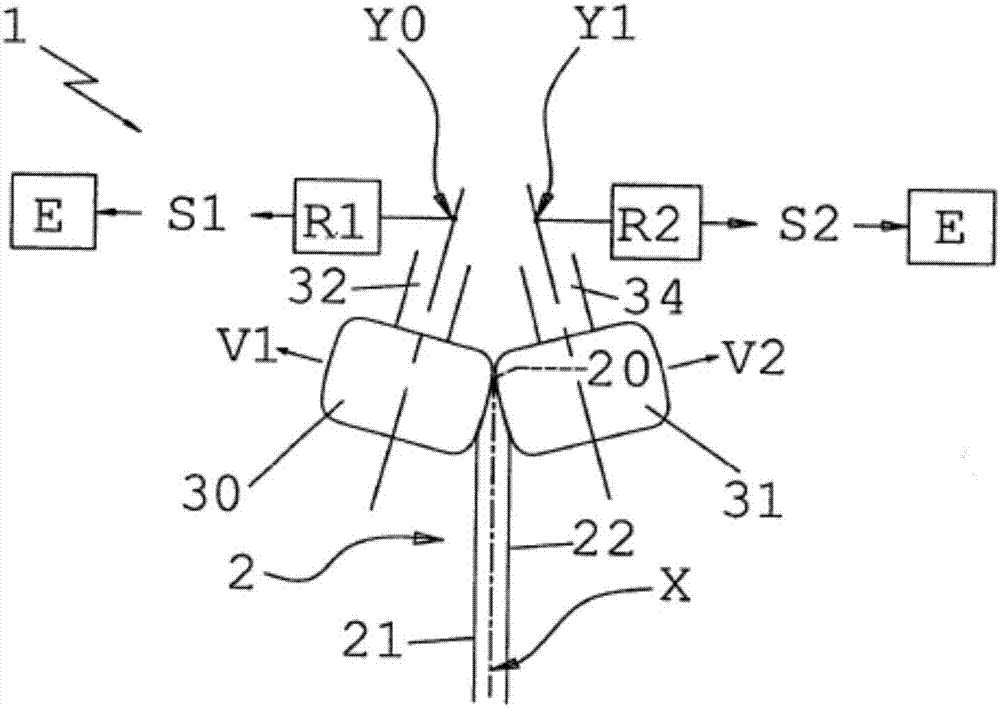
本发明涉及一种用于控制条带刀片的磨锐状态的设备,该条带刀片特别地可以用于生产纸卷。
背景技术:用于生产纸卷的传统工艺需要复卷机,通过该复卷机,纸幅围绕硬纸板芯缠绕以形成被称为“卷材(log)”的中间产品,该中间产品由通过围绕硬纸管缠绕纸幅所获得的纸卷制成,并且注定被横向切割以获得较短的纸卷,即,符合给定商业要求的纸卷。卷材的横向切割特别重要。实际上,沿着与卷材的纵向轴线不完全正交的平面切割卷材,会导致形成有瑕疵的卷,所述有瑕疵的卷的侧底(sidebase)是倾斜的。该缺陷在旨在将卷用在自动分配器中时更为严重,实际上,这些自动分配器要求卷的侧底与卷本身的轴线完全正交,否则卷趋于卡在分配器中。
技术实现要素:本发明的主要目的在于提供一种使得能消除或至少显著地减少上述缺陷的设备。根据本发明,提供了一种用于控制刀片的磨锐状态的设备,所述刀片具有切刃,所述切刃由朝向包含所述切刃本身的平面会聚的两侧界定,其中,所述设备包括两个控制表面,所述控制表面中的每一个均与所述切刃的对应侧接触并与至少一个传感器连接,所述传感器产生与所述控制表面相对于所述平面的位移成比例的电位移信号,并且其中,所述设备包括可编程电子单元,所述可编程电子单元接收所述位移信号并比较所述位移信号,并在该比较产生超过预定限度的值时发出误差信号,并且其中,所述可编程电子单元连接至用于支撑和移动磨锐装置的装置。进一步地,所述控制表面为两个探针式探测器的外表面。进一步地,所述探针式探测器围绕两个相应的轴线铰接。进一步地,所述传感器中的每一个为旋转编码器。进一步地,所述传感器中的每一个应用于相应探针式探测器的旋转轴线。进一步地,所述轴线相互平行且相对于所述平面彼此相对,并且由相应的臂支撑。进一步地,所述轴线是重合的。进一步地,所述控制表面为界定辊的外部凹槽的表面,所述辊沿着轴线自由地平移,该轴线垂直于所述平面并与所述刀片间隔开一定量以使得所述切刃进入所述凹槽。进一步地,所述误差信号与光信号和/或声信号相关联。本发明使得可以即刻检查刀片的磨锐状态,检查刀片切刃的对称性,并在需要时激活适合的磨锐装置,该磨锐装置可以直接或间接地与本设备连接。此外,上述检查是连续的,并提供可以在任何时候使用的检查信号。还要注意的是,检查过程实质上是机械性质的,因此避免了可能的切割残留物的不利影响。此外,检查并不会对被检查机器的运行造成不利影响。另外,本设备可以装配于现有的机器,并且能够以相对简单的组装操作集成到现有的生产线中。此外,本设备不需要大型保养,即使在长期使用后也可以基本上保持其特征不变。附图说明根据以下描述并借助于附图,本领域任何技术人员将最佳地理解本发明的这些和其他的优点以及特征,以下描述和附图是作为本发明的实践示例给出的,而不应被视为具有限制意义,在附图中:-图1示意性地示出了刀片的一部分的侧视图,其中刀片上布置有根据本发明的控制设备;-图2、图3和图4以局部截面图示意性地示出了刀片的三种可能运行状况,其中出于简化之目的,仅在图2中示出了控制设备;-图5示意性地示出了根据本发明的设备的实施例的又一示例;-图6示意性地示出了根据本发明的设备的实施例的替选形式;-图7示意性地示出了根据本发明的设备的可能操作实施。具体实施方式参照附图,根据本发明的控制设备1用于检验条带刀片2的正确磨锐,该条带刀片由具有锋利刃20的薄片状主体形成,该锋利刃由朝向切刃所在的平面会聚的两个面21、22界定。图1至图5所示的设备包括两个探头式探测器30、31,这两个探头式探测器被布置成彼此相对,且与切刃20的两侧接触,以根据每个探测器30、31与刀片2的相互作用来确定取决于切刃20的形状的信号S1、S2。实际上,取决于两个探测器30、31相对于刀片2的位移(图中用V1和V2示出),可以控制刀片2的磨锐或切刃20的对称性。每个所述探测器30、31均与切刃20的对应侧21、22接触。特别地,所述探头式探测器30、31由相应的臂32、34支撑,上述臂又围绕相应的轴线Y0、Y1铰接。图2、图3和图4中垂直于纸面的轴线Y0、Y1彼此平行,并且相对于切刃20的两侧20、21所会聚的平面X位于相对侧。在图中,示意地描绘了支撑探头式探测器的臂32、34,其他部分在下文描述。如前所述,由探头式探测器30、31的移动产生的信号S1、S2中的每一个均具有与同一探头式探测器30、31相对于刀片2的位移V1、V2相对应的值。根据本发明的可能实施例,本设备包括:感测装置R1、R2,即检测器,用于感测臂32、34围绕相应的轴线Y0、Y1的旋转;以及电子处理装置,当检测到两个探头式探测器30、31的旋转角度的幅度之间存在不一致的值时,该电子处理装置倾向于发出误差信号。所述检测器Rl、R2中的每一个均为旋转编码器,该旋转编码器测量各个臂32、34围绕相应的轴线Y0、Y1旋转的角度。所述信号S1、S2为由传感器R1、R2发出并且被发送至处理单元E的电信号。所述传感器R1、R2中的每一个均可以应用于相应探头式探测器30、31旋转轴线Y0、Y1。误差信号可以与另外的视觉信号和/或声信号相关联。当刀片2被正确地磨锐时,即,当切刃20具有适合于实现对卷材(或其他待切割的材料)的正确切割的构造时,两个探头式探测器30、31与刀片2等距,如图2所示。在这种情况下,由检测器R1、R2针对切刃20的两侧发出的信号S1、S2彼此相等,原因在于它们与探头式探测器30、31的相等角位移相对应,并且处于臂32、34围绕轴线Y0、Y1的相等位移角度。在这种情况下,切刃20的两侧相对于所述平面X对称地定向,并且没有产生误差信号。当刀片2未呈现正确磨锐的刃时,如图3和图4示例,信号S1和S2彼此不同,并且在可能考虑到阈值的情况下,设备1通过单元E发出误差信号,该误差信号例如用于指令适于对刀片2重新磨锐的装置的介入,以使刀片回到最佳构造(即,切刃的两侧相对于平面X对称定向的构造)。另外地或可替选地,由单元E生成的误差信号可以用于控制警报信号的发出。在图3和4中,沿刀片2的竖直走向,示出了两个另外的轴线X1和X2,这两个轴线表明刀片的构造不正确。特别地,在图3中,轴线X1在轴线X的左边,表明切刃20的左轮廓(面21)减少得较多。类似地,在图4中,轴线X2在轴线X的右边,表明切刃20的右轮廓面22减少得较多。在图2、图3和图4所示的示例中,前述轴线Y0和Y1彼此平行且不重合。在图5的示例中,两个探头式探测器的臂32、34铰接在相同的轴线上,即,轴线Y0和Y1重合。因此,参照图1至图5所示的示例,根据本发明的控制设备可以用于检查具有切刃20的刀片的磨锐状态,该切刃由朝向包含该切刃的平面X会聚的两侧或两面21、22界定,该设备包括两个控制探头式探测器30、31,每个探测器与所述切刃20的对应侧21、22接触并与相应的传感器Rl、R2、R4连接,所述传感器产生电位移信号S1、S2、S4,该电位移信号与探头式探测器相对于所述平面X的位移成比例,并且该设备包括可编程电子单元E,该可编程电子单元接收所述位移信号S1、S2、S4并比较所述位移信号,并在位移信号之间的差超过预定限度时发出误差信号。根据图6所示的示例,控制设备包括具有外部环形凹槽40的辊4,刀片2的切刃20进入该环形凹槽。辊4沿着与切刃20的平面X垂直的轴线A4自由地平移。优选地,辊4还围绕所述轴线A4自由地旋转。在图6所示的示例中,辊4与由线性传感器构成的侧向位移检测器R4相关联,该侧向位移检测器检测由于切刃20的不对称磨损所引起的辊4向右或向左的任何位移。由可编程电子单元E接收信号S4,如果该信号的绝对值超过预定限度,则可编程电子单元发出误差信号(与上面所描述的类似),其中取决于辊4是朝向右移动还是朝向左移动,该信号可能具有正号或负号。参照上述所有示例,根据本发明的设备包括两个控制表面,每个控制表面与所述切刃20的对应侧21、22接触并与至少一个传感器Rl、R2、R4连接,所述传感器产生与控制表面相对于所述平面X的位移成比例的电位移信号S1、S2、S4,并且根据本发明的设备包括可编程电子处理单元E,该可编程电子处理单元接收所述位移信号S1、S2、S4并处理所述位移信号,并在处理产生超过预设限度的值时发出误差信号。根据第一示例,控制表面是探头式探测器30、31的外表面,并且如果由传感器Rl、R2产生的位移信号S1、S2的值之间的差超过给定的限值,则处理单元E产生误差信号。在参照图6描述的示例中,控制表面是界定辊4的凹槽40的表面,并且如果由传感器R4产生的位移信号S4的绝对值大于预定限度,则处理单元E发出误差信号。例如,辊4可以由钢制成,涂覆有耐磨陶瓷材料。所述误差信号可以用于控制恢复装置的自动介入,该恢复装置适于恢复刀片的锋利。更特别地,当误差信号的绝对值大于/小于预定参考值时,可以自动启用/停用所述恢复装置的介入。例如,可以通过下述部件来实现恢复刀片的锋利:适合布置在刀片的两侧的机动化砂轮100,即,各自均由旋转致动器101驱动的砂轮;致动器101,其中只要误差信号的绝对值大于预定参考值,就调节砂轮100的旋转速度。或者,例如,如果砂轮100为各自均连接至相应的机动化滑动装置102的砂轮,那么只要误差信号的绝对值大于预设参考量,则可以通过下述方式来实现恢复刀片的锋利:使用误差信号以用于移动机动化滑动装置102(如图7中由箭头“F”示意性地指示的),从而调节砂轮100施加于刀片的两侧的压力。图7的图中示出了致动器101和滑动装置102,其中,为了简化之目的,致动器101和滑动装置102两者均连接至单元4,然而在磨锐装置中,通常优选的是将两个砂轮均连接至旋转致动器或机动化滑动装置。由于取决于前述误差信号的符号为正还是为负可以致动左砂轮或右砂轮100,因而刀片锋利的自动恢复是可选择的。实际上,在不脱离所采用的方案的范围并因而保持在本专利所授予的保护范围的限制内的情况下,执行的细节(如在形状、尺寸、元件布置和所使用材料的性质方面)能够以任何等效的方式变化。