该段时间为约50小时至约500小时,约100小时至约400小时,约100小时至约300小时,约200小时至约300小时,或约200小时。所述密封剂的至少一部分可被暴露于由半导体芯片发出的UV光。至少一部分密封剂所暴露的UV光的至少一部分可由半导体芯片以外的装置发出(例如,不同的发光半导体芯片,UV灯等)。所述至少一部分密封剂可被暴露于半导体芯片和半导体芯片以外的装置发出的UV光。所述至少一部分密封剂可被暴露于波长选自约210nm至约280nm的范围(例如,约250nm至约270nm)的UV光。在另一方面,本发明的实施例的特征还在于照明器件,其包括(或基本由以下部件构成):紫外(UV)发光半导体芯片,用于从所述发光半导体芯片提取光的刚性透镜,以及放置在所述刚性透镜与所述发光半导体芯片之间的密封剂层。至少一部分密封剂层包括(或基本由以下材料构成,或由以下材料构成)通过暴露于UV光而被转化为非化学计量比二氧化硅材料的有机材料。非化学计量比二氧化硅材料包括硅、氧和碳,或基本由硅、氧和碳构成,或由硅、氧和碳构成。非化学计量比二氧化硅材料的碳含量大于1ppm且小于40原子百分比。本发明的实施例可包括以下任意组合的变型中的一个或多个。非化学计量比二氧化硅材料的碳含量可大于1原子百分比。非化学计量比二氧化硅材料的碳含量可小于30原子百分比,小于20原子百分比,小于10原子百分比,或甚至小于5原子百分比。至少一部分密封剂层可包括(或基本由以下材料构成,或由以下材料构成)通过暴露于波长选自约210nm至约280nm的范围的UV光而被转化为非化学计量比二氧化硅材料的有机材料。另一方面,本发明的实施例的特征在于照明器件,其包括(或基本由以下部件构成):紫外(UV)发光半导体芯片,用于从所述发光半导体芯片提取光的刚性透镜,以及放置在所述刚性透镜与所述发光半导体芯片之间的非化学计量比二氧化硅材料层。非化学计量比二氧化硅材料包括硅、氧和碳,或基本由硅、氧和碳构成,或由硅、氧和碳构成。非化学计量比二氧化硅材料的碳含量大于1ppm且小于40原子百分比。本发明的实施例可包括以下任意组合的变型中的一个或多个。非化学计量比二氧化硅材料层可以为有机密封剂层(例如,包括有机硅、基本由有机硅构成或由有机硅构成的密封剂,)的一部分,和/或放置在有机密封剂层之中。非化学计量比二氧化硅材料的碳含量可大于1原子百分比。非化学计量比二氧化硅材料的碳含量可小于30原子百分比,小于20原子百分比,小于10原子百分比,或甚至小于5原子百分比。另一方面,本发明的实施例的特征在于照明器件,其包括(或基本由以下部件构成):紫外(UV)发光半导体芯片,以及放置在所述半导体芯片的上方和/或周围的密封剂层。至少一部分密封剂层包括(或基本由以下材料构成,或由以下材料构成)通过暴露于UV光而被转化为非化学计量比二氧化硅材料的有机材料。非化学计量比二氧化硅材料包括硅、氧和碳,或基本由硅、氧和碳构成,或由硅、氧和碳构成。非化学计量比二氧化硅材料的碳含量大于1ppm且小于40原子百分比。本发明的实施例可包括以下任意组合的变型中的一个或多个。密封剂层可为透镜的形状。非化学计量比二氧化硅材料的碳含量可大于1原子百分比。非化学计量比二氧化硅材料的碳含量可小于30原子百分比,小于20原子百分比,小于10原子百分比,或甚至小于5原子百分比。密封剂层可被放置在所述半导体芯片的顶表面上方。阻挡材料被放置为接近所述半导体芯片的侧壁。阻挡材料可对UV光不透明。阻挡材料可包括不透明树脂、铝和/或聚四氟乙烯,或由不透明树脂、铝和/或聚四氟乙烯构成,或基本上由不透明树脂、铝和/或聚四氟乙烯构成。至少一部分密封剂层可包括(或基本由以下材料构成,或由以下材料构成)通过暴露于波长选自约210nm至约280nm的范围的UV光而被转化为非化学计量比二氧化硅材料的有机材料。又一方面,本发明的实施例的特征在于照明器件,其包括(或基本由以下部件构成):紫外(UV)发光半导体芯片,以及放置在所述半导体芯片的上方和/或周围的非化学计量比二氧化硅材料层。非化学计量比二氧化硅材料包括硅、氧和碳,或基本由硅、氧和碳构成,或由硅、氧和碳构成。非化学计量比二氧化硅材料的碳含量大于1ppm且小于40原子百分比。本发明的实施例可包括以下任意组合的变型中的一个或多个。非化学计量比二氧化硅材料的碳含量可大于1原子百分比。非化学计量比二氧化硅材料的碳含量可小于30原子百分比,小于20原子百分比,小于10原子百分比,或甚至小于5原子百分比。非化学计量比二氧化硅材料层可被放置在所述半导体芯片的顶表面上方。阻挡材料被放置为接近所述半导体芯片的侧壁。阻挡材料可对UV光不透明。阻挡材料可包括不透明树脂、铝和/或聚四氟乙烯,或由不透明树脂、铝和/或聚四氟乙烯构成,或基本上由不透明树脂、铝和/或聚四氟乙烯构成。另一方面,本发明的实施例的特征在于照明器件,其包括(或基本由以下部件构成):紫外(UV)发光半导体芯片以及放置在所述半导体芯片的上方和/或周围的密封剂层。密封剂层的第一部分包括(或基本由以下材料构成,或由以下材料构成)通过暴露于UV光而被至少部分地转化为非化学计量比二氧化硅材料的有机材料。密封剂层的第二部分包括有机密封剂(例如有机硅),或基本由有机密封剂(例如有机硅)构成,或由有机密封剂(例如有机硅)构成。非化学计量比二氧化硅材料包括硅、氧和碳,或基本由硅、氧和碳构成,或由硅、氧和碳构成。非化学计量比二氧化硅材料的碳含量大于1ppm且小于40原子百分比。本发明的实施例可包括以下任意组合的变型中的一个或多个。密封剂层的第一部分包括(或基本由以下材料构成,或由以下材料构成)通过暴露于波长选自约210nm至约280nm的范围的UV光而被至少部分地转化为非化学计量比二氧化硅材料的有机材料。非化学计量比二氧化硅材料的碳含量可大于1原子百分比。非化学计量比二氧化硅材料的碳含量可小于30原子百分比,小于20原子百分比,小于10原子百分比,或甚至小于5原子百分比。密封剂层的第一部分可被放置在所述半导体芯片的顶表面上方。密封剂层的第二部分可被放置为接近所述半导体芯片的侧壁。密封剂层的第二部分被放置在半导体芯片顶表面的上方且比密封剂层的第一部分更远离半导体芯片的顶表面。密封剂层的第一部分可放置在密封剂层的第二部分之中,和/或至少部分地被密封基层的第二部分围绕。阻挡材料可被放置在半导体芯片的侧壁和密封剂层的第二部分之间。阻挡材料可对UV光不透明。阻挡材料可包括铝、聚四氟乙烯和/或不透明树脂,或由铝、聚四氟乙烯和/或不透明树脂构成,或基本上由铝、聚四氟乙烯和/或不透明树脂构成。又一方面,本发明的实施例的特征在于照明器件,其包括(或基本由以下部件构成):紫外(UV)发光半导体芯片,以及放置在所述半导体芯片的上方和/或周围的密封剂层。密封剂层的第一部分包括非化学计量比二氧化硅材料,或基本由非化学计量比二氧化硅材料构成,或由非化学计量比二氧化硅材料构成。密封剂层的第二部分包括有机密封剂(例如有机硅),或基本由有机密封剂(例如有机硅)构成,或由有机密封剂(例如有机硅)构成。非化学计量比二氧化硅材料包括硅、氧和碳,或基本由硅、氧和碳构成,或由硅、氧和碳构成。非化学计量比二氧化硅材料的碳含量大于1ppm且小于40原子百分比。本发明的实施例可包括以下任意组合的变型中的一个或多个。非化学计量比二氧化硅材料的碳含量可大于1原子百分比。非化学计量比二氧化硅材料的碳含量可小于30原子百分比,小于20原子百分比,小于10原子百分比,或甚至小于5原子百分比。密封剂层的第一部分可被放置在所述半导体芯片的顶表面上方。密封剂层的第二部分可被放置为接近所述半导体芯片的侧壁。密封剂层的第二部分被放置在半导体芯片顶表面的上方且比密封剂层的第一部分更远离半导体芯片的顶表面。密封剂层的第一部分可放置在密封剂层的第二部分之中,和/或至少部分地被密封剂层的第二部分围绕。阻挡材料可被放置在半导体芯片的侧壁和密封剂层的第二部分之间。阻挡材料可对UV光不透明。阻挡材料可包括铝、聚四氟乙烯和/或不透明树脂,或由铝、聚四氟乙烯和/或不透明树脂构成,或基本上由铝、聚四氟乙烯和/或不透明树脂构成。通过参照以下说明、附图和权利要求,这些和其他目的,以及本文公开的本发明的优点和特征将变得更加清晰。此外,应该理解的是,本文描述的各个实施例的特征并非互相排斥的,并且可以各种组合和排列存在。本文所用的术语“基本”和“约”意指±10%,在一些实施例中,指±5%。术语“基本由...构成”意指排除有助于功能的其它材料,除非本文另有限定。尽管如此,这种其它材料可共同地或单独地以微量存在。在本文中,术语“辐射”和“光”可交换使用,除非另有说明。附图说明在附图中,相似的附图标记在不同视图中一般指相同的部件。此外,附图不一定按比例绘制,而重点通常放在示出本发明的原理。在以下说明中,参考附图对本发明的各个实施例进行了说明,其中:图1A和图1B以截面示出了根据本发明的多个实施例的刚性透镜到发光芯片的接附;图1C为具有平板式刚性透镜的发光器件的截面示意图;图1D为具有纹理化平板式刚性透镜的发光器件的截面示意图;图2A为根据本发明的多个实施例的具有发光芯片、密封剂和刚性透镜的照明器件在室温下的截面示意图;图2B为图2A的密封剂内的应力状态的放大示意图;图3A为根据本发明的多个实施例的具有发光芯片、密封剂和刚性透镜的照明器件在升高的温度下的截面示意图;图3B为图3A的密封剂内的应力状态的放大示意图;图4A为本发明实施例中使用的半导体芯片的截面示意图;图4B示出了根据本发明的实施例执行衬底厚度被减薄和纹理化之后图4A的发光芯片;图5示出了根据本发明的实施例的具有和不具有施加到其上的刚性透镜的UVLED所发出的光强的曲线;图6示出了根据本发明的实施例的具有和不具有施加到其上的刚性透镜的发光芯片的远场图案;图7示出了根据本发明的实施例的透镜尺寸对于接附到其上的发光芯片发出的光的变形的影响;图8为根据本发明的实施例的具有接附到发光芯片的半球形和圆柱形部分的透镜的截面示意图;图9为本发明多个实施例中光子提取效率和远场图案随透镜尺寸和密封剂厚度的变化的表格;图10为根据本发明的多个实施例的UV发光器件的相对输出功率与时间的关系图;图11A示出了根据本发明的多个实施例的有机密封剂材料中发生的示例性光化学反应;图11B为根据本发明的多个实施例在图11A所示的光化学反应期间的器件的部分截面示意图;图11C为根据本发明的多个实施例在图11A所示的光化学反应后器件的部分截面示意图;图12为根据本发明的多个实施例的密封剂在暴露于UV光之前(0小时)以及暴露48小时和1300小时之后的密封剂的显微红外光谱表征结果的曲线图;图13A为根据本发明的实施例的在暴露于UV光之前的密封剂的能量色散X射线(EDX)光谱测量的图谱;图13B为根据本发明的实施例的在暴露于UV光之后48小时的密封剂的能量色散X射线(EDX)光谱测量的图谱;图13C是根据本发明的实施例的在暴露于UV光之后200小时的密封剂的能量色散X射线(EDX)光谱测量的图谱;图13D是根据本发明的实施例的在暴露于UV光之后1300小时的密封剂的能量色散X射线(EDX)光谱测量的图谱;图14为图13A至图13D的密封剂的大致成份的曲线图;图15A至图15C为根据本发明的多个实施例的包括转化成非化学计量比二氧化硅材料的密封剂的器件的截面示意图;图15D为根据本发明的多个实施例的包括转化成非化学计量比二氧化硅材料的密封剂以及未转化的密封剂和/或阻挡材料的器件的截面示意图;图15E和15F为根据本发明的多个实施例的包括转化成非化学计量比二氧化硅材料的密封剂的器件的截面示意图;图15G为根据本发明的多个实施例的包括转化成非化学计量比二氧化硅材料的密封剂以及未转化的密封剂和/或阻挡材料的器件的截面示意图;图15H为根据本发明的多个实施例的包括转化成非化学计量比二氧化硅材料的密封剂的器件的截面示意图;图16为根据本发明的多个实施例的包括刚性透镜和接附材料的器件的截面示意图。具体实施方式本发明的实施例包括通过使从衬底传播到周围环境的光的全内反射最小化而提高诸如UVLED的发光器件的光子提取效率的方法。该技术使用对短波UV辐射透明的薄薄的一层(例如,约10μm或者甚至更薄)的密封剂(例如环氧)。图1A示出了半导体芯片100,其表面120上放置有密封剂110,还示出了即将通过密封剂110接附到芯片100的透镜130。在一些实施例中,在芯片100在接附到透镜130之前,密封剂110被施加到透镜130的表面140,而不是芯片100的表面120,或者密封剂110除了被施加到芯片100的表面120外,还被施加到透镜130的表面140。半导体芯片100可包括发光器件或基本由发光器件构成,诸如LED或激光器。在多个实施例中,芯片100发射UV光,例如UVC光。发光芯片100在芯片100的“有源”发光区域内可包括AlN衬底及其上的一个或多个量子阱和/或应变层,该应变层包括AlN、GaN、InN或它们的二元或三元合金,或者该应变层基本上由AlN、GaN、InN或它们的二元或三元合金构成。在多个实施例中,芯片100包括的衬底和/或器件结构类似于以下文件中所详细描述的衬底和/或器件结构:于2006年8月14日提交的美国专利No.7,638,346,于2010年4月21日提交的美国专利No.8,080,833,和/或于2014年3月13日提交的美国专利申请公开No.2014/0264263,上述文件的全部公开内容通过引用合并于本文。密封剂110可为有机的和/或聚合的。在本发明的多个实施例中,密封剂110是有机硅基的,可包括例如硅油和/或硅树脂,或者基本由例如硅油和/或硅树脂构成,或者由例如硅油和/或硅树脂构成。在接附透镜130之前,芯片100的表面120可以被处理成例如粗糙的、纹理化的和或图案化的,以使从中的光子提取最大化(即,通过为逃离光增加临界角),如2010年4月21提交的美国专利序列号No.12/764,584所述,其全部公开内容通过引用合并于本文。如图1B所示,透镜130通过密封剂110(其还可具有粘附性)被接附到芯片100。透镜130通常为刚性的,且在多个实施例中,至少在形状上部分地为半球状。透镜130可以大致为半球形,如图1A和1B所示,或者由大致半球形的部分和大致圆柱形(如下文所述)的部分构成。在一些实施例中,透镜130包括(或基本由以下部件构成,或由以下部件构成):如图1C所示的大致平的板,或如图1D所示的表面被图案化或纹理化以改善其中的光子提取的平板。透镜130通常是无机的,可包括(或基本由以下物质构成,或由以下物质构成)例如熔融二氧化硅,石英和/或蓝宝石。在一些实施例中,密封剂110被加热(例如,至约60℃)以提供足够的流动性,从而在透镜130与芯片100之间大体上无缝隙地形成界面。通常,密封剂110在仍具有足够粘性的温度下被加热,以使透镜130能够适当地定位在芯片100上,即使是它们接触之后。(至少在一些实施例中,可以在室温下施加诸如硅油的液体密封剂。)在一些实施例中,向芯片100和/或透镜130施加力(图1B中以箭头150表示)以最小化它们之间的空间,从而也最小化其中的密封剂110的厚度。即便是在密封剂110退化(由于,例如暴露于来自芯片100的UV光)的实施例中,该层的薄薄的厚度也可防止器件性能的灾难性退化。透镜130被定位在芯片100上之后,整个结构的可被升至更高的温度(例如,到达约150℃至约170℃持续0.5小时至2小时),以固化密封剂110,使透镜130牢固地接附到芯片100。在一些实施例中,在透镜130被定位到芯片100之前,密封剂110可被至少部分地固化。例如,密封剂(例如分配到透镜和/或芯片100上的)可被加热到例如约150℃至约170℃保持0.5至1小时。本发明的多个实施例使用密封剂材料的薄层以至少在暴露于UV光的初期改善这种层的恶化效应。例如,尤其是对于大功率LED,本发明的多个实施例使用厚度低于约10μm的密封剂层,如于2012年7月提交的美国专利申请序列号No.13/533,093中所详细描述的,其全部公开通过引用合并于本文。在多个实施例中,器件(包括例如芯片100、密封剂110和透镜)可在固化密封剂110之前、期间和/或之后被放置于真空中,以促进陷于密封剂中和/或贴近密封剂的任何空气和/或气泡的排出。例如,器件可被置于真空度例如低于10Torr的真空炉中。可在室温(例如,约25℃)下施加真空,或者,如果密封剂同时正在被至少部分地固化,可在固化温度(例如,如上文所述)下或室温与固化温度之间的中间温度下施加真空。施加真空的时间例如可为约5分钟至约20分钟,或者,施加真空的时间为固化时间(例如,如上文所述)或者约5分钟与固化时间之间的中间时间。在多个实施例中,通过使密封剂层尽可能地薄来提高整个器件(即,接附有刚性透镜的半导体芯片)的寿命。可通过在固化程序期间向透镜和/或芯片施加力而实现这种厚度的最小化。密封剂厚度的最小化通常致使密封剂厚度不足以将密封剂作为热膨胀失配缓冲层(在这种情况下,人们通常会增加密封剂厚度来阻止其中的应变传递并提高器件的可靠性)。图2A、图2B、图3A和图3B示出了(来自例如光发射期间芯片的升高的温度)温度变化对根据本发明多个实施例的组装器件内部的应变分布的影响。图2A和图2B示出了组装的器件和密封剂110在约室温下(例如,组装后但芯片100未操作时)的应变状态分布。如图所示,由于器件处于大约其组装的温度,因此基本没有来自芯片100与透镜130之间和/或在芯片100与透镜130之间传递的热失配应变,尽管它们的热膨胀是不同的。图2B示出了,在这种情况下,密封剂110中基本没有表明这种热失配应变存在的剪切应力。相比之下,图3A和图3B示出了组装的器件和密封剂110在升高的温度下(例如,芯片100操作期间)的应变状态分布。如图所示,透镜130与芯片100之间的热膨胀系数的差异导致了热失配应变在二者之间传递,如穿过整个密封剂110层的剪切应力和变形所指示的。特别地,在这种情况下,密封剂110的厚度不足以适应热失配引起的应变并阻止其在芯片100与透镜130之间传递。(,在密封剂的厚度足够厚的对比情况中,至少部分密封剂层会非常类似于图2B中所示的密封剂110,因为该层内的剪切应力会按比例缩小。)芯片100的线性热膨胀系数可以大于透镜的线性热膨胀系数,例如大于约10倍或更多。在一个实施例中,芯片100(或至少其支撑一个或多个有源发光层的衬底部分)包括单晶AlN(或基本由单晶AlN构成),且具有约5×10-6/K的线性膨胀系数,而透镜130包括二氧化硅(或基本由二氧化硅构成),且具有约0.6×10-6/K的线性膨胀系数。无论穿过密封剂110的整个厚度的剪切应力的量以及透镜130与芯片100之间传递的热膨胀失配引起的应变的量有多大,由于密封剂110的厚度被最小化,组装器件的光学性能出人意料地优异,其限制了由光致密封剂退化导致的光传播的减少。热失配应变的影响可通过降低芯片100的厚度而降低,例如,通过去除其上形成有发光层的衬底的至少一部分。这种减薄可与上述表面图案化(参照图1A和图1B所示)一起附加地或结合地执行,如于2010年4月21日提交的美国专利号No.8,080,833所述,其全部公开通过引用合并于本文。图4A示意性示出了包括衬底600及其上的层状区域610的半导体芯片100,该层状区域610包括(或基本由以下部件构成):一个或多个外延沉积的半导体层,其包括芯片100的有源区(即发光区)。衬底600通常是半导体材料,例如硅,GaN,GaAs,InP或AlN,但在多个实施例中,包括单晶AlN,或基本由单晶AlN构成,或由单晶AlN构成。在芯片100为发光器件的实施例中,如本领域技术人员所公知的,层状区域610通常包括一个或多个缓冲层、帽层、接触层、量子阱、多量子阱(MQW)区域(即,由薄的势垒阻挡层分隔的多个量子阱)。为了减轻热失配应变对芯片100的影响并增强来自芯片的光传输,至少部分衬底600可被移除和/或纹理化,如图4B所示。例如,如果衬底600的厚度变化高于约20μm,那么背表面120可用例如600至1800的打磨轮打磨。该步骤的移除率可有目的地保持在低水平(约0.3至0.4μm/s),以避免对衬底600或者层状区域610的损伤。在可选的打磨步骤之后,可用抛光浆料抛光背表面120,例如,等量的蒸馏水和商业获得的KOH缓冲液与水中的二氧化硅胶态悬浮体的溶液。该步骤的移除率可在约10μm/min至约15μm/min之间变化。衬底600可被减薄到约200μm至约250μm厚,或者甚至约20μm至约50μm厚,尽管如此,本发明的范围并不受限于该区间。在另一实施例中,衬底600被减薄到约20μm或更低,或甚至基本全部被移除。减薄步骤之后可进行晶片清洗,例如在一种或多种有机溶剂中。在本发明的一个实施例中,清洗步骤包括将衬底浸入沸腾的丙酮约10分钟,然后浸入沸腾的甲醇约10分钟。衬底600被清洗后,其表面120可以通过在合适的溶液(例如,碱性溶液,诸如去离子(DI)水中KOH)中刻蚀来图案化,即纹理化。在本发明的另一实施例中,刻蚀剂为DI水中的NaOH溶液。碱性溶液的摩尔浓度可在约1M至约20M之间变化,刻蚀时间可在约1分钟至约60分钟之间变化。刻蚀溶液的温度可在约室温高至约100℃之间变化。当使用摩尔浓度更高的溶液和更短的时间时可获得类似的结果,反之亦然。在本发明的一个实施例中,衬底600在4M的KOH和DI水的溶液中被刻蚀8分钟,该溶液被保持在约20℃。刚性透镜130可以从所需材料的较大片形成为所需的形状和尺寸,或者可直接“模制”成所需的形状和尺寸。例如,根据本发明的多个实施例,使用溶胶-凝胶工艺形成透镜130。例如,为了制造熔融二氧化硅透镜,含有纳米级二氧化硅颗粒的前驱体化学溶液可被放入模具并在该模具中变浓为凝胶。然后变浓的部分从模具中被转移并干燥,形成开孔材料,该开孔材料具有可填充气体的孔隙。然后干燥的部分在例如大于1000℃的温度下被烧结,在烧结期间,该部分收缩到所需的尺寸并致密化为基本等同于熔融二氧化硅且在深UV下具有高透明度的材料。透镜130可包含来自例如前驱体溶液的微量的碳或其他元素。本文所描述的透镜(诸如“熔融二氧化硅”等等)还包括通过溶液工艺(诸如溶胶-凝胶工艺)形成的这种材料,即使这种材料也含有微量的诸如碳的元素(尽管在本发明的多个实施例中,透镜130的碳含量低于1ppm)。当生产刚性透镜(诸如上述熔融二氧化硅透镜)时,诸如溶胶-凝胶工艺的可模制工艺能够以高再现性和低成本调整精确的尺寸和形状。由于密封剂110的折射率与空气相比较高(例如在160nm处约1.4),因此根据斯涅尔定律计算出来的从衬底600(例如AlN)进入密封剂110的全内反射的临界角增加,其进而增加器件的光子提取效率。然后透镜130提取几乎所有来自密封剂110的光,因为透镜具有相似的折射率(例如在260nm处约1.5)。透镜130也通常比芯片100的尺寸大(例如沿横向尺寸,诸如宽度或直径),从而从芯片100提取出尽可能多的光。在一个实施例中,芯片100一侧约为0.8mm,透镜130为半球形,其直径约为2mm。如图5所示,示例性的UVLED的输出功率增加了约2.6倍,其具有用密封剂110薄层额外接附到芯片100上的半球形熔融二氧化硅透镜130。图5包括没有透镜130时发射光的强度随波长变化的曲线700,以及具有透镜130时发射光的强度随波长变化的曲线710。通过选择无机透镜材料及其表面的形状,也可改善发光半导体芯片100(例如LED)的辐射图案。图6示出了具有和不具有用密封剂110薄层接附到LED芯片100的半球形透镜的LED的辐射图案的半高宽(FWHM)。如图所示,不具有透镜130的LED芯片100的远场图案800的FWHM为约120°,而具有透镜130的LED芯片100的远场图案810的FWHM为约72°。通过使用下文详细描述的圆柱-半球形透镜甚至可以进一步降低远场图案。通常,如果密封剂很薄,接附了半球形透镜的LED在接附透镜后的发射的辐射图案仍为朗伯型(如图6所示)。然而,发射表面的尺寸通常会被额外的透镜放大。放大的量等于透镜的折射率,并且通过使透镜的直径相对于LED的尺寸较大而减少LED的变形。即(如图7所示),sinθ2=n*sinθ1(2)sinθ4=n*sinθ3(4)其中,光线900从垂直于半球形透镜130的平表面920的方向上从LED100上的点920发射的光线;X1为点920与LED100的中心点930之间的距离;X2为点940与中心点930之间的距离,点940为光线900的出射光线的反向延长线与平表面920的交点;r为半球形透镜130的半径;θ1为光线900的入射角;θ2为光线900的传播角;n为半球形透镜130的折射率;光线950为从点910发射并穿过中心点930正上方的点的光射线;X3为点960与中心点930之间的距离,点960为光线950的出射光线的反向延长线与半球形透镜130的平表面的交点;θ3为光线950的入射角;θ4为光线950的传播角。如上述公(1)和公式(3)式所示,当X1远小于r时,X2/X1与X3/X1都趋近于n,并且两条反向延长线几乎相交于透镜130的平表面的同一点。对于边界长度(或对于圆形芯片而言的直径)与透镜130半径r的二倍(即直径)相当的芯片100,芯片100的图像(以及因此从中发射的光)会变形。因此,在本发明的多个实施例中,透镜130的直径显著大于(例如,至少大2倍,大5倍或甚至大10倍或更多)芯片100的边界长度或直径,从而使芯片100发出的光的变形最小化。根据本发明的多个实施例,通过使用具有圆柱部件以及半球形部件的形状的透镜130,如图8和9所示,芯片100(例如LED)的远场发散度被改善,对光子提取效率的影响很小,或没有影响。图8示出了具有粗糙化(即,纹理化)表面120且通过密封剂110(例如有机硅基密封剂)薄层接附到这种透镜130的LED芯片100(例如,中UVLED)。如图所示,透镜130具有半球形部分1000和圆柱形部分1010(例如,具有等于半球形部分1000的最大直径的恒定直径),圆柱形部分1010具有厚度或“圆柱高度”1020。进行仿真以确定各种不同实施例的光子提取效率和远场发散度。如图9的Case1所示,将仿真结果与无透镜130或密封剂110的裸(但粗糙化的)LED光子提取效率的基线值进行比较。Cases2和3表示透镜130纯为半球形(即,无圆柱形部件)的实施例,其显示了上文所述的光子提取效率的增加以及远场发散度的适度改善。如图9所示,增加透镜的圆柱形部件的厚度能够将远场发散度降低到至少40°FWHM,对光子提取效率没有负面影响或仅有微量影响,并且甚至能够降低到更低(即,降低至至少25°),且对光子提取效率仅有微小影响(其仍比Case1基线值的光子提取效率有较大改善。)这种近准直的UV光束对于使用集中光束的某些应用而言是必须的。同样如图9所示,透镜直径的增加也趋于改善光子提取效率并降低远场发散度,同样如上文所述。除了改善单个半导体芯片的光子提取效率,当使用两个或多个半导体芯片(例如LED芯片)构成的阵列时,本发明的实施例呈现出类似的结果。例如,可使用具有刚性透镜的4×4的芯片阵列,其刚性透镜的直径显著大于(例如,至少大2倍、5倍或甚至10倍或更多)阵列的边界长度或直径从而使光的变形最小化。对于不同尺寸的阵列(即芯片数量不同)进行建模并显示出,为了使光子提取效率的改善类似于包含一个小半导体芯片的实施例,透镜的直径比整个阵列的边界长度或直径相对更大是有必要的。建模结果在下表中示出。LED阵列尺寸阵列边界长度透镜材料透镜直径光子提取效率远场FWHM1×10.8×0.8mmN/AN/A1.0×120°1×10.8×0.8mm熔融二氧化硅2mm2.2×114°3×33.8×3.4mm熔融二氧化硅6mm1.9×140°3×33.8×3.4mm熔融二氧化硅8mm2.2×134°4×45.3×4.7mm熔融二氧化硅8mm1.9×144°4×45.3×4.7mm熔融二氧化硅10mm2.2×140°5×56.8×6.0mm熔融二氧化硅10mm1.9×144°5×56.8×6.0mm熔融二氧化硅14mm2.2×134°此外,发光半导体芯片的3×3阵列被集成有直径6mm的刚性透镜,其显示出了1.4倍的光子提取效率的改善,即使透镜不够大,不足以充分优化光子提取效率。因此,包含更大的透镜的本发明的实施例将表现出2倍甚至更多倍的光子提取效率的改善。本发明的多个实施例包含在暴露于UV光时会退化的有机密封剂,诸如硅油或硅树脂。特别地,这种有机密封剂在暴露于UV光时(例如,在器件发光的初期)会经历部分氧化,改变密封剂的折射率,和/或形成小的局部区域,来自于发光芯片的光在该局部区域散射,降低到达透镜并从该处最终发射的UV光的量。根据本发明的多个实施例,在最终包装、交运给用户和/或将UV器件合并到有益地使用到发射的UV光的较大系统或装置(例如,用于液体和/或气体的消毒、净化和/或灭杀系统,医疗器械,成像系统,固化系统,印刷系统,光学传感器等)之前的老化期间,通过额外地暴露于UV光,这种密封剂出人意料且有益地至少部分地被转化为非化学计量比二氧化硅材料。特别地,当密封剂被至少部分地转化成非化学计量比二氧化硅材料时,密封剂的碳含量降低至例如小于40at.%,小于30at.%,或甚至小于20at.%,并且密封剂的透光度改善相当大,且能够稳定至少上千小时的器件操作时间。在多个实施例中,在暴露于UV光之后,密封剂被转化成非化学计量比二氧化硅材料,该材料基本由碳、氧和硅构成,或者由碳、氧和硅构成,其中碳含量大于1ppm(且在一些实施例中大于1at.%)且小于30原子半分比,或甚至小于20at.%。在这种实施例中,如上文详述的对于较小密封剂厚度的偏好可以放宽,并且密封剂可具有大于10μm(或甚至大于50μm)的厚度和/或甚至可以用于替代刚性透镜130。图10为根据本发明实施例的UV发光器件的相对输出功率的曲线图,其结合了上述密封剂的转换工艺。如图所示,当密封剂在老化期间1000(即,最终的包装和交运到用户之前的制造工序中)初始暴露于来自器件的UV光时,输出功率大幅下降了一段小于200小时的时间。然后,在继续暴露于UV光之后,输出功率在200-400小时的时间后逐步上升到几乎与初始输出功率一样高的水平(例如,短暂的初始功率水平的约80%-90%),然后在高达至少2000小时的用户操作期间1010,输出功率仍基本随器件操作时间恒定。如图10所示,初始输出功率的降低通常对应于器件制造期间以及器件销售给用户前的“老化”工序;因此,一旦这种器件被提供给用户,其在使用中不会表现出这种输出功率的大幅下降。图10所示的数据为暴露于波长约为263nm的UV光,尽管如此,本发明的实施例并不限于这种特定的波长且可使用任意波长的UV光(例如,UVC光)。图11A示出了密封剂在根据本发明的多个实施例中可能经历的光化学反应。如图所示,密封剂可以为硅油,即具有有机侧链的液态聚合硅氧烷。密封剂被暴露于来自发光芯片的高能UV光子,并且经过含碳侧链至羟基侧链的中间转换,密封剂被逐步转化为非化学计量比的二氧化硅材料(并且最终甚至转换为二氧化硅)和水。如图11B所示,在转换过程中,密封剂110的一小部分可因此被转化为具有不同折射率的材料,从而形成散射中心1100且导致散射事件,其在器件制造期间执行的老化工序中降低器件的输出功率。一旦密封剂110的大部分,或者甚至全部,被转化成非化学计量比的二氧化硅材料1110(或者最终甚至是二氧化硅),如图11C所示,散射事件的数量被降低或基本消除,并且输出功率恢复到图10中所示的较高水平图12示出了根据本发明的实施例的密封剂在暴露于UV光之前(0小时)以及暴露48小时和1300小时之后的显微红外光谱表征结果。在图12中,暴露48小时的样品被暴露于波长257nm的UV光中,并且暴露1300小时的样品被暴露于波长263nm的UV光中。这些波长并非限制性的,本发明的实施例可使用其他波长的UV光。如图所示,由烷基Si-CH3和C-H的产生的峰在48小时和1300小时的暴露时间之间基本上消失,而在此时间段内,出现O-H峰和H2O峰。特别地,1300小时后样品的光谱非常接近纯二氧化硅的光谱。此外,如图12所示,暴露1300小时的样品的输出功率(“Ptx”)恢复到初始功率水平(即0小时的时候)的约72%,远高于暴露48小时的样品所呈现的58%的初始功率水平。图13A-图13D示出了根据本发明的实施例的暴露时间分别为0小时、48小时、200小时和1300小时的密封剂的能量色散X射线光谱测量的证实结果。如图所示,密封剂中检测到的碳的量随着UV暴露时间的增加而降低,而氧的量升高。图13A示出了未暴露于UV光之前且具有初始功率输出的未转化的密封剂的结果。如图13B所示,在暴露于UV光48小时之后,密封剂的碳含量已降低,氧含量升高,并且由于例如上述的从具有不同折射率的密封剂的局部区域的散射,功率输出水平仅为初始功率输出的约60%。图13C示出了暴露于UV光200小时后的老化阶段的大致结束时所测量的EDX光谱。如图所示,由于基本上所有的密封剂被转化为非化学计量比的二氧化硅材料,密封剂的碳含量已大幅下降,并且输出功率已经恢复到与未暴露于UV光之前所呈现的水平几乎相同的水平。如图13D所示,在暴露于UV光1300小时之后,碳含量进一步降低(伴随着氧含量的增高),因为非化学计量比的二氧化硅材料继续被转化为碳含量更低的非化学计量比的二氧化硅材料(即,在甚至更多地暴露于UV光之后),进而转化为基本上纯的二氧化硅。在1300小时之后的输出功率水平已被稳定在一个中间水平(在所描述实施例中,为73%),该中间水平高于在老化程序期间所呈现的水平,但低于器件在初始供电时所呈现的水平。图14示出了图13A至图13D的密封剂的大致成份随器件操作时间(以及其带来的UV暴露时间)的变化曲线。如图所示,随着器件的操作时间接近1300小时,氧含量增加,硅含量轻微增加,碳含量降低。特别地,在1300小时之后,氧含量接近纯二氧化硅的约67%,而硅含量接近纯二氧化硅的33%。在图13A-13D和图14中,暴露了48小时的样品被暴露于波长为257nm的UV光,暴露了200小时的样品被暴露于波长为279nm的UV光,暴露了1300小时的样品被暴露于波长为263nm的UV光;这些波长并非限制性的,本发明的实施例可使用其他波长的UV光。在一些实施例中,尤其是在密封剂具有较大厚度的那些实施例中,只有最靠近发光芯片的密封剂的部分被部分地或基本上转化为非化学计量比二氧化硅材料,留下(更靠近刚性透镜的)第二部分基本未被转化。在一些实施例中,除了来自发光芯片的UV光或替代来自发光芯片的UV光,密封剂还被暴露于来自除了器件的发光芯片之外的其它光源的UV光。例如,来自其他UVLED或UV灯的UV光可从上方照射到密封剂,增强密封剂至非化学计量比二氧化硅材料的转化和/或将密封剂的额外区域转化为非化学计量比二氧化硅材料。图15A-15H示出了根据本发明的多个实施例的UV发光器件。在每个附图中,芯片被密封剂1500覆盖,该密封剂1500已经部分地或的基本全部地通过暴露于UV光而转化为非化学计量比二氧化硅材料。多个实施例还包括上述的透镜130。转化的密封剂1500通常含碳水平高于1ppm(或甚至大于约1at.%),但小于约40at.%,或小于约30at.%,或甚至小于约20at.%。如上所述,透镜130通常含有小于1ppm的碳,或者基本不含有碳。如图15B所示,密封剂1500可被成形为透镜的形状,并从而用于替代本发明的一些实施例中存在的透镜130(例如参见图15A)。如图15C所示,透镜130(无论具有圆形还是采用平板的形式)并非必须悬垂于芯片100的侧面。另外,如之前图1C和图1D所示,透镜130可包括平板,或基本由平板构成,或由平板构成,该平板可大于芯片(因此,例如悬垂于芯片的至少一侧),且可被图案化或粗糙化以有助于光子提取,例如,该平板透镜可为菲涅耳透镜。图15D示出了本发明的一个实施例,其中转化的密封剂1500和透镜130被放置在芯片100的顶表面,而接近芯片100侧面的区域1510可包括(或基本由以下部件构成,或由以下部件构成):未转化的密封剂(即,未暴露于UV光的密封剂或暴露于功率和/或时间不足以将大量的密封剂转化为非化学计量比二氧化硅材料的UV光)和/或对芯片100发出的UV光不透明或呈反射性的阻挡材料。例如,阻挡(例如,阻挡包括Al和/或另一诸如聚四氟乙烯(PTFE)的UV反射材料),或基本由Al和/或诸如聚四氟乙烯(PTFE)的另一UV反射材料构成,或由Al和/或另一诸如聚四氟乙烯(PTFE)的UV反射材料构成)可被放置在芯片100的侧壁与区域1510(如‘655号申请所详述的那样)的其余部分之间,该区域由于被遮挡从而免受芯片100发出的UV光的大量曝光,且未被转化。如图15E和15F所示,未转化的密封剂1500可在被放置到芯片100之前或之后被成形(例如,通过模制)为多种形状(例如,半球形透镜或平板)。例如,在一些实施例中,密封剂在被接附到芯片100之前被模制成所需的形状并暴露于UV光。图15H示出了一个实施例,其中转化的密封剂具有弯曲的顶表面,且与芯片100的顶表面共形。图15G与图15D类似,但是透镜130被替换为包括转化的密封剂1500(或基本由转化的密封剂1500构成,或由转化的密封剂1500构成)的区域。如图所示,器件还可含有包括未转化密封剂和/或UV光阻挡(或基本由未转化密封剂和/或UV光阻挡构成,或由未转化密封剂和/或UV光阻挡构成)的区域1510。如上文所述,一种或多种阻挡材料可将芯片100与未转化的区域1510分隔。在一些实施例中,密封剂的转化会使得转化的密封剂1500变脆,因此透镜130很可能会变松或者从发光芯片100上脱离。在这种实施例中,额外的接附件或接附材料1600可被用于进一步确保透镜与芯片的接触,如图16所示。例如,接附件1600可以为树脂(例如,可为不透明的环氧树脂),器件部分地浸入其中。在其它实施例中,接附件1600包括(或基本由以下部件构成)夹具或其他机械紧固件,其维持透镜130与芯片100(或变脆的密封剂1510)之间的接触。接附件1600可至少轻微地(例如,约0.5mm或更少,或者约0.3mm或更少,约0.1mm或更少)延伸到芯片100(或变脆的密封剂1510)与透镜130之间的界面上方,从而在器件操作和处理期间进一步稳定透镜。为了清晰起见,在图16中未示出芯片100与透镜130之间的未转化的密封剂1510的薄层。在多个实施例中,接附件1600并不明显地(例如,不超过0.5mm)延伸到透镜130的底表面的上方,从而不会阻挡从器件发出的UV光,并且不会对器件的输出功率造成负面影响。在本发明的多个实施例中,在将有机密封剂暴露于UV光(即,暴露于来自发光芯片自身的UV光和/或来自芯片以外的第二外来光源的UV光一段时间,例如约100至约300小时)的老化阶段之后,UV器件制造工艺的剩余部分已经完成,器件可被交运到用户和/或合并到更大的使用由发光芯片发射的UV光的系统或装置。例如,可以通过例如输出功率和/或发光波长对UV器件进行质量管理检验和/或分拣。器件可被合并到更大的系统中,该系统有利地使用由器件制造商或由该器件被传送(例如,销售和运送)的第三方客户发出的UV光。例如,较大的系统可包括(或基本由以下构成)用于液体和/或气体的消毒、净化和/或灭杀系统,医疗器械,成像系统(例如,用于检查货币上的水印的防伪系统),UV固化系统,印刷系统,光学传感器等。在本发明的多个实施例中,将有机密封剂暴露于UV光的老化阶段之后,测量器件的输出功率以抛弃输出功率低于标准(即,低于预定的最小的期望输出功率)的器件。该测量步骤通常在将在器件被运送到用户之前作为制造工艺中的测试来执行。由于例如老化程序中有机密封剂至非化学计量比二氧化硅的转化的可变性,老化器件的约20%至约40%的输出功率低于最小输出功率标准。即,在此处描述的老化程序期间或在老化程序之后,有一定比例的器件可能出现功率退化,尽管大多数器件会维持近乎与老化前一致的输出功率。因此,可有益地使用老化程序之后的测试步骤来消除(例如,从给客户的交运中移除)那些不满足产品规格的低输出功率器件。此外,在老化转化程序中,本发明的多个实施例可使用不同于发光器件在正常操作(即,用户的操作和/或有益地使用器件发出的UV光的较大装置内的操作)期间使用的操作条件的一种或多种操作条件。例如,超过推荐的最大操作条件的更高的电流或更高的温度条件可被应用在老化步骤中以加速向非化学计量比的二氧化硅材料的转化。在一个示例性的实施例中,当UV光发射器件的最大推荐操作电流为300mA时,可在全部或部分老化程序中(如,100小时)施加更大的电流(如,400mA),以利于有机密封剂材料的转化。在另一个示例性实施例中,当推荐的UV光发射器件的最大壳温为55℃时,可在全部或部分老化程序中施加高于推荐的最大壳温的温度(如,85℃)以利于有机密封剂材料的转化。在老化程序中,与正常操作中使用的条件不同的另一个操作条件是发光器件周围的大气中的氧气浓度。例如,老化程序可在比正常操作中使用的氧气浓度更高的氧气浓度的大气中执行。如本文描述的,在本发明的多个实施例中,通过光化学氧化反应,有机密封剂被转化为非化学计量比二氧化硅材料。因此,引入过量的氧作为氧化剂促进了转化反应。在多个实施例中,执行老化程序的大气可包括大于30%高达100%的氧。在本发明的多个实施例中,硅树脂被用作UV透明密封剂。在这种情况下,使硅树脂转化为非化学计量比二氧化硅材料的光化学反应可形成作为副产物的甲醛。因此,本发明的多个实施例平衡副产物甲醛的产生和甲醛的向外扩散,因为甲醛的累积可能导致气泡(例如,具有几纳米至几十微米的尺寸)的形成,这些气泡会阻挡或偏转半导体芯片发出的UV光,降低器件效率。如果老化程序中产生的甲醛的扩散比甲醛的形成更慢,则转化过程由于甲醛在非化学计量比二氧化硅材料中的累积而可能更加不稳定。因此,在这种情况下,全部或部分老化程序使用比标称器件操作(例如由用户执行的)推荐的更高的电流和/或更低的温度来执行。在示例性实施例中,对于推荐操作电流300mA的器件,在全部或部分老化程序中可使用更低的电流,例如20mA至150mA,以降低甲醛的形成速率并因此避免可负面影响光输出功率的甲醛的累积。在其它实施例中,甲醛的扩散被增强,以避免老化程序中生成的甲醛的累积。如上文所述,更高的壳温(即,施加到半导体芯片和/或其部分或全部封装的温度)可增加甲醛扩散到经受转化的密封剂中的速率。另外地或可选地,全部或部分老化程序可在真空气氛中执行,以促进甲醛副产物从未转化和/或转化的密封剂向外扩散。在多个其他实施例中,通过限制密封剂中的氧气浓度来降低光化学转化反应的速率,以增加甲醛相对于其形成的扩散。对于氧化反应,氧气可被用作氧化剂。氧气的来源包括密封剂材料中分解的氧气分子和或在老化期间从大气向内扩散的氧气分子。在多个实施例中,限制密封剂中的氧气浓度对于降低光化学反应的速率是有效的。在这种实施例中,密封剂中的氧气浓度被限制为在0.1ppm至1at.%之间。为了获得这种的低氧气浓度,密封剂材料的制备(包括任意捏合步骤)可在低氧的大气(例如,含0%至10%氧气的气氛)中执行,例如,在基本纯氮气(或惰性气体)的大气中。在本发明的多个实施例中,特别是当发光器件在老化前的输出功率大于15mW时,器件可能出现输出功率恢复的现象。在这种恢复现象中,输出功率可能在老化的第一阶段开始降低,但是然后在老化的稍后阶段增加。尽管发明人并不希望受限于恢复机制,并且本发明的实施例也不受受限于恢复机制,但是下文描述了一种可能的机制。在老化的初始阶段,甲醛累积可能由于气泡形成而导致输出功率的降低。在老化的后期阶段,光化学反应随着密封剂转化的完成而减少,甲醛的向外扩散变得比甲醛的形成相对更快,导致气泡(包括甲醛气体,或基本由甲醛气体构成)的减少,从而实现输出功率的恢复。因此,本发明的实施例监控了器件在老化程序中的输出功率,且所使用的老化时间长于器件的输出功率恢复到接近老化开始时的初始输出功率水平(例如,约80%至约90%)所需的时间。实现恢复的老化时间可取决于经受老化的器件的输出功率。例如,老化前输出功率为20mW的器件可使用至少200小时的老化,而输出功率为15mW的器件可使用至少300小时的老化。示例1硅树脂被用作有机密封剂并被放置在引线框架封装中的UVLED芯片的上方。通过施加足以使透镜和芯片之间的硅树脂的厚度最小化的力使熔融二氧化硅构成的刚性半球形透镜被接附到芯片。具有硅树脂和透镜的器件在室温下被放置在真空度小于10Toor的真空炉中10分钟以移除陷于硅树脂中的任何气体。器件在炉中在约150℃下被烧制约1小时以固化硅树脂。在该示例中,所得的硅树脂的厚度为约8μm。环氧树脂作为接附材料被放置,填充引线框架的腔体,覆盖键合到LED芯片的引线,且略微重叠并延伸越过刚性透镜的底表面。然后,器件在炉中在约160℃下被烧制约1小时以固化环氧树脂。固化的环氧树脂的顶表面延伸到刚性透镜底表面上方0.2mm。硅树脂被暴露于LED芯片发出的波长为265nm的UV光200小时,以将硅树脂转化为非化学计量比二氧化硅材料。所得的非化学计量比二氧化硅材料的碳含量为约20at.%。示例2硅树脂被用作有机密封剂并被放置在引线框架封装中的UVLED芯片的上方。通过施加足以使透镜和芯片之间的硅树脂的厚度最小化的力使熔融二氧化硅构成的刚性半球形透镜被接附到芯片。具有硅树脂和透镜的器件在室温下被放置在真空度小于10Toor的真空炉中10分钟以移除陷于硅树脂中的任何空气。器件在炉中在约150℃下被烧制约1小时以固化硅树脂。在该示例中,所得的硅树脂的厚度为约8μm。硅树脂被暴露于LED芯片发出的波长为265nm的UV光200小时,以将硅树脂转化为非化学计量比二氧化硅材料。所得的非化学计量比二氧化硅材料的碳含量为约20at.%。本文所用的术语和表述被用作描述性而非限定性的术语,在使用这些术语和表达时,并不旨在排除任何所示和所描述特征的等同物或其部分,但应该认识到的是,在所要求的保护的本发明范围内各种修改都是可能的。当前第1页1 2 3