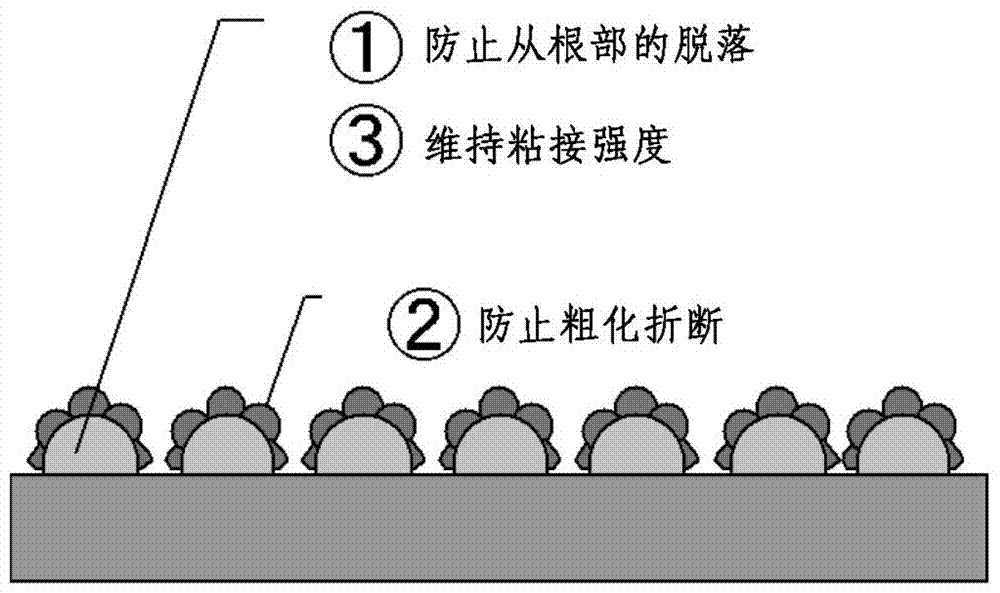
本发明涉及高频电路用铜箔、高频电路用覆铜板、高频电路用印刷布线板、高频电路用带载体的铜箔、电子设备及印刷布线板的制造方法。
背景技术:在这半个世纪以来,印刷布线板取得了大幅的进展,时至今日已经发展到几乎在所有的电子设备中均使用印刷布线板。随着近年的电子设备的小型化、高性能化需求的增大,搭载部件的高密度安装化、信号的高频化取得进展,对印刷布线板要求优异的高频应对。为了确保输出信号的品质,对高频用基板要求传输损耗的降低。传输损耗主要包括源于树脂(基板侧)的介质损耗和源于导体(铜箔侧)的导体损耗。树脂的介电常数及介质损耗角正切越小,则介质损耗越减少。在高频信号中,导体损耗的主要原因在于:因所谓频率越高而电流越仅在导体的表面流动这样的趋肤效应而使电流流过的截面积越减少,电阻越高。作为以降低高频用铜箔的传输损耗为目的的技术,例如专利文献1中公开了一种高频电路用金属箔,其在金属箔表面的一面或两面覆盖银或银合金属,并在该银或银合金覆盖层上形成厚度比上述银或银合金覆盖层的厚度更薄的除银或银合金以外的覆盖层。此外,记载有由此可以提供即使在用于卫星通信这样的超高频区域中也会减小由趋肤效应所致的损耗的金属箔。此外,专利文献2中公开了一种高频电路用粗化处理压延铜箔,其特征在于,压延铜箔经再结晶退火后的压延面的利用X射线衍射求得的(200)面的积分强度(I(200))相对于微粉末铜的利用X射线衍射求得的(200)面的积分强度(I0(200))为I(200)/I0(200)>40,利用电镀对该压延面进行粗化处理后的粗化处理面的算术平均粗糙度(以下,称作Ra)为0.02μm~0.2μm,十点平均粗糙度(以下,称为Rz)为0.1μm~1.5μm,该压延铜箔为印刷电路基板用原材料。此外,还记载了由此可以提供能够在超过1GHz的高频频率下使用的印刷电路板。进而,专利文献3中公开了一种电解铜箔,其特征在于,铜箔的表面的一部分是由瘤状突起形成的表面粗糙度为2μm~4μm的凹凸面。此外,还记载了由此可以提供高频传输特性优异的电解铜箔。【现有技术文献】【专利文献】【专利文献1】日本专利第4161304号公报【专利文献2】日本专利第4704025号公报【专利文献3】日本特开2004-244656号公报
技术实现要素:源于导体(铜箔侧)的导体损耗,是由如上所述因趋肤效应而使电阻变大所引起的,已知该电阻不仅有铜箔本身的电阻的影响,而且还有在铜箔表面由为确保与树脂基板的粘接性而进行的粗化处理形成的表面处理层的电阻的影响,具体而言,铜箔表面的粗糙度是导体损耗的主要原因,可知粗糙度越小则传输损耗越是减少。本发明人等对铜箔表面的粗糙度与传输损耗的关系进行了更深入的研究,结果发现:未必限于铜箔表面的粗糙度越小则传输损耗越减少,尤其在铜箔表面的粗糙度减小到某个程度时,传输损耗的减少与铜箔表面的粗糙度的关系出现显著的偏差,难以仅通过控制铜箔表面的粗糙度而使传输损耗良好地减少。此外,对于铜箔表面的粗化处理而言,已知有钴-镍合金镀层的形成,但是,以往的形成有钴-镍合金镀层的铜箔,在其表面形成的由铜-钴-镍合金镀敷得到的粗化粒子的形状为树枝状,因此从该树枝的上部或根部剥落而产生通常被称作落粉现象的问题。该落粉现象是难以解决的问题,铜-钴-镍合金镀敷的粗化处理层虽然具有耐热性优异的特征,但是,容易因外力而使粒子脱落,出现产生由处理中的“摩擦”所致的剥离、由剥离粉所致的辊的污染、由剥离粉所致的蚀刻残渣的问题。为此,本发明的目的在于,提供即使用于高频电路基板也能够良好地抑制传输损耗、且能够良好地抑制形成于铜箔表面的粗化粒子从该表面剥落的现象、即所谓的“落粉”的产生的高频电路用铜箔。本发明人发现:在带载体的铜箔的极薄铜层表面形成规定的粗化粒子层,且控制该粗化粒子层的三维表面积相对于二维表面积之比,这对于在高频电路基板中使用时的传输损耗的抑制、以及对铜箔表面的落粉的抑制极为有效。本发明鉴于上述见解而完成,本发明的一个方面为一种高频电路用铜箔,其是在铜箔的表面形成了铜的一次粒子层后在该一次粒子层上形成了包含铜、钴及镍的3元系合金的二次粒子层的铜箔,其粗化处理面的一定区域的基于激光显微镜得到的三维表面积相对于二维表面积之比为2.0以上且小于2.2。本发明的一个实施方案的高频电路用铜箔,其中,上述铜的一次粒子层的平均粒径为0.25~0.45μm,由包含铜、钴及镍的3元系合金形成的二次粒子层的平均粒径为0.35μm以下。本发明的另一实施方案的高频电路用铜箔,其中,上述一次粒子层及二次粒子层为电镀层。本发明的再一实施方案的高频电路用铜箔,其中,上述二次粒子为在上述一次粒子上生长的1个或多个树枝状的粒子、或者在上述一次粒子上生长的正常镀层。本发明的再又一实施方案的高频电路用铜箔,其中,上述一次粒子层及二次粒子层的粘接强度为0.80kg/cm以上。本发明的再又一实施方案的高频电路用铜箔,其中,上述一次粒子层及二次粒子层的粘接强度为0.90kg/cm以上。本发明的再又一实施方案的高频电路用铜箔,其中,在上述二次粒子层上形成有(A)合金层及(B)铬酸盐层中的任意一者或两者,所述(A)合金层包含Ni和选自Fe、Cr、Mo、Zn、Ta、Cu、Al、P、W、Mn、Sn、As及Ti中的一种以上的元素。本发明的再又一实施方案的高频电路用铜箔,其中,上述二次粒子层上依次形成有(A)合金层及(B)铬酸盐层中的任意一者或两者、和硅烷偶联层,所述(A)合金层包含Ni和选自Fe、Cr、Mo、Zn、Ta、Cu、Al、P、W、Mn、Sn、As及Ti中的一种以上的元素。本发明的再又一实施方案的高频电路用铜箔,其中,在上述二次粒子层上形成有Ni-Zn合金层及铬酸盐层中的任意一者或两者。本发明的再又一实施方案的高频电路用铜箔,其中,在上述二次粒子层上依次形成有Ni-Zn合金层及铬酸盐层中的任意一者或两者、和硅烷偶联层。本发明的再又一实施方案的高频电路用铜箔,其中,在上述二次粒子层的表面具备树脂层。本发明的再又一实施方案的高频电路用铜箔,其中,在上述包含Ni和选自Fe、Cr、Mo、Zn、Ta、Cu、Al、P、W、Mn、Sn、As及Ti中的一种以上的元素的合金层、上述铬酸盐层、上述硅烷偶联层或上述Ni-Zn合金层的表面,具备树脂层。本发明的另一个方面为一种带载体的铜箔,其是在载体的一面或两面依次具有中间层、极薄铜层的带载体的铜箔,上述极薄铜层为本发明的高频电路用铜箔。本发明的一个实施方案的带载体的铜箔,其是在上述载体的一面依次具有上述中间层、上述极薄铜层,且在上述载体的另一面具有粗化处理层。本发明的再一个方面为一种高频电路用覆铜板,其使用了本发明的铜箔。本发明的再又一个方面为一种高频电路用印刷布线板,其使用了本发明的铜箔。本发明的一个实施方案的高频电路用覆铜板,其层叠有上述铜箔、和聚酰亚胺、液晶聚合物或氟树脂。本发明的再又一个方面为一种本发明的高频电路用印刷布线板,其使用了聚酰亚胺、液晶聚合物或氟树脂中的任意一者。本发明的再又一个方面为一种电子设备,其使用了本发明的印刷布线板。本发明的再又一个方面为一种印刷布线板的制造方法,其包括:准备本发明的带载体的铜箔和绝缘基板的工序;对上述带载体的铜箔和绝缘基板进行层叠的工序;和在将上述带载体的铜箔和绝缘基板进行层叠后,经过剥离上述带载体的铜箔的载体的工序而形成覆铜板,然后,利用半加成法、减成法、部分加成法或改良半加成法中的任一方法形成电路的工序。本发明的再又一个方面为一种印刷布线板的制造方法,其包括:在本发明的带载体的铜箔的上述极薄铜层侧表面形成电路的工序;按照包埋上述电路的方式在上述带载体的铜箔的上述极薄铜层侧表面形成树脂层的工序;在上述树脂层上形成电路的工序;在上述树脂层上形成电路后剥离上述载体的工序;以及通过在剥离上述载体后除去上述极薄铜层,由此使形成在上述极薄铜层侧表面且包埋于上述树脂层的电路露出的工序。根据本发明,可以提供即使用于高频电路基板也能良好地抑制传输损耗、且能够良好地抑制形成于铜箔表面的粗化粒子从该表面剥落的现象、即所谓的“落粉”的产生的高频电路用铜箔。附图说明图1为表示在以往的铜箔上进行包括铜-钴-镍合金镀敷的粗化处理时的落粉的情况的概念说明图。图2为本发明的、在铜箔上预先形成一次粒子层、并在该一次粒子层上形成有由铜-钴-镍合金镀敷得到的二次粒子层的、无落粉的铜箔处理层的概念说明图。图3为在以往的铜箔上进行包括铜-钴-镍合金镀敷的粗化处理时的表面的显微镜照片。图4为本发明的、在铜箔上预先形成一次粒子层、并在该一次粒子层上形成由铜-钴-镍合金镀敷得到的二次粒子层的、无落粉的铜箔处理面的层的显微镜照片。图5的A~C为使用了本发明的带载体的铜箔的印刷布线板的制造方法的具体例所涉及的、直至电镀、抗蚀剂除去的工序的布线板截面的示意图。图6的D~F为使用了本发明的带载体的铜箔的印刷布线板的制造方法的具体例所涉及的、从树脂及第2层带载体的铜箔的层叠至激光开孔的工序的布线板截面的示意图。图7的G~I为使用了本发明的带载体的铜箔的印刷布线板的制造方法的具体例所涉及的、从形成通孔填充到剥离第1层的载体的工序的布线板截面的示意图。图8的J~K为使用了本发明的带载体的铜箔的印刷布线板的制造方法的具体例所涉及的、从闪速蚀刻到形成凸点、铜柱的工序的布线板截面的示意图。具体实施方式在本发明中可以使用的铜箔基材的形态并无特别限制,典型而言,本发明中使用的铜箔可以是电解铜箔或压延铜箔中的任意一种。一般而言,电解铜箔通过在钛或不锈钢的圆筒上从硫酸铜镀浴电解析出铜来制造,压延铜箔通过反复进行利用压延辊的塑性加工和热处理来制造。在要求挠性的用途中大多应用压延铜箔。作为铜箔基材的材料,除了能够使用通常被用作印刷布线板的导体图形的韧铜、无氧铜之类的高纯度的铜以外,还能够使用例如混入Sn的铜、混入Ag的铜、添加了Cr、Zr或Mg等的铜合金、添加了Ni及Si等的科森系铜合金之类的铜合金。予以说明,本说明书中单独使用术语“铜箔”时,也包括铜合金箔。予以说明,铜箔基材的板厚无需特别限定,例如为1~1000μm,或为1~500μm,或为1~300μm,或为3~100μm,或为5~70μm,或为6~35μm,或为9~18μm。此外,本发明的另一个方面为一种带载体的铜箔,其是依次具有载体、中间层、极薄铜层的带载体的铜箔,上述极薄铜层为本发明的高频电路用铜箔。即,在本发明的另一方面可以使用依次具有载体、中间层、极薄铜层的带载体的铜箔作为铜箔基材。本发明中使用带载体的铜箔时,在极薄铜层表面设置以下的粗化处理层等表面处理层。予以说明,下面将对带载体的铜箔的另一实施方式进行叙述。通常,对于铜箔的与树脂基材粘接的面、即粗化面,为了提高在层叠后的铜箔的剥离强度,对脱脂后的铜箔的表面实施进行“疙瘩”状的电附着的粗化处理。电解铜箔在制造时间点具有凹凸,利用粗化处理使电解铜箔的凸部增强而使凹凸进一步增大。作为粗化前的前处理,有时进行通常的镀铜等,作为粗化后的精加工(仕上げ)处理,为了防止电附着物的脱落,有时也进行通常的镀铜等。本发明中也包括这样的前处理及精加工处理,并根据需要包含与铜箔粗化关联的公知的处理,统称为“粗化处理”。通过铜-钴-镍合金镀敷来进行该粗化处理(以下的说明中,为了使铜-钴-镍合金镀敷的粗化处理与前工序的差异变得明确,而称作“二次粒子层”。),如上所述,单纯是仅仅在铜箔上形成铜-钴-镍合金镀层,就会如上所述产生落粉等问题。将在铜箔上形成有铜-钴-镍合金镀层的铜箔的表面的显微镜照片示于图3。如该图3所示,能够观察到扩展成树枝状的微细粒子。一般而言,以高电流密度制作该图3所示的扩展成树枝状的微细粒子。在以这样的高电流密度进行处理时,初期电附着的粒子的核生成受到抑制,因此在粒子前端形成新的粒子的核,因此粒子逐渐细长地生长成树枝状。因此,在为了防止该现象而降低电流密度进行电镀时,则尖锐的竖起消失,粒子增加,有形状发圆的粒子生长。即便在这样的状况下,落粉也稍稍被改善,但得不到足够的剥离强度,不足以实现本申请发明的目的。将如图3所示的形成有铜-钴-镍合金镀层时的落粉的情况示于图1的概念说明图中。该落粉的原因在于,如上所述在铜箔上呈树枝状地生长微细的粒子,但是,该树枝状的粒子容易因外力而使树枝的一部分被折断或从根部脱落。该微细的树枝状的粒子成为产生由处理中的“摩擦”所致的剥离、由剥离粉所致的辊的污染、由剥离粉所致的蚀刻残渣的原因。本发明为在铜箔的表面预先形成有铜的一次粒子层后在该一次粒子层上形成了由包含铜、钴及镍的3元系合金形成的二次粒子层的铜箔。将在铜箔上形成有该一次粒子及二次粒子的表面的显微镜照片示于图4(详细情况如后所述)。由此,可以得到如下的铜箔:处理中的“摩擦”导致的剥离、剥离粉对辊的污染、剥离粉导致的蚀刻残渣消失,即可以抑制称为落粉的现象和处理不均,可以改善剥离强度,且提高耐热性。由下述所示的实施例可以明确:使上述一次粒子层的平均粒径为0.25~0.45μm、由包含铜、钴及镍的3元系合金形成的二次粒子层的平均粒径为0.35μm以下是防止落粉的最佳条件。上述一次粒子层的平均粒径的下限优选为0.27μm以上,优选为0.29μm以上,更优选为0.30μm以上,更优选为0.33μm以上。上述一次粒子层的平均粒径的上限优选为0.44μm以下,优选为0.43μm以下,优选为0.40μm以下,优选为0.39μm以下。此外,上述二次粒子层的平均粒径的上限优选为0.34μm以下,优选为0.33μm以下,优选为0.32μm以下,优选为0.31μm以下,优选为0.30μm以下,优选为0.28μm以下,优选为0.27μm以下。此外,二次粒子层的平均粒径的下限无需特别限定,例如为0.001μm以上,或为0.01μm以上,或为0.05μm以上,或为0.09μm以上,或为0.10μm以上,或为0.12μm以上,或为0.15μm以上。上述一次粒子层及二次粒子层由电镀层形成。该二次粒子的特征为在上述一次粒子上生长的1个或多个树枝状的粒子。或为在上述一次粒子上生长的正常镀层。即,本说明书中使用术语“二次粒子层”时,也包括被覆镀敷等的正常镀层。此外,二次粒子层可以具有一层以上利用粗化粒子形成的层,也可以具有一层以上的正常镀层,还可以具有利用粗化粒子形成的层和正常镀层各一层以上。这样形成的一次粒子层及二次粒子层的粘接强度可以达到0.80kg/cm以上,进而粘接强度还可以达到0.90kg/cm以上。在形成有一次粒子层及二次粒子层的铜箔中,更重要的是使粗化处理面的一定区域的基于激光显微镜得到的三维表面积相对于二维表面积之比为2.0以上且小于2.2。予以说明,“基于激光显微镜得到的三维表面积相对于二维表面积之比”中的“粗化处理面”是指最终制品上的表面,其意味着形成有一次粒子层及二次粒子层的一侧的最外表面。此外,在二次粒子层上形成例如耐热层、防锈层、硅烷偶联处理层等表面处理层时,“粗化处理面”是指该表面处理层的最外表面。予以说明,在形成有后述的“树脂层”时,“粗化处理面”是指除去该树脂层后的铜箔的形成有一次粒子层及二次粒子层的一侧的最外表面。关于此种表面积比的限制和调整,使铜箔的粗化处理面由作为各个粗化粒子的集合体的粒子层形成,以与粒子的生长控制相比更宏观的范围对粒子层进行控制,由此具有无起伏、即能够防止稳定的剥离强度的提高和稳定的落粉现象的效果。此外,在即使对各个粗化粒子尺寸进行控制也会导致微细的粗化粒子在高度方向堆积的情况下,会导致发生落粉。因此,重要的是对作为三维的粗化粒子构成的表面积比的限制和调整。在上述表面积比小于2.0时,剥离强度变得不充分。使用激光显微镜对标准压延铜箔的粗化处理前的无粗化的状态下的三维表面粗糙度进行测定,结果为20043μm2,三维表面积相对于二维表面积之比为2.02,因此可以说为了确保剥离强度而理想的是使该比值至少为2.0以上。此外,在该比值超过2.20时,容易产生落粉现象,因此可以说理想的是设定成上述的范围。予以说明,上述表面积比(三维表面积相对于二维表面积之比)的上限优选为2.19以下,优选为2.17以下,优选为2.15以下。此外,上述表面积比(三维表面积相对于二维表面积之比)的下限优选为2.02以上,优选为2.04以上,优选为2.05以上,优选为2.06以上。关于利用激光显微镜的测定法,使用KEYENCECORPORATION制造的激光显微镜VK8500,对粗化处理面的相当于100×100μm的面积、以实际数据计为9924.4μm2的范围的三维表面积进行测定,并依据三维表面积÷二维表面积=表面积比的做法进行设定。在二次粒子层上可以形成有(A)合金层及(B)铬酸盐层中的任意一者或两者,所述(A)合金层包含Ni和选自Fe、Cr、Mo、Zn、Ta、Cu、Al、P、W、Mn、Sn、As及Ti中的一种以上的元素。此外,在二次粒子层上可以依次形成有(A)合金层及(B)铬酸盐层中的任意一者或两者、和硅烷偶联层,所述(A)合金层包含Ni和选自Fe、Cr、Mo、Zn、Ta、Cu、Al、P、W、Mn、Sn、As及Ti中的一种以上的元素。进而,在二次粒子层上可以形成有Ni-Zn合金层及铬酸盐层中的任意一者或两者。进而,在二次粒子层上可以依次形成有Ni-Zn合金层及铬酸盐层中的任意一者或两者、和硅烷偶联层。根据此种构成,能够在维持剥离强度的状态下提高高频传输特性。[传输损耗]在传输损耗小的情况下,以高频进行信号传输时的信号的衰减得到抑制,因此在以高频进行信号的传输的电路中,能够进行稳定的信号传输。因此,在传输损耗的值较小时,适合用于以高频进行信号传输的电路用途,故优选。将表面处理铜箔与市售的液晶聚合物树脂(可乐丽株式会社制造的VecstarCTZ-50μm)贴合后,通过蚀刻以使特性阻抗成为50Ω的方式形成微带(microstrip)线路,使用HP公司制造的网路分析仪HP8720C,对透射系数进行测定,并求得频率20GHz和频率40GHz下的传输损耗,在此种情况下,频率20GHz下的传输损耗优选小于5.0dB/10cm,更优选小于4.1dB/10cm,进一步优选小于3.7dB/10cm。将本发明的表面处理铜箔从粗化处理面侧贴合到树脂基板,由此可以制造层叠体。树脂基板只要是具有能够应用于印刷布线板等的特性的树脂基板,则并不受特别限制,例如在刚性PWB用途中可以使用纸基材酚醛树脂、纸基材环氧树脂、合成纤维布基材环氧树脂、玻璃布-纸复合基材环氧树脂、玻璃布-玻璃无纺布复合基材环氧树脂及玻璃布基材环氧树脂等;在FPC用途中可以使用聚酯膜、聚酰亚胺膜、液晶聚合物(LCP)膜、氟树脂等。予以说明,与使用聚酰亚胺膜的情况相比,使用液晶聚合物(LCP)膜、氟树脂膜的情况更具有使该膜与表面处理铜箔的剥离强度变小的倾向。因此,在使用液晶聚合物(LCP)膜、氟树脂膜的情况下,形成铜电路后,利用覆盖层(coverlay)覆盖铜电路,由此不易使该膜与铜电路剥离,能够防止由剥离强度的降低所致的该膜与铜电路的剥离。予以说明,液晶聚合物(LCP)膜或氟树脂膜的介质损耗角正切较小,因此使用液晶聚合物(LCP)膜或氟树脂膜、和本发明的表面处理铜箔的覆铜板、印刷布线板、印刷电路板,适合于高频电路(以高频进行信号的传输的电路)用途。此外,本发明的表面处理铜箔的表面粗糙度Rz较小,光泽度较高,因此表面平滑,也适合于高频电路用途。关于贴合的方法,在刚性PWB用途的情况下,使树脂浸渍于玻璃布等基材而准备使树脂固化至半固化状态的预浸料。将铜箔从覆盖层的相反侧的面与预浸料重叠,对其进行加热加压,由此可以进行贴合。在FPC的情况下,借助粘接剂将铜箔与聚酰亚胺膜等基材贴合,或者不使用粘接剂而在高温高压下对铜箔进行层叠粘接,或者进行聚酰亚胺前驱体的涂布、干燥、固化等,由此可以制造层叠板。本发明的层叠体能够用于各种印刷布线板(PWB),并没有特别限制,例如从导体图形的层数的观点出发,能够应用于单面PWB、两面PWB、多层PWB(3层以上),从绝缘基板材料的种类的观点出发,能够应用于刚性PWB、挠性PWB(FPC)、刚性-挠性PWB。进而,通过将电子部件类搭载于印刷布线板,从而完成印刷电路板。本发明中的“印刷布线板”也包括如此搭载有电子部件类的印刷布线板、印刷电路板及印刷基板。此外,可以使用该印刷布线板来制作电子设备,也可以使用搭载有该电子部件类的印刷电路板来制作电子设备,还可以使用搭载有该电子部件类的印刷基板来制作电子设备。(铜的一次粒子的镀敷条件)若要列举铜的一次粒子的镀敷条件的一个示例,则如下所述。予以说明,该镀敷条件不过示出优选的示例,形成于铜箔上的铜的一次粒子的平均粒径担负着防止落粉的作用。因此,只要平均粒径落入本发明的范围,则除下述所示以外的镀敷条件也无任何影响,其也包含在本发明中。液体组成:铜10~20g/L、硫酸50~100g/L液温:25~50℃电流密度:1~58A/dm2库仑量:4~81As/dm2(二次粒子的镀敷条件)予以说明,与上述同样,该镀敷条件不过示出优选的示例,二次粒子形成于一次粒子之上,其平均粒径担负着防止落粉的作用。因此,只要平均粒径落入本发明的范围,则除下述所示以外的镀敷条件也无任何影响,其也包含在本发明中。液体组成:铜10~20g/L、镍5~15g/L、钴5~15g/LpH:2~3液温:30~50℃电流密度:24~50A/dm2库仑量:34~48As/dm2(形成耐热层1的镀敷条件)(Co-Ni镀敷:钴镍合金镀敷)本发明可以在上述二次粒子层上进一步形成耐热层。其镀敷条件如下述所示。液体组成:镍5~20g/L、钴1~8g/LpH:2~3液温:40~60℃电流密度:5~20A/dm2库仑量:10~20As/dm2(形成耐热层2的镀敷条件)(Ni-Zn镀敷:镍锌合金镀敷)本发明可以在上述二次粒子层上进一步形成以下的耐热层。其镀敷条件如下述所示。液体组成:镍2~30g/L、锌2~30g/LpH:3~4液温:30~50℃电流密度:1~2A/dm2库仑量:1~2As/dm2(形成耐热层3的镀敷条件)(Ni‐Cu镀敷:镍铜合金镀敷)本发明可以在上述二次粒子层上进一步形成以下的耐热层。其镀敷条件如下述所示。液体组成:镍2~30g/L、铜2~30g/LpH:3~4液温:30~50℃电流密度:1~2A/dm2库仑量:1~2As/dm2(形成耐热层4的镀敷条件)(Ni-Mo镀敷:镍钼合金镀敷)本发明可以在上述二次粒子层上进一步形成以下的耐热层。其镀敷条件如下述所示。液体组成:硫酸Ni六水合物:45~55g/dm3、钼酸钠二水合物:50~70g/dm3、柠檬酸钠:80~100g/dm3液温:20~40℃电流密度:1~4A/dm2库仑量:1~2As/dm2(形成耐热层5的镀敷条件)(Ni-Sn镀敷:镍锡合金镀敷)本发明可以在上述二次粒子层上进一步形成以下的耐热层。其镀敷条件如下述所示。液体组成:镍2~30g/L、锡2~30g/LpH:1.5~4.5液温:30~50℃电流密度:1~2A/dm2库仑量:1~2As/dm2(形成耐热层6的镀敷条件)(Ni-P镀敷:镍磷合金镀敷)本发明可以在上述二次粒子层上进一步形成以下的耐热层。其镀敷条件如下述所示。液体组成:镍30~70g/L、磷0.2~1.2g/LpH:1.5~2.5液温:30~40℃电流密度:1~2A/dm2库仑量:1~2As/dm2(形成耐热层7的镀敷条件)(Ni-W镀敷:镍钨合金镀敷)本发明可以在上述二次粒子层上进一步形成以下的耐热层。其镀敷条件如下述所示。液体组成:镍2~30g/L、W0.01~5g/LpH:3~4液温:30~50℃电流密度:1~2A/dm2库仑量:1~2As/dm2(形成耐热层8的镀敷条件)(Ni-Cr镀敷:镍铬合金镀敷)本发明可以在上述二次粒子层上进一步形成以下的耐热层。其镀敷条件如下述所示。使用Ni:65~85mass%、Cr:15~35mass%的组成的溅射靶来形成镍铬合金镀层。靶:Ni:65~85mass%、Cr:15~35mass%装置:ULVACInc.制造的溅射装置输出:DC50W氩气压力:0.2Pa(形成防锈层的镀敷条件)本发明可以进一步形成以下的防锈层。其镀敷条件如下述所示。下述示出浸渍铬酸盐处理的条件,也可以是电解铬酸盐处理。液体组成:重铬酸钾1~10g/L、锌0~5g/LpH:3~4液温:50~60℃电流密度:0~2A/dm2(0A/dm2为浸渍铬酸盐处理的情况。)库仑量:0~2As/dm2(0As/dm2为浸渍铬酸盐处理的情况。)(耐气候性层(硅烷偶联层)的种类)作为一个示例,可列举二氨基硅烷水溶液的涂布。予以说明,在通过溅射等干式镀敷来设置耐热层等金属层、镀层的情况下以及在利用湿式镀敷来设置耐热层等金属层、镀层的情况下,在耐热层等金属层、镀层为正常镀层(平滑镀层、即在小于临界电流密度的电流密度下进行的镀敷)时,该金属层、镀层不会对铜箔的表面的形状带来影响。临界电流密度根据金属浓度、pH、给液速度、极间距离、镀敷液温度而发生变化,本发明中将正常镀敷(被镀敷的金属以层状析出的状态)与粗化镀敷(燃烧镀敷、镀敷的金属以结晶状(球状、针状、树挂状等)析出的状态,具有凹凸。)的边界的电流密度定义为临界电流密度,在赫尔槽试验(Hullcelltest)中将成为正常镀敷的临界(即将成为燃烧镀敷之前)的电流密度(目视判断)设定为临界电流密度。具体而言,将金属浓度、pH、镀敷液温度设定成镀层的制造条件,进行赫尔槽试验。而且,对该镀敷液体组成、镀敷液温度下的金属层形成状态(被镀敷的金属是以层状析出还是形成为结晶状)进行调查。而且,基于山本镀金试验器株式会社制造的的电流密度一览表,从试件(testpiece)的正常镀敷与粗化镀敷的边界所存在的部位的试件的位置,求出在该边界的位置处的电流密度。而且,将在该边界的位置处的电流密度规定为临界电流密度。由此可知在该镀敷液体组成、镀敷液温度下的临界电流密度。一般而言,在极间距离短时,存在使临界电流密度变高的倾向。赫尔槽试验的方法例如记载于《镀敷实务读本(メッキ実務読本)》丸山清著日刊工业新闻社1983年6月30日的157页~160页。予以说明,为了在小于临界电流密度下进行镀敷处理,而优选将镀敷处理时的电流密度设定为20A/dm2以下,优选设定为10A/dm2以下,优选设定为8A/dm2以下。此外,铬酸盐层、硅烷偶联层由于其厚度极薄,因此不会对铜箔的表面形状带来影响。作为上述二次粒子的铜-钴-镍合金镀敷,可以利用电镀形成附着量为10~30mg/dm2铜-100~3000μg/dm2钴-50~500μg/dm2镍的3元系合金层。在Co附着量小于100μg/dm2时,耐热性变差,并且蚀刻性也变差。在Co附着量超过3000μg/dm2时,在不得不考虑磁性的影响的情况下是不优选的,可能要考虑到会产生蚀刻污垢,并且耐酸性及耐化学试剂性的恶化。在Ni附着量小于50μg/dm2时,耐热性变差。另一方面,在Ni附着量超过500μg/dm2时,蚀刻性降低。即,出现蚀刻残余,并且并非是无法蚀刻的水平,但使精细图形化难以进行。优选的Co附着量为500~2000μg/dm2,而且优选的镍附着量为50~300μg/dm2。由以上情况可以说铜-钴-镍合金镀敷的附着量理想的是10~30mg/dm2铜-100~3000μg/dm2钴-50~500μg/dm2镍。该3元系合金层的各附着量不过是理想的条件,并不用来否定超过该量的范围。在此,蚀刻污垢是指在利用氯化铜进行蚀刻时Co不溶解而残留的情况,而且蚀刻残余是指在利用氯化铵进行碱性蚀刻时Ni不溶解而残留的情况。一般而言,在形成电路的情况下,使用如下述的实施例中所说明的那样的碱性蚀刻液及氯化铜系蚀刻液来进行。该蚀刻液及蚀刻条件是通用性的蚀刻液及蚀刻条件,并不受该条件的限定,应该被理解为可以进行任意的选择。本发明可以如上述那样在形成二次粒子后(粗化处理后)在粗化面上形成钴-镍合金镀层。该钴-镍合金镀层理想的是使钴的附着量为200~3000μg/dm2且钴的比率为60~66质量%。该处理在广义上被视为一种防锈处理。该钴-镍合金镀层需要进行至使铜箔与基板的粘接强度不发生实质性降低的程度。在钴附着量小于200μg/dm2时,耐热剥离强度降低,耐氧化性及耐化学试剂性变差,并且会导致处理表面发红,故不优选。此外,在钴附着量超过3000μg/dm2时,在不得不考虑磁性的影响的情况下是不优选的,可能要考虑到会产生蚀刻污垢、并且耐酸性及耐化学试剂性的恶化。优选的钴附着量为400~2500μg/dm2。此外,在钴附着量多时,有时会导致发生软蚀刻的渗入。由此可以说理想的是使钴的比率为60~66质量%。如后所述,发生软蚀刻的渗入的较大直接原因在于,是由锌-镍合金镀层构成的耐热防锈层,而钴也成为软蚀刻时发生渗入的原因,因此按上述方式进行调整是更为理想的条件。另一方面,在镍附着量较少的情况下,耐热剥离强度降低,耐氧化性及耐化学试剂性降低。此外,在镍附着量过多的情况下,碱性蚀刻性变差,因此理想的是由镍附着量与上述钴含量的平衡来确定。本发明可以在钴-镍合金镀层上进一步形成锌-镍合金镀层。将锌-镍合金镀层的总量设定为150~500μg/dm2,并且将镍的比率设定为16~40质量%。这样具有作为耐热防锈层的作用。该条件也不过是优选的条件,可以使用其他公知的锌-镍合金镀敷。该锌-镍合金镀敷大概可以被理解为本发明的优选附加条件。在电路的制造工序中进行的处理变成更高的温度,并且有时会在成为制品后的机器使用中产生热。例如在利用热压接使铜箔与树脂接合的所谓二层材料中,在接合时会受到300℃以上的热。在此种状况中,需要防止铜箔与树脂基材之间的接合力的降低,该锌-镍合金镀敷是有效的。此外,在以往的技术中,在具有利用热压接使铜箔与树脂接合的二层材料中的锌-镍合金镀层的微小电路中,在软蚀刻时会在电路的边缘部产生由渗入所致的变色。镍具有抑制在软蚀刻时使用的蚀刻剂(H2SO4:10wt%、H2O2:2wt%的蚀刻水溶液)的渗入的效果。如上所述,在将上述锌-镍合金镀层的总量设为150~500μg/dm2、该合金层中的镍比率的下限值设为16质量%、上限值设为40质量%、且镍的含量设为50μg/dm2以上时,具有作为耐热防锈层的作用,并且具有抑制在软蚀刻时使用的蚀刻剂的渗入、防止由腐蚀带来的电路接合强度的软弱化的效果。予以说明,在锌-镍合金镀层的总量小于150μg/dm2时,耐热防锈能力降低而难以担负作为耐热防锈层的作用,在锌-镍合金镀层的总量超过500μg/dm2时,存在耐盐酸性变差的倾向。此外,在合金层中的镍比率的下限值小于16质量%时,软蚀刻时的渗入量超过9μm,故不优选。镍比率的上限值40质量%是能够形成锌-镍合金镀层的技术上的临界值。如上所述,本发明可以在作为二次粒子层的铜-钴-镍合金镀层上根据需要依次形成钴-镍合金镀层以及锌-镍合金镀层。也可以对这些层中合计量的钴附着量及镍附着量进行调节。理想的是使钴的合计附着量为300~4000μg/dm2、且镍的合计附着量为100~1500μg/dm2。在钴的合计附着量小于300μg/dm2时,耐热性及耐化学试剂性降低,在钴的合计附着量超过4000μg/dm2时,有时会产生蚀刻污垢,并且有时会使传输损耗变大。此外,在镍的合计附着量小于100μg/dm2时,有时会使耐热性及耐化学试剂性降低。在镍的合计附着量超过1500μg/dm2时,有时会产生蚀刻残余,并且有时会使传输损耗变大。钴的合计附着量优选为300~3500μg/dm2,更优选为300~3000μg/dm2,更优选为300~2500μg/dm2,更优选为300~2000μg/dm2;镍的合计附着量优选为100~1000μg/dm2,更优选为100~900μg/dm2。若不满足上述的条件,则也无需特别限制成本段落记载的条件。之后,根据需要实施防锈处理。本发明中优选的防锈处理为铬氧化物单一物质的皮膜处理或铬氧化物与锌/锌氧化物的混合物皮膜处理。铬氧化物与锌/锌氧化物的混合物皮膜处理为使用含有锌盐或氧化锌、和铬酸盐的镀浴,利用电镀覆盖由锌或氧化锌、和铬氧化物形成的锌-铬基混合物的防锈层的处理。作为镀浴,可以使用具代表性的K2Cr2O7、Na2Cr2O7等重铬酸盐、CrO3等中的至少一种、水溶性锌盐例如ZnO、ZnSO4·7H2O等中的至少一种、和碱金属类氢氧化物的混合水溶液。具代表性的镀浴组成和电解条件例如下所述。这样得到的铜箔具有优异的耐热性剥离强度、耐氧化性及耐盐酸性。此外,可以以CuCl2蚀刻液来蚀刻150μm间距电路宽度以下的电路,而且还能够进行碱性蚀刻。此外,可以抑制在软蚀刻时对电路边缘部的渗入。软蚀刻液可以使用H2SO4:10wt%、H2O2:2wt%的水溶液。处理时间和温度可以进行任意的调节。作为碱性蚀刻液,已知例如NH4OH:6摩尔/升、NH4Cl:5摩尔/升、CuCl2:2摩尔/升(温度50℃)等液体。上述的全部工序中得到的铜箔具有黑色~灰色。从对位精度及热吸收率高的方面出发,黑色~灰色是有意义的。例如包括刚性基板及挠性基板,电路基板已经在自动化处理中搭载IC、电阻、电容器等部件,但是此时一边利用传感器读取电路一边进行芯片组装。此时,会通过Kapton等膜而进行铜箔处理面上的对位。此外,形成通孔时的定位也同样。处理面越接近黑色,光的吸收越好,因此定位的精度越高。进而,在制作基板时,大多对铜箔和膜边加热边进行熟化(curing)而使其粘接。此时,在通过使用远红外线、红外线等长波进行加热的情况下,处理面的色调越黑,加热效率越好。最后,以改善铜箔与树脂基板的粘接力为主要目的而根据需要对防锈层上的至少粗化面实施涂布硅烷偶联剂的硅烷处理。作为该硅烷处理中使用的硅烷偶联剂,可列举烯烃系硅烷、环氧系硅烷、丙烯酸系硅烷、氨基系硅烷、巯基系硅烷,可以从它们之中适当选择使用。予以说明,在使用液晶聚合物作为树脂时,优选使用氨基系硅烷(具有氨基的硅烷)作为硅烷偶联剂。此外,更优选使用二氨基硅烷作为硅烷偶联剂。涂布方法可以是硅烷偶联剂溶液的利用喷雾器的喷涂、利用涂布机的涂布、浸渍、流挂等中的任一种。例如日本特公昭60-15654号记载了如下内容:对铜箔的粗面侧实施铬酸盐处理后,进行硅烷偶联剂处理,由此改善铜箔与树脂基板的粘接力。详细情况请参照该专利文献。之后,还可在需要时以改善铜箔的延展性为目的来实施退火处理。〔带载体的铜箔〕本发明的另一实施方案的带载体的铜箔,在载体的一面或两面依次具有中间层、极薄铜层。而且,上述极薄铜层是上述的本发明的一个实施方案的高频电路用铜箔。<载体>典型而言,本发明中可以使用的载体为金属箔或树脂膜,例如可以以铜箔、铜合金箔、镍箔、镍合金箔、铁箔、铁合金箔、不锈钢箔、铝箔、铝合金箔、绝缘树脂膜(例如聚酰亚胺膜、液晶聚合物(LCP)膜、聚对苯二甲酸乙二醇酯(PET)膜、聚酰胺膜、聚酯膜、氟树脂膜等)的形态来提供。作为在本发明中可以使用的载体,优选使用铜箔。这是由于:铜箔的电导率高,因此容易形成之后的中间层、极薄铜层。典型而言,载体可以以压延铜箔或电解铜箔的形态来提供。一般而言,电解铜箔通过从硫酸铜镀浴中向钛、不锈钢的圆筒上电解析出铜来制造,压延铜箔通过重复进行利用压延辊的塑性加工和热处理来制造。作为铜箔的材料,除了韧铜、无氧铜之类的高纯度的铜以外,还可以使用例如混入Sn的铜、混入Ag的铜、添加了Cr、Zr或Mg等的铜合金、添加了Ni及Si等的科森系铜合金之类的铜合金。本发明中可以使用的载体的厚度并无特别限制,但只要在发挥作为载体的作用的基础上适宜调节成适当的厚度即可,例如可以为5μm以上。其中,在载体的厚度过厚时,生产成本变高,因此一般优选为35μm以下。因而,典型而言,载体的厚度为12~70μm,更典型而言,载体的厚度为18~35μm。予以说明,可以在载体的与设置极薄铜层的一侧的表面相反侧的表面设置粗化处理层。可以采用公知的方法设置该粗化处理层,也可以利用上述的粗化处理进行设置。在载体的与设置极薄铜层的一侧的表面相反侧的表面设置粗化处理层的情况下,将载体从具有该粗化处理层的表面侧层叠到树脂基板等支承体时,具有不易使载体与树脂基板剥离的优点。<中间层>在载体上设置中间层。也可以在载体与中间层之间设置其他层。本发明中使用的中间层,只要是下述构成就没有特别限制:在带载体的铜箔向绝缘基层叠的工序之前不易从载体剥离极薄铜层,另一方面,在向绝缘基板层叠的工序之后能够从载体剥离极薄铜层的构成。例如本发明的带载体的铜箔的中间层,可以含有选自Cr、Ni、Co、Fe、Mo、Ti、W、P、Cu、Al、Zn、它们的合金、它们的水合物、它们的氧化物、有机物中的一种或二种以上。此外,中间层可以为多层。此外,例如中间层可以按照如下方式构成:从载体侧形成从由Cr、Ni、Co、Fe、Mo、Ti、W、P、Cu、Al、Zn构成的元素组中选择的一种元素形成的单一金属层或者含有从由Cr、Ni、Co、Fe、Mo、Ti、W、P、Cu、Al、Zn构成的元素组中选择的一种或二种以上的元素的合金层,再在其上形成含有从由Cr、Ni、Co、Fe、Mo、Ti、W、P、Cu、Al、Zn构成的元素组中选择的一种或二种以上的元素的水合物、氧化物或有机物的层、或者从由Cr、Ni、Co、Fe、Mo、Ti、W、P、Cu、Al、Zn构成的元素组中选择的一种元素形成的单一金属层、或者含有从由Cr、Ni、Co、Fe、Mo、Ti、W、P、Cu、Al、Zn构成的元素组中选择的一种或二种以上的元素的合金层。在将中间层仅设置于单面的情况下,优选在载体的相反面设置Ni镀层等防锈层。予以说明,在利用铬酸盐处理、锌铬酸盐处理、镀敷处理设置中间层的情况下,需要考虑铬、锌等所附着的金属的一部分形成水合物、氧化物的情况。此外,例如中间层可以在载体上依次层叠铬和镍或镍-磷合金或镍-钴合金而构成。镍与铜的粘接力高于铬与铜的粘接力,因此在剥离极薄铜层时,使极薄铜层与铬的界面发生剥离。此外,对中间层的镍期待其防止铜成分从载体向极薄铜层扩散的屏障效果。中间层中的镍的附着量优选为100μg/dm2以上且40000μg/dm2以下,更优选为100μg/dm2以上且4000μg/dm2以下,进一步优选为100μg/dm2以上且2500μg/dm2以下,更优选为100μg/dm2以上且小于1000μg/dm2,中间层中的铬的附着量优选为5μg/dm2以上且100μg/dm2以下。<极薄铜层>在中间层上设置极薄铜层。可以在中间层与极薄铜层之间设置其他层。极薄铜层可以通过采用了硫酸铜、焦磷酸铜、氨基磺酸铜、氰化铜等的电解浴的电镀来形成,从能够在一般的电解铜箔中使用且能够在高电流密度下形成铜箔的方面出发,优选硫酸铜浴。极薄铜层的厚度并无特别限制,一般比载体薄,例如为12μm以下。典型而言,为0.5~12μm,更典型而言,为1~5μm,进一步典型而言,为1.5~5μm,特别典型而言,为2~5μm。予以说明,可以在载体的两面设置极薄铜层。由此,可以制造具备载体、层叠于载体上的中间层和层叠于中间层上的极薄铜层的带载体的铜箔。带载体的铜箔自身的使用方法对本领域技术人员而言是公知的,例如将极薄铜层的表面贴合于纸基材酚醛树脂、纸基材环氧树脂、合成纤维布基材环氧树脂、玻璃布-纸复合基材环氧树脂、玻璃布-玻璃无纺布复合基材环氧树脂及玻璃布基材环氧树脂、聚酯膜、聚酰亚胺膜等绝缘基板,在热压接后剥离载体,制成覆铜板,并按照目标导体图形对粘接于绝缘基板的极薄铜层进行蚀刻,最终可以制造印刷布线板。此外,具备载体以及在载体上层叠中间层并在中间层上层叠的极薄铜层的带载体的铜箔,可以预先在上述极薄铜层上具有粗化处理层,在上述粗化处理层上具备一层以上的从耐热层、防锈层、铬酸盐(处理)层及硅烷偶联(处理)层中选择的层。〔树脂层〕在本发明的高频电路用铜箔(也包括高频电路用铜箔为带载体的铜箔的极薄铜层的情况)的二次粒子层的表面,可以形成树脂层。此外,树脂层可以形成在形成于高频电路用铜箔的二次粒子层上的、包含Ni和选自Fe、Cr、Mo、Zn、Ta、Cu、Al、P、W、Mn、Sn、As及Ti中的一种以上元素的合金层的表面,也可以形成在铬酸盐层的表面,也可以形成在硅烷偶联层的表面,还可以形成在Ni-Zn合金层的表面。此外,树脂层更优选形成在高频电路用铜箔的最外表面。此外,上述带载体的铜箔可以在上述粗化处理层上或者上述耐热层、防锈层、铬酸盐(处理)层或硅烷偶联(处理)层上具备树脂层。上述树脂层可以为绝缘树脂层。上述树脂层可以为粘接剂,也可以为粘接用的半固化状态(B-stage状态:B阶状态)的绝缘树脂层。半固化状态(B阶状态)包括:即使用手指触碰其表面也不会有粘着感,能够将该绝缘树脂层加以叠合后进行保管,进而在受到加热处理时,会引发固化反应的状态。此外,上述树脂层可以含有热固化性树脂,也可以为热塑性树脂。此外,上述树脂层可以含有热塑性树脂。其种类并无特别限定,例如可列举包括环氧树脂、聚酰亚胺树脂、多官能性氰酸酯化合物、马来酰亚胺化合物、聚乙烯醇缩醛树脂、聚氨酯树脂等的树脂作为优选的示例。上述树脂层可以含有公知的树脂、树脂固化剂、化合物、固化促进剂、电介质(可以使用包含无机化合物和/或有机化合物的电介质、包含金属氧化物的电介质等之类的电介质)、反应催化剂、交联剂、聚合物、预浸料、骨架材料等。此外,上述树脂层可以使用例如国际公开号WO2008/004399、国际公开号WO2008/053878、国际公开号WO2009/084533、日本特开平11-5828号、日本特开平11-140281号、日本专利第3184485号、国际公开号WO97/02728、日本专利第3676375号、日本特开2000-43188号、日本专利第3612594号、日本特开2002-179772号、日本特开2002-359444号、日本特开2003-304068号、日本专利第3992225号、日本特开2003-249739号、日本专利第4136509号、日本特开2004-82687号、日本专利第4025177号、日本特开2004-349654号、日本专利第4286060号、日本特开2005-262506号、日本专利第4570070号、日本特开2005-53218号、日本专利第3949676号、日本专利第4178415号、国际公开号WO2004/005588、日本特开2006-257153号、日本特开2007-326923号、日本特开2008-111169号、日本专利第5024930号、国际公开号WO2006/028207、日本专利第4828427号、日本特开2009-67029号、国际公开号WO2006/134868、日本专利第5046927号、日本特开2009-173017号、国际公开号WO2007/105635、日本专利第5180815号、国际公开号WO2008/114858、国际公开号WO2009/008471、日本特开2011-14727号、国际公开号WO2009/001850、国际公开号WO2009/145179、国际公开号WO2011/068157、日本特开2013-19056号中记载的物质(树脂、树脂固化剂、化合物、固化促进剂、电介质、反应催化剂、交联剂、聚合物、预浸料、骨架材料等)和/或树脂层的形成方法、形成装置来形成。将这些树脂溶解于例如甲乙酮(MEK)、甲苯等溶剂而制成树脂液,再将其利用例如辊涂法等涂布到上述铜箔上或极薄铜层上、或者上述耐热层、防锈层或上述铬酸盐皮膜层、或者上述硅烷偶联层剂上,接着,根据需要进行加热干燥,除去溶剂,形成B阶状态。干燥可以使用例如热风干燥炉,干燥温度为100~250℃、优选为130~200℃即可。具备上述树脂层的高频电路用铜箔(附有树脂的高频电路用铜箔)可以以如下形态使用:将其树脂层与基材重叠后对整体进行热压接,使该树脂层热固化,接着对铜箔形成规定的布线图形。此外,具备上述树脂层的带载体的铜箔(附有树脂的带载体的铜箔)可以以如下形态使用:将其树脂层与基材重叠后对整体进行热压接,使该树脂层热固化,接着,剥离载体,露出极薄铜层(当然露出的是该极薄铜层的中间层侧的表面),在其上形成规定的布线图形。在使用该附有树脂的高频电路用铜箔或附有树脂的带载体的铜箔时,可以减少制造多层印刷布线基板时的预浸料材料的使用件数。而且,如果使树脂层的厚度为能够确保层间绝缘的厚度,则即使完全不使用预浸料材,也能制造覆铜板。而且此时,通过将绝缘树脂底涂于基材的表面,也可以进一步改善表面的平滑性。予以说明,在不使用预浸料材料的情况下,可以节约预浸料材料的材料成本,并且也使层叠工序变得简化,因此在经济上是有利的,而且以预浸料料的厚度部分制造的多层印刷布线基板的厚度变薄,具有可以制造出1层的厚度为100μm以下的极薄的多层印刷布线基板的优点。该树脂层的厚度优选为0.1~80μm。在树脂层的厚度薄于0.1μm时,粘接力降低,在不夹杂预浸料材料的情况下将该附有树脂的带载体的铜箔层叠于具备内层材料的基材时,有时难以确保内层材料与电路之间的层间绝缘。另一方面,在树脂层的厚度比80μm厚时,难以利用1次的涂布工序形成目标厚度的树脂层,需要花费过多的材料费和功夫,因此在经济上是不利的。进而,所形成的树脂层的挠性变差,因此有时在处理时容易产生裂纹等、并且在与内层材料热压接时引起过度的树脂流动而难以顺利地层叠。予以说明,作为附有树脂的带载体的铜箔的另一制品形态,在上述极薄铜层上、或者上述耐热层、防锈层、或者上述铬酸盐层、或者上述硅烷偶联层上覆盖树脂层,形成半固化状态后,再剥离载体,能够以不存在载体的带树脂的铜箔(极薄铜层)的形态制造该铜箔。、在此,以下示出若干使用了本发明的带载体的铜箔的印刷布线板的制造工序的示例。本发明的印刷布线板的制造方法的一个实施方案包括:准备本发明的带载体的铜箔和绝缘基板的工序;将上述带载体的铜箔和绝缘基板进行层叠的工序;和在将上述带载体的铜箔和绝缘基板按照极薄铜层侧与绝缘基板对置的方式进行层叠后,经过剥离上述带载体的铜箔的载体的工序而形成覆铜板,然后,利用半加成法、改良半加成法、部分加成法及减成法中的任一方法形成电路的工序。绝缘基板也能够进入内层电路。本发明中,半加成法是指:包括在绝缘基板或铜箔种子层(seedlayer)上进行较薄的非电解镀敷,形成镀敷抗蚀剂的图形后,进行电镀、镀敷抗蚀剂的除去及蚀刻,由此形成导体图形的步骤的方法。本发明中,改良半加成法是指:包括在绝缘层上层叠金属箔,利用镀敷抗蚀剂保护非电路形成部,并利用电镀进行电路形成部的铜涂厚后,除去抗蚀剂,利用(闪速)蚀刻将除上述电路形成部以外的金属箔除去,由此在绝缘层上形成电路的步骤的方法。本发明中,部分加成法是指利用包括下述步骤的方法来制造印刷配线板的方法,所述步骤是对设置导体层而成的基板、根据需要穿设通孔、导通孔用的孔而成的基板,赋予催化剂核,进行蚀刻,形成导体电路,并根据需要设置焊接抗蚀剂(solderresist)或者镀敷抗蚀剂(platingresist)后,在上述导体电路上,通过非电解镀敷处理对通孔、导通孔等增厚。本发明中,减成法是指:包括利用蚀刻等选择性地除去覆铜板上的铜箔的不需要的部分而形成导体图形的步骤的方法。予以说明,本发明中,作为半加成法、改良半加成法、部分加成法及减成法,可以使用公知的方法。此外,在本发明中,上述的半加成法、改良半加成法、部分加成法及减成法,也可以在绝缘基板等上设置通孔或/和盲孔。在此,使用附图对使用了本发明的带载体的铜箔的印刷布线板的制造方法的具体例进行详细的说明。首先,如图5-A所示,准备表面形成有粗化处理层的具有极薄铜层的带载体的铜箔(第1层)。接着,如图5-B所示,在极薄铜层的粗化处理层上涂布抗蚀剂,进行曝光、显影,将抗蚀剂蚀刻成规定的形状。接着,如图5-C所示,形成电路用的镀层后,除去抗蚀剂,由此形成规定形状的电路镀层。接着,如图6-D所示,以覆盖电路镀层的方式(包埋电路镀层的方式)在极薄铜层上设置填埋树脂而层叠树脂层,接着,从极薄铜层侧粘接其他带载体的铜箔(第2层)。接着,如图6-E所示,从第2层的带载体的铜箔剥离载体。接着,如图6-F所示,在树脂层的规定位置进行激光开孔,露出电路镀层,形成盲孔。接着,如图7-G所示,在盲孔填埋铜,形成通孔填充物(viafill)。接着,如图7-H所示,在通孔填充物上按照上述图5-B及图5-C所示形成电路镀层。接着,如图7-I所示,从第1层的带载体的铜箔剥离载体。接着,如图8-J所示,利用闪速蚀刻除去两表面的极薄铜层,露出树脂层内的电路镀层的表面。接着,如图8-K所示,在树脂层内的电路镀层上形成凸点,在该焊料上形成铜柱。由此制作使用了本发明的带载体的铜箔的印刷布线板。上述其他的带载体的铜箔(第2层)可以使用本发明的带载体的铜箔,也可以使用以往的带载体的铜箔,还可以使用通常的铜箔。此外,可以在图7-H所示的第2层的电路上进一步形成1层或多层电路,也可以利用半加成法、减成法、部分加成法或改良半加成法中的任一方法形成这些电路。根据如上所述的印刷布线板的制造方法,由于采用电路镀层被树脂层填埋的构成,因此例如在如图8-J所示那样利用闪速蚀刻除去极薄铜层时,电路镀层受到树脂层的保护,其形状得以保持,由此容易形成微细电路。此外,由于电路镀层受到树脂层的保护,因此耐迁移性提高,电路布线的导通得到良好的抑制。因此,容易形成微细电路。此外,在如图8-J及图8-K所示那样利用闪速蚀刻除去极薄铜层时,电路镀层的露出面成为从树脂层凹下的形状,因此在该电路镀层上容易形成凸点,并其在该凸点上容易形成铜柱,使制造效率提高。予以说明,填埋树脂(resin)可以使用公知的树脂、预浸料。例如可以使用作为浸渗有BT(双马来酰亚胺三嗪)树脂、BT树脂的玻璃布的预浸料、AjinomotoFine-TechnoCo.,Inc.制造的ABF膜或ABF。此外,上述填埋树脂(resin)可以使用本说明书中记载的树脂层和/或树脂和/或预浸料。此外,上述第一层中使用的带载体的铜箔,可以在该带载体的铜箔的表面具有基板或树脂层。通过具有该基板或树脂层,在第一层中使用的带载体的铜箔得到支承,不易带入褶皱,因此具有使生产率提高的优点。予以说明,上述基板或树脂层只要具有支承上述第一层中使用的带载体的铜箔的效果,则可以使用所有的基板或树脂层。例如作为上述基板或树脂层,可以使用本申请说明书中记载的载体、预浸料、树脂层、或公知的载体、预浸料、树脂层、金属板、金属箔、无机化合物的板、无机化合物的箔、有机化合物的板、有机化合物的箔。实施例以下,基于实施例及比较例进行说明。予以说明,本实施例不过是一个示例,本发明不仅仅限制为该示例。即,包含本发明中所含的其他方案或变形。予以说明,以下的实施例1~8、13~17及比较例1~5的原箔使用标准压延铜箔TPC(JISH3100C1100中规定的韧铜、JX日矿日石金属制造)18μm。此外,实施例9~12的原箔使用按照以下的方法制造出的带载体的铜箔。实施例9~11中,准备厚度18μm的电解铜箔(JX日矿日石金属制造JTC箔)作为载体,实施例12中,准备上述的厚度18μm的标准压延铜箔TPC作为载体。而且,以下述条件在载体的表面形成中间层,并在中间层的表面形成极薄铜层。予以说明,在载体为电解铜箔时,在光泽面(S面)形成有中间层。·实施例9<中间层>(1)Ni层(Ni镀层)在以下的条件下利用辊到辊型的连续镀敷生产线对载体进行电镀,由此形成了附着量为1000μg/dm2的Ni层。具体的镀敷条件如以下所述。硫酸镍:270~280g/L氯化镍:35~45g/L醋酸镍:10~20g/L硼酸:30~40g/L光泽剂:糖精、丁炔二醇等十二烷基硫酸钠:55~75ppmpH:4~6浴温:55~65℃电流密度:10A/dm2(2)Cr层(电解铬酸盐处理)接着,对由(1)形成的Ni层表面进行水洗及酸洗后,接着,在辊到辊型的连续镀敷生产线上以以下的条件在Ni层上进行电解铬酸盐处理,由此附着附着量为11μg/dm2的Cr层。重铬酸钾1~10g/L、锌0g/LpH:7~10液温:40~60℃电流密度:2A/dm2<极薄铜层>接着,将由(2)形成的Cr层表面进行水洗及酸洗后,接着,在辊到辊型的连续镀敷生产线上以以下的条件在Cr层上进行电镀,由此形成厚度1.5μm的极薄铜层,制造出带载体的铜箔。铜浓度:90~110g/L硫酸浓度:90~110g/L氯化物离子浓度:50~90ppm流平剂1(双(3-磺丙基)二硫化物):10~30ppm流平剂2(胺化合物):10~30ppm予以说明,作为流平剂2,使用了下述的胺化合物。【化1】(上述化学式中,R1及R2为选自羟基烷基、醚基、芳基、芳香族取代烷基、不饱和烃基、烷基中的基团。)电解液温度:50~80℃电流密度:100A/dm2电解液线速:1.5~5m/sec·实施例10<中间层>(1)Ni-Mo层(镍钼合金镀层)在以下的条件下利用辊到辊型的连续镀敷生产线对载体进行电镀,由此形成了附着量为3000μg/dm2的Ni-Mo层。具体的镀敷条件如以下所述。(液体组成)硫酸Ni六水合物:50g/dm3、钼酸钠二水合物:60g/dm3、柠檬酸钠:90g/dm3(液温)30℃(电流密度)1~4A/dm2(通电时间)3~25秒<极薄铜层>在由(1)形成的Ni-Mo层上形成了极薄铜层。将极薄铜层的厚度设定为2μm,除此以外,在与实施例9同样的条件下形成了极薄铜层。·实施例11<中间层>(1)Ni层(Ni镀层)在与实施例9相同的条件下形成了Ni层。(2)有机物层(有机物层形成处理)接着,对由(1)形成的Ni层表面进行水洗及酸洗后,接着,在下述的条件下对Ni层表面以20~120秒的时间喷淋和喷雾包含浓度1~30g/L的羧基苯并三唑(CBTA)且液温40℃、pH5的水溶液,由此形成了有机物层。<极薄铜层>在由(2)形成的有机物层上形成了极薄铜层。将极薄铜层的厚度设定为3μm,除此以外,在与实施例9同样的条件下形成了极薄铜层。·实施例12<中间层>(1)Co-Mo层(钴钼合金镀层)在以下的条件下利用辊到辊型的连续镀敷生产线对载体进行电镀,由此形成了附着量为4000μg/dm2的Co-Mo层。具体的镀敷条件如以下所述。(液体组成)硫酸Co:50g/dm3、钼酸钠二水合物:60g/dm3、柠檬酸钠:90g/dm3(液温)30℃(电流密度)1~4A/dm2(通电时间)3~25秒<极薄铜层>在由(1)形成的Co-Mo层上形成了极薄铜层。将极薄铜层的厚度设定为5μm,除此以外,在与实施例9同样的条件下形成了极薄铜层。(实施例1~17)在压延铜箔(实施例1~8、13~17)或带载体的铜箔的极薄铜层表面(实施例9~12),按照下述所示的条件范围形成了一次粒子层(Cu)、二次粒子层(铜-钴-镍合金镀层)。使用的浴组成及镀敷条件如下所述。[浴组成及镀敷条件](A)一次粒子层的形成(Cu镀敷)液体组成:铜15g/L、硫酸75g/L液温:25~30℃电流密度:1~70A/dm2库仑量:2~90As/dm2(B)二次粒子层的形成(Cu-Co-Ni合金镀敷)液体组成:铜15g/L、镍8g/L、钴8g/LpH:2液温:40℃电流密度:10~50A/dm2库仑量:10~80As/dm2对上述的一次粒子层的形成(Cu镀敷)及二次粒子层的形成(Cu-Co-Ni合金镀敷)的条件进行调整,使粗化处理面的一定区域的基于激光显微镜得到的三维表面积相对于二维表面积之比为2.0以上且小于2.2。表面积的测定使用利用上述激光显微镜的测定法。(比较例1~5)比较例中,所使用的浴组成及镀敷条件如下所述。[浴组成及镀敷条件](A)一次粒子层的形成(铜镀敷)液体组成:铜15g/L、硫酸75g/L液温:25~35℃电流密度:1~70A/dm2库仑量:2~90As/dm2(B)二次粒子层的形成(Cu-Co-Ni合金镀敷条件)液体组成:铜15g/L、镍8g/L、钴8g/LpH:2液温:40℃电流密度:20~50A/dm2库仑量:30~80As/dm2<除一次粒子层及二次粒子层以外的表面处理层>形成一次粒子层及二次粒子层后,在部分的实施例及比较例中,利用以下的条件形成了表面处理层。(实施例3、4、10、11、比较例1~5)·Co-Ni镀敷:钴镍合金镀敷液体组成:镍5~20g/L、钴1~8g/LpH:2~3液温:40~60℃电流密度:5~20A/dm2库仑量:10~20As/dm2(实施例5、12)·Ni-Zn镀敷:镍锌合金镀敷液体组成:镍2~30g/L、锌2~30g/LpH:3~4液温:30~50℃电流密度:1~2A/dm2库仑量:1~2As/dm2予以说明,在实施例5及12中,在Ni-Zn镀敷后,进行电解铬酸盐处理以及使用了二氨基硅烷的硅烷偶联处理。(实施例7)·Ni‐Cu镀敷:镍铜合金镀敷液体组成:镍2~30g/L、铜2~30g/LpH:3~4液温:30~50℃电流密度:1~2A/dm2库仑量:1~2As/dm2(实施例13)·Ni-Mo镀敷:镍钼合金镀敷液体组成:硫酸Ni六水合物:45~55g/dm3、钼酸钠二水合物:50~70g/dm3、柠檬酸钠:80~100g/dm3液温:20~40℃电流密度:1~4A/dm2库仑量:1~2As/dm2予以说明,实施例13中,在Ni-Mo镀敷后,进行了电解铬酸盐处理。(实施例14)·Ni-Sn镀敷:镍锡合金镀敷液体组成:镍2~30g/L、锡2~30g/LpH:1.5~4.5液温:30~50℃电流密度:1~2A/dm2库仑量:1~2As/dm2予以说明,实施例14中,在Ni-Sn镀敷后,进行了使用二氨基硅烷的硅烷偶联处理。(实施例15)·Ni-P镀敷:镍磷合金镀敷液体组成:镍30~70g/L、磷0.2~1.2g/LpH:1.5~2.5液温:30~40℃电流密度:1~2A/dm2库仑量:1~2As/dm2(实施例16)·Ni-W镀敷:镍钨合金镀敷液体组成:镍2~30g/L、W0.01~5g/LpH:3~4液温:30~50℃电流密度:1~2A/dm2库仑量:1~2As/dm2予以说明,实施例16中,在Ni-W镀敷后,进行了电解铬酸盐处理以及使用了二氨基硅烷的硅烷偶联处理。(实施例17)·Ni-Cr镀敷:镍铬合金镀敷使用Ni:80mass%、Cr:20mass%的组成的溅射靶而形成了镍铬合金镀层。靶:Ni:80mass%、Cr:20mass%装置:ULVACInc.制造的溅射装置输出:DC50W氩气压力:0.2Pa形成了在利用上述实施例形成的铜箔上的一次粒子层(Cu镀层)及二次粒子层(Cu-Co-Ni合金镀层)时,对一次粒子的平均粒径、二次粒子的平均粒径、落粉、剥离强度、耐热性、粗化处理面的一定区域的基于光显微镜得到的三维表面积相对于二维表面积之比进行了测定,其结果示于表1。在此,所测定的“粗化处理面”设定为形成有一次粒子层及二次粒子层一侧的最外表面。予以说明,当在二次粒子层上形成有Co-Ni镀层、Ni-Zn镀层、铬酸盐层、硅烷偶联层等除一次粒子层及二次粒子层以外的表面处理层时,将这些层中的最表层的表面作为粗化处理面来进行测定(即,对铜箔的形成全部表面处理层后的有一次粒子层及二次粒子层存在的一侧的表面进行了测定)。关于粗化处理面的一次粒子及二次粒子的平均粒径,使用HitachiHigh-TechnologiesCorporation制造的S4700(扫描型电子显微镜),以30000倍的倍率进行粒子观察和照片拍摄,根据所得的照片,对各一次粒子及二次粒子分别测定粒径。而且,将该所得的各一次粒子及二次粒子的粒径的算术平均值设定为一次粒子的平均粒径和二次粒子的平均粒径的值。予以说明,在扫描型电子显微镜照片的粒子上引直线时,将横切粒子的直线长度最长的部分的粒子的长度设定为该粒子的粒径。予以说明,测定视野的大小设定成每个视野的面积为13.44μm2(=4.2μm×3.2μm),并对一个视野进行了测定。予以说明,在利用扫描型电子显微镜照片进行观察时,将看起来重叠且存在于铜箔侧(下方)的粒子以及不重叠的粒子判定为一次粒子,将看起来重叠且存在于其他粒子之上的粒子判定为二次粒子。关于落粉特性,在铜箔的粗化处理面上粘贴透明的修补胶带(Mendingtape),在将该胶带剥离时会因附着于胶带粘合面的脱落粗化粒子而使胶带发生变色,并由胶带发生变色的情况对落粉特性进行了评价。即,将无胶带变色或仅有微小的胶带变色的情况设定为落粉OK,将胶带变色成灰色的情况设定为落粉NG。关于常态剥离强度,利用热压使表1中记载的树脂基板与铜箔粗化处理面贴合,制作覆铜板,使用一般的氯化铜电路蚀刻液,制作10mm电路,将10mm电路铜箔从基板剥离,边向90°方向牵拉边测定常态剥离强度。(传输损耗的测定)将18μm厚度的各样品与表1中记载的树脂基板(LCP:液晶聚合物树脂(可乐丽株式会社制造的VecstarCTZ-50μm)、聚酰亚胺:KANEKA公司制造厚度50μm、氟树脂厚度50μm:DuPont公司制造)贴合后,通过蚀刻以使特性阻抗成为50Ω的方式形成微带线路,并使用HP公司制造的网路分析仪HP8720C对透射系数进行测定,求出频率20GHz和频率40GHz下的传输损耗。予以说明,实施例9~12中,将带载体的铜箔的极薄铜层侧的表面与表1中记载的树脂基板贴合后,将载体剥离,然后进行镀铜,使极薄铜层与铜镀层的合计厚度为18μm后,进行与上述同样的传输损耗的测定。作为频率20GHz下的传输损耗的评价,将小于3.7dB/10cm的情况评价为“◎”,将3.7dB/10cm以上且小于4.1dB/10cm的情况评价为“○”,将4.1dB/10cm以上且小于5.0dB/10cm的情况评价为“△”,将5.0dB/10cm以上的情况评价为“×”。此外,作为比较例,将同样的结果示于表1。予以说明,在表1的一次粒子电流条件栏中记载两个电流条件、库仑量的示例是指:在左边记载的条件下进行镀敷后,再在右边记载的条件下进行镀敷。例如在实施例1的一次粒子电流条件栏中记载了“(65A/dm2、80As/dm2)+(20A/dm2、30As/dm2)”,这表示:在形成一次粒子的电流密度为65A/dm2、库仑量为80As/dm2的条件下进行了镀敷后,再在形成一次粒子的电流密度为20A/dm2、库仑量为30As/dm2的条件下进行了镀敷。由表1可以明确:本发明的实施例的结果如下所述。实施例1为将形成一次粒子的电流密度设为65A/dm2和20A/dm2、库仑量设为80As/dm2和30As/dm2且将形成二次粒子的电流密度设为28A/dm2、库仑量设为20As/dm2的情况。予以说明,形成一次粒子的电流密度和库仑量呈现为两个阶段,通常在形成一次粒子的情况下,需要两个阶段的电镀。即,为第1阶段的核粒子形成的镀敷条件和第2阶段的核粒子生长的电镀。最初的镀敷条件为用于第1阶段的核形成粒子的形成的电镀条件,接下来的镀敷条件为用于第2阶段的核粒子的生长的电镀条件。对于以下的实施例及比较例也是同样的,因此省略对其的说明。其结果是一次粒子的平均粒径为0.45μm、二次粒子的平均粒径为0.30μm,基于激光显微镜得到的粒子形成后的三维表面积为21589μm2。另一方面,相同区域的二维表面积为9924.4μm2(这相当于100×100μm的面积),因此三维表面积相对于二维表面积之比为2.18,满足本发明的条件。该结果表明具备如下特征:落粉少,常态剥离强度高达1.16kg/cm,耐热性劣化率(在常态剥离测定后对180℃、加热48小时后的剥离强度进行测定,将其差设定为劣化率)小至30%以下。予以说明,耐热劣化率按照以下式子求得。耐热劣化率(%)=(常态剥离强度(kg/cm)-180℃、加热48小时后的剥离强度(kg/cm))/常态剥离强度(kg/cm)×100实施例2为将形成一次粒子的电流密度设为65A/dm2和2A/dm2、库仑量设为80As/dm2和4As/dm2且将形成二次粒子的电流密度设为25A/dm2、库仑量设为15As/dm2的情况。其结果是一次粒子的平均粒径为0.40μm、二次粒子的平均粒径为0.15μm,基于激光显微镜得到的粒子形成后的表面积为20978μm2。另一方面,相同区域的二维表面积为9924.4μm2(这相当于100×100μm的面积),因此三维表面积相对于二维表面积之比为2.11,满足本发明的条件。该结果表明具备如下特征:无落粉,常态剥离强度高达1.08kg/cm,耐热性劣化率(在常态剥离测定后对180℃、加热48小时后的剥离强度进行测定,将其差设定为劣化率)小至30%以下。实施例3为将形成一次粒子的电流密度设为60A/dm2和10A/dm2、库仑量设为80As/dm2和20As/dm2且将形成二次粒子的电流密度设为25A/dm2、库仑量设为30As/dm2的情况。其结果是一次粒子的平均粒径为0.30μm、二次粒子的平均粒径为0.25μm,基于激光显微镜得到的粒子形成后的三维表面积为21010μm2。另一方面,相同区域的二维表面积为9924.4μm2(这相当于100×100μm的面积),因此三维表面积相对于二维表面积之比为2.12,满足本发明的条件。该结果表明具备如下特征:无落粉,常态剥离强度高达0.92kg/cm,并且耐热性劣化率(在常态剥离测定后对180℃、加热48小时后的剥离强度进行测定,将其差设定为劣化率)小至30%以下。实施例4为将形成一次粒子的电流密度设为55A/dm2和1A/dm2、库仑量设为75As/dm2和5As/dm2且将形成二次粒子的电流密度设为25A/dm2、库仑量设为30As/dm2的情况。其结果是一次粒子的平均粒径为0.35μm、二次粒子的平均粒径为0.25μm,基于激光显微镜得到的粒子形成后的表面积为20847μm2。相同区域的二维表面积为9924.4μm2(这相当于100×100μm的面积),因此三维表面积相对于二维表面积之比为2.10,满足本发明的条件。该结果表明具备如下特征:无落粉,常态剥离强度高达0.94kg/cm,耐热性劣化率(在常态剥离测定后对180℃、加热48小时后的剥离强度进行测定,将其差设定为劣化率)小至30%以下。实施例5为将形成一次粒子的电流密度设为50A/dm2和5A/dm2、库仑量设为70As/dm2和10As/dm2且将形成二次粒子的电流密度设为25A/dm2、库仑量设为30As/dm2的情况。其结果是一次粒子的平均粒径为0.30μm、二次粒子的平均粒径为0.25μm,基于激光显微镜得到的粒子形成后的表面积为20738μm2。相同区域的二维表面积为9924.4μm2(这相当于100×100μm的面积),因此三维表面积相对于二维表面积之比为2.09,满足本发明的条件。该结果表明具备如下特征:无落粉,常态剥离强度高达0.94kg/cm,耐热性劣化率(在常态剥离测定后对180℃、加热48小时后的剥离强度进行测定,将其差设定为劣化率)小至30%以下。实施例6为将形成一次粒子的电流密度设为50A/dm2和2A/dm2、库仑量设为70As/dm2和3As/dm2且将形成二次粒子的电流密度设为15A/dm2、库仑量设为30As/dm2的情况。其结果是一次粒子的平均粒径为0.25μm、二次粒子大部分为被覆(正常)镀层状态(粒径小于0.1μm),基于激光显微镜得到的粒子形成后的表面积为20112μm2。相同区域的二维表面积为9924.4μm2(这相当于100×100μm的面积),因此三维表面积相对于二维表面积之比为2.03,满足本发明的条件。该结果表明具备如下特征:无落粉,常态剥离强度高达0.81kg/cm,耐热性劣化率(在常态剥离测定后对180℃、加热48小时后的剥离强度进行测定,将其差设定为劣化率)小至30%以下。实施例7为将形成一次粒子的电流密度设为60A/dm2和15A/dm2、库仑量设为80As/dm2和20As/dm2且将形成二次粒子(二次粒子层)的电流密度设为20A/dm2、库仑量设为60As/dm2而制成被覆镀层(正常镀层)后,再将电流密度设为20A/dm2、库仑量设为20As/dm2而形成粒子的情况。其结果是一次粒子的平均粒径为0.35μm、二次粒子呈现被覆(正常)镀层状态(粒径小于0.1μm)及平均粒径0.15μm的2级构成,基于激光显微镜得到的粒子形成后的表面积为20975μm2。相同区域的二维表面积为9924.4μm2(这相当于100×100μm的面积),因此三维表面积相对于二维表面积之比为2.11,满足本发明的条件。该结果表明具备如下特征:无落粉,常态剥离强度为0.83kg/cm,耐热性劣化率(在常态剥离测定后对180℃、加热48小时后的剥离强度进行测定,将其差设定为劣化率)小至30%以下。实施例8为将形成一次粒子的电流密度设为40A/dm2和1A/dm2、库仑量设为40As/dm2和2As/dm2且将形成二次粒子的电流密度设为20A/dm2、库仑量设为20As/dm2的情况。其结果是一次粒子的平均粒径为0.15μm、二次粒子的平均粒径为0.15μm,粒子形成后的表面积为20345μm2。相同区域的二维表面积为9924.4μm2(这相当于100×100μm的面积),因此三维表面积相对于二维表面积之比为2.05,满足本发明的条件。该结果表明具备如下特征:未产生落粉,并且常态剥离强度为0.71kg/cm,耐热性劣化率(在常态剥离测定后对180℃、加热48小时后的剥离强度进行测定,将其差设定为劣化率)为35%。实施例9为将形成一次粒子的电流密度设为65A/dm2和2A/dm2、库仑量设为80As/dm2和4As/dm2且将形成二次粒子的电流密度设为25A/dm2、库仑量设为15As/dm2的情况。其结果是一次粒子的平均粒径为0.41μm、二次粒子的平均粒径为0.16μm,基于激光显微镜得到的粒子形成后的表面积为21177μm2。另一方面,相同区域的二维表面积为9924.4μm2(这相当于100×100μm的面积),因此三维表面积相对于二维表面积之比为2.13,满足本发明的条件。该结果表明具备如下特征:无落粉,常态剥离强度高达1.09kg/cm,耐热性劣化率(在常态剥离测定后对180℃、加热48小时后的剥离强度进行测定,将其差设定为劣化率)小至30%以下。实施例10为将形成一次粒子的电流密度设为60A/dm2和10A/dm2、库仑量设为80As/dm2和20As/dm2且将形成二次粒子的电流密度设为25A/dm2、库仑量设为30As/dm2的情况。其结果是一次粒子的平均粒径为0.31μm、二次粒子的平均粒径为0.25μm,基于激光显微镜得到的粒子形成后的三维表面积为21208μm2。另一方面,相同区域的二维表面积为9924.4μm2(这相当于100×100μm的面积),因此三维表面积相对于二维表面积之比为2.14,满足本发明的条件。该结果表明具备如下特征:无落粉,常态剥离强度高达0.93kg/cm,并且耐热性劣化率(在常态剥离测定后对180℃、加热48小时后的剥离强度进行测定,将其差设定为劣化率)小至30%以下。实施例11为将形成一次粒子的电流密度设为55A/dm2和1A/dm2、库仑量设为75As/dm2和5As/dm2且将形成二次粒子的电流密度设为25A/dm2、库仑量设为30As/dm2的情况。其结果是一次粒子的平均粒径为0.35μm、二次粒子的平均粒径为0.26μm,基于激光显微镜得到的粒子形成后的表面积为21010μm2。相同区域的二维表面积为9924.4μm2(这相当于100×100μm的面积),因此三维表面积相对于二维表面积之比为2.12,满足本发明的条件。该结果表明具备如下特征:无落粉,常态剥离强度高达0.95kg/cm,耐热性劣化率(在常态剥离测定后对180℃、加热48小时后的剥离强度进行测定,将其差设定为劣化率)小至30%以下。实施例12为将形成一次粒子的电流密度设为50A/dm2和5A/dm2、库仑量设为70As/dm2和10As/dm2且将形成二次粒子的电流密度设为25A/dm2、库仑量设为30As/dm2的情况。其结果是一次粒子的平均粒径为0.30μm、二次粒子的平均粒径为0.25μm,基于激光显微镜得到的粒子形成后的表面积为20978μm2。相同区域的二维表面积为9924.4μm2(这相当于100×100μm的面积),因此三维表面积相对于二维表面积之比为2.11,满足本发明的条件。该结果表明具备如下特征:无落粉,常态剥离强度高达0.94kg/cm,耐热性劣化率(在常态剥离测定后对180℃、加热48小时后的剥离强度进行测定,将其差设定为劣化率)小至30%以下。实施例13为将形成一次粒子的电流密度设为60A/dm2和10A/dm2、库仑量设为80As/dm2和20As/dm2且将形成二次粒子的电流密度设为25A/dm2、库仑量设为30As/dm2的情况。其结果是一次粒子的平均粒径为0.30μm、二次粒子的平均粒径为0.25μm,基于激光显微镜得到的粒子形成后的三维表面积为21008μm2。另一方面,相同区域的二维表面积为9924.4μm2(这相当于100×100μm的面积),因此三维表面积相对于二维表面积之比为2.12,满足本发明的条件。该结果表明具备如下特征:无落粉,常态剥离强度高达0.93kg/cm,并且耐热性劣化率(在常态剥离测定后对180℃、加热48小时后的剥离强度进行测定,将其差设定为劣化率)小至30%以下。实施例14为将形成一次粒子的电流密度设为60A/dm2和10A/dm2、库仑量设为80As/dm2和20As/dm2且将形成二次粒子的电流密度设为25A/dm2、库仑量设为30As/dm2的情况。其结果是一次粒子的平均粒径为0.30μm、二次粒子的平均粒径为0.25μm,基于激光显微镜得到的粒子形成后的三维表面积为21009μm2。另一方面,相同区域的二维表面积为9924.4μm2(这相当于100×100μm的面积),因此三维表面积相对于二维表面积之比为2.12,满足本发明的条件。该结果表明具备如下特征:无落粉,常态剥离强度高达0.92kg/cm,并且耐热性劣化率(在常态剥离测定后对180℃、加热48小时后的剥离强度进行测定,将其差设定为劣化率)小至30%以下。实施例15为将形成一次粒子的电流密度设为55A/dm2和1A/dm2、库仑量设为75As/dm2和5As/dm2且将形成二次粒子的电流密度设为25A/dm2、库仑量设为30As/dm2的情况。其结果是一次粒子的平均粒径为0.35μm、二次粒子的平均粒径为0.25μm,基于激光显微镜得到的粒子形成后的表面积为20848μm2。相同区域的二维表面积为9924.4μm2(这相当于100×100μm的面积),因此三维表面积相对于二维表面积之比为2.10,满足本发明的条件。该结果表明具备如下特征:无落粉,常态剥离强度高达0.94kg/cm,耐热性劣化率(在常态剥离测定后对180℃、加热48小时后的剥离强度进行测定,将其差设定为劣化率)小至30%以下。实施例16为将形成一次粒子的电流密度设为50A/dm2和5A/dm2、库仑量设为70As/dm2和10As/dm2且将形成二次粒子的电流密度设为25A/dm2、库仑量设为30As/dm2的情况。其结果是一次粒子的平均粒径为0.30μm、二次粒子的平均粒径为0.25μm,基于激光显微镜得到的粒子形成后的表面积为20737μm2。相同区域的二维表面积为9924.4μm2(这相当于100×100μm的面积),因此三维表面积相对于二维表面积之比为2.09,满足本发明的条件。该结果表明具备如下特征:无落粉,常态剥离强度高达0.94kg/cm,耐热性劣化率(在常态剥离测定后对180℃、加热48小时后的剥离强度进行测定,将其差设定为劣化率)小至30%以下。实施例17为将形成一次粒子的电流密度设为50A/dm2和2A/dm2、库仑量设为70As/dm2和3As/dm2且将形成二次粒子的电流密度设为15A/dm2、库仑量设为30As/dm2的情况。其结果是一次粒子的平均粒径为0.25μm、二次粒子大部分呈现被覆(正常)镀层状态(粒径小于0.1μm),基于激光显微镜得到的粒子形成后的表面积为20108μm2。相同区域的二维表面积为9924.4μm2(这相当于100×100μm的面积),因此三维表面积相对于二维表面积之比为2.03,满足本发明的条件。该结果表明具备如下特征:无落粉,常态剥离强度高达0.81kg/cm,耐热性劣化率(在常态剥离测定后对180℃、加热48小时后的剥离强度进行测定,将其差设定为劣化率)小至30%以下。与此相对,比较例呈现出如下结果。比较例1为将形成一次粒子的电流密度设为63A/dm2和10A/dm2、库仑量设为80As/dm2和30As/dm2且未形成二次粒子的情况。其结果是一次粒子的平均粒径为0.50μm,基于激光显微镜得到的粒子形成后的表面积为20804μm2。相同区域的二维表面积为9924.4μm2(这相当于100×100μm的面积),因此三维表面积相对于二维表面积之比为2.10,满足本发明的条件。该结果表明:虽然是无落粉且常态剥离强度高达1.38kg/cm的实施例水准,但是耐热性劣化率(在常态剥离测定后对180℃、加热48小时后的剥离强度进行测定,将其差设定为劣化率)显著变差,为60%,作为整体的高频电路用铜箔的评价结果为不良。比较例2表示不存在一次粒径且仅存在二次粒子层的以往例。即,比较例2是将形成二次粒子的电流密度设为50A/dm2、库仑量设为30As/dm2的情况。其结果是二次粒子的平均粒径为0.30μm,基于激光显微镜得到的粒子形成后的三维表面积为21834μm2。相同区域的二维表面积为9924.4μm2(这相当于100×100μm的面积),因此三维表面积相对于二维表面积之比为2.20,未满足本发明的条件。该结果表明:大量产生粗化粒子的落粉,常态剥离强度为1.25kg/cm,是实施例水准,耐热性劣化率(在常态剥离测定后对180℃、加热48小时后的剥离强度进行测定,将其差设定为劣化率)小至30%以下,是实施例水准,如上述所述,由于存在大量产生落粉的问题,因此作为整体的高频电路用铜箔的综合评价结果为不良。比较例3为将形成一次粒子的电流密度设为63A/dm2和1A/dm2、库仑量设为80As/dm2和2As/dm2且将形成二次粒子的电流密度设为28A/dm2、库仑量设为73As/dm2的情况。其结果是一次粒子的平均粒径为0.35μm、二次粒子的平均粒径为0.60μm,基于激光显微镜得到的粒子形成后的三维表面积为21797μm2。相同区域的二维表面积为9924.4μm2(这相当于100×100μm的面积),因此三维表面积相对于二维表面积之比为2.20,未满足本发明的条件。该结果表明:大量产生了落粉,常态剥离强度高达1.42kg/cm,耐热性劣化率(在常态剥离测定后对180℃、加热48小时后的剥离强度进行测定,将其差设定为劣化率)小至30%以下,是实施例水准,但是大量产生了落粉,因此作为整体的高频电路用铜箔的评价结果为不良。比较例4为将形成一次粒子的电流密度设为63A/dm2和1A/dm2、库仑量设为80As/dm2和2As/dm2且将形成二次粒子的电流密度设为31A/dm2、库仑量设为40As/dm2的情况。其结果是一次粒子的平均粒径为0.35μm、二次粒子的平均粒径为0.40μm,粒子形成后的表面积为22448μm2。相同区域的二维表面积为9924.4μm2(这相当于100×100μm的面积),因此三维表面积相对于二维表面积之比为2.26,未满足本发明的条件。该结果表明:虽然常态剥离强度高达1.37kg/cm,耐热性劣化率(在常态剥离测定后对180℃、加热48小时后的剥离强度进行测定,将其差设定为劣化率)小至30%以下,是实施例水准,但是大量产生了落粉。因此作为整体的高频电路用铜箔的评价结果为不良。比较例5为将形成一次粒子的电流密度设为63A/dm2和10A/dm2、库仑量设为80As/dm2和30As/dm2且将形成二次粒子的电流密度设为31A/dm2、库仑量设为40As/dm2的情况。其结果是一次粒子的平均粒径为0.50μm、二次粒子的平均粒径为0.40μm,粒子形成后的表面积为22086μm2。相同区域的二维表面积为9924.4μm2(这相当于100×100μm的面积),因此三维表面积相对于二维表面积之比为2.23,未满足本发明的条件。该结果表明:常态剥离强度为1.35kg/cm,耐热性劣化率(在常态剥离测定后对180℃、加热48小时后的剥离强度进行测定,将其差设定为劣化率)小至30%以下,是实施例水准,但是产生了落粉。因此作为整体的高频电路用铜箔的评价结果为不良。由上述实施例及比较例的对比可以明确:当在铜箔(原箔)的表面形成铜的一次粒子层后在该一次粒子层上形成由包含铜、钴及镍的3元系合金形成的二次粒子层时,粗化处理面的一定区域的基于激光显微镜得到的三维表面积相对于二维表面积之比为2.0以上且小于2.2,由此具有能够稳定抑制被称作落粉的现象的优异效果,而且能够进一步提高剥离强度,且能够提高高频特性。此外,将一次粒子层的平均粒径设为0.25~0.45μm且由包含铜、钴及镍的3元系合金形成的二次粒子层的平均粒径设为0.35μm以下,这在实现上述效果方面是更为有效的。予以说明,在耐热处理层中含有Co时,具有使传输损耗变大的倾向。