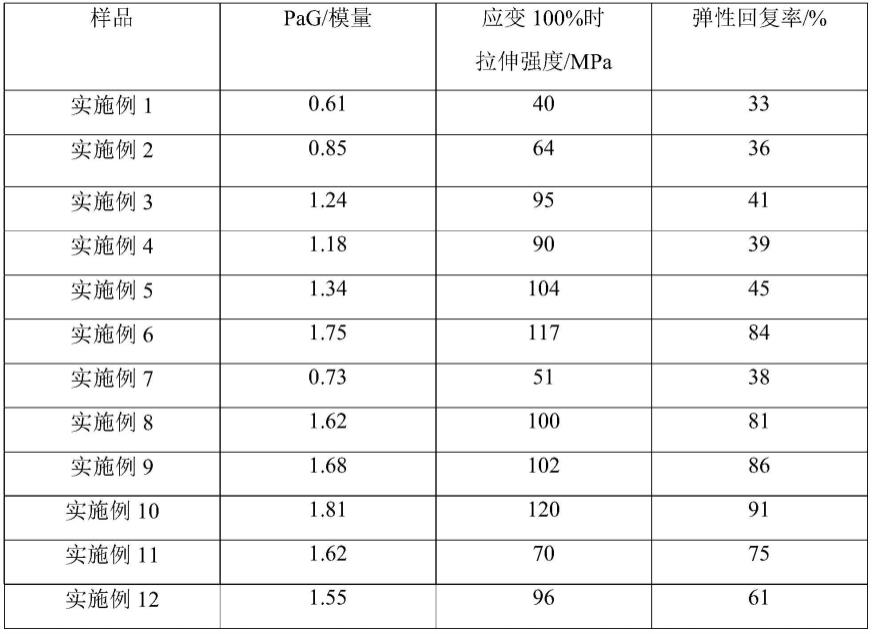
1.本发明属于中空纤维及其制备技术领域,特别涉及一种高强高弹可降解中空纤维及其制备方法。
背景技术:2.随着高分子学科的高速发展,塑料、橡胶、纤维等高分子材料在各个领域得到了广泛的应用与发展。但是传统高分子材料制品在给人们的生产生活带来极大的便利的同时,也不可避免地造成了恶劣的环境问题:废弃的高分子材料大多在自然环境中难以降解,不仅会污染土壤、水体,也会给大部分生物的生存条件带来危害。而开发可再生资源制备的降解高分子材料是解决上述问题的有效途径。
3.聚丁二酸丁二醇酯(pbs)是一种新型脂肪族可生物降解聚酯材料,pbs的合成原料丁二醇和丁二酸及其衍生物可以通过纤维素、葡萄糖、乳糖等可再生资源生物发酵得到,是一种环境友好型绿色材料。而与其他可生物降解聚酯材料如聚乳酸、聚羟基丁酸酯相比,具有良好的物理机械性能、易加工成型等特点。pbs中空纤维在很多领域都有应用,如医护用品、组织工程材料、农林业行业等。
4.为了得到可降解中空纤维,目前主要的技术方法有以下几种,一是配制铸膜液,经熟化脱泡后,加压通过喷丝头挤出纺丝,再经溶剂挥发、凝胶后成膜,如申请号为201410621531.2的中国专利申请,但此时需要大量的有机溶剂并产生含溶剂废水,这无疑不利于环保;另一种方法采用热致相分离的方法,将可降解树脂与高温致孔剂在树脂熔点以上搅拌共混得到原料液,随后使用专用喷丝头挤出得到中空纤维,如申请号为201210039735.6的中国专利申请,但此方法所需要的高温致孔剂价格昂贵、后续脱处工序繁琐,并且获得的中空纤维力学性能较差,限制了可降解中空纤维的应用。此外,目前制备可降解中空纤维较为成熟的技术都集中于聚乳酸(pla)、聚碳酸丁二醇酯(pbc)、聚己内酯(pcl)等价格昂贵的高分子材料,如申请号为cn201210547368.0的中国专利申请。
5.基于以上,制备可降解中空纤维仍存在较大的问题,难以在保证制备过程不对环境造成污染的前提下以较低成本获得性能优异的中空纤维。开发一种简单环保的方法,得到高强高弹的pbs中空纤维已成为发展的重要方向。
技术实现要素:6.为了克服现有技术中存在的缺点与不足,本发明的首要目的在于提供一种高强高弹可降解中空纤维的制备方法。
7.本发明的又一目的在于提供一种上述制备方法制备得到高强高弹可降解中空纤维。
8.本发明的再一目的在于提供一种上述高强高弹可降解中空纤维的应用。
9.本发明的目的通过下述技术方案实现:
10.一种高强高弹可降解中空纤维的制备方法,包括以下操作步骤:
11.(1)选取聚丁二酸丁二醇酯(pbs)生物降解树脂并用真空烘箱进行干燥除水;
12.(2)将所得的干燥聚丁二酸丁二醇酯生物降解树脂加入挤出机中熔融得到熔体,熔体由口模进行挤出成型,并通过环形风刀对所得中空纤维外表面进行冷却,环形风刀温度为5~20℃,再经过一个带有温控系统的水槽对中空纤维进行冷却,控制水槽的冷却温度为30~50℃,最后将中空纤维经由牵引辊牵引进行收卷,得到外表面具有致密球晶,内表面具有片晶的聚丁二酸丁二醇酯初纤;将聚丁二酸丁二醇酯初纤放入真空烘箱进行干燥除水;所述口模的内径为1.5mm,外径为3~6mm;
13.(3)将干燥除水后的聚丁二酸丁二醇酯初纤进行热处理退火,得到高强高弹可降解中空纤维。
14.步骤(1)中所述聚丁二酸丁二醇酯生物降解树脂熔融指数为5g/10min,测试条件为190℃下采用2.16kg载荷测试。
15.步骤(1)中所述干燥的温度为50~80℃,干燥的时间为2~8h,优选为4~8h;步骤(2)中所述挤出成型的温度为130~200℃,优选为140~180℃。
16.步骤(2)中所述的熔体在所述口模的挤出速度与牵引辊线速度比为1:(20~100);牵引辊与口模的距离为50mm~200mm。
17.步骤(2)中所述的真空烘箱度的温度为40~60℃。
18.步骤(3)中所述的热处理的温度为90~110℃,热处理的时间为30~60min。
19.一种由上述的制备方法制备得到的高强高弹可降解中空纤维,所述高强高弹可降解中空纤维在合适的制备条件下,所得可降解中空纤维强度高达1.81mpa的模量以及具有91%弹性回复率的高强高弹性能。
20.上述的高强高弹可降解中空纤维在香烟过滤嘴中的应用。
21.本发明的原理是:
22.(1)由于不同的壁厚会导致pbs中空纤维有着不同结构与性能,较薄的壁厚会使熔体的冷却速度变慢,挤出拉伸后会使pbs形成更多的片晶进而有着更高的强度以及弹性回复率,而较厚的壁厚则会形成更多的球晶无法制备高强高弹的pbs中空纤维。
23.(2)环形风刀会使缓慢结晶的pbs中空纤维外壁熔体瞬间降温,形成致密的球晶用于阻隔烟中的焦油等粒子;不同的风刀温度会影响中空纤维外壁的冷却速度,更低的环形风刀温度能使得pbs中空纤维外壁能形成更多的球晶。
24.(3)温控水槽的温度可以使pbs中空纤维内壁形成具有弹性的片状晶体,这是使pbs中空纤维能够拥有高强高弹的前提。不同的水槽温度会影响中空纤维内壁的冷却速度,并且高温度的水槽也能够使pbs冷却过程中,减少的冷却过程中产生的内应力,使其机械性能更好。
25.(4)牵伸比须控制在(20~100):1,如果过低,pbs会展现出其特殊的应力震荡行为,并且弹性回复率急剧下降,其内部含有大量的球晶结构,不适用于制备高弹高强的pbs中空纤维。
26.综上,本发明的创新点在于制备中空纤维的过程中采用的口模外径、环形风刀温度、冷却水槽温度、牵伸比。这几个不同的条件,在适中的范围时能制备具有不对称结构的中空纤维,这种不对称的结构是制备高强高弹可降解中空纤维的关键,热处理是在这基础上使其获得更高更好的强度和弹性回复率。
27.本发明相对于现有技术具有如下的优点及效果:
28.本发明制备得到的高强高弹可降解中空纤维外表面的球晶可以阻挡香烟中的焦油等微粒,并且内表面的片晶能形成微孔隙,使得空气可以流通;所述高强高弹可降解中空纤维能够在阻隔香烟中的有害颗粒的同时,不影响气体的流动,并且其可降解性使得烟头随意丢弃并且造成环境污染的危害减少。
附图说明
29.图1为实施例4的弹性回复率测试。
30.图2为实施例9的弹性回复率测试。
31.图3为实施例10的弹性回复率测试。
32.图4为对比例2的弹性回复率测试。
具体实施方式
33.下面结合实施例和附图对本发明作进一步详细的描述,但本发明的实施方式不限于此。
34.以下实施例所使用的干燥的pbs树脂是将熔融指数为5g/10min(测试条件为190℃下采用2.16kg载荷测试)的pbs树脂用真空烘箱50~80℃下进行干燥除水4~8h。
35.实施例1
36.将干燥的pbs树脂加入单螺杆挤出机中熔融得到pbs熔体,pbs熔体经内径为1.5mm,外径为3mm的140℃口模挤出成型,成型后经20℃的环形风刀鼓风冷却表面,再经过一个带有温控系统的水槽对中空纤维进行冷却,控制水槽的冷却温度为30℃,最后将中空纤维上牵引辊牵引收卷得到pbs初纤;牵引辊线速度与口模挤出速度的线速度比为20:1,牵引辊与口模的间距为100mm。将pbs初纤放入40℃真空烘箱进行干燥除水;最后对干燥除水后的pbs初纤进行退火热处理得到pbs中空纤维,处理温度为90℃,时间为30min。
37.实施例2
38.将干燥的pbs树脂加入单螺杆挤出机中熔融得到pbs熔体,pbs熔体经内径为1.5mm,外径为4mm的140℃口模挤出成型,成型后经20℃的环形风刀鼓风冷却表面,再经过一个带有温控系统的水槽对中空纤维进行冷却,控制水槽的冷却温度为40℃,最后将中空纤维上牵引辊牵引收卷得到pbs初纤;牵引辊线速度与口模挤出速度的线速度比为50:1,牵引辊与口模的间距为100mm。将pbs初纤放入60℃真空烘箱进行干燥除水;最后对干燥除水后的pbs初纤进行退火热处理得到pbs中空纤维,处理温度为90℃,时间为30min。
39.实施例3
40.将干燥的pbs树脂加入单螺杆挤出机中熔融得到pbs熔体,pbs熔体经内径为1.5mm,外径为3mm的140℃口模挤出成型,成型后经20℃的环形风刀鼓风冷却表面,再经过一个带有温控系统的水槽对中空纤维进行冷却,控制水槽的冷却温度为50℃,最后将中空纤维上牵引辊牵引收卷得到pbs初纤;牵引辊线速度与口模挤出速度的线速度比为100:1,牵引辊与口模的间距为100mm。将pbs初纤放入50℃真空烘箱进行干燥除水;最后对干燥除水后的pbs初纤进行退火热处理得到pbs中空纤维,处理温度为90℃,时间为30min。。
41.实施例4
42.将干燥的pbs树脂加入单螺杆挤出机中熔融得到pbs熔体,pbs熔体经内径为1.5mm,外径为5mm的140℃口模挤出成型,成型后经15℃的环形风刀鼓风冷却表面,再经过一个带有温控系统的水槽对中空纤维进行冷却,控制水槽的冷却温度为30℃,最后将中空纤维上牵引辊牵引收卷得到pbs初纤;牵引辊线速度与口模挤出速度的线速度比为100:1,牵引辊与口模的间距为100mm。将pbs初纤放入50℃真空烘箱进行干燥除水;最后对干燥除水后的pbs初纤进行退火热处理得到pbs中空纤维,处理温度为90℃,时间为60min。弹性回复率测试如图1所示。
43.实施例5
44.将干燥的pbs树脂加入单螺杆挤出机中熔融得到pbs熔体,pbs熔体经内径为1.5mm,外径为3mm的140℃口模挤出成型,成型后经15℃的环形风刀鼓风冷却表面,再经过一个带有温控系统的水槽对中空纤维进行冷却,控制水槽的冷却温度为50℃,最后将中空纤维上牵引辊牵引收卷得到pbs初纤;牵引辊线速度与口模挤出速度的线速度比为100:1,牵引辊与口模的间距为100mm。将pbs初纤放入50℃真空烘箱进行干燥除水;最后对干燥除水后的pbs初纤进行退火热处理得到pbs中空纤维,处理温度为100℃,时间为60min。。
45.实施例6
46.将干燥的pbs树脂加入单螺杆挤出机中熔融得到pbs熔体,pbs熔体经内径为1.5mm,外径为3mm的140℃口模挤出成型,成型后经10℃的环形风刀鼓风冷却表面,再经过一个带有温控系统的水槽对中空纤维进行冷却,控制水槽的冷却温度为50℃,最后将中空纤维上牵引辊牵引收卷得到pbs初纤;牵引辊线速度与口模挤出速度的线速度比为100:1,牵引辊与口模的间距为100mm。将pbs初纤放入40℃真空烘箱进行干燥除水;最后对干燥除水后的pbs初纤进行退火热处理得到pbs中空纤维,处理温度为110℃,时间为30min。。
47.实施例7
48.将干燥的pbs树脂加入单螺杆挤出机中熔融得到pbs熔体,pbs熔体经内径为1.5mm,外径为3mm的160℃口模挤出成型,成型后经15℃的环形风刀鼓风冷却表面,再经过一个带有温控系统的水槽对中空纤维进行冷却,控制水槽的冷却温度为50℃,最后将中空纤维上牵引辊牵引收卷得到pbs初纤;牵引辊线速度与口模挤出速度的线速度比为20:1,牵引辊与口模的间距为150mm。将pbs初纤放入60℃真空烘箱进行干燥除水;最后对干燥除水后的pbs初纤进行退火热处理得到pbs中空纤维,处理温度为100℃,时间为30min。
49.实施例8
50.将干燥的pbs树脂加入单螺杆挤出机中熔融得到pbs熔体,pbs熔体经内径为1.5mm,外径为3mm的160℃口模挤出成型,成型后经10℃的环形风刀鼓风冷却表面,再经过一个带有温控系统的水槽对中空纤维进行冷却,控制水槽的冷却温度为40℃,最后将中空纤维上牵引辊牵引收卷得到pbs初纤;牵引辊线速度与口模挤出速度的线速度比为80:1,牵引辊与口模的间距为150mm。将pbs初纤放入50℃真空烘箱进行干燥除水;最后对干燥除水后的pbs初纤进行退火热处理得到pbs中空纤维,处理温度为110℃,时间为30min。
51.实施例9
52.将干燥的pbs树脂加入单螺杆挤出机中熔融得到pbs熔体,pbs熔体经内径为1.5mm,外径为3mm的160℃口模挤出成型,成型后经10℃的环形风刀鼓风冷却表面,再经过一个带有温控系统的水槽对中空纤维进行冷却,控制水槽的冷却温度为50℃,最后将中空
纤维上牵引辊牵引收卷得到pbs初纤;牵引辊线速度与口模挤出速度的线速度比为80:1,牵引辊与口模的间距为150mm。将pbs初纤放入50℃真空烘箱进行干燥除水;最后对干燥除水后的pbs初纤进行退火热处理得到pbs中空纤维,处理温度为110℃,时间为30min。弹性回复率测试如图2所示。
53.实施例10
54.将干燥的pbs树脂加入单螺杆挤出机中熔融得到pbs熔体,pbs熔体经内径为1.5mm,外径为3mm的160℃口模挤出成型,成型后经10℃的环形风刀鼓风冷却表面,再经过一个带有温控系统的水槽对中空纤维进行冷却,控制水槽的冷却温度为50℃,最后将中空纤维上牵引辊牵引收卷得到pbs初纤;牵引辊线速度与口模挤出速度的线速度比为100:1,牵引辊与口模的间距为150mm。将pbs初纤放入40℃真空烘箱进行干燥除水;最后对干燥除水后的pbs初纤进行退火热处理得到pbs中空纤维,处理温度为110℃,时间为30min。弹性回复率测试如图3所示。
55.实施例11
56.将干燥的pbs树脂加入单螺杆挤出机中熔融得到pbs熔体,pbs熔体经内径为1.5mm,外径为6mm的160℃口模挤出成型,成型后经10℃的环形风刀鼓风冷却表面,再经过一个带有温控系统的水槽对中空纤维进行冷却,控制水槽的冷却温度为40℃,最后将中空纤维上牵引辊牵引收卷得到pbs初纤;牵引辊线速度与口模挤出速度的线速度比为100:1,牵引辊与口模的间距为150mm。将pbs初纤放入60℃真空烘箱进行干燥除水;最后对干燥除水后的pbs初纤进行退火热处理得到pbs中空纤维,处理温度为110℃,时间为30min。
57.实施例12
58.将干燥的pbs树脂加入单螺杆挤出机中熔融得到pbs熔体,pbs熔体经内径为1.5mm,外径为3mm的180℃口模挤出成型,成型后经5℃的环形风刀鼓风冷却表面,再经过一个带有温控系统的水槽对中空纤维进行冷却,控制水槽的冷却温度为50℃,最后将中空纤维上牵引辊牵引收卷得到pbs初纤;牵引辊线速度与口模挤出速度的线速度比为70:1,牵引辊与口模的间距为200mm。将pbs初纤放入40℃真空烘箱进行干燥除水;最后对干燥除水后的pbs初纤进行退火热处理得到pbs中空纤维,处理温度为110℃,时间为30min。
59.实施例13
60.将干燥的pbs树脂加入单螺杆挤出机中熔融得到pbs熔体,pbs熔体经内径为1.5mm,外径为3mm的180℃口模挤出成型,成型后经5℃的环形风刀鼓风冷却表面,再经过一个带有温控系统的水槽对中空纤维进行冷却,控制水槽的冷却温度为50℃,最后将中空纤维上牵引辊牵引收卷得到pbs初纤;牵引辊线速度与口模挤出速度的线速度比为100:1,牵引辊与口模的间距为200mm。将pbs初纤放入50℃真空烘箱进行干燥除水;最后对干燥除水后的pbs初纤进行退火热处理得到pbs中空纤维,处理温度为110℃,时间为30min。
61.对比例1
62.将干燥的pbs树脂加入单螺杆挤出机中熔融得到pbs熔体,pbs熔体经内径为1mm,外径为2mm的140℃口模挤出成型,成型后经30℃的环形风刀鼓风冷却表面,再经过一个带有温控系统的水槽对中空纤维进行冷却,控制水槽的冷却温度为20℃,最后将中空纤维上牵引辊牵引收卷得到pbs初纤。牵引辊线速度与口模挤出速度的线速度比为5:1,牵引辊与口模的间距为150mm。将pbs初纤放入40℃真空烘箱进行干燥除水;最后对干燥除水后的pbs
初纤进行退火热处理得到pbs中空纤维,处理温度为110℃,时间为30min。
63.对比例2
64.将干燥的pbs树脂加入单螺杆挤出机中熔融得到pbs熔体,pbs熔体经内径为0.5mm,外径为2mm的140℃口模挤出成型,成型后经30℃的环形风刀鼓风冷却表面,再经过一个带有温控系统的水槽对中空纤维进行冷却,控制水槽的冷却温度为20℃,最后将中空纤维上牵引辊牵引收卷得到pbs初纤。牵引辊线速度与口模挤出速度的线速度比为5:1,牵引辊与口模的间距为150mm。将pbs初纤放入40℃真空烘箱进行干燥除水;最后对干燥除水后的pbs初纤进行退火热处理得到pbs中空纤维,处理温度为110℃,时间为30min。弹性回复率测试如图4所示。
65.对比例3
66.将干燥的pbs树脂加入单螺杆挤出机中熔融得到pbs熔体,pbs熔体经内径为3mm,外径为7mm的160℃口模挤出成型,成型后经30℃的环形风刀鼓风冷却表面,再经过一个带有温控系统的水槽对中空纤维进行冷却,控制水槽的冷却温度为15℃,最后将中空纤维上牵引辊牵引收卷得到pbs初纤。牵引辊线速度与口模挤出速度的线速度比为80:1,牵引辊与口模的间距为100mm。将pbs初纤放入40℃真空烘箱进行干燥除水;最后对干燥除水后的pbs初纤进行退火热处理得到pbs中空纤维,处理温度为110℃,时间为30min。
67.对比例4
68.将干燥的pbs树脂加入单螺杆挤出机中熔融得到pbs熔体,pbs熔体经内径为3mm,外径为7mm的180℃口模挤出成型,成型后经25℃的环形风刀鼓风冷却表面,再经过一个带有温控系统的水槽对中空纤维进行冷却,控制水槽的冷却温度为10℃,最后将中空纤维上牵引辊牵引收卷得到pbs初纤。牵引辊线速度与口模挤出速度的线速度比为80:1,牵引辊与口模的间距为100mm。将pbs初纤放入40℃真空烘箱进行干燥除水;最后对干燥除水后的pbs初纤进行退火热处理得到pbs中空纤维,处理温度为110℃,时间为30min。
69.对实施例1-13以及对比例1-4进行拉伸测试,拉伸速率为50mm/min,夹样距离为50mm,应变倍率为100%。测试数据中,模量为前1%区域的斜率;拉伸强度为应变100%时的强度;弹性回复率为pbs中空纤维拉伸应变到100%保持1min后回到初始位置,再从初始位置拉伸到100%过程中,应力开始增加的应变点,50mm减去该应变点除以50mm即为弹性回复率。
70.表1为实施例各项性能
[0071][0072][0073]
表1给出了各项实施例的参数情况,实施例1-13为不同热处理温度下的pbs中空纤维,对比例1-4则为进行过最佳热处理条件的中空纤维。可以发现,在高的牵伸比时,pbs中空纤维有着较高的模量以及应变100%时拉伸强度,并且最佳实施例为实施例10。由上述性能测试分析可知,低的热处理温度以及处理时间的长短对pbs中空纤维性能影响不大,而合适的热处理温度能极大的提高pbs中空纤维的各项性能,在弹性回复率上尤其明显。并且冷却水槽的温度对pbs中空纤维的弹性回复率有着一定的影响,如高水温可以使pbs中空纤维内部的晶体更好的生长从而使得pbs中空纤维内部有着更好的片晶结构,能有更好的弹性回复率;大的口模外径会使熔体冷却得更慢,形成的片晶会更少。由对比例2可知,在低牵伸比下,pbs会展现出其特殊的应力震荡行为,并且弹性回复率急剧下降,其内部含有大量的球晶结构,不适用于制备高弹高强的pbs中空纤维。由此可以更加说明合适的热处理、冷却水温、口模内外径对于制备高强高弹pbs中空纤维是非常有效且十分必要
[0074]
上述实施例为本发明较佳的实施方式,但本发明的实施方式并不受上述实施例的限制,其他的任何未背离本发明的精神实质与原理下所作的改变、修饰、替代、组合、简化,均应为等效的置换方式,都包含在本发明的保护范围之内。