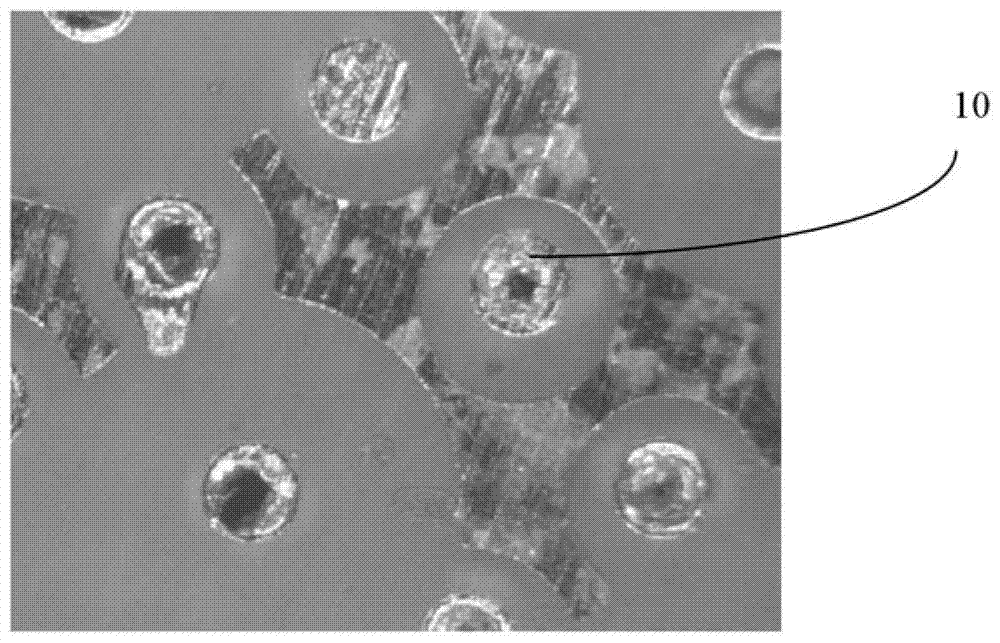
本发明属于PCB背板制作领域,尤其涉及PCB背板的压合制程的作业方法。
背景技术:随着集成电路等元件的集成度提高及其I/O数的增加、电子组装技术的进步和信号传输的高频化和高速数字化的发展,以及电子设备高速发展的升级与换代需求,PCB背板能够承载功能子板、信号传输及电源传输等功能,而其信号处理功能逐渐弱化。该PCB背板具有板于尺寸大、层数高、厚度大、孔径纵横比高等特点,该PCB背板的尺寸为660*810mm,而普通PCB的尺寸为550*610mm。现有技术中压合PCB的过程包括棕化步骤、铆合步骤、排板步骤、压合步骤及拆板步骤,其中,棕化时的温度为80℃,棕化后烤板的方式为叠在一起烤板;铆合时,铆钉机台面平铺压合用的钢板,且铆合方式为在铆钉机上边排边铆,且铆钉机下模冲针为10mm,由于铆钉机下模冲针太短,可能使冲针不会露出来,从而不能牢固的将背板各芯板进行铆合;在排板的时候,排版的层数为4-5层,排版的方式如图1所示,为铆合好的PCB21的两侧加铝片22,铝片22之后加钢板23,钢板23之后加20张牛皮纸24,即牛皮纸24+铜板23+铝片22+铆合好PCB背板21的方式;在压合的时候,压合的压力为350-380PSI,温度为90℃。通过上述制程压合后的板于,芯板与芯板之间存在图2所示的空洞10,且由于气泡沿有排出,形成在图3所示裸铜区11,所以在钻孔,沉铜,板电之后,药水容易渗入空洞10及裸铜区11中,导致内层短路。
技术实现要素:本发明实施例的目的在于提供一种超大尺寸PCB背板压合制作方法,旨在解决由于现有技术中的PCB制作中,压合之后容易出现空洞,气泡,从而使在后续钻孔,沉铜,板电之后,药水渗入,导致内层短路的问题。本发明实施例是这样实现的,一种超大尺寸PCB背板压合制作方法,该PCB背板包括多个芯板,该制作方法包括:棕化步骤:将各所述芯板进行棕化处理后烘干;铆合步骤:在每两个芯板之间加入PP片,并将加入PP片的多个所述芯板在铆钉机上铆合在一起形成多层芯板;排板步骤:对铆合好的多层芯板在钢板上进行排板,并与其他压合需要的材料进行叠合;压合步骤:将叠合后的的多层芯板推入热压机,经过高温、高压使PP片融化,使各所述芯板结合在一起。。优选地,该方法还包括钻孔排气的步骤,在芯板铆合后或铆合前容易产生气泡的位置钻排气孔。优选地,所述棕化步骤中包括烘干子步骤,烘干子步骤中的烘干温度为90℃。优选地,所述棕化步骤包括烤板子步骤,烤板子步骤中的烤板方式为插架式,烤板温度为120℃,烤板时间为1小时。优选地,所述铆合步骤中铆合的方式为:先将需要铆合的芯板用钢板支承,然后用Pin钉套好四角或四边,再放到铆钉机上铆合。本发明实施例通过增加钻排气孔的步骤,且对棕化,铆合,压合各个步骤中的参数进行改进,有效的减少了PCB背板制作中,压合制程中产生的空洞及气泡,从而有效的减少了后续经过钻孔,沉铜,板电制程之后的内层短路问题。附图说明图1是现有技术中的PCB制作方法中叠板方式的示意图;图2及图3为现有技术中的PCB制作方法中芯板经压合后产生的空洞及有气泡产生的裸铜区的照片;图4是本发明一实施例中的PCB制作方法中压合制程的流程图;图5是图4所示方法中排板步骤中的叠板方式的示意图。具体实施方式为了使本发明的目的、技术方案及优点更加清楚明白,以下结合附图及实施例,对本发明进行进一步详细说明。应当理解,此处所描述的具体实施例仅仅用以解释本发明,并不用于限定本发明。以下结合具体实施例对本发明的具体实现进行详细描述:如图4所示,为本发明一实施方式中制作PCB背板的的方法的工艺流程图。该PCB背板包括多个芯板(图未示),该多个芯片经过压合工艺之后形成PCB背板,本实施方式中,该PCB背板为背板,具体的压合工艺流程如图4所示。步骤S40为棕化步骤:将所述芯板进行棕化处理后烘干,该步骤又包括烘干子步骤及烤板子步骤,其中烘干子步骤中芯板的烘干温度从正常的80℃提高到90℃,在烤板子步骤中,烘烤芯板的方式为由原来叠在一起的方式改为插架方式,而且保持120℃的温度烤一个小时,以保证板内水汽充分蒸发。插架方式具体为将芯板放在一个架子上,且芯板在该架子上被互相隔开,从而缩短烤板时间,且有利于水蒸气的蒸发。步骤S41为铆合步骤:在每两个芯板之间加入PP片(胶片),并将加入PP片的多个芯板在铆钉机上铆合在一起形成多层芯板,在铆合时,铆钉机台面平铺压合用钢板,铆合方式由原来的在铆钉机上边排边铆的方式改成用钢板支承先用PIN钉套好四角或四边再放在铆钉机上铆合,如此,防止层与层之间产生偏位,滑板;同时,调整上、下模具在同一直线,并将铆钉机下模冲针由原来的10mm更换成15mm的冲针,使芯板套上去后冲针能够露出来,从而保证铆钉开花均匀,如此使芯板之间的空隙减少,从而减小后续空度及气泡的产生。步骤S42为钻孔排气步骤,在PCB背板尺寸大,板较厚,内层铜厚较厚时,压合时因气体不能完全排出释放形成气泡残留在PCB背板内,在铆合后的多层芯板上填胶不良或者容易产生气泡的地方钻排气孔,具体所选择的排气孔的位置应当为后续钻孔制作中有需要钻孔的位置,即在有钻孔位的地方钻排气孔,所钻排气孔大小比所实际要钻的孔的孔径小0.3mm,这样可以保证压合时气体从这些排气孔中释放出来,同时这些排气孔孔在压合后重新填胶被封住,后续钻孔时再用原孔径钻掉,后续正常制作即可。在其他实施方式中,该步骤也可在铆合步骤之前对单个芯板钻排气孔。步骤S43为排板步骤:对铆合好的多层芯板在钢板上进行排板,并与其他压合需要的材料进行叠合,其他压合需要的材料包括铝片、钢板、及牛皮纸等,本实施方式中,还包括离型膜和硅胶垫,本实施方式中,排板的层数为2层,每层板的叠板如图4所示,即在图1所示叠板方式的基础上,在钢板22与铝片21之间加离型膜25及硅胶垫26,其中,硅胶垫25在铝片21之后,离型膜26在硅胶垫25之后,加了硅胶垫25及离型膜26之后,有助于在压合时缓冲热量,使铆合好的PCB21受热均匀,从而使气泡缓慢排出。在其他实施方式中,其他压合需要的材料不限于上述材料,叠板的次序也不限于本实施方所描述的方式,具体可以根据实际情况进行变化。步骤S44为压合步骤:将叠好的PCB背板推入热压机,经过高温,高压使PP片融化,从而使芯板紧密的结合在一起,压合时的转高压时间不能太早也不能太迟,本实施方式中为35分钟,如此可保证PP在充分流动使填高压,保证填胶的均匀性。转高压压力由普通的350-380PSI提高到450PSI,转高压的温度为由原来的90℃左右提高到106℃,且根据材料特性来调整升温速率,本实施方式中,温度为80-140℃之间的升温速率为2.0-2.5℃/分钟,如此在压合的时候,可使流胶均匀,从而有效的减少了空洞及气泡。本发明通过对压合制成中的各个步骤进行改进,从而有效减少了PCB背板在压合后产生的空洞和气泡,从而减少了PCB背板后续渗铜短路的问题。以上所述仅为本发明的较佳实施例而已,并不用以限制本发明,凡在本发明的精神和原则之内所作的任何修改、等同替换和改进等,均应包含在本发明的保护范围之内。