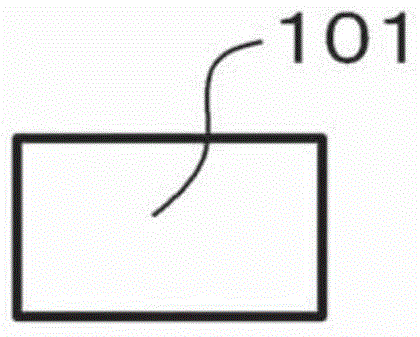
本发明涉及压粉磁芯及其制造方法。
背景技术:
:近年来,电动化车辆的普及快速发展。电动化车辆例如包括:混合动力车(hev:hybridelectricvehicle)、插电式混合动力车(phev:plug-inhybridelectricvehicle)、电动车(ev:electricvehicle)等。对于这样的电动化车辆,为了进一步改善油耗(电耗),要求各种电子部件或系统的小型化及轻量化。另外,受电动化车辆的市场扩大所带动,对扼流线圈、电抗器、变压器等中使用的软磁性粉末及使用该粉末的压粉磁芯,也要求具有越来越高的性能。对于使用了该软磁性粉末的压粉磁芯,要求高磁导率,为此需要高密度地填充软磁性粉末。另外,对于使用了该软磁性组合物的粉末的压粉磁芯,为了小型化和轻量化,要求饱和磁通密度高,磁芯损耗小、以及直流叠加特性优异等。例如,在专利文献1中公开了以下方法:通过将薄板状的粉碎粉末和基于雾化法形成的球状粉末混合而高密度地填充软磁性粉末。图12a及图12b中示出专利文献1中公开的fe系非晶合金薄带的粉碎粉。粉碎粉是指将薄带粉碎而得到的粉。在本说明书中,也将粉碎粉称作“粉末”或“颗粒”。图12a是表示粒径为50μm以上的粉碎粉1的图。图12b是表示粒径为50μm以下的粉碎粉2的图。专利文献1的压粉磁芯的主要成分为:fe系非晶合金薄带(以下,简称作“薄带”)的粉碎粉、以及fe系非晶合金雾化球状粉(以下,简称作“雾化球状粉”)。图12a所示的粉碎粉1的粒径为薄带的厚度的2倍(厚度25μm×2=50μm)以上且6倍(厚度25μm×6=150μm)以下。另外,粉碎粉1为全部粉碎粉的80质量%以上。图12b所示的粉碎粉2的粒径为薄带的厚度的2倍(厚度25μm×2=50μm)以下。另外,粉碎粉2为全部粉碎粉的20质量%以下。此外,在专利文献1中,将被粉碎为薄板状的粉的主面的面方向的最小值作为粉碎粉1、2的粒径。另外,雾化球状粉的粒径为3μm以上且薄带的厚度的1/2(厚度25μm×1/2=12.5μm)以下。现有技术文献专利文献专利文献1:日本专利第4944971号公报技术实现要素:发明要解决的问题为了高密度地填充构成压粉磁芯的软磁性粉末,在压粉磁芯的制作时,需要在较高的压力下进行加压成型。但是,由于软磁性粉末彼此接触而无法确保粉末间的绝缘,因此耐电压性能下降。尤其是,在对如专利文献1所公开的那样的、具有锐利的边缘的薄板状的粉末进行加压的情况下,锐利的边缘扎入相邻的粉末,从而粉末间会导通。其结果,耐电压性能的下降变得显著,难以高密度地填充。另外,在专利文献1中,在全部粉碎粉中,50μm以上的粉碎粉1占全部粉碎粉的80质量%以上,且粉碎粉1的内部电阻较小。因此,施加电压时的电荷集中于50μm以上的粉碎粉1而导致耐电压性能下降。其结果,难以高密度地填充。另外,薄板状的粉末在加压成型时会在流动方向上取向,因此在与专利文献1中公开的那样的球状粉末组合的情况下,难以填埋球状粉末间的间隙,未必可得到较高的填充密度。即,使用专利文献1的方法,无法得到兼顾了高磁导率和高耐电压的压粉磁芯。本发明的一个方式的目的在于,提供兼顾高磁导率和高耐电压的压粉磁芯及其制造方法。解决问题的方案本发明的一个方式的压粉磁芯包含软磁性组合物的粉末,其中,所述软磁性组合物的粉末至少包含扁平度为3.0以上且6.0以下的椭圆体状的粉末。本发明的一个方式的压粉磁芯的制造方法包括:通过使软磁性组合物相互摩擦,从而至少制作椭圆体状的粉末的第一工序;使所述椭圆体状的粉末混合于粘结剂中来制作造粒粉的第二工序;将所述造粒粉填充在规定的模具中,并进行加压成型而得到压粉体的第三工序;以及在所述粘结剂发生固化的温度下,对所述压粉体进行加热的第四工序,所述椭圆体状的粉末的扁平度为3.0以上且6.0以下。发明效果根据本发明,能够提供兼顾高磁导率和高耐电压的压粉磁芯。附图说明图1a是示意性地表示本发明的实施方式1~3的软磁性粉末的制造过程的图。图1b是示意性地表示本发明的实施方式1~3的软磁性粉末的制造过程的图。图1c是示意性地表示本发明的实施方式1~3的软磁性粉末的制造过程的图。图2是示意性地表示本发明的实施方式1~3的旋风磨的结构的一例的图。图3是表示本发明的实施例1的软磁性粉末的sem(scanningelectronmicroscope,扫描电子显微镜)图像的图。图4是表示本发明的实施例1的软磁性粉末的粒度分布的图。图5是表示本发明的实施例1的压粉磁芯的剖面的sem图像的图。图6是表示本发明的实施例2的软磁性粉末的sem图像的图。图7是表示本发明的实施例2的软磁性粉末的粒度分布的图。图8是表示本发明的实施例2的压粉磁芯的剖面的sem图像的图。图9是表示本发明的实施例3的软磁性粉末的sem图像的图。图10是表示本发明的实施例3的软磁性粉末的粒度分布的图。图11是表示本发明的实施例3的压粉磁芯的剖面的sem图像的图。图12a是表示专利文献1中公开的fe系非晶合金薄带的粉碎粉(粒径为50μm以上)的图。图12b是表示专利文献1中公开的fe系非晶合金薄带的粉碎粉(粒径为50μm以下)的图。附图标记说明1、2粉碎粉101软磁性薄带102、103、104、105、106、601、602、701粉末201粉碎室202原料投入口203、204旋转翼205排出口206原料207原料颗粒501、502、503、504、505、506剖面301第一粉末302第二粉末303第三粉末具体实施方式参照附图对本发明的各实施方式进行说明。此外,对各附图中相同的构成要素,标以相同的附图标记,并适当省略它们的说明。(实施方式1)以下,对本发明的实施方式1进行说明。<软磁性粉末的制造方法>对本实施方式的软磁性粉末的制造方法进行说明。软磁性粉末是软磁性组合物的粉末。首先,在通过高频加热等将合金组合物熔解之后,通过液体骤冷法进行冷却,来制作非晶层的薄带或薄片(工序1)。在实施液体骤冷法时,例如,可以使用在fe基非晶薄带的制造等中使用的单辊式的非晶制造装置或双辊式的非晶制造装置。此外,以下,以制作非晶层的薄带(以下,简称作“薄带”)的情况为例进行说明,但毋庸置疑,下述说明也适用于制作薄片的情况。接着,将工序1中所得到的薄带粉碎而得到粉碎粉(工序2)。作为薄带的粉碎方法,例如,可列举使用旋风磨来使薄带相互摩擦的方法。使用图2对该方法的细节进行后述。一般来说,已知,若在粉碎前对薄带进行加热而使其结晶,则薄带变脆,变得易于粉碎。另一方面,若进行加热则薄带的硬度变高,因此难以将薄带粉碎得较小。其结果,粒径较小的粉碎粉在全部粉碎粉中的比例较少。因此,在本实施方式中,采用在工序2中在未加热的状态下将薄带粉碎的方法。由此,薄带的硬度变低,所以能够粉碎得较小。其结果,能够提高粒径较小的粉碎粉在全部粉碎粉中的比例。此外,例如也可以使用筛子等将通过工序2而得到的粉碎粉进行分级,从而得到具有所希望的粒度分布的粉碎粉。此外,在本说明书中,也将“粉碎粉”称作“粉末”或“颗粒”。在此,使用图1a~图1c,对上述工序2中的粉碎粉的制造机理进行说明。图1a所示的软磁性薄带101(软磁性组合物的一例)只要是例如金属、合金、硅钢板、非晶或纳米晶合金等具备软磁性特性的薄带即可。在使用旋风磨的情况下,图1a所示的软磁性薄带101搭乘气流,从而软磁性薄带101相互摩擦。由此,软磁性薄带101的表面被刮削,产生图1b所示的粉末102及粉末103。并且,通过继续进行粉碎,粉末102及粉末103也搭乘气流,从而这些粉末相互摩擦。由此,粉末102的表面被刮削,产生图1c所示的球状的粉末104及鳞片状的粉末106。另外,粉末103的表面被刮削,产生图1c所示的椭圆体状的粉末105及鳞片状的粉末106。粉末106是从粉末102或粉末103刮削出的削屑。以上,对粉碎粉的制造机理进行了说明。下面,对工序2之后的工序3进行说明。对通过工序2而得到的粉碎粉进行热处理,从而消除因粉碎导致的内应变,或使αfe结晶层析出(工序3)。作为热处理装置,例如可以使用热风炉、热压机、灯、护套加热器、陶瓷加热器、回转窑等。通过以上所说明的工序1~3,能够制造非晶层的薄带的粉碎粉即软磁性粉末。<压粉磁芯的制造方法>对本发明的实施方式的压粉磁芯的制造方法进行说明。首先,将通过上述工序1~3制造的软磁性粉末与粘结剂混合,来制作造粒粉(工序4)。作为粘结剂,可以使用绝缘性良好且耐热性高的树脂(例如,酚醛树脂或有机硅树脂等)。接着,将工序4中所得到的造粒粉填充在具有所希望的形状的耐热性高的模具中,进行加压成型而得到压粉体(工序5)。接着,在粘结剂发生固化的温度下,对工序5中所得到的压粉体进行加热(工序6)。通过以上所说明的工序4~6,能够制造具有高磁导率的压粉磁芯。(实施例1)下面,对具体地实施了上述的本实施方式的软磁性粉末的制造方法及压粉磁芯的制造方法的实施例1进行说明。在本实施例中,使用旋风磨将通过骤冷单辊法制作的fe73.5-cu1-nb3-si13.5-b9(元素符号之后的数值表示原子%)的fe系非晶合金薄带进行了粉碎,得到了非晶层的软磁性合金粉末。<旋风磨的粉碎机理>使用图2对旋风磨的粉碎机理进行说明。图2是示意性地表示本实施例所使用的旋风磨200的结构的一例的图。旋风磨200具有:粉碎室201、原料投入口202、旋转翼203、204、排出口205、旋转轴208、驱动源209。原料投入口202是投入原料206的开口部,与粉碎室201连通。原料206例如是图1a所示的软磁性薄带101。排出口205与粉碎室201连通,是排出在粉碎室201所产生的原料颗粒207的开口部。在排出口205的外部设置有吸引装置(省略图示)。粉碎室201是进行原料206的粉碎的空间。在粉碎室201中设置有旋转翼203、204。旋转翼203、204分别固定于旋转轴208。旋转轴208通过驱动源209(例如,电机)而被赋予旋转力,如箭头a所示那样旋转。由此,旋转翼203、204也同样地旋转。在旋转翼203、204旋转时,稳定地产生气流210及循环流211、212。气流210是从粉碎室201的入口侧经由粉碎室201内而流向粉碎室201的出口侧的气流。循环流211是沿着旋转翼203的表面循环的气流。循环流212是沿着旋转翼204的表面循环的气流。下面,对在具有这种结构的旋风磨200中投入原料206而得到原料颗粒207的流程进行说明。从原料投入口202投入的原料206搭乘气流210向粉碎室201流入。另一方面,流入到粉碎室201的原料206搭乘循环流211或循环流212,在粉碎室201内移动。这时,搭乘循环流211的原料206与搭乘循环流212的原料206相互摩擦而被粉碎。通过该摩擦粉碎,生成原料颗粒207。在此产生的原料颗粒207例如是图1c所示的粉末104、105、106。原料颗粒207中的微粉(例如,图1c所示的粉末106)搭乘气流210而从粉碎室201流出,通过吸引装置(省略图示)的吸引力而从排出口205被回收。在本实施例中,粉碎的执行时间为50分钟。即,在50分钟的期间,一边使旋转翼203、204旋转,一边从原料投入口202投入了原料206(软磁性薄带101)。由此,搭乘循环流211的原料206与搭乘循环流212的原料206相互摩擦,从而各原料206的表面被刮削,产生了图1c所示的粉末104、105、106,作为最终的原料颗粒207。作为微粉的粉末106在旋转轴208的轴向(旋转翼203、204的中心部)上集聚,搭乘气流210从粉碎室201流出,通过吸引装置的吸引力从排出口205排出。这样,做到了仅对一定粒度的粉末106连续地进行回收。所回收的粉末106为鳞片状。另一方面,作为比粉末106大的颗粒的粉末104、105搭乘循环流211或循环流212而表面被刮削,并滞留在粉碎室201内。即,在该滞留的期间,也会从粉末104、105中产生粉末106。对于该粉末106,也与上述同样地从排出口205回收。然后,在粉碎的执行结束时(经过50分钟后),在粉碎室201内残留有没有棱角的球状的粉末104和没有棱角的椭圆体状的粉末105。此外,在本实施例中,粉碎的执行时间为50分钟,但能够根据所希望的形状或粒径来适当调整。另外,在本实施例中,以使用旋风磨200制作粉末104~106的情况为例进行了说明,但也可以通过其他装置或其他方法制作粉末104~106。另外,在本实施例中,作为旋风磨200,使用了株式会社静冈工厂制的、150s、单电机的旋风磨。优选转速为11000rpm~15000rpm,最优值为15000rpm。因此,在本实施例中采用的转速为15000rpm。此外,在使用行星式球磨机、磨碎机、样品磨或振动磨的情况下,无法做成球状粉或椭圆体状粉(去不掉颗粒的棱角),且粉末的平均粒径超过20μm。在使用混合磨的情况下,粉末的平均粒径成为10μm多,但无法做成球状粉或椭圆体状粉(去不掉颗粒的棱角)。另外,喷磨机无法进行粉碎。对于按以上方式得到的粉末104、105、106,进行了以下的处理。首先,对粉末104、105、106进行了热处理,消除了因粉碎导致的内应变,并且使αfe结晶层析出。进行了如下处理来作为热处理:使用热压机,在560℃下对粉末104、105、106加热2秒。接着,以满足以下条件的方式将粉末104、105、106混合,制作了混合粉末:粉末104+粉末105:粉末106=90重量%:10重量%。接着,将混合粉末与作为粘结剂的有机硅树脂混合,制作了造粒粉。有机硅树脂为混合粉末的3重量%左右。接着,将造粒粉投入到模具中,使用冲压机在成型压力为4吨/cm2的压力下进行加压成型,制作了压粉体。<初始磁导率的评价>对于以上述方式得到的压粉体,使用阻抗分析仪测定了频率100khz下的初始磁导率。在此,将初始磁导率合格与否的基准设定为19以上。该设定的理由为:以达到损耗为相同程度的一般的金属系材料的初始磁导率以上为目标。由阻抗分析仪测定出的结果为:初始磁导率为21。因此,达到了合格基准,实现了高磁导率。<软磁性粉末的形状>使用图3对本实施例中所得到的软磁性粉末的形状进行说明。图3是表示本实施例的软磁性粉末的sem(scanningelectronmicroscope,扫描电子显微镜)图像的图。在图3中,第一粉末301相当于图1c所示的粉末104,第二粉末302相当于图1c所示的粉末105,第三粉末303相当于图1c所示的粉末106。如图3所示,第一粉末301是球状的粉末,第二粉末302是椭圆体状的粉末,第三粉末303是鳞片状的粉末。<软磁性粉末的粒度分布>第一粉末301的粒径大于32μm。另外,第一粉末301为全部粉碎粉的36重量%。第二粉末302的粒径为32μm以下。另外,第二粉末302为全部粉碎粉的54重量%。第三粉末303的粒径为32μm以下。另外,第三粉末303为全部粉碎粉的10重量%。此外,粒径的测定是根据第一粉末301、第二粉末302及第三粉末303各自是否能够通过32μm直径的开口而进行判断的。上述的第一粉末301、第二粉末302、第三粉末303的特征的汇总如表1所示。[表1]形状粒径重量%第一粉末301球状大于32μm36重量%第二粉末302椭圆体状32μm以下54重量%第三粉末303鳞片状32μm以下10重量%为了提高软磁性粉末的填充密度,在本实施例中,如上所述,以满足以下条件的方式将第一粉末301、第二粉末302及第三粉末303进行了混合:第一粉末+第二粉末:第三粉末=90重量%:10重量%。具体而言,以满足以下条件的方式将各粉末进行了混合:第一粉末301:第二粉末302:第三粉末303=36重量%:54重量%:10重量%。有时微小的粉末会妨碍加压成型时的粉末的流动,而不能提高粉末的填充密度,因此优选软磁性粉末之中最微小的第三粉末303的重量比为全部粉碎粉的50重量%以下。进一步来讲,优选第三粉末303的重量比为全部粉碎粉的30重量%以下。更进一步来讲,优选第三粉末303的重量比为全部粉碎粉的20重量%以下。另一方面,优选第一粉末301和第二粉末302的合计的重量比为全部粉碎粉的50重量%以上。另外,为了提高软磁性粉末的填充密度,优选粒径较小的第二粉末302的比例比粒径较大的第一粉末301的比例大。即,在将第一粉末301、第二粉末302及第三粉末303混合时,优选使第二粉末302比第一粉末301多。根据以上内容,在本实施例中设定为,如图3所示,粒径大于32μm的第一粉末301存在一定数量,粒径为32μm以下的第二粉末302、第三粉末303也存在一定数量。本实施例的软磁性粉末的粒度分布如图4所示。利用microtracmt3000ii系列,测定出了图4所示的粒度分布。在图4中,横轴表示粒径,纵轴表示各粒径的软磁性粉末存在的频度。在累积分布中,d10%约为9μm,d50%约为29μm,d90%约为59μm。<粒径的细节>第一粉末301、第二粉末302、第三粉末303各自的粒径是如上述那样的。下面,对各粒径更详细地进行说明。在本实施例中,粒径大于32μm的第一粉末301的平均粒径约为47μm。另外,粒径为32μm以下的第二粉末302的平均粒径约为16μm。另外,粒径为32μm以下的第三粉末303的平均粒径约为8μm。此处所说的平均粒径,是利用microtracmt3000ii系列测定出的累积粒度分布的d50%的数值。为了提高软磁性粉末的填充密度,优选第一粉末301、第二粉末302、第三粉末303各自的平均粒径的关系满足以下条件:第一粉末301的平均粒径>第二粉末302的平均粒径>第三粉末303的平均粒径。另外,若第一粉末301、第二粉末302、第三粉末303各自的平均粒径之间的差过大,则有时微小的第三粉末303会妨碍加压成型时的粉末的流动,而导致不能提高粉末的填充密度。因此,优选第一粉末301的平均粒径为30μm以上且60μm以下。进一步来讲,优选第一粉末301的平均粒径为40μm以上且50μm以下。另外,优选第二粉末302的平均粒径为10μm以上且20μm以下。另外,优选第三粉末303的平均粒径为4μm以上且12μm以下。<压粉磁芯>使用本实施例的软磁性粉末制造的压粉磁芯的剖面的sem图像如图5所示。剖面501是第一粉末301(图1c所示的粉末104)的剖面。剖面502是第二粉末302(图1c所示的粉末105)的剖面。剖面503是第三粉末303(图1c所示的粉末106)的剖面。第一粉末301如上述那样为球状,因此第一粉末301的剖面501如图5所示为圆状。另外,第二粉末302如上述那样为椭圆体状,因此第二粉末302的剖面502如图5所示为椭圆状。另外,第三粉末303如上述那样为鳞片状,因此第三粉末303的剖面503如图5所示为鳞状。另外,使用旋风磨200,使软磁性组合物的粉末滞留,并使粉末彼此冲撞,由此,粉末表面的温度上升,在粉末表面形成fe氧化膜。在将氧浓度设定为0.1%(n2吹扫)而进行了粉碎的情况下,fe氧化膜的厚度为20nm以下。fe氧化膜的厚度优选为20nm以下,进一步优选为10nm以下。旋风磨200的粉碎方式是使粉末彼此冲撞的方式,因此与使粉末冲撞到叶片或球等的粉碎方式相比,能够减小粉末表面的fe氧化膜厚度。并且,通过在低氧浓度下进行粉碎,能够使fe氧化膜厚度变薄,能够使压粉磁芯的软磁特性提高。<表面平滑性>对第一粉末301、第二粉末302、第三粉末303各自的表面平滑性进行说明。表面平滑性是指颗粒(粉末)的实际的表面积s1除以与该颗粒(粉末)为相同的体积等效直径d且表面粗糙度ra为0即表面完全平滑的正球状颗粒的表面积s2而得到的值。表面平滑性越接近1则越是表面平滑的颗粒。表面积s1例如可以利用气体吸附式的比表面积仪来测定。另外,表面积s2可以通过计算以体积等效直径d为直径的球的表面积而得到。在本实施例中,第一粉末301的表面平滑性为1.616,第二粉末302的表面平滑性为2.138,第三粉末303的表面平滑性为4.268。通过减小表面平滑性从而颗粒间的摩擦阻力降低,因此能够得到良好的流动性。尤其是,在制造压粉磁芯时,与软磁性粉末混合的热固化性树脂(粘结剂的一例)进入软磁性粉末的表面的微细的凹凸而不再有助于流动的情况受到抑制,能够以更少量的热固化性树脂来加压成型。由此,能够提高软磁性粉末的填充密度。因此,每单位体积的软磁性粉末的比例增加,能够使压粉磁芯的饱和磁通密度、磁导率之类的软磁特性提高。只要表面平滑性为1.1以上,就能充分得到通过减小表面平滑性而提高软磁性粉末的填充密度的效果。此外,表面平滑性小于1.1的颗粒的制造比较花费成本。因此,优选第一粉末301的表面平滑性为1.1以上且2.0以下。另外,优选第二粉末302的表面平滑性为1.7以上且2.5以下。另外,优选第三粉末303的表面平滑性为3.4以上。<扁平度>对第一粉末301、第二粉末302、第三粉末303各自的扁平度进行说明。扁平度是指椭圆体的三个半轴中的最大半轴除以最小半轴而得到的值。扁平度越接近1.0,则越是接近球的形状。在本实施例中,第一粉末301中,扁平度为1.0以上且1.2以下的粉末占多数。另外,第二粉末302中,扁平度为3.0以上且6.0以下的粉末占多数。另外,第三粉末303中,扁平度大于6.0的粉末占多数。在加压成型时,扁平度为1.2以上的粉末以其长度方向沿着粉末的流动方向的方式配置。因此,从流动方向观察时,扁平度为1.2以上的粉末的投影面积比扁平度小于1.2的大致球形的粉末的投影面积小,因此能够降低流动阻力。即,能够降低加压成型时的压力。因此,在制造将软磁性颗粒与热固化性树脂(粘结剂的一例)混合而形成的压粉磁芯时,即便是减少了树脂量及溶剂量的、粘度更高的混合物也能够成型,因此能够提高软磁性粉末的填充密度。对于表面平滑性比第一粉末301大的第二粉末302和第三粉末303,通过增大它们的扁平度,能够使粘结剂的流动性提高。由此,第二粉末302能够以少量的粘结剂进入第一粉末301之间。另外,第三粉末303能够以少量的粘结剂进入第二粉末302之间。此外,与表面平滑性相比,扁平度对上述效果的影响更大。这是由于,与表面平滑性相比,扁平度对外形的影响更大。另外,若加长粉碎时间,则虽然颗粒的扁平度不会明显变化,但通过粉末彼此的冲撞从而表面被一点点逐渐削去,所以表面平滑性逐渐变小。另外,在制作压粉磁芯时,与表面平滑性相比,扁平度对于得到粘结剂的良好的流动性来说,是更重要的。由以上内容可知,每单位体积的软磁性粉末的比例增加,能够使压粉磁芯的饱和磁通密度、磁导率之类的软磁特性提高。<效果>根据本实施方式及本实施例中所使用的摩擦粉碎,能够对粒径大于32μm的球状的第一粉末301、粒径为32μm以下的椭圆体状的第二粉末302、以及粒径为32μm以下的鳞片状的第三粉末303的粒度分布容易地进行控制。而且,本实施方式及在本实施例中,制作包含以下粉末的压粉磁芯:表面平滑性为1.1以上且2.0以下,并且扁平度为1.0以上且1.2以下的球状的第一粉末301;表面平滑性为1.7以上且2.5以下,并且扁平度为3.0以上且6.0以下的椭圆体状的第二粉末302;以及表面平滑性为3.4以上且扁平度大于6.0的鳞片状的第三粉末303。由此,在压粉磁芯的制作时,能以少量的粘结剂得到良好的流动性,第二粉末302能够进入第一粉末301之间,第三粉末303能够进入第二粉末302之间。由此,能够提高软磁性粉末的填充密度。因此,每单位体积的软磁性粉末的比例增加,能够使压粉磁芯的饱和磁通密度、磁导率之类的软磁特性提高。并且,本实施方式的软磁性粉末为球状或椭圆体状,不具有边缘之类的棱角部。因此,不会有扎入相邻的粉末而使粉末间导通的情况,能够使耐电压性能提高。另外,鳞片状的粉末虽然也存在具有棱角部的情况,但粒径较小,所以不会有扎入相邻的粉末而引起电场集中,从而导致耐电压性能下降的情况。由以上内容可知,在本实施方式及本实施例中,能够在确保软磁性粉末间的绝缘性的同时,高密度地填充软磁性粉末。因此,能够提供兼顾了高磁导率和高耐电压的压粉磁芯。(实施方式2)下面,对本发明的实施方式2进行说明。<实施方式2的压粉磁芯的特征>本实施方式的压粉磁芯包含软磁性组合物的粉末,该软磁性组合物的粉末是扁平度为1.0以上且1.2以下的球状的粉碎粉、以及扁平度为3.0以上且6.0以下的椭圆体状的粉碎粉的混合物。或者,本实施方式的压粉磁芯包含软磁性组合物的粉末,该软磁性组合物的粉末是以下的粉碎粉的混合物:表面平滑性为1.1以上且2.0以下,并且扁平度为1.0以上且1.2以下的球状的粉碎粉;以及表面平滑性为1.7以上且2.5以下,并且扁平度为3.0以上且6.0以下的椭圆体状的粉碎粉。此外,软磁性组合物只要是金属、合金、硅钢板、非晶、纳米晶合金等呈现软磁性特性的组合物即可,不特别地进行限制。另外,在软磁性组合物的粉末中,只要至少包含球状的粉碎粉及椭圆体状的粉碎粉即可,也可以包含一部分形状不属于上述形状的成分。下面,对软磁性组合物的粉末的物性和制造方法进行说明,之后,对压粉磁芯及其制造方法进行说明。<软磁性组合物的粉末的表面平滑性>如上述那样,软磁性组合物的粉末至少包含球状的粉碎粉及椭圆体状的粉碎粉。其中,球状的粉碎粉的表面平滑性为1.1以上且2.0以下,优选为1.1以上且1.7以下。另一方面,椭圆体状的粉碎粉的表面平滑性为1.7以上且2.5以下,优选为1.7以上且2.2以下。表面平滑性是指颗粒的实际的表面积s1除以与该颗粒为相同的体积等效直径d且表面粗糙度为0即表面完全平滑的正球状颗粒的表面积s2而得到的值,表面平滑性越接近1则越是表面平滑的颗粒。实际的颗粒的表面积s1例如可以利用气体吸附式的比表面积仪来测定。另外,正球状颗粒的表面积s2可以通过计算以体积等效直径d为直径的球的表面积而得到。通过减小软磁性组合物的粉末所包含的、球状的粉碎粉及椭圆体状的粉碎粉的表面平滑性,能降低制作压粉磁芯时的颗粒间的摩擦阻力,得到良好的流动性。尤其是,在将软磁性组合物的粉末与粘结剂(例如热固化性树脂)混合来形成压粉磁芯时,进入粉碎粉的表面的微细的凹凸而不再有助于流动的树脂量减少。因此,能够以更少量的粘结剂(热固化性树脂)来加压成型。其结果,能够提高压粉磁芯中的软磁性组合物的粉末的填充密度。由此,每单位体积的软磁性组合物的粉末的比例增加,能够使压粉磁芯的饱和磁通密度、磁导率之类的软磁特性提高。此外,对于球状的粉碎粉,只要表面平滑性为2.0以下就能够充分得到通过减小表面平滑性而提高填充密度的效果。另一方面,具有表面平滑性小于1.1的过度平滑的表面的颗粒,从制造成本等方面来看是不优选的。另外,对于椭圆体状的粉碎粉,只要表面平滑性为2.5以下就能够充分得到上述效果。<软磁性组合物的粉末的扁平度>另外,软磁性组合物的粉末所包含的球状的粉碎粉的扁平度为1.0以上且1.2以下,优选为1.0以上且1.1以下。另一方面,椭圆体状的粉碎粉的扁平度为3.0以上且6.0以下,优选为3.0以上且4.0以下。扁平度是指软磁性组合物的粉末(尤其是椭圆体状粉末)的三个半轴中的最大半轴除以最小半轴而得到的值,扁平度越接近1.0,则越是接近球的形状。如后述那样,在制造压粉磁芯时,对包含软磁性组合物的粉末的造粒粉进行加压成型。这时,与扁平度小于1.2的大致球状的粉碎粉相比,扁平度为1.2以上(更优选为扁平度为3.0以上)的椭圆体状的粉碎粉更易于沿着粉末的流动方向取向。而且,若粉碎粉如这样取向,则从上游观察时的投影面积比球形的小。因此,流动阻力降低。即,通过包含球状的粉碎粉和一定量的椭圆体状的粉碎粉,能够降低加压成型时的压力。其结果,能够减少树脂量及溶剂量等,并且即使粘度较高也能够成型。因此,能够提高压粉磁芯中的软磁性组合物的粉末的填充密度。此外,与表面平滑性相比,扁平度对上述效果的影响更大。这是由于,与表面平滑性相比,扁平度对外形的影响更大。另外,若加长粉碎时间,则虽然颗粒的扁平度不会明显变化,但通过粉末彼此的冲撞从而表面被一点点逐渐削去,所以表面平滑性逐渐变小。另外,在制作压粉磁芯时,与表面平滑性相比,扁平度对于得到粘结剂的良好的流动性来说,是更重要的。另外,通过增大平面平滑性较大(也就是说,表面平滑性比较低)的椭圆体状的粉碎粉的扁平度,从而易于得到粘结剂的良好的流动性。而且,较小的椭圆体状的粉碎粉能够利用少量的粘结剂,进入较大的球状的粉碎粉之间。由此,每单位体积的软磁性组合物的粉末的比例增加,能够使压粉磁芯的饱和磁通密度、磁导率之类的软磁特性提高。<软磁性组合物的粉末的粒径>软磁性组合物的粉末所包含的球状的粉碎粉的平均粒径优选为30μm以上且60μm以下,更优选为30μm以上且50μm以下。另一方面,椭圆体状的粉碎粉的平均粒径优选为10μm以上且20μm以下。这些平均粒径分别是利用microtracmt3000ii系列测定的累积粒度分布的d50%的数值。在此,软磁性组合物的粉末所包含的、粒径大于32μm的粉末的比例优选为50重量%以下,更优选为45重量%以下。另一方面,粒径为32μm以下的粉末的比例优选为50重量%以上,更优选为55重量%以上。对于粉末的粒径是否为32μm以下,可以根据是否能够通过32μm的开口来进行判断。如后述那样,若使用旋风磨来进行软磁性组合物的粉末的制造,则球状的粉碎粉的平均粒径容易变大,椭圆体状的粉碎粉的平均粒径容易变小。因此,软磁性组合物的粉末所包含的上述的球状的粉碎粉的比例优选为50重量%以下,上述的椭圆体状的粉碎粉的比例优选为50重量%以上。另外,更优选为,椭圆体状的粉碎粉的比例更多。<软磁性组合物的粉末的制造方法>对具有上述物性的软磁性组合物的粉末的制造方法进行说明。能够通过以下工序来制造软磁性组合物的粉末:制作软磁性组合物的薄带或薄片的工序1;利用旋风磨将薄带或薄片粉碎的工序2;以及对粉碎粉进行热处理的工序3。具体而言,在工序1中,通过高频加热等将合金组合物(软磁性组合物)熔解,通过液体骤冷法来制作由非晶层构成的薄带或薄片。作为液体骤冷法,可以使用fe基非晶薄带的制造等中使用的单辊式的非晶制造装置或双辊式的非晶制造装置。在工序2中,将工序1中所得到的薄带或薄片粉碎而使其粉末化。在薄带或薄片的粉碎中,通过旋风磨,使薄带和/或薄片彼此之间产生摩擦,进行摩擦粉碎。此外,若如以往技术那样,对薄带或薄片进行加热而使其结晶,则他们变脆而变得易于粉碎。但在该情况下,薄带或薄片的硬度变高,难以粉碎得较小。也就是说,粒径较小的粉碎粉的比例较少。因此,在本实施方式中,在未加热的状态下将薄带或薄片粉碎。由此,能够将硬度低的薄带或薄片粉碎得充分小,使粒径较小的粉碎粉的比例增加。对于粉碎而得到的粉末,也可以使用筛子来分级。由此,能够使软磁性组合物的粉末的粒度分布成为所希望的范围。在工序3中,对薄带或薄片的粉碎粉进行热处理,从而消除因粉碎导致的内应变,或使αfe结晶层析出。对于热处理装置,例如可以使用热风炉、热压机、灯、护套金属加热器、陶瓷加热器、回转窑等。此外,对于加热温度,只要是能够消除内应变或使αfe结晶层析出的温度即可,不特别地进行限制。<工序2的细节>在此,使用图1对上述的工序2中的粉碎粉的制造机理进行说明。在使用旋风磨时,图1a所示的软磁性薄带(也可以是软磁性薄片)101搭乘气流,从而软磁性薄带101相互摩擦。由此,如图1b所示,软磁性薄带101的表面被刮削,产生粒径较大的粉末102和粒径较小的粉末103。并且,通过继续进行粉碎,粒径较大的粉末102和粒径较小的粉末103也搭乘气流,从而粉末相互摩擦。由此,如图1c所示,粒径较大的粉末102的表面被刮削,产生上述的球状的粉末104。另外,粒径较小的粉末103的表面被刮削,产生椭圆体状的粉末105。此外,除了球状的粉末104和椭圆体状的粉末105以外,还产生软磁性薄带101的表面被刮削而得到的削屑即鳞片状的粉末106。接下来,使用图2对旋风磨的粉碎机理进行说明。旋风磨是有多个(在此为两个)旋转翼的装置,该旋转翼具有多个翼。在该旋风磨的粉碎室201的原料投入口202侧,产生由一方的旋转翼203产生的朝向半径方向外侧的气流和被另一方的旋转翼204带动的气流。另外,在连接着吸引装置的粉碎室201的排出口205侧,产生由旋转翼204产生的朝向半径方向外侧的气流和由吸引装置向排出口205侧带动的气流。也就是说,在旋风磨的粉碎室201中,在旋转翼203及旋转翼204的周围分别稳定地生成循环流。而且,若由原料投入口202投入原料206,则原料206搭乘原料投入口202侧的旋转翼203所生成的循环流,而移动至粉碎室201。移动至粉碎室201的原料的一部分(受到吸引装置的吸引力的作用的原料颗粒207)通过排出口205而被回收。另一方面,受到排出口205侧的旋转翼204的循环流的作用的原料搭乘循环流再次移动至粉碎室201的中央侧。另外,在粉碎室201的中央侧,产生了由原料投入口202侧的旋转翼203生成的朝向半径方向外侧的气流。因此,受到旋转翼203所生成的气流的作用的原料与受到旋转翼204所生成的气流的作用的原料相互摩擦。由此,进行原料的摩擦粉碎。而且,经粉碎的粉碎粉受到排出口205侧的旋转翼204所生成的气流的作用,向粉碎室201的外部方向移动。之后,受到吸引装置的作用而从排出口205被回收。重复这样的操作来进行原料的粉碎。对于进行原料的粉碎的时间,不进行限制,可根据粉碎的程度来适当选择。此外,在后述的实施例中,粉碎时间为50分钟。但是,能够通过调整粉碎时间,来得到所需的形状或粒径。通过使软磁性组合物的薄带101搭乘两张旋转翼所生成的循环流,能够对软磁性组合物的薄带101的表面进行刮削,最终能够产生球状的粉末104和椭圆体状的粉末105。在该过程中,较大的颗粒通过离心力而被引导至粉碎室的外周。另一方面,微粉在旋转轴的轴向(旋转翼的中心部)上集聚并被吸引至排出口205侧。因此,仅一定粒度的微粉从排出口205连续地排出。此外,较大的颗粒搭乘两张旋转翼所生成的循环流而表面被刮削,并滞留在粉碎室内。其间,刮削出的削屑被吸引而从排出口205排出。因此,在粉碎室201内,产生没有棱角的球状的粉末104和没有棱角的椭圆体状的粉末105。另外,在后述的实施例中,作为旋风磨200,使用了株式会社静冈工厂制的、150s、单电机的旋风磨。优选转速为11000rpm~15000rpm,最优值为15000rpm。由此,在后述的实施例2中采用的转速为15000rpm。此外,在使用行星式球磨机、磨碎机、样品磨或振动磨的情况下,无法做成球状粉或椭圆体状粉(去不掉颗粒的棱角),且粉末的平均粒径超过20μm。在使用混合磨的情况下,粉末的平均粒径成为10μm多,但无法做成球状粉或椭圆体状粉(去不掉颗粒的棱角)。另外,喷磨机无法进行粉碎。<压粉磁芯>压粉磁芯只要至少包含上述的软磁性组合物的粉末即可,也可以根据需要包含粘结剂或其他成分。对于压粉磁芯的形状和大小,可根据其用途来适当选择。可以是与一般的压粉磁芯的形状和大小相同。<压粉磁芯的制造方法>接下来,对使用上述的软磁性组合物的粉末制作压粉磁芯的方法进行说明。例如,能够通过进行以下工序来制作压粉磁芯:将通过上述工序1~3制造的软磁性组合物的粉末与粘结剂混合,来制作造粒粉的工序4;进行加压成型的工序5;以及使粘结剂加热固化的工序6。具体而言,在工序4中,将以上述方式得到的软磁性组合物的粉末、与酚醛树脂或有机硅树脂等绝缘性良好且耐热性高的粘结剂混合,来制作造粒粉。相对于软磁性组合物的粉末的量100质量份,制作造粒粉时使用的粘结剂的量优选为1~8质量份,更优选为1~3质量份。在工序5中,将工序4中所制作的造粒粉填充在具有所希望的形状的耐热性高的模具中,进行加压成型而得到压粉体。对于加压成型时的压力及加压成型的时间,可根据粘结剂的量或所需的压粉磁芯的强度等来适当选择。可以使用一般的冲压装置来进行加压成型。在工序6中,在工序5之后,根据需要而在粘结剂发生固化的温度下进行加热,从而得到在高频区域中损耗小的压粉磁芯。对于这时的温度,可根据粘结剂的种类来适当选择。(实施例2)下面,对具体地实施了上述的本实施方式的软磁性粉末的制造方法及压粉磁芯的制造方法的实施例2进行说明。使用旋风磨将通过骤冷单辊法制作的fe73.5-cu1-nb3-si13.5-b9(元素符号之后的数值表示原子%)的fe系非晶合金薄带粉碎50分钟,得到了由非晶层构成的软磁性组合物的粉末。对该软磁性组合物的粉末进行了热处理,消除了因粉碎导致的内应变,并且使αfe结晶层析出。热处理中,利用热压机在560℃下加热了2秒。并且,将有机硅树脂作为粘结剂混合到该软磁性组合物的粉末中,进行造粒,制作了造粒粉。接着,将造粒粉投入到模具中,使用冲压机在成型压力为4吨/cm2的压力下进行加压成型之后,使粘结剂固化而制作了压粉磁芯。相对于软磁性组合物的粉末100质量份,有机硅树脂为3质量份左右。<磁芯损耗的评价>对于所得到的压粉磁芯,使用b-h分析仪测定了频率100khz、磁通密度25mt时的磁芯损耗。将磁芯损耗的合格与否的基准设定为110kw/m3以下。将达到一般的金属系材料的磁芯损耗以下作为目标。利用b-h分析仪测定出的磁芯损耗为58kw/m3,达到了合格基准。也就是说,得到了在高频区域中损耗小的压粉磁芯。<粉末的形状的评价>图6中示出实施例2中所得到的软磁性组合物的粉末(压粉磁芯制作前的粉末)的sem图像。粒径较大的粉末601是上述的球状的粉碎粉(相当于上述的图1c中的粉末104),粉末602是上述的椭圆体状的粉碎粉(相当于上述的图1c中的粉末105)。通过上述的粉碎机理,粒径比较大的粉末601成为球状,粒径较小的粉末602成为椭圆体状。对所得到的软磁性组合物的粉末的粒径进行了评价。其结果,粒径大于32μm的颗粒(粉末)的比例为全部粉碎粉的40重量%。另外,粒径为32μm以下的颗粒(粉末)的比例为全部粉碎粉的60重量%。此外,粒径是根据是否能够通过32μm直径的开口而判断出来的。接下来,在图7中示出实施例2中的软磁性组合物的粉末的粒度分布。利用microtracmt3000ii系列,测定了粒度分布。图7中,横轴表示粒径,纵轴表示各粒径的软磁性组合物的粉末存在的频度。如图7所示,成为如下粒度分布:粒径大于32μm的粉末存在一定数量。另一方面,粒径为32μm以下的粉末大量存在。此外,粒径大于32μm的粉末中,扁平度为1.0以上且1.2以下的占多数,粒径小于32μm的粉末中,扁平度为3.0以上且6.0以下的占多数。而且,粒径大于32μm的粉末的平均粒径为47.3μm,粒径为32μm以下的粉末的平均粒径为16.2μm。此处所说的平均粒径,是利用microtracmt3000ii系列,针对大于32μm的粉末以及32μm以下的粉末分别测定粒度分布时,测定出的累积粒度分布的d50%的数值。此外,在对软磁性组合物的粉末整体的粒度分布进行测定的情况下,累积粒度分布的d10%约为9μm,d50%约为19μm,d90%约为49μm。另外,粒径大于32μm的粉末的表面平滑性为1.616,粒径为32μm以下的粉末的表面平滑性为2.138。也就是说,明显可知在该软磁性组合物的粉末中包含以下的粉碎粉:表面平滑性为1.1以上且2.0以下,并且扁平度为1.0以上且1.2以下的球状的粉碎粉;以及表面平滑性为1.7以上且2.5以下,并且扁平度为3.0以上且6.0以下的椭圆体状的粉碎粉。<压粉磁芯的剖面>图8中示出实施例2中的使用了软磁性组合物的粉末的压粉磁芯的剖面的sem图像。剖面504是上述的球状的粉末(相当于上述的图1c中的粉末104)的剖面。剖面505是上述的椭圆体状的粉末(相当于上述的图1c中的粉末105)的剖面。如此,明显可知:在实施例2的压粉磁芯中包含球状的粉末及椭圆体状的粉末。另外,使用旋风磨200,使软磁性组合物的粉末滞留,并使粉末彼此冲撞,由此,粉末表面的温度上升,在粉末表面形成fe氧化膜。在将氧浓度设定为0.1%(n2吹扫)而进行了粉碎的情况下,fe氧化膜的厚度为20nm以下。fe氧化膜的厚度优选为20nm以下,进一步优选为10nm以下。旋风磨200的粉碎方式是使粉末彼此冲撞的方式,因此与使粉末冲撞到叶片或球等的粉碎方式相比,能够减少粉末表面的fe氧化膜厚度。并且,通过在低氧浓度下进行粉碎,能够使fe氧化膜厚度变薄,能够使压粉磁芯的软磁特性提高。<效果>根据使用了旋风磨的摩擦粉碎,能够以大量地存在粒径大于32μm的球形状的粉碎粉和粒径为32μm以下的椭圆体形状的粉碎粉的方式,容易地对软磁性组合物的粉末的粒度分布进行控制。由此,在使用该软磁性组合物来制作压粉磁芯时,能以少量的粘结剂得到良好的流动性。而且,例如,能够使粒径为32μm以下的椭圆体形状的粉碎粉进入粒径大于32μm的球形状的粉碎粉之间。因此,能够提高压粉磁芯内的软磁性组合物的粉末的填充密度。由此,每单位体积的软磁性组合物的粉末的比例增加,能够提高压粉磁芯的饱和磁通密度、磁导率之类的软磁特性。并且,粒径大于32μm的粉碎粉为全部粉碎粉的50重量%以下,且粒径为32μm以下的粉碎粉为全部粉碎粉的50重量%以上,因此粉碎粉的电阻变大。另外,尤其是,在高频(例如,100khz以上)区域中也能够减少涡流,从而能够减少涡流损耗。因此,能够减少使用了该粉碎粉的压粉磁芯的损耗。并且,软磁性组合物的粉末是球形状的粉末粉和椭圆体形状的粉末粉的混合物,在这些粉末中没有边缘之类的棱角。因此,不会有扎入相邻的粉末而使粉末间导通的情况,能够使耐电压性能提高。然而,在通过专利文献1的技术而得到的粉碎粉中,粒径为薄带的厚度的2倍(粒径50μm)以上的粉碎粉1的比例较多。因此,粉碎粉1自身的电阻较小。并且,若达到高频(例如,100khz以上),则涡流增加,涡流损耗激增。因此,使用了该粉碎粉的压粉磁芯的损耗容易增加。由以上内容可知,根据本实施方式及本实施例,在高频区域中也能够减小软磁性组合物的粉末的涡流损耗,并且能够实现高饱和磁通密度、且可得到优异的软磁特性的压粉磁芯。(实施方式3)下面,对本发明的实施方式3进行说明。<实施方式3的压粉磁芯的特征>本实施方式的压粉磁芯包含软磁性组合物的粉末,该软磁性组合物的粉末是扁平度为3.0以上且6.0以下的椭圆体状的粉碎粉的混合物。或者,本实施方式的压粉磁芯包含软磁性组合物的粉末,该软磁性组合物的粉末是表面平滑性为1.7以上且2.5以下,并且扁平度为3.0以上且6.0以下的椭圆体状的粉碎粉的混合物。此外,软磁性组合物只要是例如金属、合金、硅钢板、非晶、纳米晶合金等呈现软磁性特性的组合物即可。另外,在软磁性组合物的粉末中,只要至少包含椭圆体状的粉碎粉即可,也可以包含一部分形状不属于上述形状的成分(例如,鳞片状的粉碎粉)。<软磁性组合物的粉末的表面平滑性>如上述那样,软磁性组合物的粉末至少包含椭圆体状的粉碎粉。椭圆体状的粉碎粉的表面平滑性为1.7以上且2.5以下,优选为1.7以上且2.2以下。另外,当在软磁性组合物的粉末中包含鳞片状的粉碎粉的情况下,优选鳞片状的粉碎粉的表面平滑性为3.4以上。表面平滑性是指颗粒的实际的表面积s1除以与该颗粒为相同的体积等效直径d且表面粗糙度为0即表面完全平滑的正球状颗粒的表面积s2而得到的值。表面平滑性越接近1则越是表面平滑的颗粒。实际的颗粒的表面积s1例如可以利用气体吸附式的比表面积仪来测定。另外,正球状颗粒的表面积s2可以通过计算以体积等效直径d为直径的球的表面积而得到。通过减小软磁性组合物的粉末中包含的椭圆体状的粉碎粉的表面平滑性,能降低制作压粉磁芯时的颗粒间的摩擦阻力,得到良好的流动性。尤其是,在将软磁性组合物的粉末与粘结剂(例如,热固化性树脂)混合来形成压粉磁芯时,进入粉碎粉的表面的微细的凹凸而不再有助于流动的树脂量减少。因此,能够以更少量的粘结剂来加压成型。其结果,能够提高压粉磁芯中的软磁性组合物的粉末的填充密度。由此,每单位体积的软磁性组合物的粉末的比例增加,能够使压粉磁芯的饱和磁通密度、磁导率之类的软磁特性提高。此外,对于椭圆体状的粉碎粉,只要表面平滑性为2.5以下就能够充分得到通过减小表面平滑性而提高填充密度的效果。<软磁性组合物的粉末的扁平度>软磁性组合物的粉末中包含的椭圆体状的粉碎粉的扁平度为3.0以上且6.0以下,优选为3.0以上且4.0以下。并且,也可以包含鳞片状的粉碎粉。对于鳞片状的粉碎粉的扁平度,优选以扁平度大于6.0的粉碎粉为主要成分。扁平度是指软磁性组合物的粉末(尤其是,椭圆体状的粉碎粉)的三个半轴中的最大半轴(长半轴)除以最小半轴(短半轴)而得到的值。扁平度越接近1.0,则越是接近球的形状。如后述那样,在制造压粉磁芯时,对包含软磁性组合物的粉末的造粒粉进行加压成型。这时,扁平度为1.2以上的椭圆体状的粉碎粉易于沿着粉末的流动方向取向。而且,若粉碎粉如这样取向,则从上游观察时的投影面积比球形的小。因此,流动阻力降低。即,通过构成为在全部粉碎粉中包含一定量的椭圆体状的粉碎粉,能够降低加压成型时的压力。其结果,能够减少树脂量及溶剂量,并且即使粘度较高也能够成型。因此,能够提高压粉磁芯中的软磁性组合物的粉末的填充密度。另外,通过增大平面平滑性较大(也就是说,表面平滑性比较低)的椭圆体状的粉碎粉的扁平度,从而易于得到粘结剂的良好的流动性。由此,每单位体积的软磁性组合物的粉末的比例增加,能够使压粉磁芯的饱和磁通密度、磁导率之类的软磁特性提高。<软磁性组合物的粉末的粒径>软磁性组合物的粉末中包含的椭圆体状的粉碎粉的平均粒径优选为10μm以上且20μm以下。鳞片状的粉碎粉的平均粒径优选为4μm以上且12μm以下。这些平均粒径分别是利用microtracmt3000ii系列测定的累积粒度分布的d50%的数值。在此,软磁性组合物的粉末中包含的椭圆体状的粉碎粉及鳞片状的粉碎粉的粒径优选为32μm以下。关于粉末的粒径是否为32μm以下,可以根据粉末是否能够通过筛子等中的32μm的开口来进行判断。<软磁性粉末的制造方法>对本发明的实施方式的软磁性粉末的制造方法进行说明。首先,在通过高频加热等将合金组合物熔解之后,通过液体骤冷法进行冷却,来制作非晶层的薄带或薄片(工序1)。在实施液体骤冷法时,例如,可以使用fe基非晶薄带的制造等中使用的单辊式的非晶制造装置或双辊式的非晶制造装置。此外,以下,以制作非晶层的薄带(以下,简称作“薄带”)的情况为例进行说明,但毋庸置疑,下述说明也适用于制作薄片的情况。接着,将工序1中所得到的薄带粉碎而得到粉碎粉(工序2)。作为薄带的粉碎方法,例如,可列举使用旋风磨来使薄带相互摩擦的方法。使用图2对该方法的细节进行后述。一般来说,已知,若在粉碎前对薄带进行加热而使其结晶,则薄带变脆,变得易于粉碎。另一方面,若进行加热则薄带的硬度变高,因此难以将薄带粉碎得较小。其结果,粒径较小的粉碎粉在全部粉碎粉中的比例较少。因此,在本实施方式中,在工序2中,采用在未加热的状态下将薄带粉碎的方法。由此,薄带的硬度变低,所以能够粉碎得较小。其结果,能够提高粒径较小的粉碎粉在全部粉碎粉中的比例。此外,例如也可以使用筛子或分级机等,将通过工序2而得到的粉碎粉分级。由此,能够得到具有所希望的粒度分布的粉碎粉。例如,也可以使用形成有32μm的开口的筛子,来获得通过工序2而得到的粉碎粉中的、32μm以下的粉碎粉。另外,也可以使用气流式的分级机,来获得通过工序2而得到的粉碎粉中的、32μm以下的粉碎粉。接着,对通过工序2而得到的粉碎粉进行热处理,从而消除因粉碎导致的内应变,或使αfe结晶层析出(工序3)。作为工序3中使用的热处理装置,例如,可以使用热风炉、热压机、灯、护套加热器、陶瓷加热器、回转窑等。此外,对于工序3中对粉碎粉进行加热时的温度,只要是能够消除内应变或使αfe结晶层析出的温度即可,不特别地进行限制。通过以上所说明的工序1~3,能够制造非晶层的薄带的粉碎粉即软磁性粉末。<粉碎粉的制造机理>在此,使用图1a~图1c,对上述工序2中的粉碎粉的制造机理进行说明。图1a所示的软磁性薄带101(软磁性组合物的一例)只要是例如金属、合金、硅钢板、非晶或纳米晶合金等具备软磁性特性的薄带即可。在使用旋风磨的情况下,图1a所示的软磁性薄带101搭乘气流,从而软磁性薄带101相互摩擦。由此,软磁性薄带101的表面被刮削,如图1b所示,产生粒径较大的粉末102及粒径较小的粉末103。并且,通过继续进行粉碎,粉末102及粉末103也搭乘气流,从而这些粉末相互摩擦。由此,粉末102的表面被刮削,产生图1c所示的球状的粉末104及鳞片状的粉末106。另外,粉末103的表面被刮削,产生图1c所示的椭圆体状的粉末105及鳞片状的粉末106。粉末106是从粉末102或粉末103刮削出的削屑。以上,对粉碎粉的制造机理进行了说明。<旋风磨的粉碎机理>使用图2对旋风磨的粉碎机理进行说明。图2是示意性地表示本实施方式中使用的旋风磨200的结构的一例的图。旋风磨200具有:粉碎室201、原料投入口202、旋转翼203、204、排出口205、旋转轴208、驱动源209。原料投入口202是投入原料206的开口部,与粉碎室201连通。原料206例如是图1a所示的软磁性薄带101。排出口205与粉碎室201连通,是排出在粉碎室201所产生的原料颗粒207的开口部。在排出口205的外部设置有吸引装置(省略图示)。粉碎室201是进行原料206的粉碎的空间。在粉碎室201中设置有旋转翼203、204。旋转翼203、204分别固定于旋转轴208。旋转轴208通过驱动源209(例如,电机)而被赋予旋转力,如箭头a所示那样旋转。由此,旋转翼203、204也同样地旋转。在旋转翼203、204旋转时,稳定地产生气流210及循环流211、212。气流210是从粉碎室201的入口侧经由粉碎室201内而流向粉碎室201的出口侧的气流。循环流211是沿着旋转翼203的表面循环的气流。循环流212是沿着旋转翼204的表面循环的气流。下面,对在具有这种结构的旋风磨200中投入原料206而得到图1c所示的各种粉末的流程进行说明。从原料投入口202投入的原料206搭乘气流210向粉碎室201流入。流入到粉碎室201的原料206的一部分搭乘循环流211或循环流212,在粉碎室201内移动。这时,搭乘循环流211的原料206与搭乘循环流212的原料206相互摩擦而被粉碎。由此,各原料206的表面被刮削,产生图1c所示的粉末104、105、106。作为微粉的粉末106(图2所示的原料颗粒207)在旋转轴208的轴向(旋转翼203、204的中心部)上集聚,搭乘气流210从粉碎室201流出,通过吸引装置(省略图示)的吸引力从排出口205排出。这样,能够仅对一定粒度的粉末106连续地进行回收。所回收的粉末106例如为鳞片状。另一方面,比粉末106大的粉末104、105搭乘循环流211或循环流212而表面被刮削,并滞留在粉碎室201内。此外,在该滞留的期间,也会从粉末104、105产生粉末106。该粉末106也与上述同样地从排出口205排出。然后,在粉碎的执行结束时,在粉碎室201内残留没有棱角的球状的粉末104和没有棱角的椭圆体状的粉末105。接着,利用筛子等将残留于粉碎室201内的粉末104、105分级,从而仅得到粉末105。此外,也可以在此处所得到的粉末105中,掺混从排出口205所回收的粉末106。对于旋风磨200的粉碎的执行时间,能根据所希望的形状或粒径来适当选择。此外,在后述的实施例中,粉碎的执行时间为20分钟。另外,在后述的实施例中,作为旋风磨200,使用了株式会社静冈工厂制的150bms、单电机的旋风磨。该旋风磨200中,转速优选为11000rpm~15000rpm,最优值为15000rpm。由此,在后述的实施例中采用的转速为15000rpm。此外,在使用行星式球磨机、磨碎机、样品磨或振动磨的情况下,去不掉薄带中颗粒的棱角,无法形成椭圆体状的粉末。并且,形成的粉末的平均粒径超过20μm。在使用混合磨的情况下,粉末的平均粒径达到10μm~20μm,但去不掉薄带中颗粒的棱角,无法形成椭圆体状的粉碎粉。另外,喷磨机无法进行粉碎。<压粉磁芯的制造方法>对于本实施方式的压粉磁芯,既可以仅用上述的软磁性粉末中的椭圆体状的粉末105来制造,也可以在椭圆体状的粉末105中掺混粘结剂或其他成分(例如,鳞片状的粉碎粉106)来制造。对于本实施方式的压粉磁芯的形状或大小,可根据其用途来适当选择。因此,本实施方式的压粉磁芯可以是与一般的压粉磁芯的形状和大小相同。下面,对本实施方式的压粉磁芯的制造方法进行说明。首先,将通过上述工序1~3制造的软磁性粉末与粘结剂混合,来制作造粒粉(工序4)。作为粘结剂,可以使用绝缘性良好且耐热性高的树脂(例如,酚醛树脂或有机硅树脂等)。相对于软磁性粉末的量100质量份,制作造粒粉时使用的粘结剂的量优选为1~8质量份,更优选为1~3质量份。接着,将工序4中所得到的造粒粉填充在具有所希望的形状的耐热性高的模具中,进行加压成型而得到压粉体(工序5)。对于加压成型时的压力和执行加压形成的时间,可根据粘结剂的量或所需的压粉磁芯的强度等来适当选择。可以使用一般的冲压装置来进行加压成型。接着,在粘结剂发生固化的温度下,对工序5中所得到的压粉体进行加热(工序6)。对于加热时的温度,可根据粘结剂的种类来适当选择。通过以上所说明的工序4~6,能够制造在高频区域中损耗较小且具有高磁导率的压粉磁芯。(实施例3)下面,对具体地实施了上述的本实施方式的软磁性粉末的制造方法及压粉磁芯的制造方法的实施例3进行说明。在本实施例中,首先,使用旋风磨将通过骤冷单辊法制作的fe73.5-cu1-nb3-si13.5-b9(元素符号之后的数值表示原子%)的fe系非晶合金薄带粉碎20分钟,得到了非晶层的软磁性粉末。并且,对所得到的软磁性粉末进行了分级而将粒径32μm以下的软磁性粉末作为处理对象取出。接着,对软磁性粉末进行了热处理,消除了因粉碎导致的内应变,并且使αfe结晶层析出。进行了如下处理来作为热处理:使用热压机,在570℃下加热10秒。接着,在完成了热处理的软磁性粉末中混合作为粘结剂的有机硅树脂以进行造粒,从而制作了造粒粉。相对于软磁性粉末100质量份,有机硅树脂为3质量份左右。接着,将造粒粉投入到模具中,使用冲压机在成型压力为4吨/cm2的压力下进行加压成型,使粘结剂固化而制作了压粉磁芯。<耐电压的评价>对以上述方式得到的压粉磁芯的耐电压进行了测定。耐电压是从压粉磁芯的上下施加电压时流过的电流超过一定量的电压。与作为比较对象的、包含球状的粉末104及椭圆体状的粉末105的软磁性粉末相比,测定出的耐电压约提高了20%。也就是说,能够得到耐电压高的压粉磁芯。<软磁性粉末的形状>使用图9对本实施例中所得到的软磁性粉末(制作压粉磁芯之前的粉末)的形状进行说明。图9是表示本实施例的软磁性粉末的sem(scanningelectronmicroscope,扫描电子显微镜)图像的图。在图9中,粉末701相当于图1c所示的粉末105。通过上述的粉碎机理和分级,图9所示的粉末701成为粒径为32μm以下的椭圆体状的粉末。<软磁性粉末的粒度分布>本实施例的软磁性粉末的粒度分布如图10所示。利用microtracmt3000ii系列,测定出了图10所示的粒度分布。在图10中,横轴表示粒径,纵轴表示各粒径的软磁性粉末存在的频度。如图10所示,软磁性粉末的平均粒径为17.4μm。此处所说的平均粒径,是利用microtracmt3000ii系列测定粉末的粒度分布时的累积粒度分布的d50%的数值。另外,32μm以下的软磁性粉末的表面平滑性为2.138。也就是说,明显可知:在32μm以下的软磁性粉末中,包含表面平滑性为1.7以上且2.5以下,并且扁平度为3.0以上且6.0以下的椭圆体状的粉末105。此外,在旋风磨200的粉碎的执行时间比20分钟长的情况下,虽然椭圆体状的粉末105的扁平度不会明显变化,但通过粉末彼此的冲撞从而表面被一点点削去,所以椭圆体状的粉末105的表面平滑性变小。在制作压粉磁芯的时候,与表面平滑性相比,扁平度对于得到粘结剂的良好的流动性来说,是更重要的。<压粉磁芯的剖面>使用本实施例的软磁性粉末制造的压粉磁芯的剖面的sem图像如图11所示。图11所示的剖面506是图1c所示的粉末105的剖面。另外,使用旋风磨200,使软磁性组合物的粉末滞留,并使粉末彼此冲撞,由此,粉末表面的温度上升,在粉末表面形成fe氧化膜。在将氧浓度设定为0.1%(n2吹扫)而进行了粉碎的情况下,fe氧化膜的厚度为20nm以下。fe氧化膜的厚度只要至少为3nm以上即可。旋风磨200的粉碎方式是使粉末彼此冲撞的方式,因此与使粉末冲撞到叶片或球等的粉碎方式相比,能够减小粉末表面的fe氧化膜厚度。并且,通过在低氧浓度下进行粉碎,能够使fe氧化膜厚度变薄,能够使压粉磁芯的软磁特性提高。<效果>根据本实施方式及本实施例中的使用了旋风磨200的摩擦粉碎,能够以仅存在粒径为32μm以下的椭圆体状的粉末105的方式或以存在粒径为32μm以下的椭圆体状的粉末105及粒径为32μm以下的鳞片状的粉末106的方式,容易地对软磁性粉末的粒度分布进行控制。由此,在压粉磁芯的制作时,能以少量的粘结剂得到良好的流动性,鳞片状的粉末106能够进入椭圆体状的粉末105之间。由此,能够提高压粉磁芯内的软磁性粉末的填充密度。因此,每单位体积的软磁性粉末的比例增加,能够使压粉磁芯的饱和磁通密度、磁导率之类的软磁特性提高。并且,在本实施方式中,椭圆体状的粉末105不具有边缘之类的棱角部。因此,不会有粉末105扎入相邻的粉末而使粉末间导通的情况,能够使耐电压性能提高。另外,鳞片状的粉末106虽然也存在具有棱角部的情况,但粒径较小。因此,不会有粉末106扎入相邻的粉末而引起电场集中,从而使耐电压性能下降的情况。并且,椭圆体状的粉末105及鳞片状的粉末106的颗粒尺寸较小,内部电阻较高,因此施加电压时的电荷分散,能够使耐电压性能提高。由以上内容可知,本实施方式及在本实施例中,能够在确保软磁性粉末间的绝缘性的同时,高密度地填充软磁性粉末。因此,能够提供兼顾了高磁导率和高耐电压的压粉磁芯。此外,本发明不限于上述各实施方式的说明,能够在不脱离其要点的范围内进行各种变形。另外,也可以对各实施方式进行适当组合。工业实用性本发明的压粉磁芯及其制造方法,例如可用于在扼流线圈、电抗器、变压器等电感器中使用的、使用了软磁性粉末的压粉磁芯。当前第1页12