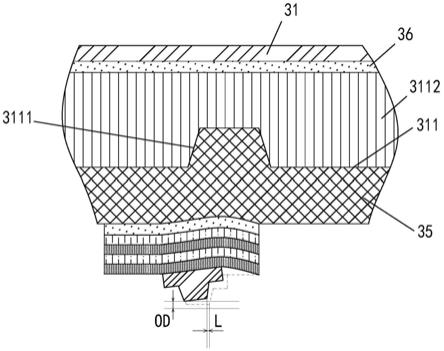
一种实现薄膜探针测量滑移的方法
1.技术领域
2.本发明属于探针卡、晶圆测试技术领域,具体涉及一种实现薄膜探针测量滑移的方法,该方法适用于薄膜探针头及薄膜探针卡。
背景技术:3.近年来,随着5g技术和消费电子技术的发展和普及,半导体器件不断朝着小型化、集成化、衬垫间距密集化发展,工作频率不断提高,面向高频的晶圆级测试逐渐成为rf芯片生产中不可获取的重要一环。相较于其他类型探针卡,薄膜探针卡实现了小尺度的探针结构加工和高精度的信号线结构参数控制,减少了寄生电容和电感的产生,极大地缩短了信号路径,提高了阻抗匹配程度,广泛应用于面向高频的晶圆级测试分析。
4.晶圆测试过程中,需提供适当的测量滑移量和可控的接触力大小。
5.测量滑移,是指探针与被测pad开始接触并开始垂直抬升运动时,探针作出微小的水平运动。适量的对推开被测焊垫或凸块表面氧化物,获得稳定电接触极为必要:滑移过小,可能会导致探针获得稳定接触所需的垂直接触力过大,对pad产生损伤;滑移过大,可能导致探针接触到pad外钝化层区域,损伤被测物。
6.可控的接触力对保证芯片pad不受损伤具有积极作用。目前常用的焊盘及凸块材料包括铝、金、铜或焊料:在空气中铝表面易发生氧化,测试过程中一般需要3-5gf的力,以穿透或推开表层氧化物,实现稳定接触;金由于材质较软,所需接触力很小, 一般在0.1-1gf之间;铜材料则需要更大的力建立良好的接触,约为5-6gf。随着半导体工艺的小型化和集成化,焊垫金属层和低k层间介质层变薄,也提高了对探针接触力控制的要求。
7.专利us5395253中提出:初始薄膜处于拉伸状态,当探针与被测pad开始接触并开始垂直抬升运动时,薄膜逐渐处于放松状态,探针会因此向薄膜中心区域做微小水平运动,产生测量滑移。这种方式存在的一个显著缺点在于探针的测量滑移量与探针相对薄膜中心位置有关,不均一。
8.现有技术中,最具代表性的结构可参见美国专利us7893704,它提出了一种新型的薄膜探针结构,它是将探针设计为类似悬臂的结构,利用测试过程中类似悬臂的探针结构绕悬臂末端的旋转实现了测量滑移的实现,但这种方式由于探针需反复绕悬臂末端进行旋转运动,该处应力集中,薄膜易损坏。
9.可见,本领域亟须一种实现薄膜探针测量滑移的方法,能够实现适当的测量滑移,并提供可控的接触力,特别地,可降低薄膜探针应力,延长薄膜探针寿命。
技术实现要素:10.本发明目的是提供一种实现薄膜探针测量滑移的方法,可实现测试过程中探针的适当测量滑移,提供可控的接触力,特别地,可降低薄膜探针使用过程中的应力,延长使用
寿命。
11.为达到上述目的,本发明采用的技术方案是:一种实现薄膜探针测量滑移的方法,在薄膜探针中头的刚性作用面与上设探针的薄膜之间垫设一弹性体层;该弹性体层在探针的轴向平面上,以穿过探针的任一轴向线为界线,其一侧的厚度与另一侧的厚度具有一差值,以此使测试时探针能够发生偏转从而产生测量滑移。
12.上述方案中,在所述刚性作用面上开设凹槽,且将凹槽壁对准所述界线,并以弹性体层布满整个刚性作用面以及填充凹槽,使所述弹性体层以穿过探针的任一轴向线为界线,使其一侧的厚度与另一侧的厚度具有差值。
13.上述方案中,将所述刚性作用面设计为在探针的轴向平面上倾斜的斜面,并以所述弹性体层一侧表面与该斜面相贴合。
14.上述方案中,在所述刚性作用面上设置一个或多个在探针的轴向平面上内凹的曲面,并以所述弹性体层一侧表面与所述曲面相贴合。
15.上述方案中,所述弹性体层在探针的轴向平面上,靠所述刚性作用面中心侧的厚度大于其外侧的厚度。
16.上述方案中,所述界线与探针的轴心线相重合。
17.现有技术通常的薄膜探针卡,包括pcb板、连接件以及薄膜探针头,而薄膜探针头包括提供一刚性作用面的支撑体、覆在支撑体的刚性作用面上的薄膜、以及设置在薄膜上的探针和互连线,其薄膜直接覆于刚性作用面上。
18.而本发明突破性地在刚性作用面与上设探针的薄膜之间垫设一弹性体层,且该弹性体层在探针的轴向平面上,以穿过探针的任一轴向线为界线,其一侧的厚度与另一侧的厚度具有一差值,从而使探针在接触过程能够发生适量偏转产生测量滑移,以穿透或推开被测芯片表层氧化物,实现更稳定地接触。
19.所述“穿过探针的任一轴向线为界线,其一侧的厚度与另一侧的厚度具有一差值”中的差值的数值具体需根据弹性体弹性系数进行调整,一般来说,测试过程中探针卡的垂直方向运动在60-100um之间,水平滑移量仅需3-8um左右。按照针长50um计算,产生3-8um的水平滑移量,需要探针的偏转角度在3-10
°
左右,即要求探针两侧的弹性体表面与水平角度仅为3-10
°
。假设探针针座水平方向长度为300um,此时探针两端的高度差在18-48um。如单位厚度弹性体,弹性范围内的极限压缩量为a,则要求两端弹性体厚度差至少为18/a。假设,弹性体弹性系数为b,即压缩单位位移所需力为b,探针测试过程中所需接触力为c,则弹性体总体厚度不得小于c/b。
20.在测试过程中:初始状态探针与被测芯片pad未接触,衬在刚性支撑体上方的弹性组件处于初始压缩状态,弹性体层也处于未压缩状态;随着测试od的施加,探针与被测芯片pad接触,垂直方向发生位移,大部分位移被弹性组件吸收,剩余部分位移由探针和弹性体层共同吸收;这时就由于探针两侧所衬的弹性体的厚度的不一致,在探针垂直运动的同时就发生了稍稍地偏转,探针在水平方向上产生滑移,可推开被测芯片表面脏污和氧化物,实现更稳定的电连接。
21.本发明有益效果:1、本发明每个探针两侧所衬的弹性体层具有厚度差,使得探针在垂直方向运动的同时实现了水平方向的侧滑,实现了稳定可靠的电接触。
22.2、本发明通过控制所述界线与探针轴心线之间的偏心量,以及两侧弹性体的厚度差值等参数,即可最终控制弹性体层在探针两侧的厚度差,就可实现测量滑移量的控制,再通过控制弹性体层的平面部分的厚度,就实现了接触力的控制。
23.3、本发明通过增加弹性体层,实现了探针局部高度差异及整体倾斜等平面度问题的吸收和兼容,防止由于局部探针过长或多短导致的接触力过大,被测pad损伤或探针虚接、开路等问题。
附图说明
24.图1为应用本发明实施例一及实施例二的薄膜探针卡的结构示意图;图2为应用本发明实施例一、实施例二的薄膜探针头的结构示意图;图3为应用本发明实施例一及实施例二的薄膜探针头的局部放大示意图;图4为应用本发明实施例一的薄膜探针头的各凹槽与探针的对应位置的示意图;图5为应用本发明实施例一的薄膜探针头测试前探针位置示意图;图6为本发明实施例一的薄膜探针头测试时探针位置对比示意图;图7为应用本发明实施例二的薄膜探针头测试前探针位置示意图;图8为应用本发明实施例二的薄膜探针头测试时探针位置示意图。
25.以上附图中:1、pcb板;11、同轴连接器;12、信号连接点;13、pcb走线;14、弹簧结构;15、pcb端螺纹孔;2、连接件;3、薄膜探针头;31、支撑体;311、刚性作用面;3111、凹槽; 3112、支撑刚性体;3113、斜面。
26.32、薄膜;33、探针;331、针座结构;332、针尖结构;34、互连线;35、弹性体层;36、黏附层;37、弹性组件;38、补强板;381、装配用螺丝孔;382、调平用螺丝孔;39、调平螺丝。
具体实施方式
27.下面结合附图及实施例对本发明作进一步描述:实施例一:一种实现薄膜探针测量滑移的方法,参见附图1-6所示:薄膜探针卡,通常都包括pcb板1、连接件2以及薄膜探针头3;所述薄膜探针头3包括提供一刚性作用面311的支撑体31、覆在支撑体31的刚性作用面311上的薄膜32、以及设置在薄膜32上的探针33和互连线34。
28.本施例方法是在薄膜探针头3中的刚性作用面311与上设探针33的薄膜32之间垫设一弹性体层35;该弹性体层35在探针33的轴向平面上,以穿过探针的任一轴向线为界线a,其一侧的厚度与另一侧的厚度具有一差值,以此使测试时探针33能够发生偏转从而产生
测量滑移l。
29.具体,是在所述刚性作用面311开设凹槽3111,如图举例是支撑体31上包括有一固定在其上的支撑刚性体3112,将支撑刚性体3112上的表面作为刚性作用面311,在其上开设凹槽3111。且将凹槽3111的槽壁对准所述界线a,并以弹性体层35布满整个刚性作用面以及填充凹槽3111,使所述弹性体层35以穿过探针33的任一轴向线为界线a,其一侧的厚度与另一侧的厚度具有所述差值。
30.该差值的数值具体需根据弹性体弹性系数进行调整,一般来说,测试过程中探针卡的垂直方向运动在60-100um之间,水平滑移量仅需3-8um左右。按照针长50um计算,产生3-8um的水平滑移量,需要探针的偏转角度在3-10
°
左右,即要求探针两侧的弹性体表面与水平角度仅为3-10
°
。假设探针针座水平方向长度为300um,此时探针两端的高度差在18-48um。如单位厚度弹性体,弹性范围内的极限压缩量为a,则要求两端弹性体厚度差至少为18/a。假设,弹性体弹性系数为b,即压缩单位位移所需力为b,探针测试过程中所需接触力为c,则弹性体总体厚度不得小于c/b。
31.再进一步,较佳是所述弹性体层35在探针的轴向平面上,靠所述刚性作用面311中心侧的厚度大于其外侧的厚度,以免探针测试偏转后薄膜中部受力过大。
32.如图5所示,较佳是,所述界线a与探针的轴心线相重合。
33.具体,应用本实施例一的薄膜探针卡的结构如下:pcb板1为多层环氧树脂线路板,其上分布有同轴连接器11和信号连接点12,其内部分布有pcb走线13,分别连接同轴连接器11到对应信号连接点12,实现电信号导通和传输;pcb板1表面还分布有弹簧结构14和pcb端螺纹孔15;pcb板1中心位置掏空,用于容纳薄膜探针头3;弹簧结构14位于pcb板1中心掏空处外周,用于实现与薄膜探针头3的紧密连接。
34.所述支撑体31为一刚性体,其中部具有一向下突出的凸部,该凸部的下表面作为所述刚性作用面311。所述支撑体31上在凸部的外围设有供与pcb板1相抵的连接面,该连接面也被所述薄膜32覆盖,在对应于连接面的薄膜32部位也设有探针33,该探针33用于与pct板1对接。
35.所述支撑体31上通过黏附层36先固定上一支撑刚性体3112,支撑刚性体3112的表面作为所述刚性作用面311,在其开设凹槽3111,这些凹槽3111朝向探针33设置,且与探针33一对一对应,凹槽3111与所对应的探针33在作用面311上的投影相互偏心;所述弹性体层35嵌在作用面311与薄膜32之间,弹性体层35上对应每个凹槽3111设有凸起嵌块,弹性体层35的凸起嵌块填满对应凹槽3111,以此,所述弹性体层35上在每个探针33两侧的部分具有厚度差。
36.具体,弹性体层35的上表面与支撑刚性体3112的表面共形,完全充填于凹槽3111中,而弹性体层35的下表面与作用面311相平行。弹性体层35相对所述支撑刚性体3112表面具有一定厚度,且弹性体层35在凹槽3111壁面边缘两侧的厚度不一致。弹性体层35材料为pdms、硅胶等柔性材料,可通过调节材料配比、固化温度等条件实现弹性调整,实现被测芯片pad或探针结构间的微小高度差吸收和兼容。
37.具体,所述凹槽3111的竖向截面为柱状或锥台状,图中所示为锥台状,在上下方向上投影所述探针33跨在对应的凹槽3111的外轮廓线上。
38.所述探针33具体包括针座结构331和针尖结构332两部分。针尖结构332位于针座
结构331之上。针座结构331形状为长方体、圆柱、棱柱等,材料可为铑、ni或pd-ni、ni-b合金等高硬度材料。针尖结构形状为截断金字塔形或棱台、圆台等,材料为铑、ni或pd-ni、ni-b合金等耐磨性材料。
39.所述支撑体31的上方还设有一补强板38,该补强板38为一中心设凹陷区域的金属板,其上分布有装配用螺丝孔381和调平用螺丝孔382,边缘与支撑体31连接,其中心凹陷区域用于容纳弹性组件37,弹性组件37可为气囊、多爪弹簧等弹性体结构,如图示为弹性组件37为一气囊。调平螺丝39位于调平用螺丝孔382中,底部与弹性组件37上表面接触,调整多个调平螺丝39的相对位置可实现增强板38和支撑体31之间倾斜的校正。
40.弹性组件37位于补强板38与支撑体31之间,测试过程中弹性组件37处于压缩状态,施加od,弹性组件37可发生弹性形变,吸收垂直方向运动位移。
41.测试过程中:初始状态如图5所示,探针33与被测芯片pad未接触,弹性组件37处于初始压缩状态,弹性体层35处于未压缩状态;随着测试od的施加,如图6所示,探针与被测芯片pad接触,垂直方向发生位移,大部分位移被弹性组件37吸收,剩余部分位移由探针33和弹性体层35共同吸收;由于探针33两侧对应的弹性体层35厚度不一致,因此垂直运动的同时会发生倾斜,探针33侧向产生距离为l的滑移,可推开被测芯片表面脏污和氧化物,实现更稳定的电连接。
42.实施例二:一种实现薄膜探针测量滑移的方法,参见附图7-8所示:本实施例方法是在薄膜探针中的刚性作用面311与上设探针33的薄膜32之间垫设一弹性体层35,与实施例一的不同之处在于:所述刚性作用面311设计为一个或多个在探针33的轴向平面上倾斜的斜面3113,该斜面3113在所述界线a处的斜率按需要偏转的角度选择。具体测试状态如图7和图8所示。
43.其具体结构同实施例一中的薄膜探针头相同,这里不再赘述。
44.上述实施例为举例,实际中可作出以下实际变化:1、还可以在所述刚性作用面311上设置一个或多个在探针33的轴向平面上内凹的曲面,同样也能达到使弹性体层35一侧的厚度与另一侧的厚度具有一差值,以此使测试时探针能够发生偏转从而产生测量滑移。
45.2、所述界线a可以按需要探针33偏转的情况进行调整,界线a只要穿过探针33,其并不需要与探针33的轴心线重合,而当将界线a与探针33的轴心线重合为较佳的情况。
46.3、所述支撑刚性体3112可以去除不采用;所述薄膜32与弹性体层35之间的黏附层36也可以去除,薄膜32以其他方式相对支撑弹性层352下表面固定,或者不固定而仅是绷紧抵靠在支撑弹性层352下表面上也可。
47.上述实施例只为说明本发明的技术构思及特点,其目的在于让熟悉此项技术的人士能够了解本发明的内容并据以实施,并不能以此限制本发明的保护范围。凡根据本发明精神实质所作的等效变化或修饰,都应涵盖在本发明的保护范围之内。