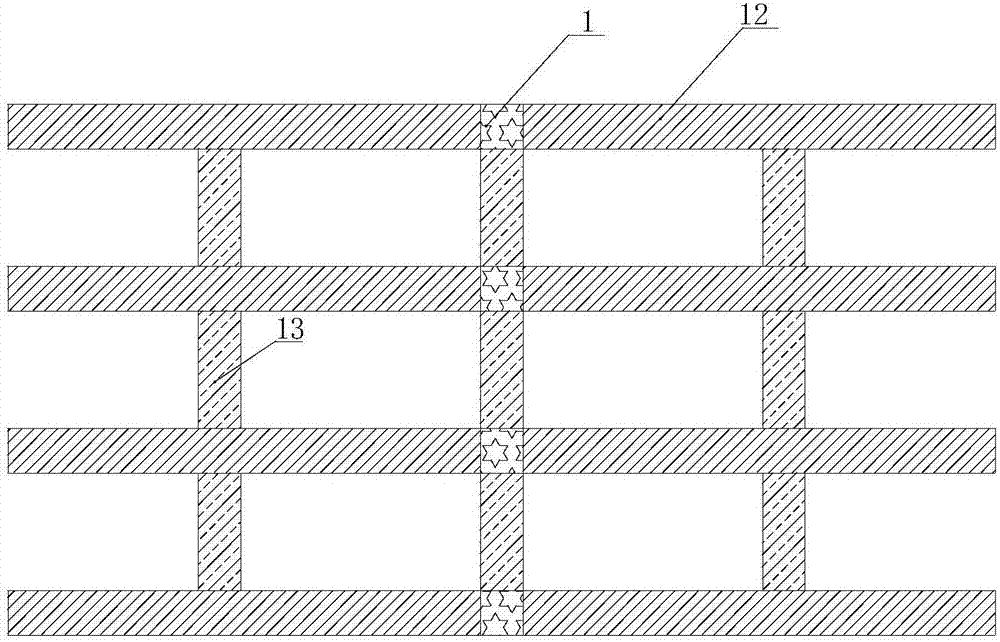
本实用新型属于混凝土结构加固
技术领域:
,特别涉及一种提升混凝土结构承载能力的加固系统。
背景技术:
:目前,混凝土结构加固有粘贴钢板法、粘贴碳纤维、钢丝绳网片-复合砂浆外加层加固法、加大截面加固法和体外预应力加固法多种方法,但每种方法都存在不足之处。粘贴钢板法,通过在被加固梁体底部粘贴钢板来实现梁承载能力提高。粘贴钢板法加固结构形式单一,承载能力提升较低,钢板与混凝土梁的连接部位是关键部位,同时也是薄弱部位,不能充分发挥钢材的力学材料特性,加固结构合理性有待进提高。粘贴碳纤维,复合材料法通过在被加固梁底部粘贴碳纤维复合材料来实现梁承载能力的提高。碳纤维复合材料法对梁体承载能力提升较低,材料强度利用率不高,同时碳纤维材料存在耐久性和老化问题,尤其是复杂恶劣环境下,碳纤维复合材料不耐火,火灾会导致承载能力丧失。钢丝绳网片-复合砂浆外加层加固法:通过粘结强度及弯曲强度优秀的渗透性聚合砂浆附着,与混凝土紧密结合形成一体来实现梁承载能力的提高。不足之处是:(1)对复合砂浆性能和质量的要求较高,而市场上供应的产品(聚合物砂浆)一般性能较差,若不专门配制,容易发生安全质量问题;(2)高强不锈钢丝及高性能的复合砂浆的单价较高,就经济角度考虑有所欠缺,此外对结构承载能力的加固效果有限;(3)使用前,需做较细致的技术经济综合评估才能确定其适用性。加大截面加固法,采取增大混凝土结构或构筑物的截面面积,以提高其承载力和满足正常使用。对结构承载能力提升较低,施工湿作业时间长,在混凝土养护期间需限制荷载,对交通影响比较大,加固后结构自重增大、建筑使用空间减小。体外预应力加固法,需要对桥梁主要受力结构进行加固时,可在梁体外部(梁底与梁两侧)设置钢筋或钢丝束,并施加预应力,以改善桥梁的受力状况,提高桥梁承载能力。存在的问题是(1)体外索布置在截面外,防腐、保护相对较困难,易受外界影响。(2)锚固及转向区域易产生应力集中,局部应力大,对锚固施工要求高。(3)体外索张拉力较小,不能充分发挥体外索强度高的优点,对锚具及夹片的要求很高。(4)体外预应力筋的变形和混凝土的变形不一致,容易造成预应力损失,且对结构承载能力提升较低。技术实现要素:本实用新型要解决的技术问题是提供一种能大幅度提高被加固结构的承载能力,加固系统能够灵活调整,结构受力更加科学合理,加固效率高,后期维护方便、快捷,耐火性好,使用寿命长的提升混凝土结构承载能力的加固系统及其施工方法。本实用新型采用以下技术方案解决上述技术问题:一种提升混凝土结构承载能力的加固系统,包括拱圈、拱脚和钢梁;所述钢梁连接在被加固结构主梁的底面,拱圈的跨中顶部连接钢梁底面,拱圈的两个端部分别通过拱脚连接被加固结构主梁两侧的混凝土构筑物。所述拱圈的跨中顶部设有支座垫,支座置于支座垫上,支座顶部连接钢梁底面。所述混凝土构筑物的内侧设有预埋件,预埋件分别焊接钢筋网和拱圈的端部,并浇注混凝土形成拱脚。所述钢梁顶面与被加固结构主梁底面粘贴并通过螺栓紧固。所述拱圈为多个,相邻两个拱圈之间用横向联系梁连接。一种提升混凝土结构承载能力的加固系统的施工方法,包括以下步骤:①预制拱圈;②拱脚安装处的表面处理对混凝土构筑物内侧的拱脚安装处表面清洁和粗糙处理;③搭设模板与支架;④绑扎钢筋网;⑤焊接预埋件和安装拱圈拱脚安装处设有预埋件,将钢筋网与预埋件焊接,然后吊装拱圈,将拱圈的端部和预埋件焊接;⑥浇筑混凝土拱脚安装处浇筑混凝土形成拱脚;⑦完成所有拱圈12和横向联系梁安装重复步骤①至步骤⑥,直至完成所有拱圈的安装;相邻两个拱圈之间用横向联系梁连接,横向联系梁的顶面与被加固结构主梁底面栓接或焊接;⑧被加固结构主梁底部安装钢梁钢梁顶面与被加固结构主梁底面粘贴并通过螺栓坚固;⑨在拱圈跨中顶部放置支座垫和支座使用千斤顶将钢梁顶升,在拱圈跨中顶部依次放置支座垫和支座,然后移除千斤顶,施工完成。本实用新型的优点在于:(1)承载能力提升方面。本实用新型可以大幅度地提高被加固结构的承载能力,能通过灵活调整拱圈的矢跨比、截面形式、材料等级,型钢的截面形式、材料等级,顶升力大小等,确定承载能力提高幅度,并且后期的调整和维护非常方便、快捷。(2)结构形式方面。与现有加固方法相比,本实用新型的加固系统受力更加科学合理,既能充分的发挥材料特性,又能很好的利用结构设计合理的优势。(3)受力机理方面。粘贴钢板法,粘贴碳纤维法等是在被加固结构一次受力的基础上进行加固,加固效率较低,本实用新型加固系统的加固效果可以抵消被加固结构的一次受力和二次受力,加固效率能接近100%。与体外预应力加固方法相比,本实用新型加固效果显著,尤其是不存在后期的预应力损失问题。(4)后期维护方面。与现有的加固方法相比,本实用新型加固系统后期可随时进行加固效果的调整,方便快捷,并且使用寿命远大于其它加固方法,综合经济效益高。(5)耐火性方面。粘贴碳纤维法存在一个显著的问题就是耐火性差,火灾作用下会瞬间丧失承载力,本实用新型的加固系统比粘贴碳纤维法在耐火性方面存在优势。附图说明图1是本实用新型加固系统安装在被加固结构上的结构示意图。图2是本实用新型加固系统的平面示意图。图中,1:支座,2:支座垫,3:顶升垫板,4:千斤顶,5、预埋件,6:钢筋网,7:拱脚,8:钢梁,9:被加固结构主梁,10:混凝土构筑物,11:被加固结构主梁支座,12:拱圈,13:横向联系梁。具体实施方式以下结合附图和具体实施例对本实用新型的具体实施方式作详细说明,但不构成对本实用新型权利要求保护范围的限制。一种提升混凝土结构承载能力的加固系统,包括支座1、支座垫2、拱圈12、拱脚7和钢梁8;所述钢梁8连接在被加固结构主梁9的底面,在拱圈12跨中顶部放置支座垫2,支座1置于支座垫2上,支座1顶部连接钢梁8底面;拱圈12的两个端部分别通过拱脚7连接被加固结构主梁9两侧的混凝土构筑物10。被加固结构主梁9两端分别通过被加固结构主梁支座11连接混凝土构筑物10的顶部。所述混凝土构筑物10的内侧设有预埋件5,预埋件5分别焊接钢筋网5和拱圈12的端部并浇注混凝土形成拱脚7。所述钢梁8顶面与被加固结构主梁9底面粘贴并通过螺栓坚固。所述拱圈为多个,相邻两个拱圈之间用横向联系梁连接。上述一种提升混凝土结构承载能力的加固系统的施工步骤:①预制拱圈12根据需要达到的加固效果、桥下净空等实际条件和要求,控制拱圈12特性例如材料等级、截面形式和矢跨比等,制作拱圈12。②拱脚7浇筑处的表面处理拱脚7浇筑处分别位于被加固结构两侧的混凝土构筑物的内侧。施工时要求混凝土表面洁净、无污染、杂质、油渍、尘土等。首先用凿毛机对需要处理的混凝土表面进行凿毛处理,把表面的浮浆、杂物凿除,露出受力钢筋,注意不要损伤原结构中钢筋,然后用旋转钢丝刷清扫机清扫,再用鼓风机或吸尘器清除浮沉、细粒,用高压水枪冲洗一遍,待干燥后,即可进行施工。③搭设模板与支架在拱脚7浇筑处搭设模板与支架。模板要具有足够的强度、刚度和稳定性,能安全可靠的承担施工中可能出现的各种荷载,其次要保证结构的设计形状、尺寸及各部分相互之间位置的准确性,最后模板的接缝必须密合,确保混凝土浇筑过程中不漏浆。④绑扎钢筋网6钢筋网6要严格按设计图纸要求绑扎,注意钢筋间距、位置的准确,绑扎点牢固,保证受力钢筋不产生位移,双向受力的钢筋交叉点应全部扎牢,拱脚7浇筑处钢筋与原结构中钢筋连接在一起。⑤焊接预埋件5,安装拱圈12拱脚7浇筑处设有预埋件5。将钢筋网6与预埋件5焊接,然后吊装拱圈12,将拱圈12端部分别和预埋件5焊接。⑥浇筑混凝土拱脚7浇筑混凝土。混凝土等级根据具体施工要求和加固设计计算选定。在浇筑过程中,振动棒应避免与预埋件和钢筋直接接触,需小心谨慎振捣。混凝土成型后,需加强养护,确保混凝土浇筑质量。⑦完成所有拱圈12和横向联系梁13安装重复以上施工步骤,直至完成所有拱圈12的安装,最后进行横向联系梁13安装,横向联系梁13尺寸根据设计计算确定,横向联系梁13与各拱圈之间采用栓接或焊接。⑧搭设施工平台在各拱圈12之间搭设下一步施工平台,确保强度、刚度和稳定性符合安全生产施工标准。⑨被加固结构主梁9底部安装钢梁8A、被加固结构主梁9底面处理在被加固结构主梁9的底面放出加固位置大样,凿除钢梁8放置区混凝土表面2~5mm厚的表层砂浆,使坚实的混凝土外露,并形成平整的粗糙面,表面不平处应用尖凿轻凿整平。再用钢丝轮清除表面浮浆,剔除表层疏松物,最后用压缩空气吹净表面粉尘,并用甲苯或工业丙酮擦拭表面。对较大面积的劣质层,剔除后应用聚合物水泥砂浆修复平整。加固前用丙酮擦洗干净。B、在被加固结构主梁9底部植埋锚固螺杆。C、安装钢梁8钢梁8可选用型钢或钢板,依据实际放样进行下料和加工,并依据现场植埋的螺杆,对钢梁8配套打孔,然后将钢梁8的上表面用磨光砂轮机或钢丝刷磨机进行除锈和粗糙处理,打磨粗糙度越大越好,打磨纹路应与加固装置受力方向垂直。用脱脂棉沾丙酮将钢梁8的上表面擦拭干。将钢梁8固定在螺杆上,并保证钢梁8的上表面与被加固结构主梁9底面之间的间隙在3mm以上,以确保灌注胶层的厚度在3mm以上,焊接型钢或钢板接缝,完成安装。D、配制结构胶。E、封边将钢梁8用封边胶封闭边缘。F、灌注结构胶往钢梁8的上表面与被加固结构主梁9底面之间的间隙灌注结构胶直至灌注密实,最后用封边胶堵住灌注孔。G、钢梁8表面防腐处理钢梁8固化密实效果可靠后,去除所有注入咀和排气管,并清除钢梁8表面污垢和锈斑,对钢梁8外露处作防腐处理。⑩在拱圈12跨中顶部放置支座垫2和支座1使用多个千斤顶4同时将钢梁8顶升,在拱圈12跨中顶部安装支座垫2和支座1,支座1置于支座垫2上。为保护拱圈12,千斤顶4底部可放置顶升垫板3。安装好支座垫2和支座1后拆卸千斤顶及顶升垫板3,施工完成。现有的加固方法均是在一次受力的基础上进行加固,例如粘贴钢板和碳纤维等,加固效率比较低,本实用新型加固系统安装后可以抵消结构的一次受力和二次受力,加固效果可控且后期调整方便、快捷,这是本实用新型加固系统与其它加固方法最大的不同之处,可以大幅提升结构承载能力,具有显著的加固效果。以单片梁为例,运用本加固系统,采用简化的方法,在自重荷载作用下,分别从理论和有限元计算两个方面对结构加固系统进行计算:(1)加固系统的理论方面计算加固效率公式为:式中:η:加固效率;MI:加固前被加固结构主梁中最大弯矩;MII:加固后被加固结构主梁中最大弯矩。其中,MI与MII计算方法:①加固前,在自重荷载作用下,被加固结构主梁内最大弯矩为:最大正弯矩:式中:MI-加固前被加固结构主梁内最大弯矩;q1-被加固结构主梁自重均布荷载;l-被加固结构主梁计算长度。②加固后,在自重荷载作用下,被加固结构主梁内最大弯矩为:最大正弯矩:式中:MII-加固前被加固结构主梁内最大弯矩;q1-被加固结构主梁自重均布荷载;q2-被加固结构主梁底部钢梁8(型钢)自重均布荷载;E1-混凝土弹性模量;E2-型钢弹性模量;I1-被加固结构主梁截面抗弯惯性矩;I2-被加固结构主梁底部钢梁8(型钢)截面抗弯惯性矩;③加固效率实际加固中,可以采用轻质高强的材料降低q2,不局限于钢材,可以是铝合金等,通过合理布置截面形式增大E2I2,使得加固效率接近100%。(2)加固系统的有限元计算方面计算为了验证本专利的加固效果,采用ANSYS通用有限元软件进行计算,计算梁的横截面尺寸为0.4m×0.5m,梁跨度10m,在自重荷载作用下,加固前梁上各个节点(主梁纵向每隔1m设置一个节点)的挠度见表1。加固钢板厚度为0.015m,加固拱圈的跨度为10m,拱圈的矢高为4m,钢材选用40#A工字钢,尺寸为400mm×142mm×10.5mm。表1计算梁加固前后对比测点编号加固前挠度(mm)加固后挠度(mm)挠度提升值(mm)100021.60610.69330.912833.03821.29881.739444.15911.75562.403554.87092.03022.840765.11472.11672.998074.87092.03022.840784.15911.75562.403593.03821.29881.7394101.60610.69330.912811000由表1可知看出,采用本实用新型的加固系统,加固后梁体的挠度(刚度)得到了大幅度的提升,在实际加固中,由于横梁联系梁的整体增强作用,梁体的挠度还会进一步提升,同时主拱圈工字钢的型号、数量,横向联系梁的型号、数量等参数均可以调整,即梁体的加固效果可以根据不同的加固要求进行相应的调整。当前第1页1 2 3